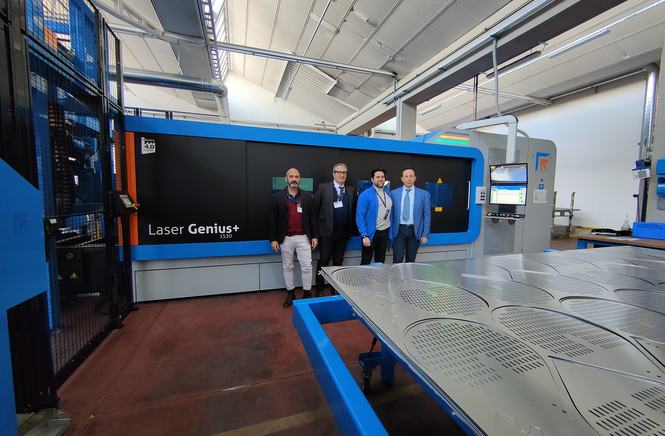
Gi.Metal, ready for a batch of productivity
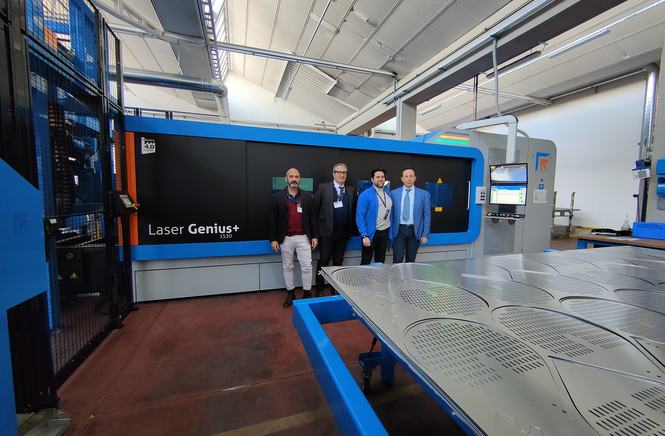
If Italian cuisine is one of the most famous and renowned in the world, then this is definitely thanks to chefs who have exported the recipe, but those who produce kitchen utensils also play a very important role. Such is the case for Gi.Metal, who specialises in the manufacture of pizzeria equipment, which use prima power lasers in the cutting process.
Pizza is now eaten worldwide. Where there is a pizzeria, there is an oven and where there is an oven, there is (most likely) a peel made by Gi.Metal. Today, the Montale company in the province of Pistoia is a real colossus in the production of catering industry accessories but, looking back over its history, it was not always this way. “The company was founded in 1986 by my father,” says the current CEO, Marco D'Annibale, “It was a blacksmith's shop with the intention of doing something completely different. At that time I was finishing my studies but as soon as I finished in 1988, I joined the company and started working in production. In those days we were already making a few pizza peels, and each phase was done manually: cutting, grinding and assembling exactly like it was done 100 years ago. Over time, we came to realise that these products were slowly becoming our core business, so we decided to specialise and this has been the key to our success”.

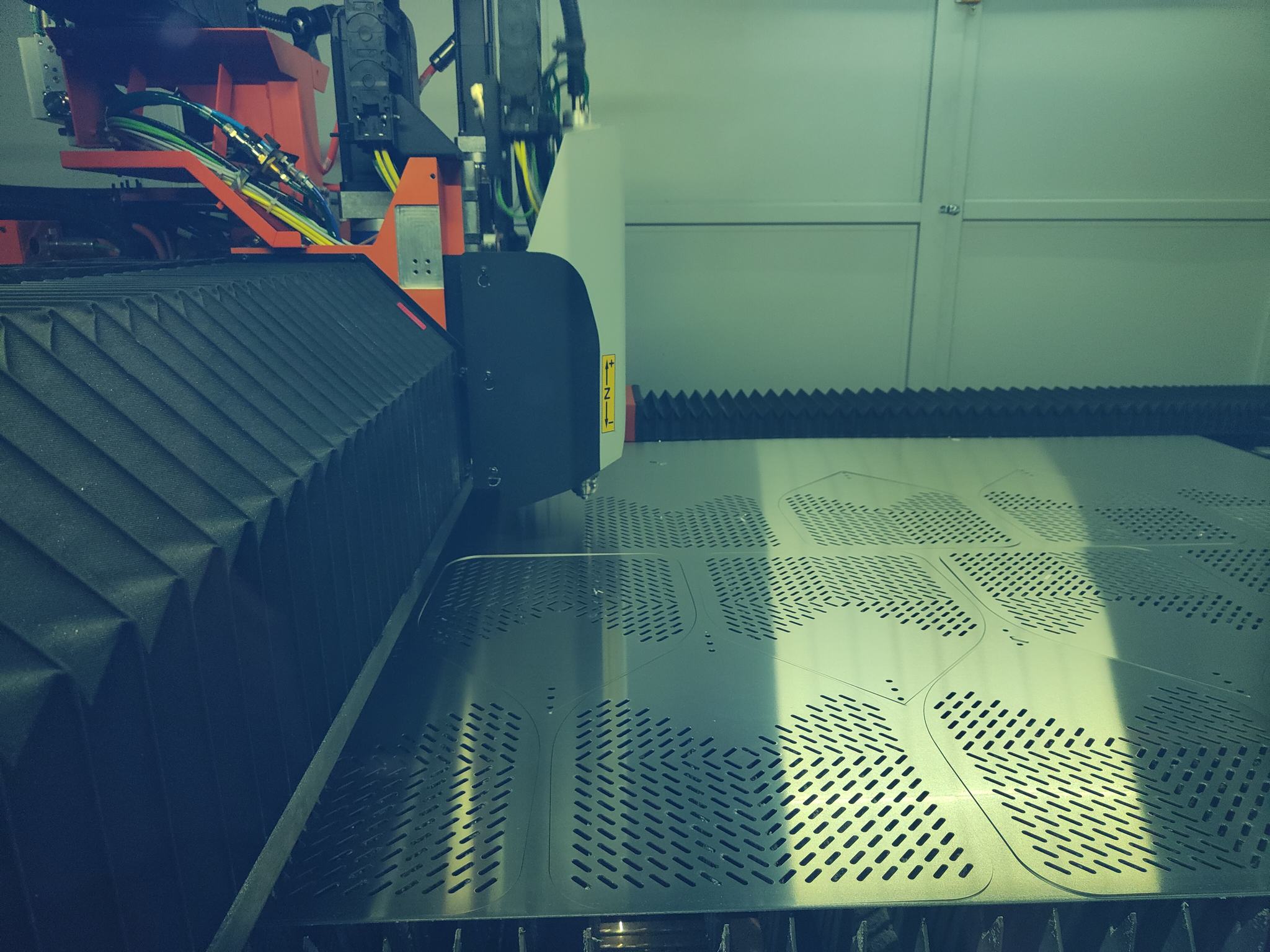
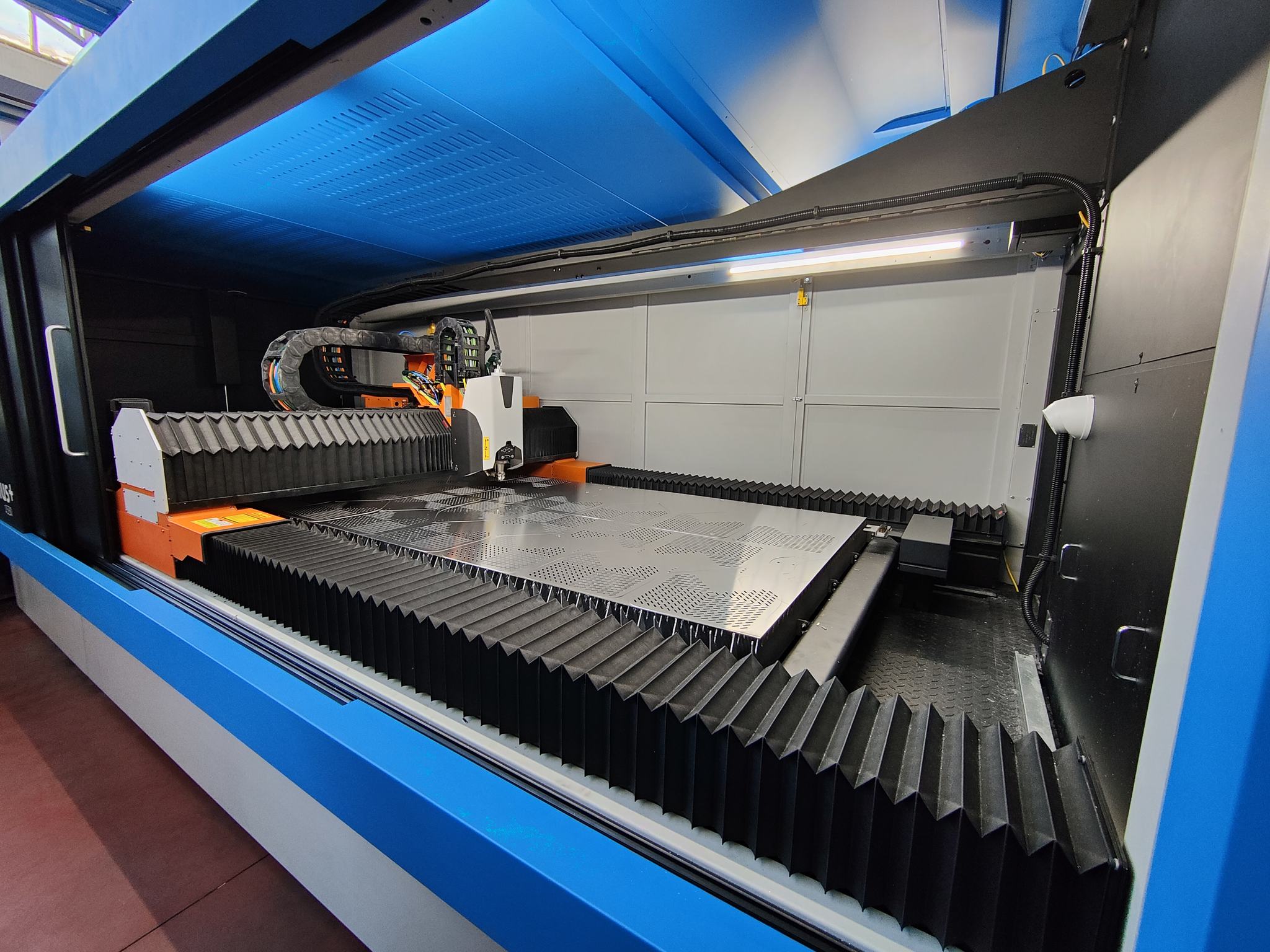
This is a craft vocation and although it has been adapted and revamped to suit modern times, it has not been compromised over the years; in fact, despite its significant structure, the company is always attentive to the needs of its customers and does not hesitate to produce limited editions or custom products according to customer requirements. “Peels and equipment for pizza making require you to know the customer and his kitchen,” says D'Annibale. “In fact, there is no single way of cooking pizza across the world and each customer has his own tastes and requirements. So, as we came into contact with new companies, we tried to understand their preferences and needs, which often lead us to the development of new products. The difficulty for us has been in combining our craft vocation with the industrial spirit and, in this challenge, technology is of the utmost importance as it must allow productivity without sacrificing flexibility.”
Today Gi.Metal covers 8,000 square metres of plant. There is a production department, an assembly area and a logistics centre that manages the delivery of products worldwide, since 70% of production is destined for foreign countries, mainly Europe and America (where Gi.Metal is present both with an office in Chicago, the US home of American pizza, and in Brazil, in Curitiba). All the sheet metal working phases are carried out internally, starting with the cutting of the shape, for which the company uses Prima Power 2D laser technology.
MADE IN ITALY TECHNOLOGIES FOR THE STANDARD OF ITALIAN CUISINE WORLDWIDE
Going into more detail about pizza equipment, D'Annibale explains: “Our customer mainly needs three items. The first is the pizza peel, which must have at least the necessary surface area to place the rolled dough on top; this is usually made of aluminium to ensure lightness. Next, a smaller peel is required to rotate the pizza in the oven. This tool is usually smaller since agility and manageability are preferred: larger dimensions are no longer necessary since the pizza gains structure as it cooks and you don't need a tool that holds the whole pizza; this needs to be made of steel to protect against the increased heat exposure; the third tool is the oven cleaning brush”.
Gi.Metal has completely internalised the sheet metal working part of these products. Once the material has been identified, which is mainly stainless steel 441 or pre-hardened steel or even aluminium 6000 series in thicknesses ranging from 0.8 mm to 2.5 mm, we proceed to the cutting phase. For this, the company boasts a solid partnership with Prima Power, which began over 15 years ago with the purchase of a CO2 laser, followed by a fibre model and recently renewed with a brand new Laser Genius+ with loading/unloading automation and Combo Tower Laser storage. Other production steps involve the use of laser tubes to machine the handles, press brakes, milling machines and moulding presses to shape and produce the ribbing on the peel and, finally, satin-finishing machines for surface treatment. The only work outsourced to a trusted network of companies is the painting and anodising, as well as the production of a few plastic components. In addition to peels, Gi.Metal's flagship product, the Pistoia-based company also produces accessories for dough preparation, cutting, serving and transport, as well as a line of trolleys for the catering industry. These are all products in which sheet metal plays a leading role.
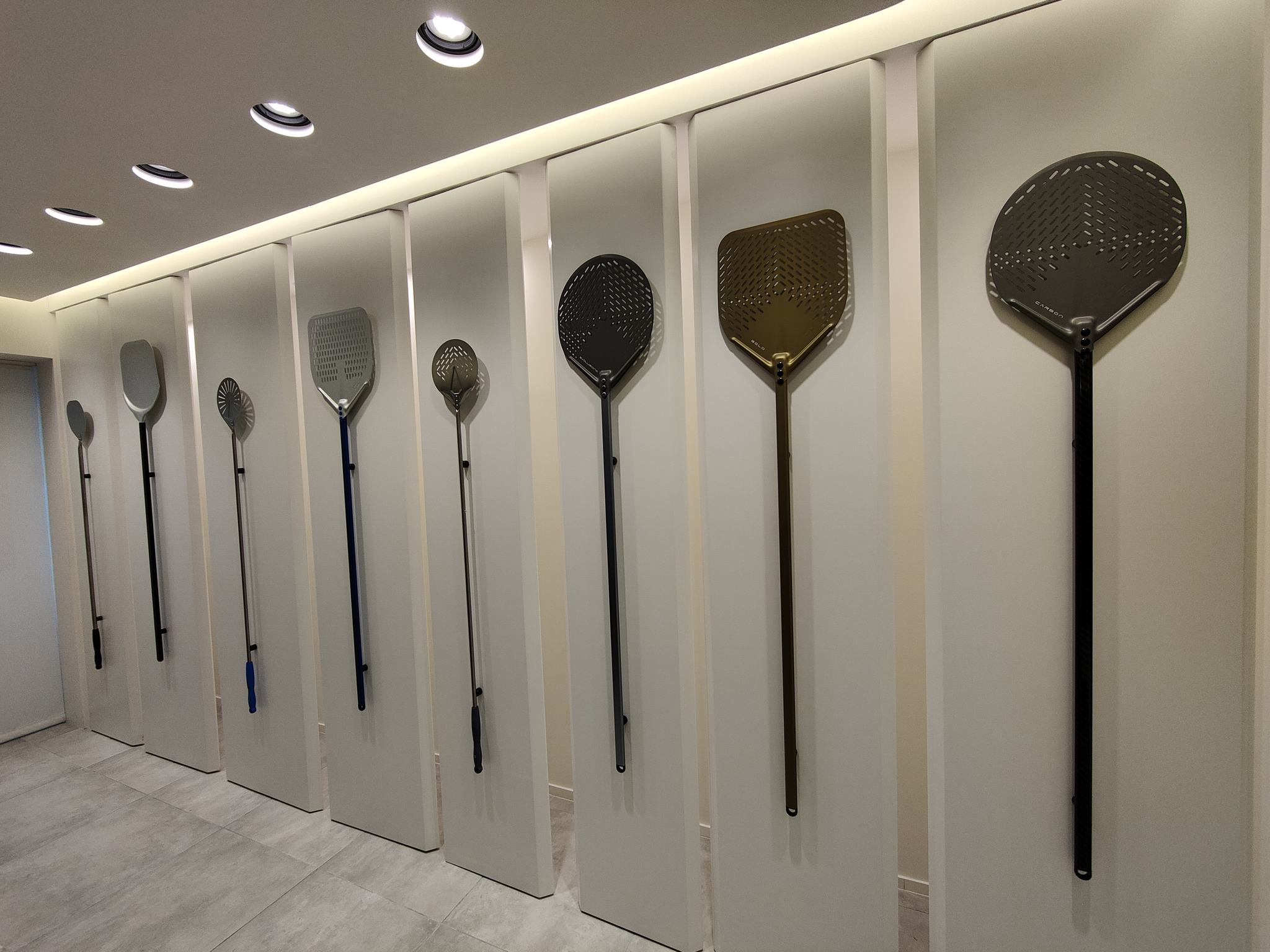
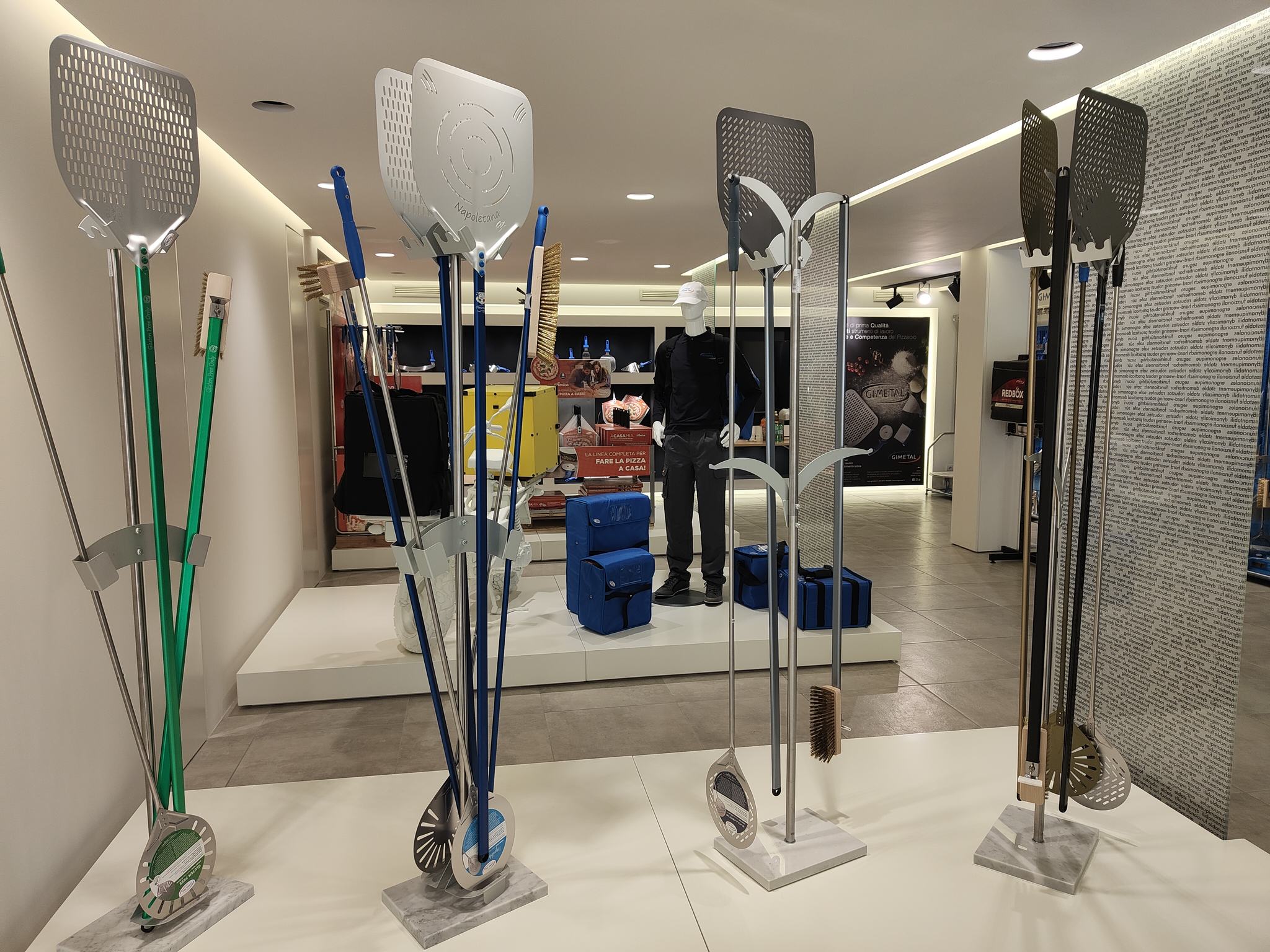
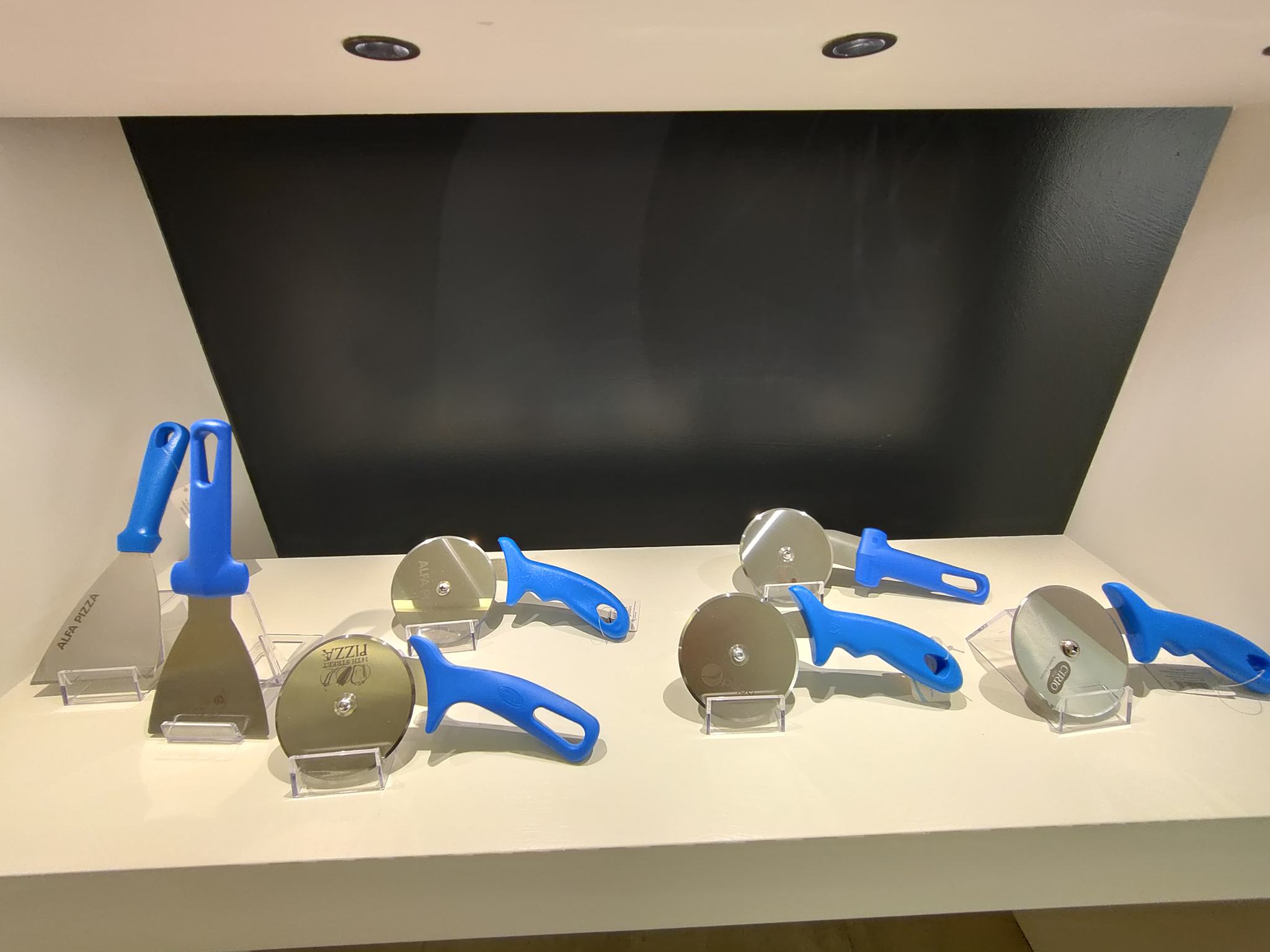
THE TECHNOLOGY BEHIND THE SIMPLICITY
It is not immediately apparent that even behind such simple items like pizza peels, there are important design and manufacturing factors that often make all the difference, and these require precise planning and state-of-the-art technology.
The CEO explains: “Peels are mainly round or rectangular, the latter being easier to use but much depends on the tastes of the pizza maker. The main feature of our products is that some of them have holes to help remove any excess flour from the peel before the pizza is placed on it. If there is too much flour on it, the taste of the pizza won't be the same and the oven will need cleaned more often. Not everyone is able to produce these holes. The Laser Genius+ system has been of paramount importance for us as it guarantees high production volumes due to its dynamics while also allowing the creation of clean holes with well-defined edges, which avoids the accumulation of flour.”
One of the advantages of Laser Genius+ is its performance in making holes: during tests at the Tech Center in Collegno, 11 holes were made in less than 5 seconds.
Another key aspect in enabling the high production volumes required is the automation of the Laser Genius+. The Combo Tower Laser means the machine can easily work unmanned, and Prima Power technicians have implemented a series of customisations and improvements to maintain the quality and aesthetic finish of the semi-finished products. “We machine extremely fine sheets,” says Riccardo Barneschi, plant manager at Gi.Metal, “and if a sheet gets scratched during handling, the anodising does not adhere effectively to the peel, so the quality suffers. This was initially one of our worries about adopting a solution with automated loading and unloading, but Prima Power was able to resolve the situation by proposing belts that allow the workpiece to slide gradually towards the unloading bay without any real friction, and also by inserting a tier sheet between the two semi-finished products if they have sharp parts.
Of no less importance and still related to the automation system that completes the plant is waste management: the management of waste by the Prima Power system is automatic and allows Gi.Metal a quantified saving of 3-4 hours of work per week while allowing the separation of materials into various bins.
“We are very pleased to have reconfirmed our choice of Prima Power," says Barneschi. “With the Laser Genius+ we are able to cut in 40 minutes what aCO2 laser cuts in two hours and what took a previous generation fibre laser to process in just over an hour.”
This consistent choice is not only determined by technological performance, but also by the characteristic flexibility and problem-solving approach of the Turin-based company which has been greatly appreciated at Gi.Metal. The plant manager explains: “Although we have had Prima Power technology for over 15 years, we also consulted other manufacturers before purchasing our latest laser. The availability of Prima Power technicians who analysed our nesting and products and helped us optimise our cutting programs - for example by reducing head movements when drilling - was fundamental to increasing productivity and is one of the factors that allowed us to reconfirm our trust in the Turin-based manufacturer. When the machine was installed, we were also able to appreciate the plug&play configuration of the Laser Genius+, which enabled installation in record time.
TECHNOLOGY 4.0 AND A FOCUS ON “OLD-SCHOOL” PERSONNEL
Such efficient production, imbued with a lean philosophy, cannot be achieved without complete mapping and management of process data in full compliance with the dictates of Industry 4.0. All machines in the company, starting with Prima Power lasers, are connected within the business ecosystem to supply managers with timely information so they can make the best possible decisions. The process not only involves the latest generation of machines with Prima Power lasers at the forefront, but older technologies have also been retrofitted to allow complete mapping of the production area. These information flows are then integrated with downstream and upstream phases such as invoicing, purchasing and warehousing to provide a real-time business management dashboard that can be used anywhere in the world.
With such a modern approach to machinery management, Gi.Metal clearly understands that the operator behind the machine is just as important for production, as best summed up by the company's motto "Made with passion". “In my opinion, the focus on people is key,” says D'Annibale, “because they are not machines but rather much more complex entities, each with their own fragilities, ambitions and hopes, so empathy is essential. If you keep this in mind, you can create a favourable environment in the company in which employees feel protected; by this I mean not just providing them with a fair financial reward but also good company welfare, rewards and training that reflects their ambitions.”
ALWAYS READY FOR NEW CHALLENGES
Gi.Metal's plans for the future include moving beyond the post-pandemic world. Management used to travel all over the world attending trade fairs and exhibitions together with other companies in the sector with a view to take the idea of Italian cuisine abroad; this custom has had to take a back seat over the past two years, but this has not halted turnover, which has been constantly increasing.
“We used to attend more than 50 trade fairs before the pandemic,” says D'Annibale, “and this was an excellent opportunity to meet new businesses from which we drew important ideas to translate into new products. It’s been hard for me in recent years not being able to take all the planes I used to, but I hope that things will resume under this new normality and that I’ll continue to discover that it’s always possible to create something new even in a world where people think that everything has already been invented, continuing to take Gi.Metal forward as it stands now: a modern industry but with an emphasis on craftsmanship, while promoting the Made in Italy label worldwide. The contribution of a partner like Prima Power who also promotes Made in Italy branding will be increasingly fundamental in this regard.”
PRECISION AND PRODUCTIVITY MADE IN COLLEGNO
Speed, precision and efficiency are the main features of the Laser Genius+, the latest addition to Prima Power's range of machines dedicated to 2D laser cutting. It is an extremely productive and flexible fibre laser machine that can adapt to any customer layout without compromising configuration. Laser Genius+ features a gantry architecture that ensures high levels of thermal stability, vibration damping and high dynamics, also thanks to compact motors and transmission with greater power per footprint and maximum energy efficiency.
Laser Genius+ is a plug&play machine designed to make installation easy, allowing immediate operation and reducing the return on investment. The laser generator, chillers, motors and optics are integrated within the cabin and guarantee easy and quick installation: it takes just two days from delivery to production in any plant.
To meet the production needs of the widest range of customers, Laser Genius+ is available in three sizes: 1530 (with 3,150 x 1,600 mm axis strokes and a maximum machinable load of 1,150 kg), 2040 (with 4,320 x 2,200 mm axis strokes and a maximum machinable load of 2,100 kg) and 2060 (with 6,320 x 2,200 mm axis strokes and a maximum machinable load of 3,050 kg). The maximum achievable trajectory speed in all versions is 180 m/min and fibre sources from 2 to 10 kW can be installed. To ensure maximum productivity, the Laser Genius+ can be supplied with all the automations in the Prima Power portfolio: from loading and unloading solutions to sorting systems and the Night Train flexible production system.
The availability of Prima Power technicians who analysed our nesting and products and helped us optimise our cutting programs was fundamental to increasing productivity and is one of the factors that allowed us to reconfirm our trust in the Turin-based manufacturer.