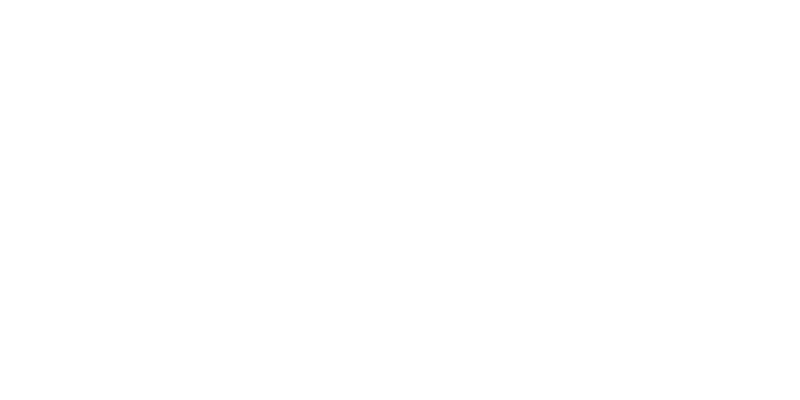
Prestazioni al top
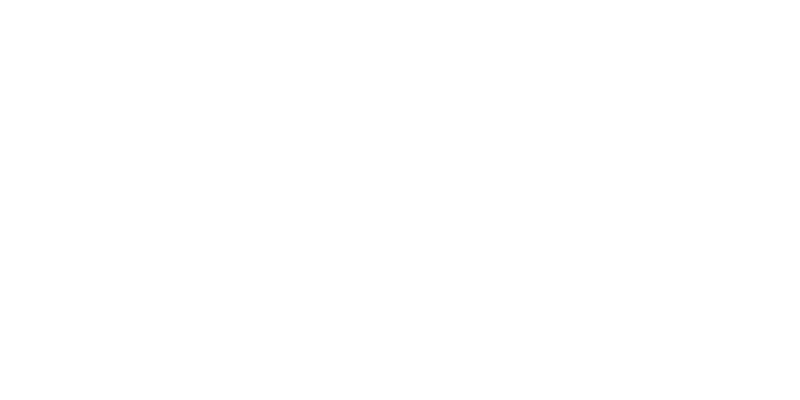
Con oltre un decennio d’esperienza alle spalle nel campo del taglio laser e della piegatura della lamiera, Laserlam è sempre alla ricerca di nuove soluzioni per incrementare la produttività, come la nuova macchina 2D Laser Genius+ di Prima Power
Raddoppio della produttività, dinamiche evolute di processo, prestazioni d’alto livello in chiave 4.0 ed una struttura compatta, di facile installazione e manutenzione. Parliamo della nuova macchina laser 2D Laser Genius+, progettata e realizzata da Prima Power e in funzione presso la Laserlam S.r.l., a conclusione di una fase sperimentale concordata tra le due società, finalizzata ad una valutazione generale del funzionamento e della piena operatività, prima della sua presentazione ufficiale sul mercato. Test affidato proprio all’azienda di Orbassano (TO) in virtù della grande esperienza maturata, in oltre un decennio di attività, da una realtà nata nel 2008 dall’idea dei suoi tre soci fondatori Carlo Ferraro, Bertrand Luchino e Giovanni Luca Davito Gara, professionisti con una lunga e consolidata esperienza nel settore della lamiera.
Evolversi per seguire il mercato
Da puro contoterzista focalizzato sul taglio laser e sulla piegatura, Laserlam ha accresciuto il proprio know-how per arrivare a fornire un servizio completo, dalla scelta dei materiali alla saldatura, dalle lavorazioni meccaniche ai trattamenti termici, divenendo un riferimento sul mercato per la qualità dei propri prodotti. Oggi, la società vanta una trentina di dipendenti dislocati in quattro capannoni produttivi, impegnati nell’analisi e nello sviluppo delle richieste, per formulare una proposta economica il più possibile precisa e competitiva, cui segue tutta la fase realizzativa, che termina con la consegna del prodotto completo in tempi brevi, grazie ad un modello produttivo molto dinamico, organizzato su più turni giornalieri e con una disponibilità di più macchinari e fornitori per ogni singola lavorazione. In virtù degli investimenti fatti in ricerca e sviluppo, uniti alle partnership create e consolidate negli anni, l’azienda torinese è oggi in grado di soddisfare le più diversificate richieste del comparto manifatturiero, garantendo un’elevata qualità dei prodotti e dei servizi, grazie anche all’ottenimento, nel 2010, delle certificazioni ISO 9001:2008 e ISO 14001:2004. «Se nel 2008 il nostro obiettivo era quello del taglio e della piegatura delle lamiere, oggi l’approccio è volto a coprire tutto il ciclo di produzione, ricevendo il disegno dal cliente, per realizzare un prodotto finito, completo anche dei trattamenti termici. Ci rivolgiamo ad una vasta platea di aziende, che possono andare dalla realtà di tipo artigianale, fino alla grande multinazionale dell’automobile e con volumi che possono partire dal singolo pezzo, per arrivare al milione di esemplari, con una media di 25/30 pezzi a commessa - ha affermato Giovanni Davito, Responsabile commerciale di Laserlam S.r.l. - Il nostro vero punto di forza è proprio quello di poter fornire un servizio che vada oltre il particolare: qualsiasi cosa che parta dalla lamiera e che sia possibile realizzare con un laser ed una macchina di piegatura, viene gestita senza problemi e con tempistiche davvero molto strette». Questo, in risposta ad un mercato che, dopo la crisi economica e finanziaria del biennio 2008/2009, ha cambiato volto, seguendo dinamiche molto differenti rispetto a quelle cui il settore manifatturiero era abituato. I clienti s’aspettano sempre più un servizio completo, perché non vogliono dover gestire magazzini o relazionarsi con gruppi di fornitori, preferendo l’interlocutore unico, capace di fornire impianti chiavi in mano. «In questo senso, oggi l’80% delle aziende ci assegna le specifiche del progetto, ma siamo noi ad occuparci dell’approvvigionamento del materiale da lavorare, che abbiamo sempre a magazzino, proprio per essere reattivi alla commessa. Tenendo poi presente che realizziamo circa 2000 nuovi codici al mese, è facile comprendere la complessità della logistica, con un grande dispendio d’energia e di risorse dedicate a quest’attività - ha aggiunto - Più in generale, la gestione di tutto il flusso produttivo è legata ad un software preposto alla generazione dei codici di nuovi prodotti, processando il materiale iniziale, il nesting e le operazioni in macchina, rilevando i tempi di produttività, in un’ottica legata ai concetti dell’Industria 4.0. Così siamo sempre in grado di tracciare ogni fase che porta al prodotto finito, risalendo a tutte le informazioni che possono servire in caso di eventuali problematiche». Dal punto di vista produttivo, Laserlam è strutturata con due impianti per il taglio laser d’ultima generazione, due piegatrici (una elettrica da 40 tonnellate e una idraulica da 250 tonnellate), a cui presto si aggiungerà una hP 1630 di Prima Power, e sette postazioni di saldatura, oltre a tutta una serie di macchine utensili dedicate a piccole lavorazioni a contorno, come maschiature, forature, burattature e lavaggio pezzi, utili a completare la proposta al cliente, senza allungare i tempi di consegna. «Al fine di rispondere alle mutate esigenze del comparto avevamo la necessità di realizzare prodotti sempre di alta qualità, abbassando però i costi legati al consumo di corrente, gas ed aria compressa che, con il nostro laser a CO2, erano davvero molto elevati, divenendo quasi insostenibili. Inoltre, ci serviva un impianto laser, in sostituzione dell’attuale, capace di rendimenti superiori, grazie alla tecnologia in fibra - è intervenuto Bertrand Luchino, Responsabile di Produzione, Qualità, Acquisti e Logistica di Laserlam - Avendo già installato un impianto laser della serie Platino Fiber, fornito da Prima Power, con il quale ci siamo trovati molto bene, abbiamo deciso di accettare la proposta dell’azienda, che aveva la necessità di testare la nuova macchina Laser Genius+ presso una realtà che lavorasse intensamente e con una diversificazione di spessori e materiali piuttosto ampia».
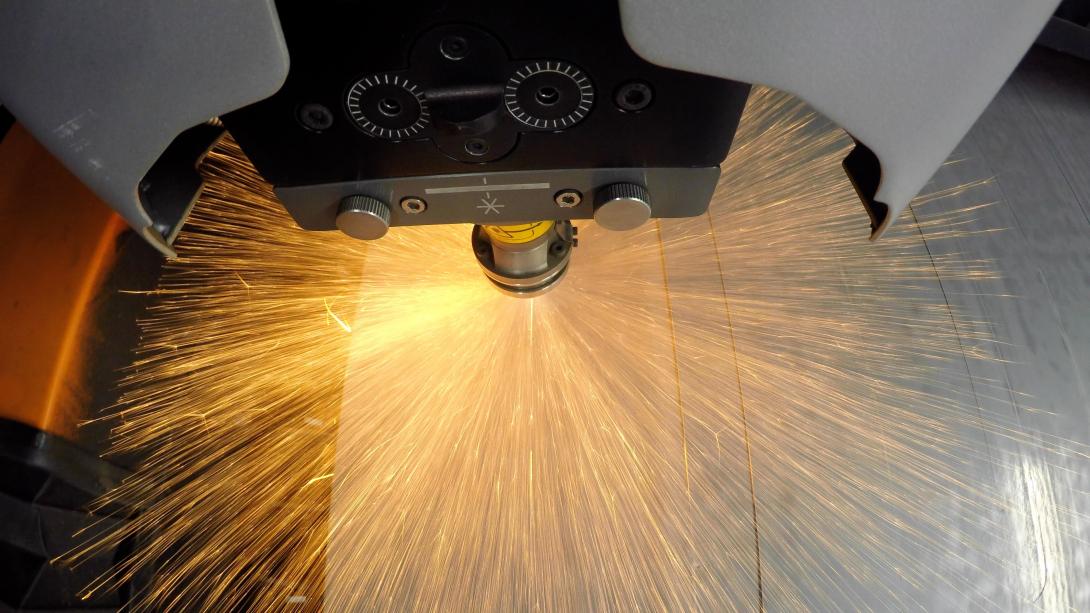
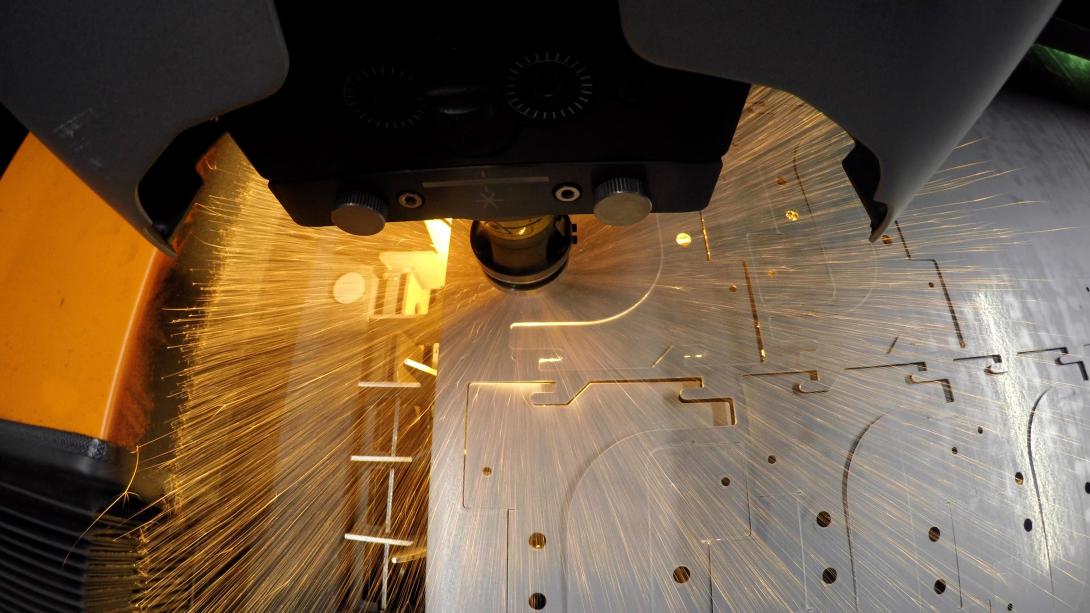
Partnership di successo
Divisione Machinery del gruppo Prima Industrie, specializzata in sistemi laser industriali e macchine per la lavorazione della lamiera, Prima Power è un riferimento internazionale, con un’offerta tra le più ampie, che comprende applicazioni di taglio, punzonatura, cesoiatura, piegatura ed automazione. Con stabilimenti in Italia, Finlandia, USA e Cina ed una rete di vendita e assistenza attiva in oltre 80 paesi, la società è oggi tra i principali operatori nel segmento laser 2D, con una gamma di macchine impiegate in ogni campo e in tutto il mondo, con eccellenti prestazioni ed efficienza. «La versione della nuova macchina Laser Genius+ fornita da Prima Power, da 1.5 x 3 metri di taglia e 6 kW di potenza, vanta contenuti tecnologici davvero importanti. Tra gli aspetti che più ci hanno colpito, ci sono le elevate prestazioni dell’impianto, che ci consente dinamiche di taglio molto più elevate rispetto a quelle cui eravamo abituati - ha proseguito - Proprio la differente dinamica di questa macchina ci ha richiesto una riorganizzazione produttiva. Il nuovo impianto Laser Genius+ , con tempistiche notevolmente ridotte, ci ha imposto una revisione del ciclo produttivo per seguire i ritmi della nuova macchina laser che, su alcuni elementi, ha portato anche ad un raddoppio della produttività». L’impianto sta lavorando in produzione, 24 ore su 24 e, tra gli aspetti positivi sottolineati da Luchino in merito alla nuova proposta di Prima Power, c’è anche quello legato alla compattezza dell’impianto, formato sostanzialmente da due macro-gruppi (macchina e tavola per carico/scarico), grazie ai quali la fase d’installazione s’è rivelata rapida, così come la manutenzione ordinaria e le operazioni di pulizia. Parliamo di un impianto che rappresenta l’evoluzione, con soluzioni tecniche alternative ed innovative, della linea Laser Genius, sulla quale Prima Power ha deciso di puntare anche per il futuro. «È una macchina plug&play, bastano due giorni per installare e avviare la produzione in qualsiasi stabilimento - ha voluto illustrare Cristiano Porrati, Countries Manager South Europe di Prima Power – L’architettura di Laser Genius+ è completamente nuova, e ogni suo dettaglio è ottimizzato per velocizzare la messa in linea, ridurre la manutenzione e aumentare le prestazioni. La macchina è composta da un singolo blocco che include sorgente laser, chiller, motori, ottiche, armadio elettromeccanico ed area di taglio e da un secondo blocco costituito da una tavola di carico/scarico. Portata la macchina in stabilimento, si posizionano i due blocchi e si effettuano i collegamenti elettrici e pneumatici per essere pronti, in breve tempo, all’avviamento e alla produzione». Questo, anche al fine di non lasciar ferma a lungo l’azienda, in attesa della sostituzione di un vecchio impianto con quello nuovo, in aree produttive con spazi sempre più ristretti. La macchina è totalmente interfacciabile dal punto di vista dell’automazione, essendo già disponibile con sistemi di magazzino, carico/scarico e sorting dei particolari lavorati. «È la macchina più smart e interconnessa che Prima Power abbia mai prodotto, – ci spiega Giulio Amore, Product Manager 2D Laser di Prima Power - con nuovi sensori della testa laser e algoritmi di intelligenza artificiale per funzionalità avanzate di monitoraggio e controllo del processo». La visualizzazione e reportistica dei processi produttivi in tempo reale garantisce la totale compatibilità con i criteri di Industria 4.0 e la capacità di interconnessione con qualsiasi sistema analitico gestionale. «Lo dimostra anche la presenza, come dotazione standard, di due monitor HD da 24”, - continua Giulio Amore - il primo dedicato all’interfaccia HMI e il secondo alla visualizzazione di ciò che avviene all’interno dell’area di lavoro. Inoltre, ci tengo a sottolineare che Laser Genius+ è caratterizzata da un layout simmetrico e reversibile, che aumenta la praticità e la flessibilità di installazione della macchina per una migliore collocazione in qualunque contesto produttivo».
«Anche dal punto di vista dell’assistenza tecnica, è risultato tutto molto fluido e snello. Prima Power è un’azienda ancora molto basata sulle persone, dunque spesso ci interfacciamo direttamente con il tecnico che verrà poi a fare manutenzione, così da avere la garanzia che il problema venga compreso sin dall’origine, prima dell’intervento - ha concluso Bertrand Luchino, Inoltre, essendo tutti i componenti high tech della macchina sviluppati e prodotti da PrimaPower - CNC, generatore laser e struttura meccanica -, abbiamo un unico interlocutore, che ci garantisce il controllo totale del processo laser e la massima affidabilità - La professionalità e le competenze che caratterizzano una realtà come Prima Power ci hanno indirizzato, sin da subito, all’utilizzo dei loro impianti, con la certezza di fare sempre la scelta giusta, che meglio si adatta alle nostre necessità, sapendo di poter contare sempre su un’ampia gamma di prodotti d’alta qualità, competitivi e dalle elevate prestazioni. Proprio per questi motivi, anche per la nuova piegatrice che entrerà presto a far parte del nostro parco macchine, abbiamo scelto Prima Power, e in particolare una pressa piegatrice idraulica hP 1630, che ci aiuterà ad aumentare la nostra competitività anche nel processo di piegatura»
Il nuovo impianto Laser Genius+ ci ha imposto una riorganizzazione del ciclo produttivo per seguire i ritmi della nuova macchina laser che, su alcuni elementi, ha portato anche ad un raddoppio della produttività
Stai cercando una soluzione simile per la tua azienda? Ecco qui
Laser Genius+
MACCHINE PER IL TAGLIO LASER 2D