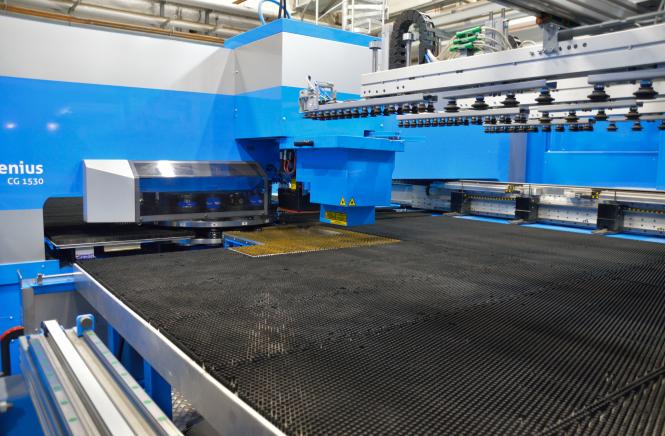
Соответствие требованиям будущего с комбинированным станком для пробивки и лазерной резки
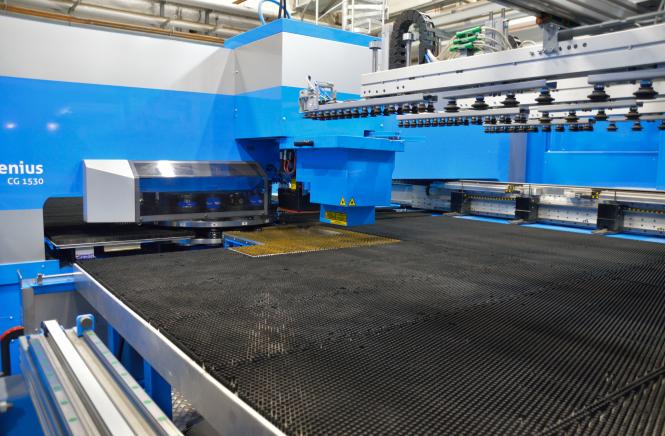
Компания Eisenwerk Wittigsthal GmbH вкладывает средства в комбинированную систему для пробивки и лазерной резки, чтобы быть готовой к цифровому будущему.
«Мы в большей степени занимаемся изготовлением специальной продукции по индивидуальным заказам, чем серийным производством», – сказал Йохен Брова, генеральный директор и совладелец (совместно со своей женой) компании Eisenwerk Wittigsthal GmbH в г. Йоханнгеоргенштадт, расположенном в регионе Эрцгебирге (Рудные горы). Компания, которая специализируется в изготовлении системного оборудования для зданий и сооружений, так или иначе занимается обработкой листового металла в больших масштабах, поэтому переход на контрактное производство, связанное с листовым металлом, был логичным шагом. С этой целью компания Eisenwerk Wittigsthal в прошлом году приобрела комбинированную систему для пробивки и лазерной резки Combi Genius от Prima Power.
Название Eisenwerk Wittigsthal может быть знакомо людям в Восточной Германии не только потому, что компания существует уже 366 лет, но и потому, что в 1980-х годах она была крупнейшим поставщиком дровяных водогрейных котлов с эмалированным баком. Любой, кто хотел принять теплую ванну в бывшей Восточной Германии, полагался на эти котлы. Годовой объем выпуска котлов порой достигал 250000 единиц, а в общей сложности их было продано более 4 миллионов. Незадолго до падения Берлинской стены на заводе в Йоханнгеоргенштадте велась подготовка к производству компонентов для восточногерманского малолитражного автомобиля Trabant, но из этого ничего не вышло.
После воссоединения Германии заказы резко сократились, и компании пришлось ждать до 1992 года, когда она была полностью реструктурирована и реорганизована после ее перехода под контроль предпринимателя Винфрида Фридриха. Компания Eisenwerk Wittigsthal превратилась в поставщика готовых системных решений для зданий, основным направлением деятельности которого являются системы измерения, распределения и управления. Эти измерительные системы и распределители устанавливаются в шкафах из листового металла для открытого или скрытого монтажа. Когда Винфрид Фридрих ушел на пенсию в 2008 году, компанию возглавили Йохен Брова и его жена. Они активизировали свою работу в секторе систем вентиляции, продвинули контрактное производство в секторе обработки листового металла и превратили компанию в успешную организацию, в которой на сегодняшний день трудится 60 человек, а годовой оборот составляет около 10 миллионов евро.
Старые и новые технологии автоматизации
Во время нашей экскурсии Йохен Брова показал нам производственный объект площадью 55000 м2. Наша первая остановка была на производстве дровяных водогрейных котлов, которое автоматизировано по технологиям того времени. Один или два раза в год прессы и линия эмалирования запускаются примерно на семь недель для производства 3000-4000 водогрейных котлов, которые все еще пользуются спросом сегодня. Как-никак 10% оборота компании приходится именно на них – пусть небольшая, но, тем не менее, значительная доля, а 75% оборота приходится на системные решения для зданий и сооружений. Оставшийся оборот занимают системы вентиляции и контрактное производство в секторе обработки листового металла.
Индивидуальные решения и серийное производство
«В нашем прайс-листе около 5000 наименований,» – с улыбкой сказал Йохен Брова, – «однако клиенты часто заказывают 5000 компонентов, которых нет в нашем прайс-листе. Наши клиенты действительно ценят тот факт, что они получают от нас индивидуальные решения».
Мы занимаемся как доработкой геометрии стандартных изделий из каталога, так и разработкой совершенно новых конструкций. Это доказывает профессиональную компетентность компании, занятой в том числе в контрактном производстве.
«Мы уже давно занимаемся контрактным производством, но в довольно небольших масштабах. Наше оборудование позволяло выпускать продукцию в ограниченных объемах», – пояснил Йохен Брова. Для этой цели использовались система пробивки и высечки 1990-х годов производства компании Finn Power и относительно новый комбинированный станок для пробивки и лазерной резки от компании Boschert, без автоматизации. Тем не менее, прессы, которые уже есть у компании, также используются для выполнения заказов в секторе систем вентиляции, где объем выпускаемых изделий составляет от 400000 до 500000 единиц ежегодно.
Долгосрочная цель: Индустрия 4.0
Йохен Брова видит потенциал для расширения контрактного производства более крупных серий и унифицированных деталей. «Однако для этого нам нужно гибкое и автоматизированное решение, которое также соответствует критериям Индустрии 4.0.» Идея Йохена Брова заключается в разработке приложения для конфигурирования, с помощью которого клиент может спроектировать свое собственное изделие на своем смартфоне и отправить заказ непосредственно на станок. Однако, по его оценкам, на реализацию проекта уйдет еще 10 лет. Во-первых, внедрение сопряжено с огромными затратами для компании среднего размера, а во-вторых, «наши клиенты относятся к довольно консервативной отрасли и не спешат ввязываться в рискованные дела».
Однако план действий определен, и компания Eisenwerk Wittigsthal GmbH в прошлом году инвестировала в достижение этой цели около 2 миллионов евро. Одним из этих вложений является полностью автоматизированная система для пробивки и лазерной резки от компании Prima Power. «Сначала мы купили только систему для пробивки и лазерной резки, но вслед за этим дополнительно приобрели интерфейсные модули для подключения накопителя и гибочного пресса. Полностью автоматизированная линия гибки, пробивки и лазерной резки будет внедрена, как только будут доступны все устройства в ее составе.
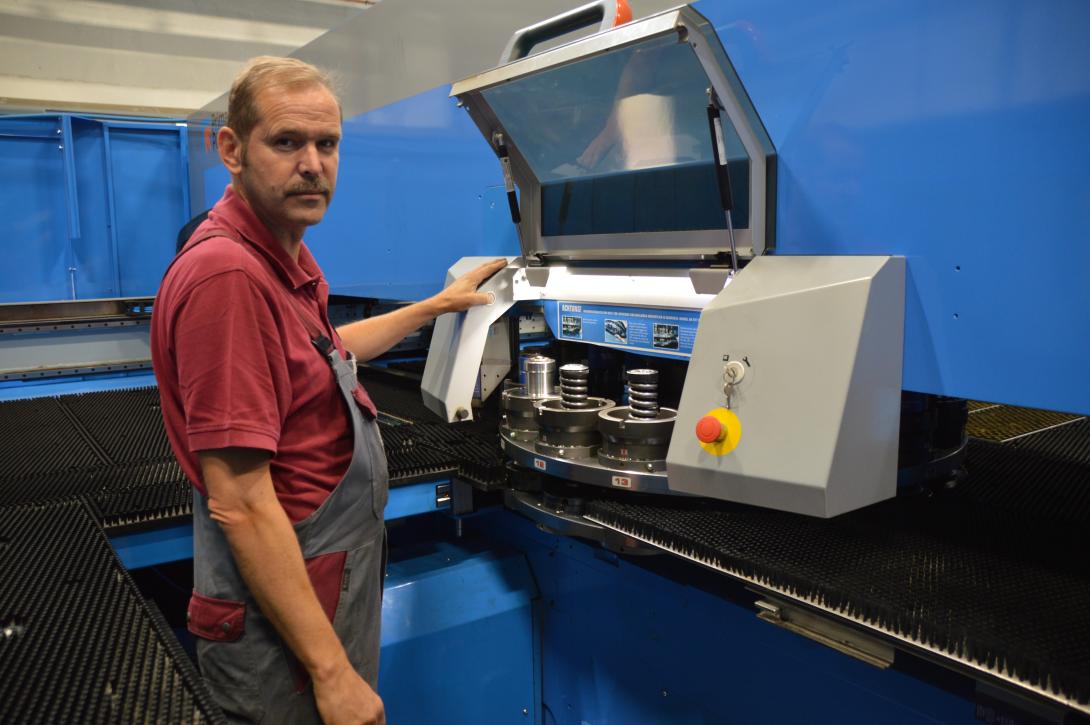
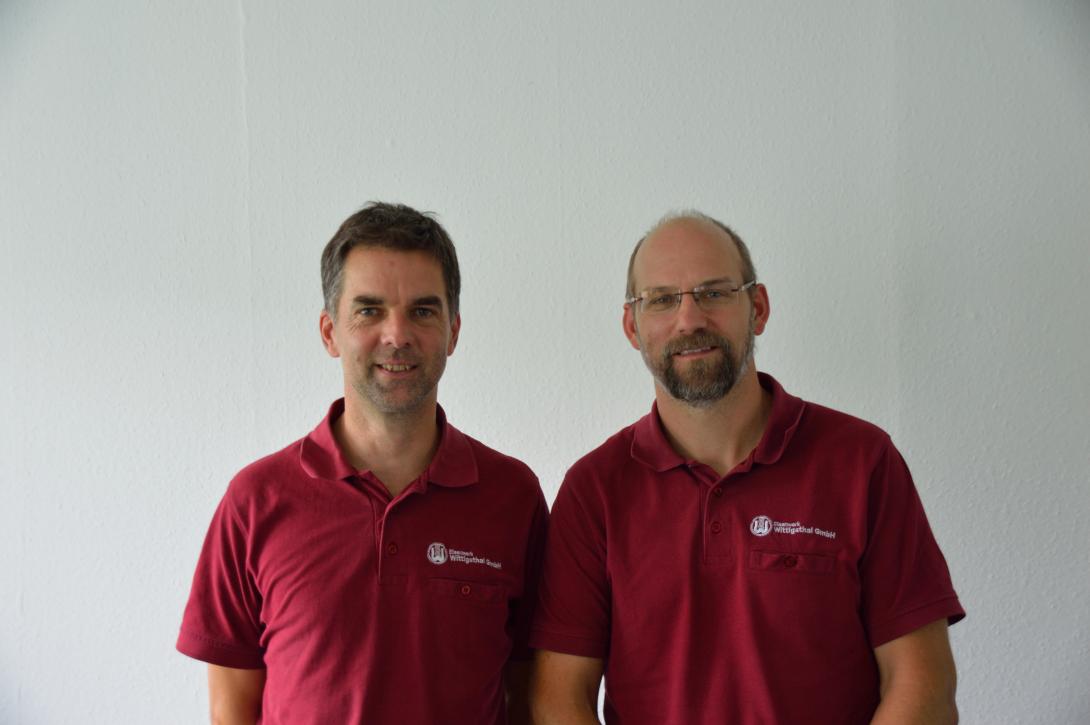
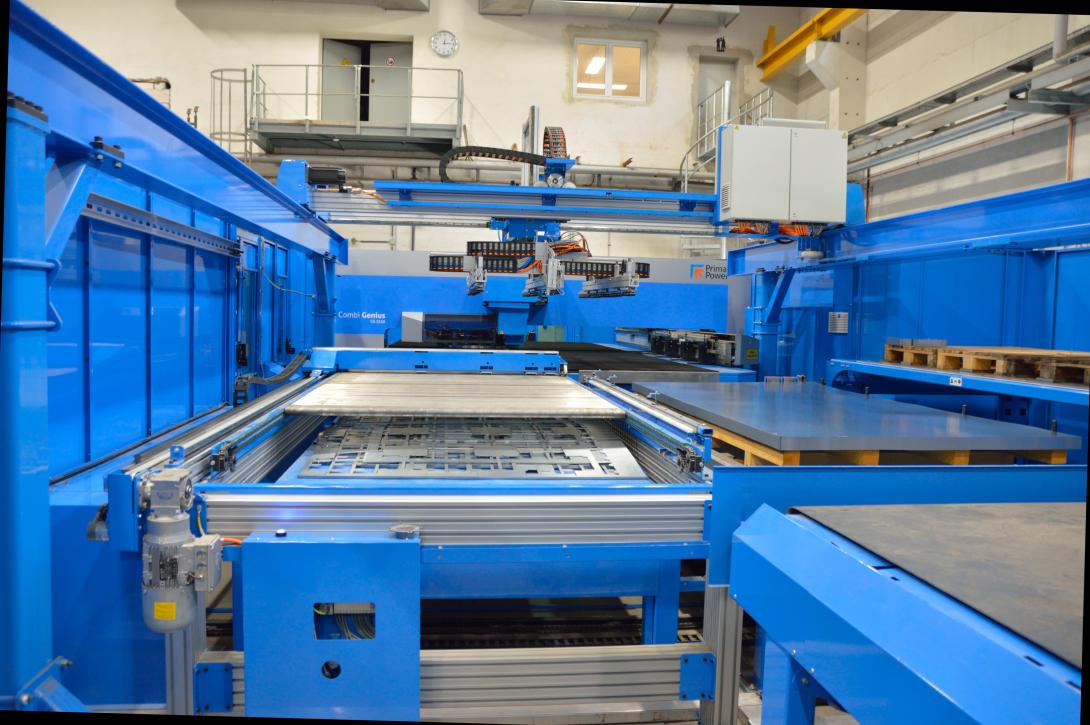
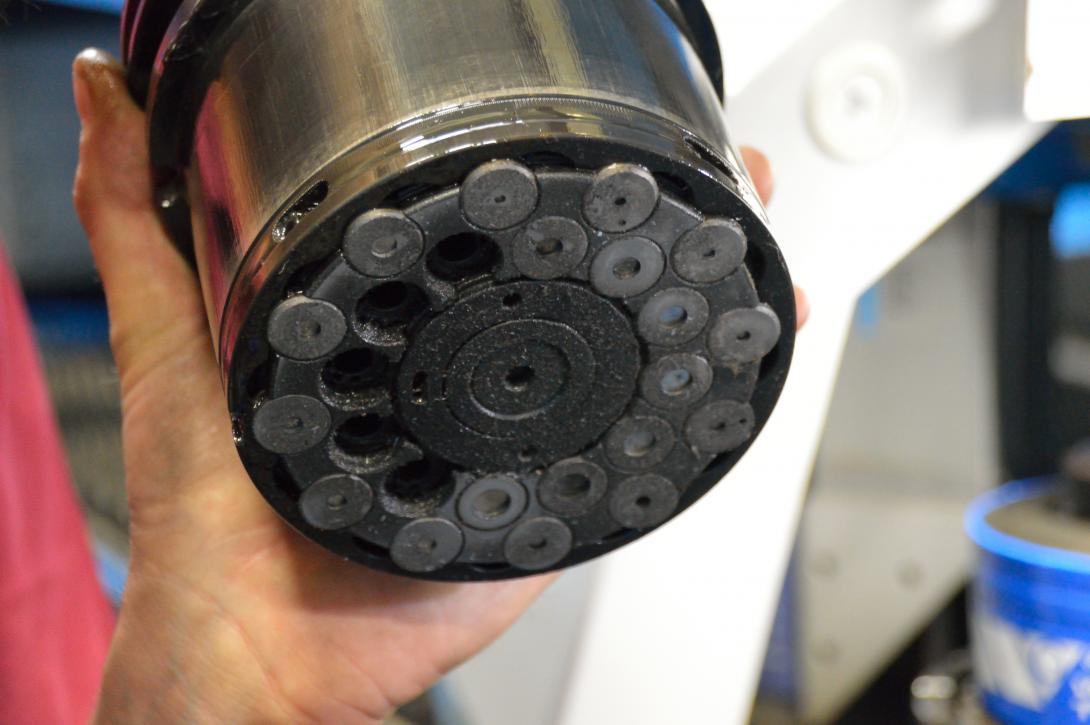
Годы положительного опыта общения
Планируемое открытие нового завода также является результатом многолетнего партнерства с компанией Finn-Power, которая сейчас входит в группу Prima Power Group. «Мы работаем со станком для пробивки и высечки от Finn-Power уже более 20 лет. По этой причине мы обратились в компанию Prima Power. Мы остались довольны этим станком, и после 23 лет эксплуатации мы даже смогли перепродать его, в пригодном для производства состоянии», – сказал Йохен Брова. Разумеется, они изучили разные ценовые предложения до того, как было принято решение об инвестировании, и цена также сыграла свою роль. «Но в конце концов, после двух посещений завода компании Prima Power в Финляндии, я был уверен, что автоматизация будет работать, как и было заявлено.»
Установленная сейчас система представляет собой комбинированный станок для пробивки и лазерной резки Combi Genius с полностью автоматизированным перемещением материалов.
«Комбинированный станок для пробивки и лазерной резки лучше всего подходит для изготовления наших изделий, позволяя в том числе выполнять операции формовки, тиснения и выполнения отверстий под резьбу, а также прошивки большого количества отверстий в компонентах», – пояснил Роберт Виганд, руководитель производства компании Eisenwerk Wittigsthal.
«В секторе систем вентиляции, к примеру, мы изготавливаем детали с несколькими отверстиями, для которых иногда используем инструменты с девятью отверстиями, т.е. инструменты, которые пробивают девять отверстий одновременно. Даже самая быстрая установка для двухмерной лазерной резки не справилась бы с этой задачей.» Для оптимального использования системы у Роберта Виганда есть простое правило: Отверстия и внутренние контуры выполняются путем пробивки, а наружные контуры вырезаются лазером.
Универсальная комбинированная система пробивки и лазерной резки
Комбинированная система Combi Genius на предприятии Wittigsthal оснащена 16-позиционной турелью для пробивных инструментов и лазерной режущей головкой с волоконным лазером мощностью 3 кВт. Все оси приводятся в действие серводвигателями и управляются компьютеризированной системой управления. Станция пробивки оснащена интеллектуальным бойком с поворотным толкателем для быстрой смены инструмента.
В общей сложности в турели может храниться до 384 простых или 128 вращающихся инструментов. «Для этой цели мы можем продолжать использовать все инструменты нашей прежней системы, включая дорогостоящие инструменты для тиснения», – пояснил Роберт Виганд. Предусмотрены дополнительные специальные инструменты, а также инструменты для многоинструментальных станций multi-tool. Можно использовать как старые инструменты системы MultiTool, так и вращающиеся. Станок обладает усилием пробивки 300 кН. Можно осуществлять прокатку роликами (зиговку) и формовку с приподнятой матрицей (высотой до 15 мм), чтобы получить различные формы (загибы, бортики, жабры и т.п.).
Как правило, на станках для пробивки и лазерной резки листовой металл во время обработки удерживается зажимами и перемещается по щеточным столам. Головка для пробивки и лазерная режущая головка остаются в своем фиксированном положении. Щеточные столы рассчитаны на металлические листы массой 250 кг. Щеточные панели с программным управлением, расположенные с передней стороны и внутри рабочей зоны обеспечивают дополнительную защиту поверхности листа. Три зажима удерживают лист, а компьютеризированная система управления настраивает положение в соответствии с управляющей программой, поэтому оптимальное использование листа возможно без переустановки и смещения.
Быстрый и не требующий обслуживания волоконный лазер
В используемой системе установлен лазерный резонатор CF мощностью 3 кВт производства Prima Power. Оптимизированная режущая головка, коллиматор, система позиционирования луча и параметры резки обеспечивают высокое качество и скорость обработки. Различные устройства упрощают работу с лазерной системой. К ним относятся защитное стекло объектива LPW, которое предотвращает осаждение пыли и грязи на объективе при резке, и устройство обнаружения плазмы LPM, которое отслеживает процесс резки и при необходимости автоматически перезапускает систему. Кроме того, датчик контролирует объектив и качество линз.
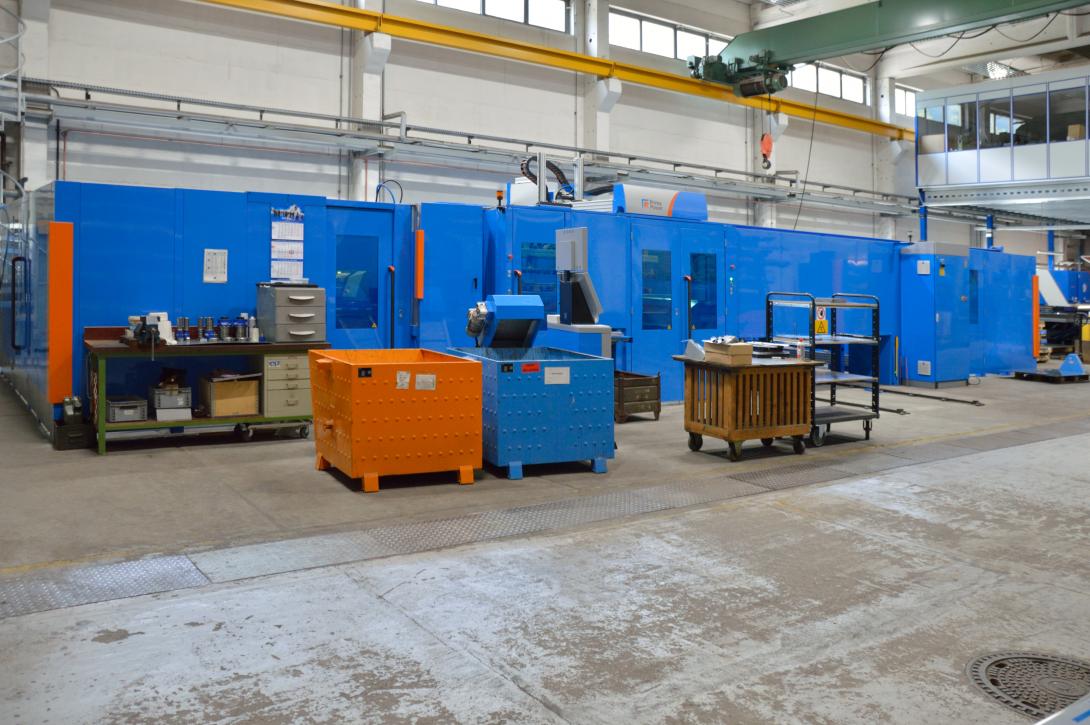
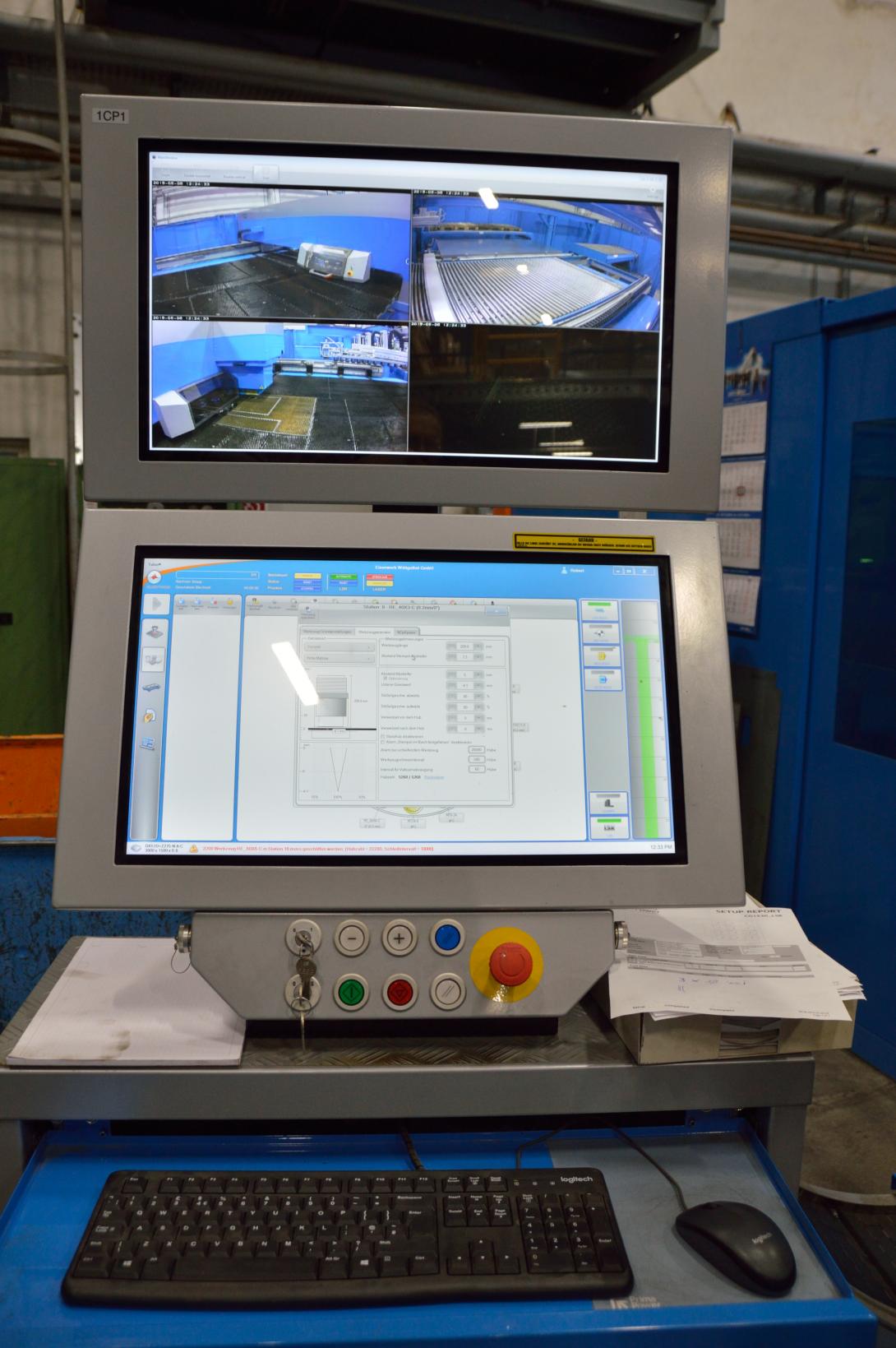
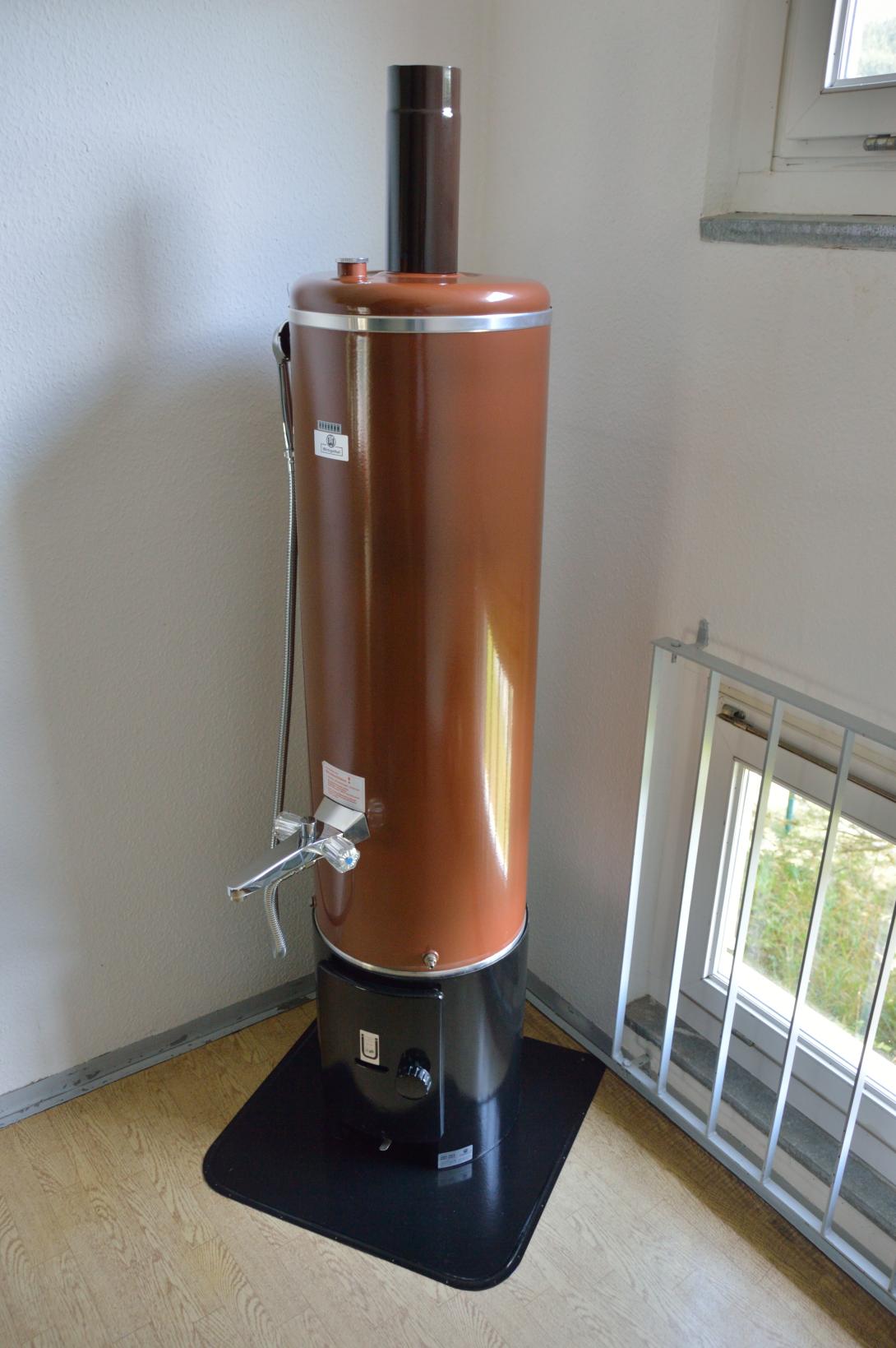
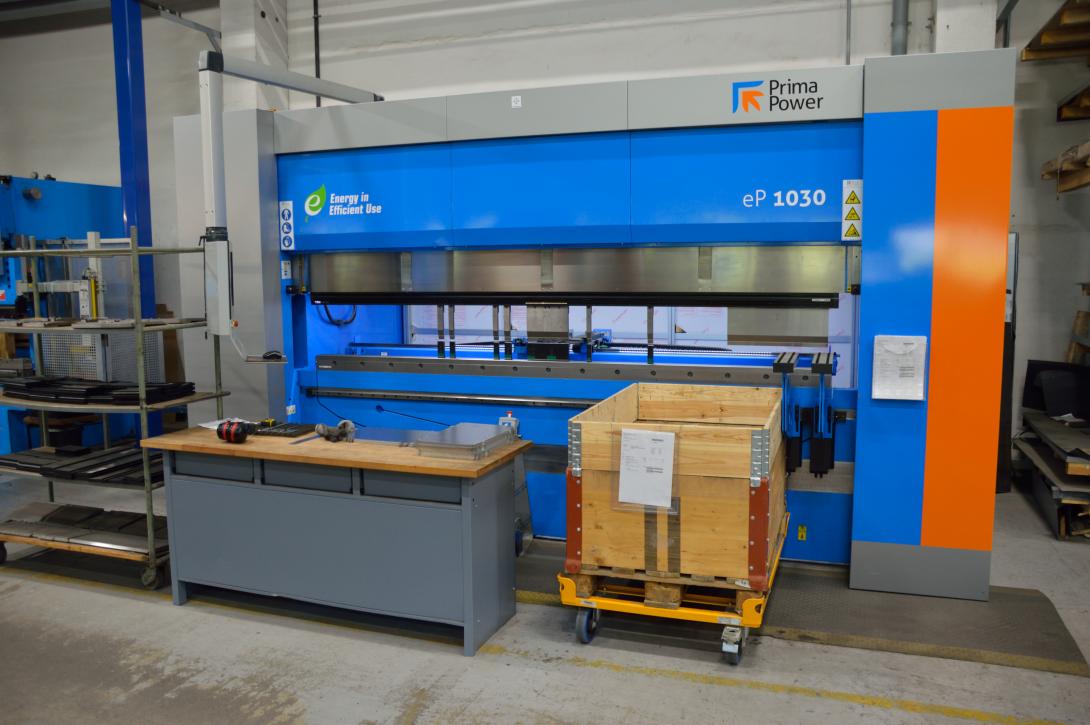
Система загрузки/выгрузки
Готовые детали после пробивки выгружаются с помощью откидного лотка (для деталей размером 500 x 500 мм). Для выгрузки деталей после лазерной резки предусмотрены два откидных лотка: размером 300 мм x 400 мм для быстрой сортировки и размером 800 мм x 800 мм для более крупных компонентов. Однако, большинство деталей выгружается с помощью робота, работающего в системе прямоугольных координат и оснащенного универсальной системой балок с вакуумными присосками.
Пакеты листов подаются в рабочую зону станка во время выполнения технологической операции. Затем робот выполняет все операции загрузки и выгрузки. Он захватывает листы один за другим, выравнивает их и перемещает на стол станка для пробивки и лазерной резки. Параллельно с загрузкой оставшаяся листовая высечка удаляется из рабочей зоны и складывается под стопкой необработанных листов.
В режиме резки робот подбирает готовые компоненты сразу после последнего реза и складывает их в предварительно заданном положении. Для укладки доступны два стола. Теоретически на станок также можно вручную загружать листы длиной до 5 м.
«Нас также привлекла простота работы системы», – сказал Роберт Виганд. «Это относится как к непосредственной работе на станке, так и к программированию. Вы довольно быстро привыкаете к системе, даже не обладая обширными базовыми знаниями. Если вы имеете представление о пробивке и высечке, лазерной резке и основах САПР, это на удивление просто, несмотря на сложность системы.»
Управление системой Combi Genius осуществляется с помощью сенсорной панели управления. Оператор может проверять и настройки системы, и списки заданий. Четыре камеры контролируют внутреннее пространство системы и следят за процессом обработки. Оператор имеет четкий обзор турели со всеми используемыми инструментами, а также наглядно видит настройки лазерной головки. Также доступна система управления инструментом, которая, например, записывает количество выполненных ходов и отображает соответствующие инструкции по обслуживанию.
Операционная система и система программирования NC Express e3 без проблем работают вместе. Задания, созданные в ПО NC Express e3, можно добавлять в перечень заданий с помощью сканера штрих-кода или используя модуль загрузки задач Task loader, который автоматически выбирает их из базы данных и вставляет в список заданий со всей необходимой дополнительной информацией, такой как управляющая программа, данные на инструмент или материал.
«Мы рассматривали возможность использования системы программирования, которая позволяла бы нам программировать все станки,» – вспоминает Йохен Брова, – «однако мы решили использовать систему Prima Power из-за ее надежного измерения и расчета времени.»
Роберт Виганд отметил, что он уже не единожды поражался тому, насколько точно время, рассчитанное при программировании, совпадает с фактическим временем обработки на станке, даже при работе со сложными изделиями. «Это имеет огромное значение для крупносерийного производства, где часто разница в один цент или доли цента играет существенную роль». А поскольку именно для таких случаев исключительно важна стабильная автоматическая работа, он добавил: «Станок в основном работает автоматически без вмешательства оператора. Если управляющие программы правильно настроены и протестированы, то станок может работать непрерывно и без лишних проверок до тех пор, пока не будет израсходована загруженная пачка листов.»
Тот факт, что системой Combi Genius можно также управлять через смартфон, является еще одним свидетельством того, что компания Eisenwerk Wittigsthal GmbH движется к цифровому производству и Индустрии 4.0. Йохен Брова определенно рассматривает возможность расширения до полностью взаимосвязанной линии гибки, пробивки и лазерной резки.
В нашем прайс-листе около 5000 наименований,» – с улыбкой сказал Йохен Брова, – «однако клиенты часто заказывают 5000 компонентов, которых нет в нашем прайс-листе. Наши клиенты действительно ценят тот факт, что они получают от нас индивидуальные решения
Вы ищете аналогичное решение для вашей компании? Найдите его здесь
Комбинированный пробивной пресс с лазером Combi Genius
КОМБИНИРОВАННЫЕ ПРОБИВНЫЕ/ЛАЗЕРНЫЕ СТАНКИ