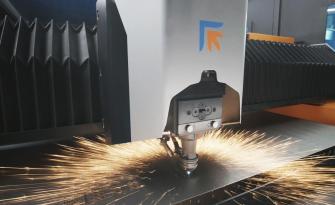
Prendre le Night train pour une meilleure productivité
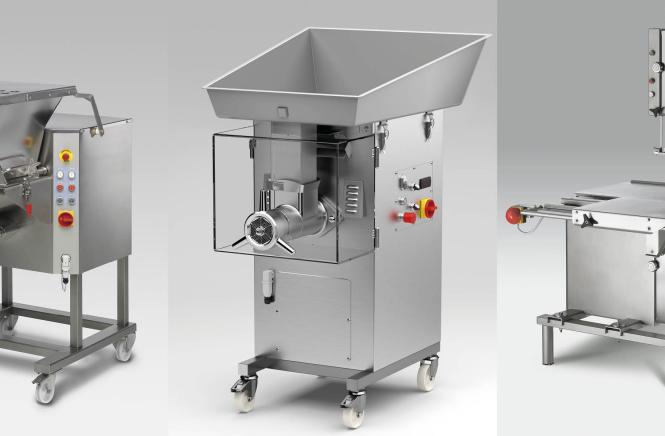
Le groupe Minerva de Bologne, en Italie est une entreprise qui incarne véritablement les compétences, la technologie et l'esprit d'entreprise.
Le groupe Minerva de Bologne, en Italie est une entreprise qui incarne véritablement les compétences, la technologie et l'esprit d'entreprise.
Des idées claires et de la détermination sont les traits de caractère qui ont permis à Andrea Salati Chiodini, DSI et responsable technique du groupe, de se concentrer sur l'automatisation des processus dans l'atelier. Cela a permis à l'entreprise de prendre une longueur d'avance sur ses concurrents dans le monde très réglementé des machines pour l'industrie alimentaire. Ce résultat a été obtenu grâce à l'installation du système de fabrication flexible (FMS) entièrement automatisé et intégré de Night Train par Prima Power, capable de produire un produit semi-fini qui est immédiatement prêt pour les étapes de fabrication suivantes.
Aujourd'hui, le groupe Minerva Omega, dont la réputation internationale a été renforcée par un système de gestion moderne et gagnant, peut donc se targuer d'avoir l'une des gammes de produits les plus complètes du marché et un portefeuille de clients bien établi, présent dans tous les secteurs de l'alimentation, dans la grande distribution ainsi que par l'intermédiaire de distributeurs dans tous les pays du monde. Salati Chiodini, ainsi que son frère et sa sœur, représentent la troisième génération de la famille à la tête de cette entreprise industrielle historique et pérenne.
Minerva Omega Group s.r.l. est née en 2012 de la fusion de deux entreprises historiques, Minerva de Bologne et Omega Ceg de Varèse. Les deux entreprises ont une longue histoire, une tradition et une expérience. La Minerva, qui fêtera ses 75 ans d'activité en 2020, a été fondée en 1945 à Bologne, une région à forte tradition mécanique et d'ingénierie, grâce à l'initiative entrepreneuriale de Mario Chiodini, le grand-père des propriétaires actuels. Elle conçoit et fabrique des machines pour la transformation de la viande, la restauration, l'industrie alimentaire, les centres de conditionnement, et propose une gamme de produits de haute qualité avec un excellent rapport qualité-prix et une longue durée de vie.
« Nous sommes l'une des plus anciennes entreprises familiales d'Italie, » explique Andrea Salati Chiodini. « C'est précisément grâce à ce leadership entrepreneurial et à un état d'esprit managérial orienté vers le marketing que nous avons amené Minerva à acquérir et à incorporer certains de nos concurrents : d'abord Artex, basé à Bologne, puis Omega, propriétaire d'autres marques historiques telles que Ceg, General Machine, Regina, Suprema et, récemment, Aria et Mincer2000, toutes marques bien connues des experts du secteur dans le monde entier. »
L'excellence italienne
Le groupe Minerva Omega est un exemple d'entreprise entièrement italienne bien établie et de premier plan dans l'industrie, avec une forte capacité d'investissement dans la conception et le développement de nouveaux modèles, dans des équipements automatisés et des lignes de production. « Nous croyons en la qualité du travail, preuve d'un engagement collectif important réalisé par nos employés et associés, » explique Salati Chiodini.
« Malgré les grandes difficultés et la concurrence de pays dans lesquels la fabrication a un coût bien inférieur, nous défendons et soutenons de toutes nos forces la marque Made-in-Italy, sans délocaliser la production des principaux composants et l'assemblage des machines des établissements de Bologne et de Varèse. »
L'engagement est important... et les investissements, pour nous maintenir technologiquement et qualitativement compétitifs, sont réalisés régulièrement et impliquent toute la chaîne d'approvisionnement. L'excellence, la compétitivité et la qualité sont des valeurs impératives pour nous. La croissance continue de l'entreprise sur tous les marchés est la meilleure réponse à la question de savoir s'il vaut encore la peine d'investir dans la production manufacturière italienne aujourd'hui. »
Un choix technologique majeur
La mission du groupe Minerva Omega est claire. Il y a quelque temps, l'entreprise s'est engagée dans la voie de l'automatisation des processus de fabrication les plus avancés, non seulement dans un souci de compétitivité mais aussi pour respecter les normes de qualité exigées par la réglementation en vigueur sur les machines alimentaires.
« Nous avons introduit les premières machines automatiques en 1984 », explique Salati Chiodini. « Il s'agissait de machines-outils à enlèvement de copeaux, car notre produit résultait auparavant du traitement de corps moulés. Très peu de tôles ont été utilisées, et leur traitement a été sous-traité. Vers 1994/95, cependant, nous avons commencé à percevoir un changement sur le marché. En plus de la fonctionnalité, une certaine valeur esthétique commençait à être exigée pour les machines. Nous avons donc introduit l'acier inoxydable et commencé à fabriquer certaines machines avec ce matériau, tout en continuant à faire appel à des sous-traitants. »
« En 1998, nous avons décidé d'acheter notre premier système de découpe laser - un système Prima Industrie Platino , avec une zone de travail typique de 1 500 x 3 000 mm et un changeur automatique de palettes, ce qui a donné une forte impulsion à l'entreprise. En 2002, nous avons commencé à construire ces nouveaux locaux où nous avons également installé une solution combinée laser/poinçon Finn Power avec une source de CO2 de 2,5 kW, que nous avons utilisée jusqu'à l'année dernière. Ce choix découle de la volonté d'automatiser le plus possible le cycle de traitement. C'est pourquoi nous avons décidé de combiner la machine avec une unité de stockage Night Train FMS comprenant 10 tours et 12 tiroirs. Une organisation de la production innovante et efficace qui nous a permis de donner une forte impulsion à l'activité sans accroc jusqu'au 18 janvier 2018, où un incendie a ravagé notre département tôlerie, nous obligeant à externaliser la transformation de l'acier pendant quelques mois. Nous avons également commencé à remplacer ce qui avait été détruit, en remettant sur la table tous les grands acteurs du marché, même si, en fin de compte, nous avons préféré poursuivre sur la voie technologique dans laquelle nous nous étions engagés plusieurs années auparavant, et avons opté pour Prima Power, le seul système à nous assurer la continuité après la reprise de Finn Power. On pourrait croire qu'il s'agissait d'un choix basé sur la sympathie, mais je vous assure que nous avons vraiment remis tout le monde en jeu en analysant les forces et les faiblesses de la solution de chacun. Finalement, en sachant précisément ce dont nous avions besoin, Prima Power s'est avéré être le système qui correspondait le mieux à nos attentes en matière de production et à nos besoins également en termes d'aménagement de l'usine. »
« Nous avons pris une décision sous le signe de la continuité », ajoute Andrea Salati Chiodini. « En termes de calendrier également, car le fait de pouvoir utiliser la même unité de stockage nous a permis de réduire les délais d'installation de plusieurs mois. C'était un choix judicieux, cohérent avec notre volonté de réduire au maximum les temps d'arrêt, mais aussi parce qu'en recourant à des partenaires extérieurs pour la tôlerie, on ne peut jamais vraiment maîtriser la situation, tant en termes de délais que de niveau de qualité auquel nos clients étaient habitués. »
Un système véritablement sur mesure
Aujourd'hui, il va sans dire que le nouveau cœur battant de la production de Minerva Omega est toujours le Night Train, composé de 14 blocs et de 200 tiroirs, qui s'impose comme le nec plus ultra dans le domaine des unités de stockage automatisées. Il est connecté à la machine de poinçonnage/découpe laser Prima Power Combi Genius 1530 avec laser à fibre de 4 kW et robot de chargement/déchargement et d'empilage LSR6, ainsi qu'à un système de découpe laser à fibre bidimensionnel Prima Power Laser Genius 1530 avec moteurs linéaires, équipé d'une source à fibre de 6 kW, d'un robot de chargement et de déchargement de tôle LU et d'un robot de tri et d'empilage automatique LST.
« Nous avons spéculé sur quatre schémas, car nous avons essayé d'optimiser le système en fonction de l'espace disponible en récupérant, là où c'était possible, ne serait-ce que 15/20 cm pour améliorer chaque petit détail, comme le passage des chariots élévateurs ou les flux de déchargement des copeaux, ou encore les portes d'accès des opérateurs », poursuit Salati Chiodini. « À cet égard, je tiens à souligner la grande volonté et la capacité de personnalisation de Prima Power, qui a réussi à créer un produit vraiment sur mesure, car ils se sont mis à notre place pour mieux comprendre nos problèmes et n'ont jamais proposé de raccourcis en termes de solutions standard. Ils ont immédiatement compris l'importance d'offrir un système de production totalement automatisé, capable de fabriquer un produit semi-fini immédiatement prêt pour les étapes suivantes. La tôle est introduite, et le produit fini ayant le niveau de finition que nous exigeons est sorti. Pour nous, cela a toujours été un aspect gagnant et le résultat de notre habitude de travailler 24 heures sur 24 et 7 jours sur 7. La technologie a atteint un tel niveau de fiabilité que nous pouvons lancer une imbrication le vendredi après-midi, et le lundi matin, toutes les pièces sont prêtes à être triées dans la zone de pliage - où une Prima Power eP-0520a également été installée - et dans la zone d'assemblage ; c'est un aspect essentiel pour nous permettre de planifier notre travail, de réduire les temps d'arrêt et de minimiser les rejets »
Machine combinée ou découpe au laser ?
Aujourd'hui, la disposition de l'installation de Prima Power Night Train permet à Minerva Omega de fonctionner à la fois sur la base de la fabrication à la commande et sur la base de l'inventaire des travaux en cours avec l'unité de stockage, qui est également utilisée pour stocker les pièces semi-finies. Le traitement à la commande comprend les commandes étrangères caractérisées par de grandes quantités. Une commande est saisie dans le système de gestion de l'entreprise, une date de livraison estimée (conforme aux attentes du client) est générée et la production est lancée. MRP gère tout, des commandes aux fournisseurs de composants commerciaux ainsi que, en interne, les opérations d'enlèvement des copeaux et de découpe des tôles. Chaque phase du cycle est planifiée au moyen d'un outil de planification qui gère de manière logique et efficace le flux de travail sur les différentes machines de l'atelier, ainsi que dans les différentes étapes de progression, jusqu'à l'assemblage et la livraison du produit. En ce qui concerne les lancements de production liés aux performances du système Prima Power Night Train, chez Minerva, on essaie d'exploiter les processus d'imbrication d'usinage de manière à obtenir le moins de rebuts possible, tout en optimisant au maximum le traitement.
« Ayant des pièces composées à 90% de tôle d'acier inoxydable, nous parvenons toujours à créer d'excellents processus d'imbrication qui combinent le meilleur mélange de pièces, voire de consommables, en fonction des commandes à traiter. Nous essayons de rassembler le plus de pièces possible dans l'imbrication afin d'arriver à un pourcentage de remplissage de la feuille de 85% », explique Salati Chiodini.
Il était également intéressant de comprendre quels aspects sont pris en compte pour décider si un type de pièce doit être traité sur un Combi Genius ou sur un système de découpe Laser Genius. Dans ce cas, la réponse de Salati Chiodini était claire et sans ambiguïté : « Nous ne fabriquons que des pièces à découper ou des pièces épaisses sur le système laser, tandis que nous utilisons l'unité combinée pour fabriquer toutes les pièces qui nécessitent d'autres processus de travail, comme les déformations, les trous filetés, le gaufrage, les encoches et les fentes. Si, toutefois, je devais établir une comparaison avec le passé, lorsque nous avions des lasers CO2 au lieu de sources à fibres, je dirais que l'aspect le plus évident est peut-être celui lié à la consommation d'énergie, car nous réalisons des économies assez importantes si l'on considère que la machine combinée seule consommait environ 80kW, alors qu'aujourd'hui, avec les deux machines, nous n'atteignons pas ce chiffre.
Le laser à fibre ne nécessite que très peu d'entretien et garantit une coupe plus fine et de meilleure qualité dans la plupart des cas, et ce, tant pour la machine Combi 4kW que pour la Laser Genius 6kW, qui assurent des performances de coupe comparables.
La Laser Genius, ayant une puissance plus élevée, à épaisseur égale, parvient à obtenir une qualité légèrement supérieure et un timing plus court. Cependant, je dirais que dans les deux cas, pour une épaisseur allant jusqu'à 15 mm, nous pouvons obtenir une qualité de coupe pratiquement parfaite, conformément aux dispositions des certifications auxquelles nous sommes soumis. De plus, le fait d'avoir une coupe parfaitement finie et sans bavures nous permet d'éviter de retravailler les pièces pour les poncer ou les rectifier. Tout cela implique une réduction du temps et des avantages économiques considérables avec un impact favorable sur le client utilisateur final. »
Traduit, édité et réimprimé avec la permission de la revue Deformazione, Oct. 2019.
Le laser à fibre ne nécessite que très peu d'entretien et garantit une coupe plus fine et de meilleure qualité dans la plupart des cas, et ce, tant pour la machine Combi 4kW que pour la Laser Genius 6kW.
MACHINES COMBINÉES DE POINÇONNAGE ET DE DÉCOUPE LASER
Expertise en matière d'intégration
Approche axée sur le client
Solutions flexibles à grande vitesse
Notre approche du développement durable : la réduction de notre impact sur la planète a aussi des effets économiques. En savoir plus
Nous sommes présents dans le monde entier : trouvez le bureau Prima Power le plus proche de chez vous et contactez-nous.
© PRIMA INDUSTRIE S.p.A., single-member company | Via Torino-Pianezza, 36 - 10093 COLLEGNO (TO) ITALIA | Share Capital €26.208.185 | VAT 03736080015 - C.C.I.A.A. Torino 582421 | Reg. Impr. Torino n. 03736080015