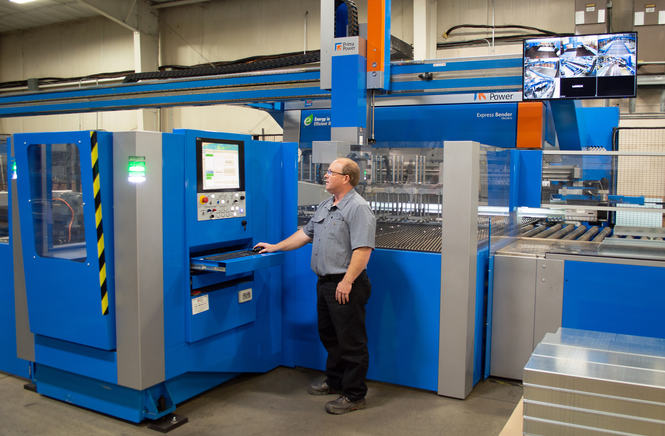
Raytec, always with an eye toward automation
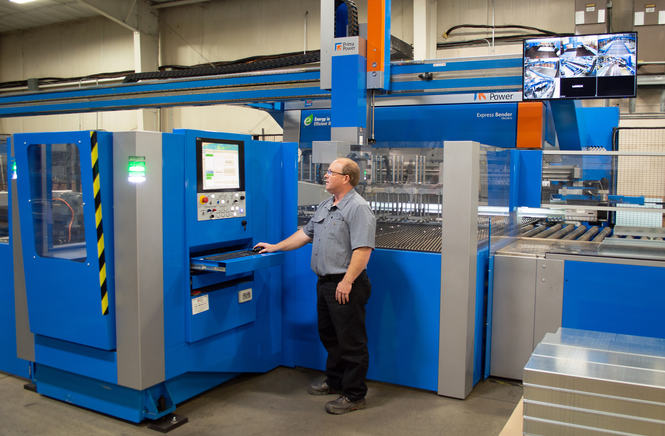
Raytec LLC, a fourth-generation Pennsylvania family business, has experienced rapid expansion by investing in Prima Power equipment and turning their operation from completely manual to fully automated.
How to boost production capacity in sheet metal fabrication? Glen Zimmerman, owner of Raytec LLC, New Holland, PA, has a simple philosophy: Automate production wherever possible. Raytec is now in its fourth generation of family management. Zimmerman’s grandfather founded the company in 1956 producing mainly building products. His father named the company Raytec in 1971 and expanded the company’s production line to include agricultural equipment, and added a shear, press brake, and spot welder to the equipment list.
Today, the company has grown to fill a 44,000-square-foot facility with an extra 46,000-square feet of space that will be completed in 2023. In addition to the building and agricultural products, the job shop market is now a growing area of the company’s rapid expansion. “We try to maintain diversity so we are not just locked into one segment of the business,” explains Zimmerman.
“We bought our first CNC press brake in 1992. We had a CNC stand-alone turret punch press for a number of years that was a manual load/unload. As our production demand kept growing over the years, we saw the need to invest in automation in order to minimize labor, maximize throughput, while increasing accuracy.”
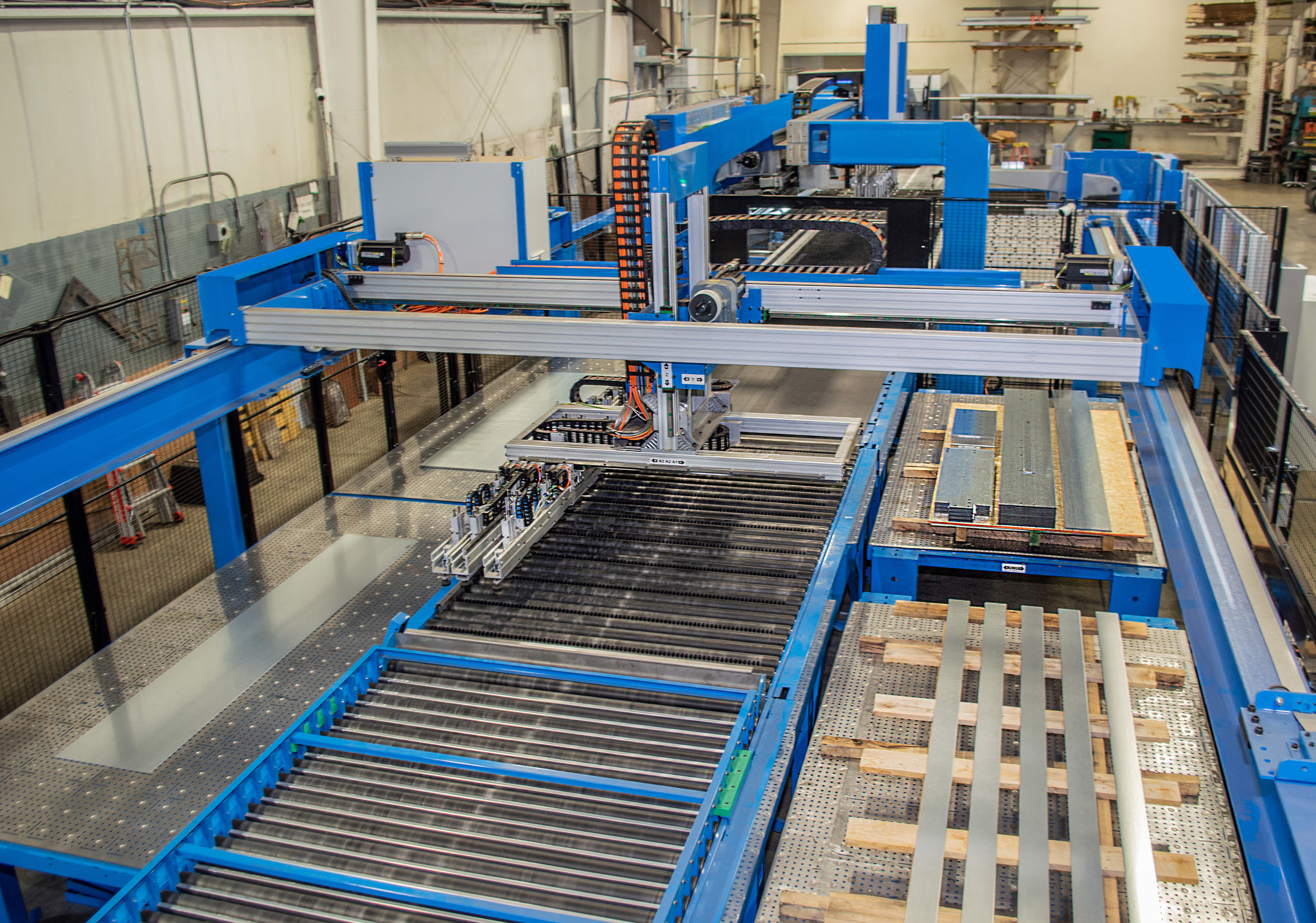
RAYTEC LLC’S PATH TO AUTOMATION WITH PRIMA POWER
In 2015, the company purchased a fully-integrated automated system from Prima Power. The first stage included a Shear Genius servo-electric punch/shear combination SGe8 with a C1500 sorting conveyor.
With the Shear Genius concept, the objective is to provide a machine capable of transforming a full-size sheet into finished parts. These parts can be moved to the final production stages for immediate integration directly into the final product assembly.
“We went from a completely manual operation to an automated process,” says Zimmerman. “Because we are a job shop, we never know what job is coming through our door next. We needed the most versatile machine tool that we could purchase. We chose Prima Power also because we liked the way it integrates the software control to the machine. A big plus for us was the servo-electric feature: we went from the hydraulic world to servo-electric world and we are very happy with that process.”
“We were impressed by how easy it was to upgrade with Prima Power,” continues Zimmerman. “We talked to them about upgrading and adding more equipment down the road. Prima Power had a clear path forward to allow that to happen.”
Raytec’s ultimate goal was to complete the installation of a compact Prima Power PSBB line (Punching/Shearing/Buffering/Bending) to process blank sheets into ready-bent, high-quality components automatically. The Combo Tower storage allows the processing of components from a variety of materials, which can be changed, as programmed, automatically. The sheets are transferred into a Shear Genius punch/shear cell. After shearing, the components are sent to buffering and subsequent bending in an automatic bending cell. By 2020, Raytec had begun the process for total automation.First, a 14-station Combo Tower was installed. “This allowed us to load and run multiple materials very efficiently and quickly,” explains Zimmerman.
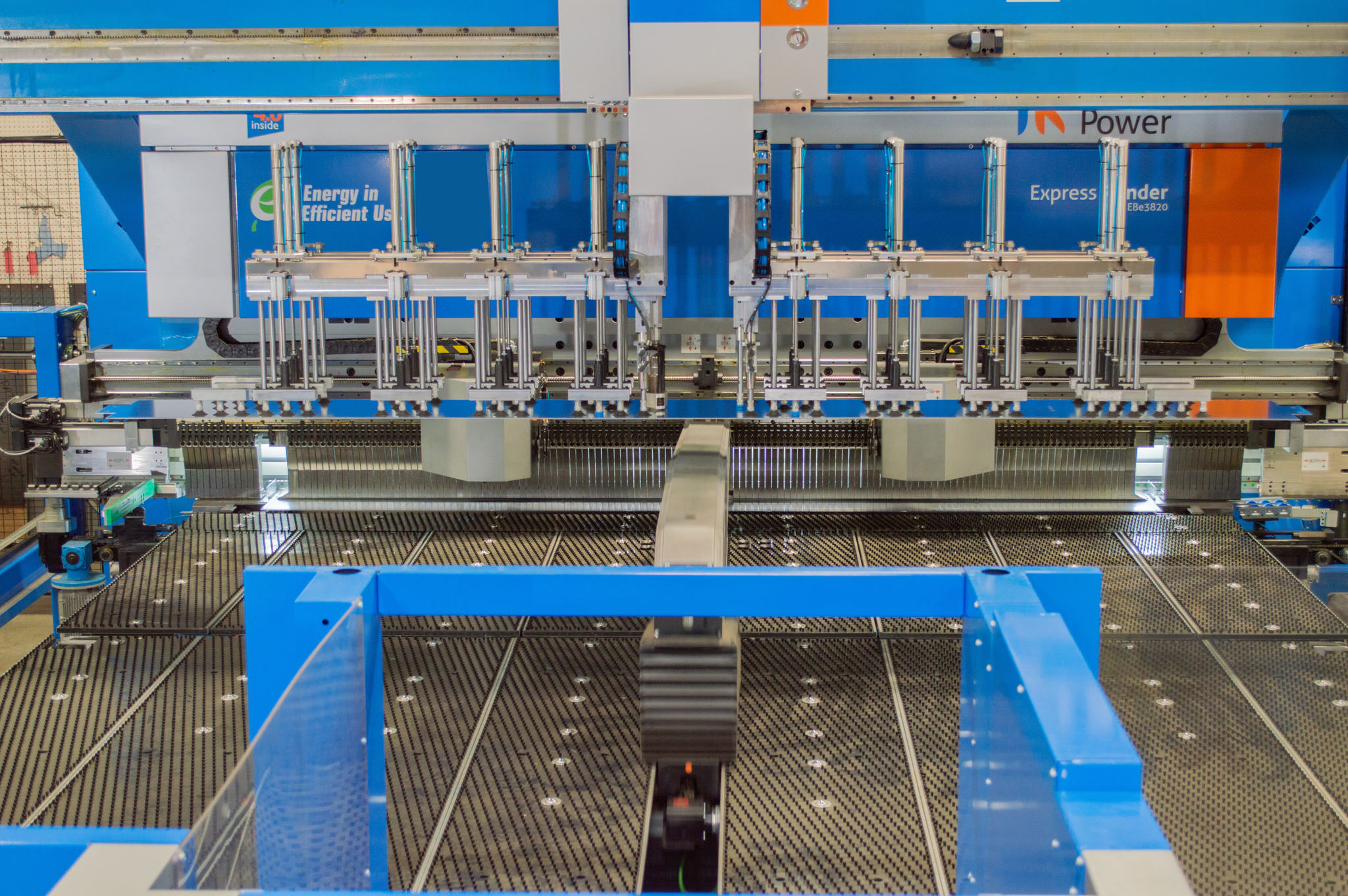
THE BENEFITS OF AN INTEGRATED PANEL BENDING LINE
The company also purchased Prima Power EBe servo-electric Express Bender, a bending solution that is designed specifically to achieve maximum productivity, quality, and repeatability.
At the same time, the company added the PSR stacking robot which provides high flexibility and allows it to automatically stack larger parts. Material flow can be arranged to transfer parts directly to automatic bending, to balance the different time requirements of bending and punching/shearing, to exit material from the system, and to bring new material into it.
Parts are always placed directly to the stack and never dropped. The PSR with buffering functions allows the reorganization and optimization of production flow from the Shear Genius to the EBe.
“The bender has been phenomenal,” confirms Zimmerman.
“I would not want to be without it. We were looking for flexibility and versatility being the key to the job shop business. On our customer side, we were seeking ways to fulfill missed opportunities. We saw that there were very few, if any, integrated panel bending lines in the job shop market. This allowed us to open up the small- to medium-sized volume market to have fully-integrated panel bending capabilities in the job shop market. Historically, most of the panel bending lines have been found in dedicated manufacturing lines.”
“The Prima Power solution has other benefits,” adds Zimmerman. “The bender is integrated in line to the SG, so there is no material handling in parts coming down the line. The programming of parts is a fully-automated setup. We don’t touch the part until we unload it and stack it on the pallet. That is the first human intervention needed on the entire line. This solution allows us to maintain the quality, the consistency, and fast throughput with very little labor involved.”
UNLOCKING NEW CAPABILITIES THROUGH PRIMA POWER AUTOMATED SOLUTIONS
“The Prima Power equipment is very efficient because of the servo-electric system,” reflects Zimmerman. “It is highly versatile, it has increased our capability and sped up our turnaround times, while improving part accuracy and consistency. But most importantly it gave us the capability to run three shifts with the one-shift operation. It increased our capacity dramatically.”
Once the new addition to the building is complete, Raytec will continue to evaluate further automation options from Prima Power, such as coil cut-to-length integration and the Night Train FMS automated material and information system.
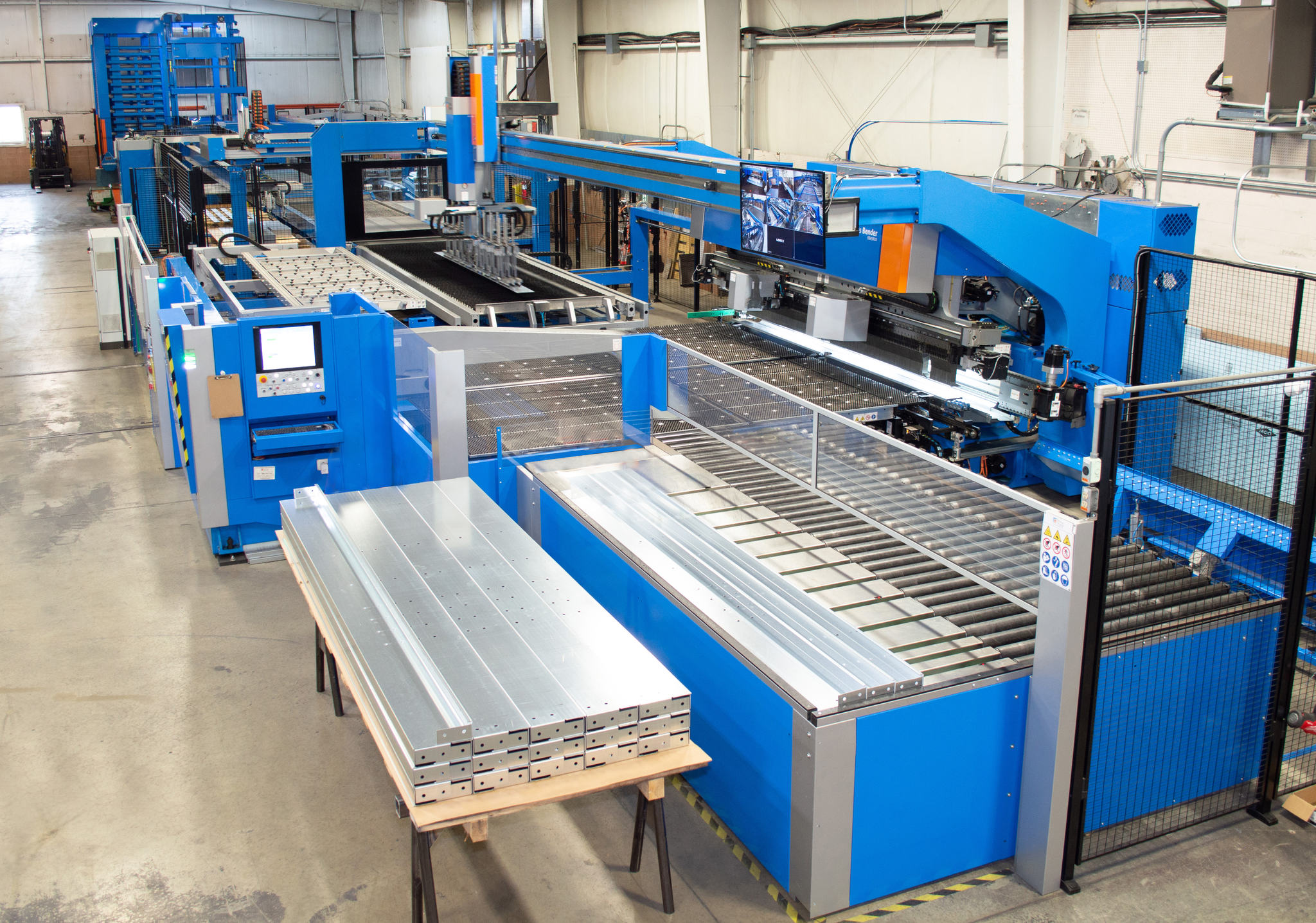
Portions of this article were used in the article that appeared in the March, 2023 issue of the FABRICATOR.
On our customer side, we were looking at ways to fulfill missed opportunities. One of them that we saw was that there were very few, if any, integrated panel bending lines in the job shop market.
Are you looking for a similar solution for your company? Find it here
Shear Genius EVO
ZIMBALAMA VE KESME KOMBİNE MAKİNALARI