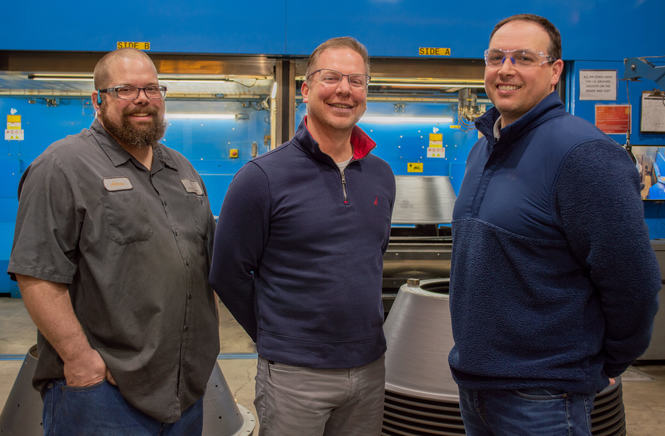
Glenn Metalcraft, going Big on 3D Fiber Laser: A Perfect Fit for Heavy-Gauge Metal Spinner
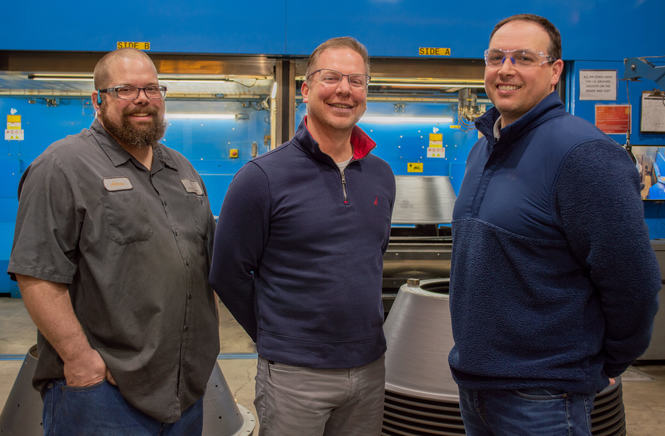
Sometimes size matters. Both in terms of business growth, as well as the methods and machinery used to facilitate success especially as the size (dimensions) of your parts get bigger for new applications. As businesses grow, they also must increasingly rely on strategic partnerships with key customers and suppliers, adopt new technologies and processes, take calculated risks including acquisitions and continually become more efficient.
Glenn Metalcraft Inc. of Princeton, Minn., is a case in point. The company was founded in 1947 as a tool and die shop, and has been growing ever since. Through the years, the third-generation, family owned company has built on its core competency of metal spinning while continually adding capabilities, capacity and automation to meet customer needs. Under the leadership of CEO Joe Glenn, Glenn Metalcraft has grown into Elemet Group, consisting of Minnesota Industrial Coatings, also in Princeton, Elemet Manufacturing in Aitkin, Minn., and a second Glenn Metalcraft location in Ft. Worth, Texas. By the end of 2023, the company plans to move into a larger Princeton facility for a total of 169,000 sq ft [15,700 sq m].
LASER FOCUS
While Glenn Metalcraft has the capability to provide fabrication and welding, spinning remains its core business, explains President Dan Patnode. “We were one of the first U.S. companies to invest in CNC spin-forming technology, and we continue to lead the industry in high-quality, close-tolerance, heavy-gauge metal spinning.” The company specializes in heavy-gauge metals for agriculture and construction applications. And a critical part of its strategy is vertical integration and expanding its capabilities, which is why Glenn Metalcraft has acquired various painting, machining and waterjet operations. “We have put ourselves in a position to manufacture and provide in-house finished parts for our OEM customers,” Glenn asserts.
More recently, Glenn Metalcraft has transitioned from waterjet cutting to laser technology with the help of Prima Power North America Inc. Prior to 2020, Glenn Metalcraft had been using a waterjet to cut the thickness of its production parts. “We were cutting five-axis on the waterjet for years, because the 3D lasers were unable to cut the thickness that we needed to process our heavy-gauge parts. Our parts were too thick for the technology at that time.” But Glenn Metalcraft’s growth, coupled with evolving customer needs prompted a change. “We were a very competent, skilled, waterjet company. So we were at the max of what those machines could do from a throughput standpoint, and it just wasn’t enough,” Patnode says. At the same time, laser technology had advanced to the point where Glenn Metalcraft was not only ready to make the switch— it wanted to go big. In March 2020, the company ordered the largest model available, Prima Power’s 4-kW Laser Next 2141, for its Princeton facility.
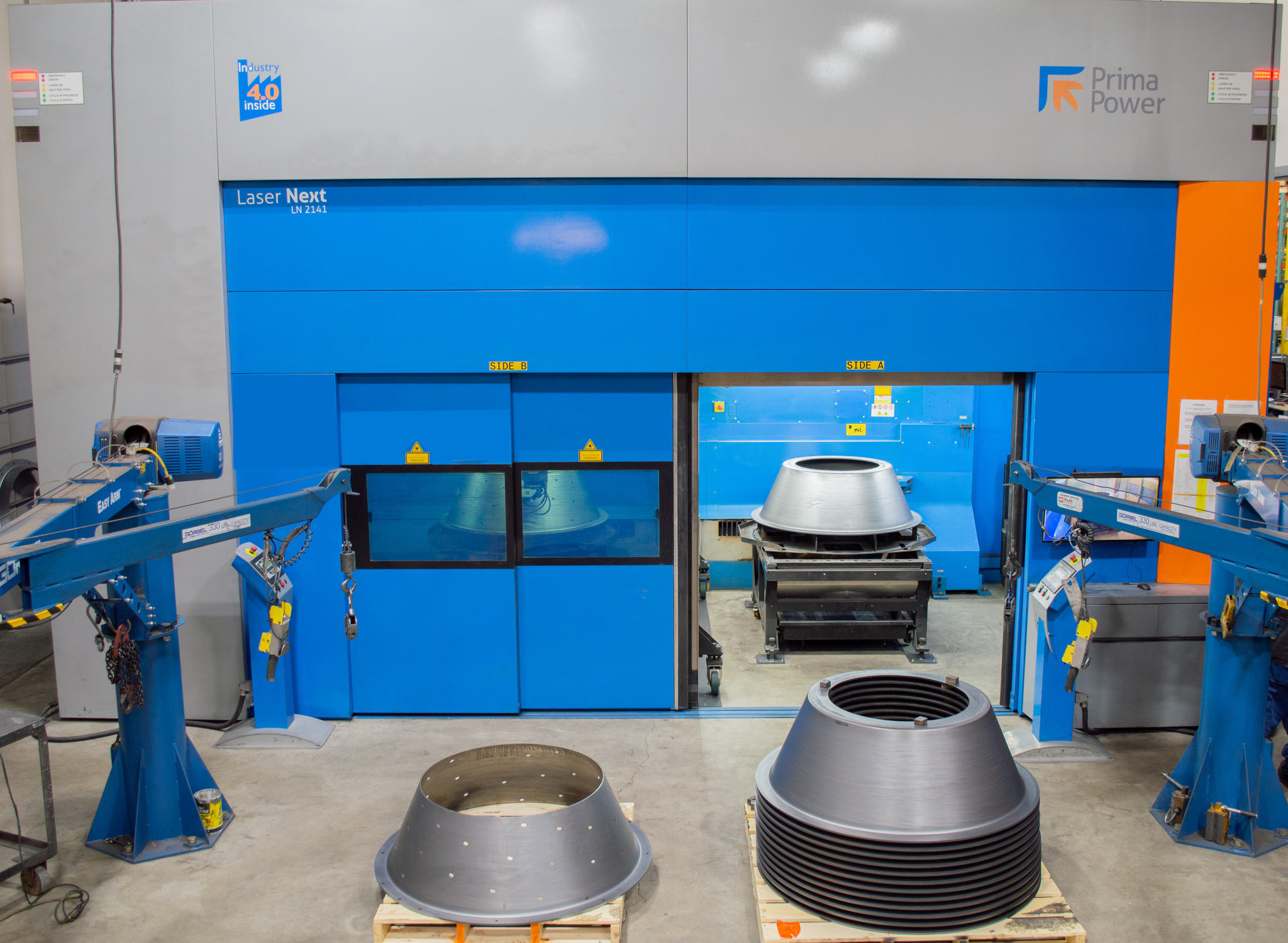
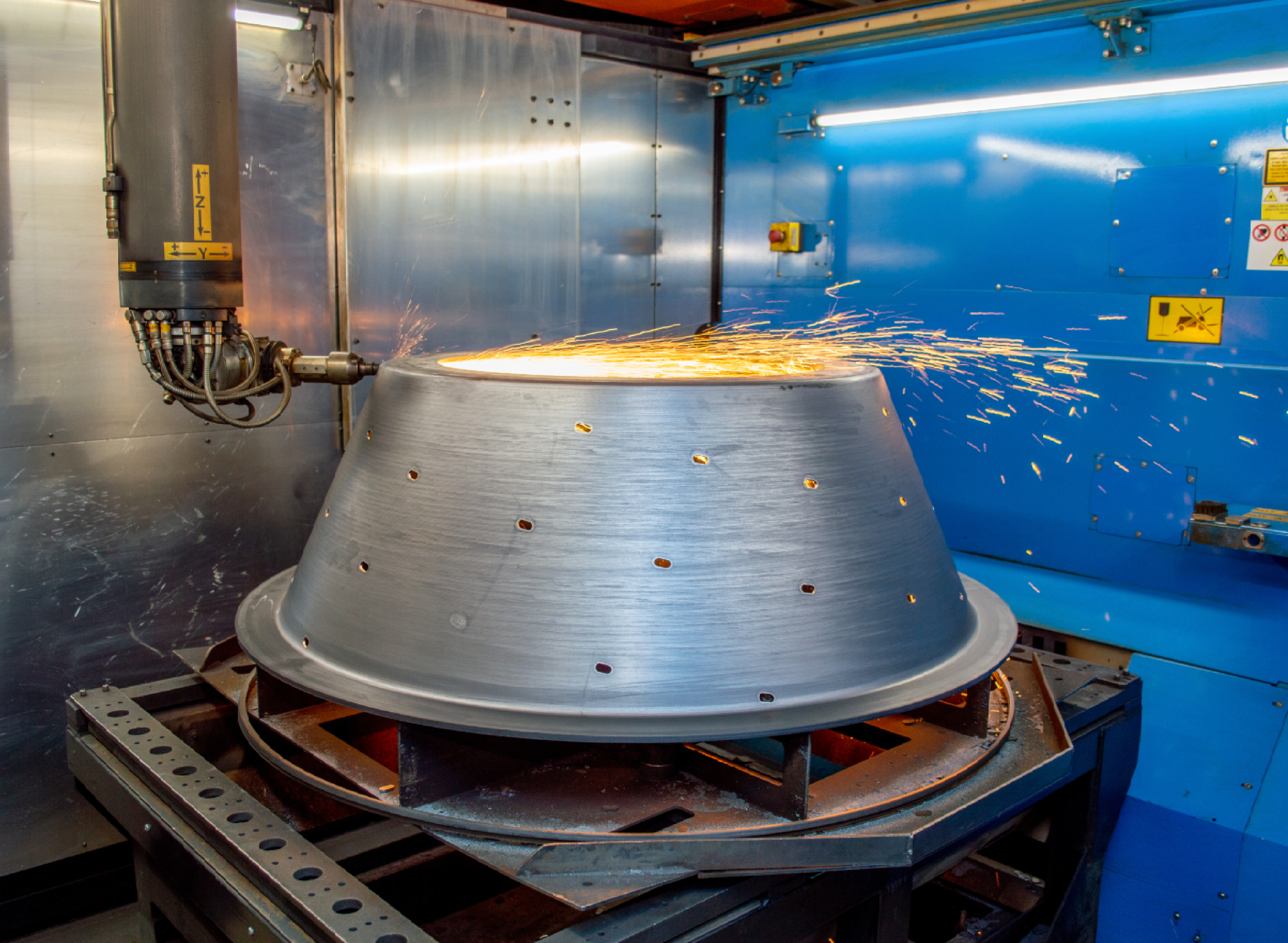
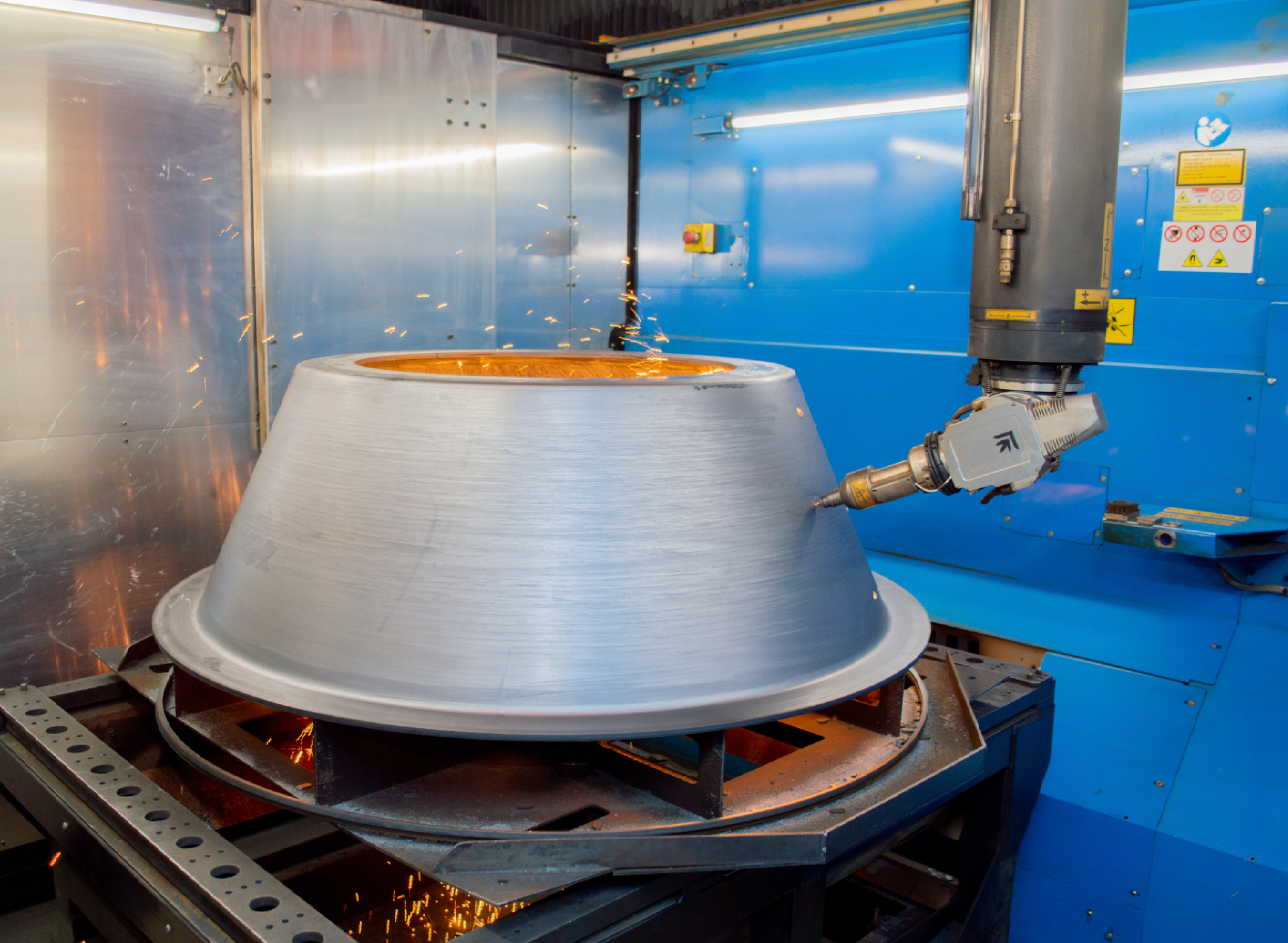
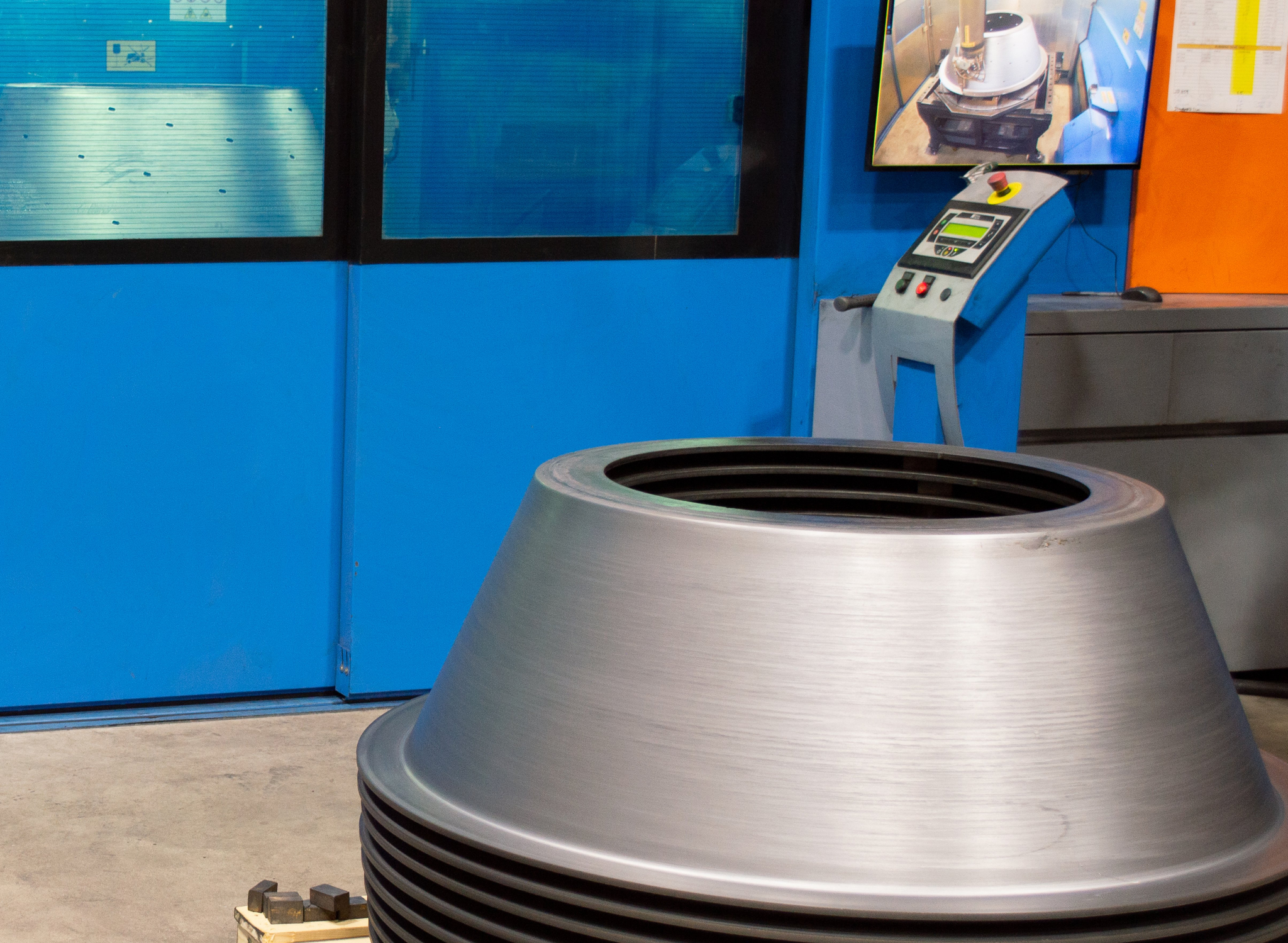
Our introduction into the U.S. market was in 1979 with our first 3D machine,” confides Dan Polto, sales engineer at Prima Power, the laser and sheet metal machinery business unit of Prima Industrie Group. As Polto describes it, "Prima Power broke into the United States and was used to cut bodywork for General Motor’s Cadillac division and we’ve been here in 3D ever since.”
In subsequent decades, Prima Power has serviced a wide range of industries, from automotive, aerospace and beyond, with an expanding catalogue of 3D lasers. The most recent is the company’s Laser Next line.
The Laser Next 2141 is the newest product in Prima Power’s 3D fiber-laser machine range. According to Prima Power, the working volume (4,140 x 2,100 x 1,020 mm) of this machine is the largest in the industry. At the same time, it has a compact footprint and is suitable for virtually all 3D-stamped and flat-sheet metal part sizes.
“The Laser Next 2141 is originally envisioned for large parts, but in truth it doesn’t matter how big the part is," Polto says. “They could process very large parts and very small parts. It’s just the fact that it’s a big machine, and I think the versatility of that is what really appeals to the market as a whole.”
The company says the Laser Next 2141 3D fiber laser is designed and developed to satisfy the needs of stamped-metal parts manufacturers in diversified industrial sectors, such as job shops, press shops, aerospace, agricultural, construction and automotive. The Laser Next 2141 also provides flexibility in terms of processes, part sizes and configurations. Its technological features allow it to process both three- and two-dimensional parts, and to switch from cutting to welding applications.
DIFFERENT CONFIGURATIONS
Laser Next 2141 is available in different configurations to suit various modes of production. The standard version with fixed tables exploits the entire working envelope to process large parts and features accessibility from all sides. With the split-cabin configuration, the working volume is separated into two halves by a removable wall and a sliding roof so parts can be alternatively processed or loaded/unloaded. “Glenn Metalcraft went a little bit further to take the splitcabin version, which allows them to load, unload, run in different parts in one work cabin while they’re processing parts on the other,” Polto says. When needed for larger parts, the wall can be removed to restore the entire working envelope. For faster part-handling operations without machine stops, a turntable configuration is also available. This solution is meant for large-series production of medium- to large-size parts. The shuttle table version allows the fast and automatic movement of parts and fixtures outside the working area from the sides or the front of the machine.
GO BIG
“We purchased the Laser Next 2141 to accommodate the large diameter of our parts,” Patnode notes. “We needed to purchase the biggest model available. The Laser Next has reduced our cycle time significantly. It has increased throughput by four or five times on some of our production projects. While there has been a learning curve with the new technology, the Laser Next has done a really nice job.” According to Patnode, the Laser Next 2141 is a user friendly machine, and Prima Power offers on-site training to Glenn Metalcraft operators to ensure competency. “Our operators have been really happy with the training they received… it’s a pretty intuitive system. Since our operators went to that beginning training they’ve been really competent with the equipment,” Patnode continues. “Today, it is just a matter of moving as much work as we can onto the Laser Next workcenter.” “The speed of the machine is phenomenal for lighter gauge materials,” adds Aaron Palmer, team leader for the laser and machine department. “I also like the fact that it can cut up to halfinch materials [12.7 mm]. The size of the cutting area is extremely important for us. We can remove the center wall in a matter of minutes and it more than doubles our single-cabin cutting space, which allows for our very large parts. “When we process our highest-volume part,” Palmer adds, “the twin-cabin capability allows us to switch back and forth from side to side. If we ran just one side per shift we would get 24 parts per shift. However, running both sides eliminates the load and unload time, and we produce 45 parts per shift. When we used to cut with the waterjet, we averaged 45 minutes for each part. Our cycle time on the Laser Next is eight-and-a-half minutes per part. I love the versatility of the machine. We can switch from oxygen to nitrogen cutting within the program. It doesn’t require us to stop and change a lens, we can just call out a material library right in the program. On some parts the thickness varies partway through the part, and I can change my cutting parameters mid cut to accommodate that thickness change.”
ADDING CAPACITY
Glenn Metalcraft is set to move into a larger Princeton location by the end of 2023. “This is an opportunity for us to capture some efficiencies with product flow, capture some efficiencies with different work cells and then also be set for some additional growth opportunity,” Patnode says. The move has prompted the company to purchase a second Prima Power 4-kW Laser Next 2141. This will allow it to maintain throughput during the transition and realize growth opportunities in the larger facility. “We are on a strong growth pattern, and we are projecting significant growth over the next four to five years,” Patnode notes. “We have been consistently moving production from other areas in our shop to the Laser Next work center. In addition to providing the extra capacity, the second machine, allows us to avoid any downtime in moving the current Laser Next to the new facility while still maintaining our consistent production levels.”
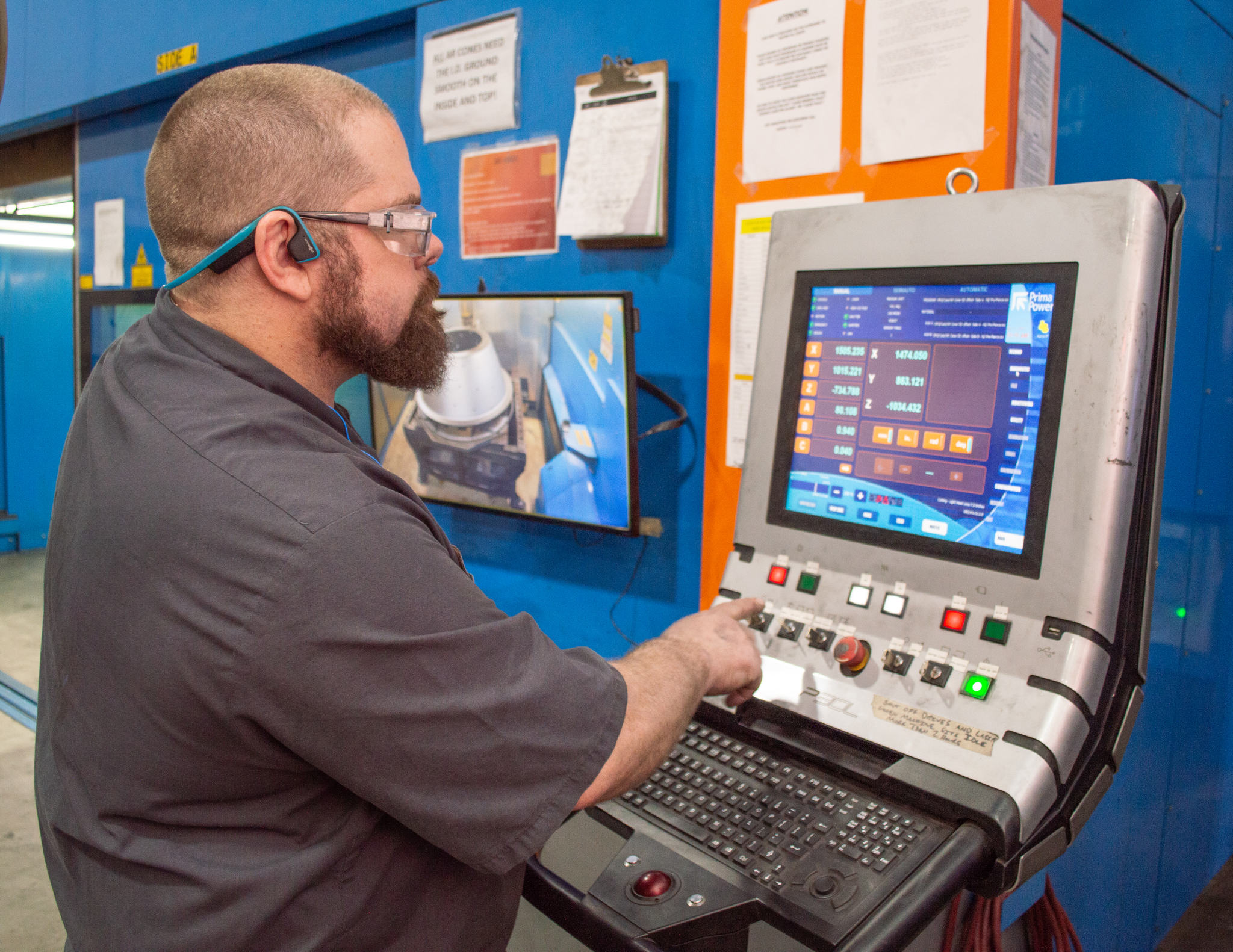
The Laser Next has reduced our cycle time significantly. It has increased throughput by four or five times on some of our production projects.
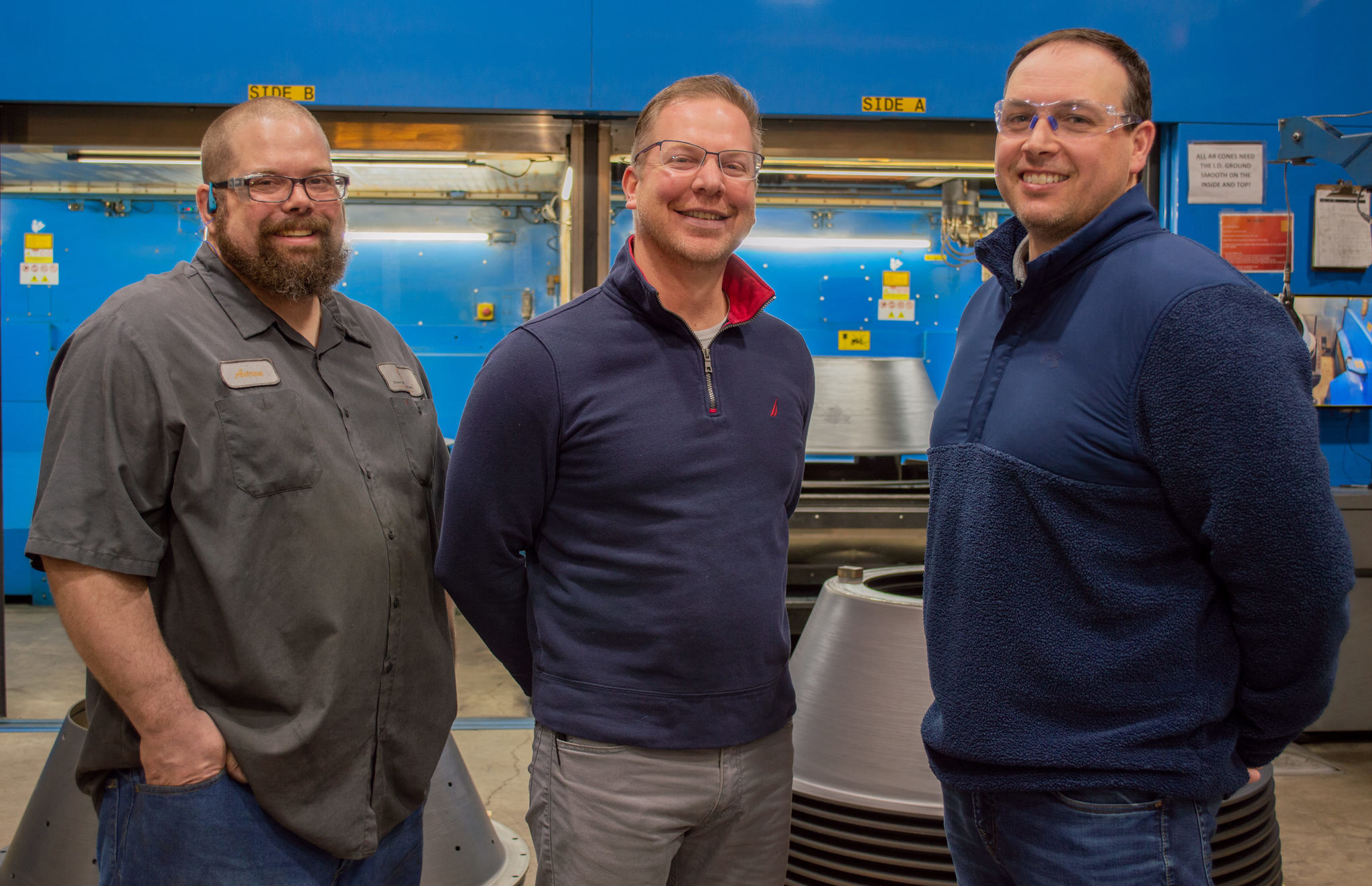
Are you looking for a similar solution for your company? Find it here
Laser Next 2141
3D-LASERSKÄRNINGSMASKINER