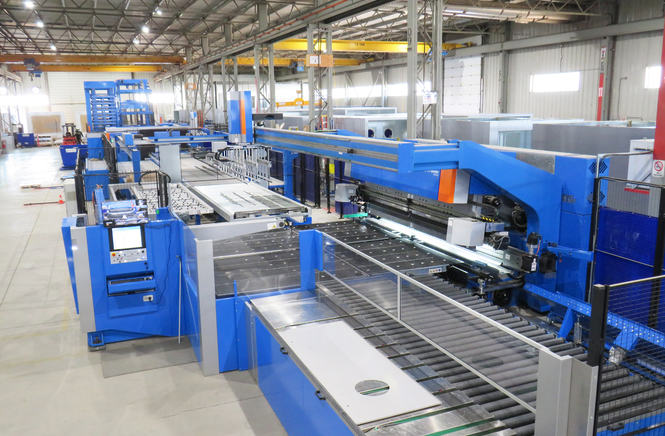
Scott Springfield Mfg, Eine kompakte Lösung für den Kundenerfolg
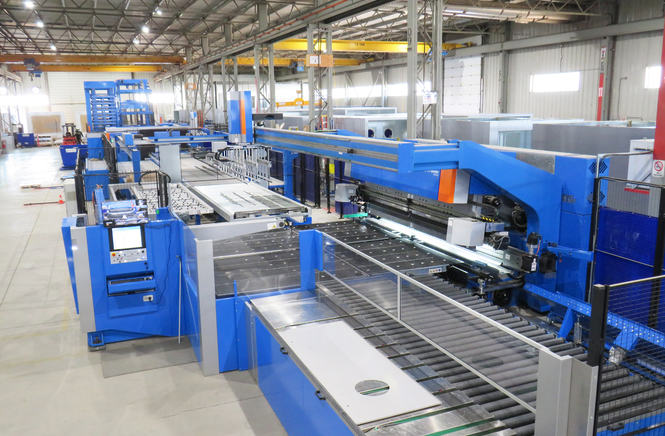
Scott Springfield Mfg, in Calgary, Kanada,ist ein führender Anbieter von kundenspezifischen Luftaufbereitungssystemen, der die neuesten Technologien einsetzt, um seinen Kunden eine flexible Lösung für ihren Bedarf an Luftaufbereitungsanlagen zu bieten.
Scott Springfield Mfg. arbeitet eng mit Handelsvertretern, Gebäudeeigentümern, Gebäudetechnikern, Ingenieuren und Bauunternehmern zusammen, um zuverlässige, sichere und energieeffiziente Lüftungsanlagen zu entwickeln. Dabei folgen wir stets der gleichen Philosophie, auf der das Unternehmen gegründet wurde: Aufbau von Marktpartnerschaften, Optimierung der Gerätekonstruktion, Maximierung der Leistung, Kontrolle der Endkosten und Lieferung eines Produkts, auf das Kunden stolz sein können. Laut Nathan Smith, Director of Sales & Business Development, wurde das Unternehmen im Jahr 1978 hauptsächlich für HLKProdukte für Krankenhäuser und die Ölindustrie in Alberta und British Columbia gegründet.
„Heute haben wir unseren Markt stark erweitert und unsere Kundenliste umfasst hochkarätige medizinische Einrichtungen, Labore, institutionelle Einrichtungen, Regierungsbehörden, Rechenzentren sowie Industrieunternehmen in der Öl- und Gasindustrie, im Bergbau, in der Luft- und Raumfahrt und überall dort, wo spezielle Materialien oder besondere Anforderungen an die Luftaufbereitung erforderlich sind.“
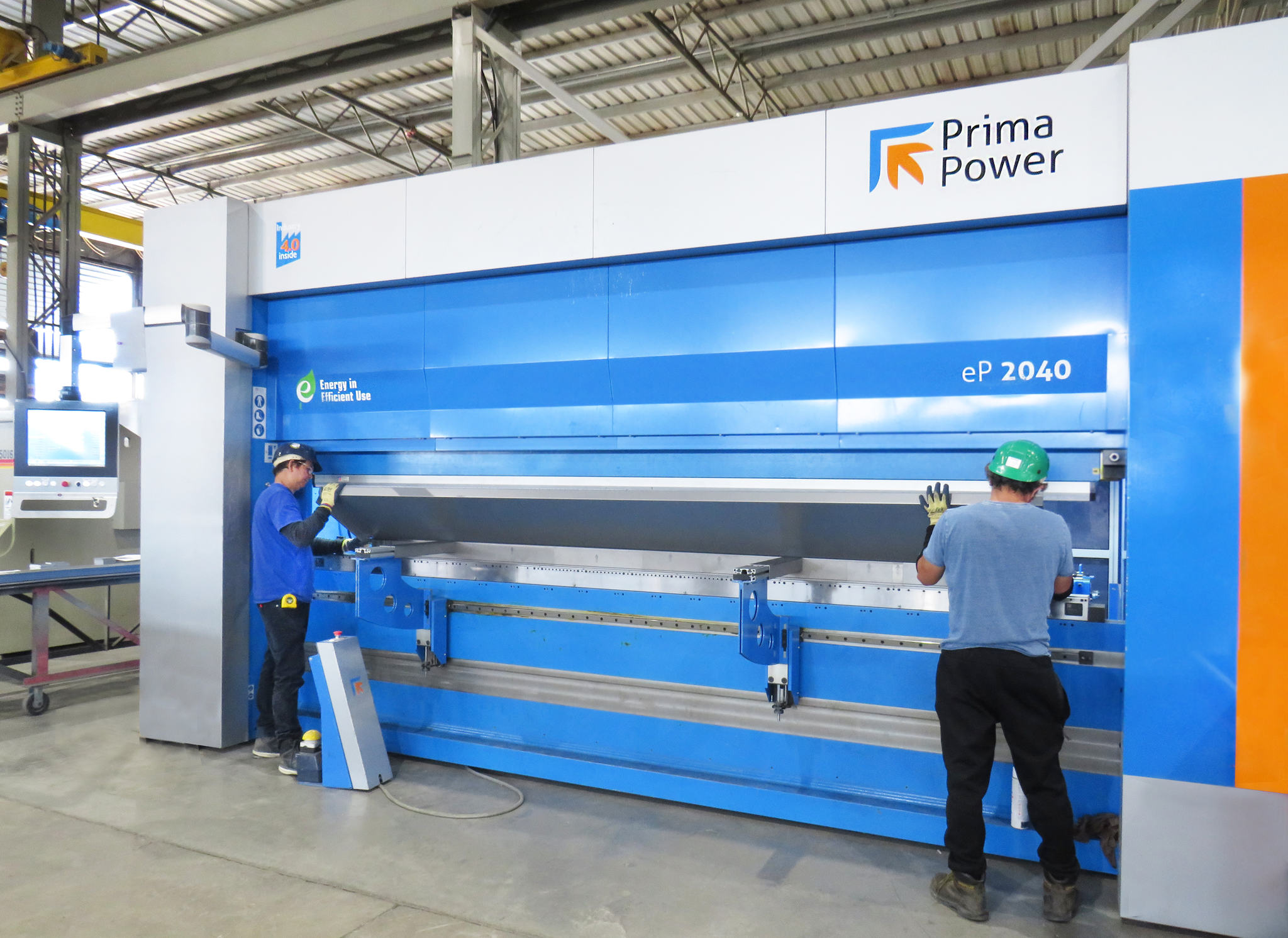
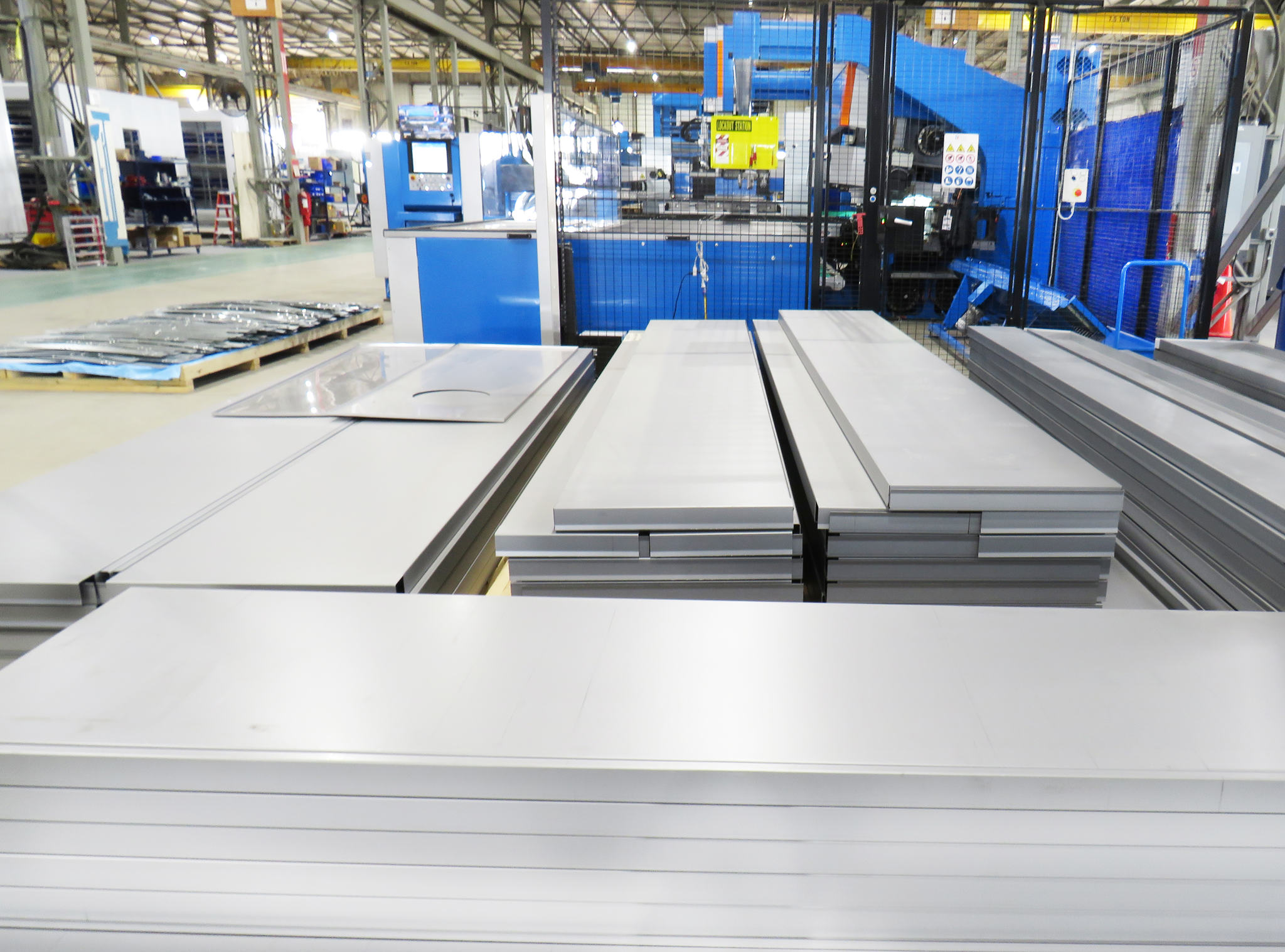
FERTIGUNG
Die HKL-Produkte werden in einem der beiden Werke in Calgary hergestellt. Das Eine ist 11.000 m² groß und das Andere, der Hauptfertigungsbereich, ist 13.500 m² groß. In den beiden Werken sind insgesamt 250 Mitarbeiter beschäftigt. Im Laufe der Jahre umfasste die Fertigungsausrüstung manuelle Scheren, Pressen, Ausklinkmaschinen, Abkantpressen und eine Blechbiegemaschine. Bei der Erweiterung des zweiten Werks im Jahr 2021 beschloss die Unternehmensleitung jedoch, die Blechfertigung zu automatisieren und entschied sich für das PSBB System: ein kompaktes, flexibles Fertigungssystem von Prima Power, welches das Stanzen, Scheren, Puffern und Biegen kombiniert, um Rohbleche automatisch zu fertig gebogenen, hochwertigen Bauteilen zu verarbeiten. Der Combo Speicher ermöglicht die Verarbeitung von Bauteilen aus einer Vielzahl von Materialien, die je nach Programmierung automatisch gewechselt werden können. Die Bleche werden in eine servoelektrische Shear Genius SGe-Stanz-/Scherzelle übergeben. Nach dem Scheren werden die Bauteile in einer automatischen servoelektrischen Biegezelle von Express Bender gepuffert und anschließend gebogen. Mit der Pufferfunktion kann der Materialfluss flexibel gestaltet werden, um Teile direkt an das automatische Biegen zu übergeben. Weiterhin kann dadurch Material aus der Anlage entnommen und neues Material eingebracht, sowie die unterschiedlichen Zeitanforderungen beim Biegen und Stanzen/Scheren ausgeglichen werden.
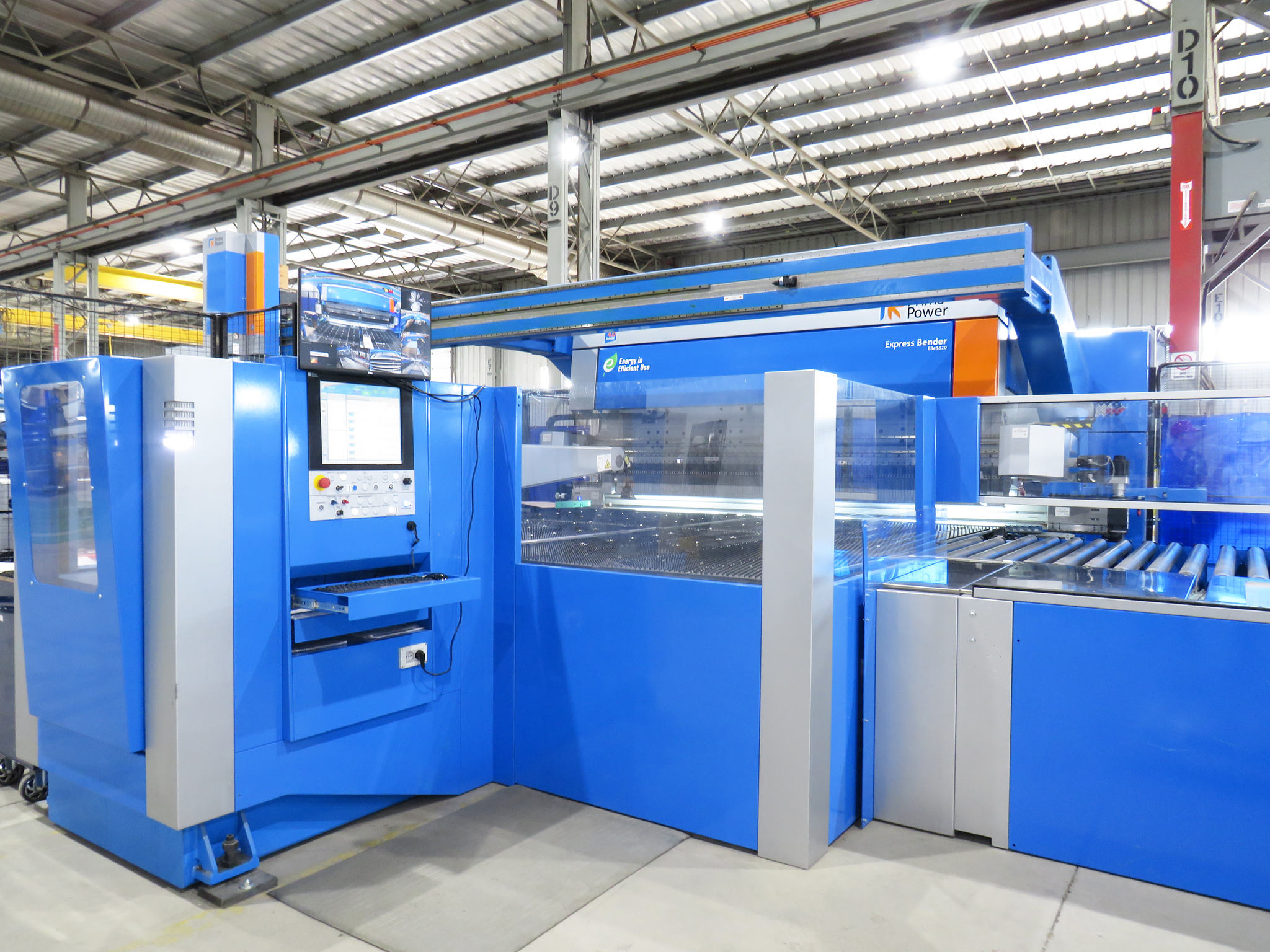
SERVO-ELEKTRISCHE SHEAR GENIUS
Die SGe ist in der Lage, die anspruchsvollsten Aufgaben mit minimalen Rüstzeiten und im bedienerlosen Betrieb durchzuführen. Die Shear Genius erhöht die Materialproduktivität durch effiziente und vielseitige Verschachtelungsprogramme. Automatisiertes Laden, Stanzen, Formen und Umprofilieren, Entladen, Sortieren und Stapeln führt zu einer drastischen Reduzierung von Materialausschuss und manueller Arbeit bei gleichzeitiger Steigerung der Produktivität. Der Kommissionier- und Stapelroboter (PSR) bietet eine hohe Flexibilität. Die Teile werden immer direkt auf den Stapel gelegt und nie fallen gelassen. Der PSR mit Pufferfunktionen ermöglicht die Neuorganisation und Optimierung des Produktionsflusses vom Shear Genius zum EBe. Die SGe eliminiert verschwenderische Restgitter und kostspielige Nachbearbeitungen wie das Entgraten. Nibbelkanten an den Teileaußenseiten werden durch den Einsatz der integrierten Winkelschere eliminiert. In der SGe wird das Blech ohne manuelle Eingriffe automatisch eingelegt und ausgerichtet, wodurch sehr genaue Teile gewährleistet werden.
„Beim Stanzen mehrerer Bleche mit vielen Löchern benötigen wir eine hervorragende Genauigkeit und Geschwindigkeit“, sagt Javier Vazquez, Produktionsleiter. „Bei einem Blech haben wir früher 40 Minuten gebraucht, um die Löcher zu bohren. Mit der Shear Genius dauert es nur zwei Minuten. Wir setzen jedes Teil, das wir automatisieren können und dabei trotzdem ein gleichbleibendes und zuverlässiges Maß bei gleicher Qualität haben, sofort auf die PSBB.“
Die SGe ist in der Lage, die anspruchsvollsten Aufgaben mit minimalen Rüstzeiten und im bedienerlosen Betrieb durchzuführen.
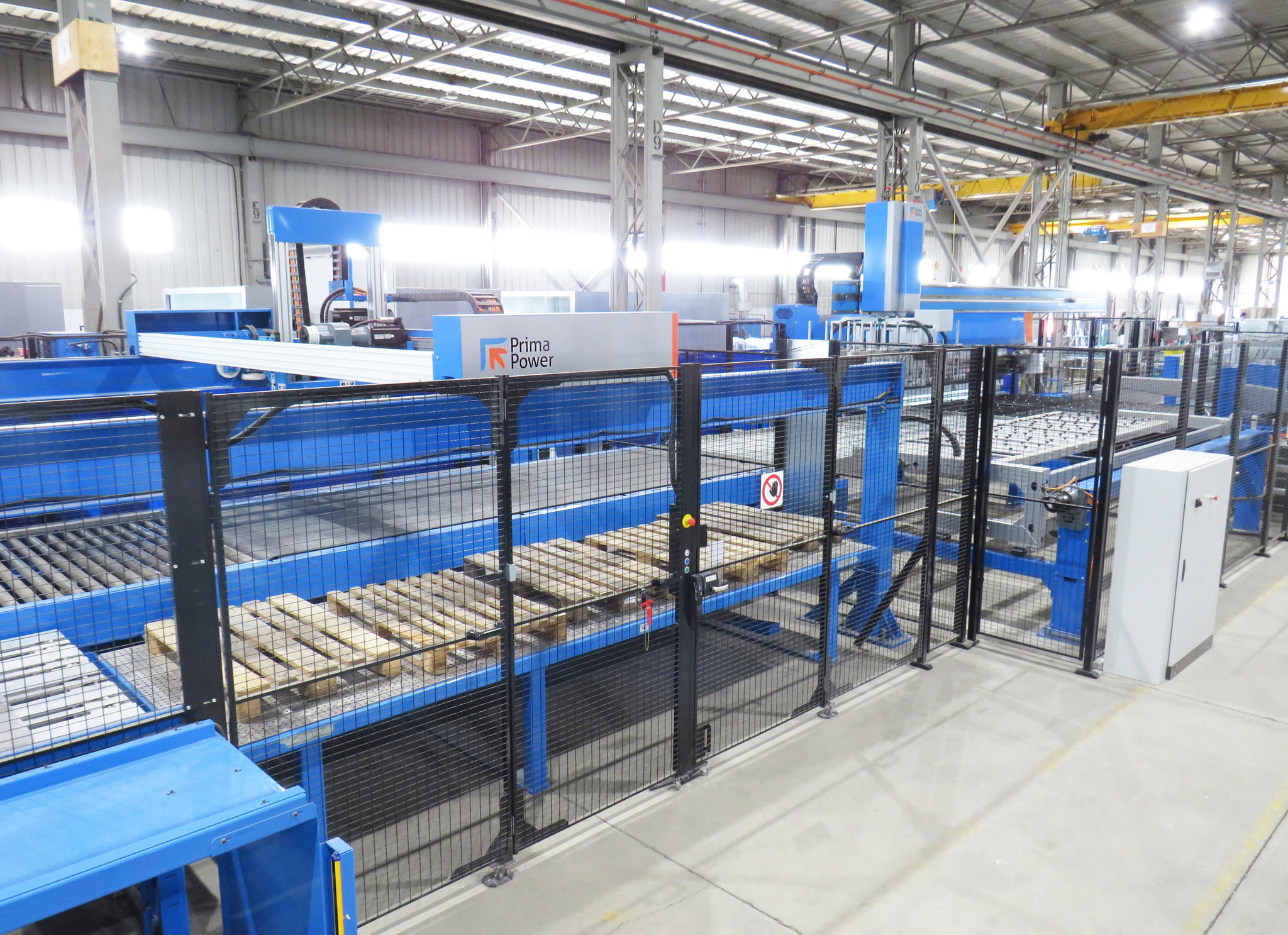
SERVOELEKTRISCHES BIEGEN
Die servoelektrische Express Biegemaschine EBe ist eine Biegelösung, die speziell für die Produktionsanforderungen eines jeden Verarbeiters entwickelt wurde, um maximale Produktivität, Qualität und Wiederholbarkeit zu erreichen. Der Biegevorgang ist vollautomatisiert, vom Beladen der flachen Stanzteile bis zum Entladen des fertigen Produkts. Die Prima Power EBe bietet die für anspruchsvolle Anwendungen erforderliche hohe Biegequalität. „Die Effizienz der EBe ermöglicht es uns, einen Auftrag, der mit einer manuellen Abkantpresse 10 Stunden benötigen würden, in einer Stunde zu erledigen“, sagt Vazquez.„Wir gehen davon aus, dass dieses Verhältnis von 10 zu 1 mit zunehmender Erfahrung an der Maschine noch viel höher ausfallen wird.“
„Wir produzieren Hunderte von Blechen auf der EBe und sie kommen alle in der gleichen Qualität heraus“, fügt Byron Paegel, Produktionsleiter, hinzu.
Scott Springfield hat auch eine servoelektrische Abkantpresse Prima Power eP gekauft. Die eP-Brake bietet die Vorteile des servoelektrischen Antriebssystems: hohe Beschleunigung, Verzögerung und schnelle Reaktionszeiten. Im Vergleich zum herkömmlichen Verzögern kann sie die Produktivität erheblich steigern und die Zykluszeiten um 30% und mehr reduzieren.
„Wir stellen einige Teile her, die nur gestanzt und geschert und dann – aufgrund ihrer Größe – manuell auf der Abkantpresse gebogen werden“, erklärt Vazquez.
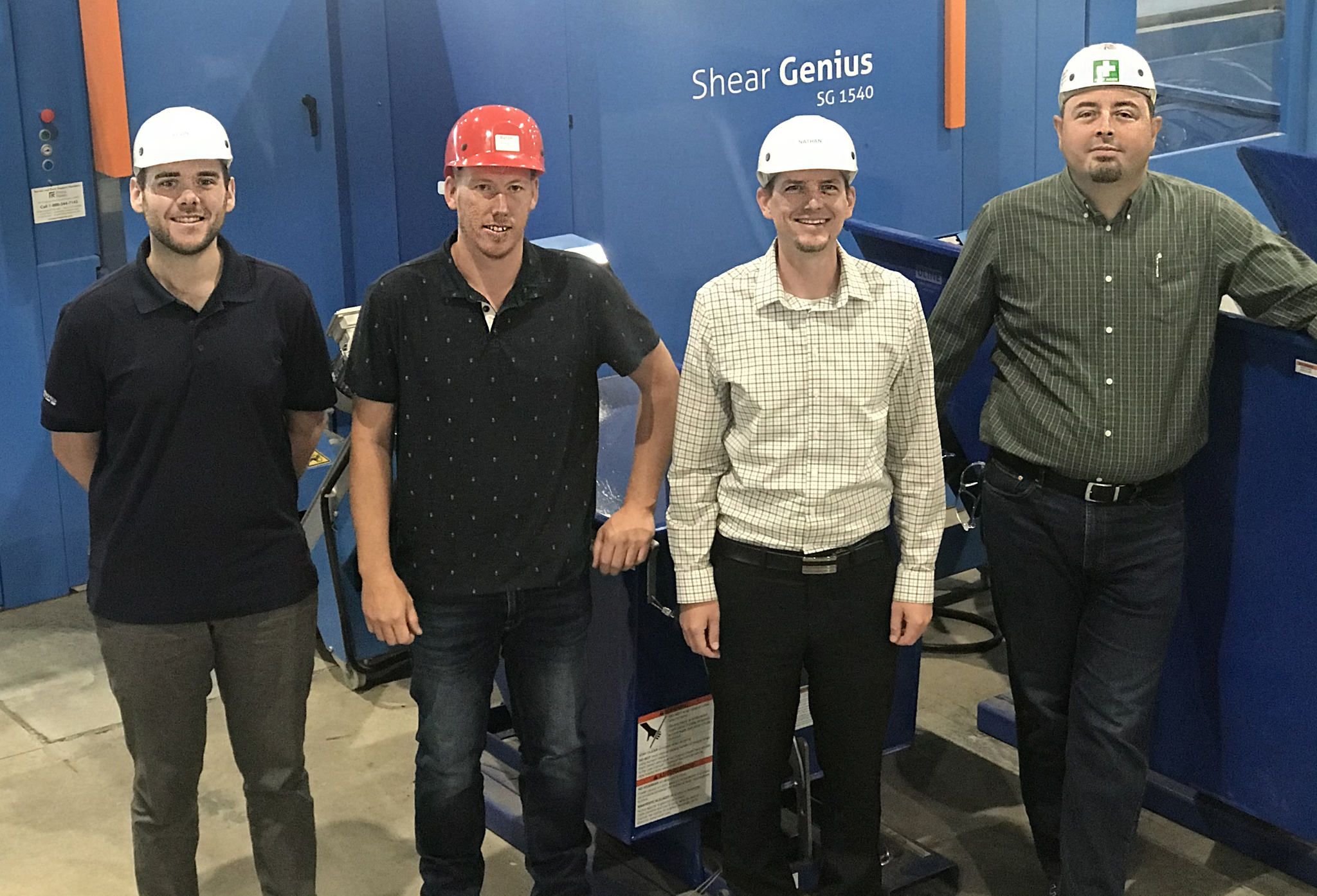
NEUE MARKTHERAUSFORDERUNG
„Die Möglichkeit, neue Märkte zu erschließen, erforderte viel mehr Kapazität als wir vor dem Kauf der PSBB hatten“, erklärt Vazquez. „Die automatisierte Prima Power-Linie ermöglichte es uns, unsere Produktion zu erhöhen, um dieser Herausforderung gerecht zu werden, und trotzdem mit nur einer Linie über zusätzliche Kapazitäten zu verfügen.“
„Der Platzbedarf war eine weitere wichtige Entscheidung, die wir hatten,„ fügt Smith hinzu. „Jedes Produkt, das wir herstellen, ist kundenspezifisch und variiert in Layout und Größe - bis zu 45m x 13m. All diese separaten Prozesse beanspruchen eine Menge Platz. Die kompakte Grundfläche der PSBB hat uns wirklich geholfen, diese zu reduzieren und gab uns die Fläche, mehr Einheiten zu bauen.“
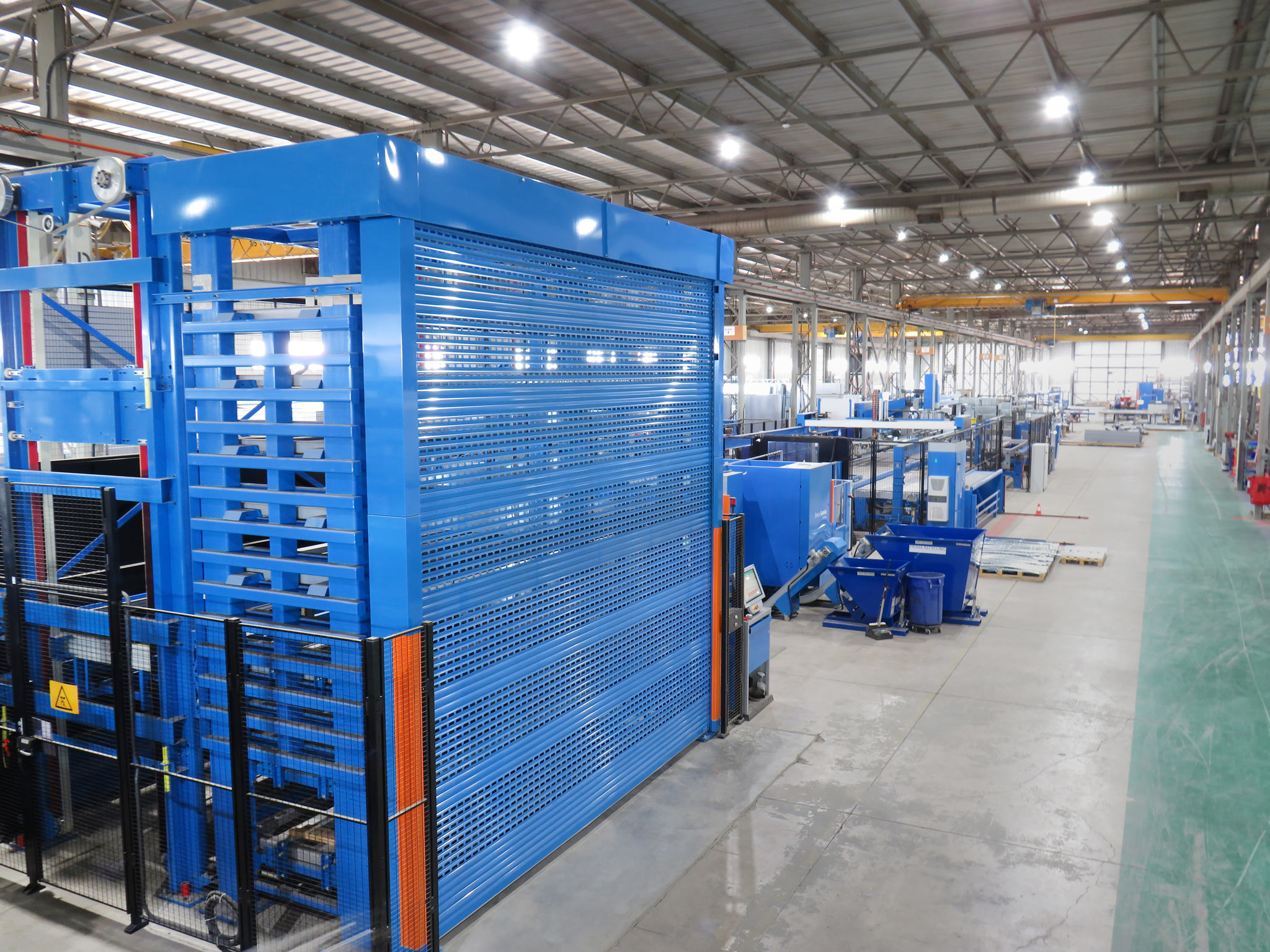
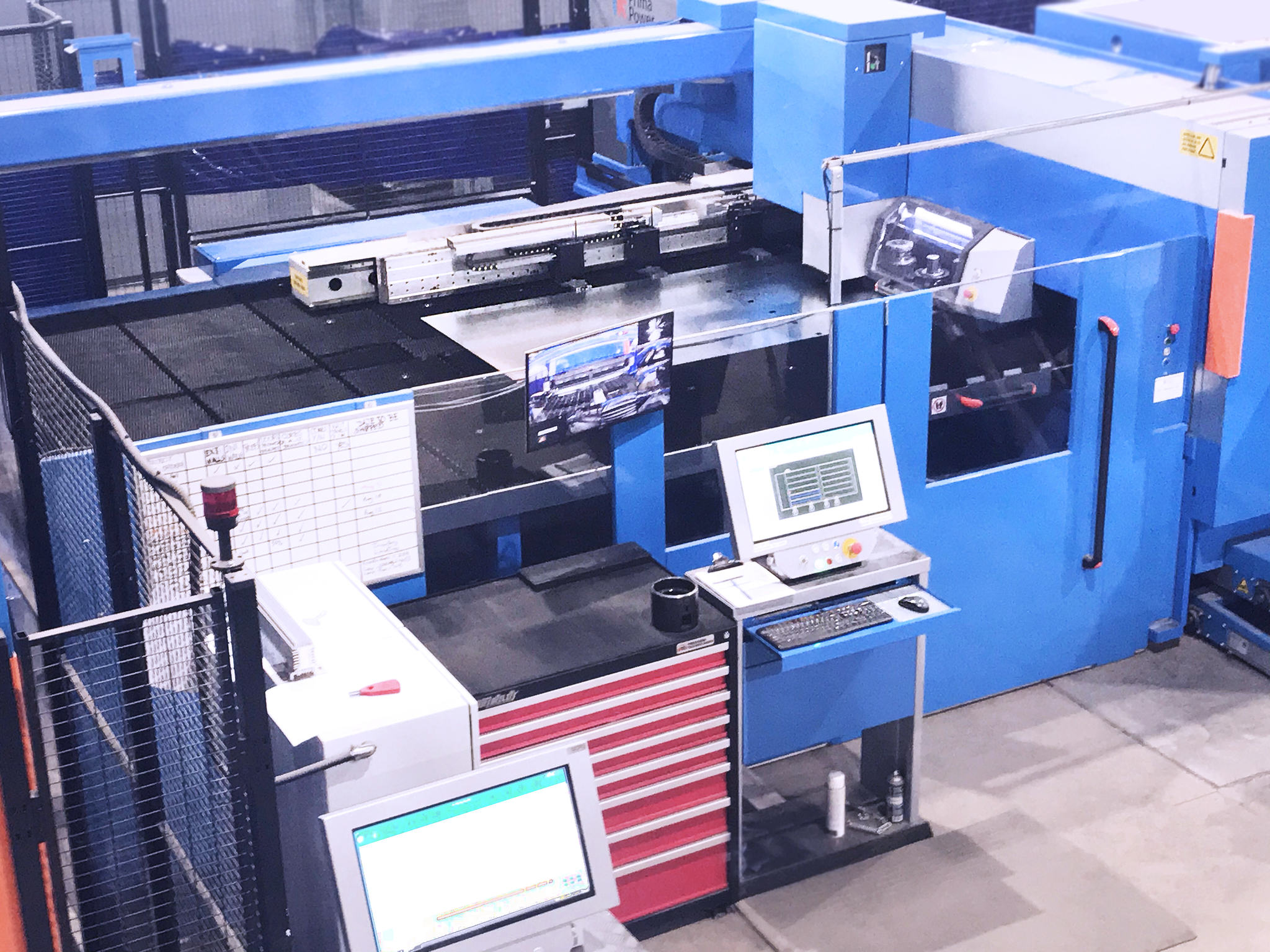
SCHULUNG UND SERVICE
„Die Schulung und der Service von Prima Power waren großartig“, fasst Paegel zusammen. „Die Techniker sind gut ausgebildet und immer erreichbar. Wenn man die Support-Hotline anruft, wird man bedient und an die richtige Person weitergeleitet. Man kriegt das Problem gelöst und das System ist schnell wieder betriebsbereit.
DAS FAZIT
„Die PSBB-Automatisierung hat es uns ermöglicht, unsere Kapazität mindestens zu verdoppeln und wird unseren Output sogar verdreifachen“, so Vazquez abschließend. „Es wird uns auch ermöglichen, mehr Marktanteile zu erobern und wir können unsere Kunden heute und in Zukunft noch besser bedienen.“
„Die Automatisierung ist wirklich der Weg in die Zukunft der Fertigung“, betont Kevin Whittaker, Konstrukteur. „Unsere Bediener können ihre Karriere verbessern, indem sie den Umgang mit Maschinen wie der Shear Genius und EBe zu lernen.“
„Die PSBB hat unser Wachstum unterstützt und unser Endergebnis verbessert“, sagt Smith. „Sie hat sich nicht nur auf die Fertigung von Blechen ausgewirkt, sondern auch zusätzliche Schneid- und Layoutanforderungen beseitigt, die wir entlang der Linie zu erledigen haben.“ „Die PSBB ist zu einem zentralen Punkt bei Scott Springfield geworden“, bemerkt Paegel. „Wenn einer unserer Kunden die PSBB sieht, hat er ein Lächeln im Gesicht, wenn er sieht, wie sich ein Teil von einem flachen Blech in ein schön gebogenes Teil am Ende der Linie verwandelt.“
Die automatisierte Prima Power-Linie ermöglichte es uns, unsere Produktion zu erhöhen, um diese Herausforderung zu meistern, und trotzdem mit nur einer Linie zusätzliche Kapazitäten zu haben.