
Raytec, 항상 자동화를 생각하며

펜실베니아의 작업장은 펀칭/전단기에 자동화된 자재 처리 및 자동절곡기를 추가하여 생산 능력을 향상시켰습니다.
조직 사회에 적합한 금속 가공 회사를 찾는 것은 수년간 지속적인 과제였습니다. 물론 최근에는 요식업, 접객업 등 다른 경제 분야에서도 시급이 높아지면서 신입사원 채용 경쟁이 더욱 치열해지고 있습니다.
이러한 지속적인 추세에 대처하기 위해 금속 제조 업체는 작업장에서 제조 활동을 자동화하는 데 최대한 많은 투자를 하여 직원들이 더 복잡한 작업을 처리할 수 있도록 했습니다. 그러나 일부 사람들에게는 이것은 새로운 전략이 아니었습니다. 예를 들어, Raytec Fabricing사는 몇 년 동안 불길한 징조를 느끼고 수년간 더 생산적인 제조 기술을 구입했을 뿐만 아니라, 각 구매에 따른 자동화된 미래를 계획했습니다.
이 모든 레이저 절단력은 벤딩 작업에 추가적인 부담을 줍니다. 단순히 프레스 브레이크를 추가하는 것은 답이 아닙니다. 숙련된 브레이크 작업자 또는 이를 배우는 데 관심이 있는 사람을 찾는 것이 그렇게 쉽지 않기 때문입니다.
"우리는 곧 성공적인 자동화를 위해서는 이 여정을 계속해야 한다는 것을 알게 되었습니다."라고 Zimmerman은 말했습니다. “[펀칭/전단 장비에] 스태킹 로봇을 추가하려고 했을 때였습니다. 당시 우리는 자동 패널 벤딩에 대해 별로 생각하지 않았습니다. 적어도 해당 유형의 기계에 적합한 작업을 수행할 기회가 생길 때까지는 말입니다.”
원래 2015년에 구입한 Prima Power Sher Genius SGe8 펀칭/전단 복합기에 패널 벤딩 장비를 추가한 것은 보다 자동화된 미래를 향한 회사의 원래 계획에 걸맞는 확장이었습니다. 콤비네이션 장비의 스태킹 로봇은 자재의 이동 및 보관 과정을 없애고 장비 작업자가 한 대 또는 두 대의 다른 장비를 작동시킬 수 있도록 합니다. 로봇과 연결된 패널 벤딩 장비는 부품이 사람의 개입 없이 블랭킹, 펀칭 및 성형되는 시스템으로 전환되었습니다.
2020년 Raytec은 완전 자동화를 추구하기로 결정했습니다. 싱글 팔레트 로딩 및 언로딩 시스템을 대체하는 펀치/전단 셀을 공급하기 위해 14개의 스테이션 타워를 설치했습니다. Prima Power 서보 일렉트릭 EBe Express Bender; SGe에서 나오는 부품을 돕는 피킹 및 스태킹 로봇; 작업물이 한 스테이션에서 다른 스테이션으로 원활하게 흐를 수 있도록 두 셀 사이에 버퍼링 스테이션이 있습니다.
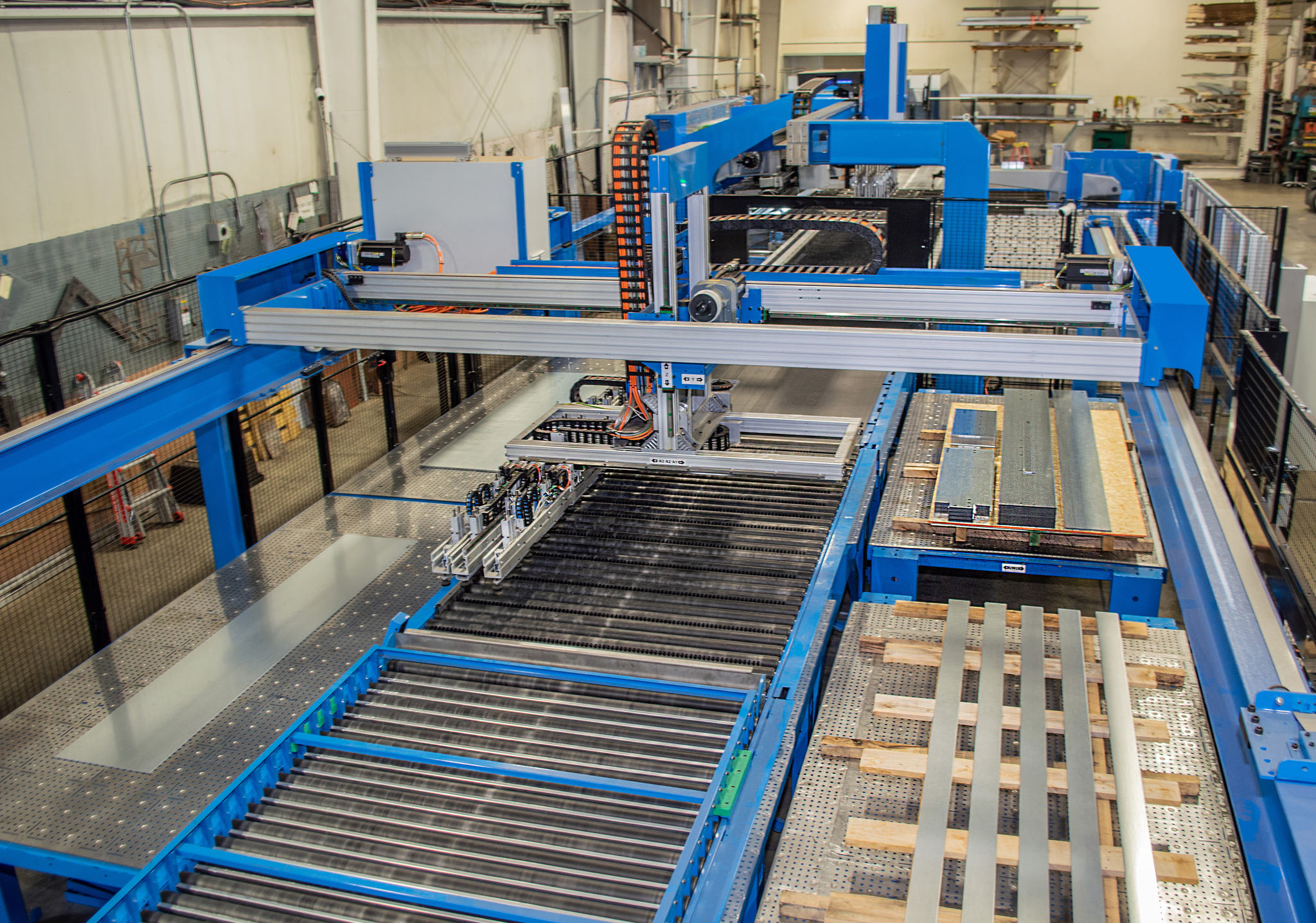
새로운 라인 셋업
노후화에도 불구하고 펀치/전단 결합 장비는 새로운 자동화 제조 라인을 운영할 수 있는 유력한 후보로 남아 있었습니다. 결국, 그것은 주변에 작업자 없는 상태에서 무인 방식으로 작동하도록 Raytec에 설치된 최초의 셀 중 하나였습니다.
특히 Zimmerman은 장비의 부품 분류 기능이 생산을 간소화하는 것이라고 말했습니다. SGe는 뼈대에서 분리된 중간 크기 부품을 위한 두 개의 30x60인치 낙하구역과 더 작은 부품을 캡처하여 테이블 아래에 있는 다섯 개의 빈 중 하나로 전달하는 크로스 컨베이어를 갖추고 있습니다.
펀치/전단 복합기에 연결되는 원자재 저장 타워를 추가하는 것은 장비 근처에 배치할 수 있는 공간이 존재하기 때문에 어렵지 않게 수행할 수 있었습니다. 그러나 전체 라인은 정확하게 계획되어야 했습니다.
"문제는 도크 도어로 결정된 부분이 공장 내부 길이 만큼에 머무는 것이었습니다."라고 Prima Power의 영업 관리자인 Fred Cook은 말했습니다. "그래서 우리는 맞춤형 구성으로 구성요소를 제공했습니다.
" SGe8은 14피트 포맷이었습니다. 장비에 연결된 FLS1540 단일 시트 전달 시스템과 피킹/스태킹 로봇 시스템 모두 해당 부품 크기를 수용할 수 있었습니다. 벤더에 공급하는 피킹 센터 장치는 14피트 부품도 수용하여 벤딩 시스템에 의해 레이저 절단 자재를 처리할 수 있는 문을 열도록 했습니다. 그러나 패널 벤더 설계는 수정되어야 했습니다.
벤더 설계는 Raytec이 정기적으로 제작한 특정 부품을 수용하기 위해 149.6인치에서 153.5인치로 확대되었습니다.
모든 것을 위한 공간을 만들기 위해 Zimmerman은 일부 기계들을 밖으로 옮겼다고 말했습니다. 전체 라인에 꼭 맞으면서 도크 도어 오른쪽에 모든 장비를 보관할 수 있었습니다.
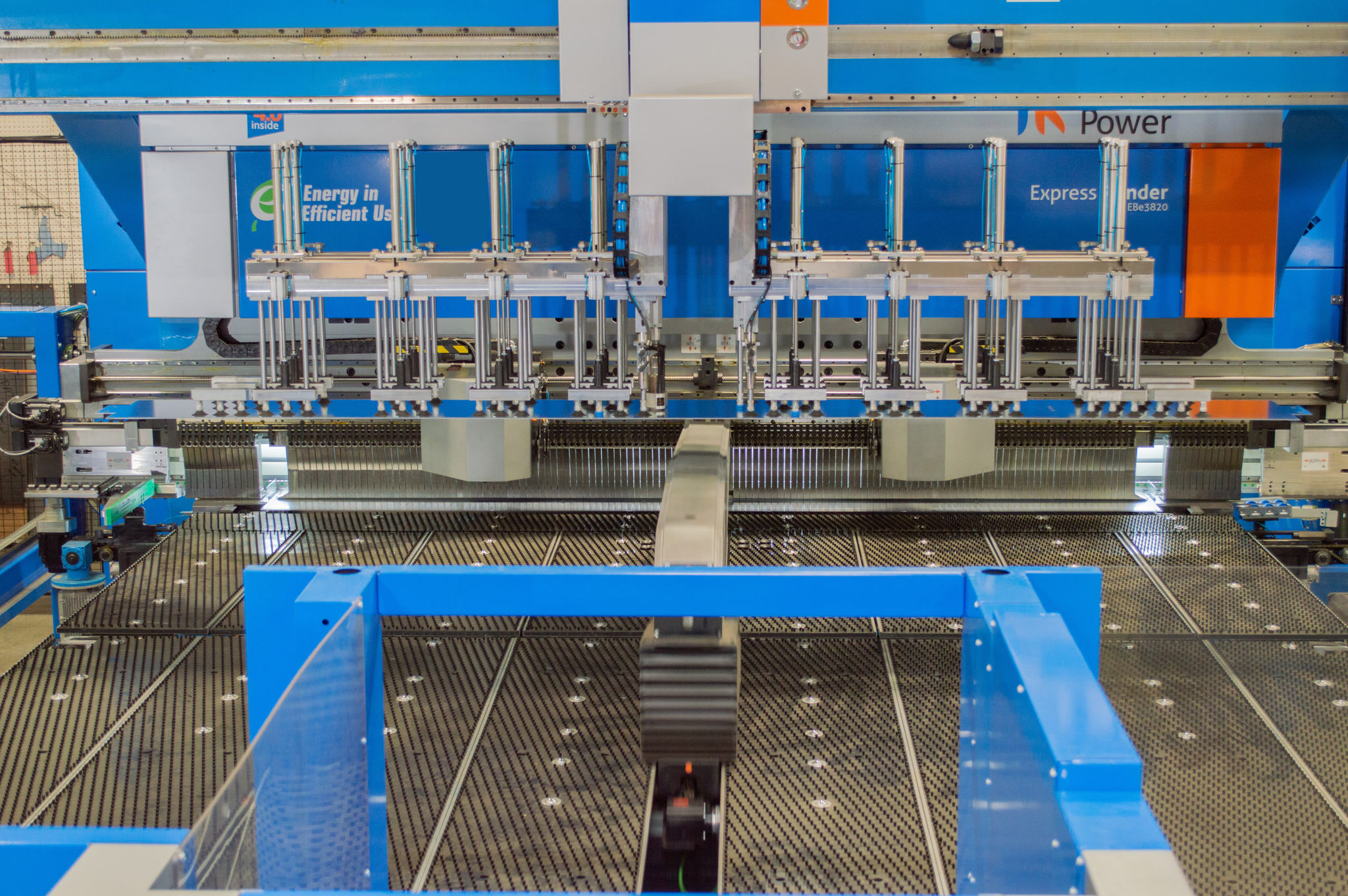
라인 작동 방식
라인은 공식적으로 PSBB(펀치, 전단, 버퍼링 및 벤딩)라고 하며, 버퍼링 장치는 모든 것이 라인을 통해 원활하게 흐르도록 생산 속도를 조절하는 데 도움이 됩니다. 예를 들어, SGe에서 많은 펀칭 또는 성형이 필요하지 않은 부품의 경우 전단이 스태킹 로봇을 매우 빠르게 앞지를 수 있습니다. 이를 방지하기 위해 부품을 펀치/전단기 에서 분리한 후 버퍼링 합니다. 여기서 로봇이 패널 벤더를 공급하기 위한 준비를 위해 부품을 쌓거나 성형이 필요 없는 경우 종료할 수 있을 때까지 부품을 고정합니다.
"프로그래밍 소프트웨어를 사용하면 시스템의 잠재적인 병목 현상에 대한 걱정 없이 생산을 운영하고 최대화할 수 있습니다."라고 Zimmerman은 말했습니다.
Zimmerman에 따르면, 특히 엠보싱 또는 업폼이 SGe의 작업에 포함된 경우 EBe는 펀치/전단기보다 약 2-3배 빠르게 작동할 수 있기 때문에 벤딩 장비 앞에 쌓인 부품은 큰 문제가 되지 않습니다.
기존의 프레스 브레이크와 달리 패널 벤더는 작업자가 작업물을 다룰 필요가 없습니다. 부품 조작기가 테이블 위에 공급된 시트를 가져와 블랭크 홀더 도구 사이에 배치한 다음 다른 쪽에 자재가 돌출된 상태에서 작업물을 하강하여 제자리에 고정합니다.
시트가 제자리에 있으면 장비의 벤딩 블레이드가 위와 아래에서 움직여 금속을 접습니다. 대부분의 공정에서 툴의 모양이 아니라 벤딩 블레이드의 동작이 최종 벤딩 각도와 반경을 결정합니다.
금속이 툴링(스로트라고 하는 기계의 영역) 너머로 더 멀리 돌출할수록 플랜지가 더 높아집니다. 스로트가 깊을수록 플랜지가 높아집니다. 패널 벤딩의 최대 벤딩 높이는 약 8인치입니다.
Zimmerman은 EBe가 부품 조작 툴이 잡을 수 있는 공간이 충분하지 않고 빈 홀더 툴 이상으로 확장할 만큼 넓지 않은 매우 좁은 부품과 같은 모든 것을 처리할 수는 없지만 매우 다기능성 툴로 다양한 작업을 처리할 수 있다고 말했습니다. 도어에서 13피트 패널에 이르는 다양한 크기의 부품을 교대로 일관되게 생산합니다.
전체 PSBB 라인은 한 사람이 담당합니다. Zimmerman은 생산성 및 일관성 향상 외에도 패널 벤더에서 자재를 꺼낼 때까지 아무도 자재를 취급할 필요가 없기 때문에 전체 라인이 훨씬 안전한 작업으로 이어졌다고 덧붙였습니다.
"프로그래밍 측면에서 다른 수준의 경험이 필요했지만 결과는 그럴 가치가 있습니다. 기존의 제조 방법보다 사무실에서 훨씬 더 예측 가능하고 통제된 방식으로 결과를 지시할 수 있습니다.”라고 Zimmerman은 말했습니다. "작업자의 전문성이나 기술에 의존할 필요가 없습니다." 패널 벤딩 장비는 Raytec의 가공 능력 뿐만 아니라 새로운 비즈니스 기회의 문을 열었습니다.
"고객 측면에서는 놓친 기회를 충족할 수 있는 방법을 찾고 있었습니다. 우리가 본 것 중 하나는 주문 생산 시장에 통합 패널 벤딩 라인이 거의 없다는 것입니다. 우리가 할 수 있었던 것은 중소 규모 시장을 열어서 일반적으로 이 기술에 접근할 수 없는 주문 생산 시장에 완전히 통합된 패널 벤딩 기능을 갖추는 것이었습니다.”라고 Zimmerman은 말했습니다.
아직 끝나지 않았다
새로운 자동화 라인이 가동됨에 따라 Raytec은 새로운 투자의 영향을 분석하는 데 잠시 시간이 걸릴 것으로 예상되지만 그렇지 않습니다. 이 금속 제조업체는 현재 46,000평방피트 규모의 설비 확장을 추진하고 있습니다.
Zimmerman 은 18,000 평방 피트의 추가 공사가 늦봄이나 초여름에 완료될 것으로 예상되며, 그 후에 올 여름 말에 28,000 평방 피트가 추가될 것이라고 말했습니다. Raytec은 올해 가을까지 크기를 두 배로 늘릴 예정입니다.
"우리는 좀 더 효율적인 운영을 위해 우리의 운영 중 일부를 약간 분산시키고 싶습니다"라고 그는 말했습니다.
두 대의 레이저 절단기가 첫 번째로 이동됩니다. 두 장비 모두 자동화된 자재 저장 및 검색 타워에 연결되어 절단을 최대화할 수 있습니다.
Raytec은 후방의 건물 확장을 통해 코일 공급 및 길이 별 절단 시스템을 펀칭/쉬어링/패널 벤딩 라인에 통합할 수 있는 방안을 모색하고 있습니다. Zimmerman은 기존 펀치/전단기 시스템을 이동하고 새 모델로 교체할 작업장 계획을 추가했습니다. 독립형 펀치/전단 결합 장비는 추가적인 무인 작동을 위해 자재 타워와 연결됩니다. 셀은 철판 및 소형 부품 형성을 위한 백업 역할을 합니다.
자동화 계획은 여기서 끝나지 않습니다. Prima Power는 후방 호환성이 있는 완전 자동화된 시스템을 통합 및 구축을 실현할 수 있기 때문에 Night Train FMS 자동 자재 저장 및 검색 시스템을 독립형 펀칭/쉬어링/패널 벤딩 라인과 펀칭/쉬어링 셀을 실제로 연결하기 위한 마지막 단계로 간주합니다.
“우리의 목표는 코일에서 시트, 그리고 각각의 장비로 이동하고 시트 저장소에서 펀칭 장비로 이동한 다음 펀칭된 부품을 Night Train 에 다시 배치하여 보관할 수 있도록 하는 것입니다."라고 Zimmerman은 말했습니다.
현재, Raytec에는 약 14명의 직원이 금속 제조 작업을 수행하고 있습니다. 추가 자동화에 대한 투자로 이 수치는 크게 변하지 않을 것입니다.
Zimmerman은 미래를 예측할 수는 없지만, Raytec이 미래에 인력을 추가하지 않고도 생산성과 유연성을 지속적으로 향상시켜야 한다라는 것을 알고 있습니다. 그것은 한동안 계획되어 왔고 가까운 시일 내에 계속해서 회사를 이끌 것입니다.
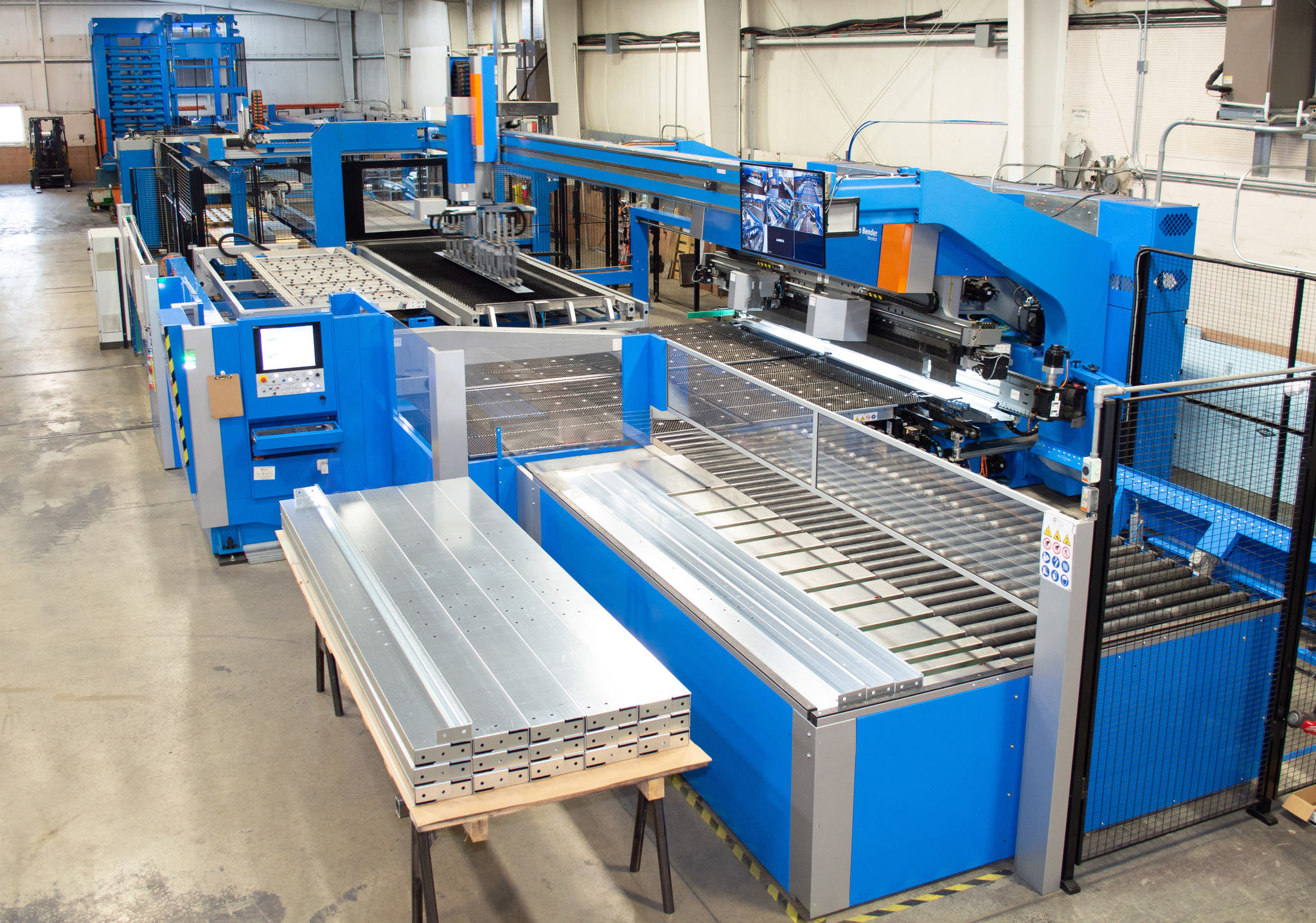
이 기사의 일부는 FABRICATOR 2023년 3월호에 게재된 기사에 사용되었습니다.
고객 측에서는 놓친 기회를 충족할 방법을 찾고 있었습니다. 우리가 본 것 중 하나는 작업장 시장에 통합 패널 벤딩 라인이 거의 없다는 것입니다.