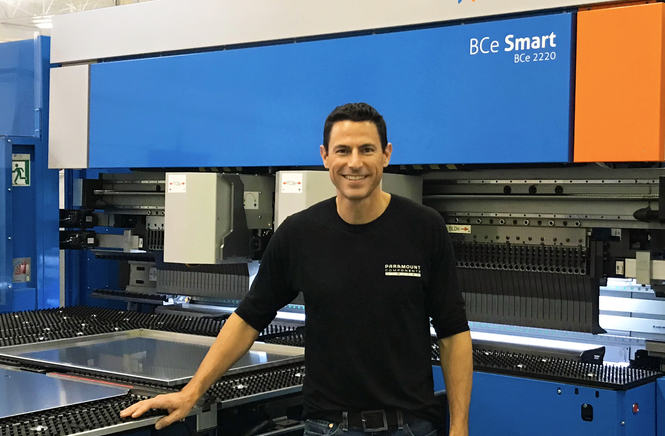
Paramount Components - Alihankintayritys purkaa tuotantonsa pullonkaulat
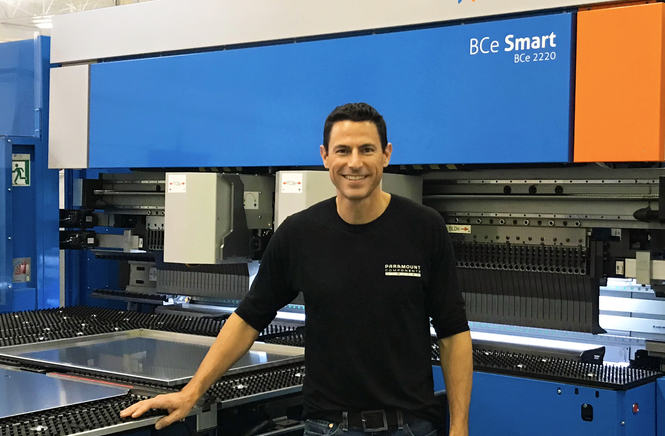
Paramount Components optimoi ajankäyttönsä ja ratkaisi työvoiman saatavuusongelmat taivutusautomaatin avulla
Vuonna 1988 perustettu kanadalainen alihankintayritys Paramount Components ei ole koskaan karttanut haasteita. Haastavista töistä on päinvastoin tullut yrityksen erikoisalaa.
”Otamme pääsääntöisesti vastaan vaikeampia töitä”, kertoo yrityksen omistaja Jamie Palliardi. ”Pysyttelemme yleensä kaukana yksinkertaisesta massatuotannosta; 10 000 kannattimen valmistaminen 90 asteen taivutuksella ei ole meidän heiniämme. Toisin kuin kilpailijamme, me emme välttele useita monimutkaisia taivutuksia sisältäviä kappaleita ja moniosaisia kokoonpanoja, joiden tulee toimia yhdessä hyvin tiukkojen toleranssien sisällä. Yrityksen perustanut isäni Mark uskoi, että työntekijöidemme haastaminen tekee henkilökunnastamme vahvemman. Siksi pyrimme aina hankkimaan haastavia töitä.”
Nykyään Paramount Components toimittaa Kanadan Abbotsfordin tehtaaltaan prototyyppejä ja räätälöityjä ohutlevykappaleita ja -kokoonpanoja ympäri Pohjois- ja Etelä-Amerikkaa, Aasiaa sekä Eurooppaa. Yrityksellä on asiakkaita esimerkiksi tietoliikenteen, elektroniikan, lääketieteen, hammashoidon, tulostuksen, maanpuolustuksen, arkkitehtuurin ja autoteollisuuden aloilta.
Varmistaakseen tasaisen korkean laadun ja toimitusaikojen pitävyyden, Paramount Components on aina panostanut innovaatioon ja huippuluokan tuotantolaitteisiin. Viimeisimpänä yritys on keskittynyt tehokkaamman taivutusprosessin toteuttamiseen.
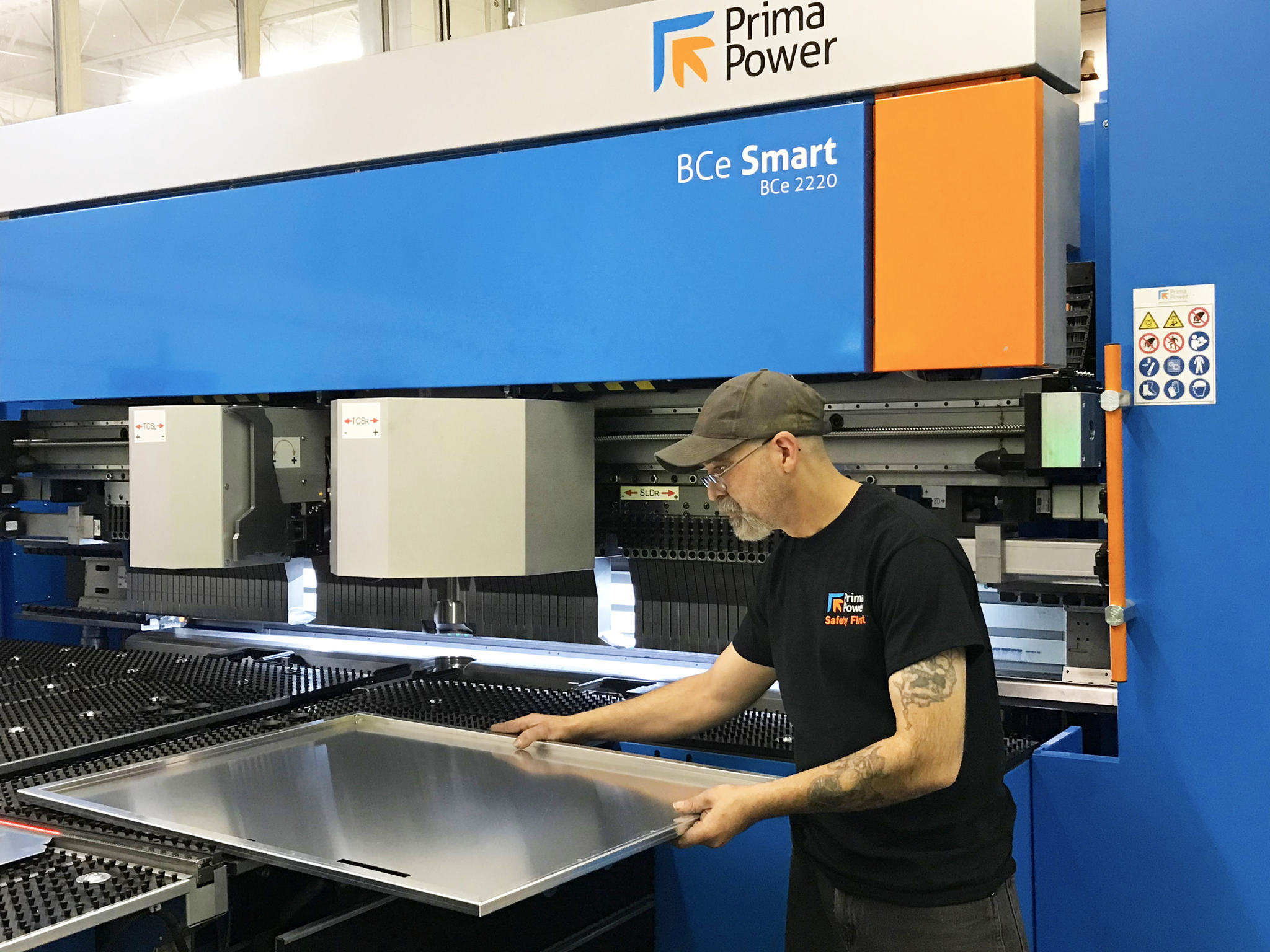
TAIVUTUKSEN PULLONKAULAT
”Taivutus on yksi vaikeimmista työvaiheista työvoiman saatavuuden kannalta”, Palliardi sanoo. ”Oikeaoppisen kappaleen taivuttamisen oppiminen särmäyspuristimella vaatii runsaasti aikaa. Särmäyspuristimen käyttäjän kouluttamiseen voi mennä vuosia, jotta hänellä on tarvittava osaaminen työstämiemme kappaleiden muotoiluun. Taivutukseen muodostuikin usein ensimmäisenä pullonkauloja. Varsinkin silloin kun taivutetaan suuria kappaleita, kuten kaappien ovia, mikä vaatii kaksi särmäyspuristinoperaattoria. Tehdessämme pitkiä ajoja olimme huolissamme työntekijöidemme jaksamisesta, koska heidän piti nostella raskaita kappaleita päivät pitkät. Tämä oli yksi pääsyistä, miksi aloimme etsiä vaihtoehtoja särmäyspuristimille.”
Palliardi tiimeineen harkitsi aluksi robotteja, mutta koki ne lopulta liian vaativiksi. ”Niiden asetuksiin menee paljon aikaa”, hän sanoo. ”Me työstämme kirjaimellisesti tuhansia kappaleita, enimmäkseen pienissä erissä. Robotin kanssa olisimme käyttäneet entistäkin enemmän aikaa asetuksiin ja taivutusprosessin valmisteluun. Robotti ei siis tarjonnut tarvitsemaamme joustavuutta.
TAIVUTUSAUTOMAATTI TULEE TALOON
Paramount Componentsin tuotantopäällikkö ehdotti taivutusautomaatteihin tutustumista, joten tiimi alkoi tutkimaan vaihtoehtoja netissä. Yritys etsi toimittajaa, jolla on toimivaksi todettu taivutusautomaatti ja joka tuntee niiden teknologian hyvin. Paramount Components päätyi Prima Powerin BCe Smartiin.
”Yksi päätökseen vaikuttavista tekijöistä oli huoltopalvelujen saatavuus”, Palliardi kertoo. Tehtyämme markkinatutkimusta ja puhuttuamme muiden ohutlevyalan toimijoiden kanssa meille oli selvää, että Prima Power pystyy toteuttamaan meille huoltopalvelut paremmin kuin sen kilpailijat.”
BCe Smart asennettiin yrityksen tiloihin elokuussa 2018.
Sähköservokäyttöinen BCe Smart soveltuu keskisuurille ja pienille tuotantomäärille sekä lean-tuotantoon. Se on suunniteltu mahdollistamaan lastaus ja purku taivutuksen aikana. Koneen käyttö ei myöskään vaadi laajaa koulutusta. Viivakoodilukija ja ATC-järjestelmä pitävät huolen asetuksien automaattisesta määrittelystä, mikä tapahtuu taustalla ja aktivoi dynaamiset tuotantojonot.
Manuaaliselle lastaukselle ei ole mitään fyysisiä esteitä. Varoitusvalot ja äänimerkit auttavat käyttäjää lastauksen ja purkamisen synkronoinnissa, ja interaktiivinen lisänäyttö ohjaa käyttäjää eri työvaiheissa, kuten kappaleiden suuntauksessa. Koneeseen voidaan myös integroida robotti lastauksen ja purkamisen automatisoimiseksi.
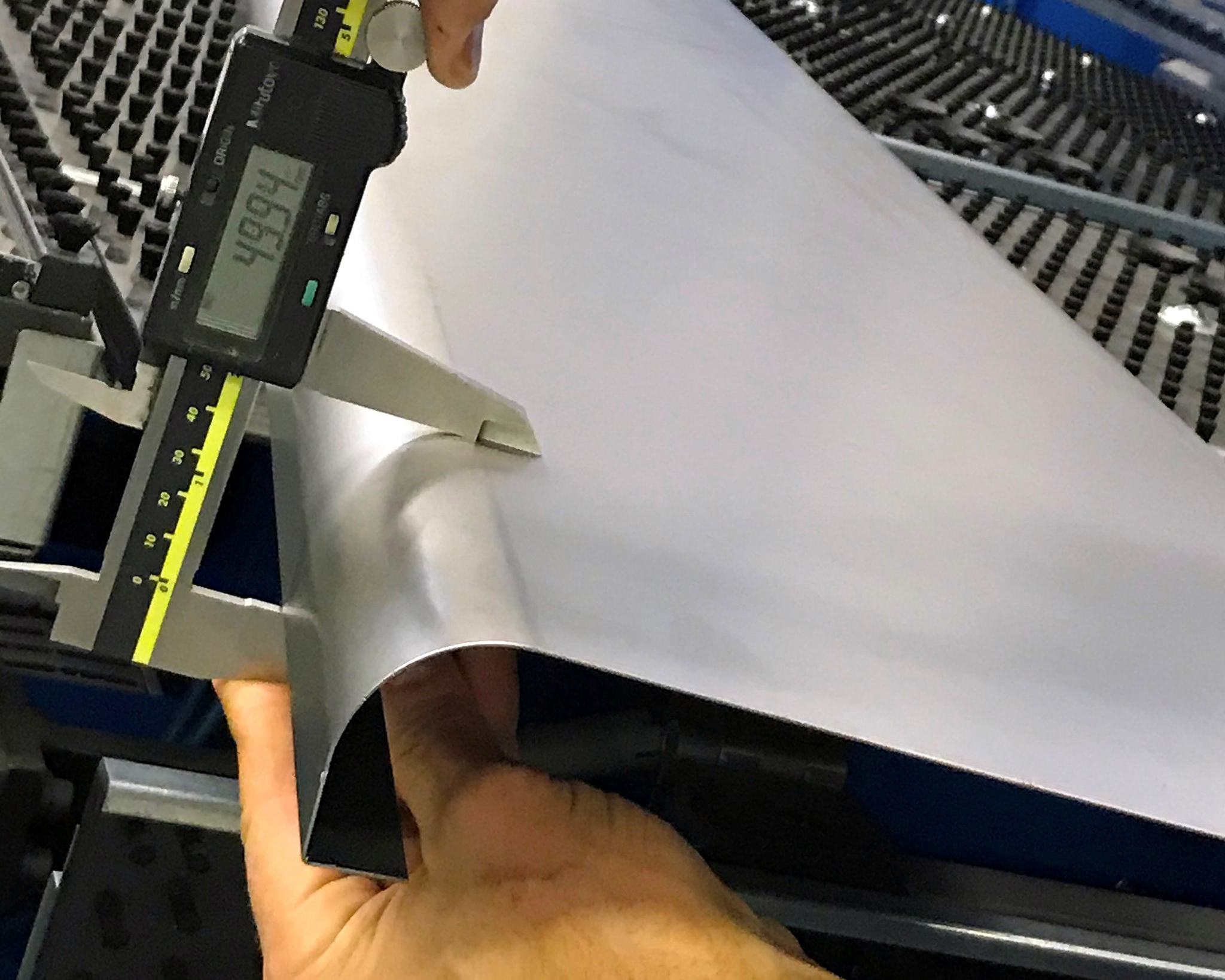
JOUSTAVUUTTA TOIMINTAAN
”Ostimme BCe Smartin alun perin suuria kappaleita ja tuotantomääriä varten”, Palliardi kertoo. ”Nyt me käytämme sitä pienemmissä erissä. Siinä missä me ajamme nyt päivässä 10–12 eri työtä läpi, ennen yksi työ vei 4–6 tuntia. Nyt me ajamme huomattavasti enemmän kappaleita, mutta pienemmissä erissä. Koska olemme alihankintayritys, tämä voi toki muuttua ajan myötä, mutta BCe Smart on valmis työstämään minkä tahansa kokoisia eriä asiakkaamme tarvitsevatkin.”
Nykyään Paramount Components pitää huippuosaajansa särmäyspuristimilla. ”Olemme palkanneet uusia työntekijöitä käyttämään BCe Smartia, koska sen käyttö ei vaadi paljon koulutusta”, Palliardi kertoo. ”Pystyn myös itse ajamaan konetta kaikissa kolmessa työvuorossamme. Voin näyttää vaikka viikko sitten aloittaneelle kaverille, kuinka taivutusautomaatin lastaus- ja purkutoiminto toimii, ja hän voi pitää tuotannon käynnissä itsenäisesti. Pyrimme tekemään taivutusautomaatilla kaikki mahdolliset työt, koska se on nopeampi kuin särmäyspuristin. Kaikki tarvitsemamme työkalut ovat valmiina koneessa, joten olisin yllättynyt, jos pisin asetusaikamme on edes viisi minuuttia. Taivutusautomaatilla pystymme siirtymään nopeasti kappaleesta toiseen – särmäyspuristimet eivät pärjää mitenkään vertailussa.”
”Taivutusautomaatin valttina oli myös se, että siinä ei ole tarvetta työkalujen poistoon. Särmäyspuristimen oston jälkeen on aina käytettävä paljon rahaa työkalustukseen. Tällä hetkellä työstämme noin 20 % kappaleistamme taivutusautomaatilla, ja aiomme tuplata tämän määrän lähitulevaisuudessa. Tähän päivään mennessä koneella ei ole koskaan ollut jonoa, koska se on niin nopea. Maanantaina saattaa näyttää, että meillä on viikolla melkoinen työkuorma taivutuksessa. Keskiviikkoon mennessä kaikki on kuitenkin jo tehtynä, eikä koneelle olo jonoa.”
TEKNOLOGIAN AALLONHARJALLA
Paramount Components oli Kanadan Brittiläisen Kolumbian ensimmäinen yritys, joka osti BCe Smart -mallin koneen. ”Meille on aina ollut tärkeää pysyä teknologian aallonharjalla”, Palliardi sanoo. ”Korkea laatu on meille kunnia-asia... ja laadukkaaseen jälkeen tarvitaan parhaimmat laitteet. Taivutusautomaatti on myös auttanut meitä tarjouksien tekemisessä, koska voimme ilmoittaa tarkan aikataulun ja hinnan työlle. Alihankkijana meillä on myös jatkuva paine lyhentää läpimenoaikoja. Taivutusautomaatista menee kaikki sujuvasti läpi, ja tuotantomme on huomattavasti nopeampaa entiseen verrattuna."
BCe Smart on myös auttanut meitä tarjouksien tekemisessä, koska voimme ilmoittaa tarkan aikataulun ja hinnan työlle. Alihankkijana meillä on myös jatkuva paine lyhentää läpimenoaikoja. Taivutusautomaatista menee kaikki sujuvasti läpi, ja tuotantomme on huomattavasti nopeampaa entiseen verrattuna."
Etsitkö vastaavaa ratkaisua yrityksellesi? Löydä se täältä
BCe Bending Centre
TAIVUTUSAUTOMAATIT
Puoliautomaattinen taivutuskone yhdistää joustavuuden ja tuottavuuden
BCe Smart+
TAIVUTUSAUTOMAATIT