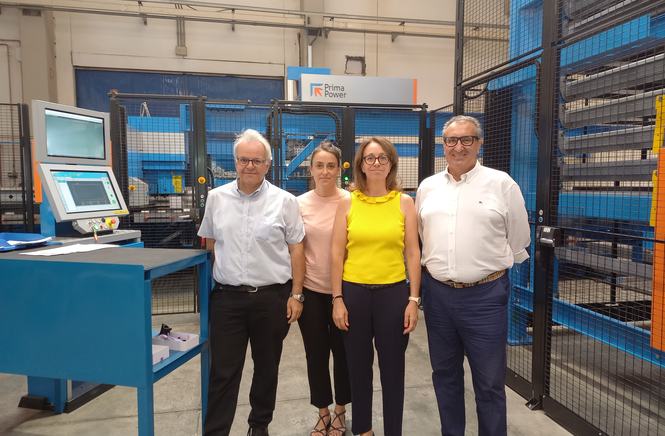
DAV, Innovators by tradition
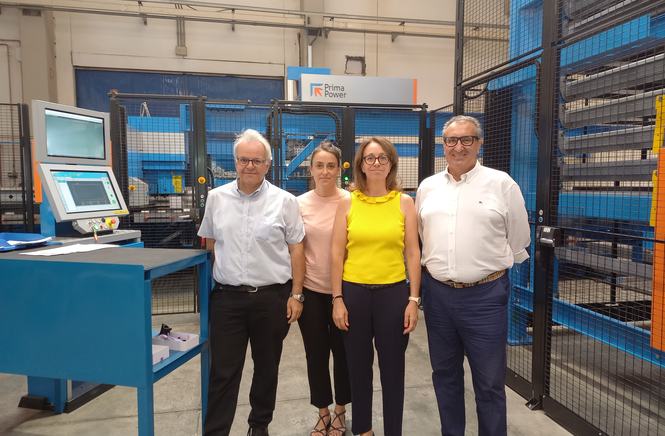
Industry 4.0 before the definition even existed and always oriented towards investing in new technologies, the DAV metalworks company in Rho has decided to focus on a highly automated Combi Genius 1530 laser and punching machine from Prima Power to increase production efficiency and expand the range of machining operations that can be performed directly on the machine.
Addressing many sectors can mean presenting yourself as a generic supplier, that is, capable of providing a useful service to many different businesses. For DAV, a metal carpentry company in Rho (Milan) founded in 1969 by Angelo Vavassori and now run by his son Stefano, and his daughters Barbara and Claudia, the ongoing challenge is to address very different target audiences and industries with expertise and technologies that will enable them to provide specialised services with high added value.
"DAV," Stefano and Barbara Vavassori explain, "is a multi-sectoral business because it is able to provide a complete and specialised service to very different companies (from automotive to pharmaceutical, right through to oil & gas, intralogistics and rail companies). As a metalworking company, we have developed a wealth of expertise; our staff's know-how and state-of-the-art technology allow us to manufacture different products through laser cutting, punching, bending, welding, painting and assembly - while optimising time and costs for greater customer satisfaction. We are a true one-stop partner in carpentry work.
" DAV is not limited to sheet metal working, it also provides specific services that are highly appreciated by customers. "We provide all-round customer support," Stefano Vavassori continues, "we contribute to developing construction solutions to perfect the customer's products, we propose improvements to production, and we prepare technical documentation (dimensional reports, welding books, PPAP documentation, FMEA analysis and certifications), providing 15,000 square metres of production space to manufacture and store products according to our customer's needs. It is important to emphasise that DAV has acquired complete knowledge over time of its customers' product types and related manufacturing issues, and this allows the company to provide valuable support in all sectors.
"It is not easy to maintain this horizontality," explains Barbara Vavassori, "indeed, it requires a commitment to always keep up to date technologically to understand the specificities of the different products and obtain the specific qualifications for that sector. DAV invests a lot precisely for this reason both in technological innovation and to maintain a high skill level, facilitating the transfer of knowledge from experienced operators to new ones, with targeted courses and on-the-job training."
In addition to presenting itself as a true partner alongside the customer, these skills create a virtuous circle in which DAV and its customers exchange skills and experiences useful for growth and innovation.
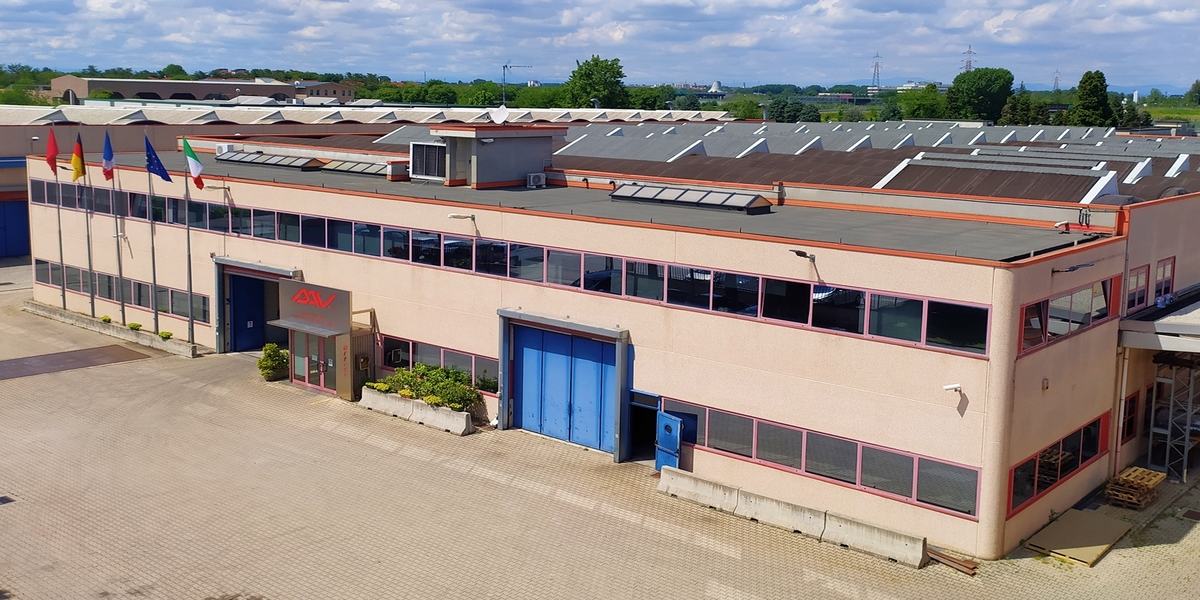
INNOVATION AT THE CUSTOMER'S SERVICE
A distinctive trait of DAV's entrepreneurial history is its willingness to always invest in innovative technologies, by identifying solutions in advance to meet its customers' needs.
"Our father," recalls Barbara Vavassori, "was one of the first in Lombardy in the 1990s to purchase a laser cutting machine: innovation has always been an element of differentiation for us, which is also demonstrated by our decision to adapt the production process and company management system to ISO 9001 quality standards as early as 1999 and to invest in an automatic sheet metal warehouse a few years later. We are talking about a company that completed the integration and interconnection of warehouse, production and design even before the concept of Industry 4.0 emerged.
"DAV had already been Industry 4.0 for laser cutting processing for many years," the owners explain. "In 2005, the in-house development of dedicated software meant that processing plans were sent from the technical department to the laser machines and then all production data was automatically written into the management system at the end of the production process, updating cutting times, quantities and raw material stocks."
The recent investment in a Combi Genius 1530 punching and laser cutting machine from Prima Power with a 4 kW fibre laser source, 3,000 mm x 1,500 mm work table and high automation is part of this strategy of continuous innovation.
"We had already been thinking about a machine like this for a few years," says Stefano Vavassori, "but in the last few years the quantity of parts requiring both cutting and forming had grown a lot. This involved first performing the cutting operations on a laser machine, then moving the parts to the punching machine to perform the other operations. This meant a huge waste of time and the rising prices of raw materials meant we were in danger of no longer being competitive in the market for these products. The lockdown was an opportunity to address this need and to search the market for a solution.
"We were all stuck at home, so we went to Prima Power's website and asked them to contact us for more information about the Combi Genius which, at that moment, seemed to be the right machine for our production requirements".
At that point, and with great ease, a relationship of exchange and mutual acquaintance began between the two companies, which allowed us to further focus on DAV's needs and the most suitable Prima Power solutions.
"With Prima Power, we were able not only to visit companies already using the Combi Genius, but we also carried out a series of tests at their factories to produce certain types of parts. The result was astonishing: when I saw the videos and production reports, we realised that it was the perfect machine for us as it allowed a reduced production time of more than 60 per cent."
Also crucial to this investment was the automation component, or rather, an LSR loading, unloading and stacking robot and a double Combo Tower storage system. "Since we already had a high level of integration between production, warehouse and technical office," explains Barbara Vavassori, "it was also quite easy to interface our management system with the Prima Power plant, which as we said earlier is supplied ready for 4.0 and with dedicated software.
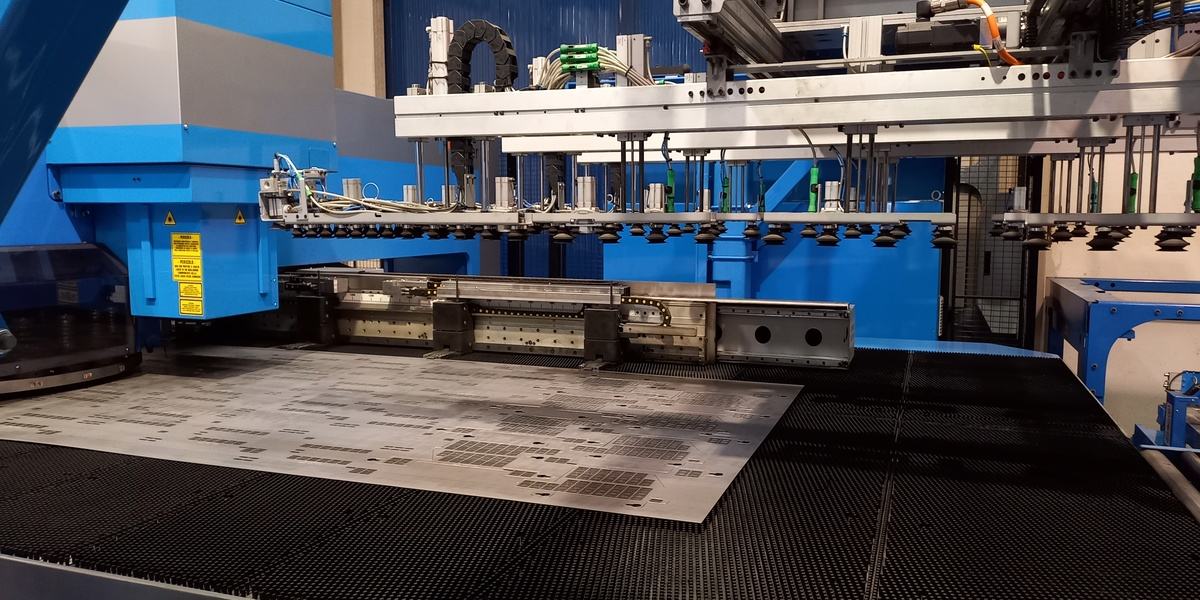
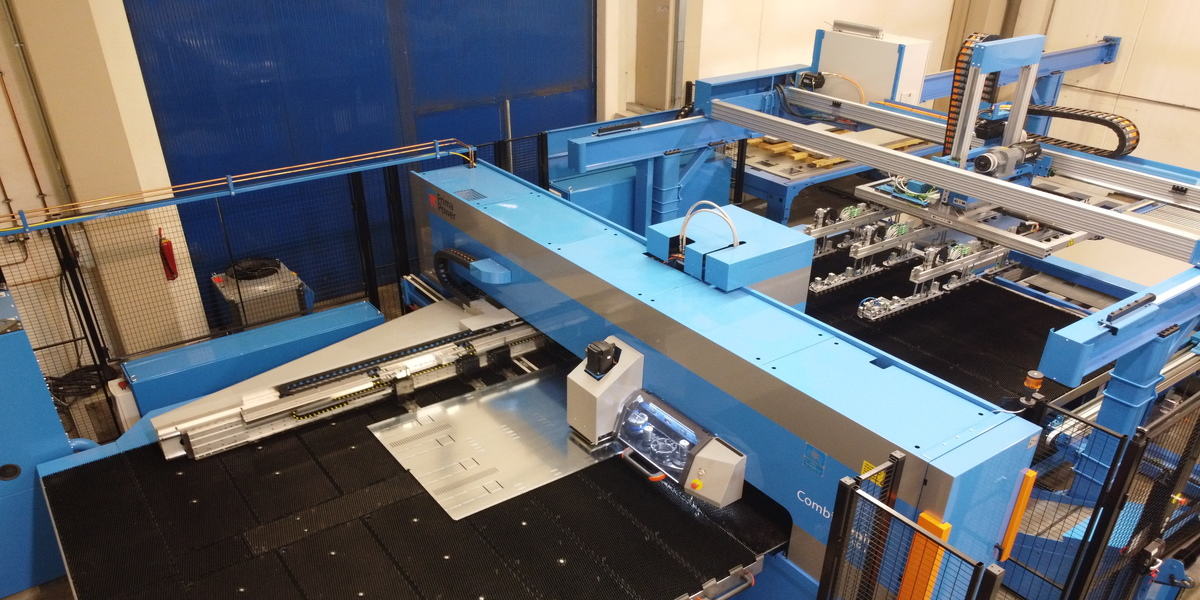
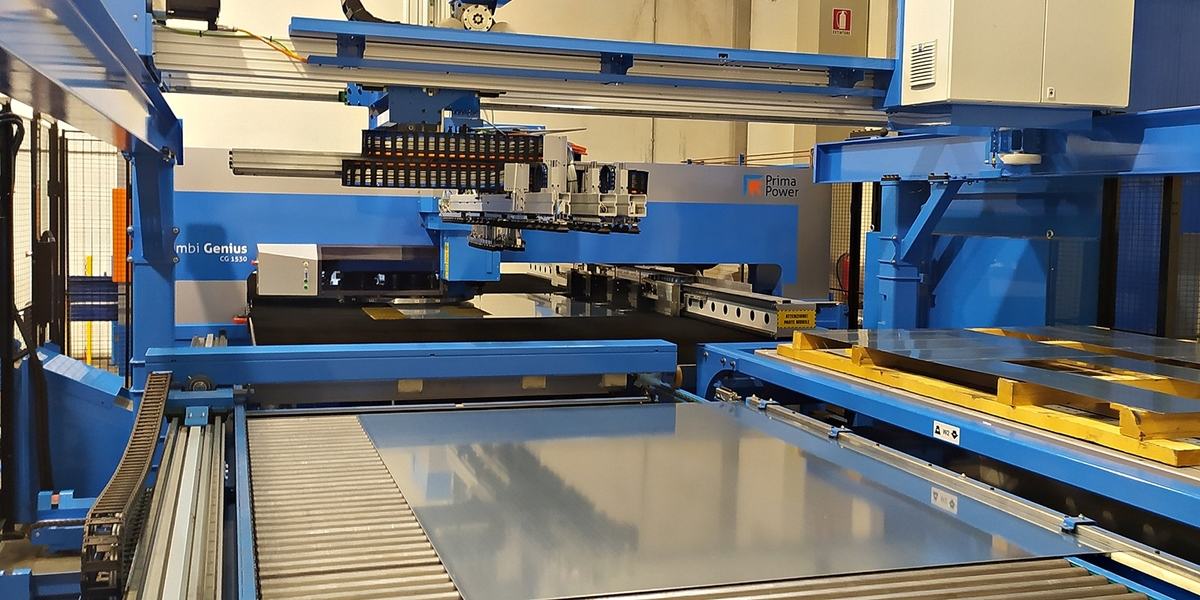
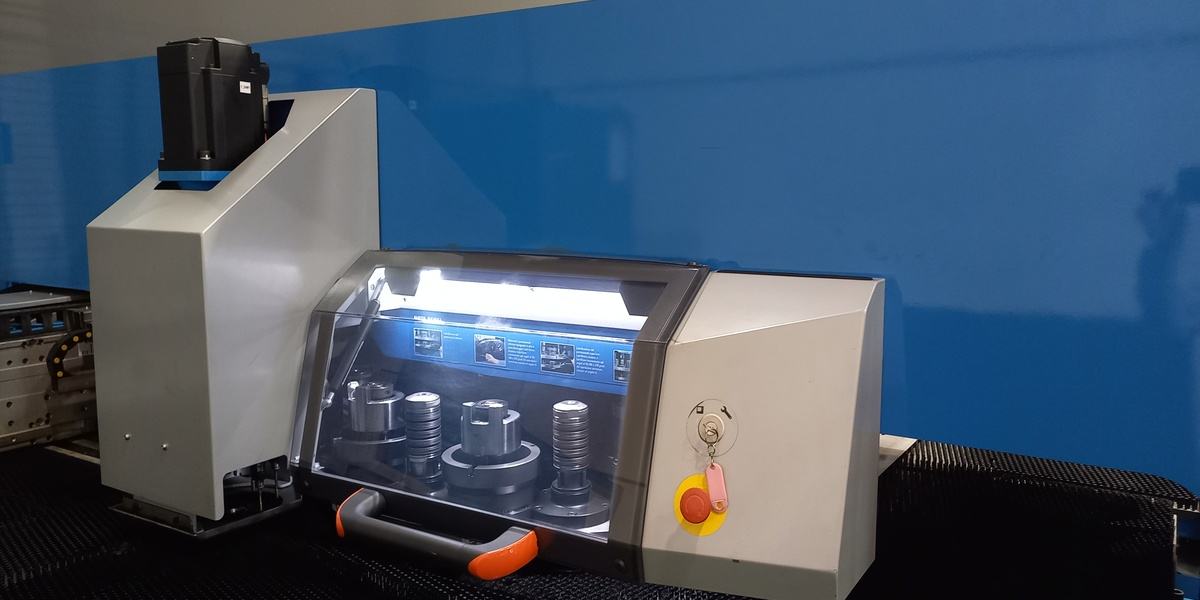
THE ADVANTAGES OF THE COMBI
The Combi Genius 1530 has been in operation since May 2021 and in its past months of use, it has given DAV several advantages, starting with a significant increase in productivity compared to the past, when these processes require a double run on two machines (laser cutting and punching machine).
"Another advantage is that we have been able to 'offload' some of the machining from the laser machines, given that the Prima Power combi has also proved to be an excellent solution for performing several cuts. As an all-electric, low-power machine, the Combi Genius was the ideal solution at a time when energy and nitrogen costs have skyrocketed, and this is supported by the fact that, although DAV has increased its turnover, it has reduced its electricity consumption this year.”
After a few weeks of using the Combi Genius, other advantages have also emerged, including the possibility of marking workpieces using the same set-up.
"At DAV, we need to mark all workpieces with a string, which we previously did by hand using presses. We can do this directly on the machine using the Combi Genius thanks to some specific tools that work by stamping or engraving."
Since the Prima Power Combi is a servo-electric machine, it is particularly effective in these operations since you have complete control of the punching axis, and you can decide the penetration and relief for marking.
It is worth emphasising that, thanks to the Prima Power combi, DAV has not only succeeded in entering new markets, but has also expanded the range of forming operations it performs, making use of the Combi Genius capabilities to perform operations directly on the machine that previously required the use of dies.
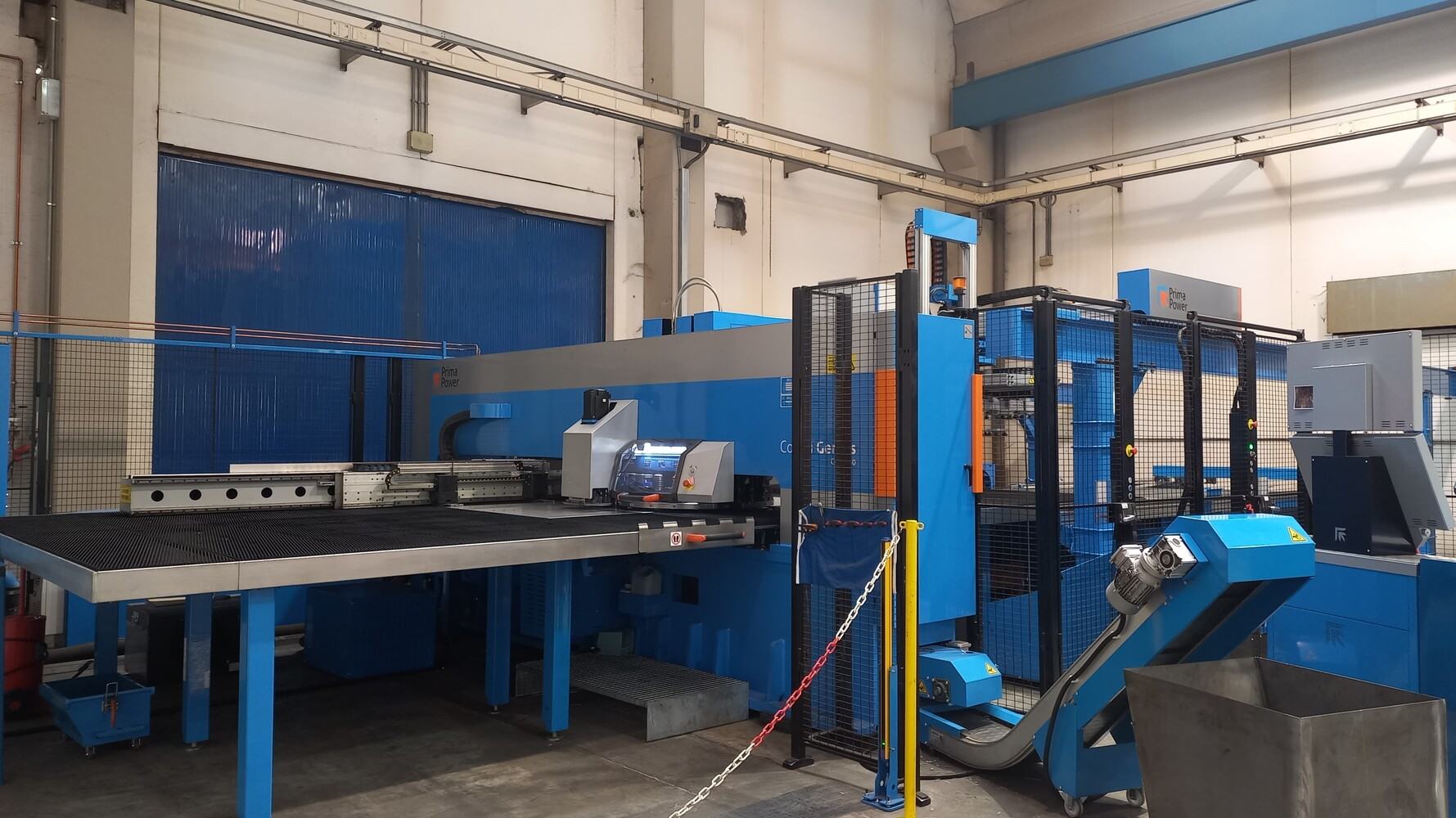
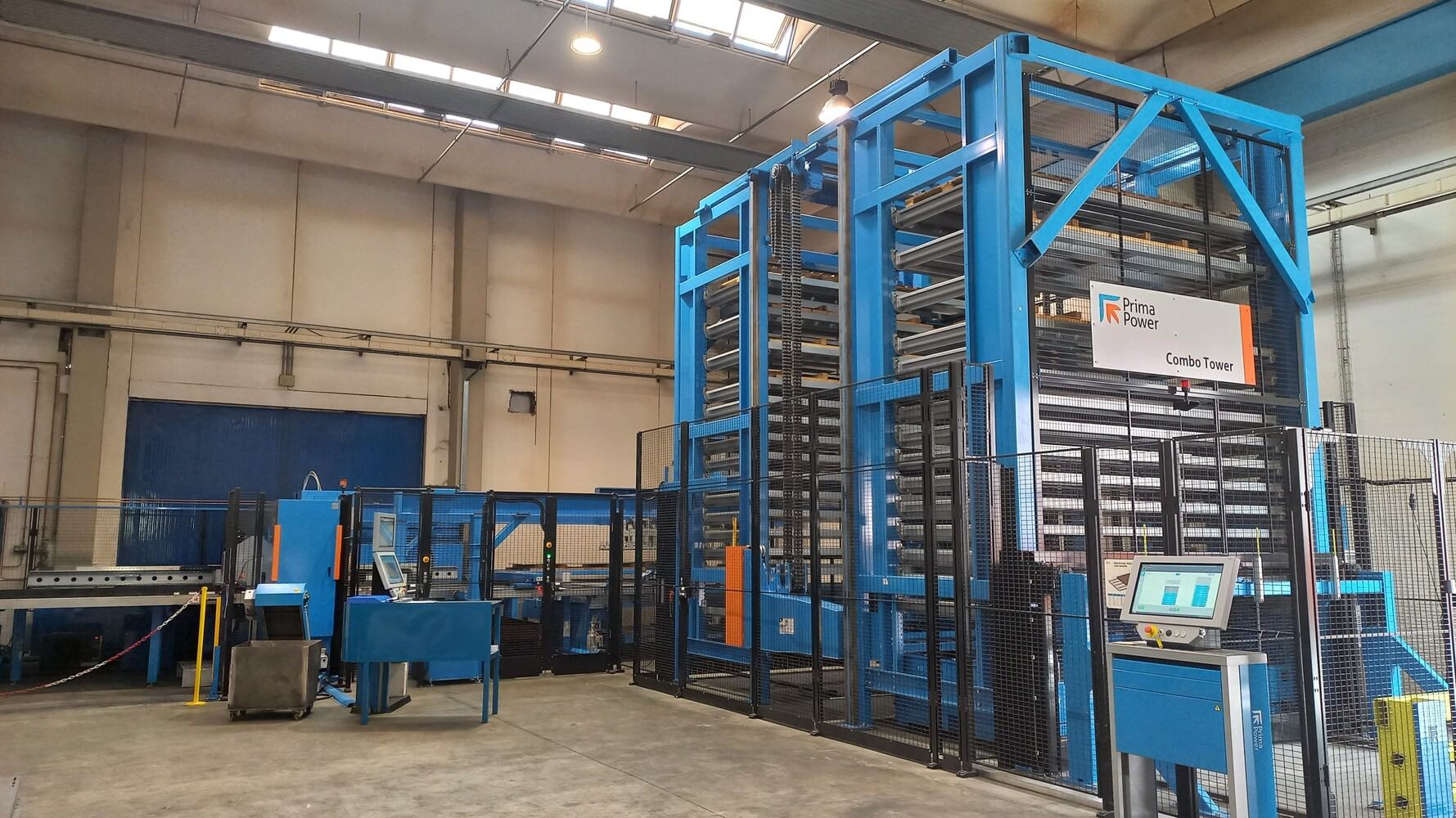
AUTOMATING... IN A SMALL SPACE!
Looking at the impact of the Combi Genius installed at DAV, we can see that the combi machine is always able to deliver the workpiece finished and clean.
"I am certain that to reduce machining times, it is more important to automate the loading and unloading section rather than increase the power of the source,'' Stefano Vavassori confirms.
"In fact, we had requested an LSR robot (Loading and Stacking Robot) from the outset to avoid manual intervention, both for greater operator safety and to avoid damaging the machined parts. It is worth noting that RALC technology (Robot Assisted Last Cut) has been provided on the LSR robot to increase the reliability of the laser-cut part pick-up process. During the last cut, the machine and robot make simultaneous and synchronised axis movements, ensuring safe and reliable part pick-up.
"For us," continue the owners of DAV, "it was also particularly important that Prima Power provided two drop doors on this machine to allow several unloading modes: directly into the drop door for small parts but also individually onto external pallets. Automated unloading is fundamental for us, we have already been linking laser machines to warehouses for years and we know the advantages this brings. It's precisely for this reason that we decided to connect an automatic storage system to the Combi Genius 1530, thus transforming the plant into a real machining cell.
"I believe the future means having automated production cells, perhaps working in parallel, which carry out the various processes with maximum flexibility. In this scenario, it is also essential to provide interconnections with automated warehouses.
" DAV has chosen to invest in a double Combo Tower storage system for the Combi Genius, which is Prima Power’s solution for flexible storage and the automation of the flow of material in its various stages: raw, semi-finished and scrap. The Combo Tower makes different materials available as soon as they are needed, automatically and without delay; it can also serve as a buffer or intermediate storage for finished components.
"From the very first layouts, we opted for a twin tower solution that greatly increased the autonomy of the cell with a minimal increase in footprint."
The issue of the plant's footprint was, as is often the case for Italian companies, the real challenge: finding space in the warehouse was not easy.
"The compactness and modular structure that characterises Prima Power solutions is what really helped us a lot," explains Vavassori. "Moreover, thanks to the LSR robot, handling workpieces takes up little more space than a stand-alone machine."
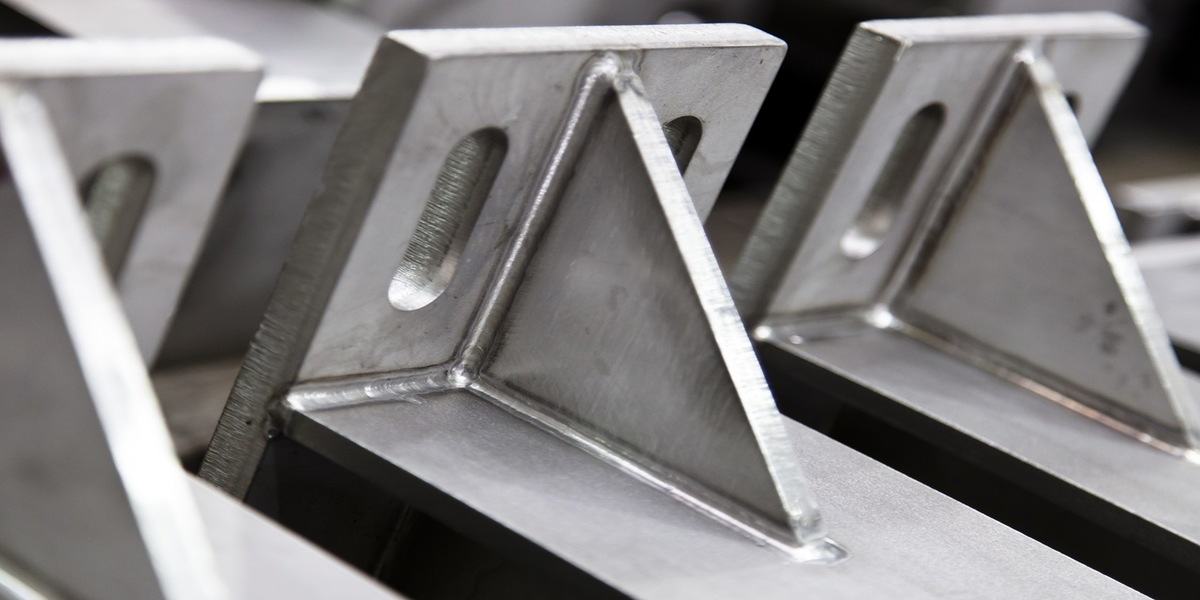
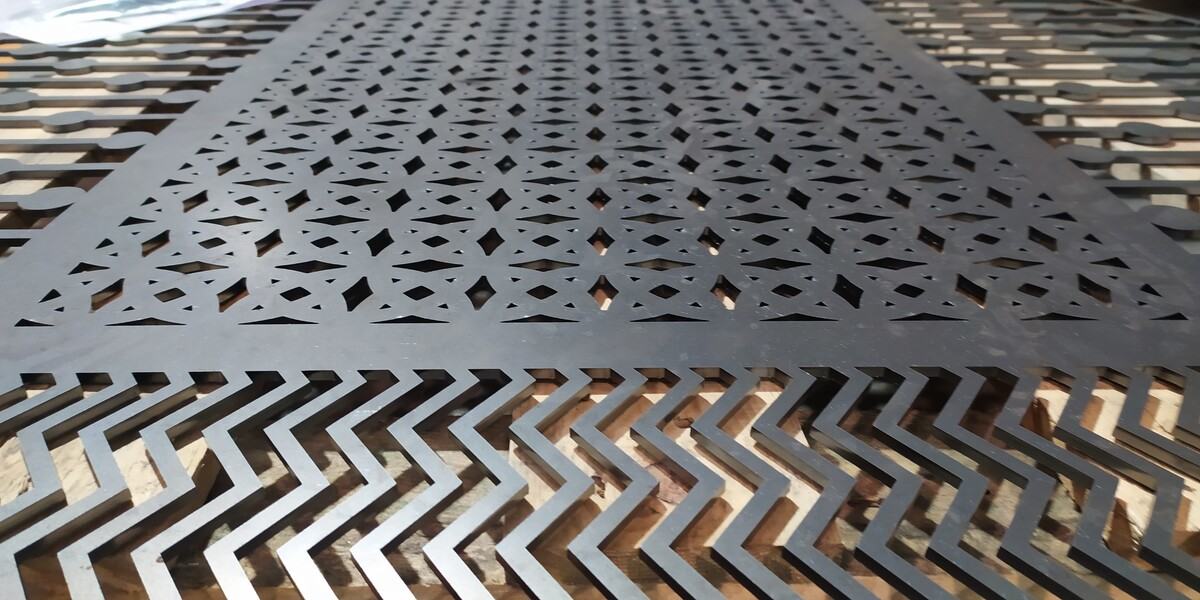
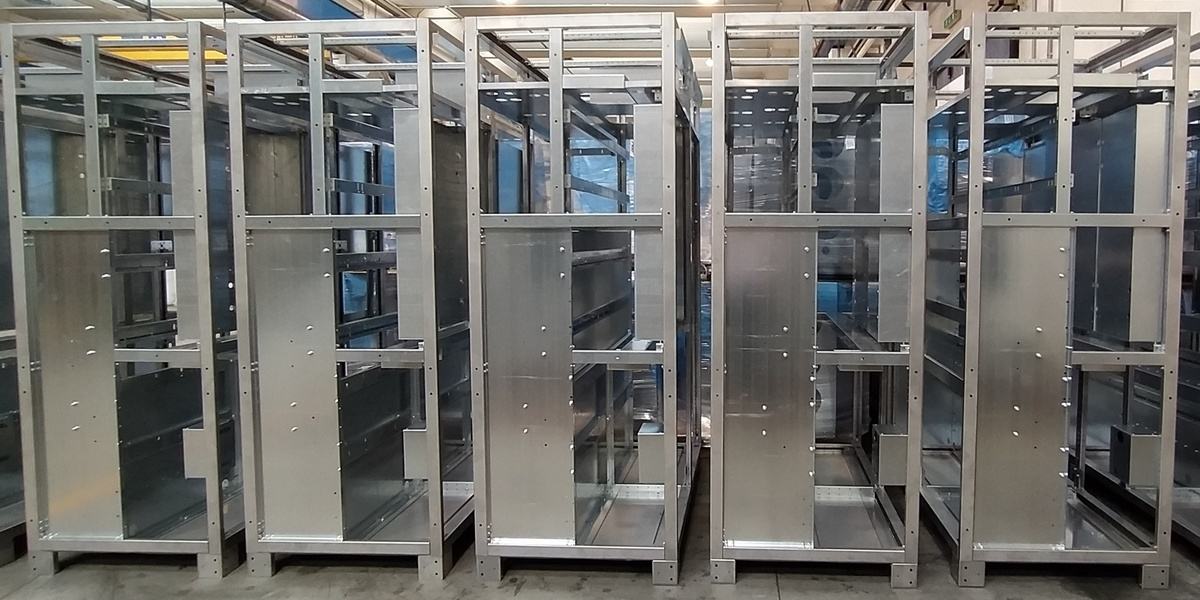
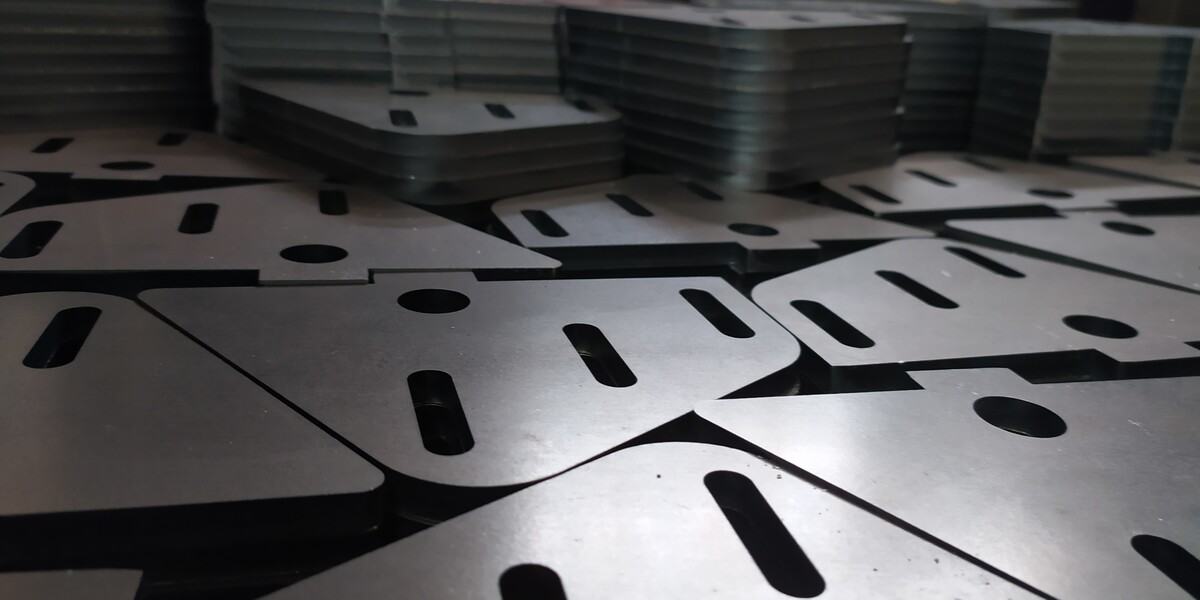
With Prima Power, we were able not only to visit companies already using the Combi Genius, but we also carried out a series of tests at their factories to produce certain types of parts. The result was astonishing: when I saw the videos and production reports, we realised that it was the perfect machine for us as it allowed a reduced production time of more than 60 per cent.
Are you looking for a similar solution for your company? Find it here
Combi Genius
ZIMBALAMA VE LAZER KESİM KOMBİNE MAKİNELERİ
Zımbalama+ Lazer kesim = Üst düzey üretim ekonomisi
1+1>2
Yükleme ve istifleme robotu (LSR)
MALZEME TAŞIMA