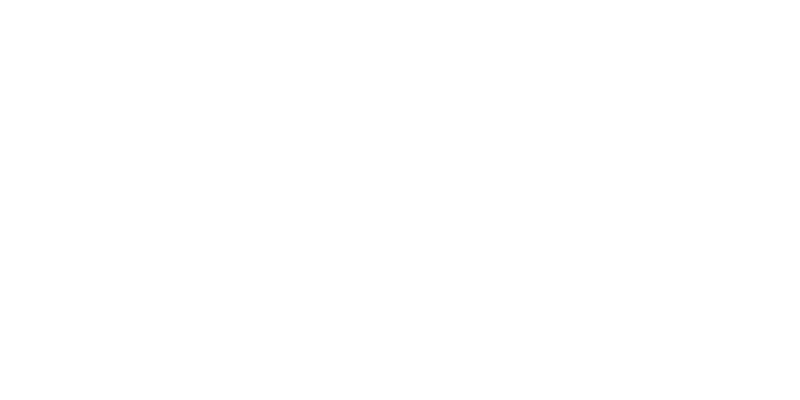
Clivet, puntare sul servo-elettrico per crescere
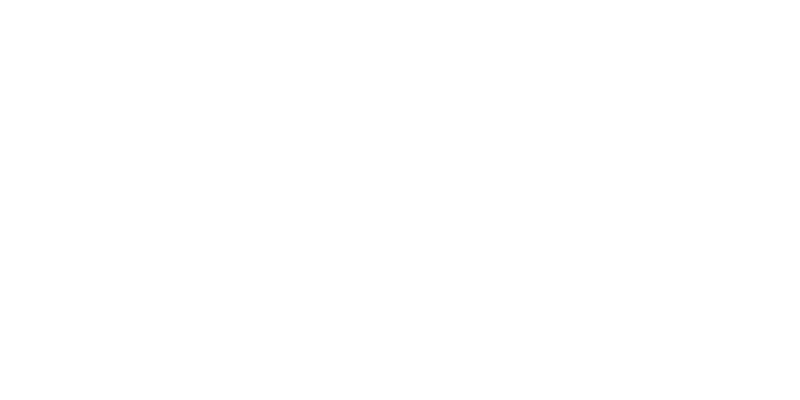
Tra i principali produttori di pompe di calore e chiller, Clivet ha scelto la tecnologia servo-elettrica Prima Power per rinnovare il proprio parco macchine dedicate alla lavorazione della lamiera con soluzioni ad elevata automazione e completamente integrate in ottica 4.0. Cuore del reparto è la linea PSBB che gestisce l’intero processo di lavorazione dei particolari con stazioni di punzonatura, cesoiatura, buffering e piegatura.
Entrare nello stabilimento Clivet di Feltre vuol dire non solo avere l’opportunità di scoprire le tecnologie che permettono all’azienda fondata nel 1989 da Bruno Bellò di essere tra i protagonisti nel settore della climatizzazione, ma anche immergersi nei valori di innovazione e sostenibilità che da anni caratterizzano la mission aziendale. Per un’evidente deformazione professionale, il nostro racconto si soffermerà solo sul reparto della lavorazione della lamiera, ma tutti i 50mila m2 dello stabilimento Clivet raccontano la loro profonda e radicata convinzione che un prodotto d’eccellenza per il comfort sostenibile e il benessere dell'individuo debba essere realizzato in un ambiente sostenibile, innovativo e salutare.
Prima di proseguire nel nostro reportage dallo stabilimento Clivet, è importante segnalare un altro elemento che emerge con la forza camminando in questo stabilimento: la continua crescita di un marchio che in trent’anni ha raggiunto un fatturato di oltre 250 milioni di euro e una riconosciuta leadership internazionale, confermata anche dall’alleanza industriale con il gruppo industriale MIDEA e dagli oltre 90 paesi raggiunti grazie alla qualità dei propri prodotti e delle proprie strategie produttive.
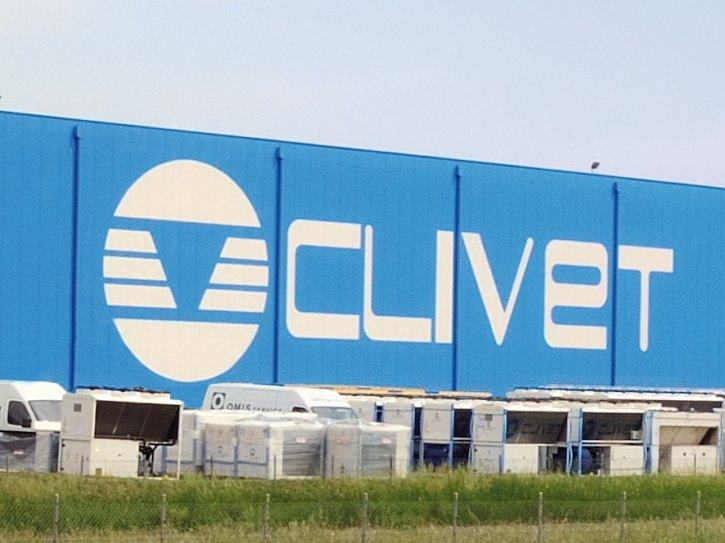
UN BALZO TECNOLOGICO IN AVANTI
Per Clivet questa crescita ha significato anche un progressivo ampliamento della propria gamma prodotti, affiancando alla produzione di chiller e pompe di calore anche sistemi specializzati basati su unità Roof-Top, sistemi ad anello d'acqua e sistemi dedicati al residenziale.
“In questo processo di crescita ci siamo anche resi conto che le macchine di cui eravamo dotati per la lavorazione della lamiera non erano più in grado di soddisfare le nostre esigenze produttive – ci spiega l’ing. Luca Martini, direttore industriale di Clivet, mentre ci accompagna nel nostro tour dello stabilimento - Si trattava di macchine con oltre 25 anni di servizio e quindi decisamente datate. La scelta a quel punto era semplice: o esternalizzare tutte le lavorazioni, oppure investire e dotarsi di nuove macchine più performanti. Abbiamo scelto la seconda opzione, anche per i vantaggi in termini di controllo della qualità del prodotto, delle tempistiche e di gestione delle priorità che derivano dall’avere internamente lavorazioni così importanti per i nostri prodotti. Il passo successivo è stato capire quale linea composta da punzonatrice e pannellatrice fosse più adatta per le nostre esigenze. Per farlo abbiamo messo a confronto vari brand e tecnologie e, dopo una serie di test, abbiamo visto come la soluzione Prima Power fosse in grado di processare per il 63% dei nostri codici senza necessità di spostare il pezzo su altre macchine. Abbiamo quindi deciso di iniziare la collaborazione con Prima Power installando in una prima fase solo la combinata punzonatrice – cesoia Shear Genius di Prima Power”.
L’introduzione della Shear Genius è stato il primo passo di Clivet nell’universo Prima Power, consapevoli che un salto tecnologico così importante avrebbe richiesto un periodo di adattamento anche per gli operatori e i tecnici.
“Siamo partiti con la combinata – prosegue Martini – perché una macchina come questa richiedeva una mentalità e un approccio completamente nuovo per noi e quindi abbiamo avuto bisogno di un po’ di tempo per adeguarci, cambiare testa e imparare ad usare al meglio una tecnologia così innovativa per la nostra realtà. Nel giro di un anno siamo andati completamente a regime e integrato completamente la Shear Genius nel nostro flusso di lavoro”.
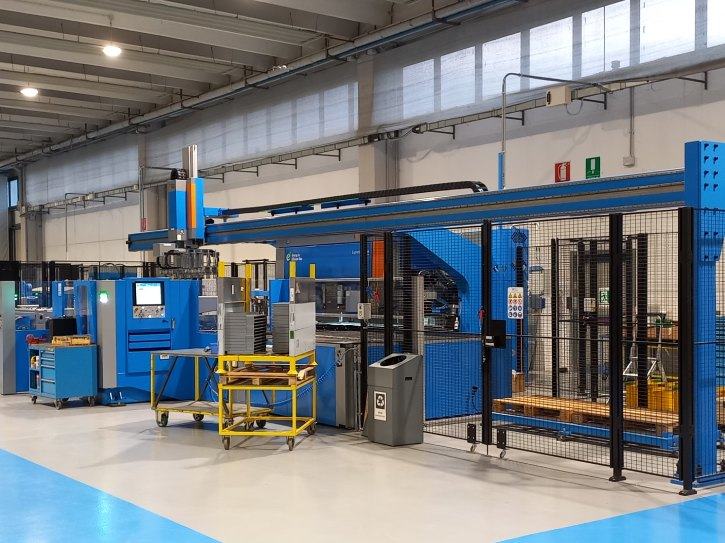
L’integrazione nel flusso produttivo rappresenta un altro tassello fondamentale della qualità ed efficienza di Clivet visto che lo stabilimento di Feltre è, a tutti gli effetti, un’Industria 4.0 al suo meglio.
“Per me integrarsi nel flusso produttivo vuol dire che si parte dall’ordine di lavoro e si arriva fino al versamento del pezzo finito senza che sia necessario nessun intervento che non sia la lettura ottica: qui ogni pezzo è etichettato fin dal foglio di lamiera con programmi e informazioni per ogni lavorazione successiva (taglio, piegatura, verniciatura, destinazione finale nel processo produttivo) che sono sempre contenuti in questa label per garantire tracciabilità, automazione e interconnessione tra sistema di gestione, macchine e linee di assemblaggio”.
In questo modo Clivet è riuscita a garantire autonomia produttiva alla macchina, riuscendo a farla lavorare circa tre turni quotidiani.
“Fino a qualche anno fa il grosso della nostra produzione era su commessa, le macchine industriali ad elevata personalizzazione, e su lotti piccoli, quello che indentifichiamo come applied e light commercial cioè macchine con potenze grandi ed intermedie. Ora entrando con forza nel settore delle pompe di calore abbiamo anche produzioni con grandi volumi: una “mass production”, considerando che con il nuovo stabilimento puntiamo a raggiungere le 100.000 pompe di calore prodotte”.
Queste nuove esigenze produttive hanno significato un nuovo investimento e un ammodernamento delle tecnologie.
“Con questi volumi una pannellatrice era un’opzione molto interessante, anche perché ci avrebbe permesso di essere meno dipendenti dai nostri fornitori esterni avendo il controllo totale sulla qualità del prodotto. Ci siamo rivolti a Prima Power per proseguire in questo percorso e la Shear Genius è stata trasformata in una linea PSBB (Punching, Shearing, Buffering, Bending), con l’aggiunta di una pannellatrice EBe 2720. La pannellatrice non lavora solamente in linea, ma può essere anche caricata dall’esterno grazie a un vagone aggiuntivo per pezzi che devono essere solamente piegati”.
La linea PSBB di Prima Power è infatti una soluzione ad elevata flessibilità in grado di trasformare automaticamente le lamiere grezze in componenti già piegati e di alta qualità. PSBB è, come detto, l’acronimo di Punching + Shearing + Buffering + Bending, ovvero punzonatura, cesoiatura, buffering e piegatura con tutte le lavorazioni eseguite con tecnologia servoelettrica.
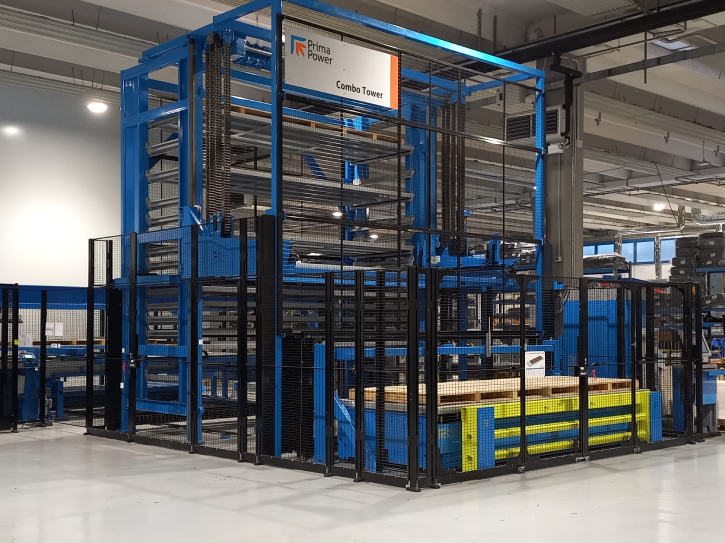
QUANDO UNA LINEA NON BASTA PIÙ
“L’introduzione della linea PSBB di Prima Power ha risposto alle nostre esigenze e quindi abbiamo deciso di fare un ulteriore passo per colmare una lacuna che avevamo: mi riferisco alla lavorazione di lamiere con spessori più elevati e, soprattutto, di fogli da 4 metri di lunghezza. Abbiamo scelto quindi di dotarci di una combinata punzonatrice laser perché avevamo la necessità di essere sia produttivi sia flessibili, grazie a queste macchine che permettono di eseguire lavorazioni laser e deformazioni. Abbiamo installato una combinata punzonatrice e laser Prima Power Combi Laser 1540 con magazzino automatico Combo Tower che ci permettesse di rispondere queste esigenze”.
Clivet nei suoi prodotti impiega infatti molta lamiera sia per componenti strutturali sia per quelli così detti estetici.
"Proprio perché gestiamo così tanti codici la combinata è la macchina più adatta alle nostre esigenze – prosegue Martini – per esempio con il laser possiamo realizzare bordi arrotondati come da richieste di nostri clienti, mentre la deformazione ci permette di risparmiare spessori garantendo comunque quell’irrobustimento della lamiera che evita vibrazioni fastidiose”.
Grazie a questi investimenti Clivet punta a diventare completamente indipendente per quanto riguarda la lavorazione della lamiera.
“Stiamo crescendo di più del 30% ogni anno e quindi continuiamo ancora ad avere bisogno dei fornitori esterni per rispondere alle nostre esigenze. Parallelamente stiamo completando il passaggio dei vecchi codici in nuovi programmi da realizzare sulla nuova linea, parliamo di 20-30mila codici ed è quindi un lavoro che richiede tempo per essere completato. Il nostro obiettivo non è però smettere di avere fornitori esterni, ma poter affiancare alla nostra capacità produttiva un supporto esterno per gestire picchi di lavoro o emergenze”.
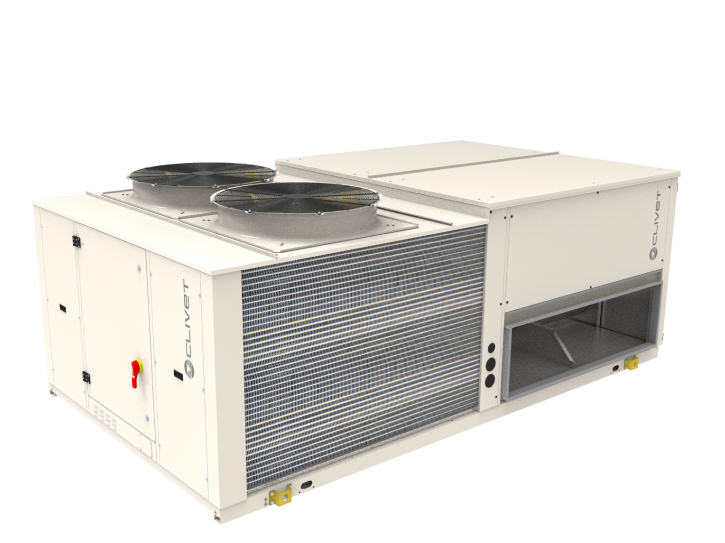
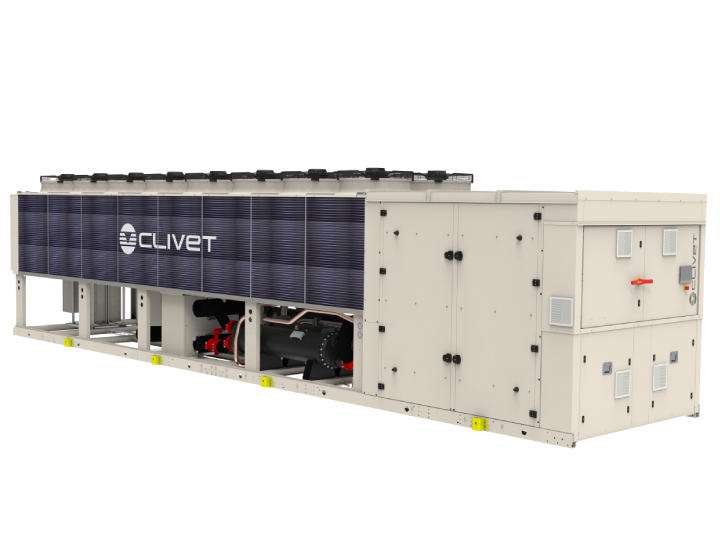
UN FUTURO SEMPRE PIÙ AUTOMATIZZATO
L’investimento nella linea PSBB e nella Combi Laser racconta anche l’importanza dell’automazione per Clivet che, anche nel nuovo sito produttivo da 30 mila m2, gestirà questi crescenti volumi produttivi con soluzioni ad elevata automazione e robotizzazione. Nella Combi Genius, ad esempio, è stata prevista la presenza del robot LSR (acronimo di “Loading and Stacking Robot”) per caricare e scaricare i pezzi in modo da evitare l’intervento manuale e per aumentare l'affidabilità del processo di prelievo dei pezzi tagliati al laser. Il robot di carico, scarico e impilamento LSR è un robot di movimentazione di materiali e pezzi per macchine combinate laser-punzonatura. LSR carica le lamiere sulla macchina e impila i pezzi finiti sui pallet di impilamento garantendo un funzionamento accurato ed efficiente del processo per la movimentazione dei materiali. Da sottolineare come la pinza robotica abbia diverse aree di aspirazione, ognuna delle quali può essere controllata separatamente. Grazie al sistema di movimento servoazionato dell'impilamento, il sistema assicura la massima precisione. Per aumentare l'affidabilità del processo di prelievo dei pezzi tagliati al laser, Prima Power ha sviluppato inoltre la tecnologia RALC (Robot Assisted Last Cut). Durante l'ultimo tratto di taglio, la macchina e il robot faranno movimenti simultanei e sincronizzati degli assi assicurando un prelievo sicuro e affidabile dei pezzi.
Anche la dotazione di un magazzino automatico dedicato è stata quasi obbligata per Clivet che, ormai da qualche anno, si propone di rendere autonomi i suoi impianti grazie a magazzini automatizzati che garantiscano un’alimentazione costante nelle 24 ore. Combo Tower è infatti una soluzione di stoccaggio flessibile destinata ad automatizzare il flusso di materiale visto che rende disponibili diversi materiali non appena necessari in modo automatico e senza ritardi, fungendo da buffer o deposito intermedio per componenti finiti.
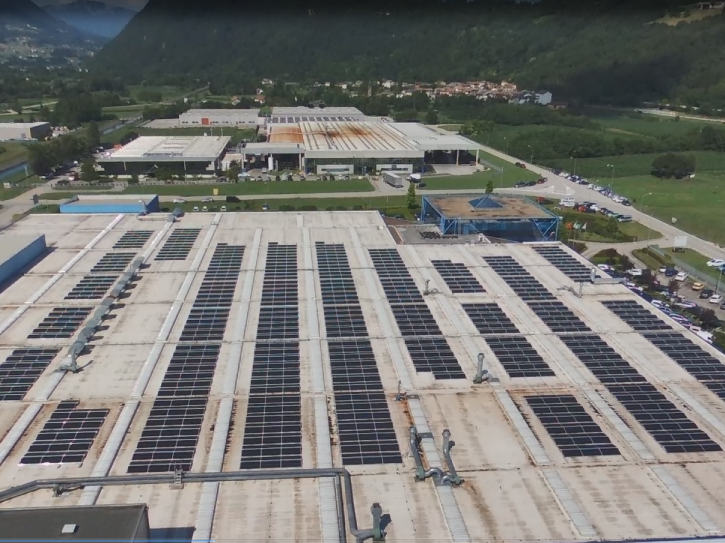
SCEGLIERE LA SOSTENIBILITÀ, SCEGLIERE IL SERVO-ELETTRICO
Clivet ha scelto di puntare sulla tecnologia servo-elettrica che caratterizza le macchine Prima Power come parte integrante della sua strategia produttiva all’insegna della sostenibilità ambientale.
“Le macchine servo-elettriche sono perfette per la nostra visione produttiva perché utilizzano potenza ed energia solo quando serve e solo nella quantità necessaria, senza sprechi. Per questo motivo siamo convinti sia la macchina con cui si risparmia più energia e questo per noi è molto importante. Clivet si è posta infatti un obiettivo green: raggiungere la carbon neutrality nei prossimi tre-quattro anni e la tecnologia Prima Power è un alleato fondamentale per vincere questa sfida”.
Proprio per questo motivo Clivet ha completato il suo parco macchine con tre presso piegatrici servo-elettriche Prima Power: due eP 1030 da 3 m e una eP 2040 da 4 m. Importante sottolineare come l’intero stabilimento di Feltre sia stato già rinnovato profondamente in questa direzione con l’installazione di luci led, sistemi di climatizzazione con pompe di calore e un impianto fotovoltaico che ora vale 1,2 MW, ma che sarà raddoppiato a marzo 2023.
Clivet si è posta un obiettivo green: raggiungere la carbon neutrality nei prossimi tre-quattro anni e la tecnologia Prima Power è un alleato fondamentale per vincere questa sfida.