
De Wave, l'efficacité et la productivité sont au rendez-vous

Ils parcourent les mers à travers le monde, accueillant de quelques dizaines à quelques milliers de personnes. Nous parlons des navires de croisière, des grands yachts et des bateaux fluviaux pour lesquels le groupe De Wave produit différents types de mobiliers et d'accessoires à bord, tous créés à l'aide de technologies intégrées d'une ligne automatique haute performance de Prima Power.
Si pour vivre éternellement sur un bateau de croisière, il suffit d'attendre quelques années et de disposer d'un million de dollars (selon l'annonce récente d'une compagnie de croisière qui a été la première au monde à dévoiler un navire résidentiel privé de plus de 500 appartements), il en faut heureusement beaucoup moins pour passer quelques jours de détente sur un bateau de croisière, en visitant des lieux de tous les continents, connus et moins connus. En effet, il existe un large choix de navires pouvant accueillir de quelques dizaines à quelques milliers de personnes (passagers et équipage), parmi lesquels de grands paquebots de croisière, de grands yachts, ainsi que des bateaux fluviaux, non moins bien équipés. Tout comme ceux pour lesquels De Wave produit du mobilier et des aménagements, ce qui en fait un prestataire de référence disposant d'un vaste réseau de bureaux et d'installations de production qui soutient l'industrie du yachting et de la navigation de plaisance à l'échelle mondiale.
Issue de la fusion de cinq entreprises, De Wave est aujourd'hui une filiale à part entière du fonds d'investissement américain Platinum Equity. Son siège social est situé à Gênes, en Italie, mais elle fait également partie d'un groupe international avec plusieurs succursales en Pologne, en France, en Allemagne, en Finlande, à Singapour et à Miami, aux États-Unis. En Italie, elle opère également à Monfalcone (GO), avec une usine qui se concentre principalement sur la production de panneaux et de plafonds pour les aménagements des cabines
Les différents types de panneaux et d'éléments de revêtement", explique Alberto Malatesta, directeur d'usine chez De Wave, "doivent répondre à des normes de précision et de qualité extrêmes pour garantir les normes élevées de l'industrie attendues en termes d'exigences esthétiques et de sécurité, tout en respectant des délais de livraison stricts.
Ces caractéristiques particulières sont aujourd'hui atteintes grâce à la technologie solide et fiable fournie et installée en 2021 par Prima Power. Bien sûr, nous parlons de la nouvelle version Ddirect de la ligne de production PSBB, qui peut traiter des tôles provenant d'un entrepôt de stockage, automatiser la gestion des matériaux et des informations, et combiner les processus de production individuels en un processus complet flexible et entièrement intégré.

De la découpe manuelle à l'automatisation de l'usine
Le système de production compact Prima Power PSBB (Poinçonnage, Cisaillage, Tamponnage, Pliage) transforme automatiquement les tôles brutes en composants de haute qualité, prêts à être pliés. Le flux de matériaux peut être organisé avec une flexibilité maximale : pour transférer les pièces directement à la machine de pliage automatique, pour équilibrer les différentes exigences de temps de pliage et de poinçonnage/cisaillage, pour sortir du système et pour introduire de nouveaux matériaux dans le système. La fonction tampon, flexible et polyvalente, permet d'optimiser les coûts et les délais à tout moment, quelle que soit la tâche à accomplir. En effet, la productivité offerte par ce concept découle de l'intégration intrinsèque d'un système de poinçonnage servo-électrique polyvalent avec des systèmes de cisaillage et de pliage servo-électriques intégrés, le tout coordonné par un logiciel sophistiqué qui garantit des flux de matériaux et des étapes de processus optimaux.
"De Wave", commente Malatesta, "a choisi d'investir dans les technologies de Prima Power afin d'augmenter son flux technologique et de production, et d'atteindre une plus grande efficacité, garantissant ainsi une plus grande productivité. La décision a également été motivée par le désir spécifique d'intégrer progressivement 100 % de la production de "coques" pour les panneaux de cabine, qui était jusqu'à présent largement externalisée.
De plus, en intégrant des technologies d'automatisation et d'assemblage supplémentaires, la nouvelle usine de Prima Power a également permis de passer d'une production par lots à un "flux unitaire " beaucoup plus rationalisé et efficace, ce qui a également permis d'améliorer la qualité et la compétitivité.
"La nouvelle ligne, ajoute M. Malatesta, a permis d'obtenir une répétabilité du processus et du produit, un facteur essentiel et décisif pour notre activité, car l'aspect esthétique dépend fortement de la jonction entre un panneau et le suivant, qui ne doit pas présenter d'imperfections. La suppression de l'installation d'un profilé d'assemblage fixé mécaniquement a permis d'augmenter la productivité, grâce aux courbes parfaites obtenues, qui permettent des assemblages précis avec des tolérances très faibles".
Le nouveau système a donc permis à De Wave d'améliorer considérablement son fonctionnement, en passant d'un processus de découpe purement manuel à une véritable automatisation de l'usine.

Du stockage au pliage rapidement et avec précision
L'équipement choisi pour le nouveau système PSBB de De Wave comprend le magasin de stockage de tôles FL utilisé en conjonction avec la cisaille combinée Shear Genius SG 1530 et la panneauteuse EBe 2720 Express Bender.
"Ces technologies de pointe, poursuit M. Malatesta, ont nécessité la formation de nos employés lors de la phase d'installation et de démarrage de l'usine, car ils se sont retrouvés à passer d'un processus traditionnel réalisé avec une cisaille, une poinçonneuse et une presse-plieuse datant du début des années 2000, à une ligne entièrement automatisée. Ce processus de croissance a toutefois conduit à une amélioration constante et continue des compétences de nos employés, ce qui nous a permis d'obtenir des résultats très satisfaisants à ce jour.
En particulier, la ligne de production automatisée se compose de trois zones d'exploitation principales. La première est le magasin de stockage de la tour FL à 10 stations, où sont chargées les tôles prêtes à être transformées. La deuxième zone est le premier poste d'exploitation où se trouve la cisaille combinée Shear Genius SG 1530 et où s'effectue l'optimisation de l'imbrication. La troisième zone est celle de la panneauteuse Express Bender EBe 2720, où les pièces cisaillées et poinçonnées sont introduites pour créer la " coque " finale. Il y a deux sorties de matériaux différentes en fin de ligne : une pour les "coques" finies, qui sont ensuite placées sur des racks spéciaux, et une autre dans laquelle sont introduites les "coques" en panneaux qui nécessitent un pliage supplémentaire. Ce dernier est effectué par une autre presse plieuse Prima Power en début de ligne, avant d'être replacé sur d'autres racks pour continuer le flux de production.
"La mise en œuvre de cette nouvelle ligne, rappelle M. Malatesta, nous a permis d'intégrer une part importante de notre production de coques, ce qui nous a permis de respecter des délais de livraison de plus en plus stricts, de réduire les non-conformités et d'obtenir un produit de meilleure qualité encore. Nous sommes désormais en mesure de produire des coques en tôle en 40 à 80 secondes en flux continu, en fonction de leur complexité et des courbures des panneaux. Nous sommes actuellement à un total d'environ 15 000 panneaux/mois, mais avec une prévision ambitieuse de plus de 18 000 par mois. Ces panneaux sont également conçus et usinés pour garantir un assemblage rapide et sans erreur sur le site, normalement dans des épaisseurs comprises entre 0,5 et 0,8 mm".
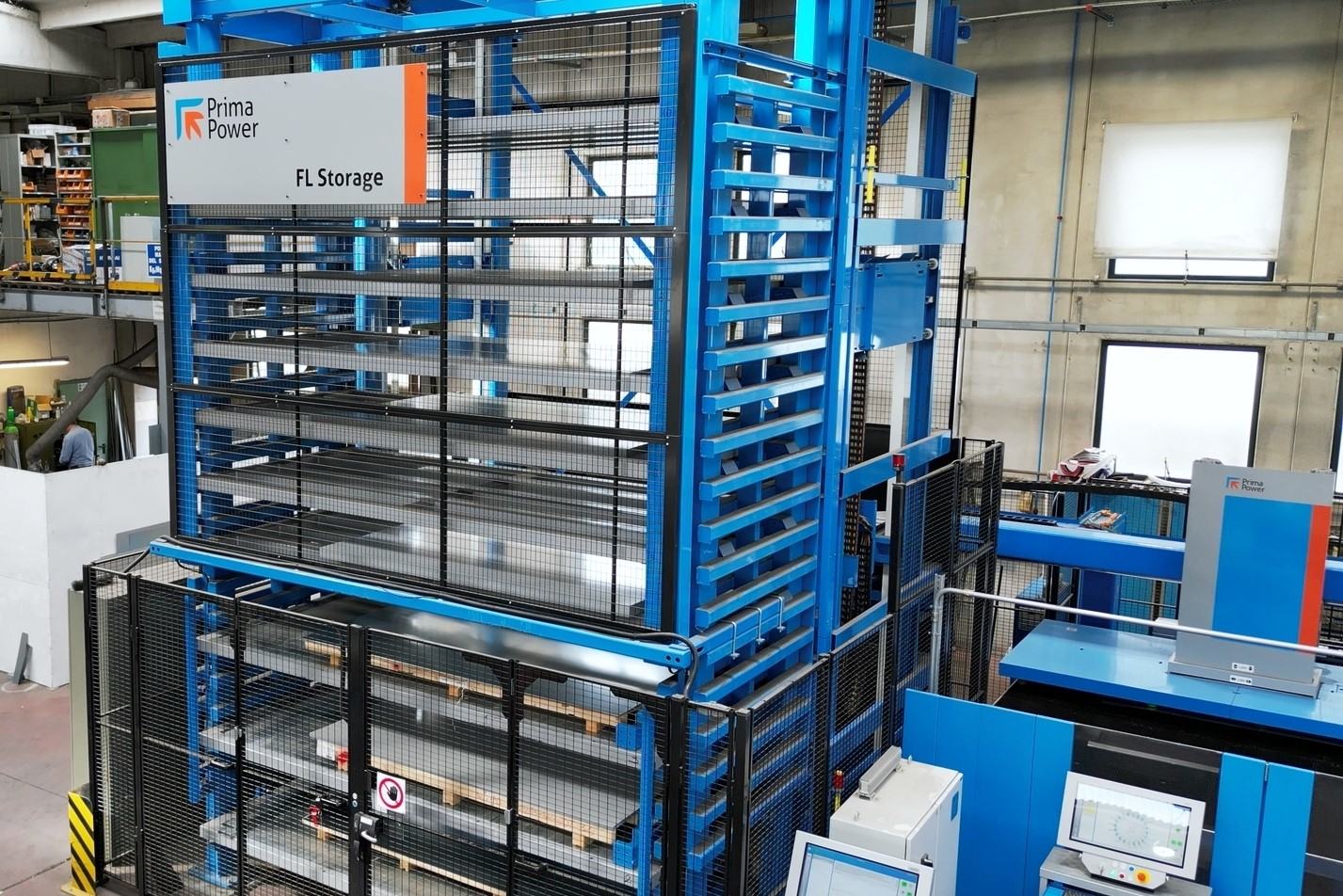



La valeur ajoutée de la programmation paramétrique
La configuration de la ligne choisie par De Wave est parfaitement calibrée pour répondre aux exigences particulières. Il s'agit d'un excellent compromis qui allie flexibilité, compacité et productivité, tandis que le système PCD équilibre et égalise le temps entre la poinçonneuse et la panneauteuse.
"L'aspect logiciel", souligne M. Malatesta, "s'est également avéré essentiel pour la croissance opérationnelle interne. De ce point de vue, la programmation paramétrique a été l'une des exigences discutées et demandées lors de l'évaluation du choix de l'installation, car nos panneaux sont essentiellement de dimensions différentes, à partir d'une géométrie de base. Une fois la section du panneau de référence définie, le système met rapidement les kits en production en utilisant l'une des variables déjà enregistrées, en ajustant seulement quelques paramètres de coupe et de pliage, avec l'avantage de pouvoir maximiser la vitesse de production et de laisser ensuite la ligne prête pour l'assemblage, l'électrification, l'emballage et l'expédition sur le site.
Le transport vers le site est traité avec le même soin et la même considération afin de respecter toutes les exigences, y compris celles déjà mentionnées relatives à l'esthétique et à la sécurité. "Ces exigences de sécurité, ajoute M. Malatesta, correspondent au respect de la résistance au feu et d'une charge structurelle spécifique une fois le panneau terminé. De ce point de vue, il faut tenir compte non seulement des contraintes continues auxquelles sont soumises les pièces, étant donné qu'elles sont montées sur des bateaux, mais aussi du fait qu'elles sont en contact avec un environnement marin, ce qui peut entraîner des phénomènes de corrosion et nuire à leur durabilité."

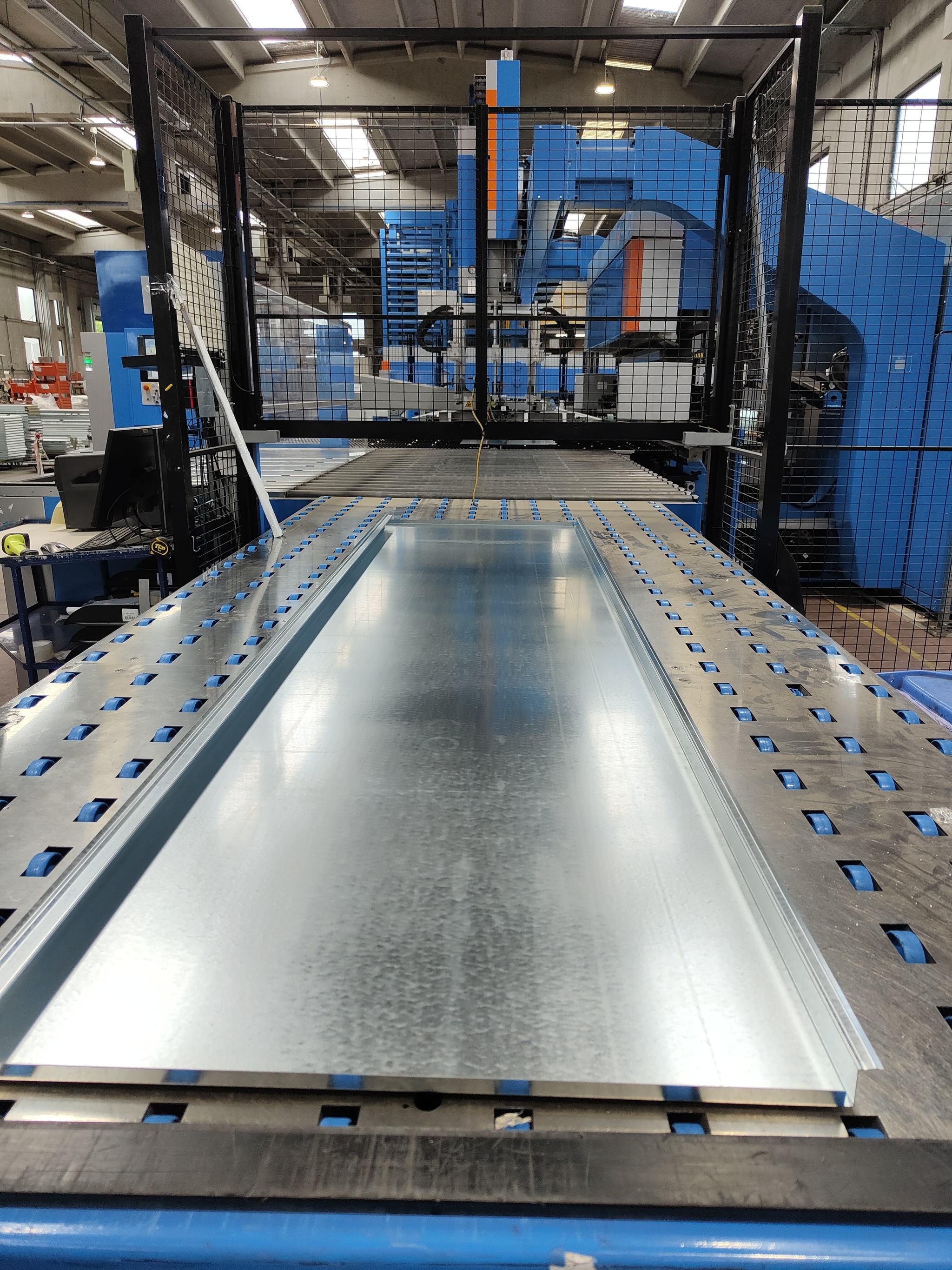
De la conception à la clé en main
L'intégration de la nouvelle ligne Prima Power a permis à De Wave de redéfinir ses actifs opérationnels, comme nous l'avons déjà mentionné, en ramenant un plus grand pourcentage de la production de " coques " à panneaux à l'intérieur de l'entreprise, mais aussi en ramenant d'autres qui étaient également externalisés auparavant, comme la production d'unités humides réalisée dans les usines polonaises de l'entreprise.
"L'usine de Monfalcone, poursuit M. Malatesta, où nous traitons actuellement environ 200 000 mètres carrés de panneaux usinés par an, compte une moyenne d'environ 80 employés répartis dans les différents départements et travaillant sur plusieurs lignes de processus".
Ces lignes de processus comprennent la nouvelle PSBB, ainsi qu'une ligne d'assemblage semi-automatique à flux continu, desservie par deux robots (l'un pour la découpe de l'isolation et l'autre pour la pulvérisation de la colle), accompagnée de deux presses plieuses et d'une poinçonneuse. Il y a également d'une machine à profilage pour la fabrication de douelles et une cisaille.
"Nous avons conservé quelques postes d'assemblage manuel de panneaux en tant que solution de secours", poursuit Malatesta, "pour faire face aux arrêts d'usine, aux travaux de maintenance ou aux pics d'activité exceptionnels."
À cet égard, de nouveaux investissements technologiques (également sur le site de Monfalcone) ont déjà été planifiés en vue d'une amélioration et d'une croissance continues, ce qui permettra d'améliorer et d'optimiser davantage le flux de production, tant par l'ajout que par le remplacement de machines devenues obsolètes.
"La vision de l'entreprise, conclut M. Malatesta, est d'intégrer toute la partie ingénierie de la construction navale à la production visible, en particulier les panneaux, les plafonds et les unités humides. C'est pourquoi nous nous implantons sur le marché non seulement en investissant dans la technologie, mais aussi en rachetant des entreprises afin de pouvoir fournir un service clé en main toujours plus complet".
En bref, il s'agit de se présenter comme un fabricant et un entrepreneur de plus en plus international, capable de couvrir toute la gamme des aménagements intérieurs pour les navires de croisière, les grands yachts et les bateaux fluviaux, qu'ils soient neufs ou réaménagés.
"La mise en œuvre de cette nouvelle ligne, rappelle M. Malatesta, nous a permis d'intégrer une part importante de notre production de coques, ce qui nous a permis de respecter des délais de livraison de plus en plus stricts, de réduire les non-conformités et d'obtenir un produit de meilleure qualité encore.
Vous cherchez une solution similaire pour votre entreprise ? Découvrez-la ici
PSBB
SYSTÈMES DE FABRICATION FLEXIBLES
Système de fabrication flexible
Shear Genius EVO
MACHINES COMBINÉES POINÇONNAGE-CISAILLE