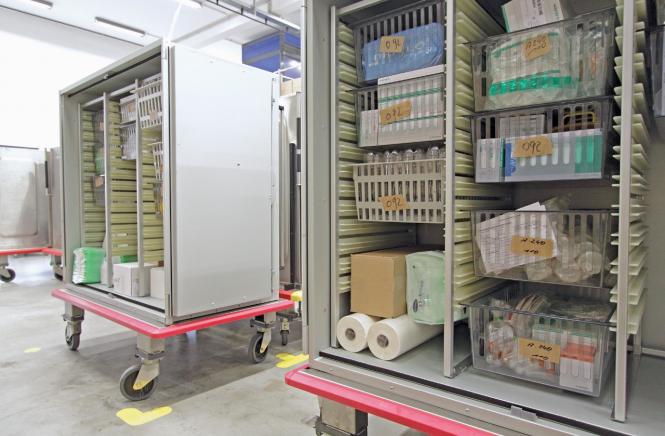
A perfect combination for the medical sector
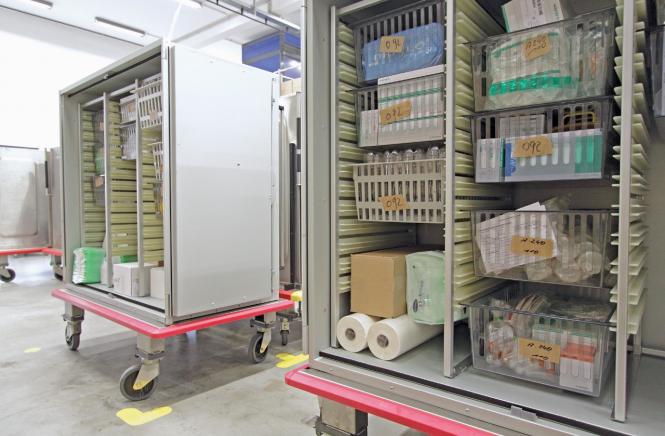
Aluminum and stainless steel are the materials used by Alvi to produce trolleys for the hospital, laundry, retirement home, hotel, industrial and textile sectors.
Its products are exported around the world and manufactured thanks to a productive sheet metal working system combining punching and right angle shearing by Prima Power supported by efficient automation.
Design and production of solutions for logistics and the distribution of materials in hospitals, hotels, laundries, retirement homes and textile industries – this is what Alvi has been doing for over half a century, a company founded in 1972 in Caresanablot in the province of Vercelli (Italy), which provides a wide range of standard and customized products. We are mainly talking about trolleys, intended in the broadest sense of their use (from sack-holder trolleys, to cabinet trolleys in various forms, to refuse containers), as well as shuttle systems, containers and shelving of many kinds.
“Solutions”, explains owner Fiorenza Viazzo, “able to satisfy the diverse needs of the market and that now we can produce in aluminum and stainless steel.”
At the basis of such flexibility and versatility is a wealth of technological equipment, whose epitome is a combined punching and right angle shearing cell supported by a picking and stacking system for advanced management of the movement of materials, with a connected system for selecting small components, further highlighting the efficiency of the process i.e. the high performance production line supplied by Prima Power, the Machinery Division of the Prima Industrie Group.
“The purchase of this new system”, underlines Viazzo, “has allowed us not only to increase production capacity and processing quality, but also to extend our ability to process thinner sheets of stainless steel, a material that has been increasingly in demand by our customers.”
From textiles to the hospital sector, from aluminum to stainless steel
Alvi started out mainly supplying the thriving textile industry, providing both the province of Vercelli and the whole of Italy with trolleys, cabinets and related aluminum products. During the 1990s, this specialty was viewed positively and great interest was shown within the industrial laundry sector, especially in hospitals and retirement homes. This was an area that, from the start of the new millennium, became even more prominent, resulting in a continuously expanding product offering.
“If for the textile industry production was initially mainly in aluminum and not stainless steel”, explains Viazzo, “within the hospital sector the choice was basically forced to turn to completely anodized products. This is the reason why over the years we created our own dedicated department, with a plant for ad hoc superficial treatments, which is still operational.”
The constant growth in volumes and orders forced the company to adapt technologically, also to increase the speed of punching and shearing. In 1995, this led to equipping a department with a sheet metal processing system by the then Finn Power, which remained operational until a few years ago, when ever increasing competition required it to be replaced. In planning its new investment, the company decided to examine what was available on the market, and went back to choosing a product from the same manufacturer that in the interim had become part of the Prima Industrie Group.
“We needed to make our product development cycle even more efficient”, revealed Viazzo, “also integrating the ability to process stainless steel, a material that up until then we had outsourced to expert external partners.”
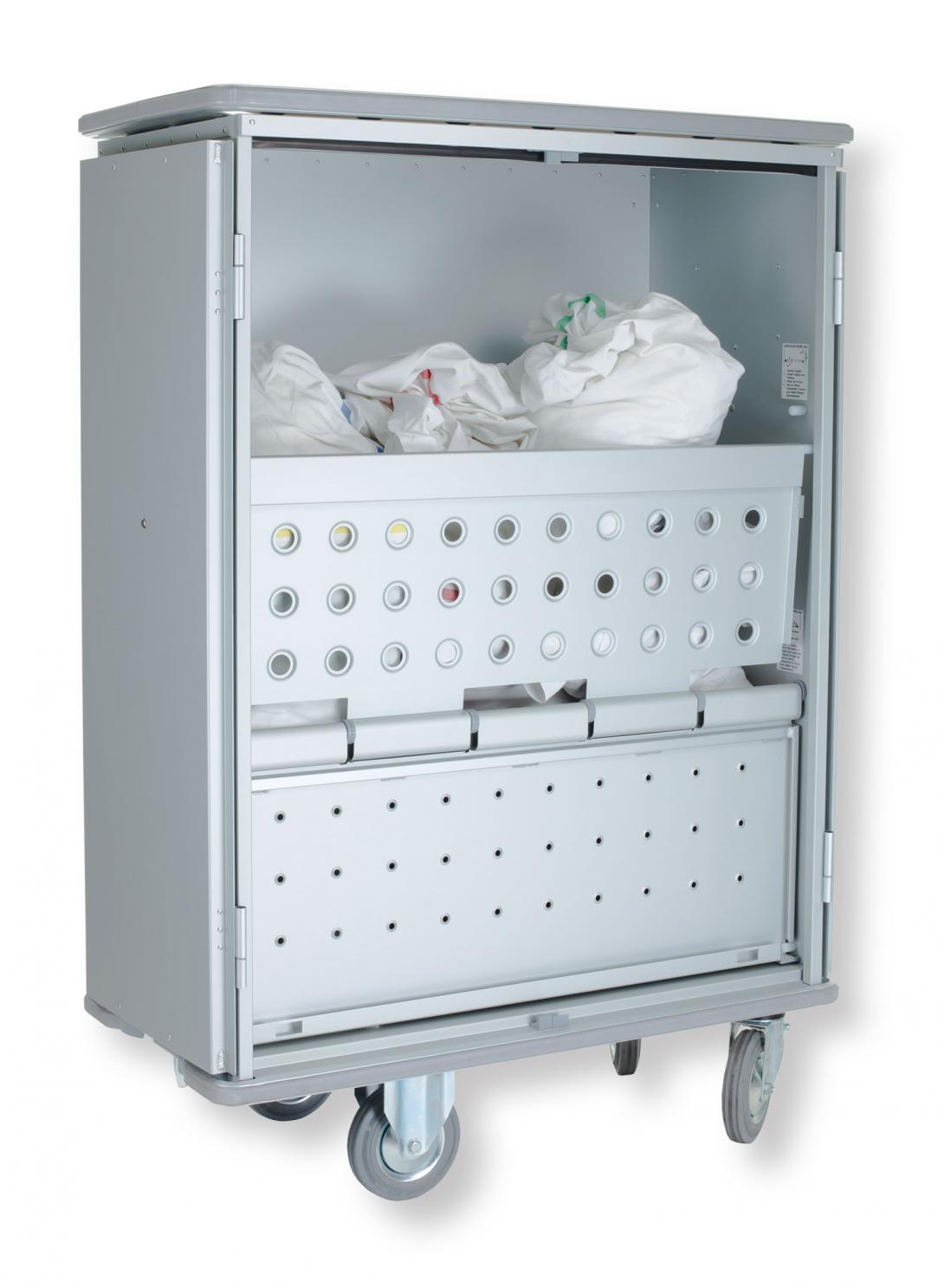
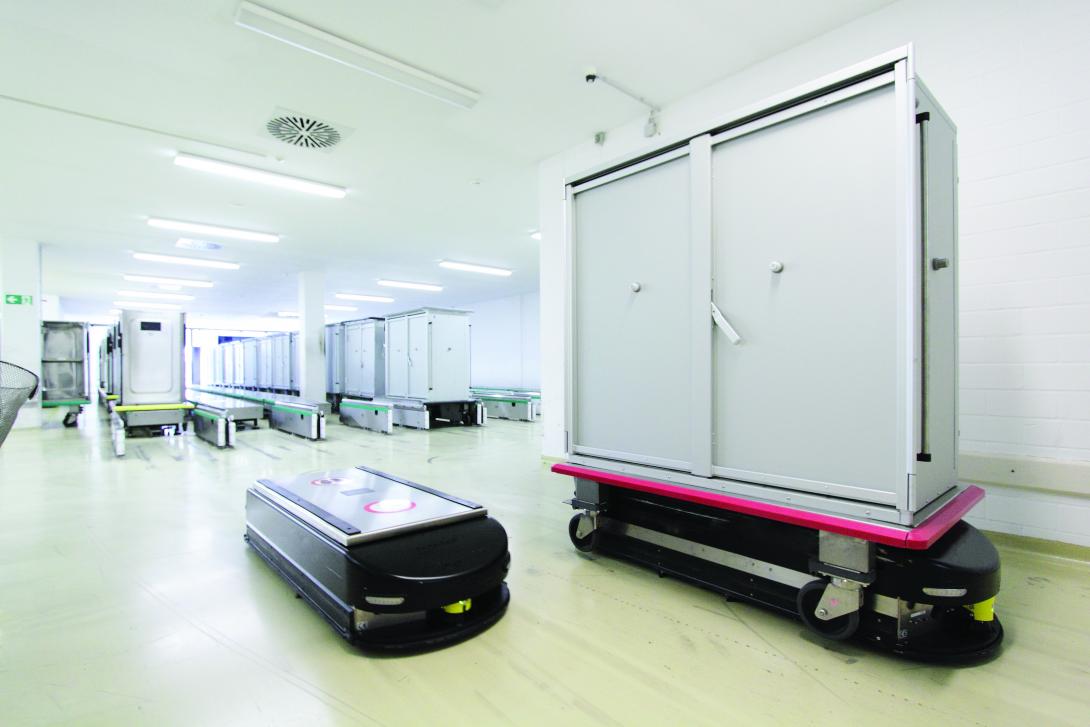
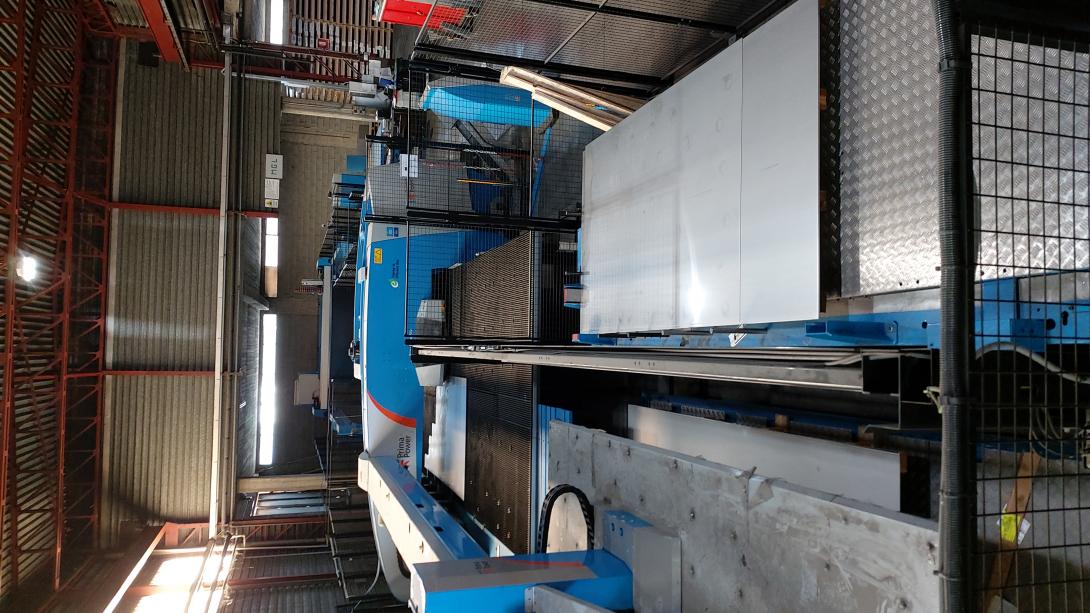
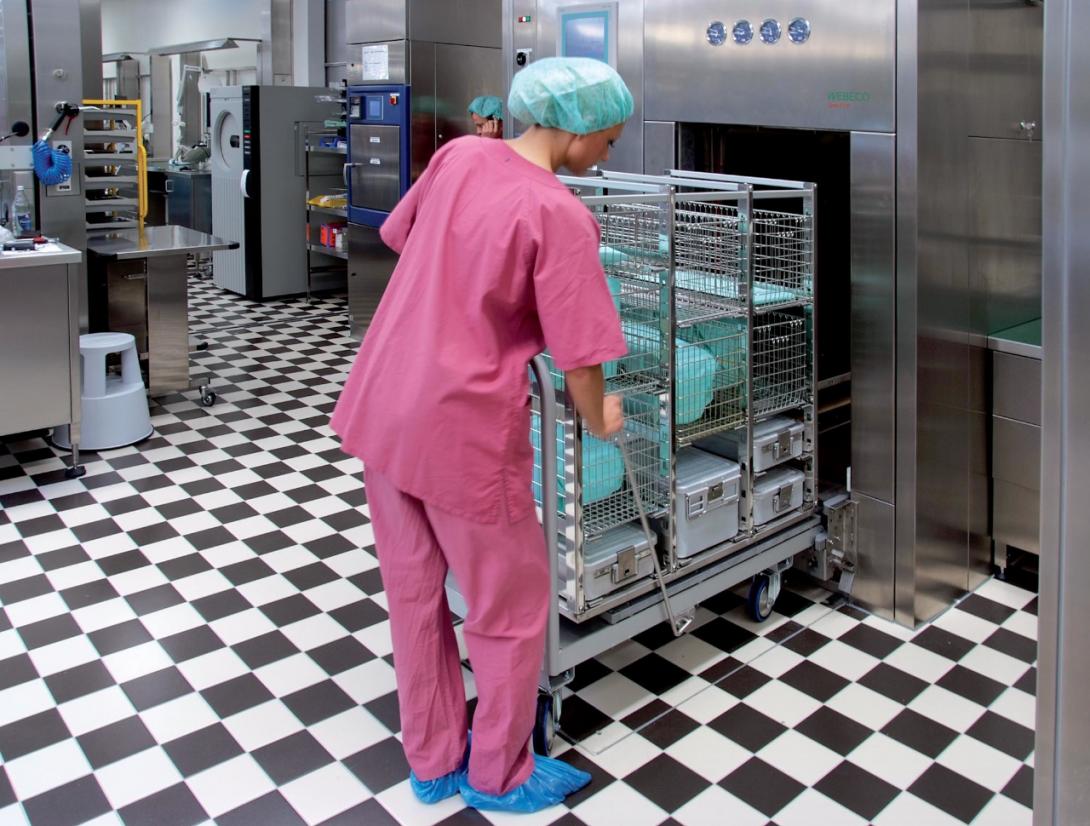
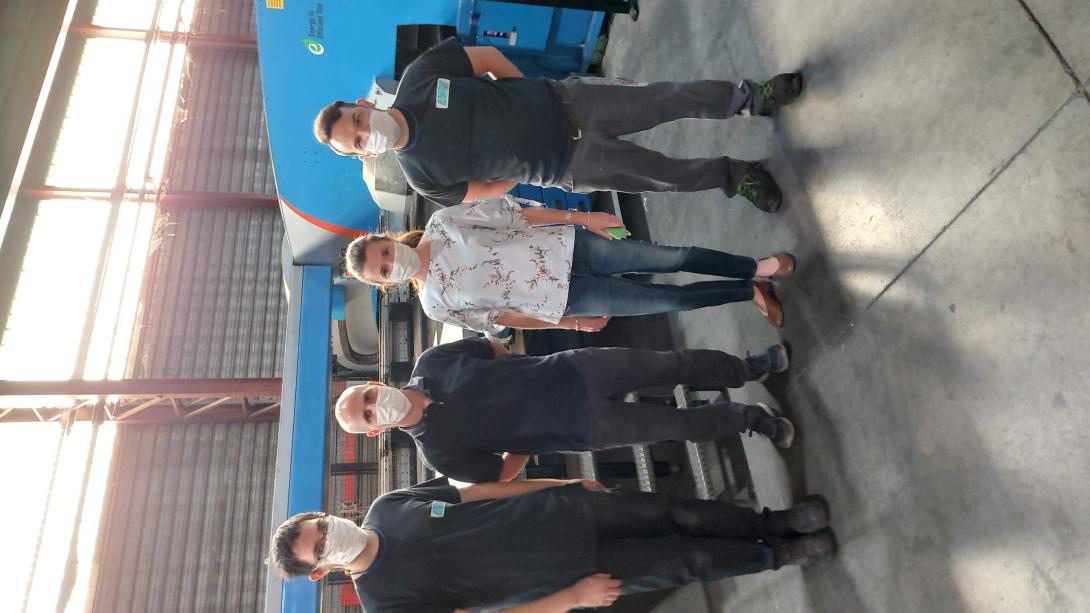
Added value in selective separation and stacking
Looking at it in detail, the new Prima Power plant installed at Alvi consists of a Shear Genius SGe8 (a servo-electric punching and shearing integrated cell), with combined PSR8 system (picking and stacking robot) and SU-C, an automatic sorting unit for parts cut to smaller dimensions.
The great majority of metal components designed by the company for its products are processed from rectangular sheets of metal. An economical and competitive method of production is without doubt punching and then shearing into single parts within the same automated process, with an integrated right-angle shear. It is important to note that parts with only two or three straight edges are perfect to use in an angular shearer. These are technologies that Prima Power boasts almost 40 years of experience in, since it has been manufacturing punches since 1982, and from 1987, has been integrating a right-angle shear into the press, resulting in a powerful production cell.
“Aluminum”, continues Viazzo, “is mainly used by us in thickness between 1.2 and 1.5mm for trolley bodies, and up to 4mm in the case of bases. In stainless steel, the thicknesses are between 0.8 and 1.2mm for the bodies and up to 2 – 2.5mm for bases.”
The Shear Genius SGe8 configuration chosen by Alvi allows to load sheets up to 1,565 x 4,300mm in size, ensures a punching force of 300kN at a rate that can reach 2,500 strikes/min, and with a positioning speed of 150m/min and a rotation index of 25 RPM. The machine can process a sheet full of details into a number of finished parts with selective separation and stacking thanks to the already-mentioned PSR robotic system. These parts can be moved to the final phases of production without the need for expensive secondary operations for loading, punching, shearing and sorting. With Shear Genius SGe8 pre-cut sheets can also be used, even though standard format sheets are processed with greater savings thanks to advanced nesting functions.
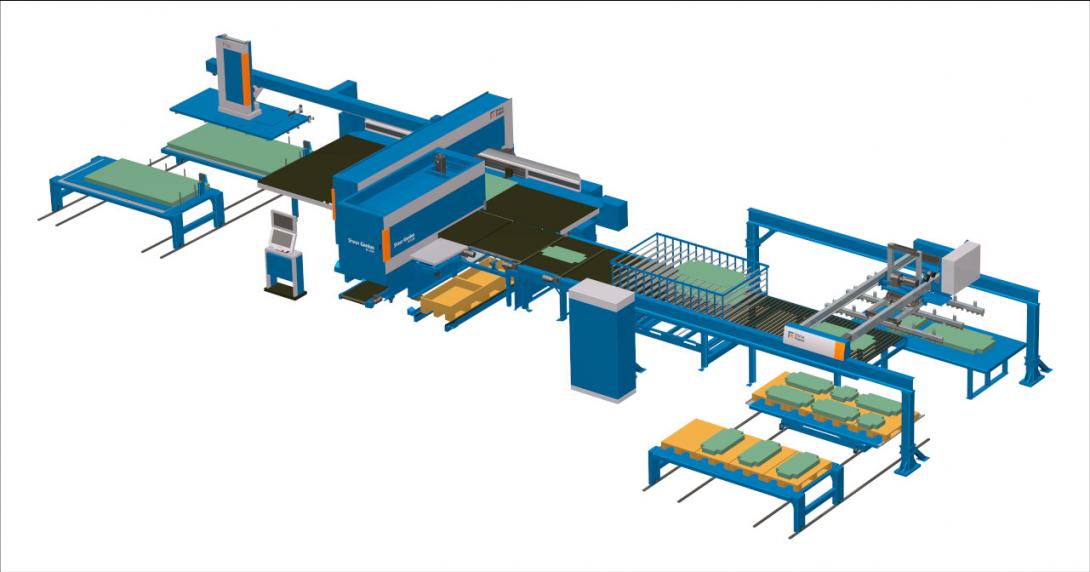
Automatic sorting, efficient process
“When choosing the system”, reveals the owner, “it was vitally important to be able to evaluate and appreciate the potential of the unloading system of the produced parts, that is, the part managed by the PSR8 suction robot with its 5 axes that can be programmed for picking and stacking; not only in terms of performance, but also regarding its operating mode, thanks to handling that ensures processing aligned to the aesthetic requirements of our product – in other words, processing without errors that could cause superficial imperfections.”
Equally valued by the company from Piedmont was the management system adopted downstream of the punching and shearing for geometrically smaller manufactured products (no greater than 200 x 300mm in size), and that therefore cannot be palletized. This is the SU-C selection system that, thanks to Prima Power’s design and development, stops the need to send this type of product to the PSR8 stacker at the end of the line. The unit is placed under the C1500 conveyor and requires two or three Euro pallets to be on the chain conveyor, which can be divided into two sections to create from four to six unloading destinations. As with the PSR8 system, this is an approach geared towards maximum efficiency.
In this context, high volumes, a high degree of automation to manage unmanned shifts in a reliable and safe way, low energy consumption (on average less than 5kW) and reduced maintenance costs (since the plant is servo-electric) are the main advantages provided by Prima Power that Alvi values.
“I would like to add”, concludes Viazzo, “the ease of use and repeatability of precision. These are all aspects that have and continue to contribute toward increasing our competitiveness, providing speed in processing, quality in finishing and the ability to also work with steel.”
Indispensable elements to overcome new market challenges, that nowadays are increasingly of international scope since approximately 70/80% of production goes abroad.
The purchase of this new system has allowed us not only to increase production capacity and processing quality, but also to extend our ability to process thinner sheets of stainless steel, a material that has been increasingly in demand by our customers
Are you looking for a similar solution for your company? Find it here
Shear Genius EVO
MASZYNY KOMBI DO WYKRAWANIA I CIĘCIA GILOTYNĄ