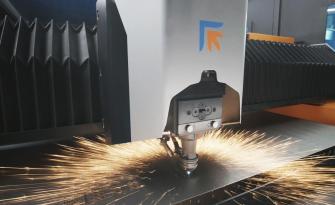
Sustainable Manufacturing: The Heart of Industrial Progress
In the realm of modern manufacturing, sustainability is no longer a mere option; it has become a pivotal goal shared by companies worldwide. This shift towards sustainable practices is driven by a collective awareness of the environmental footprint left by industrial activities. Manufacturing processes are being reimagined, not only to meet the increasing demands for efficiency and cost-effectiveness but also to align with the growing environmental consciousness.
The European Union has been particularly proactive in setting policies and regulations focused on sustainable production. These policies emphasize the reduction of material and energy waste, aiming to transform the manufacturing sector into an eco-friendlier and resource-efficient industry. The European Union's commitment to sustainability is evident in its stringent guidelines, which encourage industries to adopt practices that minimize environmental impact while maximizing productivity.
Laser cutting of sheet metal, alongside other laser-based technologies, have emerged as frontrunners in the pursuit of sustainable manufacturing. These technologies are uniquely positioned to reduce waste in several key areas: material, energy, and time. By offering precision and efficiency, laser technologies significantly reduce material waste, which is a common issue in traditional manufacturing methods. The accuracy of laser cutting ensures that materials are used optimally, minimizing scrap, and maximizing yield. This precision translates into a direct cost saving for manufacturers, as less material is wasted, and more product is produced from the same amount of raw materials.
Energy efficiency is another critical aspect where laser technologies shine. Compared to conventional manufacturing methods, laser-based processes often require less energy, leading to lower operational costs and a reduced carbon footprint. This energy efficiency is not only beneficial for the environment but also for the company's bottom line, as reduced energy consumption translates to lower utility bills.
Time efficiency is a further advantage offered by laser technologies. The speed and automation of laser cutting reduce production times, leading to faster turnaround times for projects. This efficiency enables manufacturers to meet customer demands more quickly, improving overall productivity. The time saved also means reduced operational costs, as less time is spent on each manufacturing stage. Being quick to perform a laser cutting process also means reducing energy consumption, provided that the ratio of energy to processing time remains the same, which we at Prima Power have managed to achieve with our machines.
Moreover, the adaptability of laser technology makes it suitable for a wide range of applications, from small-scale precision work to large-scale industrial projects. This versatility allows for broader adoption of laser technologies across various sectors, further enhancing their impact on sustainable manufacturing practices.
Laser Precision: Balancing Environmental Sustainability with Economic Viability
In the intricate tapestry of industrial manufacturing, laser cutting technology emerges as a beacon of innovation, adeptly balancing, as we said before, environmental sustainability with economic viability. This balance is exemplified in the groundbreaking research by Professor Bekir Sami Yilbas, titled "Laser cutting of various materials: Kerf width size analysis and life cycle assessment of cutting process", published in 2017. Yilbas' study delves into the nuanced realms of laser cutting, particularly focusing on various metal alloys, and offers critical insights into how this technology can be harnessed for sustainable manufacturing.
This research clearly shows that, by understanding and optimizing kerf width, manufacturers can significantly enhance both sustainability and cost-effectiveness.
The study further employs a life cycle assessment to evaluate the environmental impact of laser cutting. This comprehensive assessment underscores the urgent need for sustainable practices at every stage of product design and manufacturing.
The importance of Yilbas' work cannot be overstated in the context of modern manufacturing. By demonstrating how precise control over laser cutting parameters can minimize defects and waste, the study lays the groundwork for more sustainable manufacturing practices.
This way, in the larger picture of industrial manufacturing, the interplay between laser cutting, cost savings, and sustainability becomes evident. By reducing material waste, manufacturers not only adhere to environmental standards but also cut down costs associated with raw materials. The precision of laser cutting means less material is discarded as scrap, and more of the purchased material is converted into the final product, leading to significant cost savings. Additionally, the time efficiency of laser technologies means faster production cycles and energy savings, further driving down operational costs.
Eco-Efficient Solutions: Prima Power's Path to Sustainable Profitability
Prima Power manages to stand at the forefront of these innovation processes, championing a new era of eco-efficient solutions. Our commitment to sustainability is not just an environmental statement; it's a robust business strategy offering tangible economic benefits to our clients. By integrating innovative technologies and processes, we are reshaping the manufacturing world, making sustainability synonymous with profitability.
Our focus on refining production cycles enhances process efficiency, significantly reducing material and energy wastage without compromising the final output's quality. The advanced servo-electric technology we've pioneered since 1998 ensures resource conservation alongside substantial economic savings for manufacturers.
Laser cutting technology, a cornerstone of our sustainability efforts, offers unmatched precision and flexibility. Capable of processing a diverse range of materials and thicknesses, our 2D laser cutting machines ensure minimal material waste and high-quality output, leading to cost savings in material usage and a reduction in environmental impact. Knowing that laser manufacturing electrical energy consumption is surely a problematic issue both for costs and ecological footprint, we at Prima Power managed to rise our machines wall-plug efficiency up to 40%.
The implementation of our Flexible Manufacturing System technology streamlines both material and information systems within facilities. This system is particularly effective in series production and small batch manufacturing, where resource optimization is key. We provide comprehensive storage solutions that automate the flow of materials, ensuring timely availability without delays. From single tower solutions to comprehensive automated warehouses, we cater to every application and plant size, enhancing overall efficiency and reducing waste.
Our automation solutions are designed to level up production flows by reducing manual operations of low added value. By automating the working cycle of machines, we enable the possibility of unmanned 24/7 production, increasing both the quality of finished products and production efficiency.
We also offer a range of material handling solutions, including high-performance automatic loading and stacking robots, automatic loading and unloading devices, and handling robots for combined machines. These systems are crucial in reducing manual labor and enhancing overall process efficiency. Understanding the varying needs of our clients, we provide entry-level solutions for material handling, ensuring that businesses of all sizes can benefit from automated efficiency.
We invite companies across all sectors to explore the potential of sustainable manufacturing with Prima Power. If you are looking to reduce waste, enhance efficiency, and improve your bottom line, Prima Power is your ideal partner. Contact us to discover how our products and services can help you achieve sustainable manufacturing excellence. Let's work together to create a greener, more profitable future.