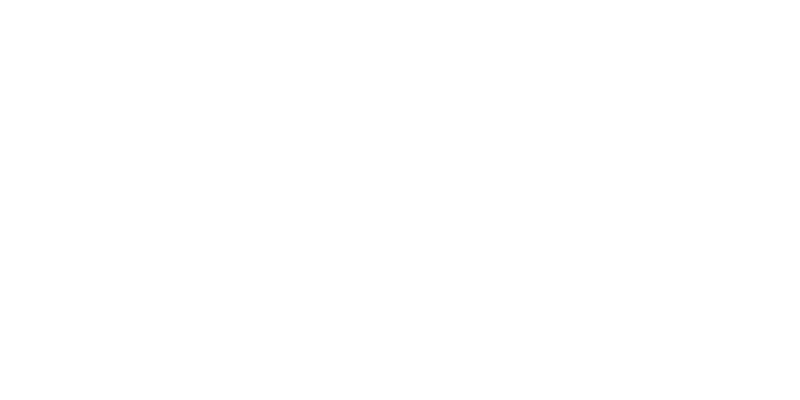
Clivet, going servo-electric for growth
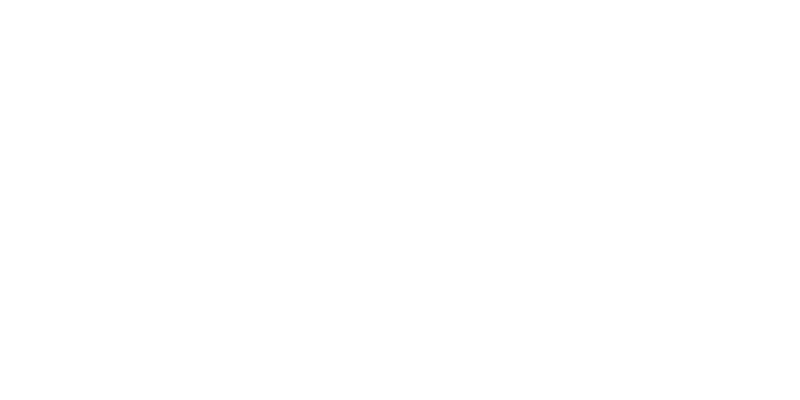
As one of the largest producers of heat pumps and chillers, Clivet has chosen Prima Power’s servo-electric technology to modernise its sheet metal processing plant with highly automated solutions that are fully Industry 4.0 integrated. The PSBB line represents the heart of the department, managing the entire production process with stations for punching, shearing, buffering and bending.
Formed in 1989 by Bruno Bellò, Clivet is one of the biggest players in the air conditioning sector. Walking into its factory in Feltre not only means having the opportunity to discover the technologies that have made the business what it is today, but also experience the values of innovation and sustainability that for years have defined the company’s mission. Since we are clearly formed by our profession, our story focuses on the sheet metal processing department. However, all 50,000m2 of Clivet’s factory tell of their deep-rooted conviction that a product of excellence providing sustainable comfort and well-being for the individual should be created in an environment that is sustainable, innovative and promotes wellness.
Before continuing with our piece on the Clivet factory, it is important to point out something else that comes through strongly when walking through this factory: the continuous growth of a brand that over 30 years has achieved turnover of over 250 million euros and has been recognised as a leader in the sector. This is also confirmed by its partnership with the MIDEA group and the 90+ countries it has reached through the quality of its products and strategies.
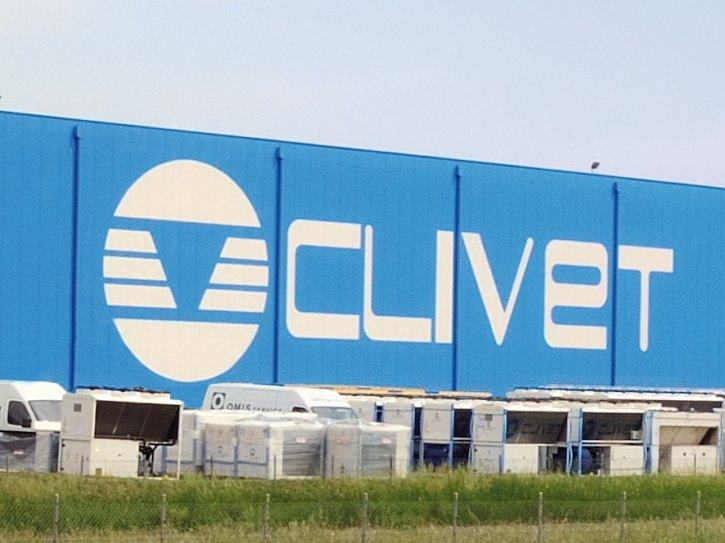
A TECHNOLOGICAL LEAP FORWARD
For Clivet this growth has also meant progressive expansion of its product range, adding specialised systems based on Roof-Top units, ring water systems and systems designed for residential use alongside its chillers and heat pumps.
“During this growth process we also realised that our sheet machining systems were no longer able to meet our needs,” explains Luca Martini, Clivet’s Industrial Director, while he takes us on a tour of the factory. “The machinery had been in service for over 25 years and was decidedly outdated. The decision at that point was a simple one: we either had to outsource machining, or invest in new, better performing machinery. We chose the second option, also because of the benefits of product quality control, timing and priority management that come with being able to perform such important processes internally. The next step was understanding which line consisting of a punch and panel bender was best suited to our needs. We compared various brands and technologies, and after a series of trials, we saw that the Prima Power solution was able to manufacture 63% of our product items without moving the part to other machines. We therefore chose to start working with Prima Power, at first installing only the punching-shearing combined machine known as Shear Genius by Prima Power.”
Shear Genius was Clivet’s first step into the world of Prima Power, knowing that a technological leap of such magnitude would require a period of adjustment both for operators and technicians. “We started with the combined solution” continues Martini, “because a machine like that required a completely new approach and mentality; we needed some time to adapt, change our mindset and learn how to best use such innovative technology for our business. Within a year, we were up to optimum production capacity and the Shear Genius was fully integrated into our workflow.”
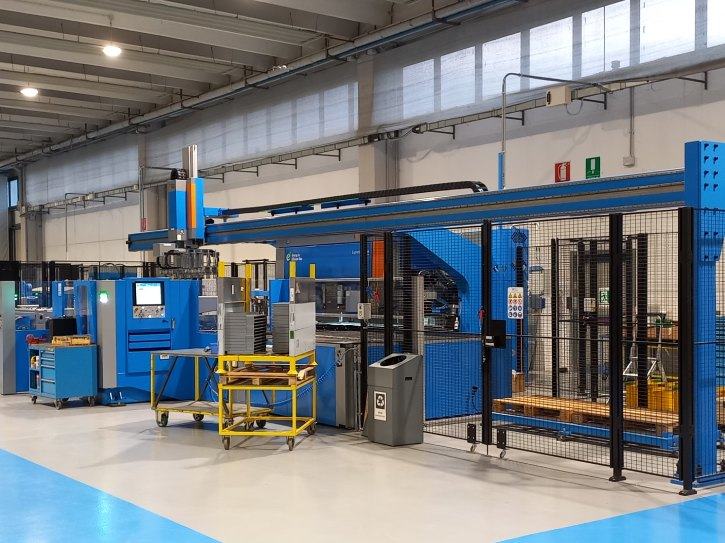
“Until a few years ago, most of what we produced was made to order. We manufactured small quantities of highly customised industrial machines, what we call applied and light commercial, i.e. machines with large and intermediate power. Now, since making significant inroads into the heat pump market, we are also looking at mass production, considering that with our new factory we have a production target of 100,000 heat pumps. These new production requirements have meant a new investment and modernisation of our technologies. A panel bender was a very interesting option for such volumes, also because it would have allowed us to be less dependent on our external suppliers and have total control over product quality. We therefore turned to Prima Power, and the Shear Genius was transformed into a PSBB (Punching, Shearing, Buffering, Bending) line, with the addition of an EBe 2720 panel bender. The panel bender not only works in line, but can also be loaded externally thanks to an additional wagon for parts that only need to be bent”.
Prima Power’s PSBB line is in fact a highly flexible solution capable of automatically transforming rough sheet metal into high quality, already bent components. As mentioned, PSBB is the acronym for Punching + Shearing + Buffering + Bending, with all processes being performed using servo-electric technology.
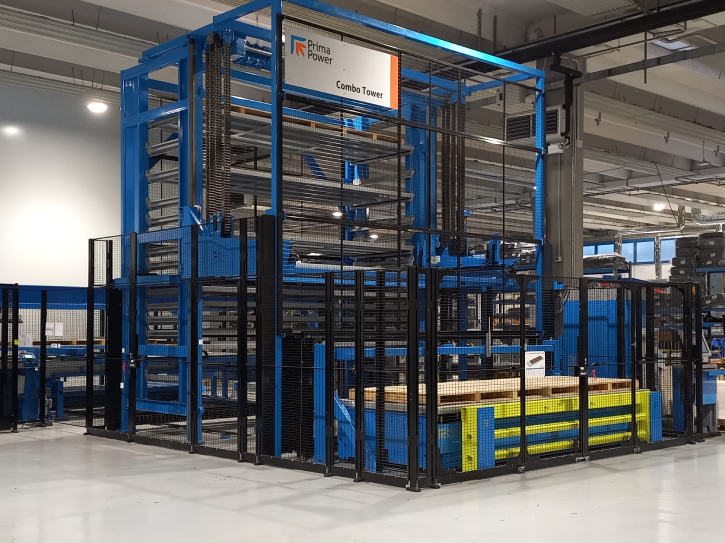
WHEN ONE LINE IS NOT ENOUGH
“The introduction of Prima Power’s PSBB line met our needs, so we decided to take it a further step to fill a gap we had: processing of thicker sheets and, especially, sheets measuring 4 metres in length. We chose a combined laser punching machine because we needed to be both productive and flexible, thanks to these machines that allow us to perform laser machining and forming. We installed the Prima Power Combi Laser 1540 combined punch and laser, with Combo Tower automatic storage that would allow us to meet these needs”.
Clivet uses a lot of sheet metal in its products both for structural and so-called aesthetic components.
"Because of the fact that we manage so many parts, the combined machine is the most suited for our needs,” continues Martini. “For example, with the laser we can create rounded edges as per our customers' requests, while the deformation allows us to save on thickness while still guaranteeing a certain strength of sheet metal which prevents annoying vibrations”.
Thanks to these investments, Clivet aims to become completely independent when it comes to sheet metal processing. “We are growing by more than 30% per year and as such we still continue to need the help of external suppliers to meet our needs. At the same time, we are completing the move of our old item codes into new programs to be created on the new line – we are talking about 20,000 to 30,000 item codes and it will therefore take some time to complete. Our goal is not to stop using external suppliers, but to be able to combine our production capacity with external support to manage work peaks or emergencies.”
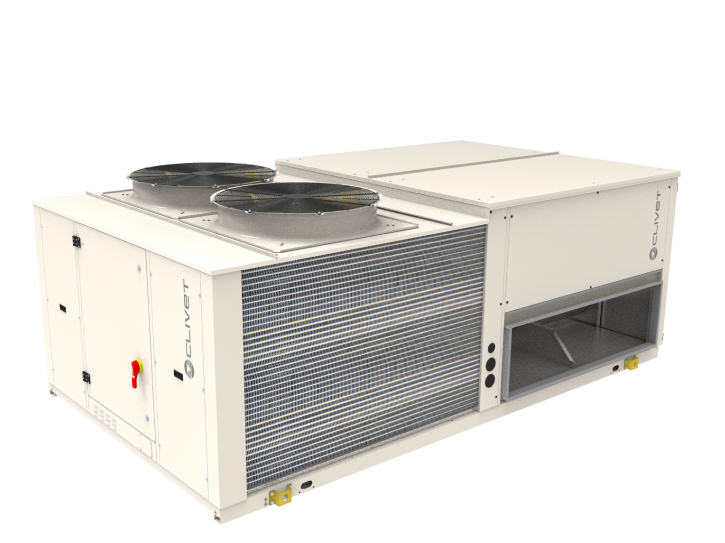
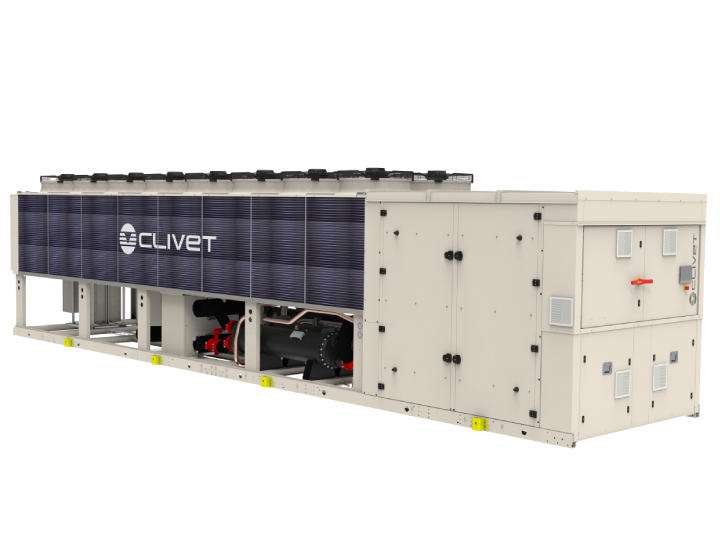
AN INCREASINGLY AUTOMATED FUTURE
The investment in the PSBB line and in the Combi Laser also demonstrates the importance of automation for Clivet which, in its new 30,000m2 factory, will manage increased volumes with highly automated and robotic solutions. The Combi Genius, for example, has been designed to include a LSR (acronym for "Loading and Stacking Robot") for loading and unloading parts in order to avoid manual intervention and increase the reliability of the picking process of laser cut parts. The LSR loading, unloading and stacking robot is a material and part handling robot for combined laser-punching machines. The LSR loads the sheets onto the machine and stacks the finished parts on the stacking pallets ensuring accurate and efficient operation of the material handling process. It should be emphasised that the robotic clamp has different suction areas, each of which can be separately controlled. Thanks to the servo-driven stacking movement system, it ensures maximum precision. To increase the reliability of picking the laser cut parts, Prima Power has also developed RALC (Robot Assisted Last Cut) technology. During the last section of cutting, the machine and the robot make simultaneous and synchronised axes movements, ensuring safe and reliable picking of parts.
A dedicated automatic warehouse was almost obligatory for Clivet which, for some years now, has been working to make its systems autonomous thanks to automated storage that guarantees a constant supply over 24 hours. Combo Tower is in fact a flexible storage solution intended to automate the material flow as it automatically makes different materials available as soon as they are needed with no delays, acting as a buffer or intermediate storage for finished components.
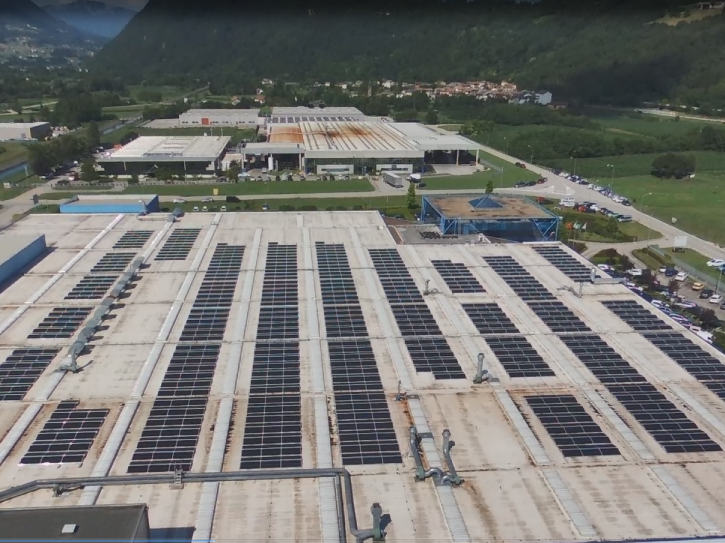
CHOOSE SUSTAINABILITY, CHOOSE SERVO-ELECTRIC
To support environmental sustainability, Clivet has chosen to focus on the servo-electric technology that is a key feature of Prima Power machines as an integral part of its production strategy.
“Servo-electric machines perfectly fit our vision when it comes to production because they only use power and energy when needed and only in the required amounts, without waste. For this reason, we are convinced that it is the machine that will save the most energy and this is very important to us. In fact, Clivet has set itself a green goal: to be carbon neutral in the next three to four years and Prima Power technology is a fundamental ally in meeting this aim”
That is why Clivet has completed its fleet of machines using three Prima Power servo-electric press brakes: two three-metre eP 1030s and one four-metre eP 2040. It is important to highlight how the entire Feltre plant has already been significantly sustainably refurbished, with the installation of LED lights, air conditioning systems using heat pumps and a 1.2 MW photovoltaic system, which will soon double in capacity.
Clivet has set itself a green goal: to achieve carbon neutrality in the next three to four years and Prima Power technology is a fundamental ally in overcoming this challenge.