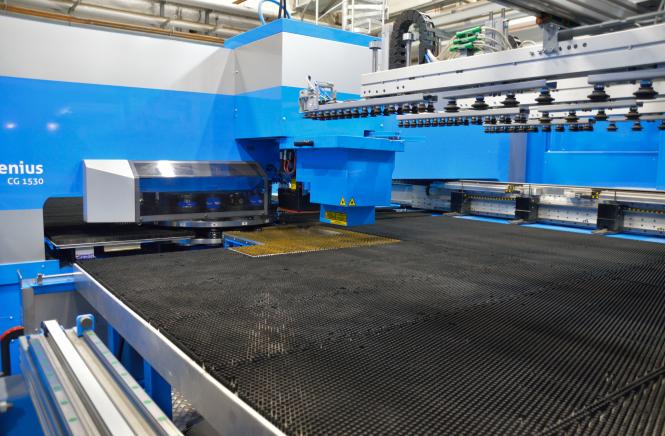
Ajustement futur avec la poinçonneuse laser
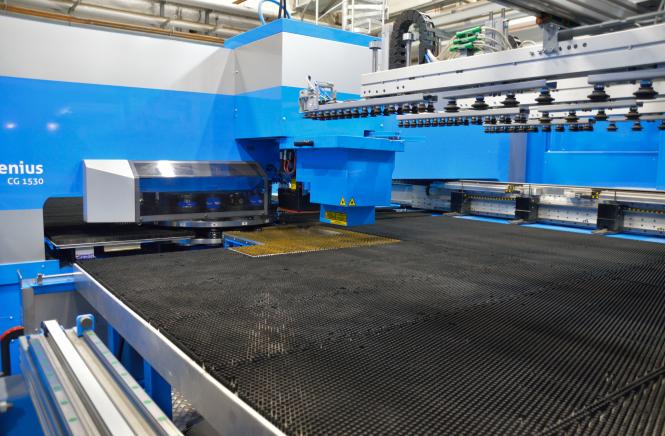
Eisenwerk Wittigsthal GmbH investit dans un système poinçon-laser afin d'être prêt pour l'avenir numérique.
« Nous sommes davantage un fabricant de produits sur mesure qu'un producteur de série », déclare Jochen Browa, directeur général et, avec son épouse, propriétaire d'Eisenwerk Wittigsthal GmbH à Johanngeorgenstadt dans la région d'Erzgebirge. L'entreprise, qui se concentre sur les systèmes de quincaillerie pour les installations de bâtiments, traite de toute façon beaucoup de tôles. Il était donc logique de se lancer dans la fabrication en sous-traitance de tôles. À cette fin, Eisenwerk Wittigsthal a investi l'année dernière dans un système de poinçonnage-laser Combi Genius de Prima Power.
Le nom d'Eisenwerk Wittigsthal est peut-être familier aux habitants de l'Allemagne de l'Est, non seulement parce que l'entreprise existe depuis 366 ans, mais aussi parce qu'elle était le plus grand fournisseur de chaudières à eau en émail chauffées au bois dans les années 1980. Dans l'ex-Allemagne de l'Est, tous ceux qui voulaient prendre un bain chaud comptaient sur ces chaudières. À certains moments, jusqu'à 250 000 chaudières ont été produites chaque année et plus de 4 millions d'unités ont été vendues au total. Peu avant la chute du mur de Berlin, l'usine de Johanngeorgenstadt s'était préparée à produire des composants pour la minicar Trabant de l’Allemagne de l’Est - mais rien ne s’est réalisé.
Après la réunification allemande, les commandes ont chuté de façon spectaculaire et l'entreprise a dû attendre 1992 pour être complètement restructurée et réorientée, après son rachat par l'entrepreneur Winfried Friedrich. Eisenwerk Wittigsthal s'est développé pour devenir un fournisseur de solutions de systèmes de construction pré-assemblés, avec pour activité principale les systèmes de mesure, de distribution et de contrôle. Ces systèmes de mesure et distributeurs sont installés dans des armoires en tôle montées en surface ou encastrées. Lorsque Winfried Friedrich a pris sa retraite en 2008, Jochen Browa et son épouse ont repris l'entreprise. Ils ont renforcé leurs activités dans le secteur de la ventilation, ont développé la fabrication en sous-traitance dans le secteur de la tôlerie et ont fait de l'entreprise une société qui emploie aujourd'hui 60 personnes et génère un chiffre d'affaires d'environ 10 millions d'euros par an.
Automatisation ancienne et nouvelle
Pendant notre visite, Jochen Browa nous a montré la surface de 55.000m2 . Notre premier arrêt a été l'installation de production des chaudières à eau chauffées au bois, qui est automatisée avec la technologie de l'époque. Une ou deux fois par an, les presses et la ligne d'émaillage sont mises en marche pendant environ sept semaines pour produire les 3 000 à 4 000 chaudières à eau, qui sont encore demandées aujourd'hui. Après tout, 10 % du chiffre d'affaires de l'entreprise provient de ce secteur - une part minime mais néanmoins significative, puisque 75 % du chiffre d'affaires provient du matériel des systèmes de construction. Le reste du chiffre d'affaires est partagé entre les techniques de ventilation et la fabrication en sous-traitance de tôles.
Solutions spéciales et production en série
« Nous avons environ 5 000 articles sur notre liste de prix », dit Jochen Browa en souriant, « cependant, les clients commandent souvent 5 000 composants qui n'y figurent pas. Nos clients apprécient vraiment le fait que nous leur fournissions des solutions sur mesure ».
Les adaptations comprennent aussi bien des adaptations purement géométriques de solutions standard du catalogue que des conceptions entièrement nouvelles. C'est la preuve de la compétence professionnelle que l'on trouve dans l'entreprise, qui est également utilisée dans sa fabrication en sous-traitance.
« Nous faisons de la fabrication en sous-traitance depuis longtemps, mais à une échelle plutôt réduite. Notre équipement nous limitait à des quantités moyennes », explique Jochen Browa. Un système de poinçon-grignotage des années 1990 fabriqué par Finn Power et une combinaison poinçon-laser relativement récente de Boschert, sans automatisation, ont été utilisés à cette fin. Cependant, les presses dont ils disposent déjà sont également utilisées pour les commandes du secteur de la ventilation, soit 400 000 à 500 000 unités fabriquées par an.
Objectif à long terme : Industrie 4.0
Jochen Browa voit un potentiel d'expansion dans la fabrication en sous-traitance de grandes séries et de pièces communes. « Pour cela, cependant, nous avons besoin d'une solution flexible et automatisée qui soit également compatible avec l'industrie 4.0 » L'idée de Jochen Browa est une application de configuration, qu'un client peut utiliser pour concevoir sa propre unité sur son smartphone, en envoyant la commande directement à la machine. Il estime toutefois qu'il faudra encore dix ans pour mettre en œuvre le projet. D'une part, la mise en œuvre implique des coûts énormes pour une entreprise de taille moyenne et, d'autre part, ses « clients proviennent d'un secteur plutôt conservateur et ne sautent pas sur tous les trains qui passent ».
Toutefois, la feuille de route est désormais établie et Eisenwerk Wittigsthal GmbH a investi environ 2 millions d'euros l'année dernière pour atteindre cet objectif. L'un de ces investissements est le système poinçon-laser entièrement automatisé de Prima Power. « Dans un premier temps, nous n'avons acheté que le système poinçon-laser, puis les interfaces avec le magasin et la plieuse ont suivi. » La ligne de pliage poinçon-laser entièrement automatisée sera mise en œuvre dès que les produits seront disponibles.
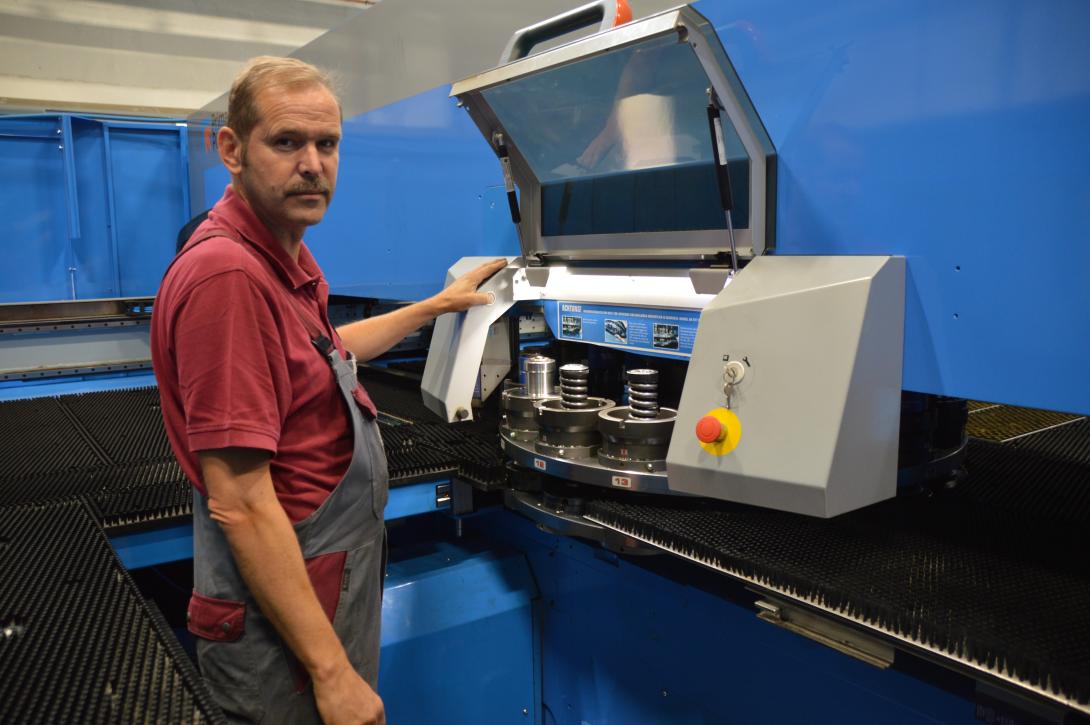
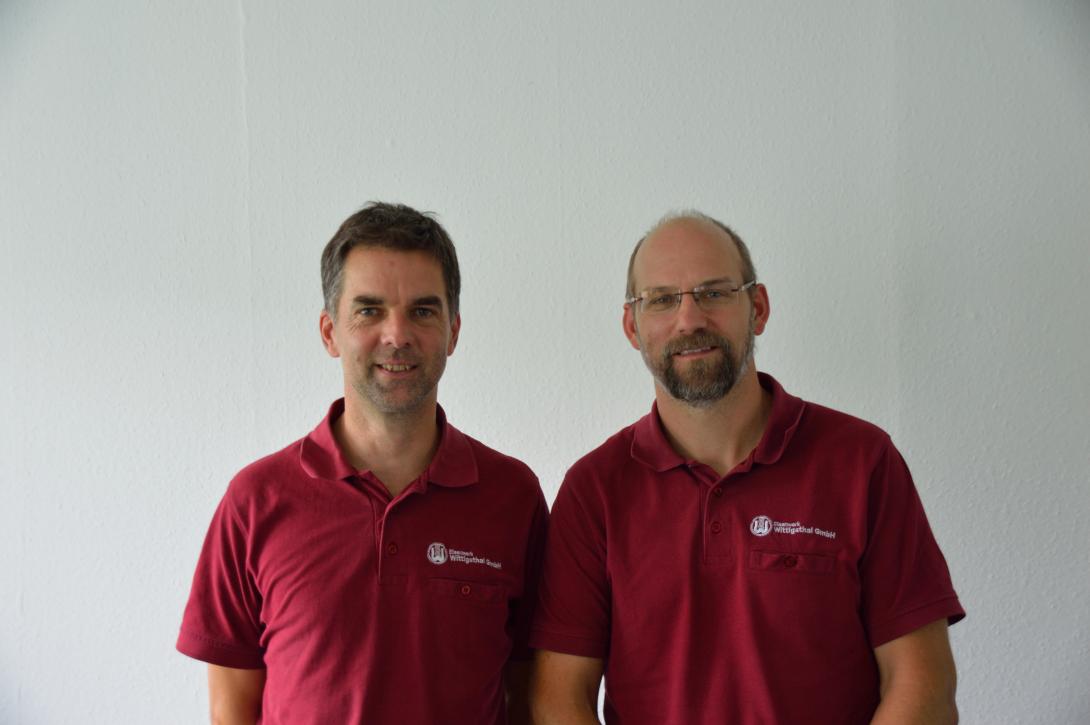
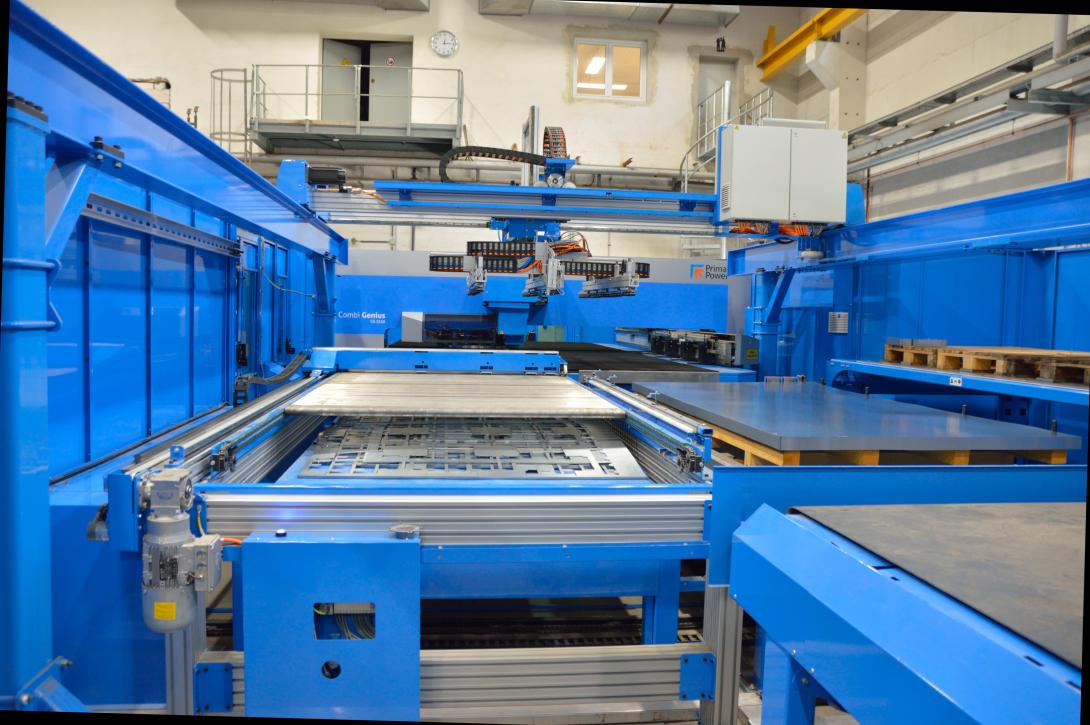
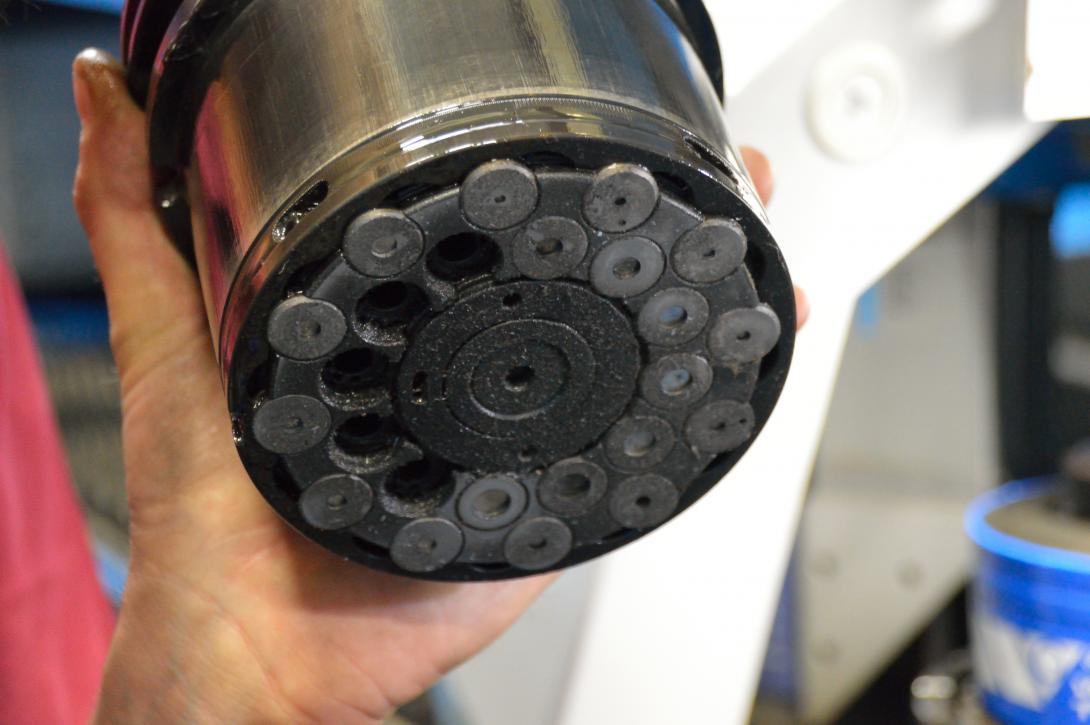
Des années de bonne expérience
La nouvelle centrale prévue est également le résultat de nombreuses années de partenariat avec Finn-Power, qui fait désormais partie du groupe Prima Power. « Nous travaillons avec une poinçonneuse-grignoteuse de Finn-Power depuis plus de 20 ans. C'est pour cette raison que nous avons pris contact avec Prima Power. Nous étions satisfaits du système et, après 23 ans de fonctionnement, nous avons même pu le revendre en état de production, » déclare Jochen Browa. Bien entendu, ils ont obtenu plusieurs devis avant de prendre la décision d'investir, et le prix a également joué un rôle. « Mais finalement, après deux visites chez Prima Power en Finlande, j'étais sûr que l'automatisation fonctionnerait comme prévu. »
Le système maintenant installé est une machine Combi Genius, un système combiné poinçon-laser dont la manipulation est entièrement automatisée.
« Un système combiné poinçon-laser convient le mieux à notre produit, qui comprend le formage, le gaufrage et le filetage et souvent de nombreux trous dans les composants », explique Robert Wiegand, responsable de la production chez Eisenwerk Wittigsthal.
« Dans le secteur de la ventilation, par exemple, nous avons aussi des pièces à plusieurs trous pour lesquelles nous utilisons parfois des outils à neuf trous - des outils qui perforent neuf trous à la fois. Dans cette application, même le système laser 2D le plus rapide ne peut pas suivre. » Afin d'utiliser le système de manière optimale, Robert Wiegand propose une ligne directrice simple : Les trous et les contours intérieurs sont poinçonnés, les contours extérieurs sont découpés à l'aide du système laser.
Système polyvalent de combinaison poinçon-laser
Le système Combi Genius de Wittigsthal utilise une tourelle d'outils de poinçonnage avec 16 positions d'indexation et une tête laser comprenant un système laser à fibre de 3kW. Tous les axes sont entraînés par des servomoteurs et contrôlés par le CPC. Le poste de poinçonnage de la machine est équipé d'un vérin intelligent comprenant un axe de poussée rotatif pour des changements d'outil rapide.
Au total, jusqu'à 384 outils simples ou 128 outils rotatifs peuvent être stockés dans la tourelle. « À cette fin, nous pouvons continuer à utiliser tous les outils de l'ancien système, y compris les coûteux outils de gaufrage », explique Robert Wiegand. Des outils spéciaux supplémentaires ainsi que des multi-outils sont fournis. On peut utiliser aussi bien les anciens multi-outils que les multi-outils rotatifs. Une force de 300 kN est disponible pour le poinçonnage. Il est possible de former des bourrelets, des ouïes et des formes similaires jusqu'à une hauteur de 15 mm.
Comme c'est la norme dans les systèmes poinçon-laser, la tôle est maintenue par des pinces pendant le traitement et déplacée sur des tables à brosses. Les têtes de poinçonnage et de découpe laser restent dans leur position fixe. Les tables à brosses sont conçues pour les tôles d'un poids de 250 kg. Des segments de brosses commandés par programme, situés devant et à l'intérieur de la tourelle de l'outil de perforation, assurent une protection supplémentaire de la surface de la tôle. Trois pinces maintiennent la feuille, et un CPC ajuste la position en fonction de la séquence de travail, de sorte qu'une utilisation optimale de la feuille est possible sans repositionnement.
Laser à fibre rapide et nécessitant peu d'entretien
Le système laser utilisé est un système à résonateur CF de 3 kW fabriqué par Prima Power. La tête de coupe optimisée, le collimateur, le guidage du faisceau et les paramètres de coupe assurent une qualité et une vitesse de coupe élevées. Divers dispositifs simplifient l'utilisation du système laser. Il s'agit notamment du verre de protection de l'objectif LPW, qui empêche la poussière de coupe et la saleté de se déposer sur l'objectif, et du moniteur plasma laser LPM, qui suit le processus de coupe et redémarre automatiquement le système si nécessaire. En outre, un capteur surveille l'objectif et sa qualité.
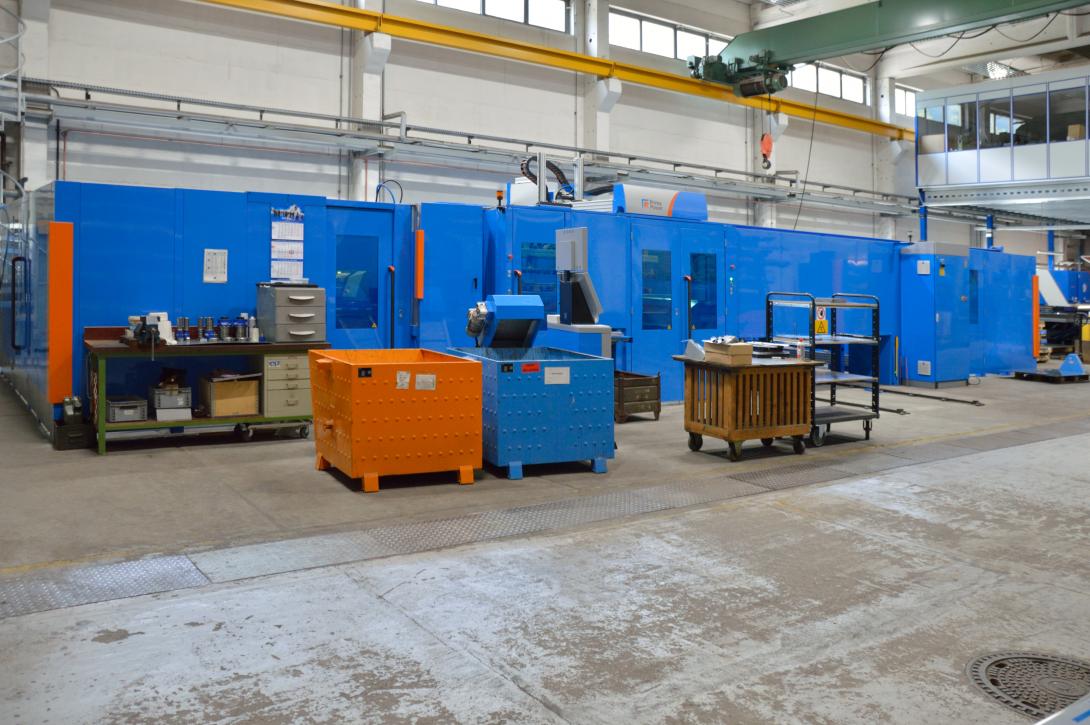
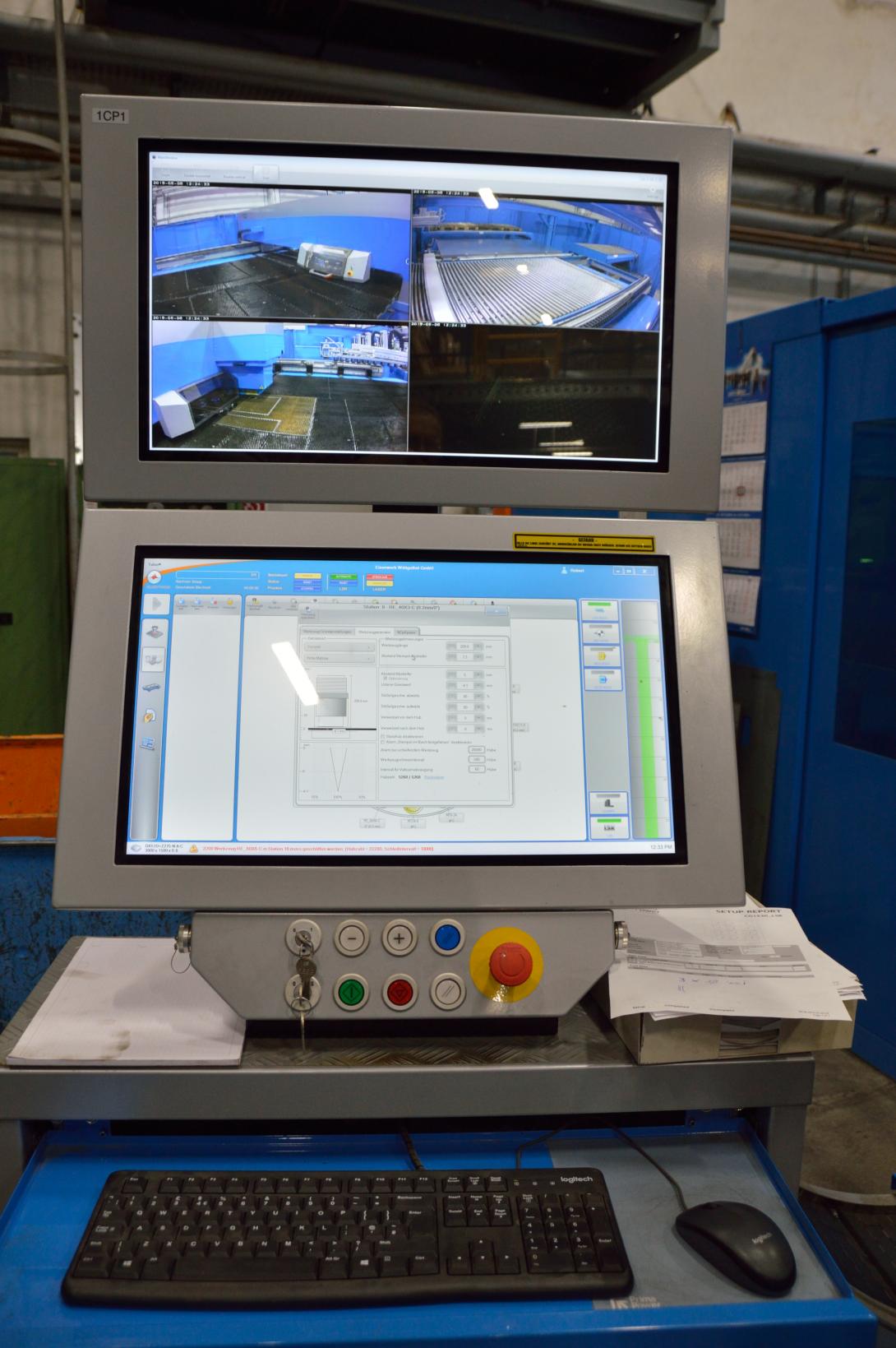
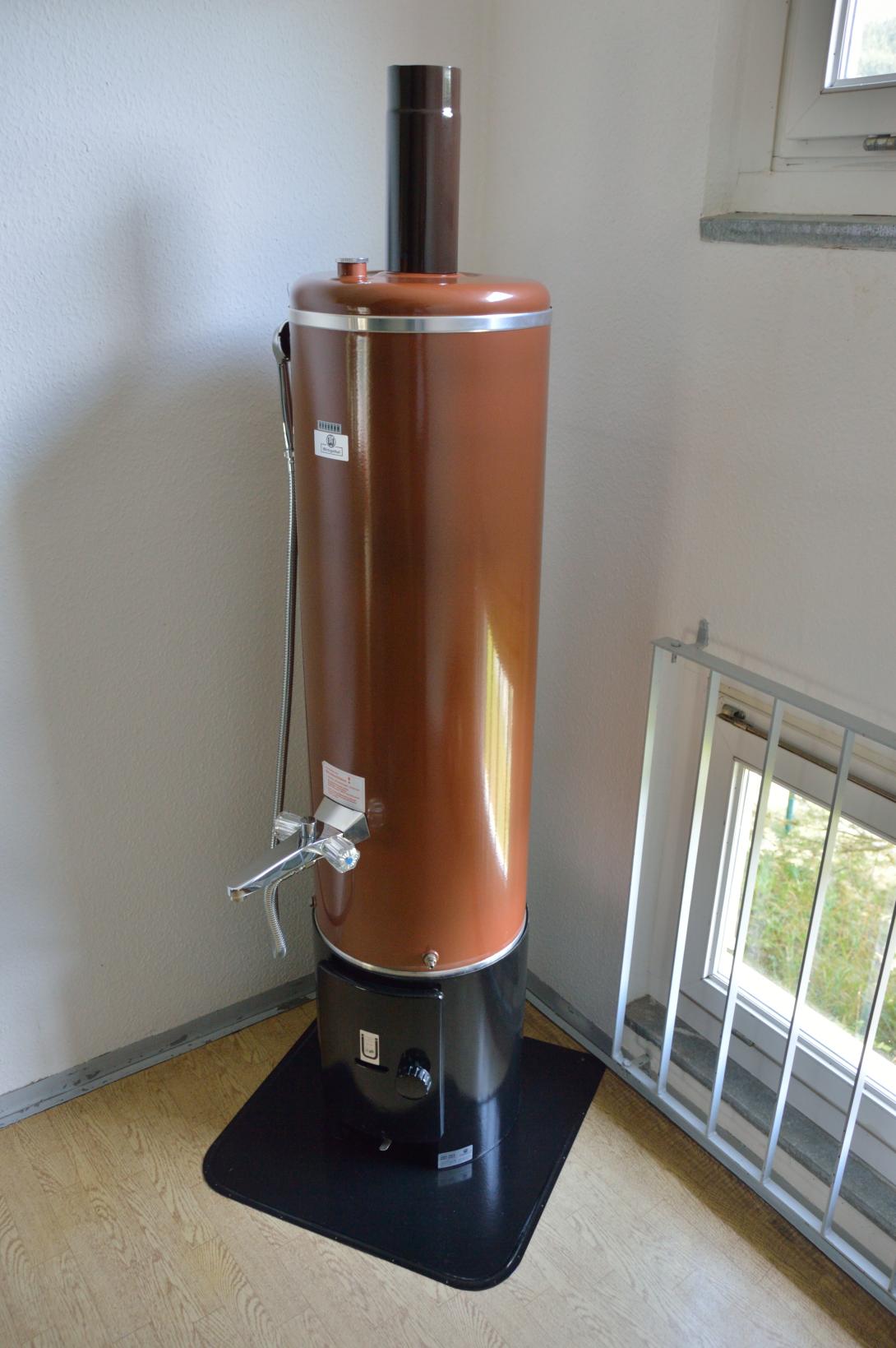
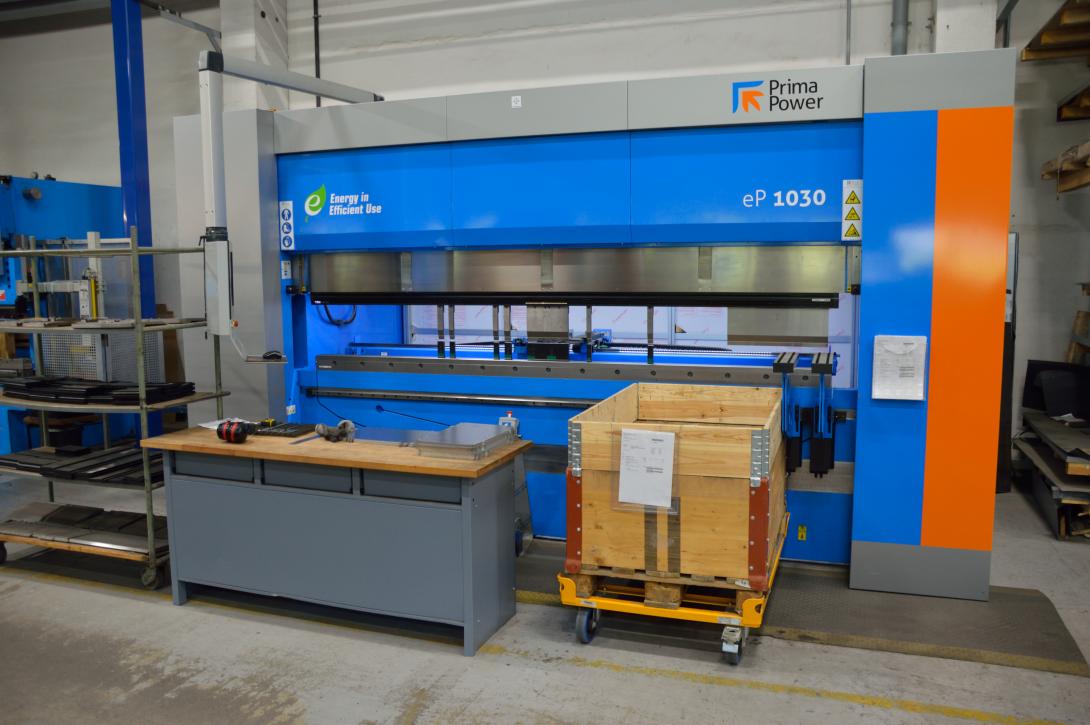
Système de chargement et de déchargement
Les pièces découpées sont déchargées par une trappe à pièces de 500 mm x 500 mm. Pour les pièces laser, il existe deux trappes de 300 mm x 400 mm pour un tri rapide, et de 800 mm x 800 mm pour les plus gros composants. La plupart des pièces, cependant, sont chargées et déchargées par un robot cartésien doté d'un système très flexible de poutres d'aspiration.
Les paquets de feuilles sont amenés dans la zone de travail de la machine pendant le temps de production. Ensuite, le robot cartésien se charge entièrement du chargement et du déchargement. Il prend les feuilles l'une après l'autre, les aligne et les déplace vers la table de l'unité de perforation-laser. Parallèlement au chargement, la grille de feuilles restante est retirée de la zone de travail et déposée sous la pile de feuilles brutes.
En mode découpe, le robot cartésien retire les composants finis directement après la dernière découpe et les empile à des coordonnées prédéfinies. Deux tables sont disponibles pour être empilées. En théorie, la machine pourrait également être chargée manuellement de feuilles d'une longueur maximale de 5 mètres.
« Nous avons également été convaincus par la simplicité d'utilisation du système », déclare Robert Wiegand. « Cela s'applique aussi bien à l'opération directe sur la machine qu'à la programmation. On s'habitue assez rapidement au système, même sans beaucoup de connaissances de base. Si vous connaissez les principes du poinçonnage-grignotage, de la découpe laser et les bases de la CAO, c'est étonnamment simple malgré la complexité du système. »
Le système Combi Genius est commandé par un panneau de commande à écran tactile. L'opérateur peut vérifier à la fois les réglages de la machine et les listes de travaux. Quatre caméras contrôlent l'intérieur du système et surveillent le processus de la machine. L'opérateur a une vue claire de la tourelle d'outils avec tous les outils utilisés, ainsi que des réglages de la tête laser. Un système de gestion des outils est également disponible, qui, par exemple, enregistre le nombre de courses effectuées et affiche les instructions d'entretien pertinentes.
Le système d'exploitation et le système de programmation NC Express e3 fonctionnent ensemble de manière transparente. Vous pouvez soit utiliser un lecteur de codes-barres pour saisir les ordres de travail créés par le NC Express e3 dans la liste des travaux, soit le chargeur de tâches les sélectionne automatiquement dans la base de données et les insère dans la liste des travaux avec toutes les informations complémentaires requises, telles que le programme NC, l'outil ou le matériau.
« Nous avions envisagé d'utiliser un système de programmation nous permettant de programmer toutes les machines », se souvient Jochen Browa, « cependant, nous avons décidé d'utiliser le système Prima Power en raison de la fiabilité de ses timings. »
Robert Wiegand ajoute qu'il est sans cesse étonné de voir avec quelle précision les temps calculés lors de la programmation correspondent au temps de production réel sur la machine, même pour des pièces complexes. « C'est d'une importance capitale pour la production en grande série, où souvent un centime ou des fractions de centime font la différence. » Et comme c'est précisément pour ces cas-là qu'un fonctionnement automatique stable est vital, il ajoute : « La machine fonctionne principalement de manière automatique, sans intervention. Si les programmes CN sont correctement configurés et testés, la machine peut fonctionner jusqu'à épuisement de la pile de feuilles dans la machine sans avoir à faire beaucoup de contrôles. »
Le fait que le système Combi Genius puisse également être utilisé via un smartphone est une autre indication que Eisenwerk Wittigsthal GmbH s'oriente vers la fabrication numérisée et l'industrie 4.0. Jochen Browa envisage sans aucun doute l'extension de la ligne de pliage par poinçon et laser, entièrement interconnectée.
Nous avons environ 5 000 articles sur notre liste de prix, cependant, les clients commandent souvent 5 000 composants qui n'y figurent pas. Nos clients apprécient vraiment le fait que nous leur fournissions des solutions sur mesure
Vous recherchez une solution similaire pour votre entreprise ? Trouvez-le ici
Combi Genius
MACHINES COMBINÉES DE POINÇONNAGE ET DE DÉCOUPE LASER