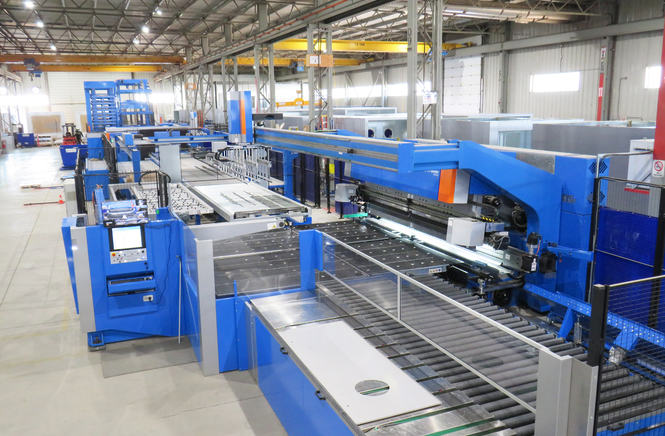
Scott Springfield Mfg, une solution compacte pour la réussite du client
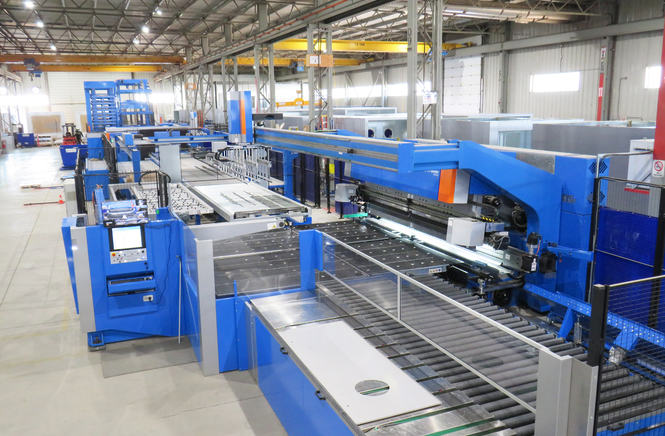
Scott Springfield Sfg, inc. à Calgary, Canada, est un fournisseur de premier plan de systèmes de traitement de l'air personnalisés, utilisant les dernières technologies pour fournir à ses clients une solution flexible à leurs besoins en matière de traitement de l'air.
Scott Springfield Mfg. travaille en étroite collaboration avec les responsables commerciaux, les propriétaires de locaux, les gestionnaires d'installations, les ingénieurs et les entrepreneurs pour concevoir des ensembles de traitement de l'air fiables, sûrs et économes en énergie. En suivant toujours la même philosophie sur laquelle la société a été fondée : développer des partenariats avec le marché, optimiser la conception des équipements, maximiser les performances, contrôler le coût final et fournir un produit dont vous pouvez être fier. Selon Nathan Smith, directeur des ventes et du développement commercial, la société a été fondée en 1978, principalement pour les produits CVC destinés aux hôpitaux et aux industries pétrolières en Alberta et en Colombie-Britannique.
"Aujourd'hui, nous avons considérablement élargi notre marché et notre liste de clients comprend des installations médicales de haut niveau, des laboratoires, des installations institutionnelles, des agences gouvernementales, des centres de données, ainsi que des entreprises industrielles dans les secteurs du pétrole et du gaz, de l'exploitation minière, de l'aérospatiale, et partout où des matériaux spéciaux ou des exigences particulières sont nécessaires du côté du traitement de l'air."
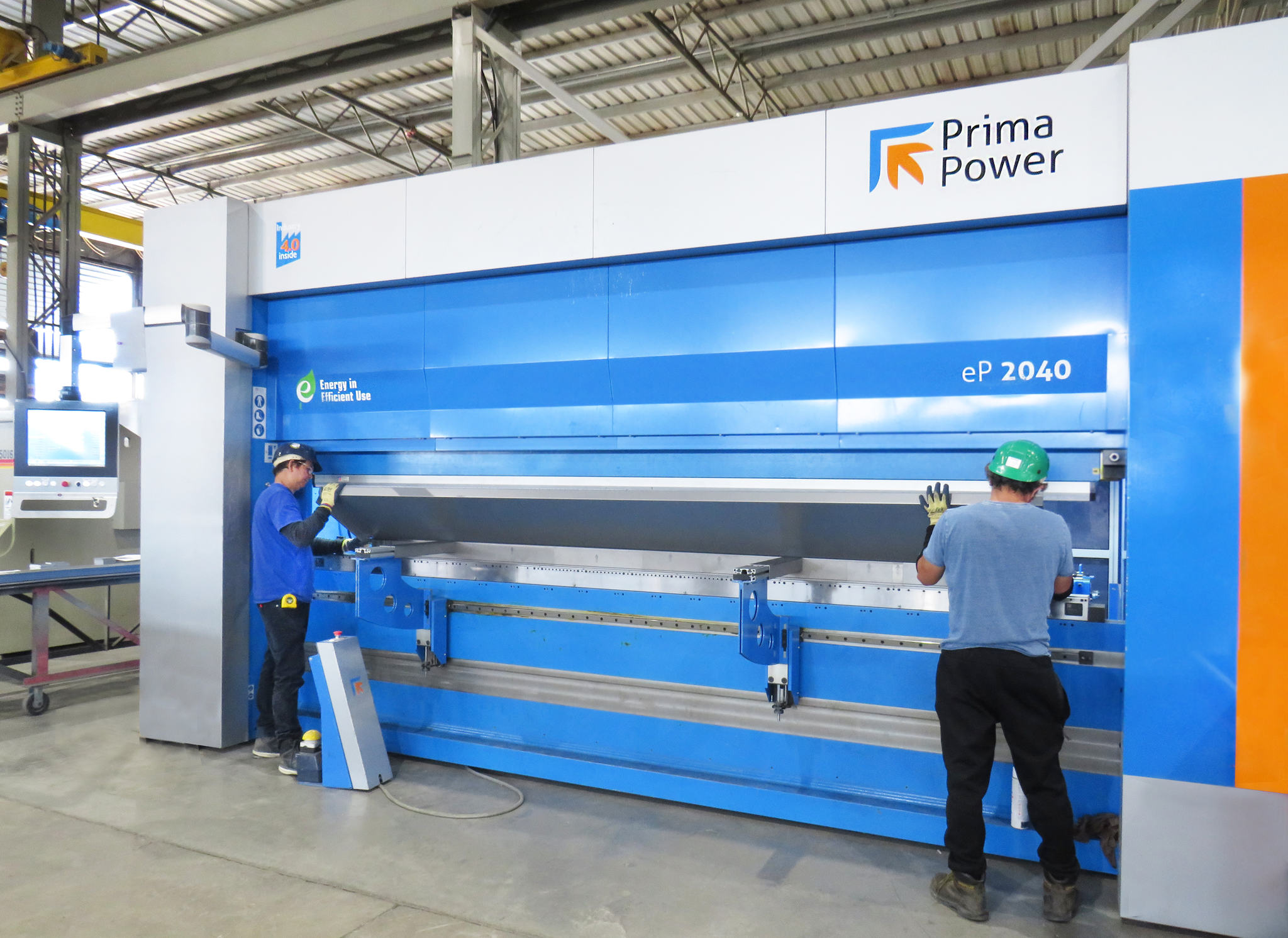
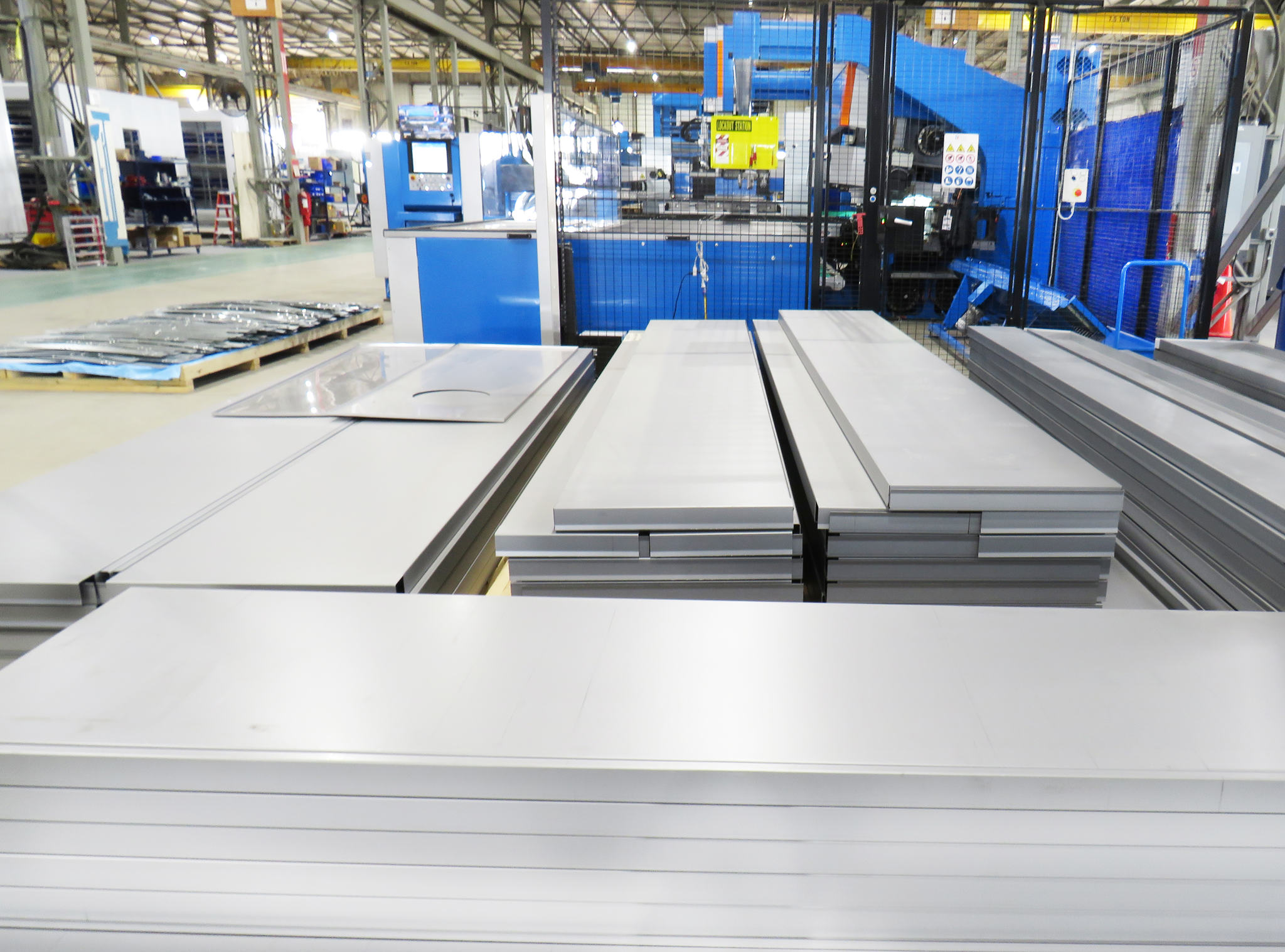
LA FABRICATION
Les produits CVC sont fabriqués dans l'une des deux installations de Calgary. L'une a une superficie de 11148 m2 et l'autre, la zone de fabrication principale, a une superficie de 13470 m2. Au total, 250 employés travaillent dans les deux installations. Au fil des ans, l'équipement de fabrication comprenait des cisailles manuelles, des presses, des encocheuses, des presses plieuses et une panneauteuse. Cependant, lors de l'expansion de la deuxième installation en 2021, la direction a décidé d'automatiser la zone de fabrication de la tôle et a choisi le PSBB : un système de fabrication compact et flexible de Prima Power qui combine le poinçonnage, le cisaillage, le tamponnage et le pliage pour transformer des tôles vierges en composants de haute qualité, prêts à être pliés automatiquement.
Le stockage combiné permet de traiter des composants à partir d'une variété de matériaux, qui peuvent être changés, selon la programmation, automatiquement. Les tôles sont transférées dans une cellule servo-électrique de poinçonnage/cisaillage Shear Genius SGe. Après le cisaillage, les composants sont envoyés vers une cellule de mise en tampon puis de pliage dans une cellule de pliage servo-électrique automatique Express Bender. Grâce à la fonction de mise en mémoire tampon, le flux de matériaux peut être organisé de manière flexible pour transférer les pièces directement vers le pliage automatique, pour équilibrer les différentes exigences de temps du pliage et du poinçonnage/cisaillage, pour sortir des matériaux du système et pour en introduire de nouveaux.
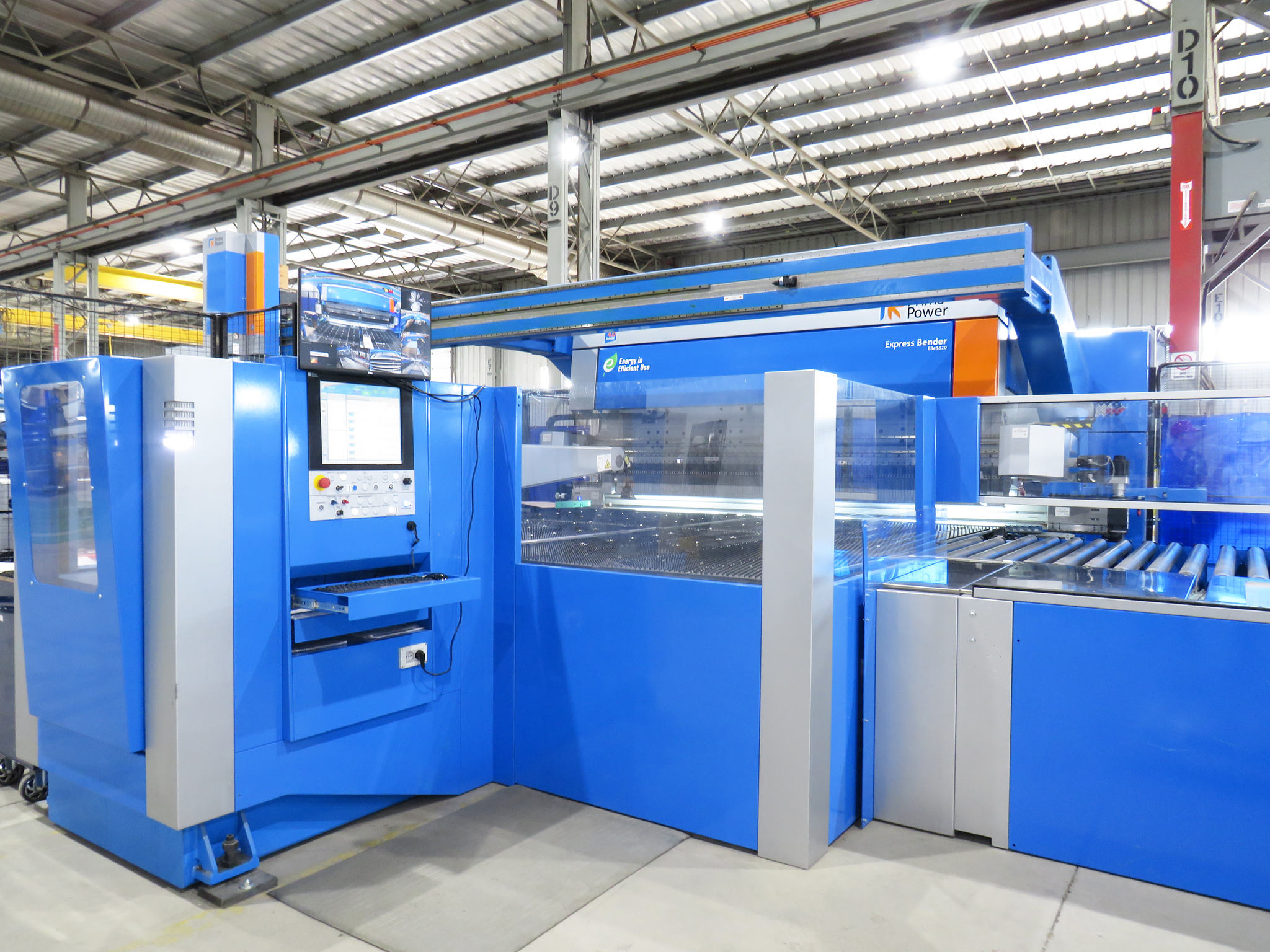
SHEAR GENIUS SERVO-ELECTRIQUE
La SGe est capable d'effectuer les travaux les plus exigeants avec des temps de préparation très courts et des opérations automatisées. Shear Genius augmente la productivité des matériaux grâce à des programmes d'imbrication efficaces et polyvalents. L'automatisation du chargement, du poinçonnage, du formage et de la transformation, du déchargement, du tri et de l'empilage permet de réduire considérablement les déchets de matériaux et le travail manuel tout en augmentant la productivité. Le robot de prélèvement et d'empilage (PSR) offre une grande flexibilité. Les pièces sont toujours placées directement sur la pile et ne tombent jamais. Le PSR, doté de fonctions de mise en mémoire tampon, permet de réorganiser et d'optimiser le flux de production entre le Shear Genius et l'EBe. La SGe élimine les chutes de pièces et les opérations secondaires coûteuses telles que l'ébavurage. Les arêtes de grignotage sur les extérieurs de la pièce sont éliminées grâce à l'utilisation de la cisaille à angle droit intégrée. Dans la SGe, la tôle est chargée et équarrie automatiquement, sans interventions manuelles, ce qui garantit des pièces très précises.
"Nous avons besoin d'une précision et d'une vitesse excellentes pour poinçonner plusieurs panneaux avec de nombreux trous", explique Javier Vazquez, directeur de la fabrication. « Sur un panneau, il nous fallait 40 minutes pour percer les trous. Sur le Shear Genius, cela prend deux minutes. Toute pièce que nous pouvons automatiser tout en ayant toujours une dimension cohérente et fiable avec la même qualité, nous la mettons immédiatement le PSBB.
La SGe est capable d'effectuer les travaux les plus exigeants avec des temps de configuration minimaux et des opérations autonomes.
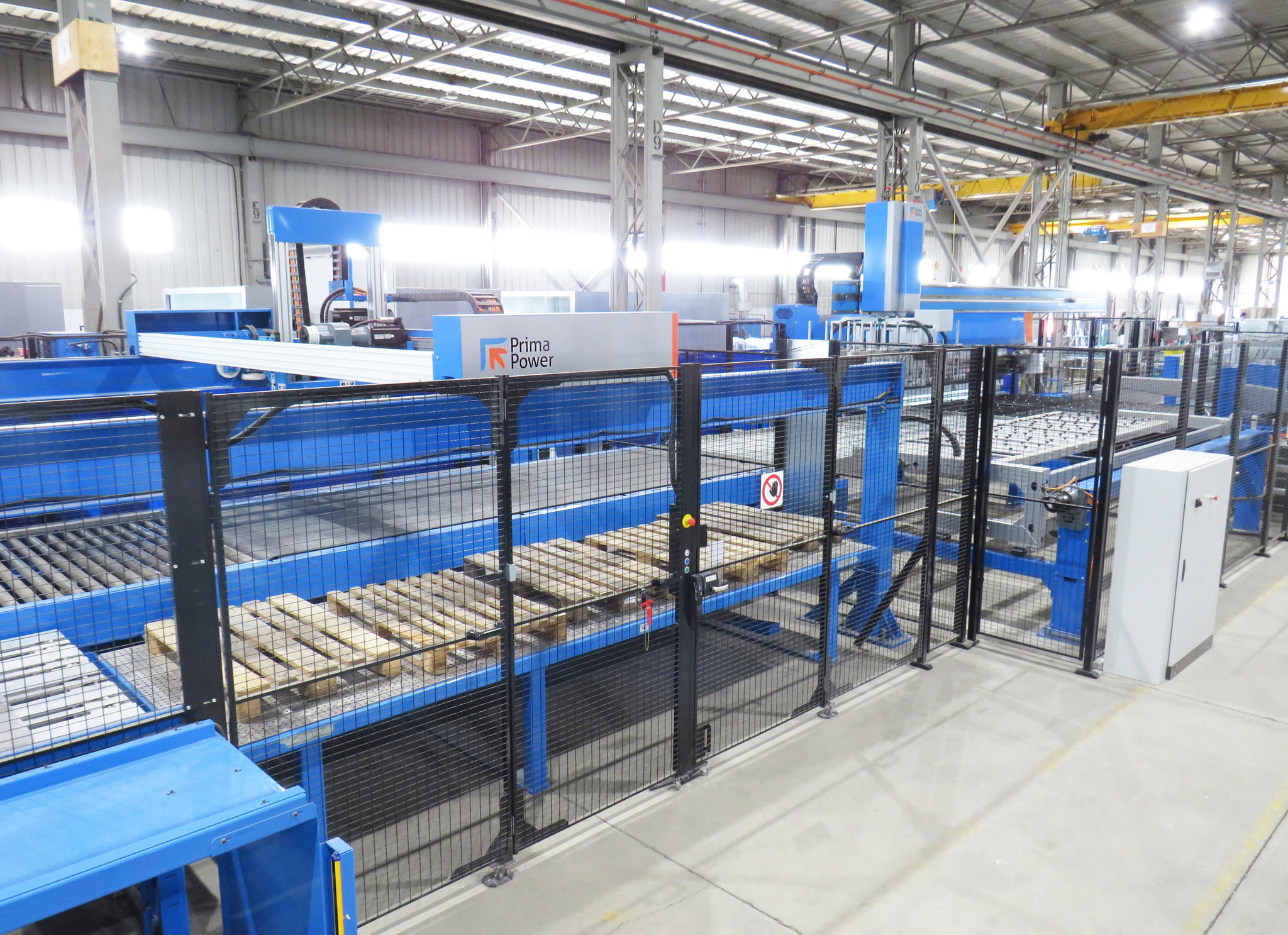
LE PLIAGE SERVO-ÉLECTRIQUE
L'Express Bender servo-électrique EBe est une solution de pliage conçue spécifiquement pour les besoins de production de chaque fabricant afin d'obtenir une productivité, une qualité et une répétabilité maximales. L'opération de pliage est entièrement automatisée, du chargement des pièces découpées à plat au déchargement du produit fini. L'EBe de Prima Power fournit la haute qualité de pliage requise dans les applications exigeantes. "L'efficacité de l'EBe nous permet de prendre un travail qui nécessiterait 10 heures sur une presse plieuse manuelle et de le réaliser en une seule heure", déclare Vazquez. "Nous nous attendons à ce que ce ratio de 10 pour 1 augmente beaucoup plus avec une meilleure expérience de la machine."
"Nous produisons des centaines de panneaux sur l'EBe et ils sortent tous avec la même qualité", ajoute Byron Paegel, superviseur de la production.
Scott Springfield a également acheté à Prima Power une presse plieuse servo-électrique eP. L'eP-Brake dispose des atouts d'une accélération et d'une décélération poussées, ainsi que des temps de réponse rapides du système d'entraînement servo-électrique. Par rapport aux freins conventionnels, elle peut augmenter considérablement la productivité et réduire les temps de cycle de 30% et plus.
"Nous fabriquons certaines pièces qui sont simplement poinçonnées et cisaillées, puis pliées manuellement sur la presse plieuse en raison de la taille des composants", explique M. Vazquez.
L'efficacité de l'EBe nous permet de prendre un travail qui prend 10 heures sur une presse plieuse manuelle et de le réaliser en une seule heure.
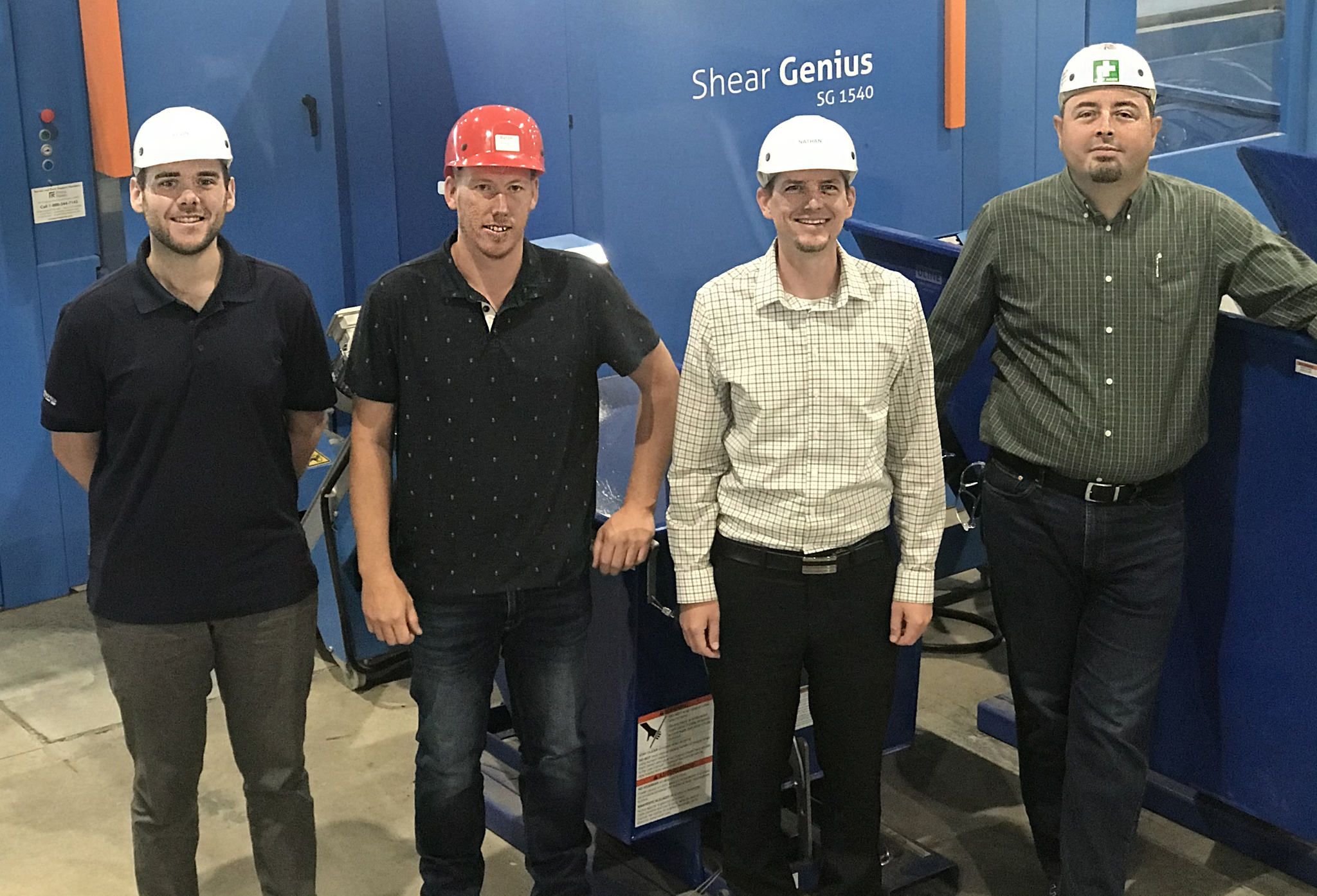
LE NOUVEAU DÉFI DU MARCHÉ
"L'opportunité de pénétrer de nouveaux marchés nécessitait une capacité beaucoup plus importante que celle dont nous disposions avant l'achat du PSBB", explique Vazquez. "La ligne automatisée Prima Power nous a permis d'augmenter notre production pour relever ce défi tout en disposant de capacités supplémentaires avec une seule ligne."
"L'espace au sol était une autre décision cruciale que nous avions à prendre", ajoute Smith. "Chaque produit que nous fabriquons est personnalisé et varie en termes de disposition et de taille - jusqu'à 150' x 44'. Tous ces processus distincts occupent beaucoup d'espace au sol. L'empreinte compacte de la PSBB nous a vraiment aidés à réduire cet espace et nous a donné la possibilité de construire plus d'unités.
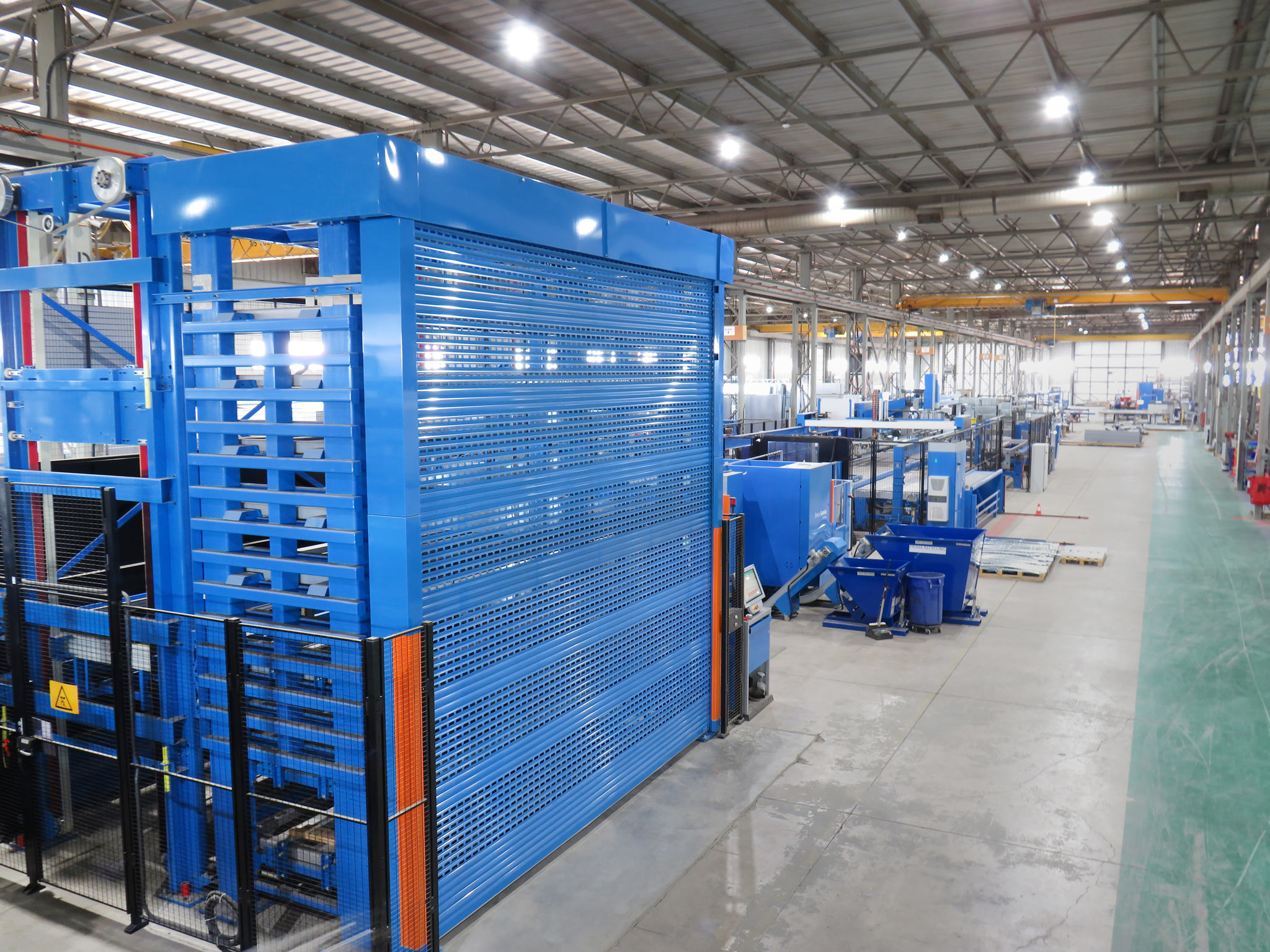
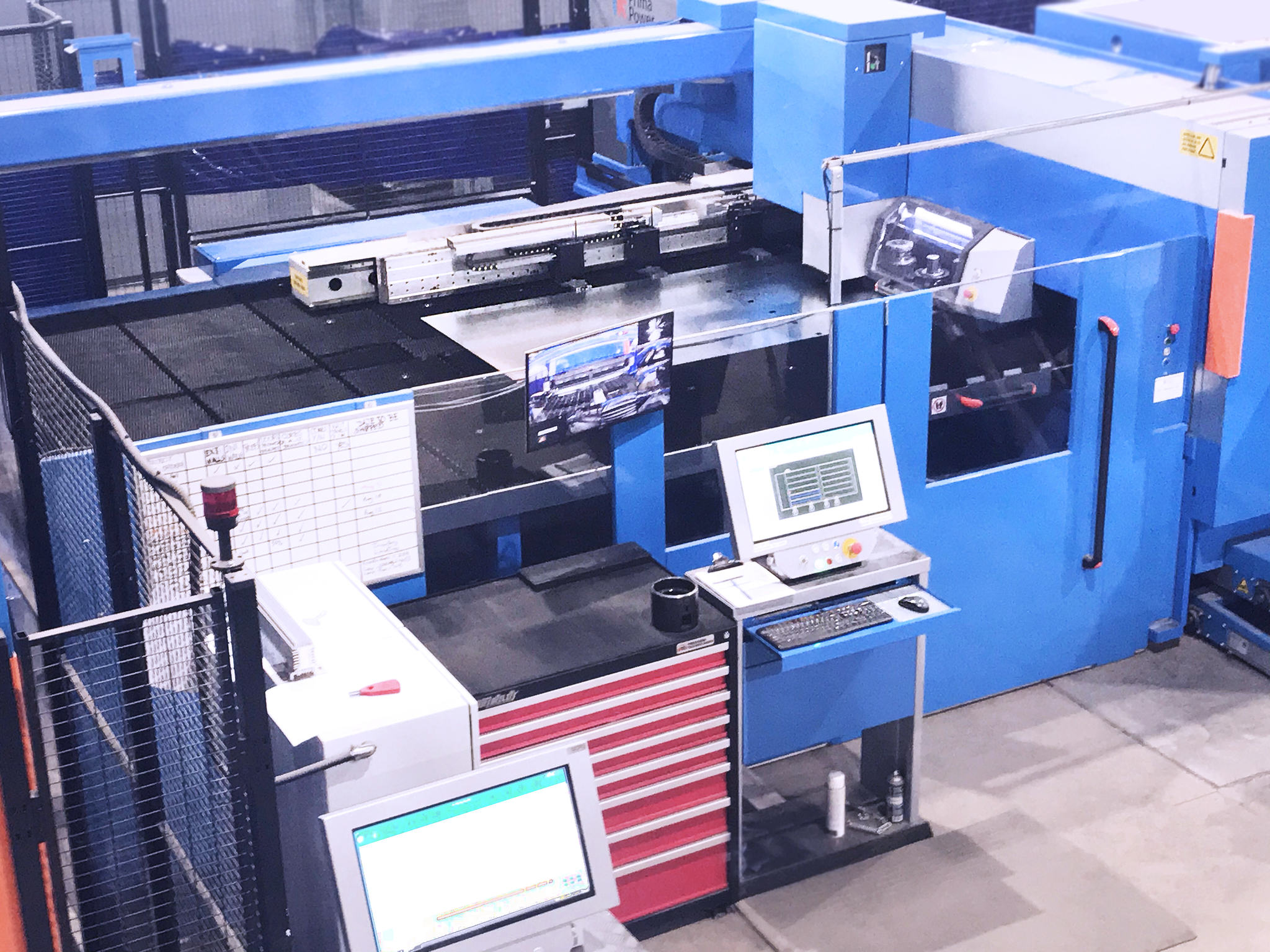
LA FORMATION ET LE SERVICE
"La formation et le service de Prima Power ont été excellents", conclut Paegel. "Les techniciens sont des personnes qualifiées et ils sont disponibles. Lorsque vous appelez la hotline, ils décrochent et vous transfèrent vers la bonne personne. Vous obtenez la résolution du problème et vous êtes de nouveau opérationnel rapidement."
LE RÉSULTAT FINAL
"L'automatisation du PSBB nous a permis d'au moins doubler notre capacité et finira par tripler notre production", conclut Vazquez. "Elle nous permettra également de conquérir davantage de parts de marché et d'être en mesure de mieux servir nos clients aujourd'hui et à l'avenir."
"L'automatisation est vraiment la voie de l'avenir dans la fabrication" souligne Kevin Whittaker, concepteur. "Nos opérateurs peuvent enrichir leur carrière en apprenant à utiliser des machines comme la Shear Genius et l'EBe."
" La PSBB a accompagné notre croissance et amélioré notre résultat net ", déclare Smith. " Elle a non seulement impacté la création de panneaux mais a supprimé les contraintes supplémentaires de découpe et de configuration que nous devions réaliser en aval. "
" La PSBB est devenue un point central chez Scott Springfield ", note Paegel. "Quand l'un de nos clients voit la PSBB, il y a des sourires sur son visage quand il observe comment une pièce est transformée d'une tôle plate à une pièce magnifiquement pliée en bout de ligne."
La ligne automatisée Prima Power nous a permis d'augmenter notre production pour relever ce défi tout en disposant d'une plus grande capacité avec une seule ligne.