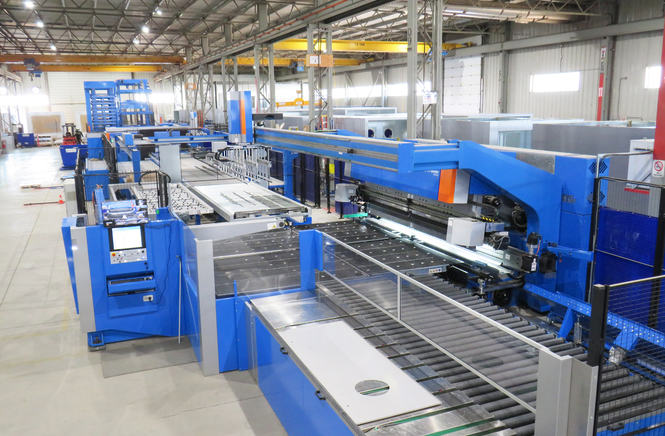
Scott Springfield Mfg, a compact solution for customer success
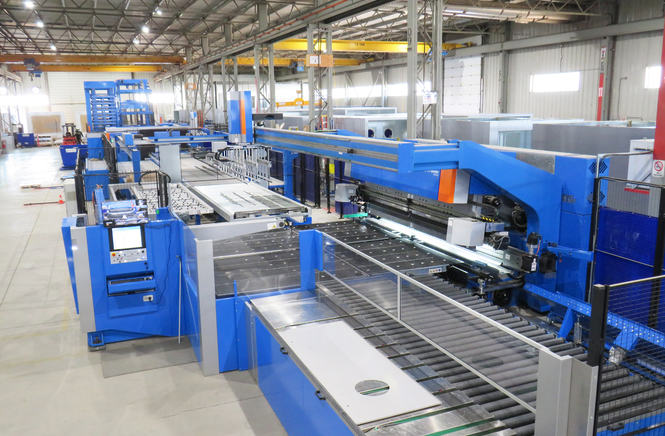
Scott Springfield Sfg, inc. in Calgary, Canada, is a leading supplier of custom air handling systems, utilizing the latest technologies to provide its customers with a flexible solution to their air handler needs.
Scott Springfield Mfg. works closely with sales representatives, building owners, facility managers, engineers, and contractors to design reliable, safe, and energy-efficient air handling packages. Always following the same philosophy upon which the company was founded: Develop market partnerships, optimize equipment design, maximize performance, control final cost, and deliver a product you can be proud of.
According to Nathan Smith, director of sales & business development, the company was founded in 1978, primarily for HVAC products for the hospital and oil industries in Alberta and British Columbia.
“Today, we have greatly expanded our market and our client list includes high-profile medical facilities, laboratories, institutional facilities, government agencies, data centers, as well as industrial organizations in oil and gas, mining, aerospace, and anywhere special materials or special requirements are needed on the air handling side.”
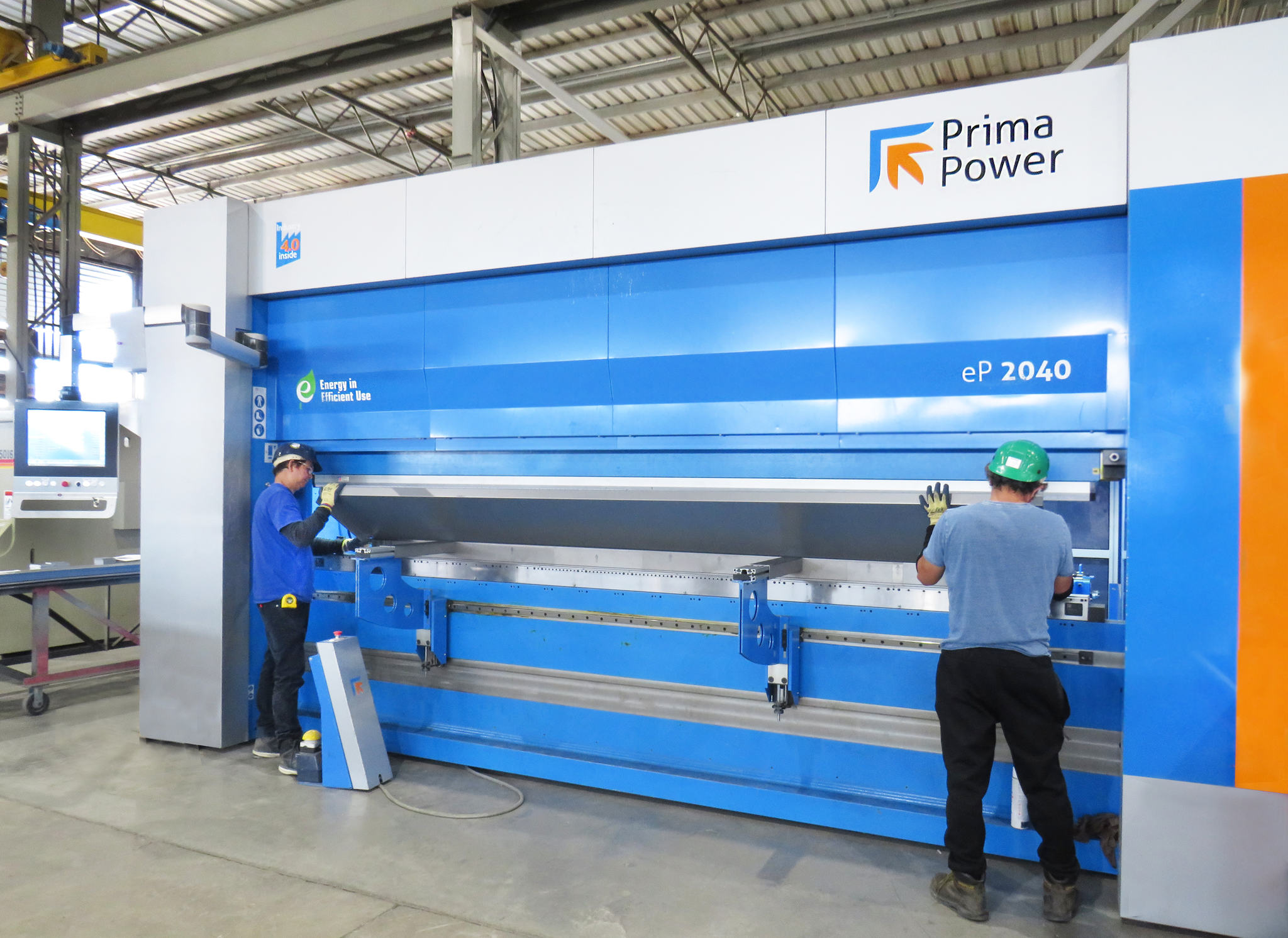
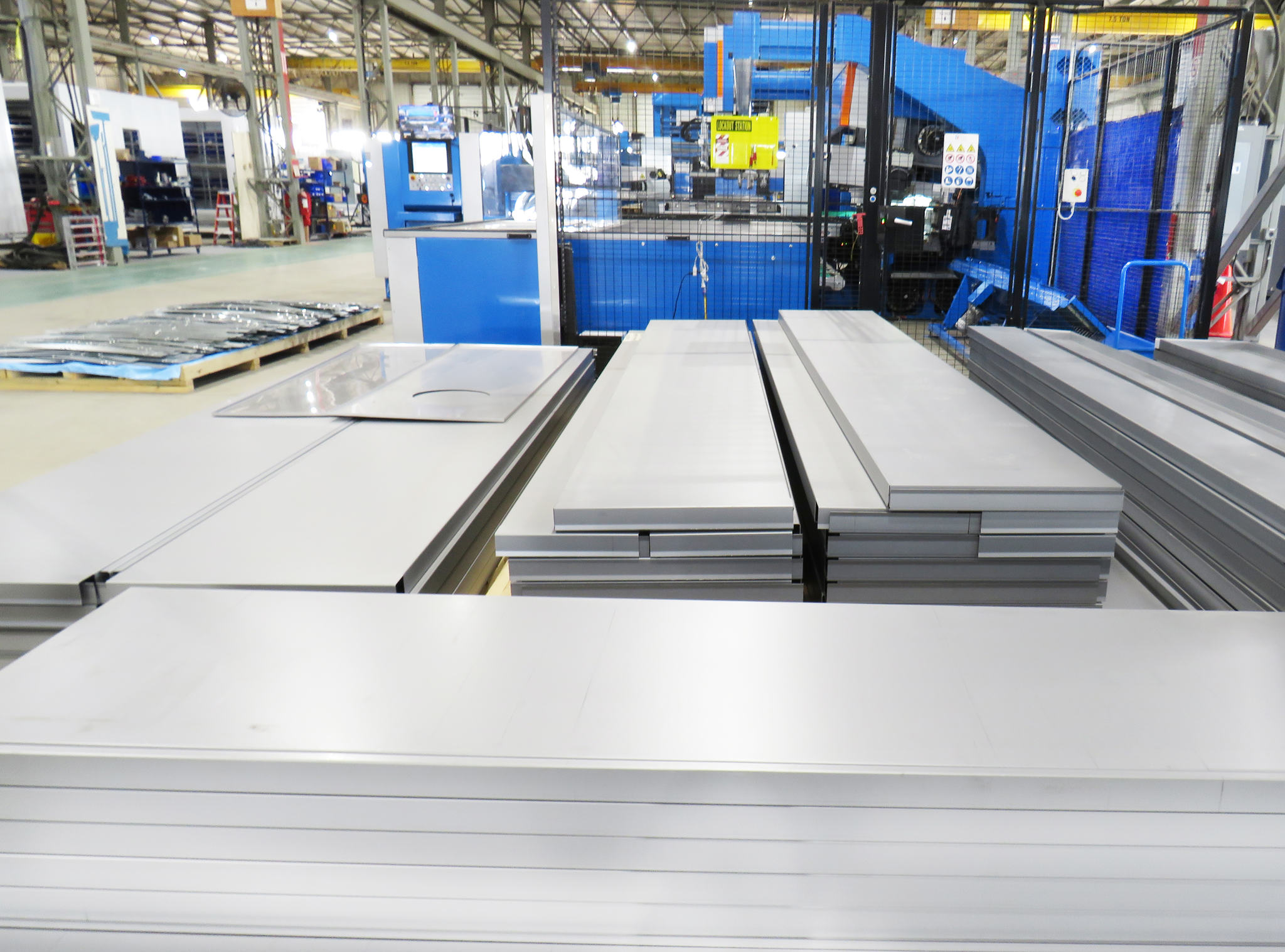
MANUFACTURING
The HVAC products are manufactured in one of the two facilities in Calgary. One is 120,000 square feet and the other, the main fabrication area, is 145,000 square feet. A total of 250 employees work in the two facilities. Over the years, the fabrication equipment has included manual shears, presses, notching machines, press brakes, and a panel bender. However, when expanding the second facility in 2021, management decided to automate the sheet metal fabrication area and chose the PSBB: a compact, flexible manufacturing system from Prima Power that combines punching, shearing, buffering, and bending to process blank sheets into readybent, high-quality components automatically. The combo storage allows processing of components from a variety of materials, which can be changed, as programmed, automatically. The sheets are transferred into a Shear Genius SGe servo-electric punch/shear cell. After shearing, the components are sent to buffering and subsequent bending in an Express Bender automatic servo-electric bending cell. With the buffering function material flow can be arranged in flexible ways to transfer parts directly to automatic bending, to balance the different time requirements of bending and punching/shearing, to exit material from the system and to bring new material into it.
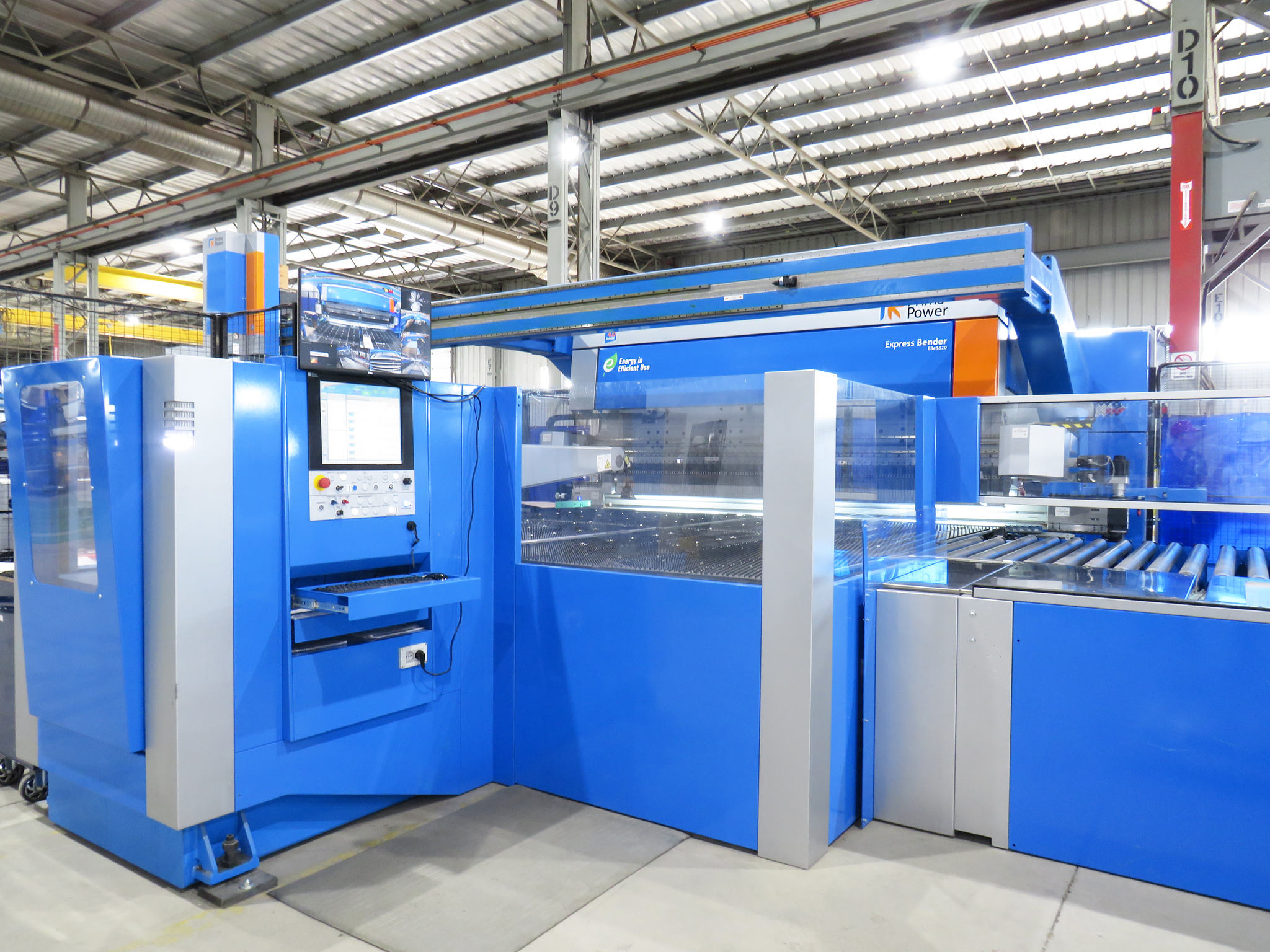
SERVO-ELECTRIC SHEAR GENIUS
The SGe is able to perform the most demanding jobs with minimal set-up times and lights-out unmanned operations. Shear Genius increases material productivity through efficient and versatile nesting programs. Automating loading, punching, forming and upforming, unloading, sorting, and stacking results in a dramatic reduction in material scrap and manual labor while increasing productivity. The picking and stacking robot (PSR) provides high flexibility. Parts are always placed directly to the stack and never dropped. The PSR with buffering functions allows reorganization and optimization of production flow from the Shear Genius to the EBe. The SGe eliminates wasteful skeletons and costly secondary operations such as deburring. Nibble edges on the part exteriors are eliminated through the use of the integrated right-angle shear. In the SGe, the sheet is loaded and squared automatically, without manual operations, ensuring very accurate parts.
“We need excellent accuracy and speed on punching multiple panels with many holes,” says Javier Vazquez, manufacturing director. “On one panel it used to take us 40 minutes to drill the holes. On the Shear Genius it takes two minutes. Any part that we can automate and still have a consistent and reliable dimension with the same quality, we immediately put on the PSBB.”
The SGe is able to perform the most demanding jobs with minimal set-up times and lights-out unmanned operations.
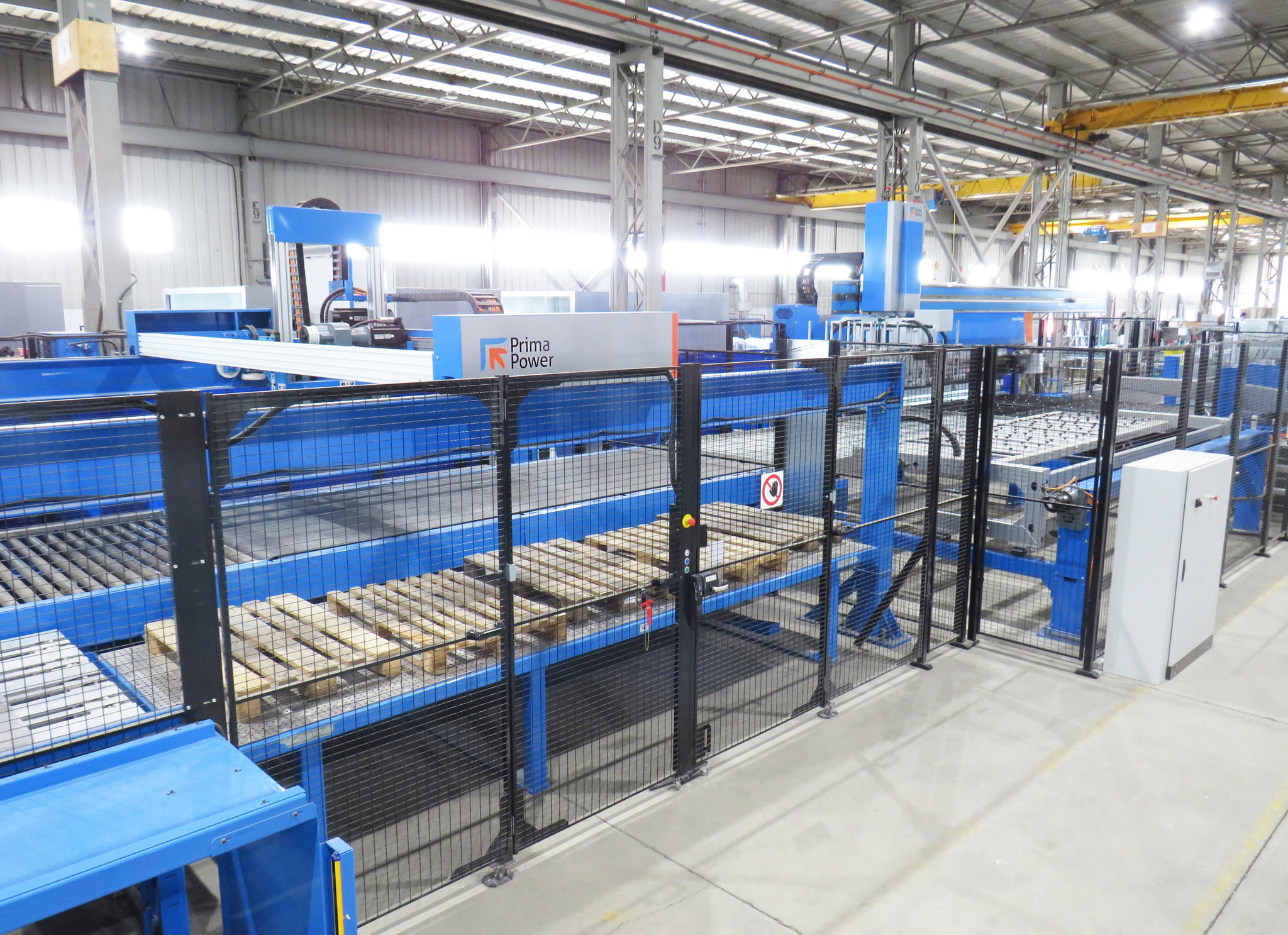
SERVO-ELECTRIC BENDING
The EBe servo electric Express Bender is a bending solution designed specifically for each fabricator’s production requirements to achieve maximum productivity, quality, and repeatability. The bending operation is fully automated, from the loading of flat punched parts to unloading of the finished product. Prima Power EBe provides the high bending quality required in demanding applications. “The efficiency of the EBe allows us to take a job that would require 10 hours on a manual press brake and complete it in one,” says Vazquez. “We expect this 10 to 1 ratio to rise much higher with additional experience on the machine.”
“We produce hundreds of panels on the EBe and they all come out with the same quality,” adds Byron Paegel, production supervisor.
Scott Springfield also purchased a Prima Power eP servo-electric press brake. The eP-Brake features the advantages of high acceleration, deceleration, and fast response times of the servoelectric drive system. Compared to conventional brakes, it can considerably increase productivity and reduce cycle times by 30% and more.
“We fabricate some parts that just get punched and sheared and then manually bent on the press brake due to the size of the components,” explains Vazquez.
The efficiency of the EBe allows us to take a job that takes 10 hours on a manual press brake and complete it in one.
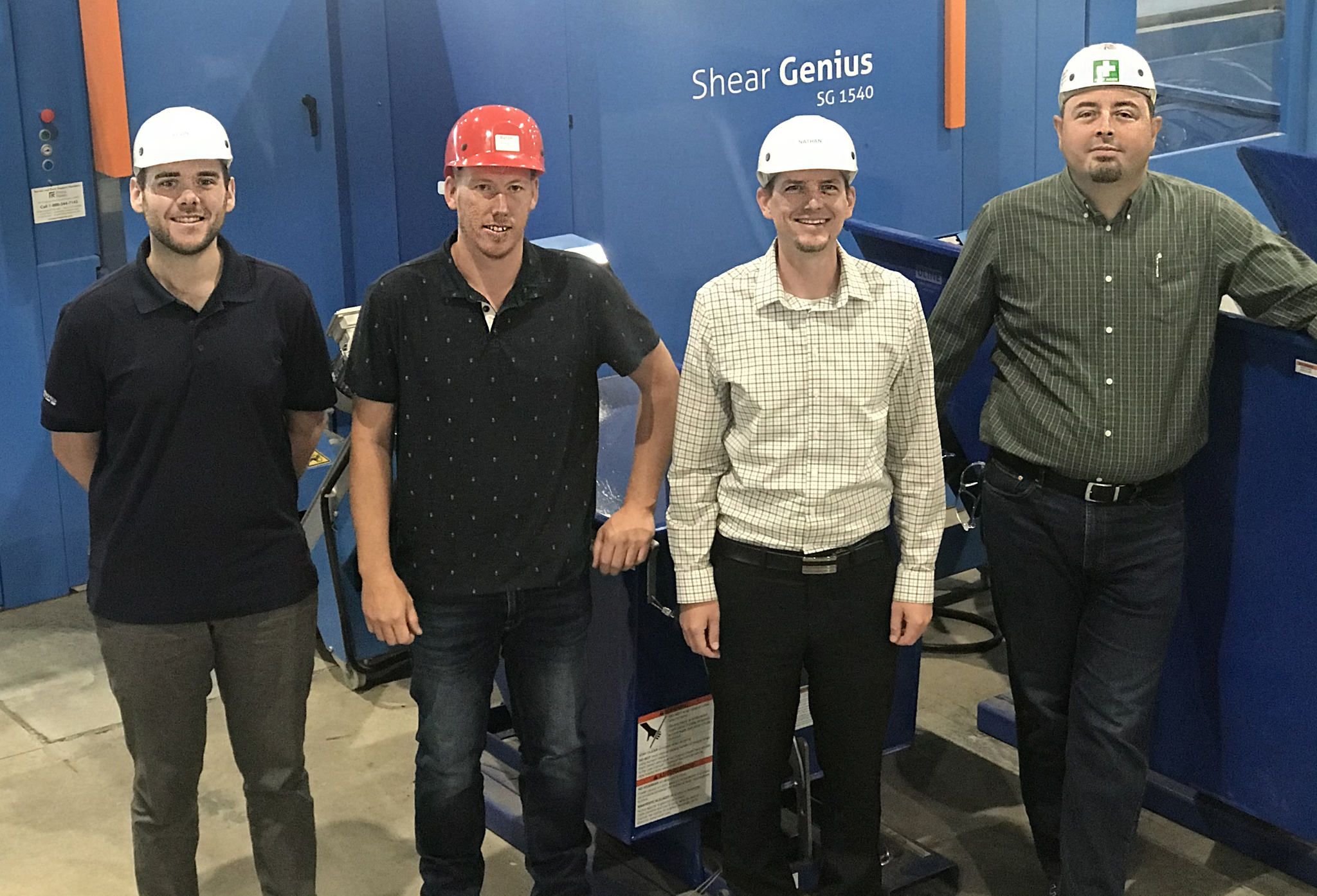
NEW MARKET CHALLENGE
“The opportunity to enter new markets required much more capacity than we had prior to our purchase of the PSBB,” explains Vazquez. “The automated Prima Power line allowed us to increase our production to meet this challenge and still have additional capacity with just one line.”
“Floor space was another critical decision we had,” adds Smith. “Every product we manufacture is custom and varies in layout and size – up to 150’ x 44’. All those separate processes take up a lot of floor space. The PSBB’s compact footprint really helped us shrink that down and gave us the area to build more units.
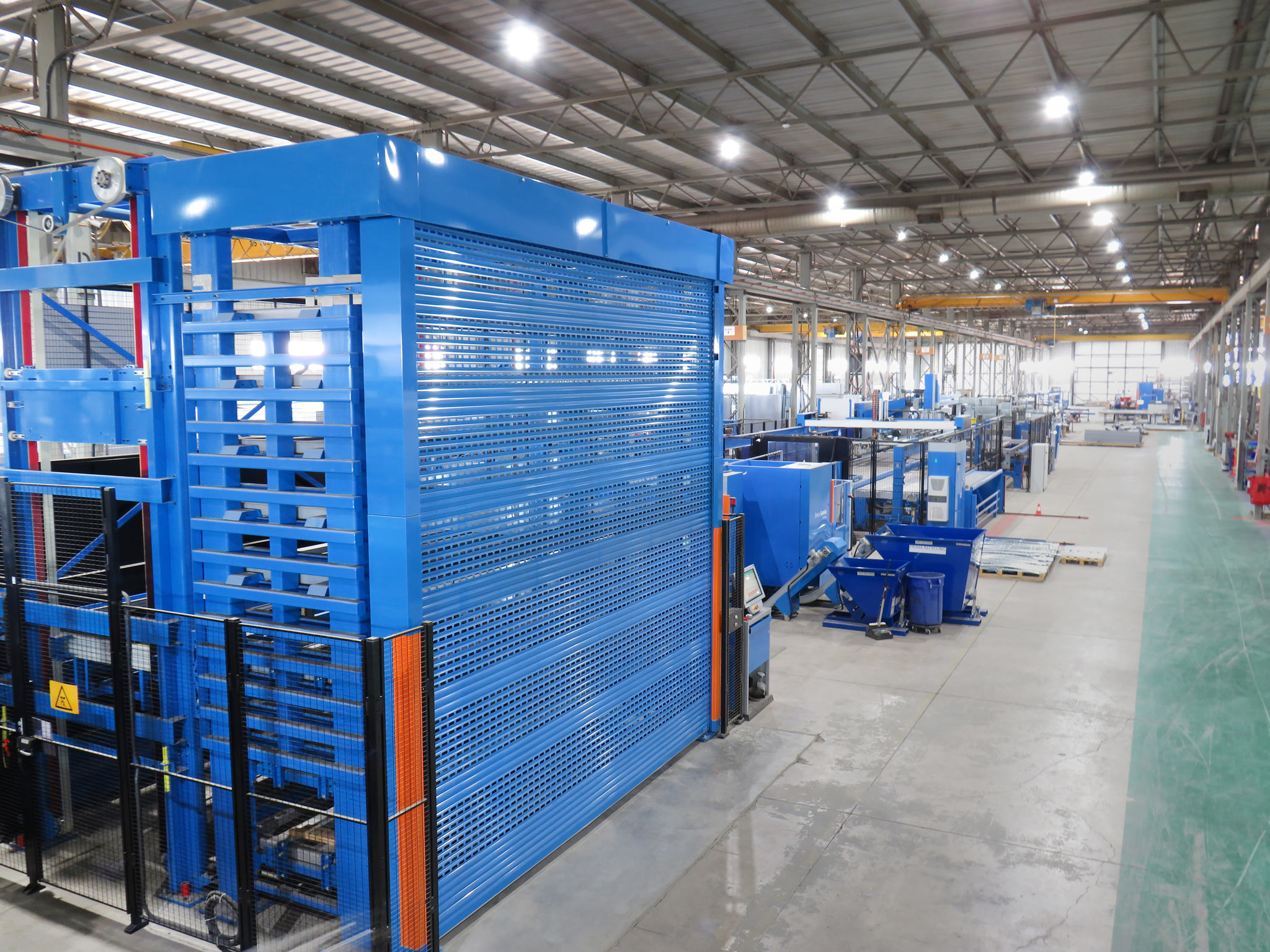
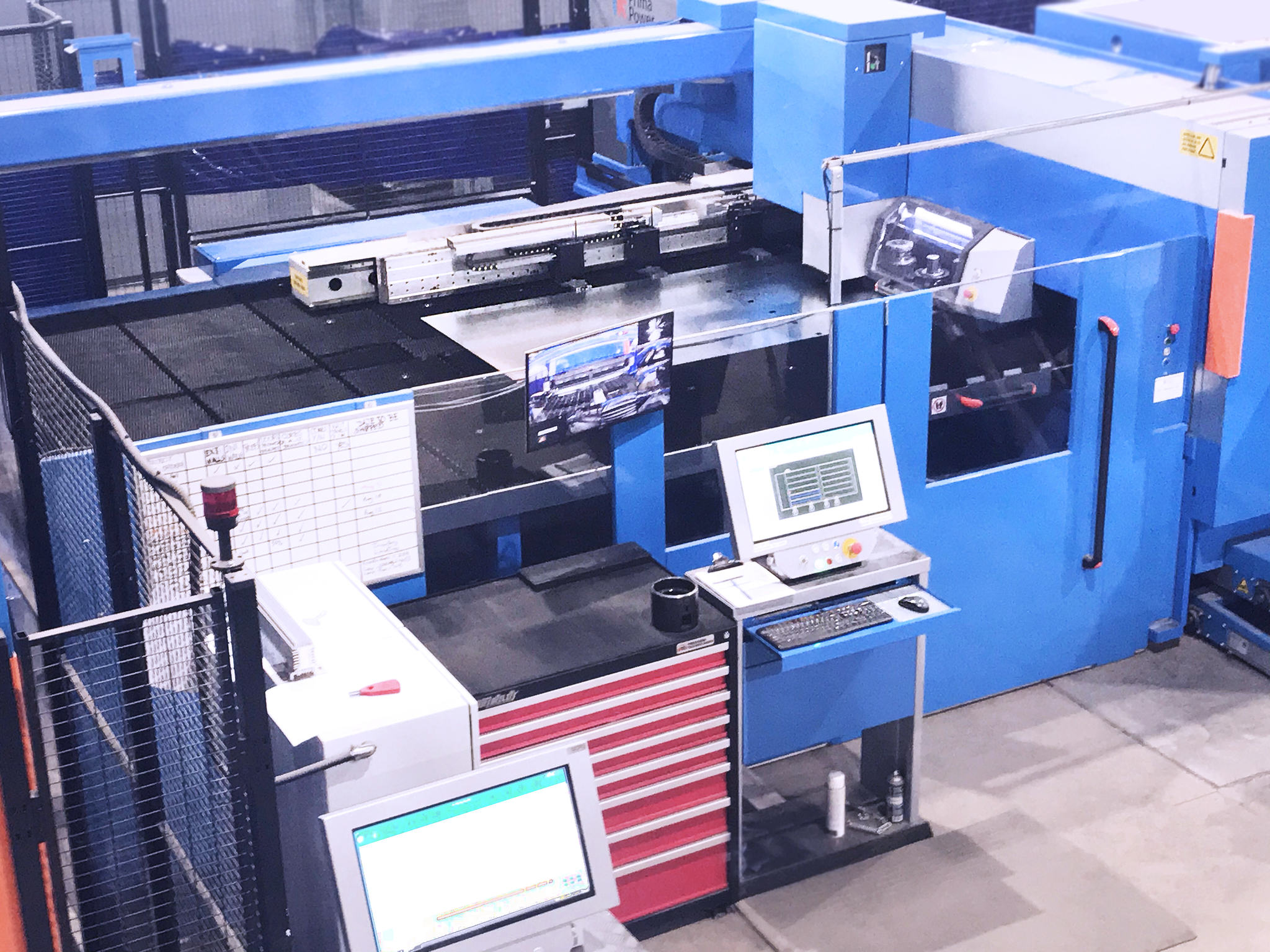
TRAINING & SERVICE
“The training and service from Prima Power have been great,” concludes Paegel. “The technicians are skilled people and they are available. When you call the support line, they pick up and transfer you to the right person. You get the problem solved and are back up and running quickly.”
THE BOTTOM LINE
“The PSBB automation has allowed us to at least double our capacity and will eventually triple our output,” concludes Vazquez. “It will also allow us to capture more market share and be able to better service our customers today and in the future.”
"Automation is really the way of the future in manufacturing" emphasizes Kevin Whittaker, designer. “Our operators can improve their careers by learning to utilize machines like the Shear Genius and EBe.”
“The PSBB has supported our growth and improved our bottom line,” says Smith. “It has affected not only the panel creation but removed additional cutting and layout requirements that we were completing down the line.”
“The PSBB has become a focal point at Scott Springfield,” notes Paegel. “When one of our customers views the PSBB, there are smiles on their faces when they see how a part is transformed from a flat sheet of material to a beautifully-bent part at the end of the line.”
The automated Prima Power line allowed us to increase our production to meet this challenge and still have additional capacity with just one line.