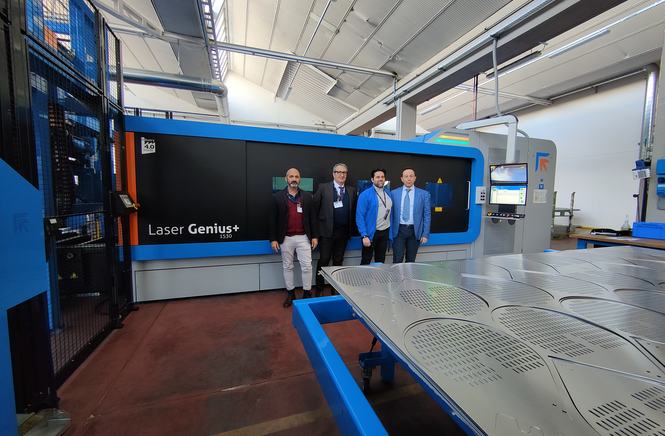
Gi.Metal, Bereit für eine Ladung Produktivität
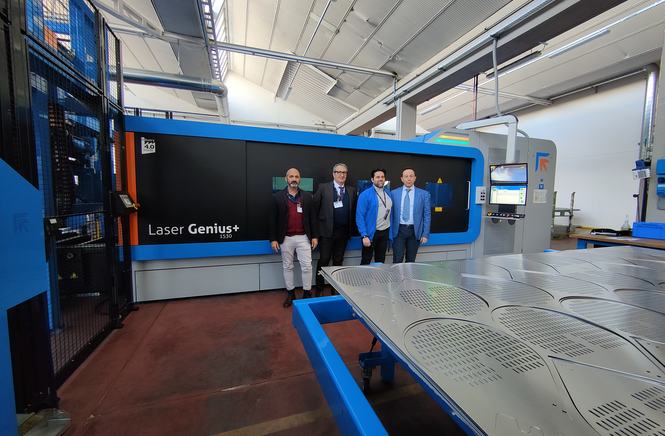
DASS DIE ITALIENISCHE KÜCHE ZU DEN BERÜHMTESTEN UND RENOMMIERTESTEN DER WELT GEHÖRT, IST SICHERLICH DEN KÖCHEN ZU VERDANKEN, DIE DAS REZEPT KREIERT HABEN. ABER DIE HERSTELLER VON KÜCHENUTENSILIEN SPIELEN EBENFALLS EINE WICHTIGE ROLLE. ZUM BEISPIEL GI.METAL. DAS UNTERNEHMEN HAT SICH AUF DIE HERSTELLUNG VON PIZZERIA-UTENSILIEN SPEZIALISIERT UND VERWENDET BEIM SCHNEIDEN PRIMA POWER-LASERTECHNIK
Pizza wird heute überall auf der Welt gegessen. Wo es eine Pizzeria gibt, gibt es einen Ofen und wo es einen Ofen gibt, gibt es höchstwahrscheinlich eine Pizzaschaufel von Gi.Metal. Heute ist das Unternehmen Montale in der Provinz Pistoia ein echter Gigant in der Produktion von Gastronomiezubehör, aber das war nicht immer so, wenn man sich seine Geschichte ansieht.
„Das Unternehmen wurde 1986 von meinem Vater gegründet“, sagt der heutige Geschäftsführer Marco D'Annibale, „es war eine Schmiede und sollte etwas ganz anderes machen. Ich beendete gerade mein Studium, und als ich es im Jahr 1988 fertig war, trat ich in das Unternehmen ein und begann in der Produktion zu arbeiten. Damals stellten wir bereits ein paar Pizzaschaufeln her und jeder Fertigungsschritt wurde, genau wie vor 100 Jahren, von Hand ausgeführt: Zuschneiden, Schleifen und Zusammenbau. Mit der Zeit stellten wir fest, dass diese Produkte langsam zu unserem Kerngeschäft wurden, also beschlossen wir, uns zu spezialisieren, und das war der Beginn unserer Erfolgs“

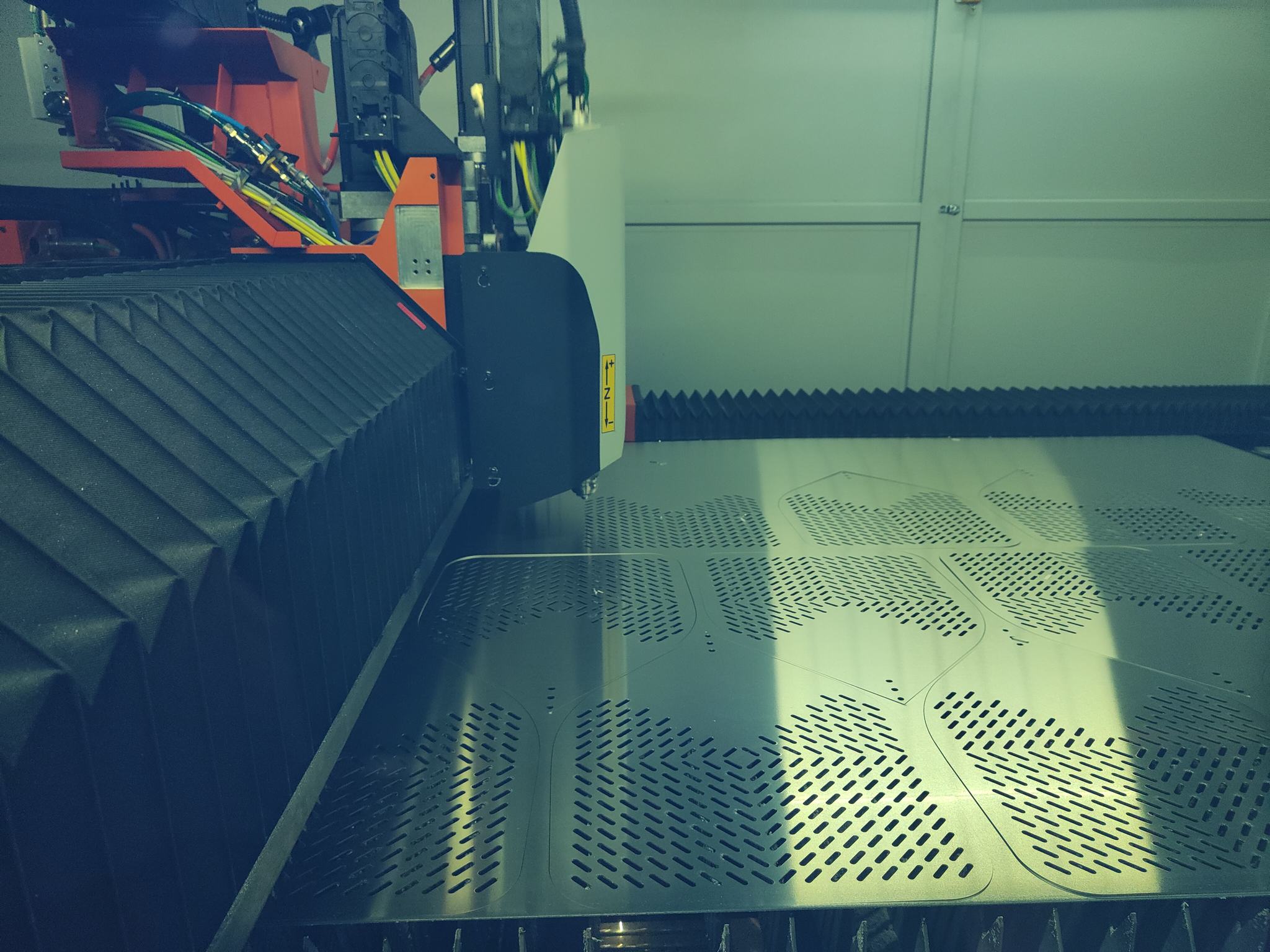

Es handelt sich um eine handwerkliche Berufung, die im Laufe der Jahre trotz der Anpassung an die moderne Zeit nicht beeinträchtigt wurde. Trotz seiner bedeutenden Struktur hat das Unternehmen immer ein offenes Ohr für die Bedürfnisse seiner Kunden und zögert nicht, limitierte Auflagen oder Sonderanfertigungen gemäß Kundenwunsch herzustellen.
„Für die Herstellung von Pizzaschaufeln und -geräten muss man den Kunden und seine Küche kennen“, sagt D'Annibale. „In der Tat gibt es keine einheitliche Zubereitungsart für Pizza auf der ganzen Welt, und jeder Kunde hat seine eigenen Vorlieben und Anforderungen. Wenn wir also mit neuen Unternehmen in Kontakt kamen, versuchten wir immer, ihre Vorlieben und Bedürfnisse zu verstehen, was häufig zur Entwicklung neuer Produkte führte. Die Schwierigkeit bestand für uns darin, unsere handwerkliche Berufung mit dem industriellen Geist zu vereinen, und bei dieser Herausforderung ist die Technologie von größter Bedeutung, da sie Produktivität ermöglichen muss, ohne die Flexibilität zu beeinträchtigen.“
Heute verfügt Gi.Metal über eine Betriebsfläche von 8.000 Quadratmetern. Es gibt eine Produktionsabteilung, einen Montagebereich und ein Logistikzentrum, das die Auslieferung der Produkte in die ganze Welt steuert, denn 70 % der Produktion geht ins Ausland, vor allem Europa und Amerika (wo Gi.Metal sowohl mit einem Büro in Chicago, der Heimat der amerikanischen American Pizza, als auch in Brasilien, in Curitiba, vertreten ist). Alle Phasen der Blechbearbeitung werden hausintern durchgeführt, beginnend mit dem Zuschnitt der Form, wofür das Unternehmen die Lasertechnologie Prima Power 2D einsetzt.
TECHNOLOGIEN „MADE IN ITALY“ FÜR DEN WELTWEITEN STANDARD DER ITALIENISCHEN
D'Annibale erläutert das Pizzazubehör näher: „Unser Kunde braucht hauptsächlich drei Dinge. Das erste ist die Pizzaschaufel, die mindestens eine ausreichende Fläche haben muss, um den ausgerollten Teig darauf zu legen. Sie besteht in der Regel aus Aluminium, um ein geringes Gewicht zu gewährleisten. Dann wird eine kleinere Schaufel benötigt, um die Pizza im Ofen zu drehen. Dieses Werkzeug ist in der Regel kleiner, da Beweglichkeit und Handlichkeit bevorzugt werden: Größere Abmessungen sind nicht mehr notwendig, da die Pizza beim Garen an Festigkeit gewinnt und man kein Werkzeug braucht, das die ganze Pizza hält. Es muss jedoch aus Stahl sein, um beständig gegenüber der größeren Hitze zu sein. Das dritte Werkzeug ist die Ofenreinigungsbürste“.
Gi.Metal hat den Teil der Blechbearbeitung bei diesen Produkten vollständig hausintern aus. Nach der Bestimmung des Materials, bei dem es sich hauptsächlich um Edelstahl 441, vorgehärteten Stahl oder auch Aluminium der Serie 6000 in Stärken von 0,8 mm bis 2,5 mm handelt, geht es an den Zuschnitt. Hier kann das Unternehmen auf eine solide Partnerschaft mit Prima Power verweisen, die vor mehr als 15 Jahren mit dem Kauf eines CO2-Lasers begann. Diesem folgte ein Fasermodell, das kürzlich durch einen brandneuen Laser Genius+ mit Be- und Entladeautomatik und Combo Tower Laser-Lagerung ersetzt wurde.
Weitere Produktionsschritte sind der Einsatz von Laserröhren zur Bearbeitung der Griffe, Abkantpressen, Fräsmaschinen und Formpressen zur Formgebung und Herstellung der Rippen auf der Schaufel und schließlich Satiniermaschinen für die Oberflächenbehandlung. Lediglich die Lackierung und Eloxierung sowie die Herstellung einiger Kunststoffteile werden an ein Netz von Unternehmen des Vertrauens vergeben.
Neben den Schaufeln, dem Hauptprodukt von Gi.Metal, stellt das Unternehmen aus Pistoia (Italien) auch Zubehör für die Teigzubereitung, das Schneiden, das Servieren und den Transport, sowie eine Reihe von Transportwagen für die Gastronomie her. Dies sind alles Produkte, bei denen das Blech eine wichtige Rolle spielt.
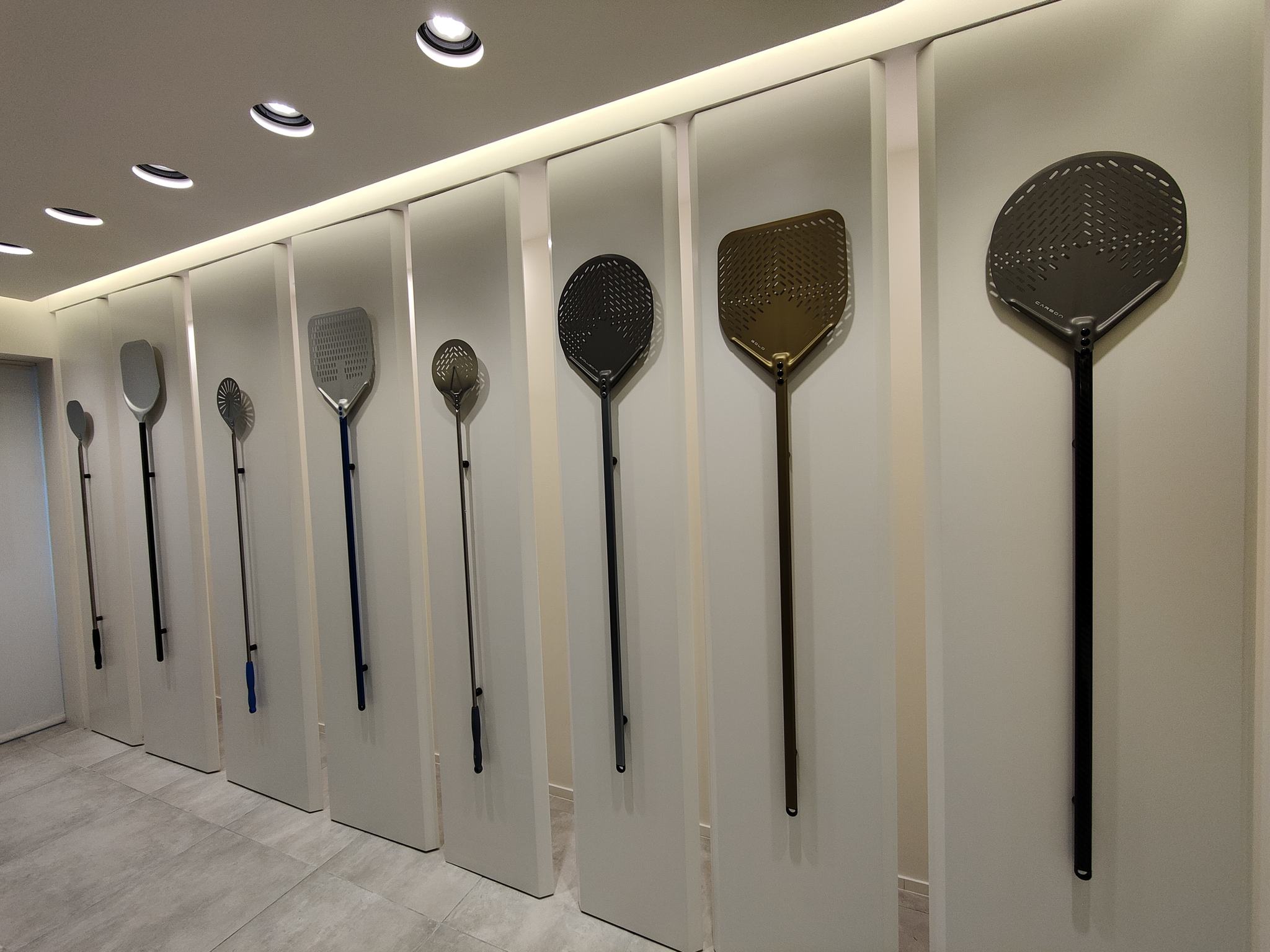
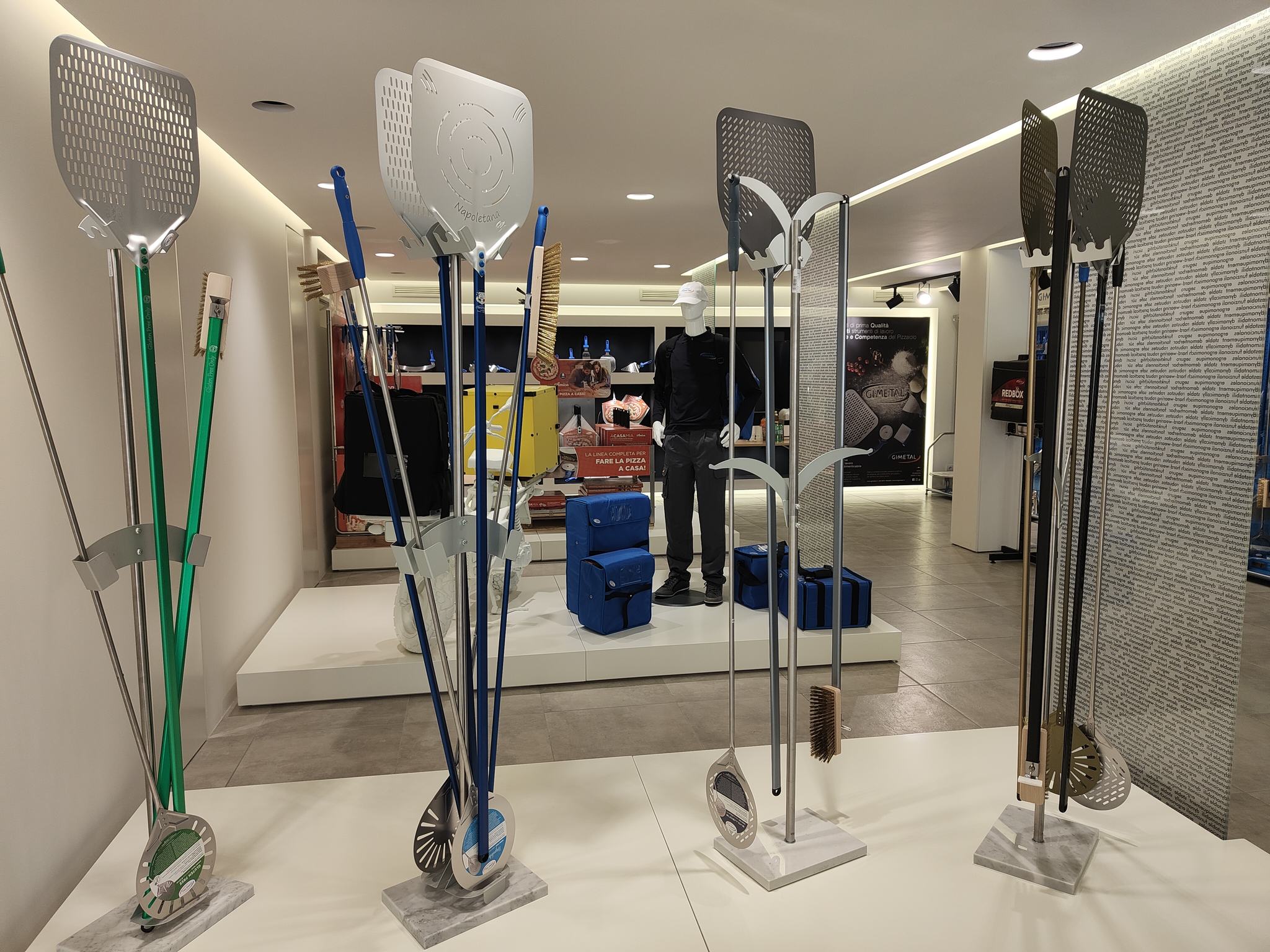
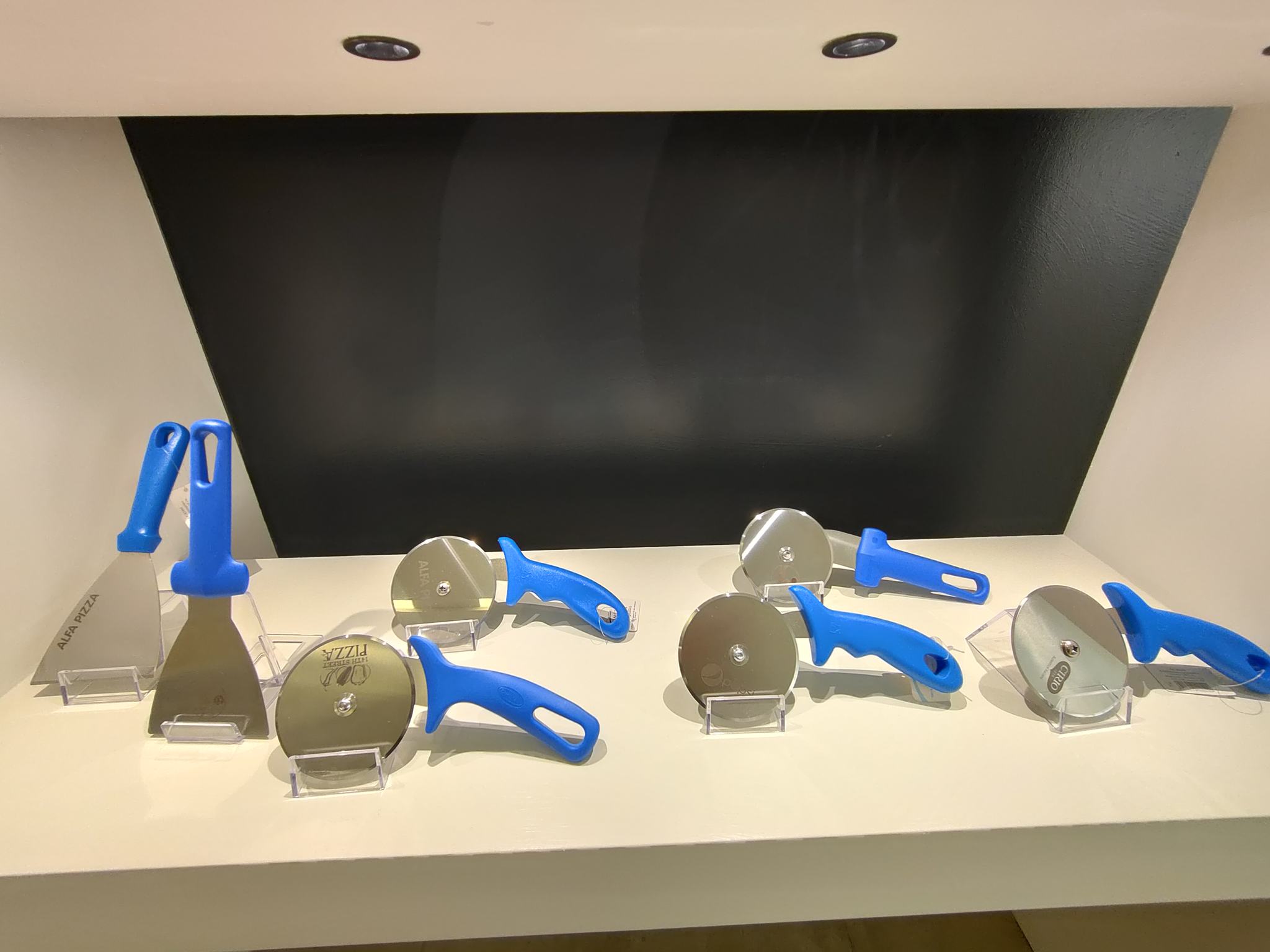
DIE TECHNIK HINTER DER EINFACHHEIT
Es ist nicht auf den ersten Blick ersichtlich, dass selbst hinter so einfachen Dingen wie Pizzaschaufeln wichtige Konstruktions- und Fertigungsfaktoren stecken, die oft den Unterschied ausmachen, und die eine präzise Planung und modernste Technologie erfordern.
Der Geschäftsführer erklärt: „Pizzaschaufeln gibt es hauptsächlich in runder oder rechteckiger Form, wobei letztere einfacher handzuhaben sind. Vieles hängt aber auch vom Geschmack des Pizzabäckers ab. Das Hauptmerkmal unserer Produkte ist, dass einige von ihnen Löcher haben, um überschüssiges Mehl von der Schaufel zu entfernen, bevor die Pizza darauf gelegt wird. Wenn sich zu viel Mehl darauf befindet, schmeckt die Pizza nicht mehr so gut und der Ofen muss häufiger gereinigt werden. Und nicht jeder ist in der Lage, diese Löcher herzustellen. Das Laser Genius+ System war für uns von größter Bedeutung, da es aufgrund seiner Dynamik ein hohes Produktionsvolumen garantiert und gleichzeitig die Herstellung von sauberen Löchern mit gut definierten Rändern ermöglicht, um die Ansammlung von Mehl zu vermeiden.“
Einer der Vorteile der Laser Genius+ ist ihre Leistung bei der Herstellung von Löchern: Bei Tests im Tech Center in Collegno (Italien) wurden 11 Löcher in weniger als 5 Sekunden hergestellt.
Ein weiterer wichtiger Aspekt, um die erforderlichen hohen Produktionsmengen zu ermöglichen, ist die Automatisierung der Laser Genius+. Mit dem Combo Tower Laser kann die Maschine problemlos bedienerlos arbeiten, und die Techniker von Prima Power haben eine Reihe von Anpassungen und Verbesserungen vorgenommen, um die Qualität und Ästhetik der Halbfertigprodukte zu erhalten.
„Wir bearbeiten extrem feine Bleche“, sagt Riccardo Barneschi, Betriebsleiter bei Gi.Metal, „und wenn ein Blech bei der Bearbeitung zerkratzt wird, haftet das Eloxal nicht mehr gut auf der Schaufel, so dass die Qualität leidet. Dies war eine unserer anfänglichen Befürchtungen bei der Einführung einer Lösung mit automatischer Be- und Entladung, aber Prima Power konnte das Problem lösen, indem es Bänder vorschlug, die das Werkstück allmählich und ohne wirkliche Reibung zur Entladestation gleiten lassen, und ein Zwischenblech zwischen die beiden Halbfertigprodukte gelegt wurde, falls diese scharfe Kanten aufweisen würden.
Nicht minder wichtig und mit dem Automatisierungssystem verbunden, das die Anlage vervollständigt, ist die Abfallentsorgung. Sie erfolgt durch das System Prima Power automatisch und ermöglicht Gi.Metal eine bezifferte Arbeitsersparnis von 3 bis 4 Stunden pro Woche, wobei die Materialien in verschiedene Behälter getrennt werden.
„Wir sind sehr froh, dass wir uns erneut für Prima Power entschieden haben“, sagt Barneschi. „Mit der Laser Genius+ sind wir in der Lage, in 40 Minuten das zu schneiden, wofür ein CO2-Laser zwei Stunden braucht und wofür ein Faserlaser der vorherigen Generation etwas mehr als eine Stunde brauchte.“
Diese konsequente Entscheidung wird nicht nur durch die technologische Leistung bestimmt, sondern auch durch die charakteristische Flexibilität und den Problemlösungsansatz des Turiner Unternehmens, der bei Gi.Metal sehr geschätzt wird.
Der Betriebsleiter erklärt: „Obwohl wir seit über 15 Jahren die Technologie von Prima Power nutzen, haben wir vor dem Kauf unseres neuesten Lasers auch andere Hersteller angefragt. Die Verfügbarkeit von Prima Power-Technikern, die unsere Verschachtelungen und Produkte analysierten und uns bei der Optimierung unserer Schneidprogramme halfen - zum Beispiel durch die Verringerung der Kopfbewegungen beim Bohren - war für die Produktivitätssteigerung von grundlegender Bedeutung und ist einer der Faktoren, die uns veranlassten, unser Vertrauen in den Hersteller aus Turin erneut zu bestätigen. Bei der Installation der Maschine konnten wir uns auch von der Plug&Play-Konfiguration des Laser Genius+ überzeugen, die eine Installation in Rekordzeit ermöglichte.
TECHNOLOGIE 4.0 UND DAS PERSONAL DER „ALTEN SCHULE“
Eine derart effiziente, von der Lean-Philosophie geprägte Produktion ist ohne eine vollständige Abbildung und Verwaltung der Prozessdaten gemäß den Vorgaben von Industrie 4.0 nicht zu erreichen. Alle Maschinen des Unternehmens, angefangen bei den Prima Power-Lasern, sind innerhalb des Unternehmens-Ökosystems vernetzt, um die Führungskräfte mit zeitnahen Informationen zu versorgen, damit sie die bestmöglichen Entscheidungen treffen können. Dabei kommt nicht nur die neueste Maschinengeneration mit Prima Power-Lasern in der Fabrik zum Einsatz, sondern es wurden auch ältere Technologien nachgerüstet, um eine vollständige Zuordnung des Produktionsbereichs zu ermöglichen. Diese Informationsflüsse werden dann mit nach- und vorgelagerten Phasen wie Einkauf, Rechnungsstellung und Lagerhaltung integriert, um ein Echtzeit-Business-Management-Dashboard bereitzustellen, das überall auf der Welt genutzt werden kann.
Bei einem derart modernen Ansatz für das Maschinenmanagement ist sich Gi.Metal darüber im Klaren, dass der Bediener hinter der Maschine für die Produktion genauso wichtig ist, wie es das Motto des Unternehmens „Made with passion“ am besten ausdrückt.
„Meiner Meinung nach ist die Konzentration auf die Menschen der Schlüssel“, sagt D'Annibale, „denn sie sind keine Maschinen, sondern viel komplexere Wesen, jedes mit seinen eigenen Schwächen, Ambitionen und Hoffnungen, und dafür ist Einfühlungsvermögen erforderlich. Wenn man dies berücksichtigt, kann man im Unternehmen ein positives Umfeld schaffen, in dem sich die Mitarbeiter geschützt fühlen. Damit meine ich nicht nur eine angemessene finanzielle Entlohnung, sondern auch ein gutes betriebliches Wohlergehen, Belohnungen und eine Ausbildung, die ihren Ambitionen entspricht.“
IMMER BEREIT FÜR NEUE HERAUSFORDERUNGEN
Zu den Plänen von Gi.Metal für die Zukunft gehört auch, die Welt der Pandemie hinter sich zu lassen. Früher reiste die Geschäftsleitung zusammen mit anderen Unternehmen der Branche in die ganze Welt zu Messen und Ausstellungen, um die Idee der italienischen Küche ins Ausland zu tragen. Diese Gewohnheit musste in den letzten zwei Jahren aufgegeben werden, was jedoch dem stetig steigenden Umsatz keinen Abbruch angetan hat.
„Vor der Pandemie haben wir mehr als 50 Messen besucht“, sagt D'Annibale, „und diese waren eine hervorragende Gelegenheit, neue Unternehmen kennenzulernen, von denen wir wichtige Ideen für die Umsetzung in neue Produkte erhielten. In den letzten Jahren fiel es mir schwer, nicht mehr so viel zu fliegen wie früher, aber ich hoffe, dass sich die Dinge in dieser neuen Normalität wieder einpendeln und ich weiterhin entdecken kann, dass es immer möglich ist, etwas Neues zu schaffen, selbst in einer Welt, in der die Menschen denken, dass alles schon erfunden wurde, und Gi.Metal in seiner jetzigen Form weiter voranzubringen: eine moderne Industrie, aber mit einem Schwerpunkt auf dem Handwerk, während das Label Made in Italy weltweit gefördert wird. Der Beitrag eines Partners wie Prima Power, der auch die Marke Made in Italy fördert, wird in dieser Hinsicht immer wichtiger.“
PRÄZISION UND PRODUKTIVITÄT MADE IN COLLEGNO, ITALIEN
Schnelligkeit, Präzision und Effizienz sind die Hauptmerkmale der Laser Genius+, der jüngsten Ergänzung der Maschinenreihe von Prima Power für das 2D-Laserschneiden. Es handelt sich um eine äußerst produktive und flexible Faserlasermaschine, die sich an jedes Kundenlayout anpassen kann, ohne dass die Konfiguration beeinträchtigt wird. Die Laser Genius+ verfügt über eine Portal-Architektur, die ein hohes Maß an thermischer Stabilität, Schwingungsdämpfung und hoher Dynamik gewährleistet, auch dank kompakter Motoren und Getriebe mit größerer Leistung pro Stellfläche und maximaler Energieeffizienz.
Die Laser Genius+ ist eine Plug&Play-Maschine, die für eine einfache Installation konzipiert wurde, so dass sie sofort in Betrieb genommen werden kann und die Amortisation verbessert. Der Lasergenerator, die Kühler, die Motoren und die Optik sind in der Kabine integriert und garantieren eine einfache und schnelle Installation: Von der Lieferung bis zur Produktion in einem Werk dauert es in der Regel nur zwei Tage.
Um den Produktionsanforderungen der unterschiedlichsten Kunden gerecht zu werden, ist die Laser Genius+ in drei Größen erhältlich: 1530 (mit 3.150 x 1.600 mm Achsenhub und einer maximalen bearbeitbaren Last von 1.150 kg), 2040 (mit 4.320 x 2.200 mm Achsenhub und einer maximalen bearbeitbaren Last von 2.100 kg) und 2060 (mit 6.320 x 2.200 mm Achsenhub und einer maximalen bearbeitbaren Last von 3.050 kg). Die maximal erreichbare Bewegungsbahngeschwindigkeit beträgt bei allen Versionen 180 m/min und es können Faserquellen von 2 bis 10 kW installiert werden.
Um die maximale Produktivität zu gewährleisten, kann die Laser Genius+ mit allen Automatisierungen des Prima Power Portfolios geliefert werden: von Be- und Entladelösungen bis hin zu Sortiersystemen und dem flexiblen Produktionssystem Night Train.
Die Verfügbarkeit der Techniker von Prima Power, die unsere Schachtelungen und Produkte analysierten und uns bei der Optimierung unserer Schneidprogramme halfen, war für die Produktivitätssteigerung von grundlegender Bedeutung und ist einer der Faktoren, die es uns ermöglichten, unser Vertrauen in den Turiner Hersteller erneut zu bestätigen.