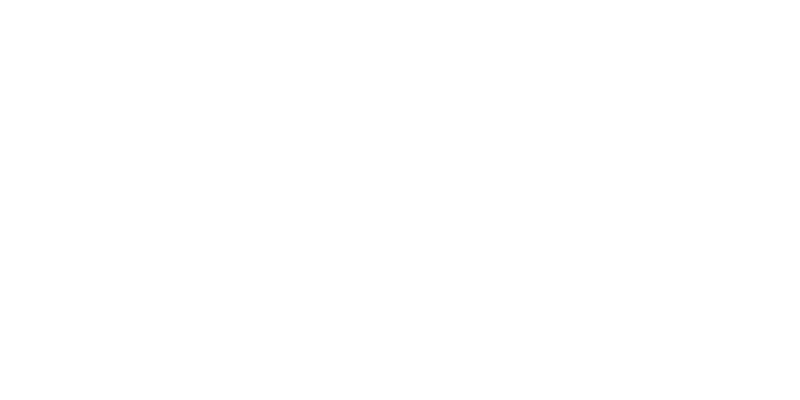
Компания Vacuum Technology Inc., выбирает лазер Platino Fiber
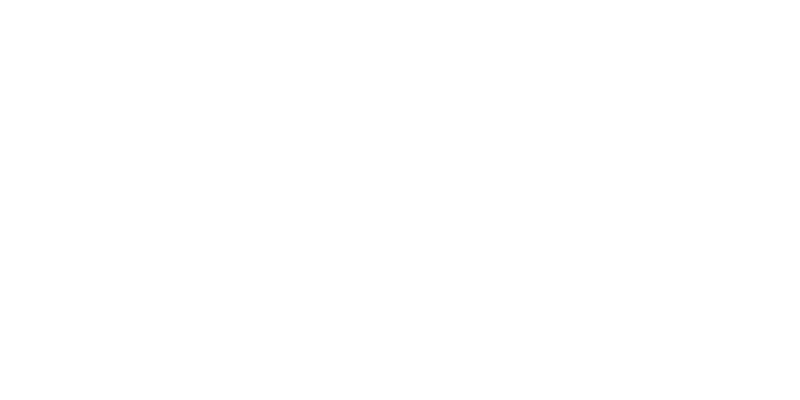
Laser cutting addition speeds production for a Tennessee supplier of gas-leak-testing technology while freeing waterjet cutting machines for other work. It’s an all-around win for Vacuum Technology Inc.
The city of Oak Ridge, TN, established in 1942 as a production site for the Manhattan Project—the massive American, British, and Canadian operation that developed the atomic bomb—most assuredly retains its technological prowess. With its Oak Ridge National Laboratory and Y-12 National Security Complex, the U.S. Department of Energy (DoE) plays a crucial role in the city's economy and culture. DoE veterans such as George Solomon contribute greatly as well.
In 1986, Solomon left his DoE position to launch his own company in the basement of his Oak Ridge home with a business partner.
“We purchased used government equipment from a closed DoE plant, which included machine tools, instrumentation, flanges, fittings, etc.,” explains Solomon, president of Vacuum Technology Inc. (VTI). “And, we began building these little gas bottles known as calibrated leaks—devices that emit tiny flow rates of gas. A calibrated leak calibrates a helium leak detector, used in industry to find leaks in products.”
VTI grew slowly but steadily and soon moved to a 4000-sq.-ft. facility as its product line expanded.
“The calibrated leaks led us into the leak-testing business,” reflects Solomon. “We also started to build the system that performed actual leak detection, utilizing our calibrated leak product line. To do this, we slowly added machine capability—milling machines, turning centers, waterjet cutters, etc.”
By 2020, VTI had evolved to occupy a new 100,000-sq.-ft. facility with 70 employees, and now is recognized as a world-leading provider of calibrated leaks, vacuum hardware and custom vacuum systems and services. It services HVAC, automotive-component, U.S. government, battery, medical and other customers.
DEMAND DEMANDS LASER ADDITION
To meet the growing demand for precision laser cutting and complement its two waterjet cutting machines, late in 2019 VTI purchased a Platino 2.0 6-kW fiber laser cutting machine from Prima Power.
“When beginning our search for a laser cutting machine, we contacted all of the major manufacturers to see what they had to offer,” says Tony Salyers, VTI design engineering manager. “We tend to go after the latest technology that we can afford in a category to give us the most flexibility.”
The machine stayed in storage for nearly a year during completion of the new building but has proved beneficial upon startup. Benefits recognized by the VTI team include:
• Efficiency, which provides energy and maintenance savings
• Productivity, particularly on thin- and medium-gauge sheets
• Flexibility, making it suitable for work on a wide range of materials
• Reliability and capability to meet a variety of production needs through a diverse selection of automation modules
• Simplicity, making it simple to install, use and maintain.
The Platino fiber laser machine provides for material flexibility, including cutting of highly reflective materials such as aluminum alloy, copper and brass, and efficiently cuts in various thicknesses, including to 20 mm on mild steel.
Salyers offers additional reasons for the machine’s selection by VTI.
“The granite-based frame makes the Platino rigid and resistant to temperature change,” he says, while also complimenting the machine’s user-friendly and intuitive software. “Another reason for its selection: Our Platino can accommodate a 5 by 10-ft. sheet size. Sometimes we must cut larger sheets, and the machine’s cantilevered gantry system allows us to open the cabinet to load overhead with a crane if the sheet won’t fit. Cabinet access also provides room for cleaning and maintenance.”
SPEED, FITUP PUMP UP PRODUCTIVITY
VTI realized productivity improvements early on resulting from its new fiber laser cutting machine.
“When we placed it into operation, we realized that it was going to take a huge percentage of the work off of our waterjet cutting machines,” says Solomon. “When cutting material 1⁄2 in. thick or less, the Platino sped manufacturing by a factor of 10. With the new building and the new laser, we realized that we could build our own storage shelving—we cut all of the shelves on the fiber laser cutting machine. And, some bars for the shelving required the cutting of 28 1⁄2-in.-dia. bolt holes. This takes 28 min. on a waterjet cutting machine, but only 57 sec. on the Platino. The laser speed provides a big benefit for us.”
VTI also employs the laser cutting machine in fabrication of NEMA 1 panels for controls.
“Instead of purchasing a prefabricated box,” Solomon explains, “we can design the panel, place all of the penetrations in it for the instruments that stick through the panel, then cut this area out, and bend, weld and paint it. The instrumentation just drops right in, which makes final assembly much easier. Instead of struggling to cut the holes in a prefabricated box, we just manufacture it all from scratch.”
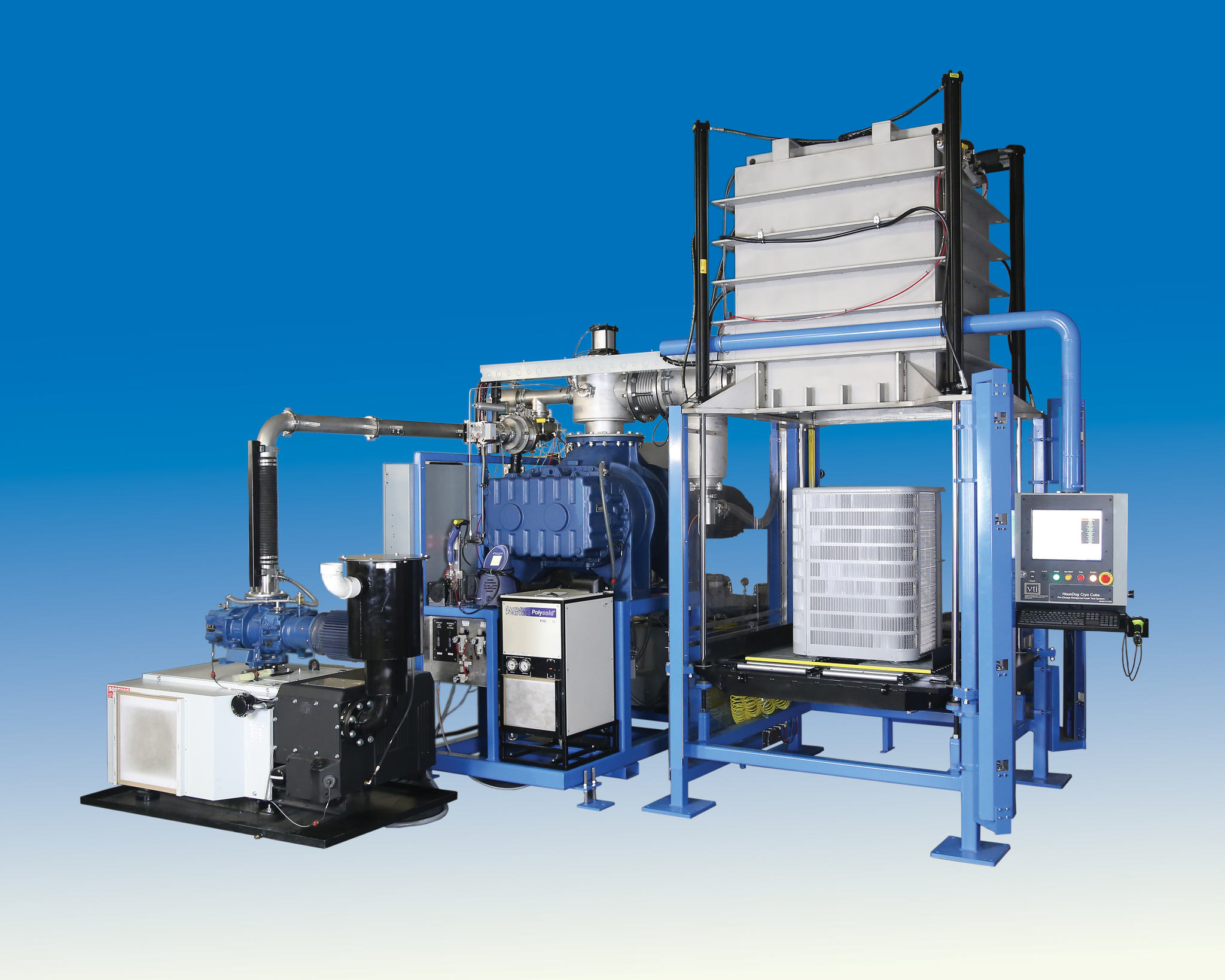
The Platino also proves its mettle on 14- and 16-gauge carbon steel, which represents the bulk of material processed at VTI.
“When cutting material on a waterjet machine,” Salyers says, “we have the rust factor to contend with if it sits too long. And, regardless of the material thickness, the waterjet cutting machine will leave burrs. With the volume we now have with boxes, flanges and small sheet metal brackets, we spend a great amount of time deburring these parts off of the waterjet. The Platino dramatically decreases cutting time, increases accuracy and eliminates the need for deburring."
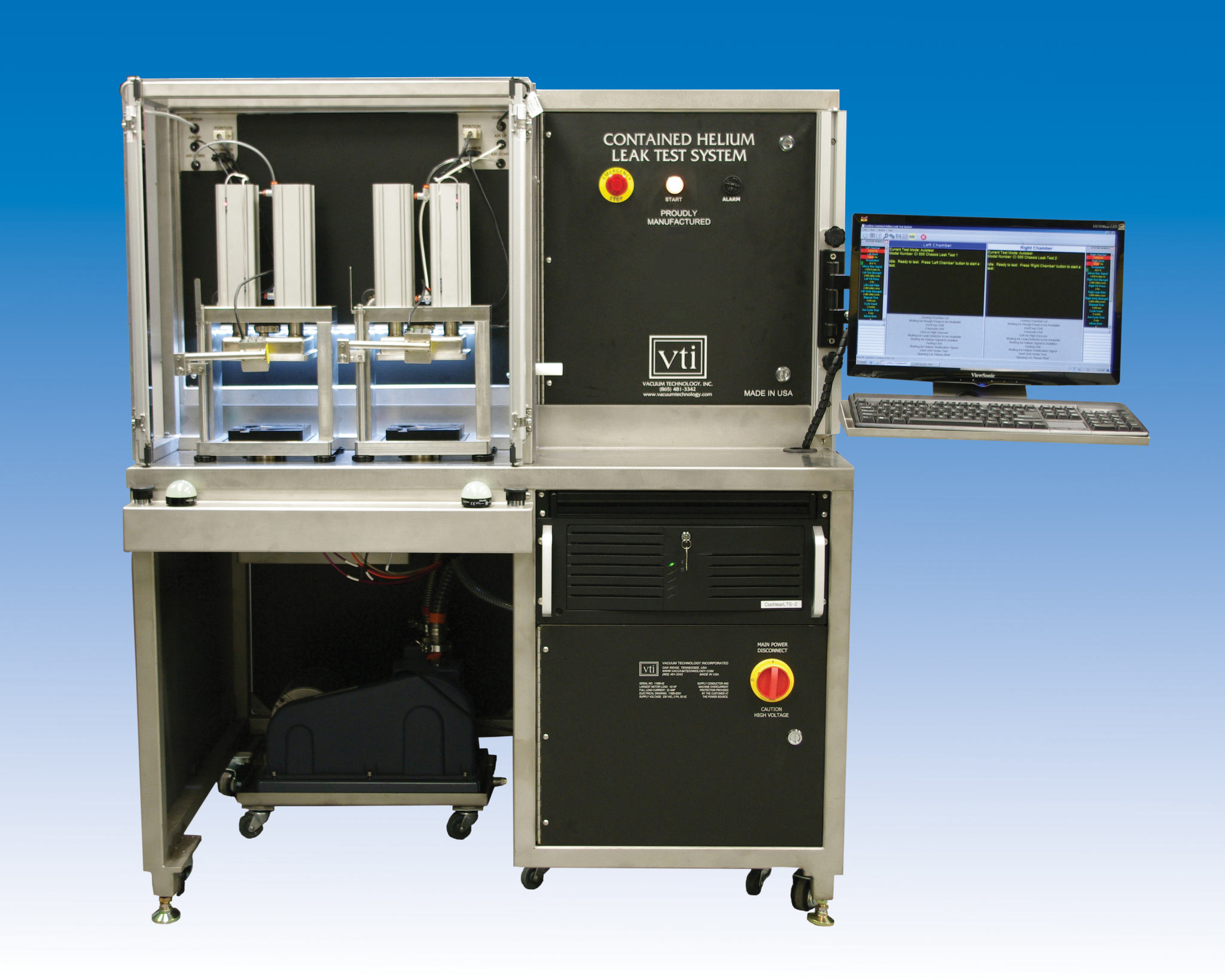
“We also have custom applications that don’t necessarily bring high productivity improvements,” Salyers continues. “However, when we can save 2 or 3 hr. consistently on an application with the laser cutting machine, it adds up to substantial production savings.”
Concludes Solomon: “Any new machine results in a learning curve. You’re going to have issues and most of them are self-induced. But we haven’t had many issues with the Platino. And, Prima Power has been very responsive with any problems. Bringing in this fiber laser cutting machine has been a good experience.”
The Platino dramatically decreases cut time, increases accuracy, and eliminates deburring of the parts.