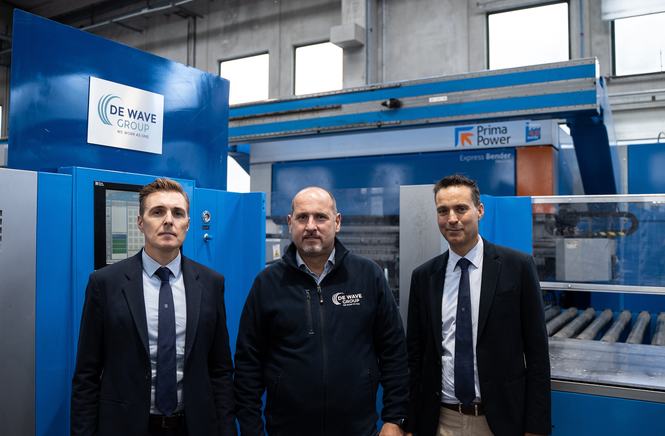
De Wave, 효율성 및 생산성 확보
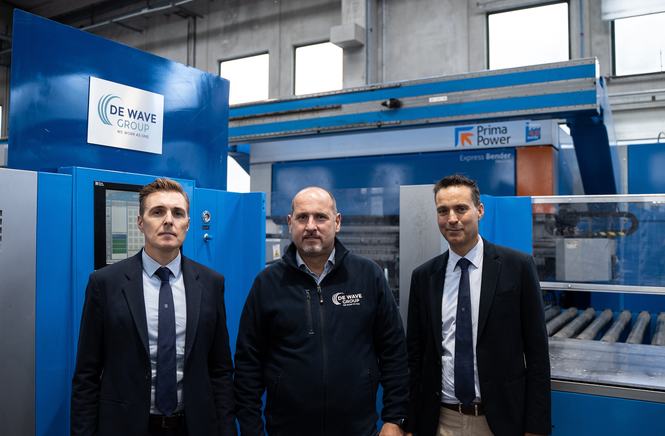
그들은 수십 명에서 수천 명의 사람들이 모이는 전 세계의 바다를 누비고 있습니다. 우리는 다양한 종류의 선내 가구와 부속품을 생산하는 De Wave 그룹의 유람선, 대형 요트, 리버 보트에 대해 이야기하고 있습니다. 모두 Prima Power의 고성능 자동 라인의 통합 기술을 사용하여 만들어졌습니다
크루즈선에서 영원히 살기 위해 '필요한 모든 것'이 몇 년을 기다면서 백만 달러의 여웃돈을 갖는 것이라면 (세계 최초로 500개 이상의 방이 있는 개인 주거용 선박을 공개 한 크루즈 회사의 최근 발표에 의하면) 운 좋게도 크루즈선에서 휴식을 취하면서 모든 대륙의 잘 알려진 장소와 덜 알려진 장소를 방문하는 데 필요한 시간이 훨씬 더 적게들 것입니다. 실제로, 대형 유람선, 대형 요트는 물론 시설이 잘 갖춰진 리버 보트를 포함하여 수십 명에서 수천 명(승객 및 승무원)을 수용할 수 있는 다양한 선박이 있습니다. De Wave는 가구 및 부속품을 생산하는 것과 마찬가지로 전 세계 요트 및 유람선 산업을 지원하는 거대한 사무실 및 생산 시설 네트워크를 공급하는 업체들의 기준을 만듭니다.
5개 회사의 합병으로 탄생한 De Wave는 현재 미국 투자 펀드인 Platinum Equity가 전액 출자한 자회사입니다. 본사는 이탈리아 제노바에 있지만 폴란드, 프랑스, 독일, 핀란드, 싱가포르, 미국 마이애미에 여러 지사를 둔 국제 그룹의 일부이기도 합니다. 이탈리아에서는 몬팔코네(GO)에서도 운영되고 있으며 주로 객실 피팅용 판넬과 덮개 생산에 중점을 둔 공장이 있습니다.
DeWave의 공장 관리자인 Alberto Malatesta는 "다양한 유형의 판넬과 외장 커버 유닛은 미관 및 안전 요구 사항에 기대되는 높은 산업 표준을 보장하고 엄격한 납품 기한을 준수하기 위해 극도의 정밀도와 품질 표준을 충족해야 합니다."라고 말합니다
이러한 특별한 기능은 현재 Prima Power가 2021년에 공급하고 설치한 견고하고 신뢰할 수 있는 기술 덕분에 달성되었습니다. 물론 우리는 스토리지 웨어하우스 에서 판금을 처리하고 재료 및 정보 관리를 자동화하고 개별 생산 프로세스를 완전히 유연하고 완전히 통합된 프로세스로 결합할 수 있는 PSBB 생산 라인의 새로운 Ddirect 버전에 대해 이야기하고 있습니다.
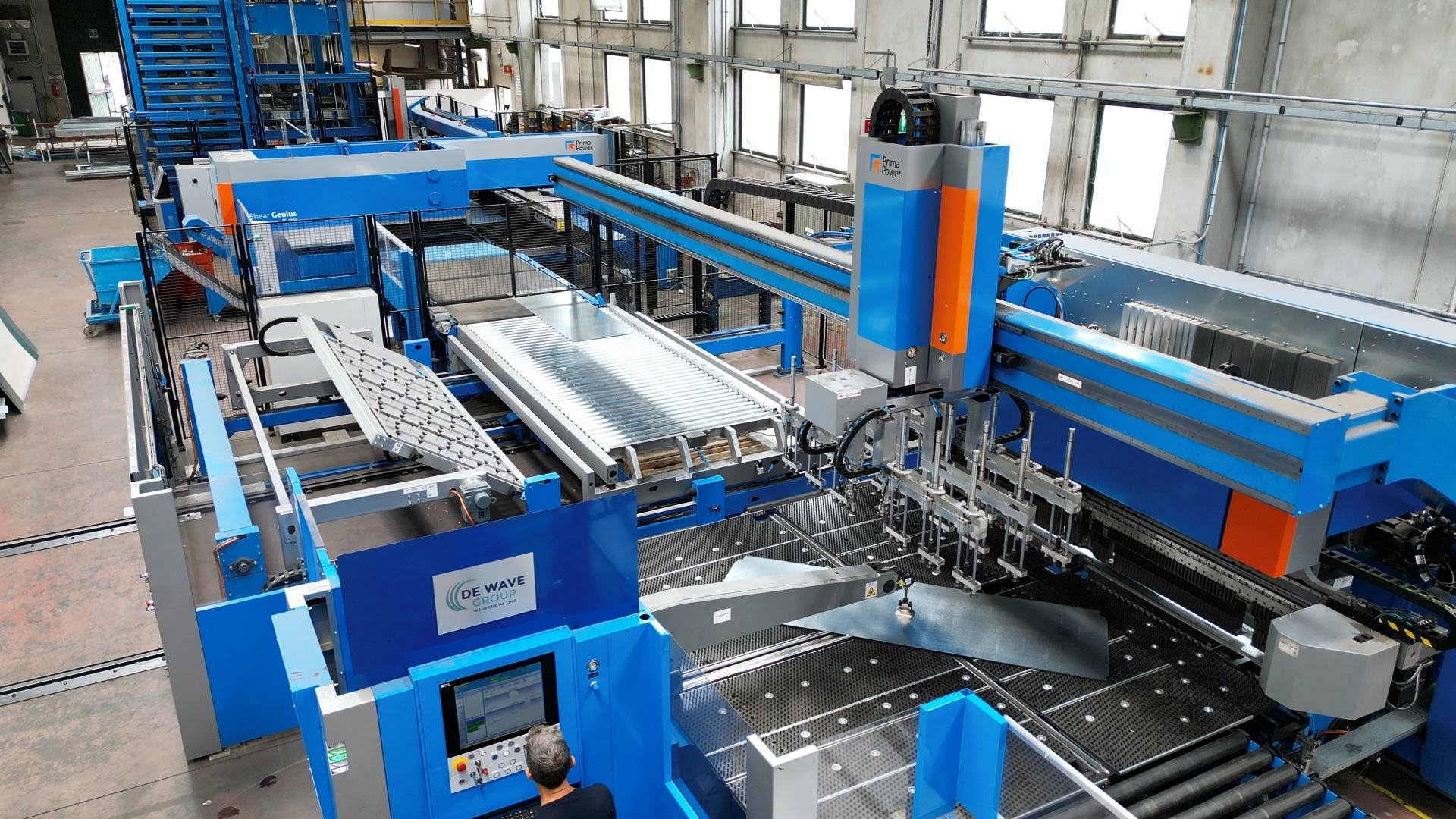
수동 절단에서 공장 자동화까지
Prima Power PSBB(펀칭, 전단, 버퍼(대기), 절곡) 소형 생산 시스템은 빈 금속 시트를 고품질의 사전 준비된 벤딩 구성 요소로 자동 변환합니다. 생산 흐름은 최대한 유연하게 구성할 수 있습니다. 공작물을 자동 벤딩 장비로 직접 옮기고, 다양한 벤딩 및 펀칭/전단 시간 요구 사항의 균형을 맞추고, 시스템을 종료하고 새로운 자재를 시스템에 도입할 수 있습니다. 유연하고 다기능의 버퍼링 기능은 어떤 작업이든 간에 항상 비용 및 시간이 최적화된 작동을 보장합니다. 실제로 이 컨셉이 제공하는 생산성은 최적의 재료 흐름과 공정 단계를 보장하는 정교한 소프트웨어로 조정되는 통합 서보-일렉트릭 전단 및 벤딩 시스템과 다기능 서보 전기 펀칭 시스템의 본질적인 통합에서 비롯됩니다
"De Wave” Malatesta는 말합니다. “Prima Power의 기술에 투자하여 기술 및 생산 흐름을 높이고 더 높은 효율성을 달성하여 생산성을 보장하기로 결정했습니다. 이 결정은 또한 지금까지 대부분 아웃소싱되었던 실내 판넬용 '쉘' 생산의 100%를 점진적으로 회사내부로 가져오고자 하는 구체적인 바람에서 비롯되었습니다."
또한 추가 자동화 및 조립 기술을 통합함으로써 새로운 Prima Power 플랜트는 일괄 생산에서 훨씬 더 능률적이고 효율적인 '일체형 흐름'으로 전환할 수 있게 하여 품질과 경쟁력도 향상시켰습니다.
“새로운 라인은”이라고 Malatesta는 덧붙입니다, “우리 사업에 필수적이고 결정적인 요소인 프로세스 및 제품 반복성을 제공했습니다. 한 패널과 다음 패널 간의 결합에 결함이 없어야 하는 미학적 요소에 크게 의존하기 때문입니다.”
따라서 새로운 시스템을 통해 DeWave는 순전한 수동 절삭 공정에서 진정한 공장 자동화로 전환하여 운영을 크게 개선할 수 있었습니다.
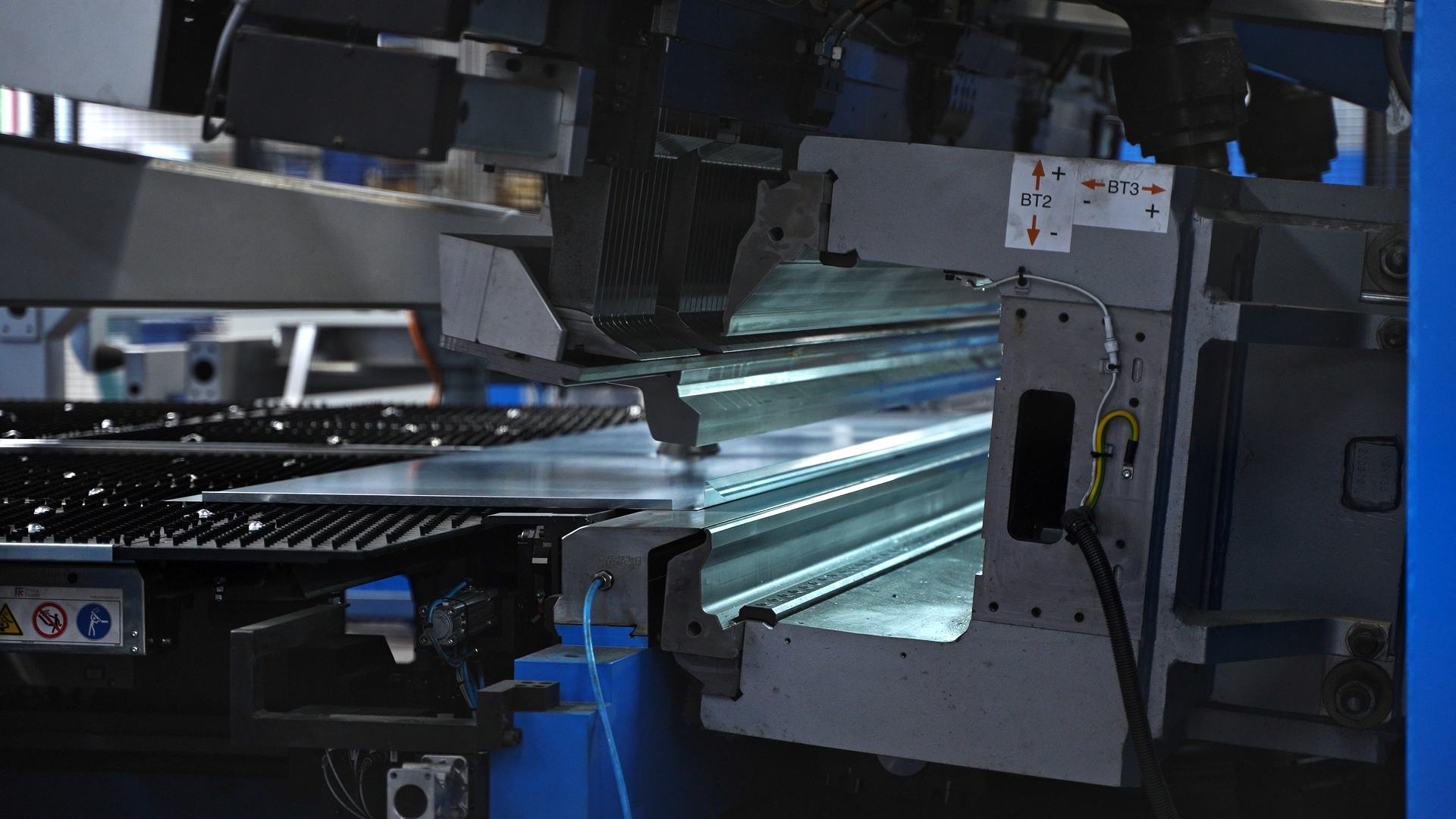
스토리지에서 프레스 벤딩에 이르기까지 빠르고 정확하게
De Wave의 새로운 PSBB 시스템을 위해 선택된 장비에는 Shear Genius SG 1530 펀치/전단기 콤비 및 EBe 2720 Express Bender 패널 벤더와 함께 사용되는 FL 판금 보관 창고가 포함됩니다.
"이러한 주목할만한 기술은" Malatesta는 계속합니다. “2000년대 초반의 전단, 펀칭 머신 및 프레스 벤더로 수행된 전통적인 프로세스를 처리하던 것에서 완전히 자동화된 라인으로 전환하여 공장의 설정 및 시작 단계에서 직원들을 교육하는 것을 의미했습니다. 그러나 이러한 성장 경로는 직원들의 기술을 지속적이고 지속적으로 향상시켜 지금까지 매우 만족스러운 결과를 달성했습니다.”
특히, 자동화 생산 라인은 세 가지 주요 운영 영역으로 구성되어 있습니다. 첫 번째는 가공 준비가 된 판금이 적재되는 10-포지션에 위치한 FL 타워 보관 창고가 있는 곳입니다. 두 번째 영역은 Shear Genius SG 1530 콤비가 위치하고 네스팅 최적화가 이루어지는 첫 번째 작업 스테이션입니다. 세 번째 영역은 Express Bender EBe 2720으로 전단 및 펀칭 부품을 공급하여 최종 '쉘'을 만듭니다. 라인의 끝에는 두 가지 다른 재료 배출구가 있습니다. 하나는 특수 랙에 배치되는 완성된 "쉘"을 위한 것이고, 다른 하나는 추가 구부림이 필요한 판넬로 된 "쉘"을 공급하는 것입니다. 이 작업은 생산 흐름을 계속하기 위해 다른 랙에 다시 배치하기 전에 라인 앞쪽에 있는 다른 Prima Power 벤딩 장비에 의해 수행됩니다.
“이 새로운 라인을 구현함으로써” Malatesta는 강조합니다. “ '쉘' 생산의 상당 부분을 인소싱할 수 있게 되었고, 점점 더 엄격해지는 납품 시간, 부적합 사항의 감소, 훨씬 더 나은 품질의 제품을 만들 수 있게 되었습니다. 이제는 복잡성과 패널 굽힘에 따라 연속적인 흐름으로 약 40~80초 안에 판금 쉘을 생산할 수 있습니다. 우리는 현재 매달 약 15,000개의 패널을 처리하고 있지만 월 18,000개 이상의 야심찬 기대를 하고 있습니다. 또한 이러한 패널은 일반적으로 0.5~0.8mm 두께로 현장에서 빠르고 오류 없는 조립을 보장하도록 설계 및 가공되었습니다.”
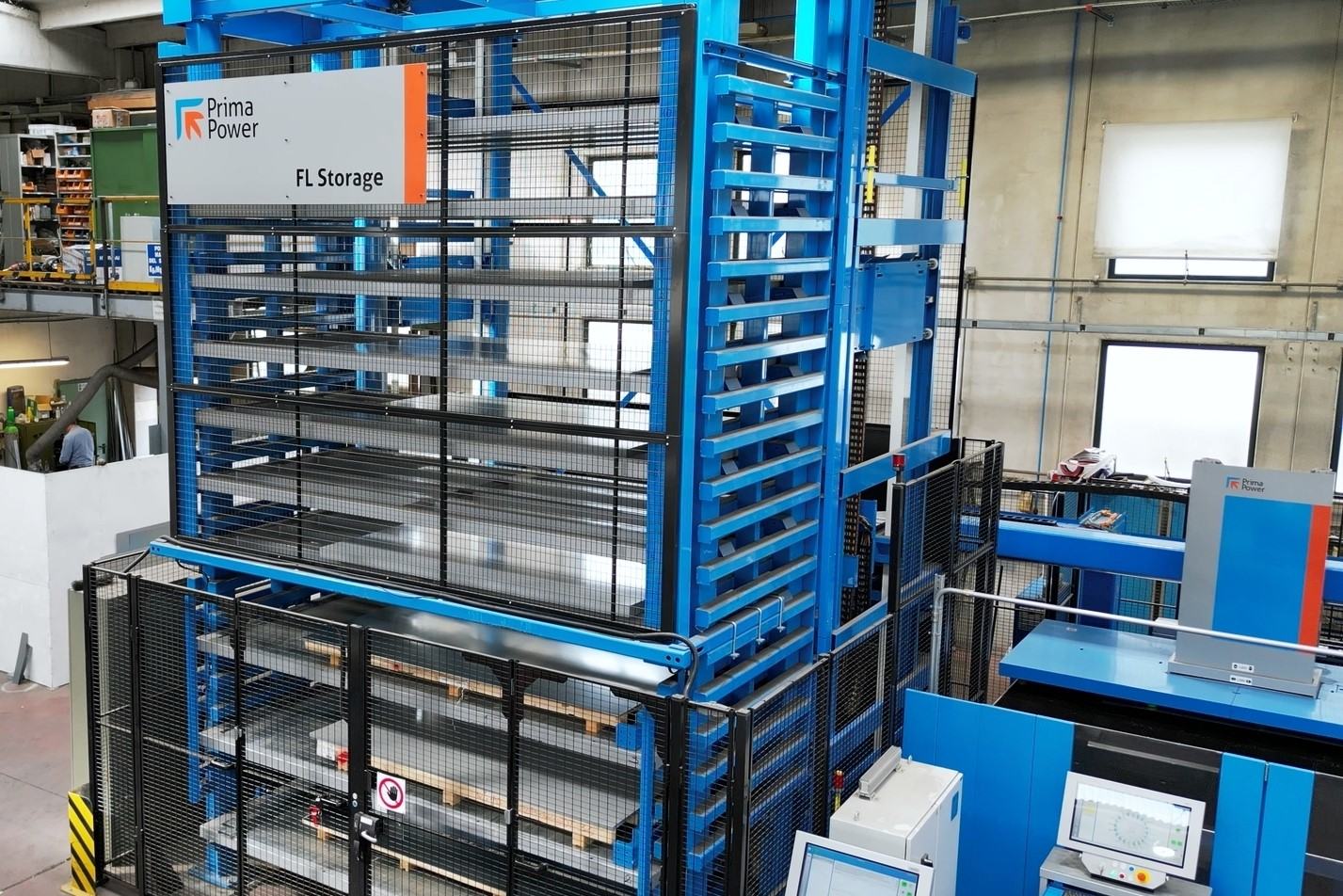

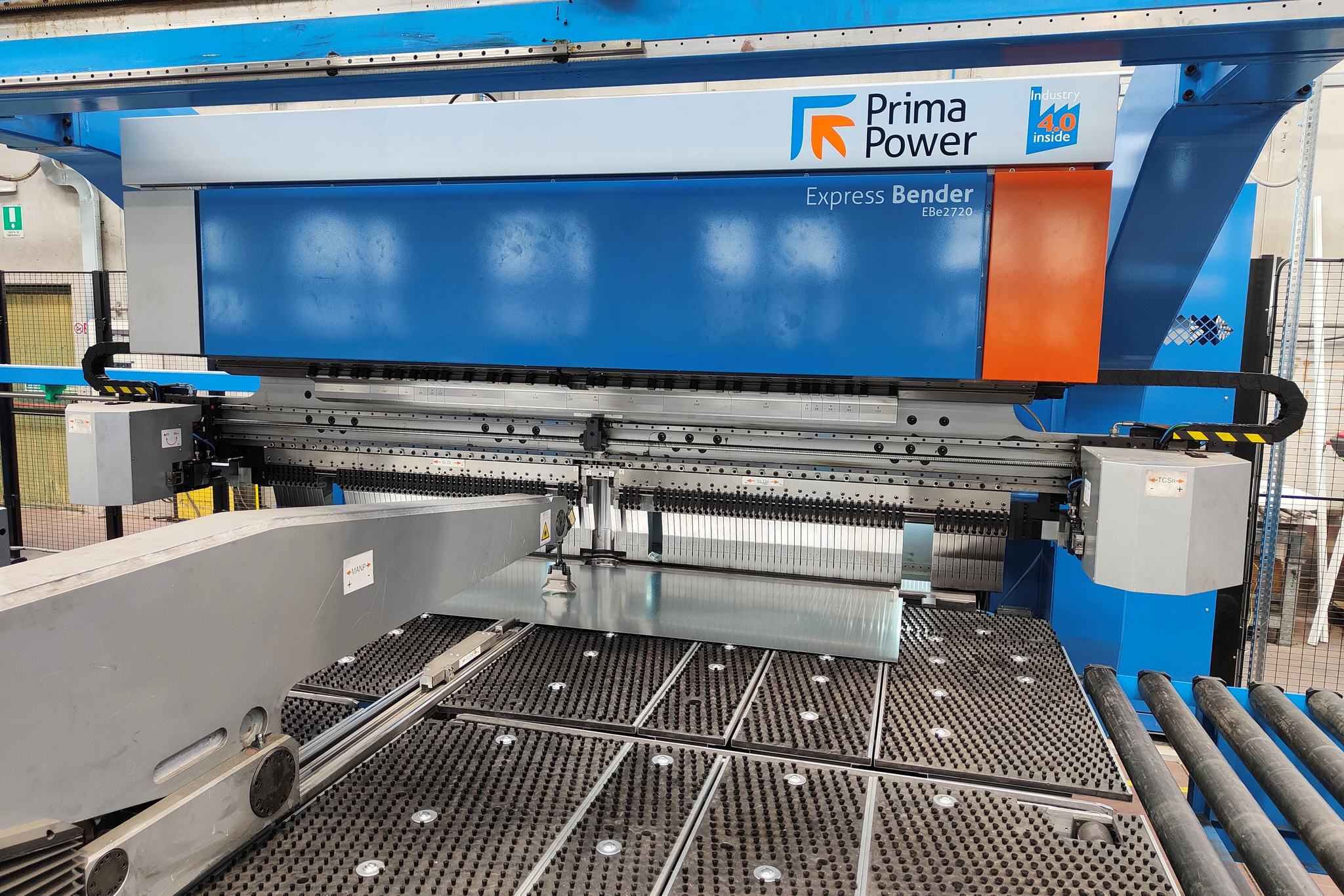
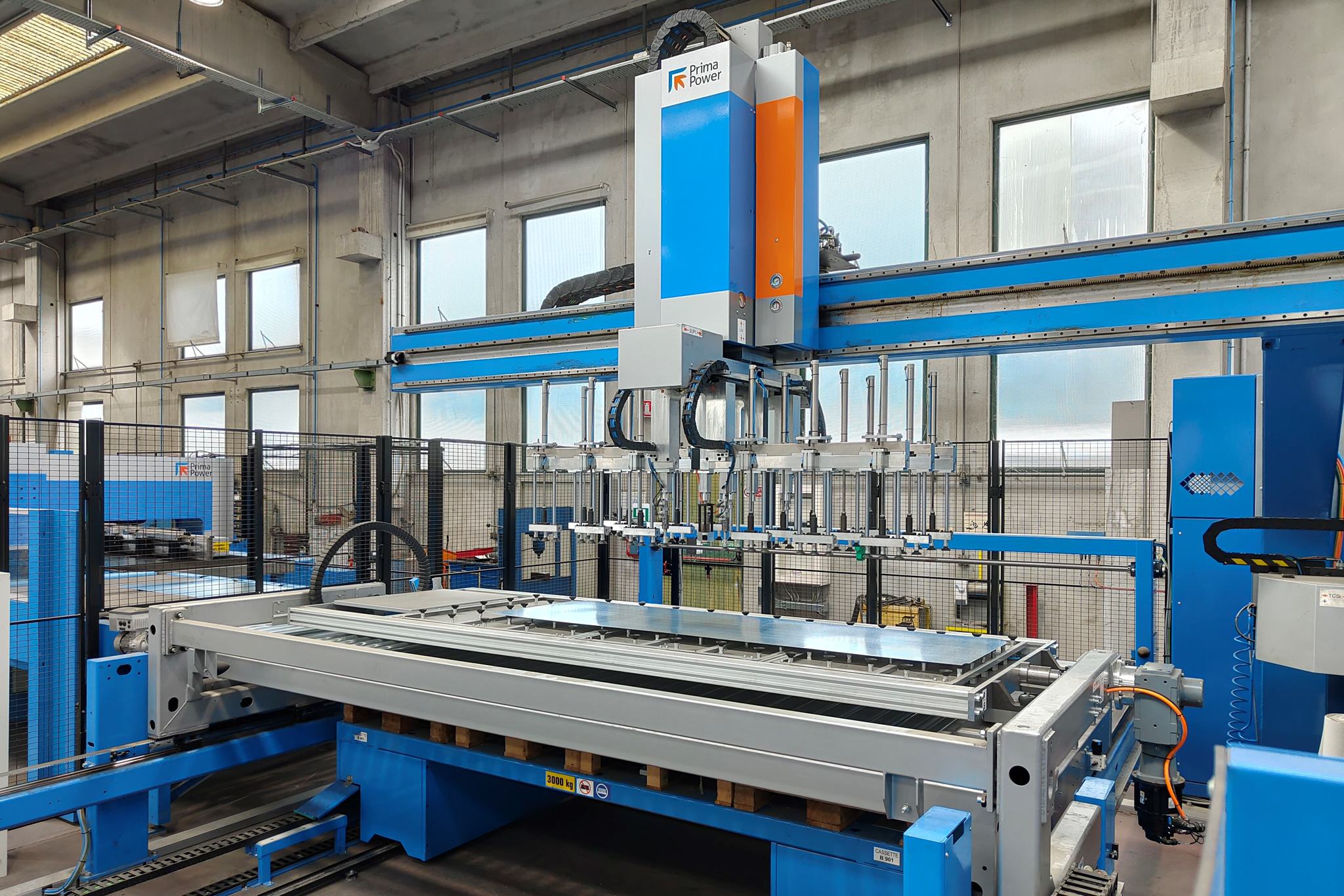
파라메트릭 프로그래밍의 부가가치
De Wave가 선택한 라인 구성은 특정 요구 사항에 맞게 완벽하게 조정됩니다. PCD 시스템이 펀칭 장비와 패널 벤더 사이의 시간 균형을 맞추고 균등하게 조정하는 동시에 유연성, 소형화 및 생산성을 결합하는 탁월한 절충안입니다.
"소프트웨어 측면도” Malatesta는 강조합니다. “내부 운영 성장의 핵심임이 입증되었습니다. 이러한 관점에서 파라메트릭 프로그래밍은 플랜트 선택을 평가할 때 논의되고 요청된 요구 사항 중 하나였습니다. 패널은 기본 기하학에서 시작하여 본질적으로 크기가 다르기 때문입니다. 기준 패널 섹션이 정의되면 시스템은 이미 저장된 변수 중 하나를 사용하여 키트를 신속하게 생산으로 전환합니다. 단 몇 가지 절단 및 벤딩 매개 변수만 조정하면 생산 속도를 극대화한 다음 라인을 현장으로 조립, 전기화, 포장 및 배송할 수 있는 상태로 유지할 수 있다는 이점이 있습니다.
미관 및 안전과 관련하여 이미 언급한 요구 사항을 포함하여 모든 요구 사항을 유지하기 위해 현장으로의 배송은 동일한 주의와 배려로 처리됩니다.
“안전 요구 사항은” Malatesta는 덧붙였습니다. “패널이 완성된 후 내화성 및 특정 구조 하중을 준수하는 것에 해당합니다. 이러한 관점에서 부품이 보트에 장착되어 있다는 점에서 지속적인 응력을 받는 것뿐만 아니라, 부식 현상이 발생하고 내구성에 지장을 줄 수 있는 해양 환경과 접촉하고 있다는 점을 기억해야 합니다”

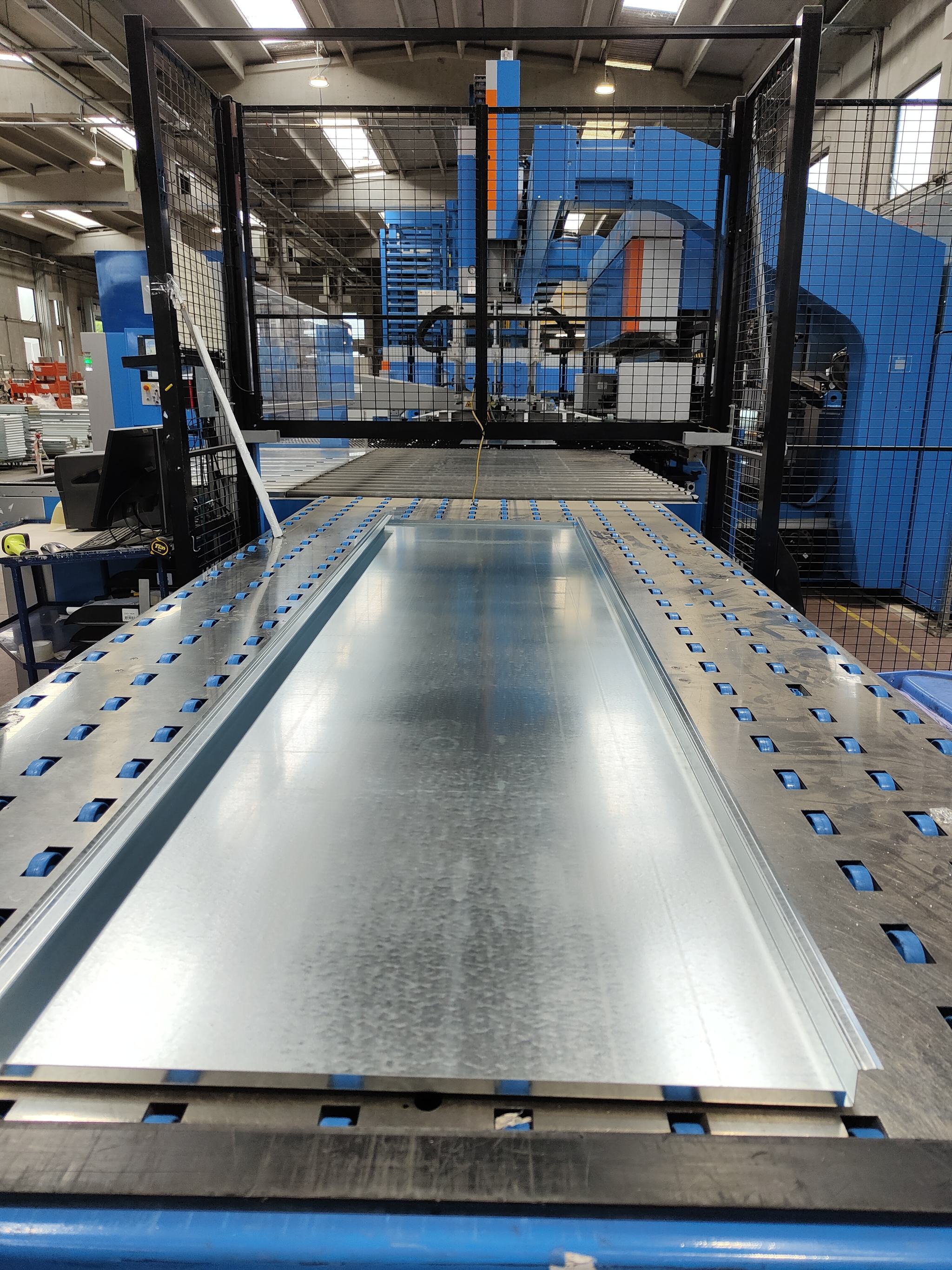
패널에서 턴키까지
새로운 Prima Power 라인의 통합을 통해 De Wave는 이미 언급한 바와 같이 패널 '쉘'의 더 많은 자체적 생산비율을 가져옴으로써 운영 자산을 재설계할 수 있었습니다. 예를 들어 회사의 폴란드 공장에서 수행되는 습식 장치 생산과 같은 것입니다.
Malatesta는 계속해서 말합니다. "우리가 현재 연간 약 200,000제곱미터의 완제품 패널을 처리하는 몬팔코네 공장"에는 평균 약 80명의 직원이 다양한 부서에 분산되어 여러 공정 라인에서 작업하고 있습니다.
이러한 공정 라인에는 새로운 PSBB와 두 대의 로봇(하나는 단열재 절단용, 다른 하나는 접착제 분사용)이 서비스하는 반자동 연속 흐름 조립 라인이 포함되며, 측면에는 두 개의 프레스 브레이크와 펀칭 장비가 있습니다. 또한 스토브를 만드는 프로파일링 장비와 전단 장비도 있습니다.”
Malatesta는 "우리는 공장 다운타임, 유지보수 작업 또는 극심한 작업 피크에 대비하기 위해 일부 수동 패널 조립 스테이션을 백업으로 보관해 왔습니다."라고 말합니다.
이와 관련하여, 지속적인 개선과 성장을 위해 기술에 대한 새로운 투자(몬팔코네 현장에서도)가 이미 계획되어 있으므로, 이제 구식이 된 장비의 추가 및 교체를 통해 생산 흐름을 더욱 개선하고 최적화할 수 있습니다.
"회사의 비전은” Malatesta는 끝맺음 합니다. “조선의 플랜트 엔지니어링 측면 전체를 가시적인 생산, 특히 패널, 천장 및 습식 장치와 통합하는 것입니다. 그렇기 때문에 우리는 기술에 대한 투자뿐만 아니라 회사 인수를 통해 시장에 진입하여 더욱 완벽한 턴키 서비스를 제공할 수 있습니다."
요컨대, 유람선, 대형 요트 및 리버보트(신규 및 개조)용 인테리어 설비의 전체 범위를 포괄할 수 있는 점점 더 세계적인 제조업체 및 계약업체로 자리매김하는 것입니다.
Implementation of this new line has allowed us to insource a significant portion of our 'shell' production, allowing us to achieve increasingly strict delivery times, a reduction in non-conformities and an even better-quality product.