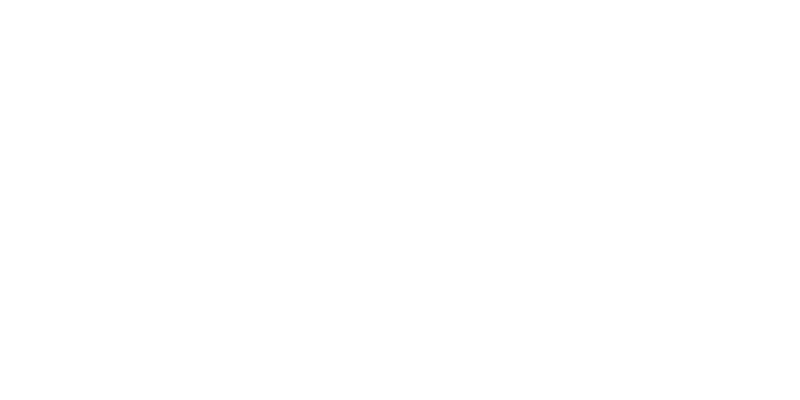
Meilleure performance
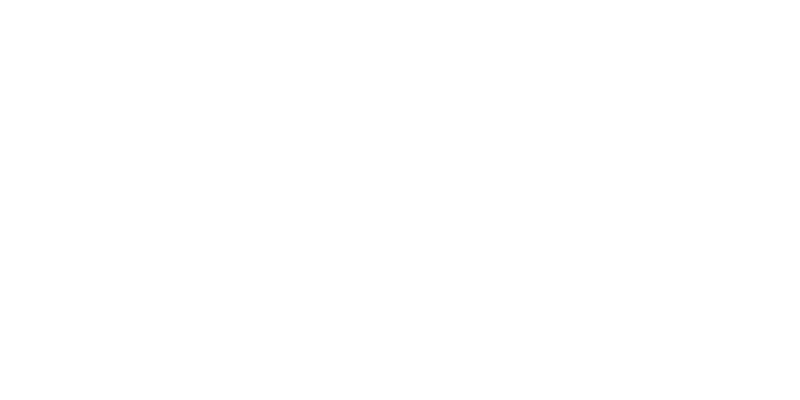
Avec plus d'une décennie d'expérience dans la découpe laser et le pliage de la tôle, Laserlam recherche constamment de nouvelles solutions pour augmenter sa productivité, comme le nouveau Laser Genius+ 2D de Prima Power.
Productivité doublée, processus avancés, performances de haut niveau de l'industrie 4.0 et taille compacte, facile à installer et à entretenir. Il s'agit de la nouvelle machine laser 2D Laser Genius+ , conçue et fabriquée par Prima Power et actuellement en fonctionnement chez Laserlam S.r.l. La machine vient de terminer une période de test convenue entre les deux sociétés qui visait à évaluer toutes ses fonctionnalités avant son lancement officiel sur le marché. Le test a été réalisé par l'entreprise d'Orbassano (TO) en raison de son expérience significative acquise au cours de plus d'une décennie de fabrication. Laserlam a été fondée en 2008 par ses trois associés fondateurs, Carlo Ferraro, Bertrand Luchino et Giovanni Luca Davito Gara, des professionnels ayant une expérience vaste et consolidée dans le secteur de la tôle.
Évoluer pour répondre aux demandes du marché
D'un simple entrepreneur concentré sur la découpe et le pliage au laser, Laserlam a accru son savoir-faire pour fournir un service complet, de la sélection des matériaux au soudage, et du traitement mécanique aux traitements thermiques, devenant ainsi un leader sur le marché pour la qualité de ses produits. Aujourd'hui, l'entreprise compte une trentaine d'employés, répartis sur quatre secteurs de production, qui analysent et développent les besoins afin de créer une offre abordable, aussi précise et compétitive que possible. La production suit ensuite, pour aboutir à la livraison d'un produit complet dans des délais très courts, grâce à un modèle de production très dynamique réparti sur de nombreuses équipes de jour et avec un certain nombre de machines et de fournisseurs disponibles pour chaque processus individuel. Grâce à ses investissements dans la recherche et le développement et aux partenariats noués au fil des ans, l'entreprise turinoise est aujourd'hui en mesure de répondre aux exigences les plus variées du secteur manufacturier, en garantissant des produits et des services de haute qualité, notamment grâce aux certifications ISO 9001:2008 et ISO 14001:2004 obtenues en 2010. « Si, en 2008, notre objectif était de couper et de plier la tôle, aujourd'hui, notre approche vise à couvrir l'ensemble du cycle de production, de la réception du projet du client à la création d'un produit fini, en passant par les traitements thermiques. Nous nous adressons à un large éventail d'entreprises, de l'artisan aux grands constructeurs automobiles, et avec des volumes allant de la pièce unique à des millions de pièces, avec une moyenne de 25/30 pièces par commande », explique Giovanni Davito, directeur commercial de Laserlam S.r.l. « Notre véritable force est que nous sommes en mesure de fournir un service qui va au-delà de la pièce unique : tout ce qui part de la tôle et qui peut être réalisé à l'aide d'un laser et d'une plieuse est géré de manière transparente dans des délais très serrés. » Il s'agit d'une réponse à un marché qui, après la crise financière de 2008/2009, a changé de visage, avec une dynamique très différente de celle à laquelle le secteur manufacturier était habitué. Les clients exigent de plus en plus un service complet car ils ne veulent pas avoir à gérer des entrepôts ou à traiter avec des groupes de fournisseurs, préférant une seule entreprise capable de fournir des solutions clés en main. « En ce sens, aujourd'hui, 80% des entreprises nous fournissent les spécifications du projet, mais nous nous chargeons de l'approvisionnement en matériaux, que nous avons toujours en stock afin d'être réactifs aux commandes reçues. Si l'on considère que nous produisons actuellement environ 2 000 nouveaux codes par mois, il est facile d'apprécier la complexité de la logistique requise, à laquelle nous consacrons une énergie et des ressources considérables », a-t-il ajouté. « Dans un sens plus général, l'ensemble du processus de production est géré par des logiciels chargés de générer des codes pour les nouveaux produits, de traiter le matériau initial, d'imbriquer et de faire fonctionner les machines, de détecter les temps de production d'un point de vue Industrie 4.0". De cette façon, nous pouvons retracer toutes les étapes menant au produit fini, ce qui nous permet de retrouver toutes les informations dont nous avons besoin en cas de problème. » Du point de vue de la production, Laserlam dispose de deux systèmes de découpe laser de dernière génération, de deux presses plieuses (une électrique de 40 tonnes et une hydraulique de 250 tonnes) auxquelles s'ajoutera bientôt une hP 1630 de Prima Power, et de sept postes de soudure, en plus d'une série de machines-outils pour le traitement des petits contours, comme le taraudage, le perçage, le culbutage et le lavage des pièces, le tout utilisé pour compléter la commande du client sans augmenter les délais de livraison. « Pour répondre aux besoins changeants du secteur, nous devions offrir des produits de haute qualité constante tout en réduisant les coûts d'électricité, de gaz et d'air comprimé, qui, avec notre laser CO2, étaient si élevés qu'ils devenaient insoutenables. De plus, nous avions besoin d'un système laser pour remplacer notre système actuel qui augmenterait les performances grâce à la technologie de la fibre », ajoute Bertrand Luchino, responsable de la production, de la qualité, des achats et de la logistique de Laserlam. « Comme nous avions déjà installé un système laser à fibre Platino de Prima Power dont nous étions très satisfaits, nous avons décidé d'accepter leur offre car ils avaient besoin de tester leur nouveau Laser Genius+ au sein d'une entreprise qui travaillait très dur avec différentes épaisseurs et une large gamme de matériaux. »
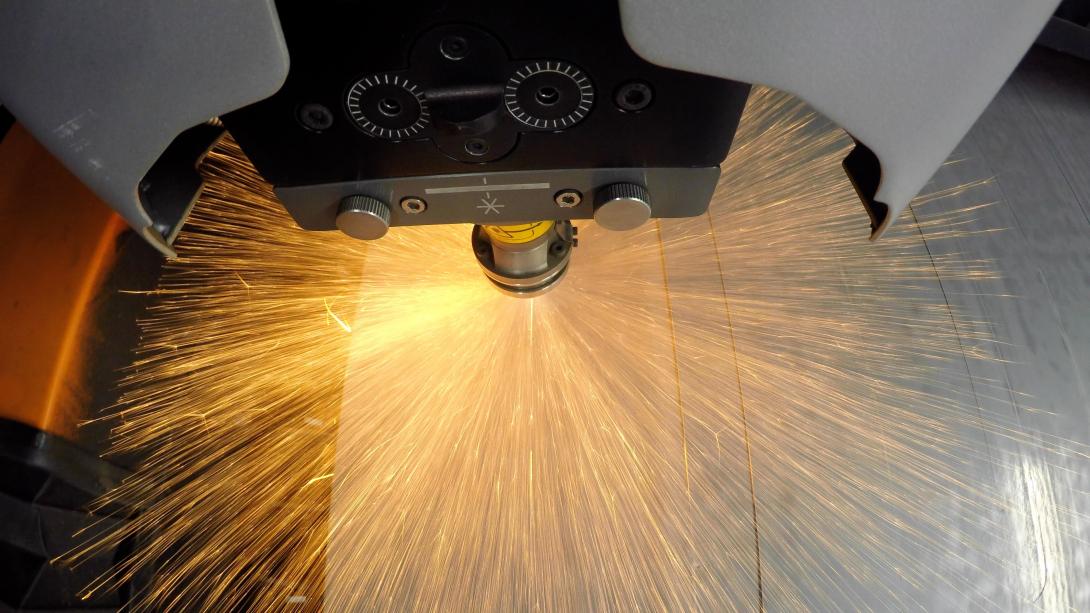
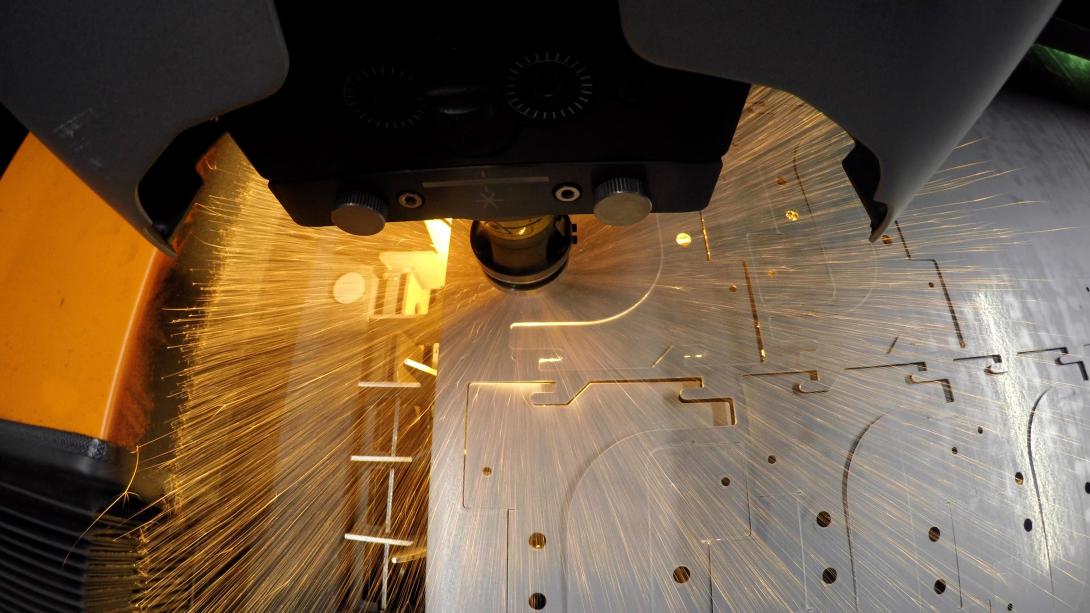
Un partenariat réussi
Prima Power, la division Machines du groupe Prima Industrie, spécialisée dans les systèmes laser industriels et les machines de traitement de la tôle, est un leader international avec l'une des offres les plus larges comprenant la découpe, le poinçonnage, le cisaillement, le pliage et l'automatisation. Avec des usines en Italie, en Finlande, aux États-Unis et en Chine, et un réseau de vente et d'assistance dans plus de 80 pays, l'entreprise figure aujourd'hui parmi les principaux opérateurs du secteur du laser 2D. Elle offre une large gamme de machines pour tous les domaines dans le monde entier, avec d'excellentes performances et une grande efficacité. « Le nouveau Laser Genius+ fourni par Prima Power mesure 1,5 x 3 mètres (59 x 118 pouces) et délivre 6kW, une technologie vraiment avancée. Parmi les caractéristiques qui nous ont le plus impressionnés, il y a les hautes performances du système, qui offre des capacités de coupe beaucoup plus avancées que celles auxquelles nous étions habitués », poursuit-il. « La dynamique différente de cette machine nous a obligés à restructurer notre production. Avec ses délais considérablement réduits, la nouvelle Laser Genius+ nous a obligés à revoir notre processus de production pour pouvoir le suivre, ce qui, sur certains éléments, a même doublé notre capacité de production. » Le système fonctionne 24 heures sur 24 et parmi les aspects positifs soulignés par Luchino concernant le nouveau produit de Prima Power, il y a sa taille compacte, constituée essentiellement de deux unités principales (la machine et une table pour le chargement/déchargement), grâce à laquelle l'installation, ainsi que l'entretien ordinaire et le nettoyage se sont avérés rapides. Grâce à la technologie alternative et innovante utilisée, ce système représente une évolution au sein de la ligne Laser Genius sur laquelle Prima Power a choisi de se concentrer pour l'avenir. « La machine est plug&play. En deux jours seulement, il peut être installé et commencer à produire dans n'importe quelle usine, » explique Cristiano Porrati, directeur des pays d'Europe du Sud chez Prima Power. « L'architecture du Laser Genius+ est entièrement nouvelle et chaque détail est optimisé pour accélérer la production, réduire la maintenance et augmenter les performances. La machine est constituée d'un seul bloc qui comprend la source laser, le refroidisseur, les moteurs, les optiques, l'armoire électromécanique et la zone de coupe et d'un second bloc constitué de la table de chargement/déchargement. Une fois la machine entrée dans l'usine, les deux blocs sont positionnés et les connexions électriques et pneumatiques réalisées, de sorte qu'en peu de temps, la machine est prête à être mise en route et à produire. » Cela signifie également que la production n'est pas arrêtée très longtemps en attendant que l'ancien système soit remplacé par le nouveau, dans des zones de production de plus en plus restreintes. La machine peut être entièrement interfacée pour l'automatisation car elle est équipée de systèmes de stockage, de chargement/déchargement et de tri des pièces traitées. « C'est la machine la plus intelligente et la plus interconnectée que Prima Power ait jamais fabriquée, » explique Giulio Amore, chef de produit laser 2D de Prima Power, » avec de nouveaux capteurs sur la tête laser et des algorithmes d'intelligence artificielle pour une surveillance et un contrôle de processus avancés. » La visualisation et le rapport en temps réel de ses processus de production garantissent une compatibilité totale avec les critères de l'industrie 4.0 et il peut être interconnecté avec n'importe quel système de gestion analytique. « Cela est également démontré par le fait qu'elle est équipée en standard de deux moniteurs HD 24" », poursuit Giulio Amore, « le premier étant utilisé pour l'interface IHM et le second montrant ce qui se passe à l'intérieur de la zone de travail. En outre, je tiens à souligner que Laser Genius+ a une disposition symétrique et réversible, ce qui augmente la praticité et la flexibilité de la machine pour un meilleur placement dans n'importe quel endroit. »
« Même en termes de support technique, elle est transparent et rationalisé. Prima Power reste une entreprise très axée sur les personnes, c'est pourquoi nous traitons souvent directement avec le technicien qui viendra plus tard pour la maintenance. De cette façon, nous avons la garantie que le problème est compris dès le début, avant que le travail ne soit effectué, » conclut Bertrand Luchino. « De plus, comme tous les composants de haute technologie de la machine sont développés et produits par Prima Power - la CNC, le générateur laser et la structure mécanique - nous traitons avec une seule partie, qui nous assure un contrôle total du processus laser et une fiabilité maximale. Dès le début, le professionnalisme et les compétences qui caractérisent une entreprise comme Prima Power nous ont guidés dans l'utilisation de leurs systèmes, avec la certitude de toujours faire le bon choix pour répondre au mieux à nos besoins, sachant que nous pouvons toujours compter sur une large gamme de produits de qualité, compétitifs et performants. C'est exactement pour ces raisons que nous avons également choisi Prima Power pour fournir la nouvelle presse plieuse qui fera bientôt partie de notre parc de machines, plus précisément la presse plieuse hydraulique hP 1630, qui nous aidera à accroître notre compétitivité dans le domaine du pliage également. »
Avec ses délais considérablement réduits, la nouvelle Laser Genius+ nous a obligés à revoir notre processus de production pour pouvoir le suivre, ce qui, sur certains éléments, a même doublé notre capacité de production.
Vous recherchez une solution similaire pour votre entreprise ? Trouvez-le ici
Laser Genius+
MACHINES POUR LA DÉCOUPE LASER 2D