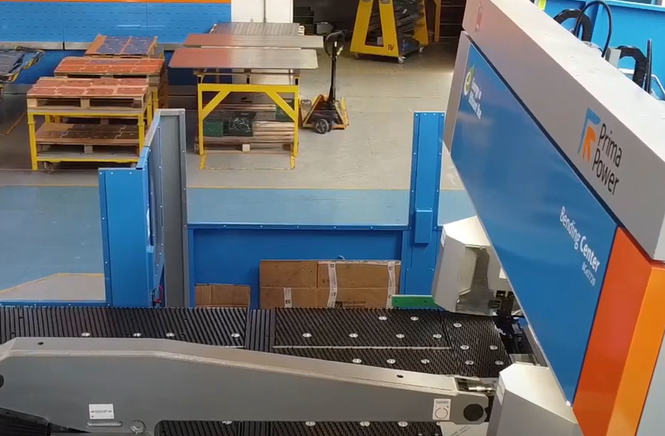
Resteghini - Crecer juntos a través de la innovación
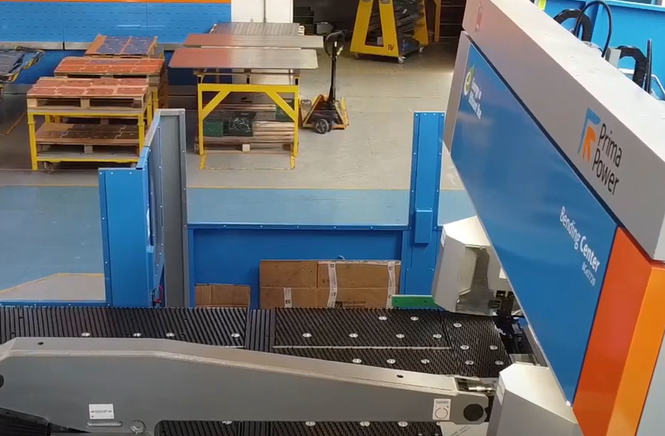
Desde la introducción de la tecnología láser, una de las primeras máquinas Platino comercializadas por Prima Power, hasta el reciente desafío de la paneladora automática BCe 2720: la colaboración entre el contratista milanés Resteghini y Prima Power es uno de los elementos fundamentales del éxito de esta empresa, ahora en su cuarta generación, capaz de completar su evolución en una perspectiva 4.0 y de continuar su proceso de desarrollo e innovación.
A menudo se dice, y con razón, que los números no bastan para describir una colaboración entre dos empresas. En el caso de Resteghini, una empresa con sede en Corsico (cerca de Milán) y especializada en metalurgia ligera civil e industrial de precisión con casi setenta años de historia, sin embargo, algunos números tienen tal valor simbólico que son excelentes puntos de partida para conocer mejor esta realidad. Empecemos por el número cuatro, como las generaciones de la familia Resteghini que se han involucrado en esta aventura empresarial. «Todo empezó en 1955 de la mano de mi abuelo Bruno», explica Sergio Resteghini, hoy propietario de la empresa junto con su hermana Claudia, «quien, en un pequeño espacio del centro de Milán, comenzó a soldar y a dar acabado a productos metálicos destinados a las industrias alimentaria, telefónica y de equipos eléctricos. La transformación tecnológica y el crecimiento fueron muy rápidos, baste decir que en pocos años pasamos de un carro tirado por caballos que entregaba chapas ya plegados a máquinas de corte y plegado, primero manuales y después mecánicas». Valter, el hijo de Bruno, se involucró de inmediato en la empresa, y en poco tiempo su esposa Virginia también empezó a trabajar con ellos, mientras Resteghini crecía, llegando a Corsico en 1974 con su propia nave, más grande. «Obviamente, yo también empecé a estar presente en el taller muy pronto, primero durante el verano aprendiendo los distintos procesos, y después a partir de 1984 incorporándome a la empresa de forma continuada. Al cabo de unos años, mi hermana Claudia también empezó a trabajar con nosotros». Fueron años de gran dinamismo para Resteghini, que amplió cada vez más su gama de mecanizados, convirtiéndose en proveedor de cuadros, atriles y armarios para equipos eléctricos, e innovando cada vez más su parque de máquinas. «Para nuestra familia, el objetivo siempre ha sido innovar un aspecto de la empresa cada año: somos subcontratistas y para nosotros invertir es esencial para ser competitivos en el mercado.
Por ello, Resteghini evoluciona continuamente, pero lo hace de forma gradual y sin sobresaltos». Gradualidad, por tanto, pero también visión empresarial y pasión, elementos que llevan a la empresa milanesa a anticiparse a todos los avances tecnológicos con grandes inversiones, entre las que destaca el sistema de corte por láser.
PIONEROS DEL LÁSER
Para describir este punto de inflexión en la historia de la empresa podemos utilizar otra cifra: 2, el número de serie del láser Platino que Prima Power, entonces Prima Industrie, instaló en Resteghini en enero de 1996. «Cuando instalamos la primera máquina de corte por láser, nos decidimos por Prima Power. Ese fue un momento importante para ambas empresas; se trataba de la primera máquina modelo Platino que comercializaron y la llegada del láser cambió radicalmente la forma de trabajar la chapa. Esta colaboración ha contribuido de forma importante a mejorar el rendimiento del láser de Prima Power, mientras que por nuestra parte ha supuesto un crecimiento constante que nos ha llevado a introducir nuevas tecnologías. Por ejemplo, el aumento del número de piezas cortadas gracias a la alta productividad de los láseres nos ha llevado a invertir en nuevas plegadoras para evitar un cuello de botella en la producción».
El plural referido a los láseres anticipa las elecciones realizadas por Resteghini en materia de inversiones: en resumen, el primer sistema Platino de 1,5 kW con mesa fija fue sustituido por una máquina de 2,5 kW con mesa doble, para llegar después a un láser Platino de 3 kW, también de Prima Power, con una torre de almacenamiento de 10 cajones capaz de alimentar la máquina sin supervisión.
«Todo este proceso», confirmó Sergio Resteghini, «se ha llevado a cabo junto con Prima Power, que nos ha apoyado con su experiencia tecnológica, y siguiendo un fuerte impulso de mi padre, que siempre fue previsor cuando se trataba de innovación. Baste decir que sentía una gran pasión por la informática y la programación, lo que le permitió crear programas que aún utilizamos hoy en día con las obvias actualizaciones». En 2015, Resteghini dio otro importante paso adelante al optar por equiparse con un almacén automático desatendido Night Train, la solución de almacenamiento de Prima Power que permitió la gestión de la materia prima y el servicio de dos máquinas de corte en un único proceso flexible y que Resteghini instaló en la versión con más de 100 cajones.
Además de las ventajas de automatizar los procesos de corte, el Night Train también fue decisivo para superar otro problema crítico de la empresa milanesa: la falta de espacio. De hecho, la planta de Prima Power de desarrollo vertical puede manipular una gran cantidad de chapas con un espacio relativamente pequeño. «Ahora disponemos de dos máquinas de corte por láser Platino, una con tecnología de fibra y otra con fuente láser de CO2 con campos de trabajo de 1500x3000 mm capaces de cortar chapas de acero dulce de hasta 20 mm, acero inoxidable de hasta 15 mm, así como diversas aleaciones como aluminio, latón, titanio y cobre. Gracias a las tecnologías Prima Power, podemos garantizar la flexibilidad, la rapidez y la trazabilidad de la fase de corte, respondiendo a cualquier necesidad urgente de nuestros clientes sin comprometer la eficacia de todo el departamento». Completa el departamento de corte una máquina automática de lijado y acabado, capaz de realizar operaciones de acabado.
DIGITALIZAR PARA CRECER
Otra cifra clave para conocer Resteghini y que caracteriza su enfoque del mercado sigue siendo el 4, o, mejor dicho, el 4.0. «Hacemos lo que consideramos realmente útil para la empresa y nuestros clientes, sin seguir tendencias ni con el único objetivo de recibir incentivos estatales», explicó Sergio Resteghini, «e incluso en el caso de la Industria 4.0 hemos actuado de acuerdo con este enfoque. Después de todo, Resteghini era 4.0 incluso antes de que se acuñara este término, de hecho, adoptamos un software de gestión desde 2016 y lo hicimos porque estábamos convencidos de que aportaría beneficios a todos los aspectos de nuestro negocio». Lo que para muchos talleres mecánicos y de carpintería resultó una época difícil y a menudo dolorosa, para Resteghini constituyó una evolución natural. «Sin duda fue un paso importante, pero habíamos llegado a un punto en el que sin un software de gestión no habríamos podido gestionar el volumen de artículos, materiales y códigos que teníamos en producción. Hoy en día, el software de gestión es una parte tan integral de nuestra forma de trabajar y producir que me pregunto cómo trabajábamos sin él». Además de estar conectado con las plantas más importantes, el software de gestión adoptado por Resteghini permite registrar todos los tiempos de ciclo mediante códigos de barras y tener una visibilidad y trazabilidad completas sobre cualquier actividad o producto que se esté procesando. La entrada de la cuarta generación, formada por Samuele Resteghini, ingeniero mecánico, y Simone Bandini, científico de datos, también ha supuesto un paso más en el desarrollo 4.0.
«Hoy en día», explican los dos jóvenes técnicos, «somos cada vez más eficaces en todos los aspectos de la producción; hemos desarrollado sistemas de alerta para mejorar la puntualidad de la entrega de las piezas mecanizadas y la supervisión en tiempo real de todos los procesos de producción. Además, analizamos los datos recopilados de forma estructurada en tres direcciones: calidad documental, inteligencia empresarial con cuadros de mando que apoyan las decisiones empresariales estratégicas y, por último, en términos de ciencia de datos, es decir, procesos de análisis de datos de forma automatizada y optimizada».
EL RETO DE LA PANELADORA
El último número que elegimos en nuestro viaje al mundo de Resteghini es el 2023. Nos referimos al año en el que se instaló la paneladora Prima Power BCe 2720, la primera máquina de este tipo para la empresa milanesa. «Estoy seguro de que la introducción de la paneladora, una máquina que siempre me ha fascinado, supondrá otro salto de calidad para nosotros gracias a Prima Power. En estos primeros meses de uso ya estamos apreciando las ventajas de lo que considero un nuevo mundo en comparación con el plegado tradicional: hay muchas ventajas, tanto en términos de productividad como de calidad. Por ejemplo, podemos producir lotes incluso de series limitadas, con una repetibilidad muy alta gracias al control angular que garantiza que la pieza producida tenga siempre las características requeridas. Esto es fundamental tanto en lotes pequeños como en piezas muy grandes, porque significa ser eficiente sin desperdiciar materiales y minimizando los tiempos de inactividad».
La paneladora BCe 2720 de Prima Power es una máquina altamente automatizada: una vez preparado el programa, el proceso de plegado es muy rápido y no requiere un operario altamente cualificado para garantizar la máxima repetibilidad de la pieza. «La tecnología servoeléctrica de Prima Power, junto con el control de ángulo,proporciona la garantía de que, incluso la primera parte, se ejecuta correctamente sin sorpresas. Además, una paneladora manipula del mismo modo una pieza pequeña que una mucho mayor: esta consideración puede parecer trivial, pero resulta sorprendente cuando pensamos en lo que supone plegar un cuadrado de 400x400 mm de forma tradicional frente a una chapa de 2500x1000 mm, tanto en términos de configuración automática de la máquina como del número de operarios necesarios. t
Podemos aprovechar la digitalización del proceso, que también nos permite trabajar de forma más segura y ergonómica. Aparte de eso, la mesa de carga y descarga LUT permite cargar la siguiente pieza en tiempo enmascarado mientras la paneladora procesa la pieza. Esto significa que los operarios no tienen siempre la pieza en las manos, como ocurre con una plegadora tradicional, y pueden realizar otros procesos mientras la máquina está ocupada, como insertar un espárrago, con grandes ventajas en términos de optimización del proceso». En cuanto a las especificaciones técnicas, la BCe 2720 tiene una longitud máxima de plegado de 2,75 m, puede procesar chapas de hasta 2,85x1,5 m, con una altura máxima de plegado de 204 mm y una curvatura máxima de retracción de 55 mm.
FLEXIBILIDAD Y CALIDAD, LOS SECRETOS DEL ÉXITO
Resteghini es hoy un subcontratista puro, capaz de procesar materiales de todo tipo y tamaño, incluso para lotes pequeños, y de atender a diferentes sectores: desde el ferroviario hasta el médico, pasando por el alimentario y el de la iluminación. Además de la gran atención prestada a la innovación tecnológica, otro elemento que caracteriza a Resteghini es sin duda la decisión de dotarse de un departamento técnico interno capaz de apoyar al cliente incluso en la creación de un prototipo o la ingeniería de una pieza. «De este modo, ofrecemos un servicio apreciado por el mercado», confirmó Sergio Resteghini, el propietario, «pero también somos capaces de maximizar la eficacia de nuestras tecnologías de producción. El requisito previo es, obviamente, que el cliente esté dispuesto a colaborar, pero observamos que cada vez con más frecuencia las grandes empresas son especialmente receptivas a ello. Parecería más difícil colaborar eficazmente cuando el cliente no tiene las competencias mínimas en materia de chapistería, pero es precisamente en estos casos en los que, gracias a nuestra experiencia y al apoyo que ofrecemos, conseguimos fidelizar a nuestros clientes con relaciones duraderas en el tiempo».
Como empresa certificada ISO 9001, UNI EN 3834 y UNI EN 15085 (CL1) para la soldadura en el sector ferroviario, Resteghini ofrece a sus clientes una amplia gama de procesamiento gracias a un parque de máquinas que incluye, además de las máquinas láser Platino y la paneladora BCe 2720 de Prima Power, también punzonadoras, plegadoras y un departamento especializado en acabado de superficies y soldadura con cuatro estaciones TIG MIG para soldar acero dulce, acero inoxidable y aluminio.
Todo este proceso se ha llevado a cabo junto con Prima Power, que nos ha apoyado con su experiencia tecnológica
Are you looking for a similar solution for your company? Find it here
Centro de panelado BCe
PANELADORAS
Paneladora semiautomática que combina flexibilidad y productividad
Platino Fiber
CORTE A LASER 2D
Rentável para uma mistura de produção que inclui todos os materiais e espessuras
Night Train FMS®
SISTEMAS DE MANUFACTURA FLEXIBLE