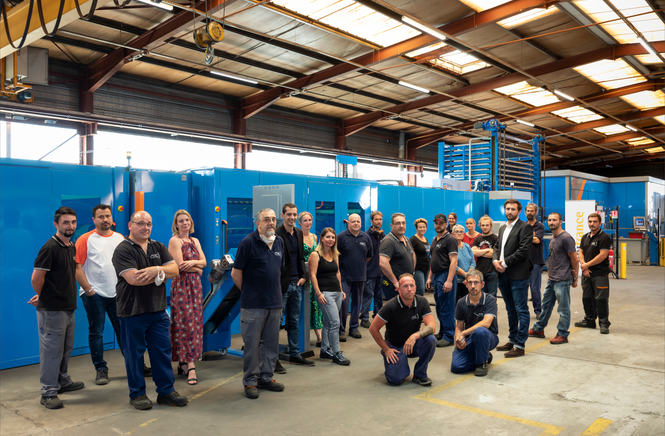
Prima Power accompagne la mise sur orbite d'ARC Industries
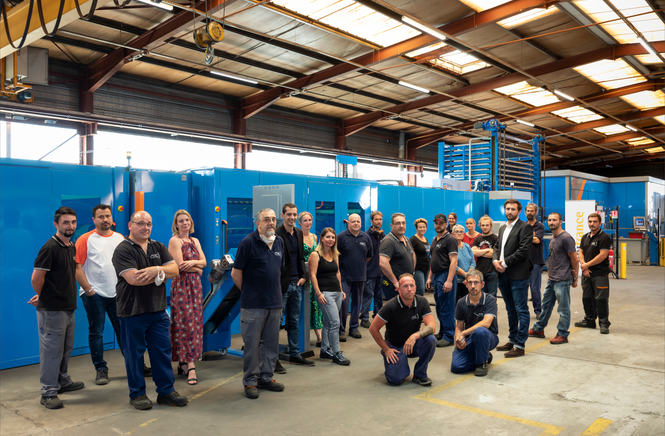
Les constructeurs de machine sont rarement confrontés à des exigences multiples comme l'a été Prima Power avec Romain de Tellier, le jeune repreneur d'Arc Industries. C'est en effet avec l'énergie de la jeunesse qu'il est parvenu à nouer une relation originale avec le constructeur.
L'origine de l'entreprise Arc Industrie remonte à 1981 lorsqu'elle fût créée par Jean-Pierre Argoud dans le but de proposer un service de tuyauterie chaudronnerie aux entreprises papetières de la région grenobloise. C'est la rencontre avec Plastic Omnium qui a permis à l'entreprise d'évoluer vers la tôlerie industrielle. Cette rencontre fût une chance pour le développement de l'entreprise, et lui a permis une politique d'investissement ambitieuse avec l'arrivée d'un robot de soudage et d'une machine laser à la fin des années quatre-vingt ou encore d'un combiné de poinçonnage découpe laser en 1996. Le début du millénaire a vu l'arrivée de nouveaux clients et le développement des compétences dans l'usinage des matériaux nobles, comme le titane, l'hastelloy ou encore des inox rares. 2008 fut avec la perte de chiffre d'affaires, ainsi que le départ d'un marché vers la Chine, une année très compliquée. Malgré la chute de 40% du chiffre d'affaires, Jean-Pierre Argoud choisit de ne pas licencier, ce qui a marqué favorablement les équipes. Cependant, le temps de remonter la pente, les investissements ont été suspendus.
Au moment de prendre sa retraite, Jean-Pierre Argoud transmit le témoin en 2016 à Romain de Tellier, qui faisait alors ses premiers pas d'entrepreneur à 31 ans, après des études d'ingénieur complétées par une formation en organisation de production en Allemagne et trois expériences professionnelles à responsabilité. « Lorsque j'ai recherché une entreprise à reprendre j'avais clairement identifié la tôlerie, éventuellement la chaudronnerie. J'ai eu la chance d'avoir des responsabilités très tôt puisqu'à 26 ans, on m'a confié la direction d'une usine. J'ai dû très rapidement m'intéresser au management et ses enjeux économiques. J'ai ensuite travaillé 3 ans au sein d'une chaudronnerie du groupe Poma » se souvient Romain de Tellier. Cette expérience industrielle et ce fort intérêt pour le secteur de la tôlerie ont été des éléments clés, qui ont poussé Jean-Pierre Argoud à faire confiance à Romain de Tellier via un crédit vendeur sur cinq ans, malgré une mise de fond insuffisante : « Un banquier m'a dit que mon dossier allait passer, mais qu'il était compliqué. J'ai également reçu le soutien de deux fournisseurs, ainsi que de BPI France et de la Fondation Arts et Métiers ».
Un projet managérial réfléchi
Le désir de reprendre une entreprise n'était pas un simple coup de tête et s'appuyait sur une réflexion aboutie sur la philosophie à mettre en place dans l'entreprise avec : « un modèle de management collaboratif pour bénéficier de l'intelligence collective, avec une bienveillance envers les personnes, qui passe par exemple par le droit à l'erreur. Nous avons un exemple concret avec une erreur dont la conséquence a été chiffrée à 25000 euros, un chiffre important pour une PME. Nous avons, non seulement accompagné la personne à l'origine de l'erreur, mais aussi l'ensemble de l'équipe pour lui permettre de comprendre pourquoi la personne qui génère ce coût reste dans l'entreprise, et en quoi cela fait progresser l'entreprise. Quand on donne aux gens des responsabilités avec la possibilité de faire des erreurs, ils en font très peu. De plus, quelle que soit la situation, les échanges se font d'adulte à adulte, avec une relation de confiance. A l'arrivée, il y a une autonomie appréciable de tout le monde, avec une sensation de liberté pour les membres de l'équipe et une forte motivation pour jouer collectif » apprécie Romain de Tellier qui a pu constater au quotidien la justesse de sa vision.
Dans cette même logique, l'entreprise a été amenée à embaucher des personnes qui ne connaissaient rien au métier, mais qui avaient une réelle volonté d'apprendre.
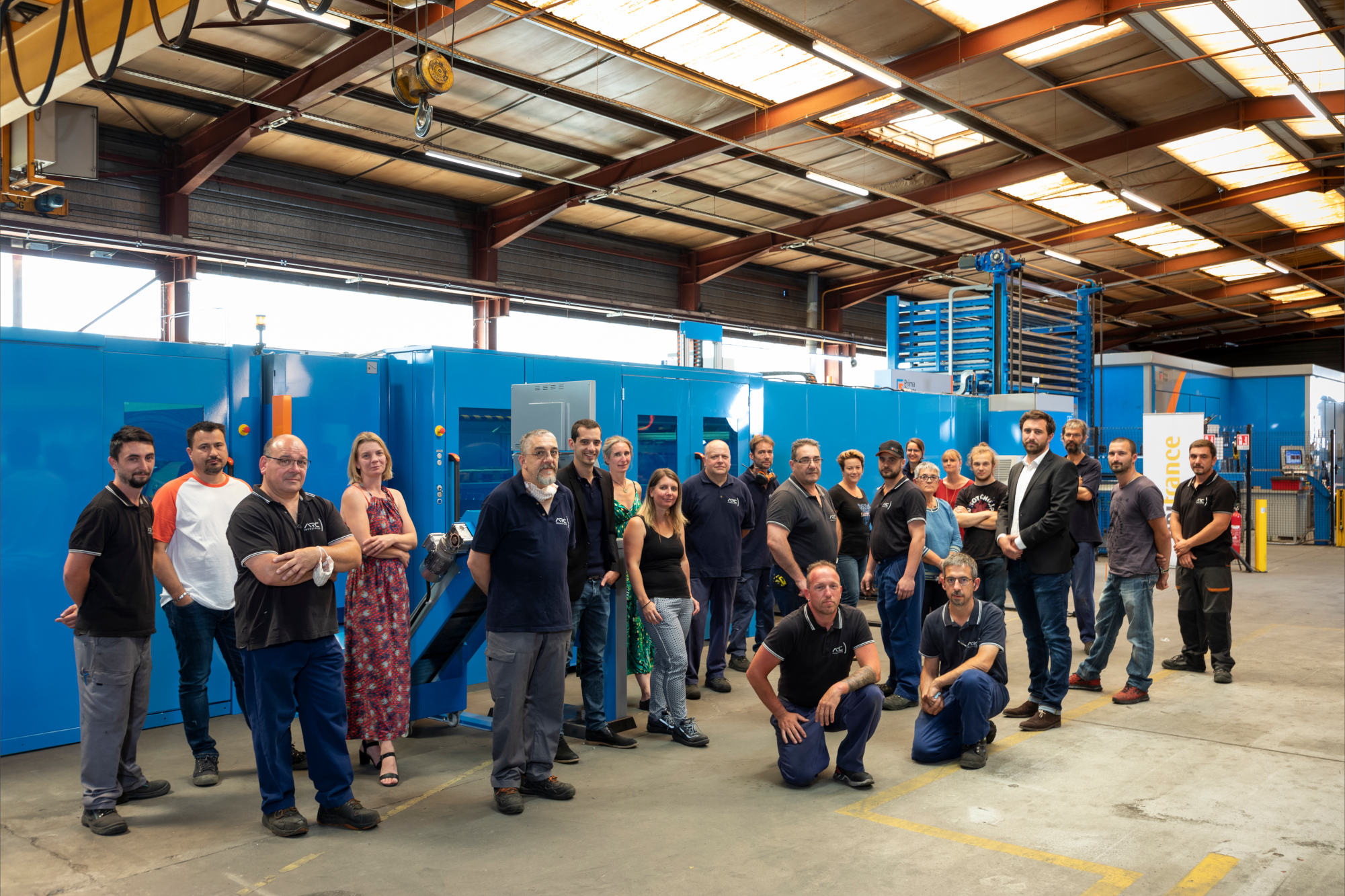
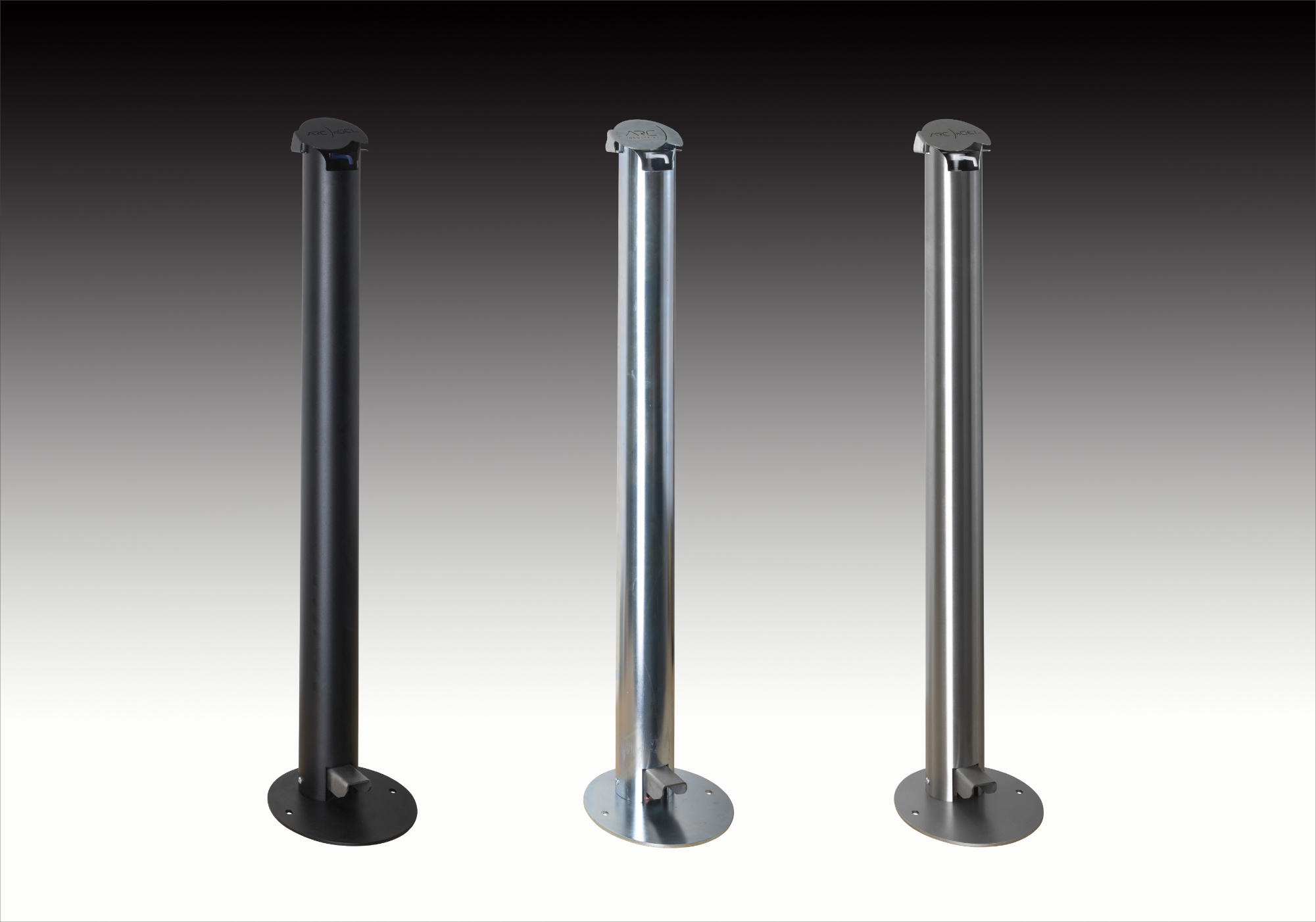
Des moyens matériels pour grossir rapidement
Si l'entreprise pouvait s'appuyer sur des grands comptes qu'elle comptait parmi ses clients, le potentiel de développement de la collaboration était proche de zéro. En effet, ces entreprises ne souhaitaient pas dépasser 30% du volume d'activité d'Arc Industries, même si elle en appréciait le savoir-faire et la qualité de service.
« Mon projet était de viser les industries qui n'avaient pas encore fait ce process de concentration de leurs fournisseurs, comme cela a été le cas dans l'automobile ou l'aéronautique. Il nous fallait donc toucher de grosses industries qui sont sur cette voie. Dès 2017, il est devenu clair qu'il fallait maîtriser la chaîne de valeur de la transformation du métal et grossir en croissance organique et en croissance externe. Or, nous sommes dans un métier où l'actif génère du chiffre » explique Romain de Tellier.
En toute logique, la réflexion sur le projet d'investissement à 3 ans a été proposé à tous les membres de l'entreprise. « J'ai proposé de faire notre liste au Père Noël » rappelle-t-il avec un large sourire. Les membres de l'équipe ont commencé par dresser un inventaire précis des lacunes de l'entreprise au niveau matériel avant de constituer la liste. Le premier jet de cette liste totalisait un montant d'environ 5 millions d'euros qui était trop important pour les capacités financières de l'entreprise. Après la prise en compte des investissements prioritaires, ce montant a été ramené à 3,8 millions sur 3 ans. Le premier étage de la fusée fût la décision d'investir dans une machine de découpe laser automatisée avec tour de chargement et palettisation. « Il s'agissait de partir d'un stock de matières premières pour obtenir des pièces prêtes à plier et triée en automatique, ce qui à l'époque était encore rare. » se souvient Christophe Berquet, Directeur Commercial de Prima Power France.
Au départ, le champ de recherche d'Arc Industries était assez large, jusqu'à des machines combinées tôle-tube. Jusqu'à ce que la rencontre avec Guy Solmini, Responsable Commercial chez Prima Power France, permette de préciser les besoins et les objectifs de l'entreprise : « Avant de nous vendre quoi que ce soit, Guy Solmini s'est intéressé à notre production et à notre manière de produire. C'est lui qui nous a poussé à aller plus loin sur l'automatisme afin d'avancer plus vite. » apprécie Romain de Tellier. Le choix s'est alors porté sur une machine laser double table avec une tour de stockage et une palettisation pièce à pièce. Un tour du marché a ensuite été réalisé, avec en particulier la volonté de construire un contrat de maintenance spécifique avec un niveau de service précis qui combinait à la fois des délais d'intervention réduits et un coût maîtrisé sous la forme d'un forfait calculé à l'avance en fonction de l'utilisation de la machine. « Nous étions dans la période de la maintenance préventive avec une évolution vers la maintenance prédictive » justifie-t-il. Comme de nombreux métiers industriels, les techniciens de maintenance sont rares et recherchés. Il était important pour Arc Industries de savoir quelle était la taille des équipes chez les différents constructeurs consultés et leur localisation, gages de rapidité d'intervention.
Prima Power a été le seul constructeur à l'époque à accepter de sortir du cadre pour construire ce contrat de maintenance : « Pour nous c'était un peu nouveau aussi. Le niveau d'exigence de Romain était relativement élevé et nous avons appris beaucoup de cet échange. Nous avons eu à faire un double travail : celui auprès de notre client afin de rester dans le domaine du possible et celui vis-à-vis de notre direction pour leur faire accepter quelque chose qu'elle n'avait jamais fait. Aujourd'hui, cela nous a permis d'être meneur en matière d'offre de maintenance et c'est devenu pour nous une arme commerciale » reconnaît Christophe Berquet.
Des visites d'entreprises ont été organisées pour voir en fonctionnement les machines de la sélection de constructeurs retenue. Assez rapidement au niveau technique, « la solution Prima Power s'est dégagée, car elle témoignait d'une bonne compréhension du flux de production avec l'enlèvement pièce à pièce qui se faisait au fil de l'eau, tandis que chez d'autres constructeurs, celui-ci se faisait après la découpe complète de la tôle. Or, nous avions constaté que ce qui marche très bien avec des tôles de 5 mm de marchait beaucoup moins bien avec des épaisseurs de 0,8 à 2 mm pour lesquelles les pièces se mettaient plus facilement en travers. » Des tests ont également été réalisés pour déterminer si le logiciel proposé par Prima Power était capable de déplier une structure complexe. Ce qui fût le cas.
La source 4 kW qui équipe la machine est capable de monter jusqu'à des épaisseurs de 25 mm acier et 15 en inox, même si Arc Industries se limite à l'acier 20 mm. La tour dispose de 9 tiroirs, dont deux sont réservés aux squelettes, ce qui permet à la machine de fonctionner la nuit, pour un total de presque 3000 heures/an, ce qui était impératif étant donné les séries à produire. Des caméras équipent la machine afin de contrôler à distance l'état de la production.
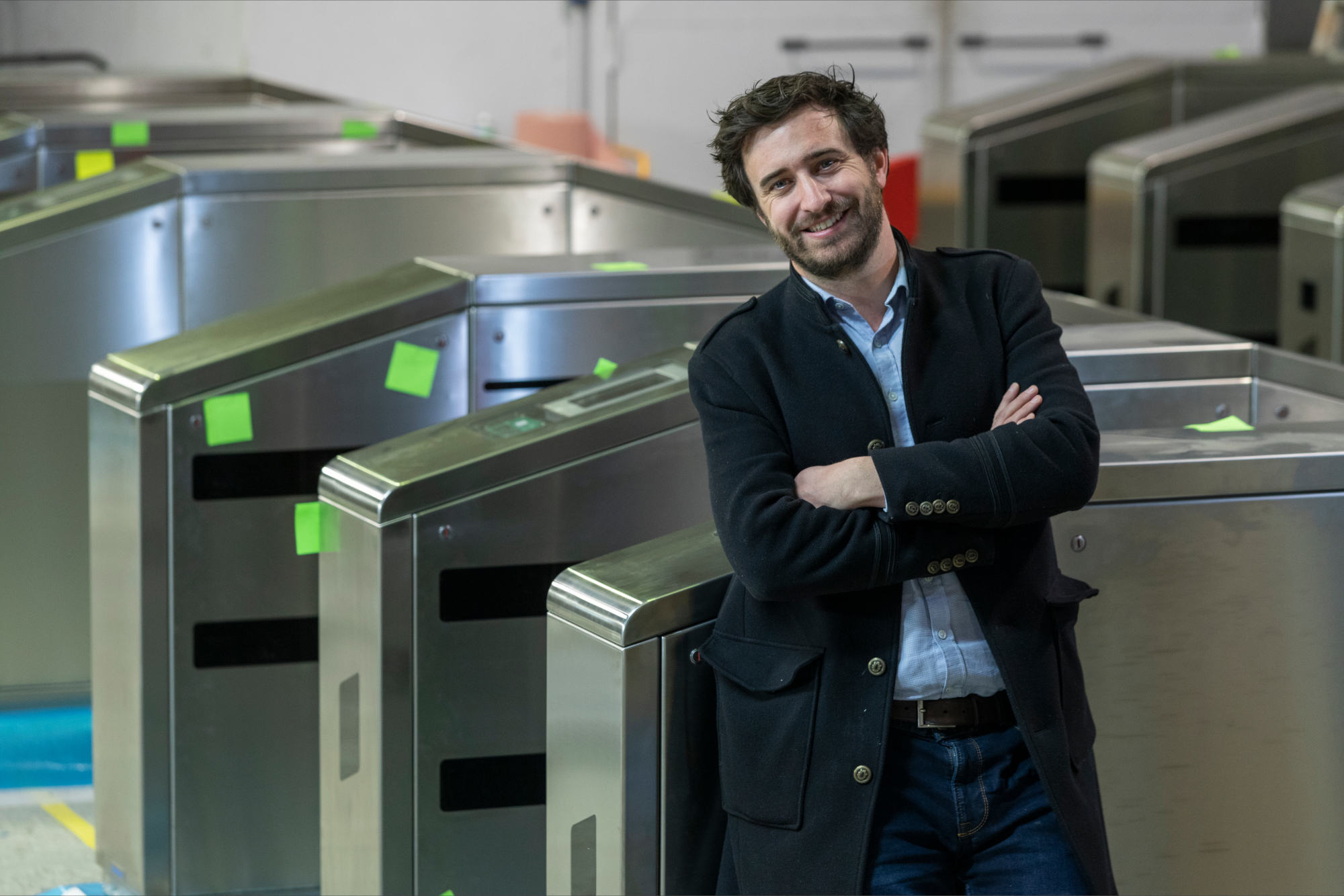
Deuxième étage de la fusée
Le process de réflexion mis en place dans l'entreprise fût à nouveau utilisé au moment de réfléchir à l'investissement dans une machine combinée de poinçonnage et découpe laser avec palettisation.
La première expérience réussie avec Prima Power, notamment pour la maintenance, a facilité l'arrivée d'une seconde machine du constructeur. Même si d'autres fabricants ont été consultés, Romain de Tellier reconnait que leurs chances de remporter ce nouveau marché étaient plus réduites : « Prima Power n'est cependant pas arrivé en terrain conquis. Et nous leur avons indiqué que la phase de réception classique s'accompagnerait d'une phase de test avec des pièces de notre conception, mariant poinçonnage, formage et taraudage dans notre atelier. Conditions supplémentaires, la programmation des pièces devait pouvoir se faire en automatique et nous avons enchaîné avec un cycle de 4 heures de production mélangeant l'usinage de tôles en acier et d'autres en inox. » Après la livraison et l'installation complète de la machine, la procédure a été lancée et tout le monde a quitté l'usine jusqu'au lendemain pour constater que tout avait parfaitement fonctionné.
De plus, la fiabilité affichée par le précédent combiné Prima Power acheté en 2001, et qui tournait encore au moment de la livraison de la nouvelle machine Combi Genius CG 1530 a été un atout supplémentaire pour le constructeur.
Ce changement de génération a été l'occasion de bénéficier de déplacements beaucoup plus rapides de la tôle, ce qui augmente la productivité, aussi bien en poinçonnage qu'en découpe laser (source 4 kW). Et le passage de la tourelle de 32 à 88 outils renforce l'autonomie de la cellule.
Le passage du poinçonnage hydraulique à l'électrique a également été la source de réduction des temps de réglage : « Lors d'un fraisurage, après la réalisation de la première pièce, nous vérifions que la profondeur est celle désirée et nous appliquons éventuellement le réglage nécessaire, sur la machine, mais sans toucher à l'outil » signale Romain de Tellier. Au-delà de cet avantage, le poinçonnage électrique d'une puissance de 30 tonnes, apporte un confort pour le niveau de bruit de l'atelier, simplifie la programmation et réduit les coûts de maintenance.
La possibilité de formage par le haut ou par le bas et l'apport du taraudage ont transformé les choses pour l'entreprise : « Nous avons un produit dont nous fabriquons, toutes références confondues, de 50.000 à 60.000 pièces par an. Le nombre de références fait qu'il n'est pas rentable de le faire sur une presse d'emboutissage. Chaque pièce comporte entre 6 et 8 inserts. Avec l'accord du client, nous avons transformé le process sur le combiné Prima Power : on a crevé, embouti, taraudé. Nous utilisons le fluotaraudage qui renforce la résistance mécanique. Et comme la pièce est pliée après usinage, il nous fallait le formage haut et bas. A l'arrivée, ce sont des opérations manuelles en moins qui apporte de la disponibilité pour faire des opérations plus forte valeur ajoutée » estime Romain de Tellier.
L'évacuation des pièces se fait soit par l'une des deux trappes (ouverture de 300 mm x 400 mm et 800 mm x 800 mm) reliées à un convoyeur, soit les ventouses qui alimentent 3 palettes qui accueillent chacune 3 emplacements. L'entreprise a d'ailleurs remporté un marché sur des petites pièces grâce à l'ouverture de trappe. Celle-ci complète en effet avantageusement le système de palettisation lorsque les pièces sont trop petites pour une préhension à la ventouse.
« Le combiné poinçonnage découpe laser est une machine avec un taux horaire élevé. Elle ne se prête donc pas à tous les produits et concerne les produits à forte valeur ajoutée. » précise Christophe Berquet. Sans compter les avantages économiques du poinçonnage sur des pièces très ajourées. Les deux technologies du combinée assurent le traitement des tôles jusqu'à 8 mm.
« La proposition commerciale chez Arc Industrie est : donner nous du volume, nous allons industrialiser et nous allons vous amener du prix et du service : design, stocks déportés, etc. » tranche Romain de Tellier qui apprécie de nouer des partenariats constructifs avec ses partenaires qu'ils soient clients ou fournisseurs.
Vous pouvez trouver ceci et d'autres histoires dans le dernier numéro de Power Line : notre magazine. Lisez-le ici.
Après la livraison et l'installation complète de la machine, la procédure a été lancée et tout le monde a quitté l'usine jusqu'au lendemain pour constater que tout avait parfaitement fonctionné.
Vous recherchez une solution similaire pour votre entreprise ? Trouvez-le ici
Platino Fiber
CORTE A LASER 2D
Rentável para uma mistura de produção que inclui todos os materiais e espessuras
Système de tri pour machines laser (LST)
MANUTENTION DES MATÉRIAUX
Un système de tri de feuilles automatisé, économique et performant pour les machines laser 2D
Combo Tower Laser
STOCKAGES
Le module clé pour automatiser le flux de matériaux avec les machines laser 2D
Combi Genius
MACHINES COMBINÉES DE POINÇONNAGE ET DE DÉCOUPE LASER