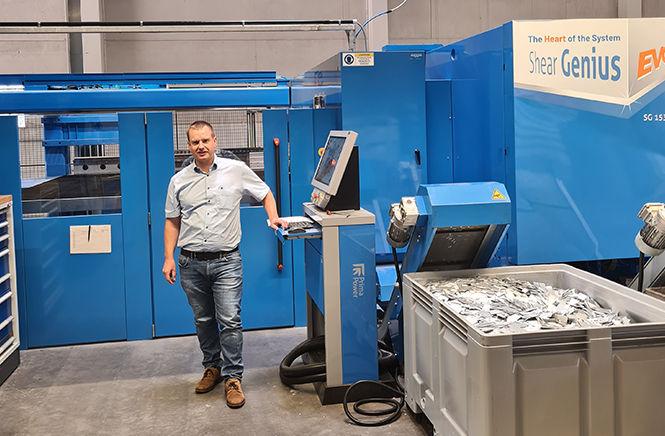
Dringenberg - Augmenter la capacité de production grâce à l'automatisation et à l'intégration
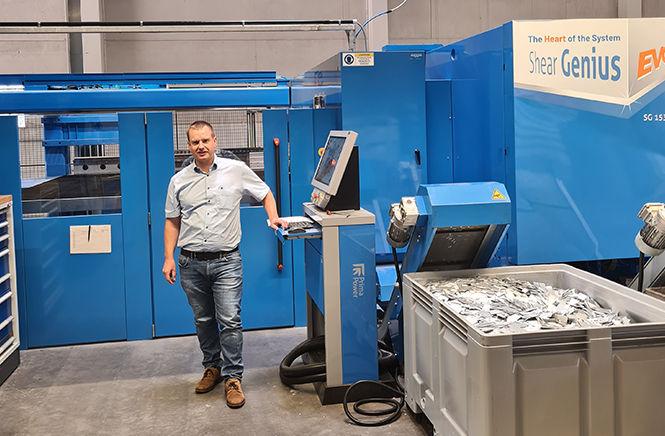
Le principal fabricant allemand a optimisé ses processus et obtenu une plus grande flexibilité grâce à la ligne PSBB entièrement automatisée et intégrée de Prima Power.
Dringenberg est l'une des entreprises à la croissance la plus rapide dans le domaine de la transformation de la tôle, se positionnant comme l'un des principaux fabricants allemands d'équipements pour les usines et les véhicules. Cette croissance remarquable repose sur une stratégie de production intelligente qui associe la plus haute qualité à une flexibilité maximale. Récemment, la société a réalisé un investissement stratégique dans une combinaison poinçonnage-pliage Prima Power, renforçant ainsi son engagement en faveur d'une fabrication de pointe.
Rationalisation des opérations : le voyage vers Prima Power pour l'optimisation des processus
Dringenberg est le centre de compétence pour l'équipement intelligent des ateliers et des véhicules au sein du groupe Würth. Son offre comprend des établis, des armoires, des rayonnages et des équipements d'ateliers mobiles. Dringenberg met l'accent sur les solutions individuelles personnalisées, qui posent des défis de production importants, en particulier pour l'équipement des véhicules. Compte tenu du grand nombre de types de véhicules et des exigences particulières des groupes de commerce, les dimensions des armoires, les configurations des tiroirs et les tailles des compartiments coulissants varient presque à l'infini.
"Grâce à un configurateur dédié, chaque client peut composer son propre mobilier", explique Heiko Stahl, directeur de la production chez Dringenberg. "Cela rend la préproduction de masse presque impossible pour notre entrepôt d'assemblage. Néanmoins, une rapidité maximale est requise, car le département d'assemblage a généralement besoin des pièces et des assemblages individuels un jour à l'avance."
Pour des raisons de poids, on traite principalement de l'aluminium d'une épaisseur comprise entre 0,8 et 2,0 mm. Comme l'esthétique joue un rôle crucial, les composants ne doivent pas présenter le moindre signe d'éraflure ou de rayure. Le matériau est généralement fourni avec un film, qui est retiré manuellement après le traitement.
Jusqu'à il y a quelques mois, le matériau était poinçonné par un employé sur une poinçonneuse et placé sur une palette. Un empileur le transportait ensuite jusqu'à la plieuse. Un autre ouvrier plaçait ensuite les feuilles poinçonnées dans la plieuse afin d'obtenir la forme souhaitée. Enfin, le film était retiré, préparant l'élément pour l'assemblage. L'équipe dirigée par Heiko Stahl souhaitait améliorer ce processus et a exploré d'autres solutions, ce qui lui a permis de découvrir Prima Power.
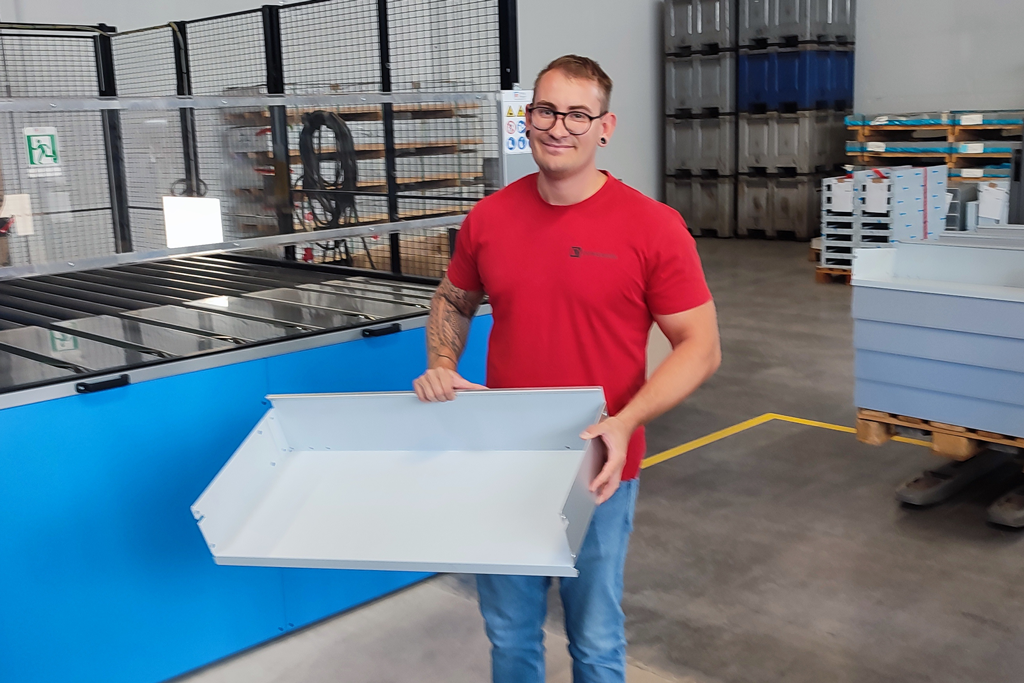
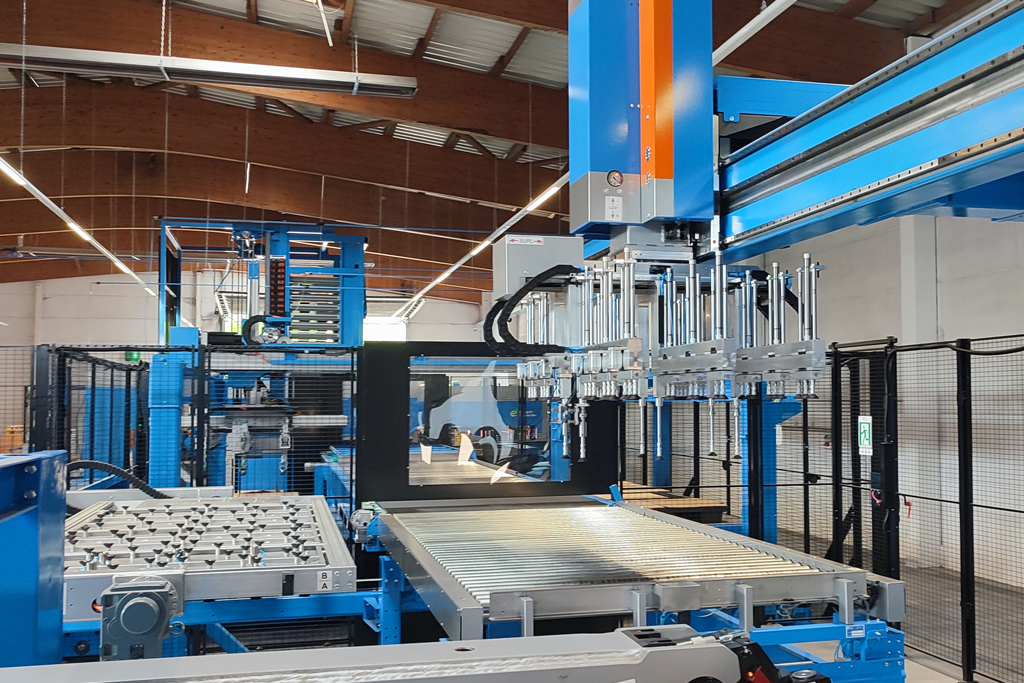

Réduire la main d'œuvre et améliorer le rendement avec la ligne PSBB servo-électrique de Prima Power
Dringenberg a opté pour Prima Power, l'un des principaux fournisseurs de machines laser et de tôlerie, qui propose la gamme de produits la plus complète du secteur : machines laser 2D et 3D, poinçonneuses et machines combinées poinçonnage/laser et poinçonnage/cisaillage, presses plieuses, panneauteuses et systèmes de fabrication flexibles. L'une des raisons principales du choix de Prima Power fut sa capacité à soutenir les clients avec des solutions efficaces d'automatisation de la production.
Avec une collaboration précedente positive avec Prima Power sur un autre site, la société a voulu travailler ensemble pour trouver une bonne solution. L'objectif était de réduire la main d'œuvre, de maximiser le rendement tout en augmentant la précision et la qualité de surface. La réponse a été une ligne PSBB (Punching, Shearing, Buffering, Bending) servo-électrique qui transforme automatiquement les tôles brutes en éléments pliés prêts à être installés.
"Notre précédente expérience positive avec Prima Power a été réaffirmée dans le cadre de ce projet. La collaboration et l'assistance de Prima Power ont été excellentes", déclare M. Stahl. Le point de départ est le système de stockage à tour de 20 palettes, qui permet de traiter des composants à partir d'une large gamme de matériaux qui peuvent être changés automatiquement sous le contrôle d'un programme. René Polz, chef de groupe pour cette ligne, réserve toujours un emplacement libre pour les rotations rapides, ce qui permet d'incorporer des tôles moins utilisées sans interruption.
Les tôles sont acheminées vers la cellule de poinçonnage/cisaillage Shear Genius, équipée d'une tourelle à 16 outils. Tous les outils destinés à la production en série s'y adaptent, ce qui élimine le réglage de ces pièces. D'autres avantages sont le destructeur de bandes de coupe intégré et la possibilité de paramétrage dans le système de contrôle. Des éléments qui ne diffèrent que par leurs dimensions, mais qui sont par ailleurs identiques, peuvent être créés en modifiant quelques paramètres, ce qui évite une programmation élaborée. La facilité d'utilisation et l'efficacité sont les caractéristiques exceptionnelles de l'ensemble de la ligne.
Après le cisaillage, les composants sont acheminés pour être mis en tampon et pliés ultérieurement dans une cellule de pliage automatique. Cette tâche est effectuée par un robot, offrant un degré élevé de flexibilité et permettant l'empilage automatique de pièces plus grandes. Le flux de matériau peut être conçu pour compenser les différents besoins en temps du poinçonnage et du pliage.
La tôle est soit transférée directement à la plieuse, soit stockée temporairement, soit introduite à partir de la zone de stockage intermédiaire. La plieuse intégrée donne la priorité à la productivité, à la qualité et à la répétabilité. Des essais sont en cours pour traiter les tôles sans film de protection, ce qui pourrait éliminer une autre étape chronophage.
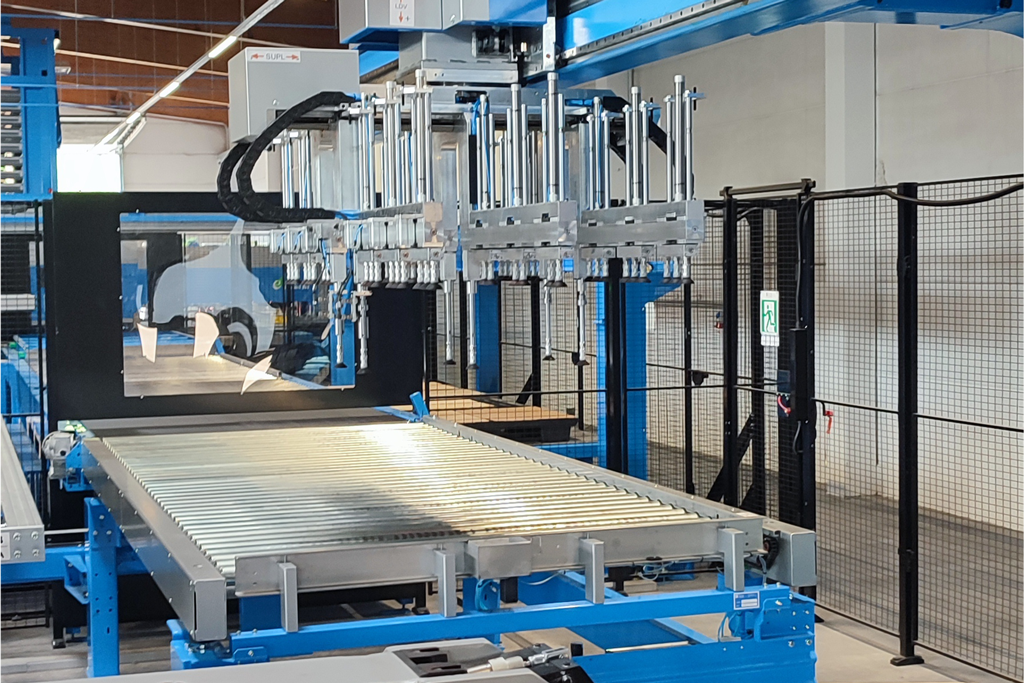
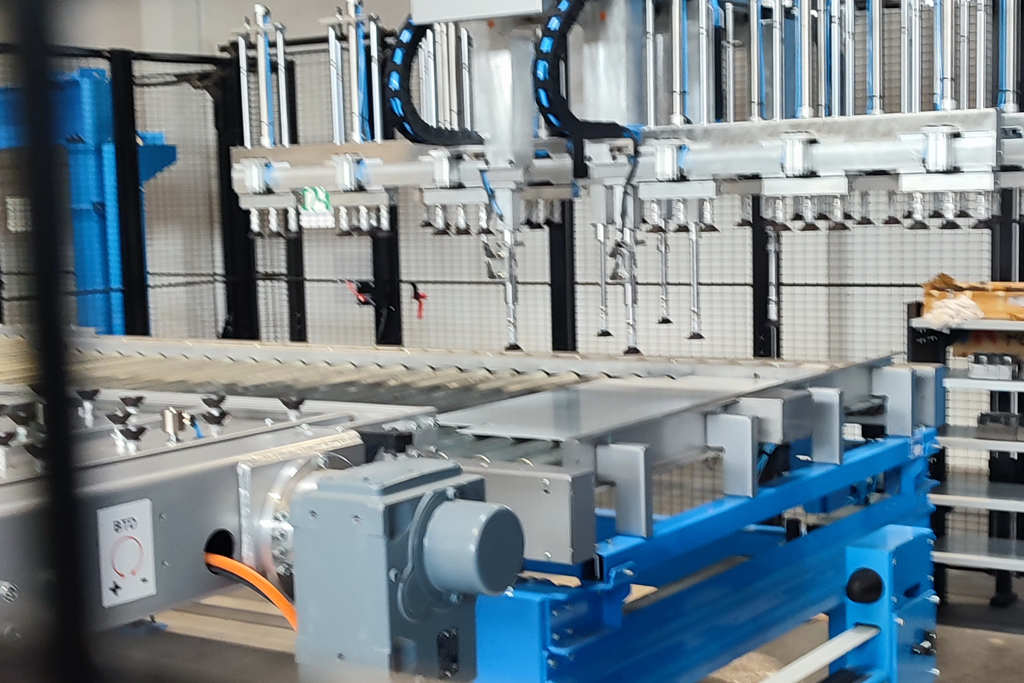
Augmentation de la productivité et de la flexibilité grâce à l'automatisation et à l'intégration complètes
"Avec cette solution, nous sommes passés d'une opération manuelle à un processus entièrement automatisé", explique M. Stahl. "Nous savions que tout ne fonctionnerait pas dès le départ, mais la collaboration et l'assistance de Prima Power ont été exceptionnelles. Depuis que les machines de poinçonnage-cisaillage et panneauteuses sont entièrement automatisées et intégrées dans une seule ligne, nous n'avons plus besoin de manutention supplémentaire. La pièce reste intacte jusqu'à ce que nous la déchargions et la palettisions. C'est la seule intervention de l'opérateur requise sur l'ensemble de la ligne".
Cette approche permet également de remédier à la pénurie de personnel qualifié. Un seul opérateur gère l'ensemble de la ligne, avec pour objectif de produire jusqu'à 400 pièces par équipe dans le cadre d'un fonctionnement fluide. La ligne fonctionne actuellement en deux équipes, mais elle pourra encore être exploitée sans surveillance par la suite. Ceci a augmenté de manière significative la capacité de production de Dringenberg, permettant de réduire le stock en entrepôt et d'améliorer la vitesse opérationnelle et la flexibilité. "Le système de Prima Power a considérablement augmenté notre flexibilité et notre productivité", conclut M. Stahl. Sur la base de cette expérience positive, Dringenberg poursuivra sa croissance aux côtés de Prima Power.
Notre précédente expérience positive avec Prima Power a été réaffirmée dans le cadre de ce projet. La collaboration et l'assistance de Prima Power ont été excellentes
Vous cherchez une solution similaire pour votre entreprise ? Découvrez-la ici
PSBB
SYSTÈMES DE FABRICATION FLEXIBLES