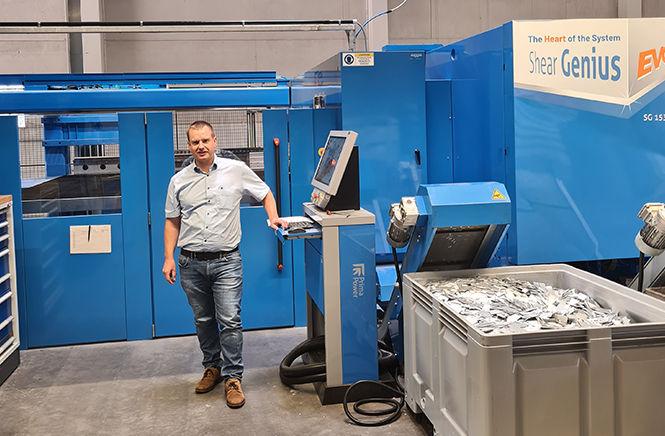
Dringenberg - Boosting production capacity through automation and integration
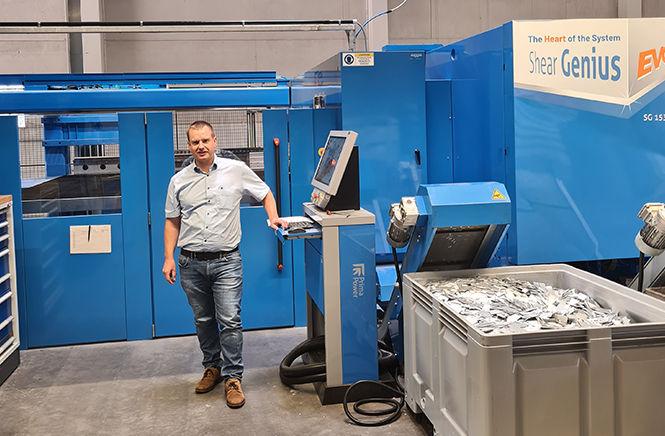
The leading German manufacturer optimized its processes and achieved higher flexibility thanks to Prima Power's fully automated and integrated PSBB line.
Dringenberg is one of the fastest growing companies in the sheet metal processing field, establishing itself as a leading German manufacturer of factory and vehicle equipment. This remarkable growth rests on an intelligent production strategy that combines the highest quality with maximum flexibility. Recently, the company made a strategic investment in a Prima Power punching-bending combination, strengthening its commitment to cutting-edge manufacturing.
Streamlining operations: the journey to Prima Power for process optimization
Dringenberg is the competence center for intelligent workshop and vehicle equipment within the Würth Group. Their offerings span workbenches, cabinets, shelving and mobile workshop equipment. Dringenberg places a strong focus on customized individual solutions, which pose major production challenges, especially for in-vehicle equipment. Given the large number of vehicle types and the special requirements of trade groups, cabinets dimensions, drawers configurations, and sliding compartments sizes vary almost infinitely.
“Through a dedicated configurator, each customer can put together his own special furnishings,” explains Heiko Stahl, production manager at Dringenberg. “This makes mass pre-production almost impossible for our assembly warehouse. Nevertheless, maximum speed is required, because the assembly department usually needs the individual parts and assemblies just one day in advance.”
For weight reasons, mainly aluminum with a thickness between 0.8 and 2.0 mm is processed. As aesthetics plays a crucial role, the components must not show any scratches or streaks. The material is usually supplied with a film, which is removed manually after processing.
Until a few months ago, the material was punched by an employee on a punching machine and placed on a pallet. A stacker then transported it to the bending machine. Subsequently, another worker placed the punched sheets into the bending machine to obtain the desired shape. Finally, the foil was removed, preparing the element for assembly. The team led by Heiko Stahl wanted to improve this process and explored alternatives, swiftly coming across Prima Power.
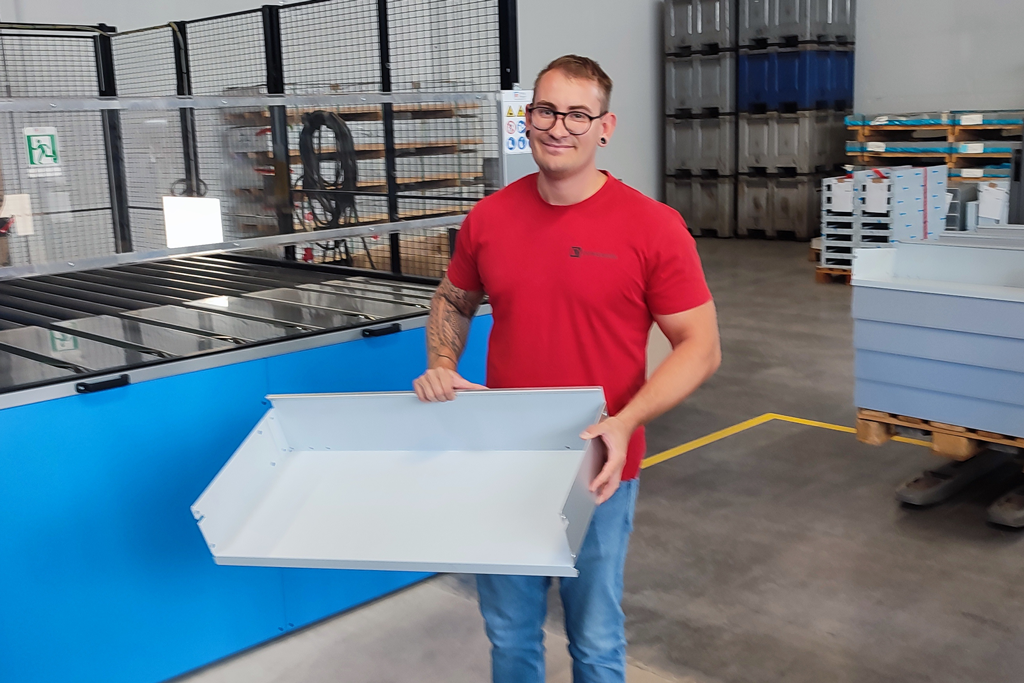
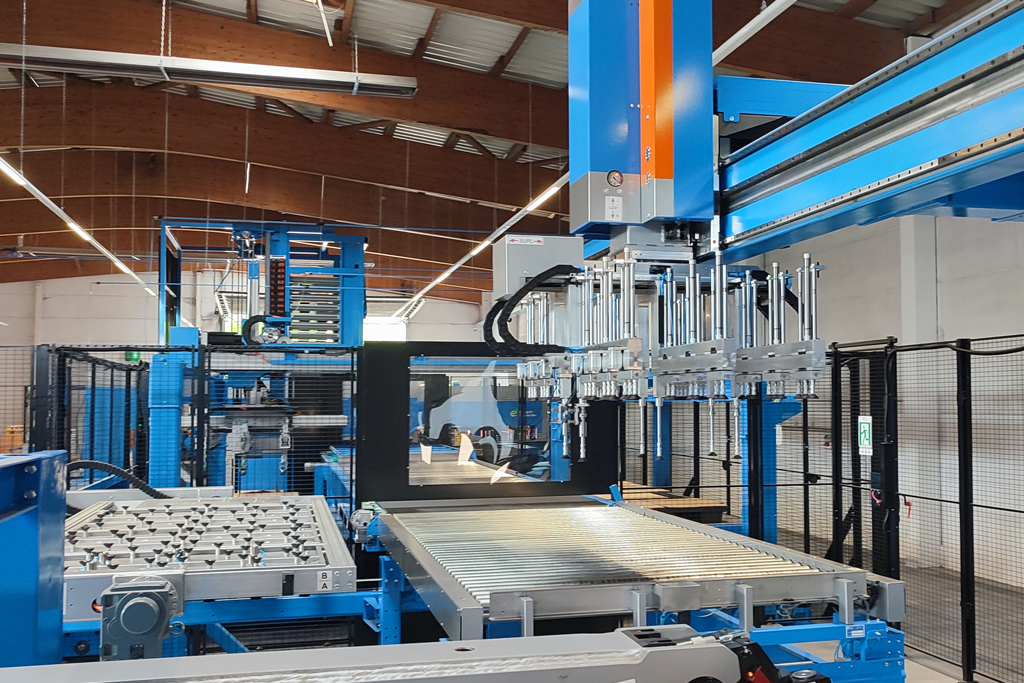

Reducing labor and enhancing throughput with Prima Power’s servo-electric PSBB line
Dringenberg opted for Prima Power, a leading supplier of laser and sheet metal machinery with the most comprehensive product range in the industry: 2D and 3D laser machines, punching and combined punching/laser and punching/shearing machines, press brakes, panel bender machines and flexible manufacturing systems. A key reason for choosing Prima Power was its ability to support customers with efficient production automation solutions.
With prior positive Prima Power collaboration at a different site, the company wanted to work together to find a good solution. The goal was to minimize labor, maximize throughput while increasing accuracy and surface quality. The answer was a servo-electric PSBB (Punching, Shearing, Buffering, Bending) line that fully automatically processes raw sheets into finished bent elements ready for installation.
"Our prior positive experience with Prima Power was reaffirmed through this project. The collaboration and assistance from Prima Power were excellent", declares Stahl. The starting point is the 20-pallet tower storage system, allowing the processing of components from a wide range of materials that can be automatically changed under program control. Rene Polz, the group leader for this line, always reserves a free spot for quick turnarounds, enabling the incorporation of less commonly used sheets without interruption.
Sheets move to a Shear Genius punching/shearing cell with a 16-tool turret. All tools for series production fit, eliminating setup for such parts. Further advantages are the integrated trim strip destroyer and the possibility of parameterization in the control system. Elements that differ only in their dimensions but are otherwise identical can be created by changing a few parameters, avoiding elaborate programming. Ease of use and efficiency are the outstanding features of the entire line.
After shearing, components are forwarded for buffering and subsequent bending in an automatic bending cell. This task is performed by a robot, offering a high degree of flexibility and enabling the automatic stacking of larger parts. Material flow can be designed to compensate for the different time requirements of punching and bending.
The sheet metal is either transferred directly to the bending machine, temporarily stored or fed in from the intermediate storage area. The integrated bending machine prioritizes productivity, quality and repeatability. Tests are underway to process sheets without protective foil, which could eliminate another time-consuming step.
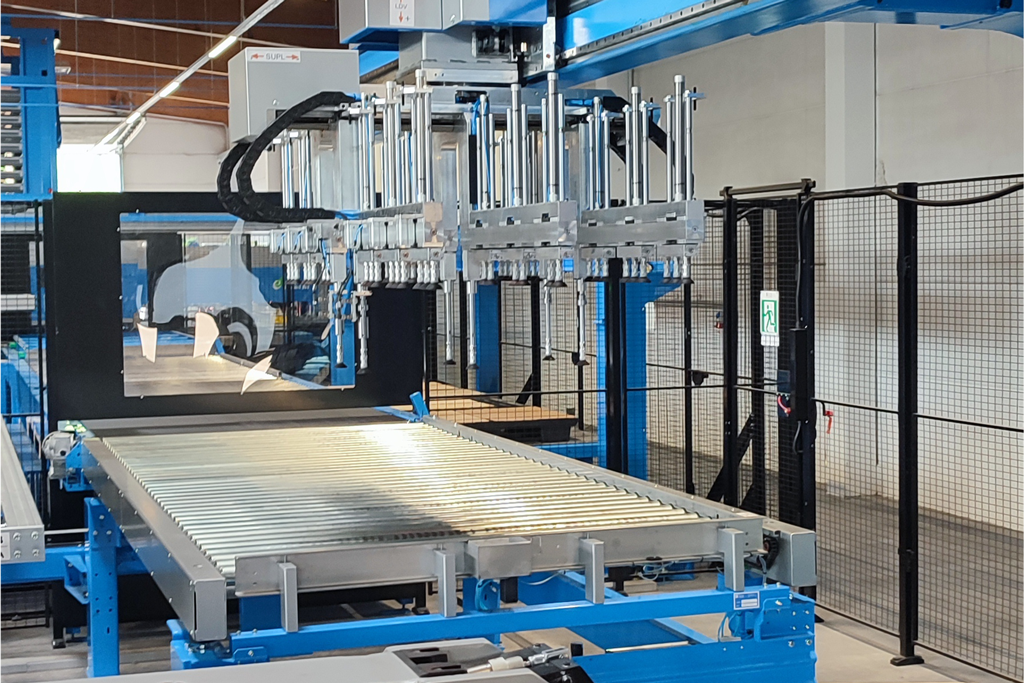
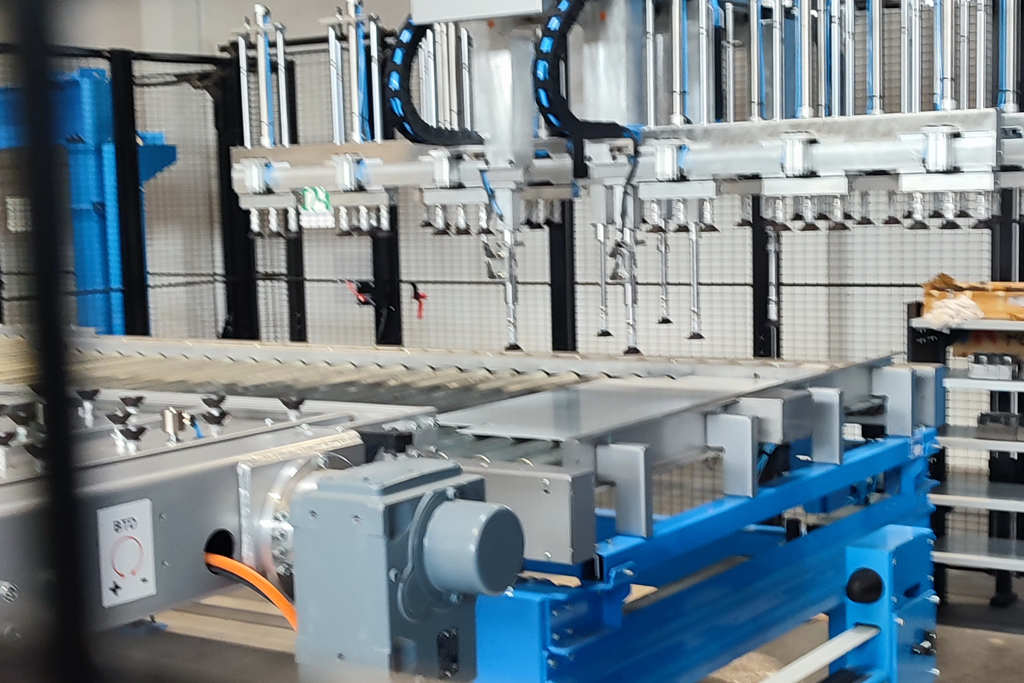
Increasing productivity and flexibility through full automation and integration
"With this solution we went from a manual operation to a fully automated process" explains Stahl. "We were aware that not everything would work right off the bat, but the collaboration and support from Prima Power were exceptional. Since the punching-shearing and panel bending machines are fully automated and integrated in one line, we no longer need any additional material handling. The workpiece remains untouched until we unload and palletize it. This is the only operator intervention required in the entire line."
This approach also addresses the shortage of skilled workers. Only one operator manages the entire line, aiming to produce up to 400 parts per shift under smooth operation. The line is currently running in 2-shift mode, but can still be operated completely unmanned afterwards. This has significantly increased Dringenberg's production capacity, allowing for reduced warehouse stock and enhanced operational speed and flexibility. "Prima Power’s system has significantly increased our flexibility and productivity", Stahl concludes. Based on this positive experience, Dringenberg will continue its growth course alongside Prima Power.
Our prior positive experience with Prima Power was reaffirmed through this project. The collaboration and assistance from Prima Power were excellent.
Are you looking for a similar solution for your company? Find it here
Dobrador expresso EBe
DOBRADORES DE PAINEL
Produtividade impulsionada ao máximo.
PSBB
SISTEMAS DE FABRICO FLEXÍVEIS