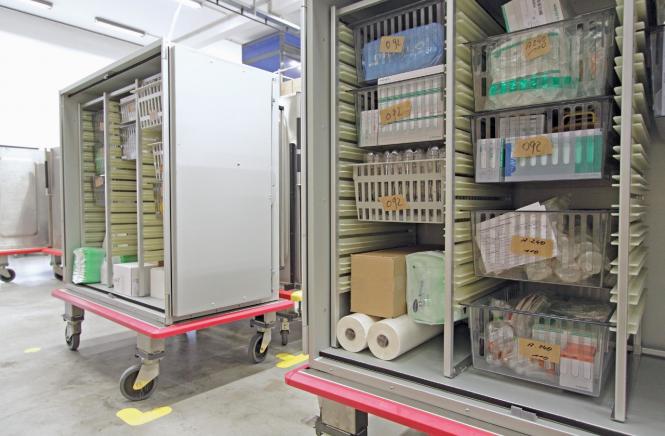
En perfekt kombination för sjukvårdssektorn
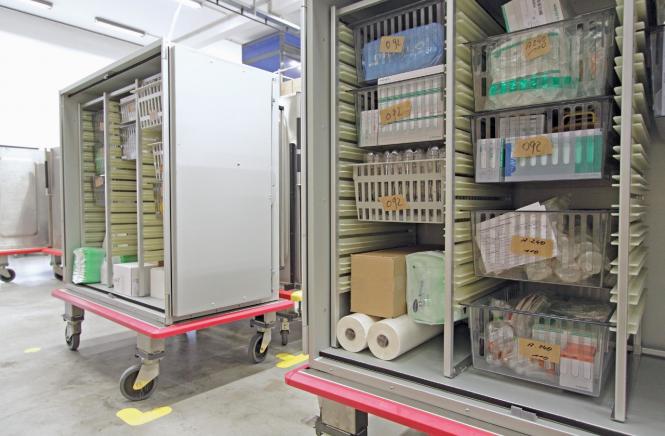
Aluminium och rostfritt stål är de material som Alvi använder för att tillverka vagnar för sjukhus, tvätterier, äldreboenden, hotell, industri och textilindustrin.
Företagets produkter exporteras världen över och tillverkas med hjälp av ett produktivt plåtbearbetningssystem som kombinerar stansning och vinkelsaxklippning från Prima Power med stöd av effektiv automatisering.
Utformning och produktion av lösningar för logistik och distribution av material på sjukhus, hotell, tvätterier, äldreboenden och textilfabriker är vad Alvi har arbetat med i över 50 år. Företaget grundades 1972 i Caresanablot i provinsen Vercelli (Italien) och man tillhandahåller ett stort utbud av standardprodukter och anpassade produkter. Det handlar främst om vagnar i ordets bredaste bemärkelse (från vagnar med säckhållare till olika typer av skåpvagnar till avfallscontainrar), samt skyttelsystem, behållare och hyllor av många olika slag.
”Våra lösningar kan tillfredsställa många av marknadens behov”, förklarar ägaren Fiorenza Viazzo, ”och nu kan vi tillverka dem i aluminium och rostfritt stål.”
I grunden för sådan flexibilitet och mångsidighet ligger en guldgruva av teknisk utrustning, som kröns av en kombinerad stansnings- och vinkelsaxcell med stöd av ett plocknings- och staplingssystem för avancerad hantering av material. Den har ett anslutet system för val av små komponenter, vilket lyfter fram processens effektivitet ytterligare när det gäller produktionslinjen med hög prestanda från Prima Power, maskindivisionen inom Prima Industrie Group.
”Genom att köpa in det här nya systemet har vi inte bara kunnat öka vår produktionskapacitet och bearbetningskvalitet”, betonar Viazzo, ”utan vi har även utökat våra möjligheter att bearbeta tunnare plåtar av rostfritt stål, ett material som efterfrågas alltmer av våra kunder.”
Från textiler till sjukhussektorn, från aluminium till rostfritt stål
Alvi började med att huvudsakligen leverera produkter till den blomstrande textilindustrin, genom att förse både provinsen Vercelli och hela Italien med vagnar, skåp och relaterade aluminiumprodukter. Under 1990-talet såg man positivt på det här specialområdet och man visade stort intresse inom industritvättsektorn, särskilt för sjukhus och äldreboenden. Det här var ett område som från början av det nya millenniet blev ännu mer framträdande, vilket ledde till ett ständigt växande produktutbud.
”Produktionen för textilindustrin var inledningsvis framför allt i aluminium och inte i rostfritt stål”, förklarar Viazzo, ”men inom sjukhussektorn var vi i princip tvungna att enbart välja eloxiderade produkter. Därför har vi genom åren utvecklat en egen avdelning med en anläggning för ytbehandlingar, som fortfarande är i drift.”
Den konstanta tillväxten av volymer och beställningar tvingade företaget att anpassa sin teknik, samt öka hastigheten för stansning och klippning. 1995 ledde det till att man utrustade en avdelning med ett system för plåtbearbetning från det som då hette Finn Power, som var i drift till för några år sedan, då allt hårdare konkurrens krävde att den byttes ut. När man planerade sin nya investering bestämde sig företaget för att undersöka vad som fanns på marknaden och valde återigen en produkt från samma tillverkare, som under tiden hade blivit en del av Prima Industrie Group.
”Vi behövde göra vår produktutvecklingscykel ännu mer effektiv”, berättar Viazzo, ”så att den även omfattade möjligheter att bearbeta rostfritt stål, ett material som vi innan dess hade lagt ut på externa partner med expertkunskaper.”
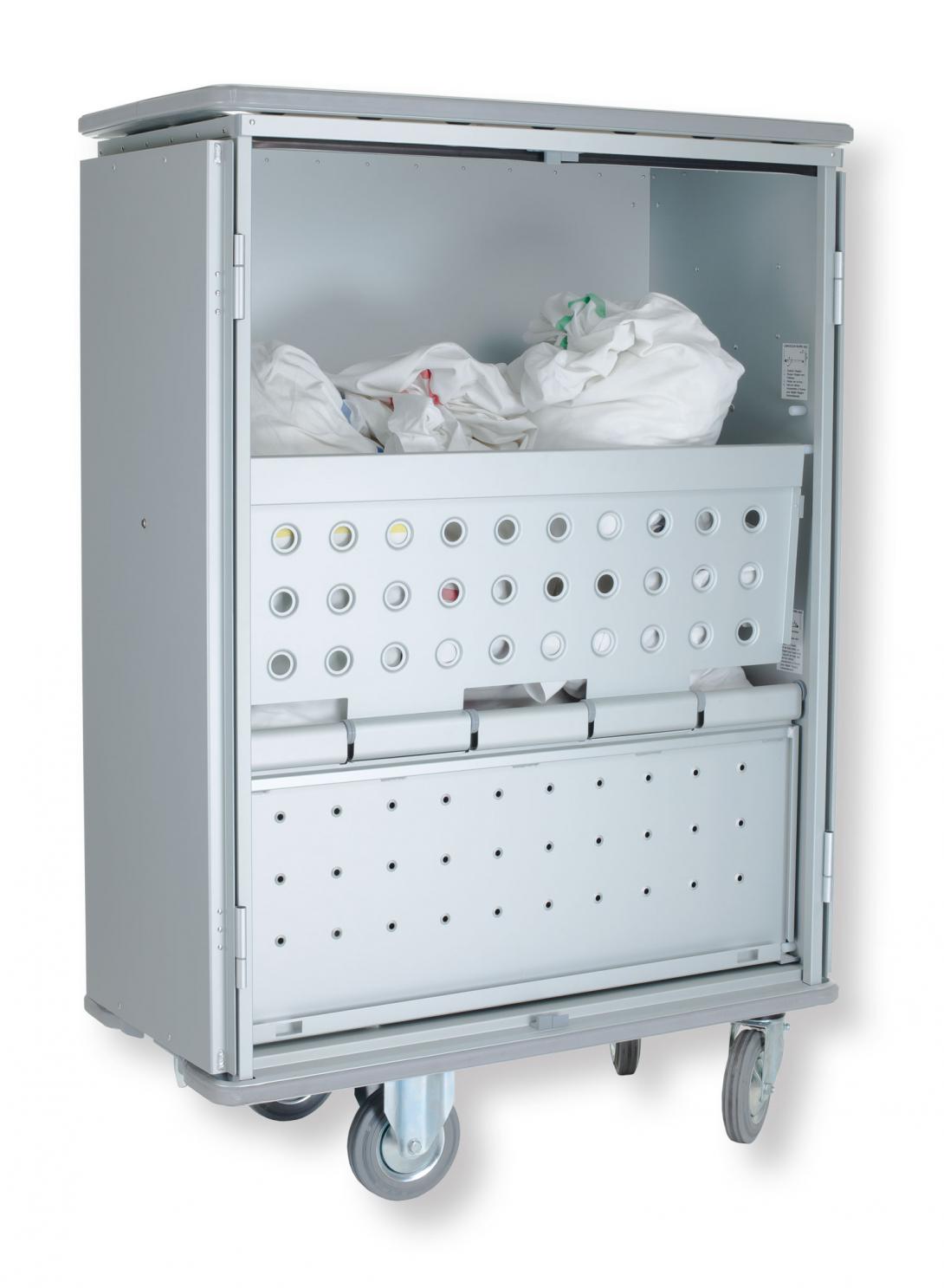
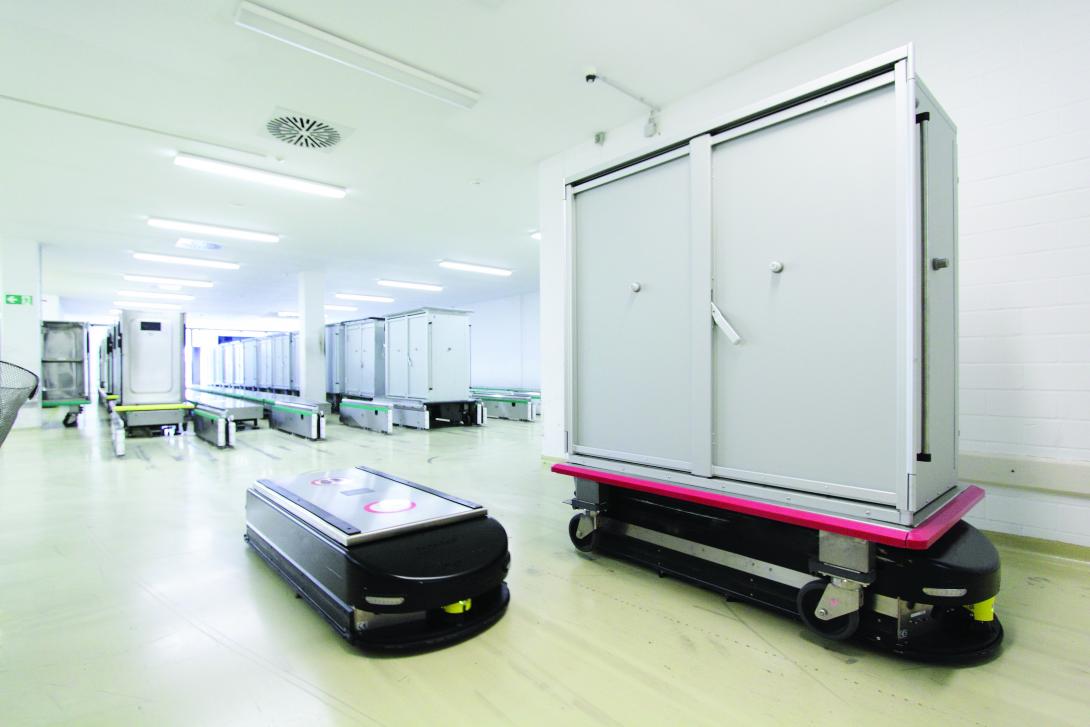
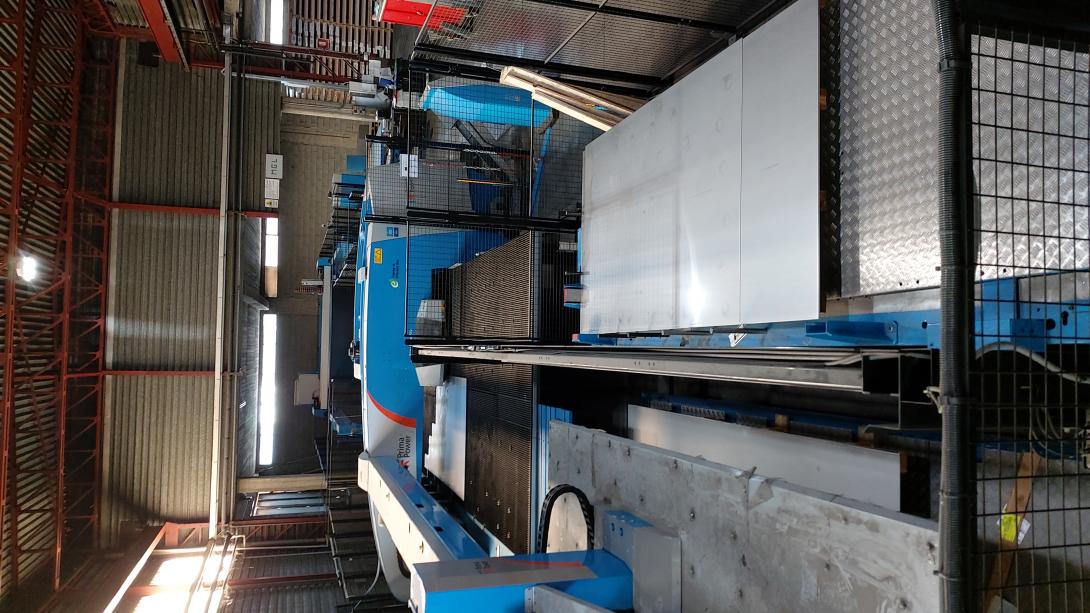
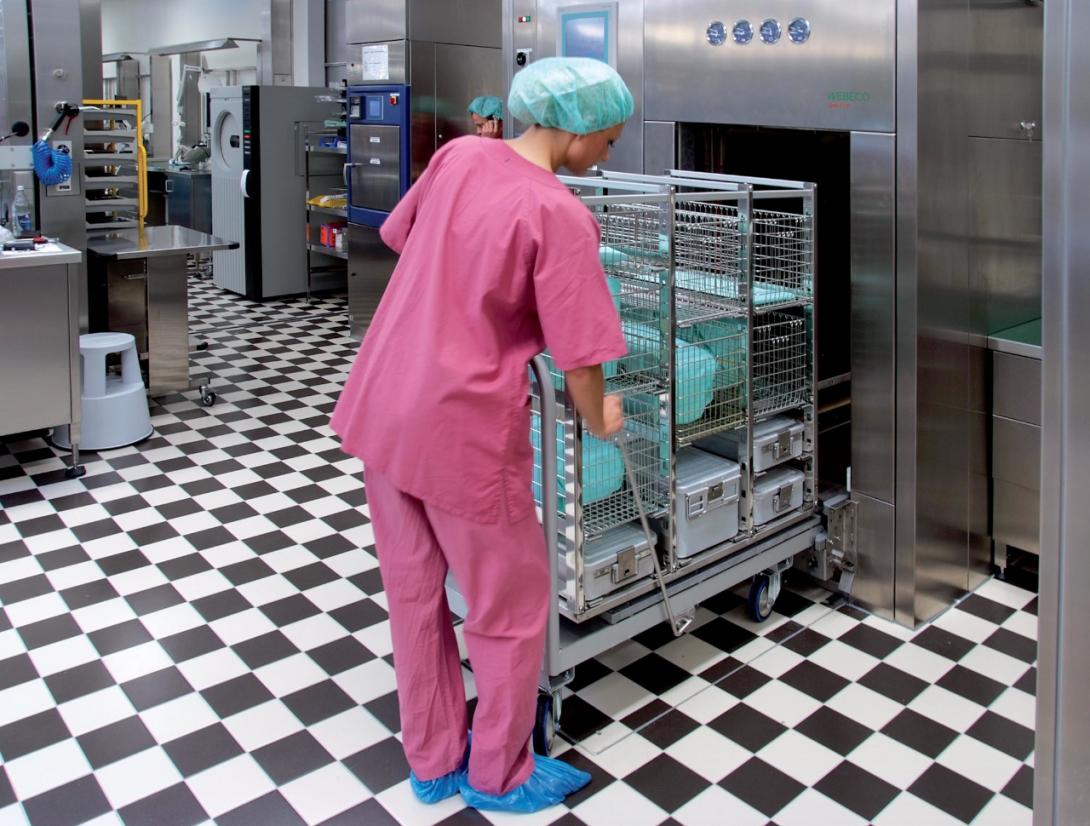
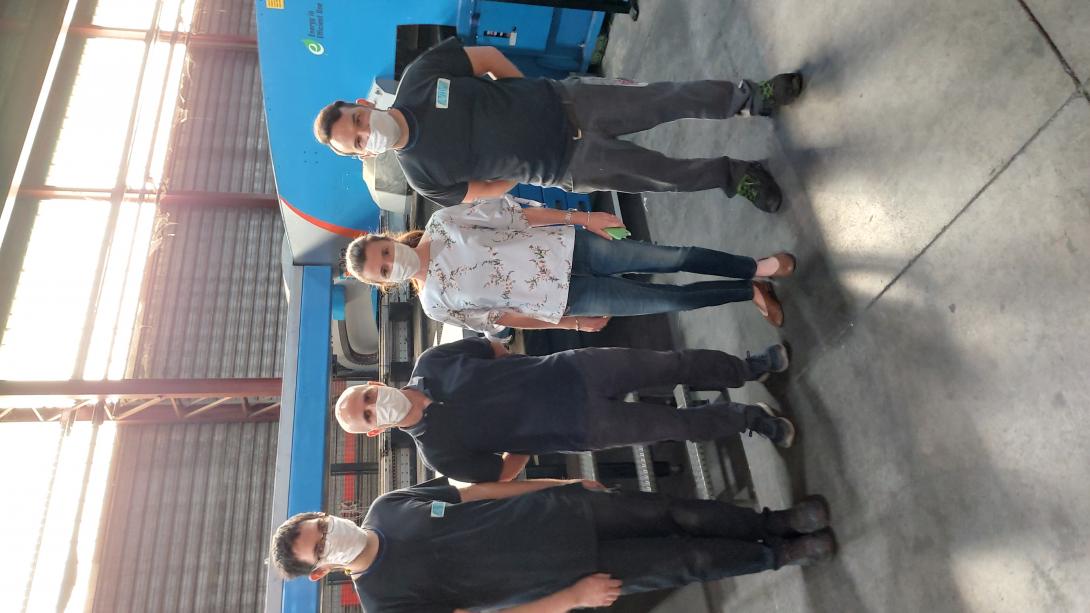
Mervärde i selektiv separering och stapling
När man tittar på den i detalj består den nya Prima Power-anläggningen som har installerats hos Alvi av en Shear Genius SGe8 (en servoelektrisk integrerad cell för stansning och klippning), med ett kombinerat PSR8-system (plocknings- och staplingsrobot) och SU-C, en automatisk sorteringsenhet för detaljer som har skurits till mindre mått.
De flesta metallkomponenter som har utformats av företaget för dess produkter tillverkas av rektangulära metallplåtar. Stansning och sedan klippning till enstaka detaljer i samma automatiserade process med en integrerad vinkelsax är onekligen en ekonomisk och konkurrenskraftig metod. Det är viktigt att komma ihåg att detaljer med bara två eller tre raka kanter är perfekta att använda i en vinkelsax. Den här tekniken har Prima Power nästan 40 års erfarenhet av, eftersom man har tillverkat stansar sedan 1982 och har haft en vinkelsax integrerad i pressen sedan 1987, vilket ger en kraftfull produktionscell.
”Vi använder aluminium huvudsakligen med tjocklekar mellan 1,2 och 1,5 mm för vagnkarosser”, fortsätter Viazzo, ”och upp till 4 mm för baser. När det gäller rostfritt stål är tjocklekarna mellan 0,8 och 1,2 mm för karosserna och upp till 2–2,5 mm för baser.”
Den Shear Genius SGe8-konfiguration som Alvi valde gör det möjligt att mata in plåtar med en storlek på upp till 1 565 × 4 300 mm, med en stanskraft på 300 kN i en hastighet som kan uppgå till 2 500 slag/min, och med en positioneringshastighet på 150 m/min och ett rotationsindex på 25 v/min. Maskinen kan bearbeta en plåt som är full av detaljer till ett antal färdiga delar med selektiv separation och stapling tack vare det ovannämnda PSR-robotsystemet. Dessa delar kan flyttas till de sista produktionsfaserna utan att man behöver dyra sekundära åtgärder för inmatning, stansning, klippning och sortering. Med Shear Genius SGe8 kan man också använda förskurna plåtar, även om plåtar i standardformat bearbetas med större besparingar tack vare avancerade nestningsfunktioner.
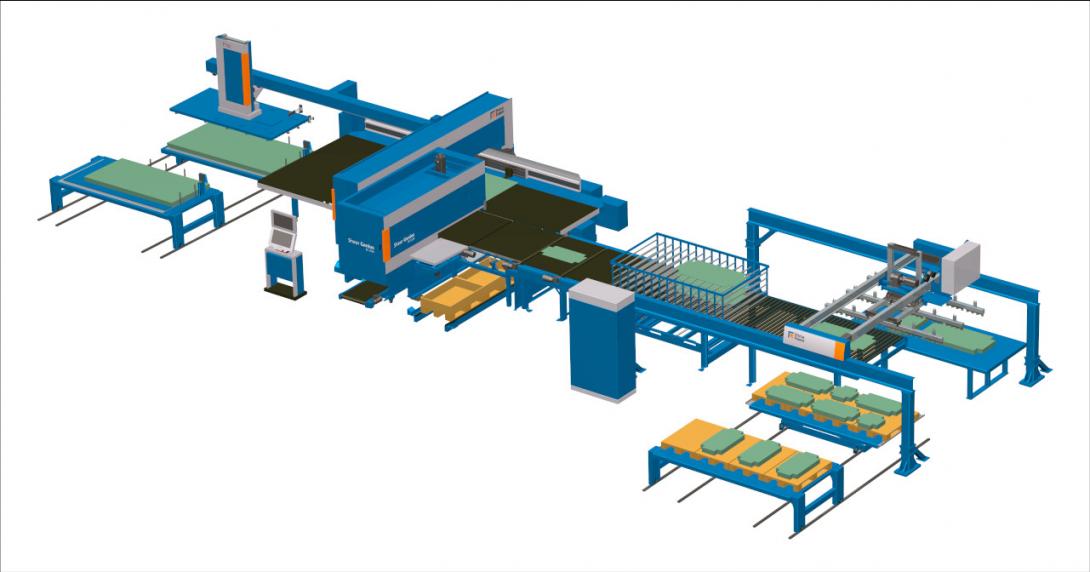
Automatisk sortering, effektiv process
”När vi valde systemet var det mycket viktigt att kunna utvärdera och uppskatta möjligheterna med utmatningssystemet för producerade delar”, avslöjar ägaren, ”dvs. den del som hanteras av PSR8-sugroboten med sina fem axlar som kan programmeras för plockning och stapling. Det gäller inte bara dess prestanda, utan även dess driftläge, tack vare hantering som säkerställer bearbetning som är anpassad efter de estetiska kraven för vår produkt – med andra ord bearbetning utan fel som kan orsaka defekter på ytan.”
Företaget värdesätter även hanteringssystemet som infördes nedströms från stansningen och klippningen för geometriskt mindre tillverkade produkter (inte större än 200 × 300 mm) och som därför inte kan palleteras. Det här är SU-C-valsystemet som, tack vare Prima Powers design och utveckling, gör att man inte behöver skicka den här typen av produkter till PSR8-staplaren i slutet av linjen. Enheten är placerad under C1500-transportören och kräver att det finns två eller tre europapallar på kedjetransportören, som kan delas in i två sektioner för att skapa från fyra till sex utmatningsdestinationer. Liksom som med PSR8-systemet är den här metoden anpassad för maximal effektivitet.
I det här sammanhanget är stora volymer, hög grad av automatisering för hantering av obemannade skift på ett tillförlitligt och säkert sätt, låg energiförbrukning (i genomsnitt mindre än 5 kW) och minskade underhållskostnader (eftersom anläggningen är servoelektrisk) de främsta fördelarna med Prima Power som Alvi värdesätter.
”Jag skulle även vilja tillägga användarvänlighet och repeterbarhet för precision”, avslutar Viazzo. ”Allt det här är aspekter som har bidragit och fortsätter att bidra till ökad konkurrenskraft, snabbare bearbetning, kvalitet vid ytbehandling och möjlighet att även arbeta med stål.”
Det är viktiga delar för att övervinna nya utmaningar på marknaden, som i dag är alltmer internationell när ungefär 70–80 % av produktionen går utomlands.
Genom att köpa in det här nya systemet har vi inte bara kunnat öka vår produktionskapacitet och bearbetningskvalitet, utan vi har även utökat våra möjligheter att bearbeta tunnare plåtar av rostfritt stål, ett material som efterfrågas alltmer av våra kunder
Vill du ha en liknande lösning till ditt företag? Du hittar den här
Shear Genius EVO
KOMBINERADE STANS- OCH KLIPPMASKINER