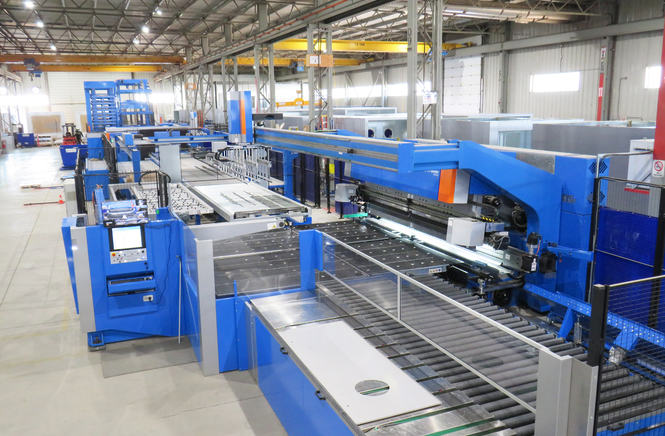
Scott Springfield Mfg, una soluzione compatta per il successo del cliente
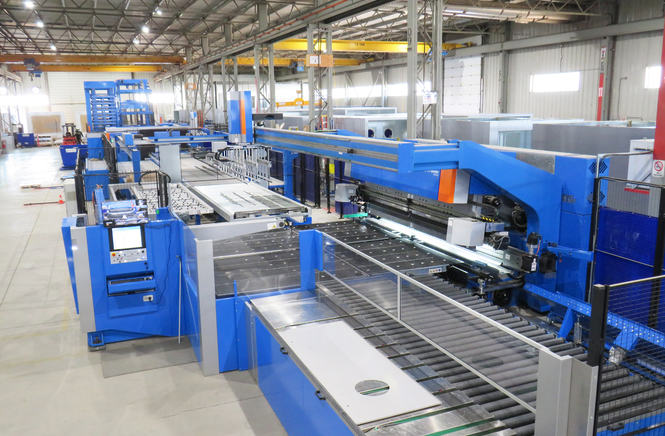
Scott Springfield Sfg, inc. a Calgary (Canada) è un fornitore leader di sistemi su misura per il trattamento dell'aria che sfrutta le più recenti tecnologie per offrire ai propri clienti una soluzione flessibile e costruita intorno alle loro esigenze.
Scott Springfield Mfg. lavora a stretto contatto con rappresentanti di vendita, proprietari di edifici, responsabili di impianto, tecnici e appaltatori per progettare pacchetti di trattamento dell’aria affidabili, sicuri ed efficienti dal punto di vista energetico, condividendo sempre la stessa filosofia su cui si basava l’azienda al momento della sua fondazione: sviluppare partnership di mercato, ottimizzare la progettazione delle apparecchiature, massimizzare le prestazioni, controllare i costi finali e fornire un prodotto di cui andare fieri. Secondo Nathan Smith, Direttore vendite e sviluppo aziendale, l’azienda fondata nel 1978 si dedicava principalmente a prodotti HVAC per le industrie ospedaliere e petrolifere in Alberta e Columbia Britannica.
“Oggi abbiamo notevolmente ampliato il nostro mercato e la nostra lista di clienti comprende strutture mediche di alto profilo, laboratori, strutture istituzionali, agenzie governative, data center, nonché organizzazioni industriali nel settore Oil&Gas, minerario, aerospaziale e ovunque siano richiesti materiali o requisiti speciali per il trattamento dell’aria”.
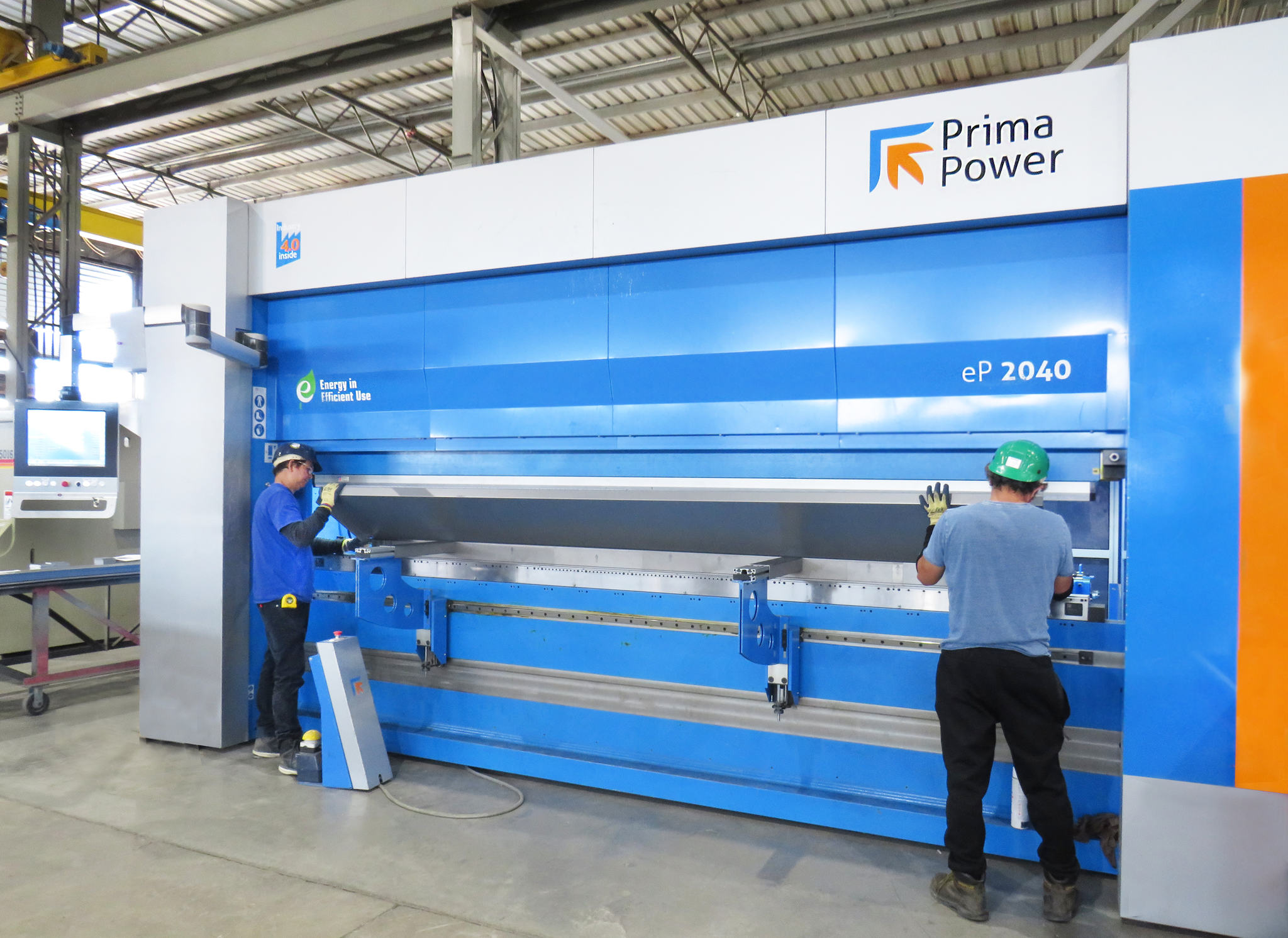
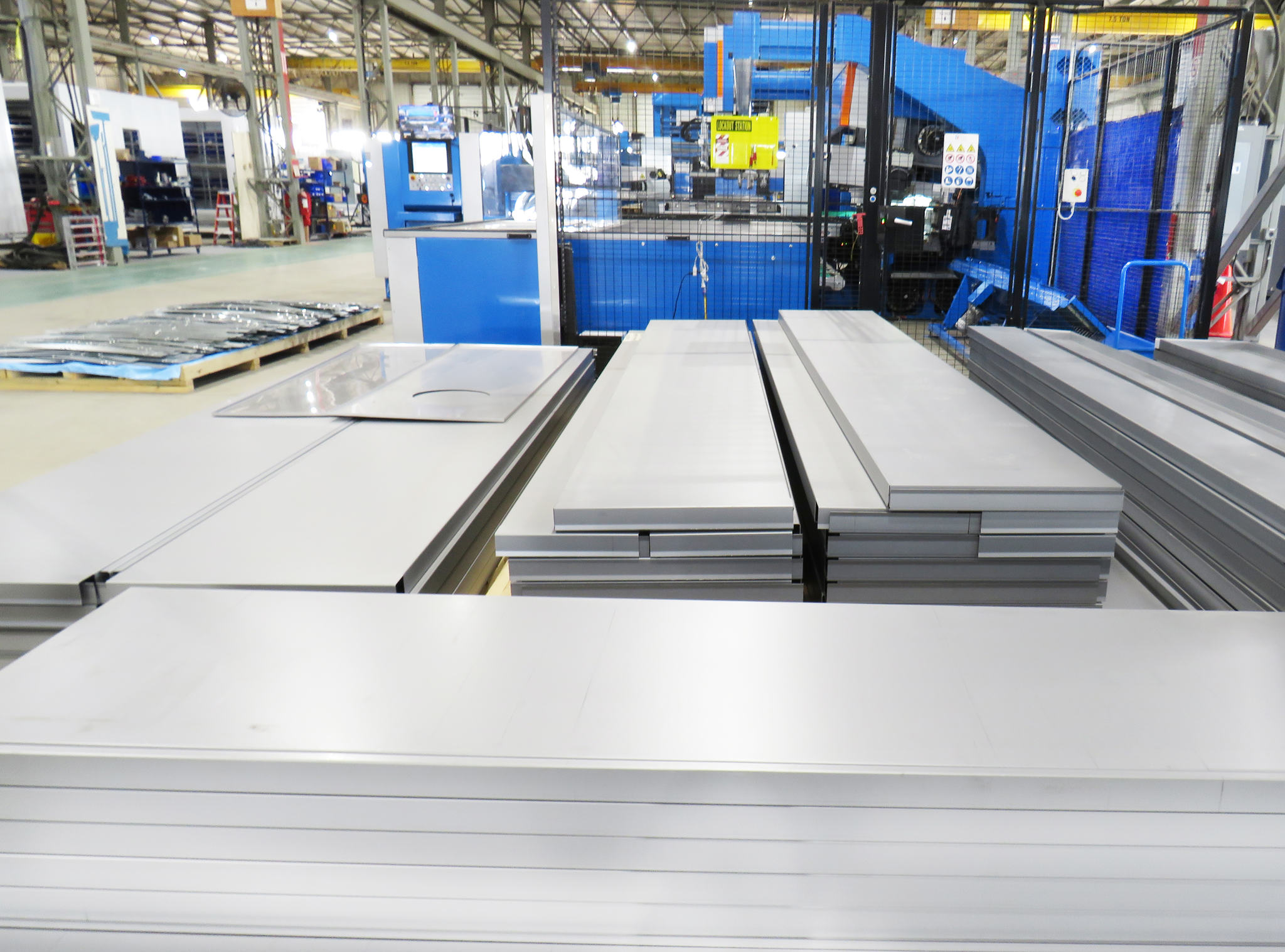
PRODUZIONE
I prodotti HVAC sono fabbricati in uno dei due stabilimenti di Calgary. Uno è di 18.580 metri quadrati mentre l’area di fabbricazione principale è di 13.470 metri quadrati. Nei due stabilimenti lavorano complessivamente 250 dipendenti. Nel corso degli anni, la fabbricazione ha potuto contare su unità di cesoiatura manuali, presse, punzonatrici, presse piegatrici e una pannellatrice. Tuttavia in occasione dell’ampliamento della seconda struttura nel 2021, la direzione ha deciso di automatizzare l’area di fabbricazione delle lamiere scegliendo PSBB, un sistema di produzione compatto e flessibile di Prima Power che combina punzonatura, cesoiatura, buffering e piegatura per trasformare automaticamente le lamiere grezze in componenti piegati di alta qualità. Il magazzino automatico consente la lavorazione di componenti da una varietà di materiali, che possono essere modificati automaticamente come programmato.
Le lamiere vengono trasferite alla cella di punzonatura/cesoiatura servoelettrica Shear Genius SGe. Dopo questa lavorazione, i componenti vengono inviati al buffering e alla successiva cella di piegatura automatica servoelettrica Express Bender. Grazie alla funzione di buffering, il flusso del materiale può essere organizzato con la massima flessibilità: trasferimento dei pezzi direttamente alla piegatura automatica, bilanciamento delle diverse esigenze di tempo di piegatura e punzonatura/cesoiatura, uscita dal sistema e introduzione di nuovo materiale al suo interno.
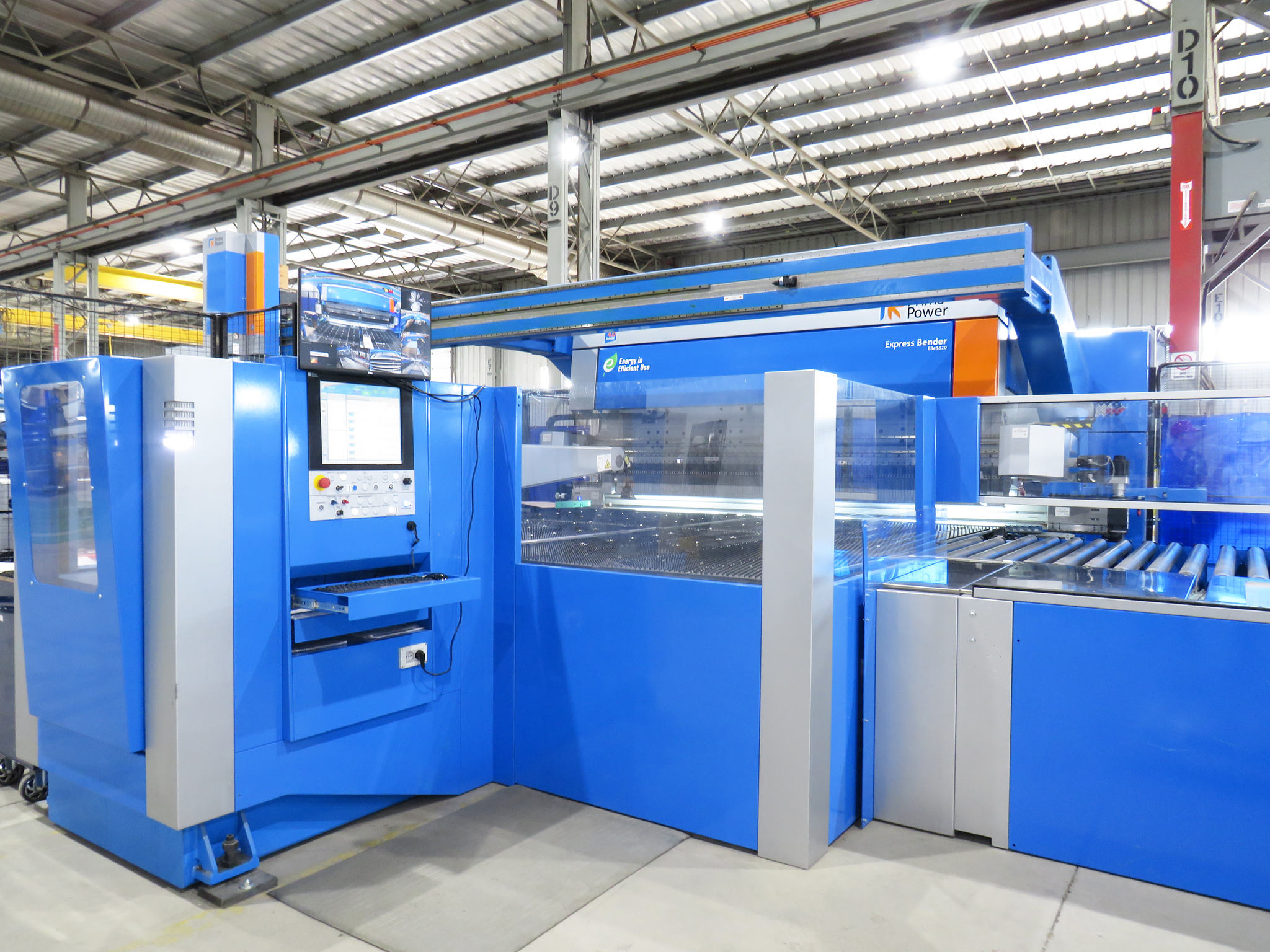
UNITÀ DI PUNZONATURA E CESOIATURA SERVO-ELETTRICA SHEAR GENIUS
SGe è in grado di eseguire i lavori più impegnativi con tempi di set-up minimi e operazioni non presidiate e automatizzate. Shear Genius aumenta la produttività del materiale attraverso programmi di nesting efficienti e versatili. Automazione di carico, punzonatura, formatura e upforming, scarico, smistamento e impilamento si traducono in una drastica riduzione degli scarti di materiale e del lavoro manuale, aumentando al contempo la produttività. Il robot di prelievo e impilamento (PSR) offre un’elevata flessibilità. I pezzi vengono sempre posizionati direttamente nella pila senza mai lasciarli cadere. Il PSR con funzioni di buffering consente la riorganizzazione e l’ottimizzazione del flusso di produzione da Shear Genius a EBe. L’SGe elimina gli scheletri inutili e le costose operazioni secondarie come la sbavatura. I bordi taglienti all’esterno del pezzo vengono eliminati grazie all’uso della cesoia angolare integrata. In SGe,
la lamiera viene caricata e squadrata automaticamente, senza operazioni manuali, garantendo la massima precisione dei pezzi.
“Abbiamo bisogno di precisione e velocità eccellenti per la punzonatura di più pannelli con molti fori”, afferma Javier Vazquez, direttore della produzione. “Impiegavamo 40 minuti per praticare i fori su un solo pannello. Con Shear Genius, ci bastano due minuti. Qualsiasi pezzo che possiamo automatizzare, ottenendo comunque una dimensione coerente e affidabile con la stessa qualità, lo
inseriamo immediatamente nella linea PSBB”.
SGe è in grado di eseguire i lavori più impegnativi con tempi di installazione minimi e operazioni non presidiate e automatizzate.
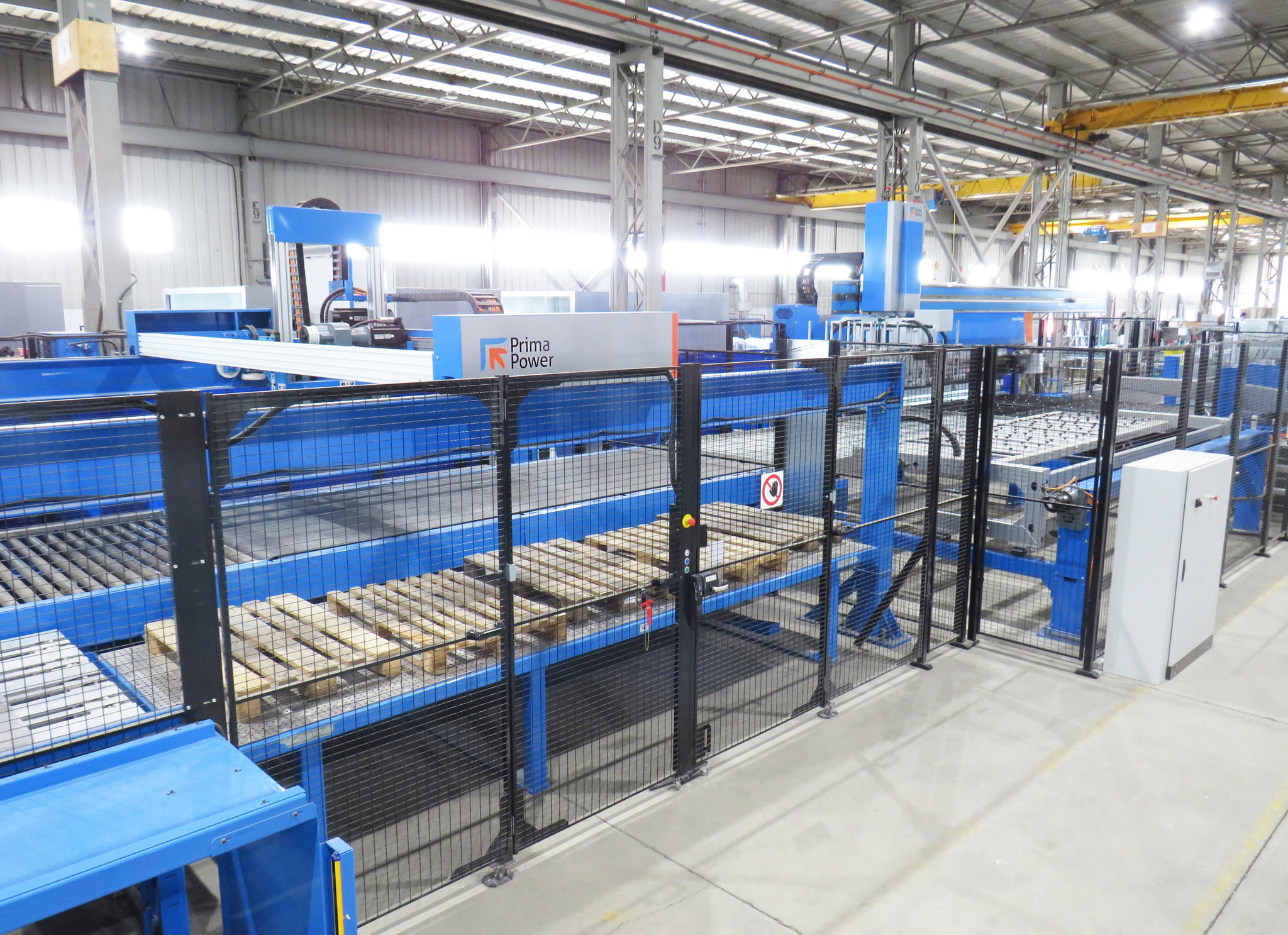
PIEGATURA SERVOELETTRICA
La pannellatrice servoelettrica EBe Express Bender è una soluzione di piegatura progettata specificamente per soddisfare i diversi requisiti di produzione e ottenere massima produttività, qualità e ripetibilità. L’operazione di piegatura è completamente automatizzata, dal caricamento delle lamiere punzonate allo scarico del prodotto finito. EBe di Prima Power offre la massima qualità di piegatura richiesta nelle applicazioni più impegnative.
“L’efficienza offerta da EBe ci consente di svolgere un lavoro che richiederebbe 10 ore su una pressa piegatrice manuale in una sola ora”, afferma Vazquez. “Prevediamo che questo rapporto 10 a 1 sarà ulteriormente ottimizzato man mano che acquisiremo maggiore esperienza con la macchina”.
“Produciamo centinaia di pannelli con EBe e tutti hanno la stessa qualità”, aggiunge Byron Paegel, supervisore della produzione.
Scott Springfield ha inoltre acquistato una pressa piegatrice servoelettrica Prima Power eP. Questa presenta il vantaggio di un’elevata accelerazione e decelerazione, nonché tempi di risposta rapidi del sistema di azionamento servoelettrico.
L’efficienza offerta da EBe ci consente di svolgere un lavoro che richiederebbe 10 ore su una pressa piegatrice manuale in una sola ora.
Rispetto alle presse piegatrici convenzionali, può aumentare notevolmente la produttività e ridurre i tempi ciclo di almeno il 30%.
“Fabbrichiamo alcuni pezzi che vengono semplicemente punzonati e tranciati per poi essere piegati manualmente sulla pressa piegatrice data la dimensione dei componenti”, spiega Vazquez.
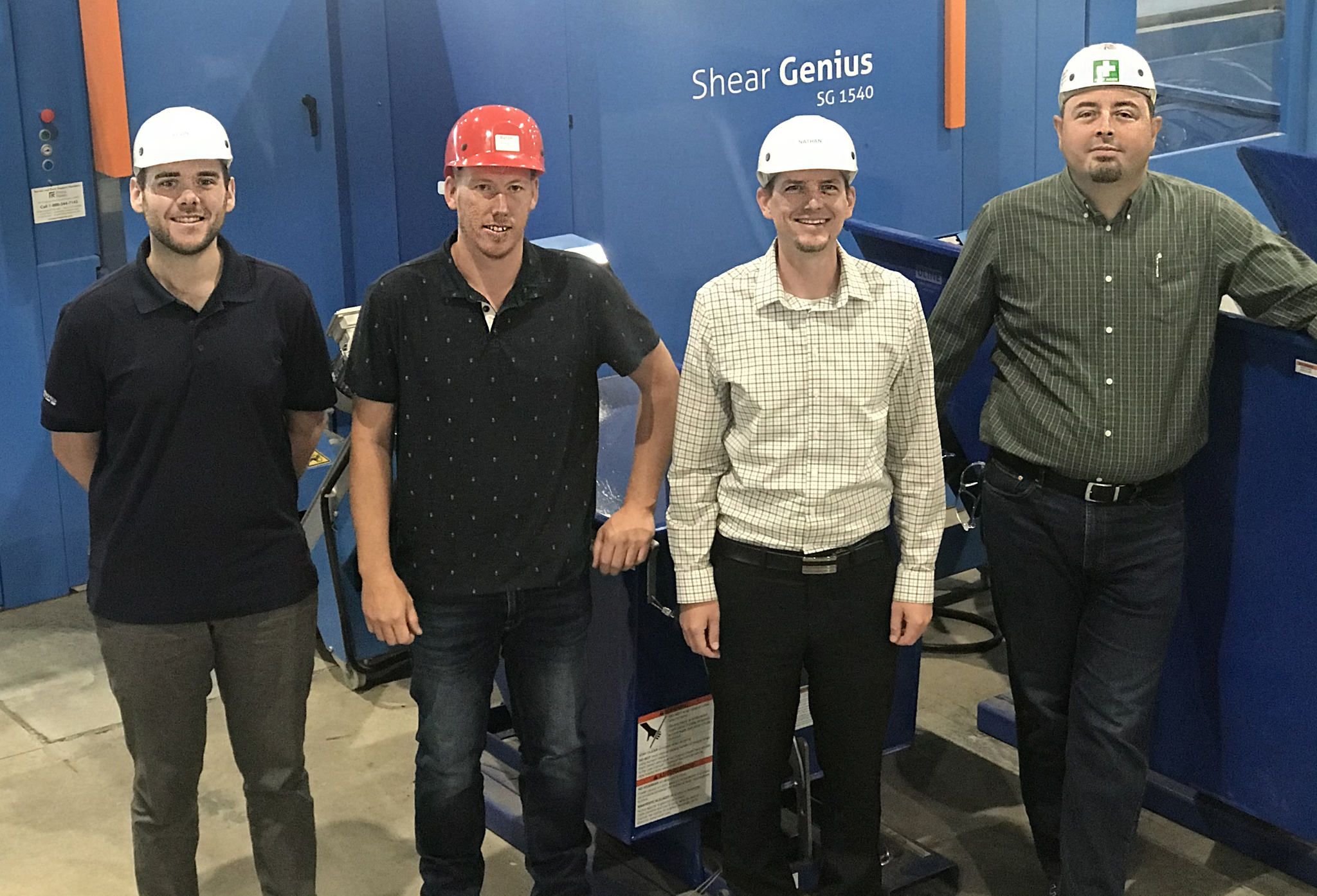
NUOVA SFIDA DI MERCATO
“L’opportunità di penetrare in nuovi mercati richiedeva molta più capacità di quella che avevamo prima dell’acquisto di PSBB”, spiega Vazquez. “La linea automatizzata Prima Power ci ha permesso di aumentare la nostra produzione per far fronte a questa sfida e disporre comunque di ulteriore produttività con una sola linea”.
“L’ingombro a terra è stata un’altra decisione critica”, aggiunge Smith. “Ogni prodotto che produciamo è personalizzato e varia in termini di layout e dimensioni, fino a 393 x 111 cm. Tutti questi processi separati occupano molto spazio. La compattezza di PSBB ci ha davvero aiutato a ridurre l’ingombro lasciandoci lo spazio per la produzione di più unità”.
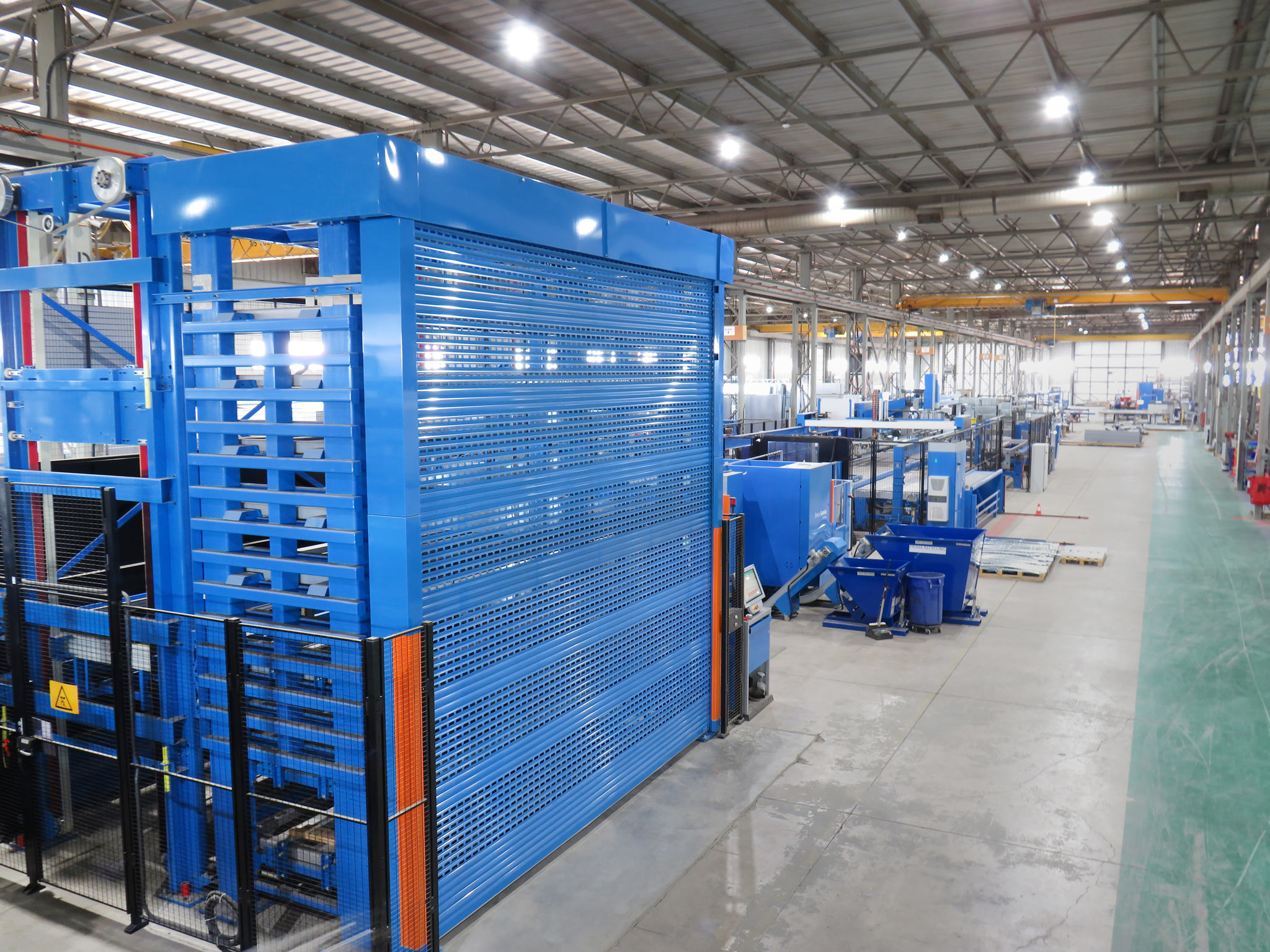
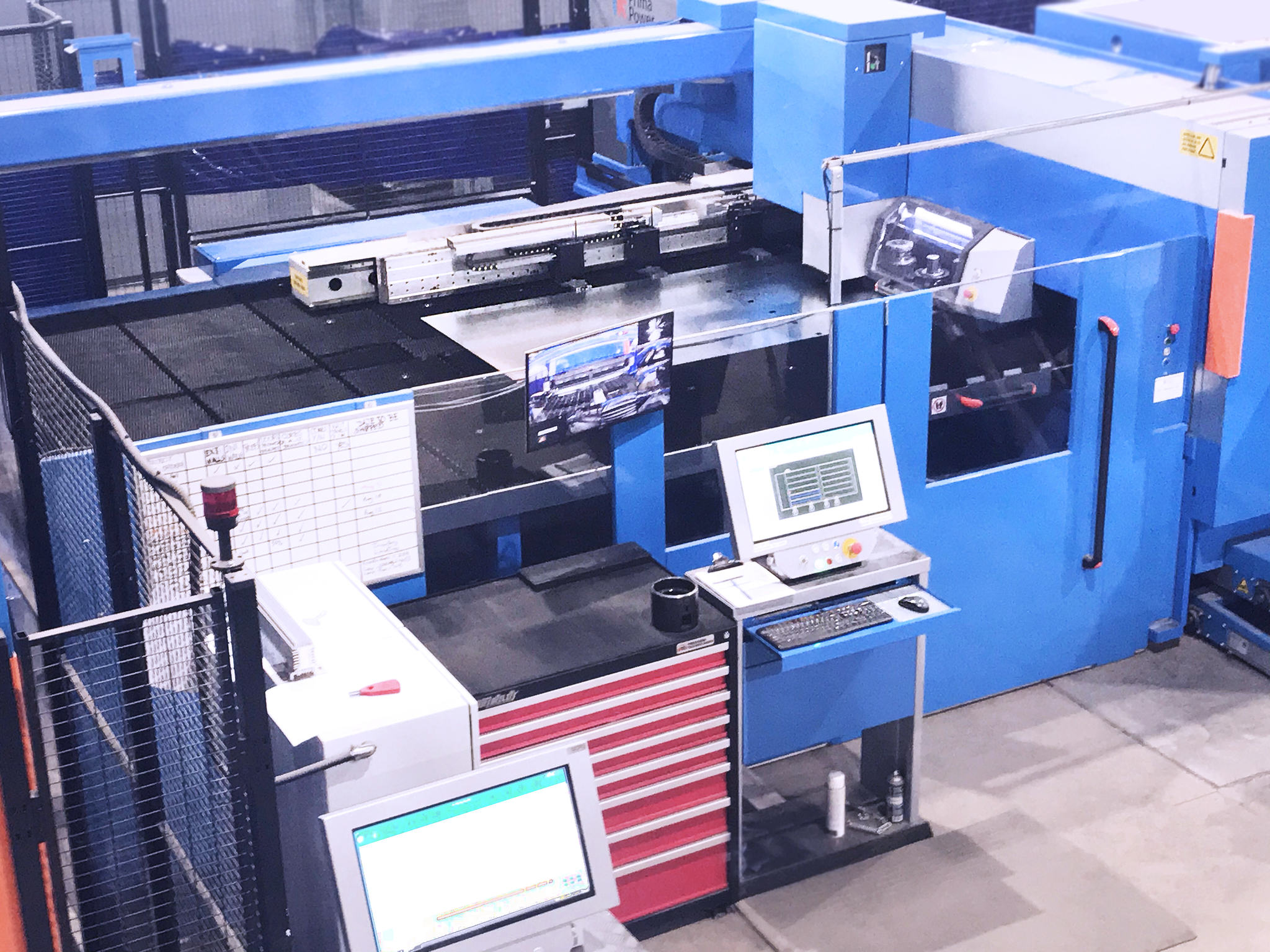
FORMAZIONE E ASSISTENZA
“La formazione e l’assistenza di Prima Power sono state eccezionali”, conclude Paegel. “I tecnici sono competenti e disponibili. Quando contatti l’assistenza, ti rispondono indirizzandoti subito alla persona giusta. Risolvi il problema e torni rapidamente a essere operativo”.
IL RISULTATO
“L’automazione di PSBB ci ha permesso in un primo momento di raddoppiare la nostra capacità, arrivando alla fine a triplicare la nostra produzione“, conclude Vazquez. “Ci consentirà inoltre di acquisire più quote di mercato e di servire meglio i nostri clienti, oggi e in futuro”.
"L’automazione è davvero la via del futuro nella produzione" sottolinea Kevin Whittaker, designer. “I nostri operatori possono migliorare professionalmente imparando a utilizzare macchine come Shear Genius ed EBe”.
“La linea PSBB ha sostenuto la nostra crescita e migliorato i nostri profitti”, afferma Smith. “Non solo ha influenzato la creazione dei pannelli, ma ha eliminato anche ulteriori necessità di taglio e di layout lungo la linea”. “La linea PSBB è diventata un punto di riferimento per Scott Springfield”, osserva Paegel. “Quando i nostri clienti vedono la linea PSBB, sorridono osservando la trasformazione da lamiera a pezzo perfettamente piegato alla fine della linea”.
La linea automatizzata Prima Power ci ha permesso di aumentare la nostra produzione per far fronte a questa sfida e disporre comunque di ulteriore produttività con una sola linea.