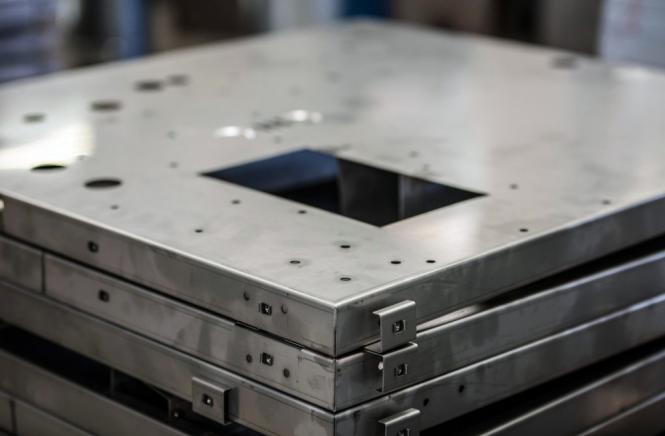
Pořádek a efektivita jsou hnací silou produktivity od prvního řezu až po hotový výrobek
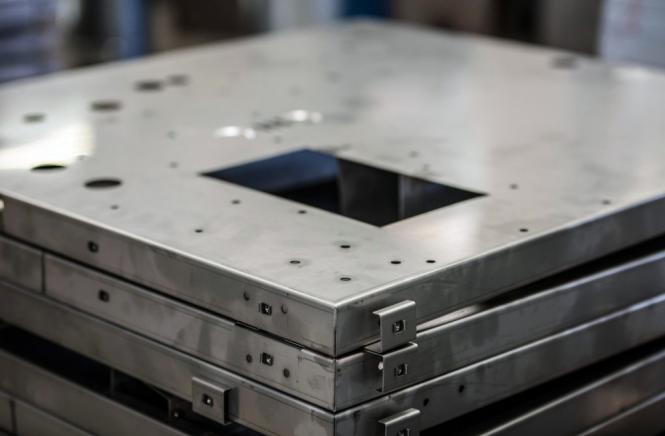
Společnost Astra byla založena před necelými třiceti lety jako výsledek inovativního instinktu, který se během několika málo let osvědčil: nerezová ocel se stala technologickým materiálem budoucnosti.
Dnes je zpracovávána a tvarována produktivním a efektivním systémem, v němž se o každou z provozních fází od řezání laserem, děrování, ohýbání, obkládání až po automatické skladování (srdce procesu) stará společnost Prima Power.
Společnost Astra se specializuje na navrhování a výrobu zařízení pro stravovací služby, přičemž vyrábí především nerezové komponenty od polotovarů až po hotové výrobky. Společnost byla založena v roce 1991 a vždy se snažila splňovat nejvyšší požadované úrovně kvality a zároveň následovat prozíravost zakladatele Rudyho Peruzzetta, který rozpoznal, že nerezová ocel se stane technologickým materiálem budoucnosti. Na základě toho byly okamžitě zaměřeny zdroje a dovednosti na náročná odvětví, jako je nemocniční a farmaceutický průmysl, a v roce 1997 byla poprvé rozšířena výroba. Ve stejném roce byla navázána spolupráce s velkou nadnárodní skupinou Electrolux Professional, světovým lídrem v oblasti domácích spotřebičů a vybavení pro profesionální použití, pro kterou se Astra rovněž stala certifikovaným dodavatelem. A právě profesionálnímu sektoru nadále slouží prostřednictvím výroby a dodávek modulárních polotovarů a hotových výrobků používaných ve velkých profesionálních zařízeních nebo řešení pro mytí, vaření a chlazení. Jedná se o efektivní spolupráci, při které spokojenost zákazníků přesahuje vynikající poměr kvality a ceny a pro kterou je společnost uznávána a respektována i v oblasti externích staveb.
„Významné provozní výsledky, kterých jsme dosáhli," říká majitel Rudy Peruzzetto, "nám umožnily dále rozšířit naši výrobní kapacitu na celkových 6 000 metrů čtverečních vnitřních prostor a stejně tolik venkovních prostor rozdělených mezi 3 závody v San Polo di Piave v provincii Treviso.“
Expanze společnosti vždy doprovázela její přirozenou tendenci k inovacím, kterou postupem času podpořil silný ideál udržitelného rozvoje (například nový sklad je napájen z obnovitelných zdrojů energie prostřednictvím speciálního fotovoltaického systému). Zvláštní péče o životní prostředí se projevuje také postupnou obměnou celého strojového parku za stále funkčnější a ekologičtější modely. Právě tento vozový park dnes zajišťuje vysoce výkonný a efektivní výrobní proces, v němž všechny technologie, od laserového řezání přes děrování, ohýbání až po automatický skladovací systém, dodává společnost Prima Power, strojní divize skupiny Prima Industrie. Mezi nejnovější přírůstky v chronologickém pořadí patří nové ohýbací centrum BCe 2720 a automatický skladovací systém Night Train FMS doplněný o nakládacího/vykládacího robota LU6 pro podporu laserového řezání (tyto systémy byly instalovány na začátku roku 2020).
Od malých sérií až po velkovýrobu
Dnes společnost Astra pracuje zejména pro zdravotnický/farmaceutický sektor, ale i pro velká zařízení a námořní sektor. Labyrintový filtr pro průmyslové digestoře Sabik je autentickým výrobkem a zároveň etalonem vynalézavosti, jednoduchosti a efektivity (vymyslel a vytvořil jej sám Rudy Peruzzetto), který dokládá know-how a schopnost společnosti podpořit zákazníka při vytváření hotového výrobku, stejně jako nespočet dalších položek (válce na zvedání plechů a zvedáky zásobníků, servisní vozíky atd.) z nerezové oceli, stejně jako z pozinkované oceli, hliníku nebo mědi.
„Přibližně 80 % toho, co zpracováváme, je nerezová ocel," upřesňuje Peruzzetto, „a běžně pracujeme s tloušťkami do 5-6 mm, i když naše zařízení nám umožňuje zpracovávat i tloušťky nad 10 mm, což pokrývá celý dodavatelský řetězec od polotovarů až po hotový výrobek. Jsme schopni spravovat 1, 10 nebo 100 kusů se stejnou flexibilitou jako tisíce kusů.“
V tomto ohledu došlo ve společnosti k prvnímu průlomu ve výrobě před více než deseti lety, kdy byl zakoupen první kombinovaný děrovací stroj SG8 1530 s pravoúhlými nůžkami od tehdejší společnosti Finn Power. Tato integrace více než ztrojnásobila množství plechů, které bylo možné do té doby zpracovávat. Další rozhodující krok byl učiněn zhruba před deseti lety zavedením vysoce výkonného laserového řezacího systému, vláknového laseru Prima Power 2D, stroje Platino o výkonu 3 kW doplněného o paletizační/stohovací robot LST pro automatické vybírání kusů a elektrického ohýbacího centra EP 1030. Jak již bylo zmíněno, poslední instalace ohýbacího centra BCe 2720 proběhla teprve před několika měsíci jako upgrade předchozího systému spolu s automatickým skladovým systémem Night Train FMS, který zahrnuje nakládací/vykládací robot LU6 pro podporu laserového řezání.
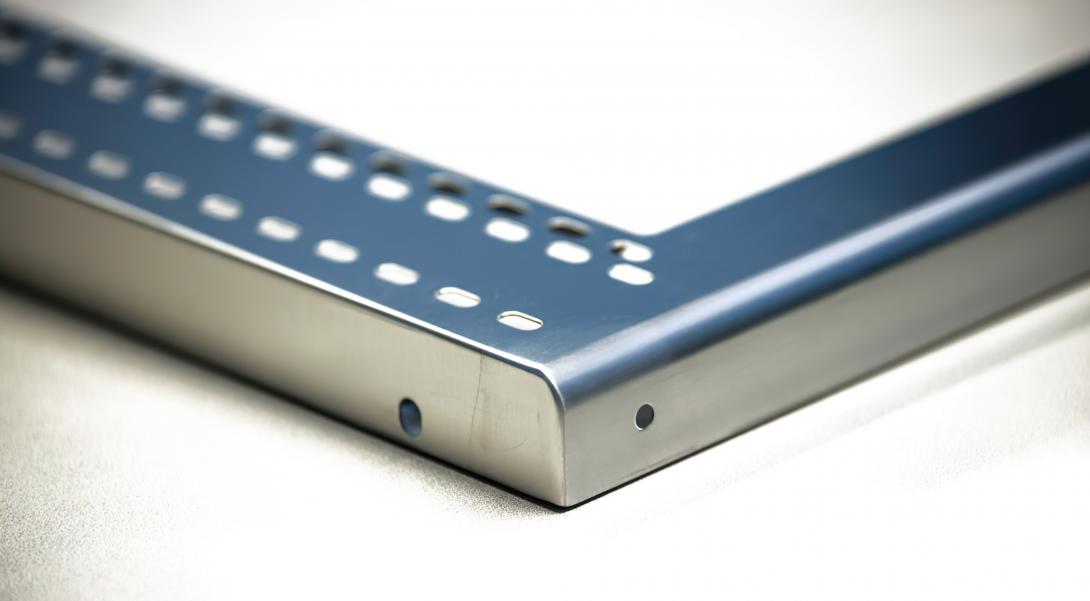
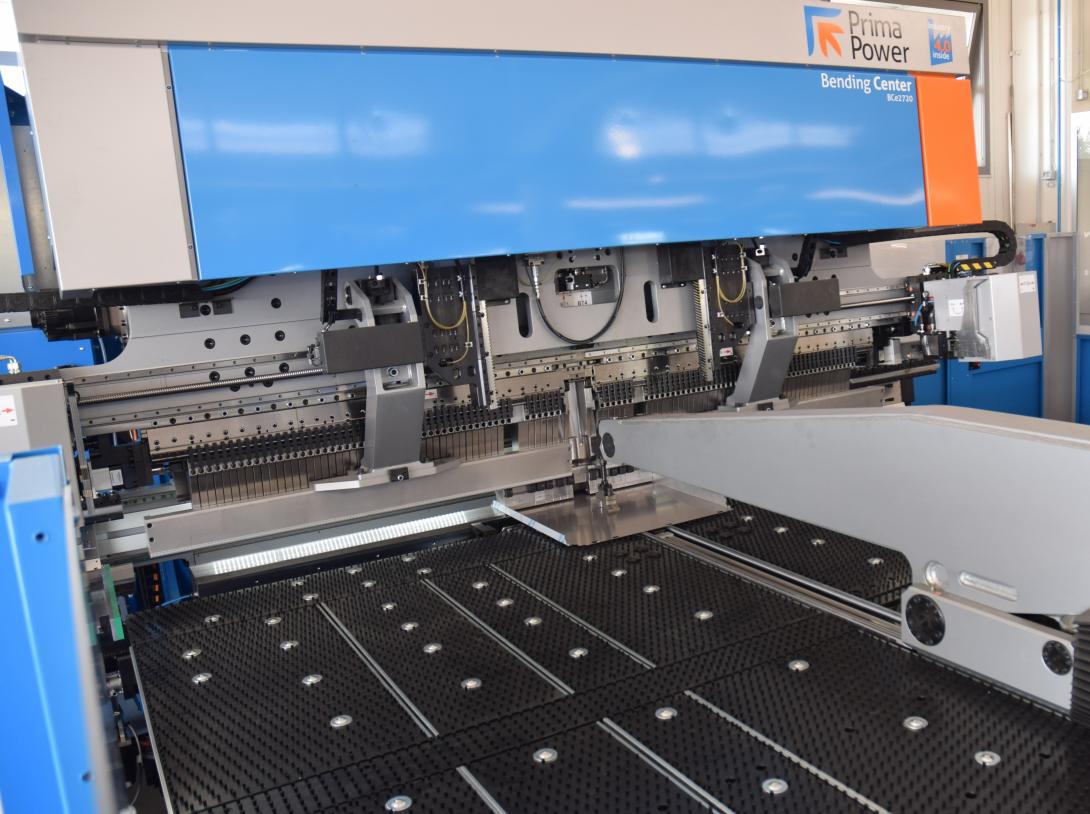
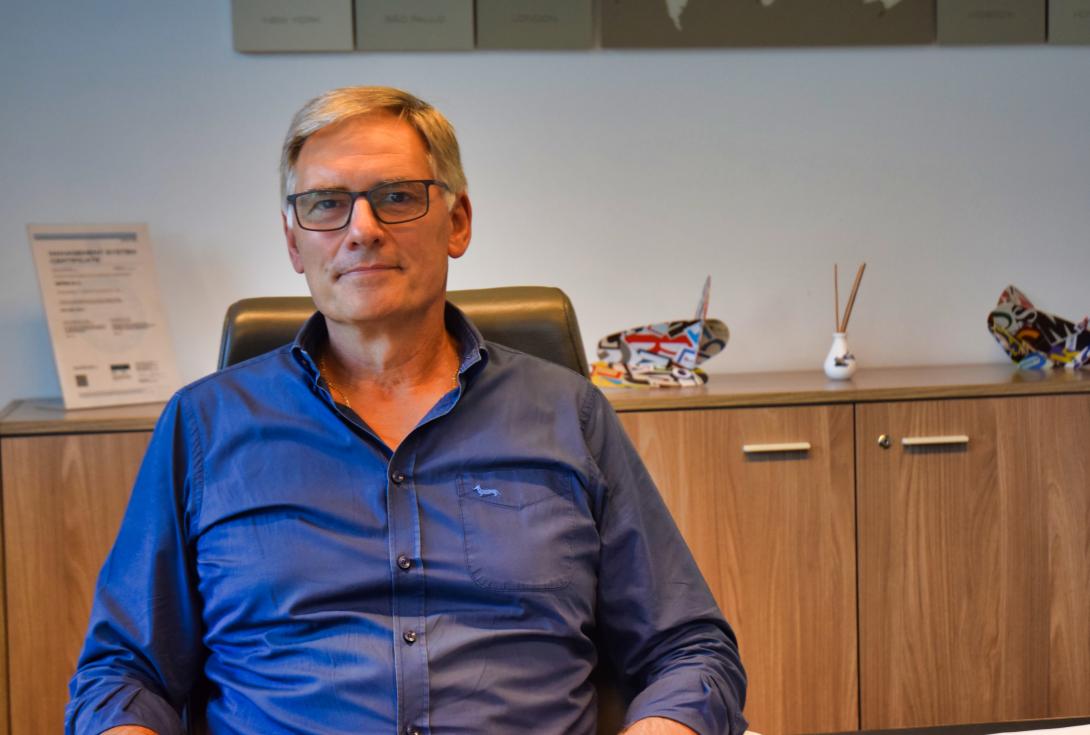
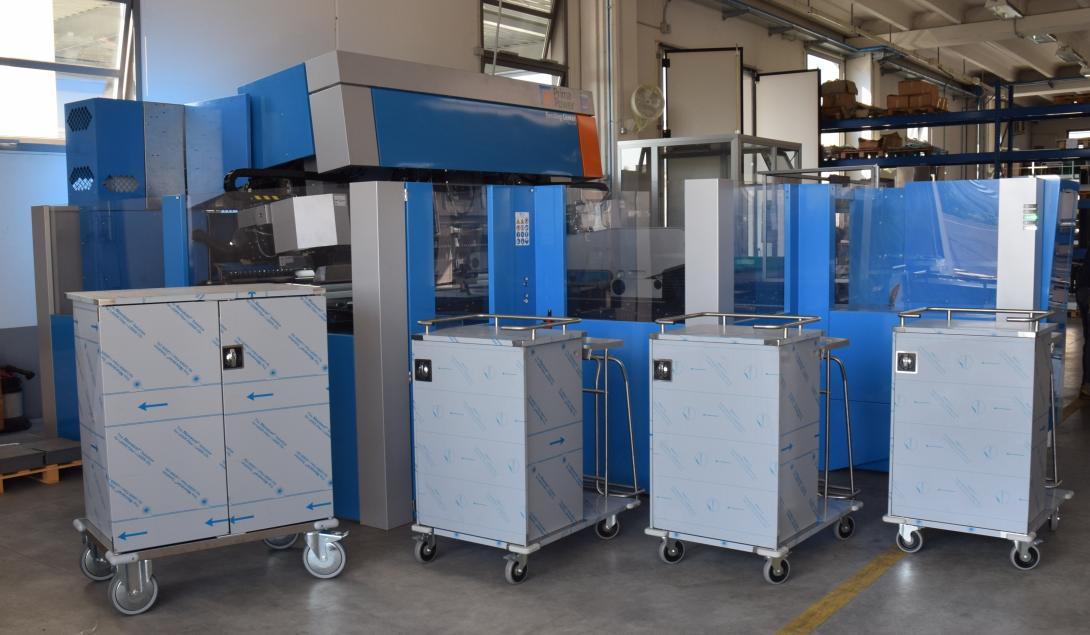
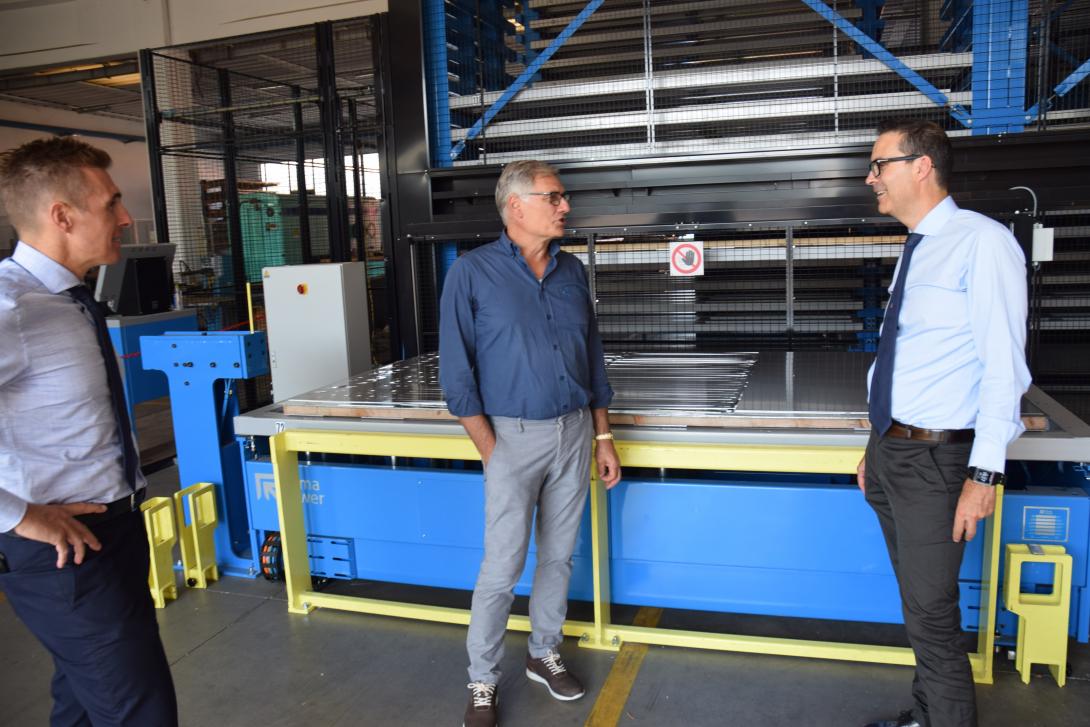
Vysoce flexibilní ohýbací centrum se stejnou produktivitou
Ohýbací centrum BCe společnosti Prima Power nabízí ideální řešení pro ty, kteří se stejně jako Astra zabývají jednotlivými kusy, malými sériemi nebo hromadnou výrobou. Cílem tohoto ohýbacího centra je totiž spojit známé výhody výrobku pro ohýbání panelů, tj. flexibilitu, přesnost a vysokou kvalitu, s poloautomatickým, ale vysoce produktivním procesem, kdy je stroj stále v provozu díky nakládacímu a vykládacímu stolu LUT, který umožňuje nakládání a vykládání kusů během provozu. Ruční podávání umožňuje také ohýbání kusů, které nelze snadno přepravovat pomocí automatických nakládacích systémů. Výroba plně perforovaných kusů, dlouhých nebo širokých tvarů nebo dokonce dílů s většími vnitřními otvory se tak stává zcela proveditelnou. Servoelektrický stroj BCe 2720, vybavený 8 nezávislými motory a několika CNC osami, umožňuje zpracovávat ocel o tloušťce 0,5 až 3,2 mm (nerezovou ocel až 2,2 mm a hliník až 4 mm). To také umožnilo společnosti zvýšit maximální délku ohybu předchozího systému z 2 250 mm na současných 2 750 mm a zvýšit úroveň automatizace procesu. Velmi ceněný je také systém AUT (Auxiliary Upper Tools). Jedná se o systém horních pomocných nástrojů, které pomáhají provádět konkrétní ohyby, což dále dokládá flexibilitu stroje.
„Naše rozhodnutí zvolit nové a výkonnější ohýbací centrum,“ Peruzzetto vysvětluje, „vychází z našeho vědomého přesvědčení a zkušeností z posledních deseti let, jak obtížné je najít speciálně kvalifikovaný personál, v tomto případě pro ohýbací centra. Tento nedostatek dovedností může občas ohrozit budoucí vizi společnosti nebo přinejmenším změnit její cestu růstu. Proto jsem se rozhodl zaměřit na jinou technologii ohýbání, kde základem produktivity je programování a automatizace. Na první pohled se ohýbací centrum snáze programuje, protože se jedná o obecně známější technologii, a díky jejím vlastnostem můžete zpracovávat i kusy, které by ohýbačka panelů neumožnila. Ale identifikace správného výrobku a naše konstrukční schopnost upravit některé kusy tak, aby je bylo možné zpracovat na tomto stroji, nám umožnily získat velké výhody, pokud jde o čas provedení, a také nástroje pro dosažení očekávané kvality.“
Toto technologické vybavení výrazně rozšířilo výrobní potenciál společnosti, která nyní může zpracovávat větší formáty.
Efektivita procesů (také) začíná od řízení surovin
Jak již bylo zdůrazněno, společnost Astra integrovala také nový automatický skladovací systém Night Train FMS, doplněný o nakládací/vykládací robot LU6 pro podporu laserového řezání, který opět dodala společnost Prima Power. Majitelé se rozhodli pro tuto investici, aby optimalizovali hospodaření s plechem, které již delší dobu přesahuje 100 000 kilogramů měsíčně, což odpovídá přibližně 200 paletám v nepřetržitém sortimentu a rotaci.
„Z hlediska efektivity je to příliš velká částka,“ říká Peruzzetto, „v porovnání se zdroji potřebnými pro vyhledávání a obstarávání surovin pro laserové řezání a s provozní dynamikou, na kterou musíme maximálně pružně reagovat.“
Nový automatický skladovací systém byl propojen s interním řídicím softwarem a sleduje všechny pohyby z pohledu Průmyslu 4.0. Jinými slovy, po naložení plechu se jeho dostupnost aktualizuje v reálném čase, přičemž se účinně odstraňují případné chyby a skutečná přítomnost se každou hodinu synchronizuje se softwarem pro správu. Je třeba mít na paměti, že rozsáhlé portfolio zákazníků společnosti s sebou přináší potřebu koordinovat množství různých formátů plechů, z nichž mnohé nejsou standardní a jsou spojeny s mnoha složitostmi.
„Efektivita a hodnota investice,“ poznamenává Peruzzetto, „se zanedlouho ukázala. Již během prvního měsíce po uvedení do provozu se výroba na laseru téměř zdvojnásobila a zároveň se minimalizovaly prostoje způsobené nakládáním s materiálem. Potřeba vytvořit pořádek a udržet materiál pod kontrolou s sebou tedy přinesla další nepřímé výhody. V neposlední řadě jsme také ušetřili podlahovou plochu, kterou předtím zabíraly různé palety plechů, které byly buď na cestě, nebo čekaly na zpracování.“
Díky nakládacímu/vykládacímu robotu a stohovacímu systému lze do nového systému Prima Power FMS dodávat také předem nařezané polotovary, které lze podle potřeby později zpracovat.
„Vylepšen byl také proces rozmístění dílů na materiál,“ dodává Peruzzetto, „protože nová metodika umožňuje zahrnout do stejné dávky kusy určené k řezání, které nejsou pro zakázku striktně relevantní, ale mohou být dočasně ‚uloženy‘ v kazetě (v jakémkoli voze, který je k dispozici), což dále optimalizuje efektivitu. Stručně řečeno, automatizované úložiště se stalo tepajícím srdcem našeho interního pracovního postupu. Tato technologie umožňuje spoléhat se na nepřetržité bezobslužnou výrobu.“
Pracujte lépe, abyste vyprodukovali více
Strojový park společnosti Astra (který kromě strojů Prima Power zahrnuje i další ohraňovací lisy, svařovací a čisticí buňky a zpevňování povrchu) umožňuje vymezit a pečlivě sledovat celý výrobní proces. Dokonalost výroby vzniká právě díky úzké spolupráci mezi profesionalitou kvalifikovaného personálu a špičkovou technologií, která umožňuje zkrácení výrobních časů a zlepšení provozních výsledků, které lze v případě potřeby zdokonalit.
„V tomto uspořádání,“ uzavírá Peruzzetto, „přinesly nejnovější přírůstky zvýšení produktivity a efektivity při zachování počtu pracovníků. Díky novému systému Night Train FMS můžeme nyní plánovat bezobslužnou výrobu na 3 směny a zároveň třídit kusy, které jsou na konci směny již naskládané a připravené k dalšímu zpracování. Mým cílem je usilovat o automatizaci všude, kde je to možné, aby se zaměstnancům lépe pracovalo a zároveň se zvýšila naše výrobní kapacita.“
Snahu o vyšší efektivitu a konkurenceschopnost potvrzují i nové projekty, které jsou ve vývoji a které v budoucnu připojí k automatickému skladování další systémy.
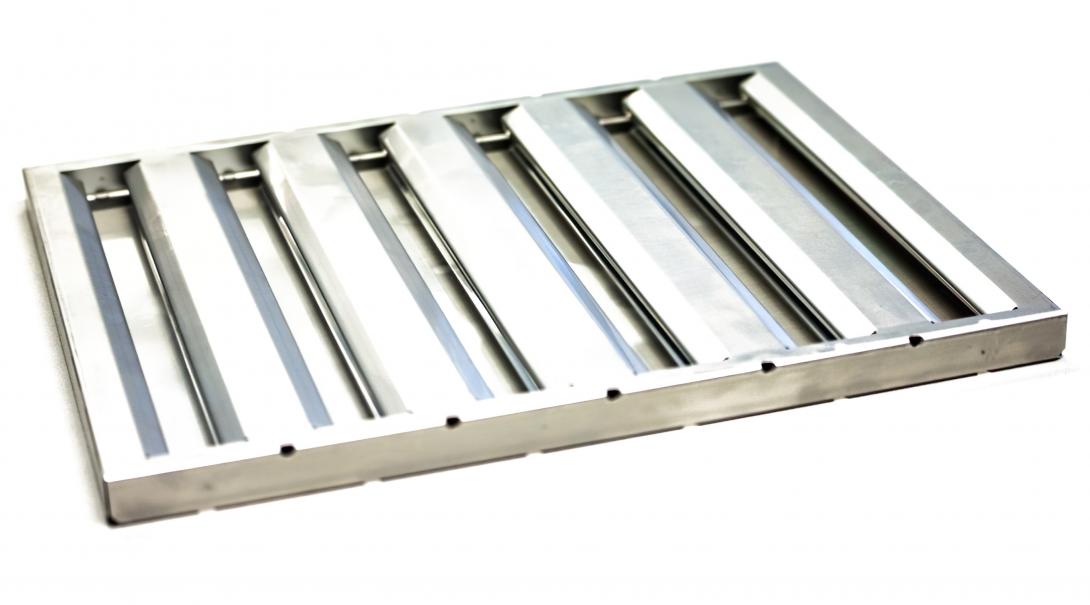
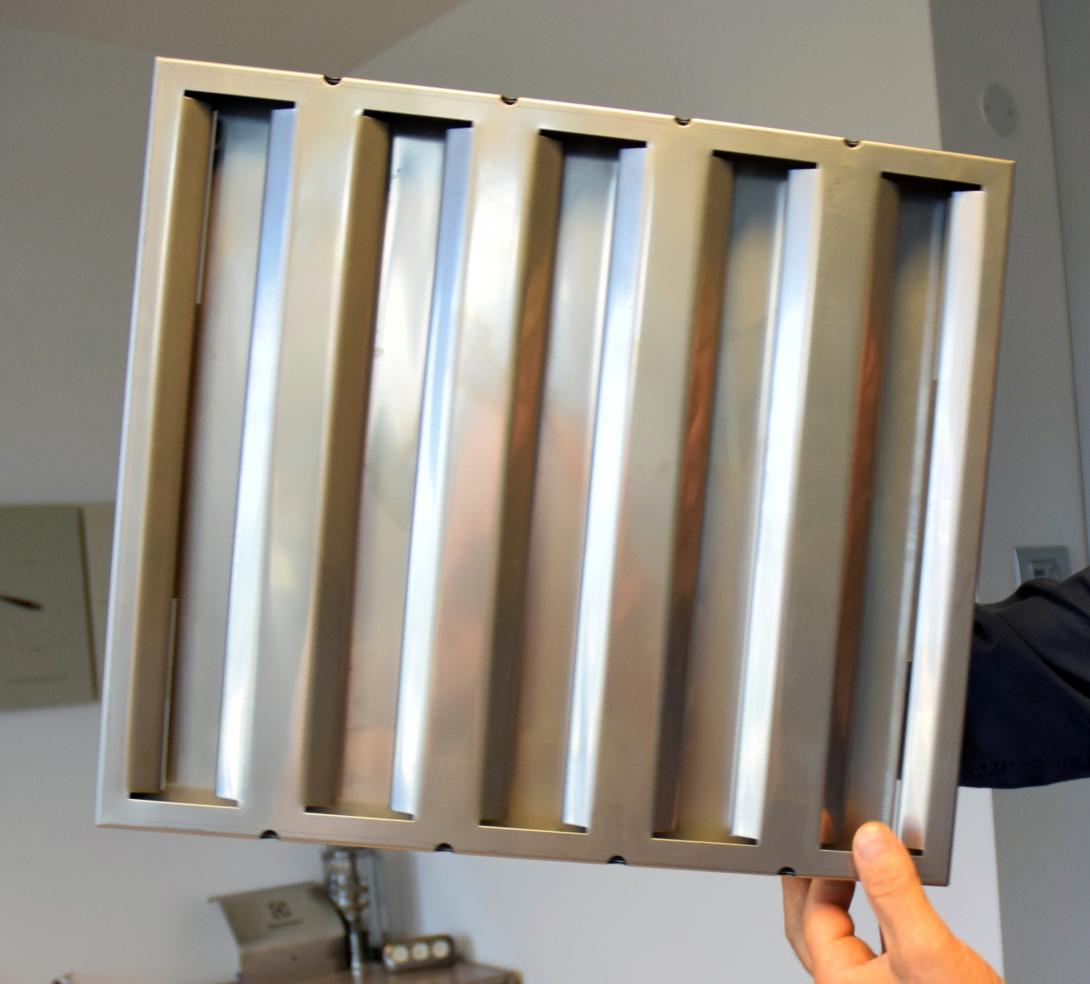
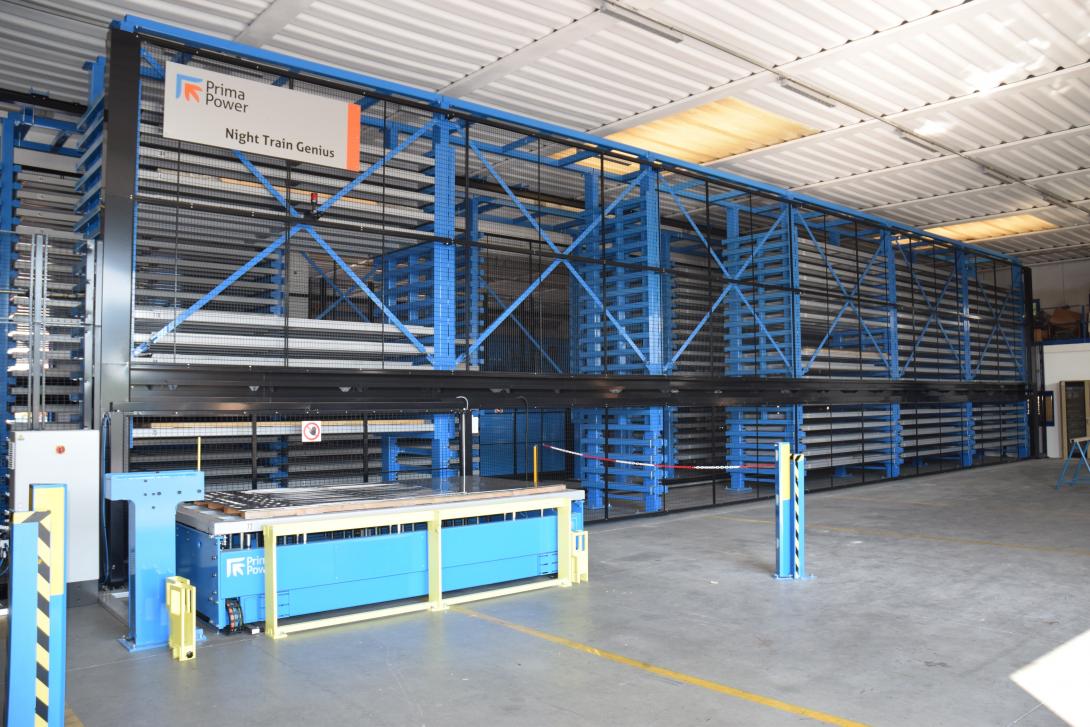
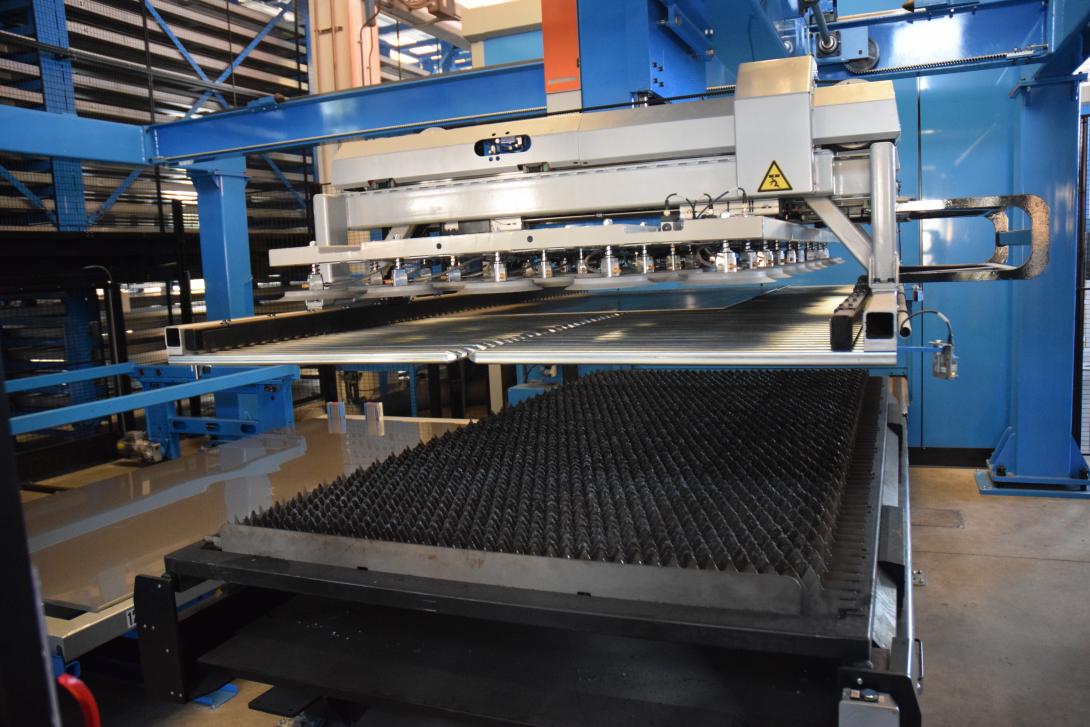
Filtry do odsavačů pro ty, kteří mají vysoké nároky
Průmyslové filtry do odsavačů par Sabik jsou exkluzivně navrženy a vytvořeny z čisté nerezové oceli 304 2B 6/10 společností Astra. Vyznačují se jemnějšími detaily, které umožňují odvádět, kondenzovat a vypouštět výpary nejvhodnějším způsobem, zatímco podstatnější prvky, jako je tuk, jsou zachycovány. Konstrukce filtru byla speciálně navržena tak, aby se díky použití jednoduchých fyzikálních principů minimalizovalo použití jednotky pro zachytávání prachu. Systém širších misek, vnitřní úhel 141°/90° a konstrukce umožňují snížit sací výkon a zároveň zvýšit množství nasátých metrů krychlových za hodinu. Tímto způsobem se výrazně snižují náklady na správu. Tento pokročilý a přitom velmi jednoduchý systém také usnadňuje čištění a údržbu a zajišťuje delší životnost a stálý vysoký výkon. Přesnost a estetika jsou zaručeny kvalitou procesu, v němž jsou použity technologie Prima Power, spolu s obvyklou metodikou práce zaměstnanců společnosti Astra: tato synergie činí z výrobku jedinečný produkt.
Sabik je filtr do odsávače navržený a vyráběný výhradně společností Astra z čisté nerezové oceli 304 2B 6/10.
Automatizace spolu s flexibilní výrobou a naopak
Systém Night Train FMS společnosti Prima Power automatizuje správu materiálů a souvisejících informací a spojuje jednotlivé výrobní procesy do jedné flexibilní linky. Způsob, jakým je systém navržen a strukturován, umožňuje větší nákladovou efektivitu a flexibilitu při výrobě dílů a je dokonale vhodný pro malosériovou i sériovou výrobu. Modulární systém umožňuje sestavit a strukturovat projekt podle specifických požadavků systému, ve kterém je instalován. V případě benátské společnosti byla zvolena konfigurace, která (prozatím) podporuje laserový řezací systém s vlákny, a to 12 modulárních skladovacích jednotek o výšce necelých 6 m s maximálním počtem 24 kazet (což umožňuje uložit do každé kazety 3 tuny materiálu nebo naskládaných komponent). To dává teoretický počet 288 kazet oproti 150, které se používají v současnosti. Hlavní předností systému je schopnost přizpůsobit se v průběhu času měnícím se výrobním potřebám: buňky, jednotlivé stroje, pracovní stanice lze aktualizovat, měnit nebo přidávat a dále rozšiřovat úložnou kapacitu.
Systém Night Train FMS společnosti Prima Power umožnil společnosti Astra strukturovat správu surovin, uvolnit podlahovou plochu a celkově zefektivnit proces laserového řezání a výrobní linku.
Efektivita a hodnota investice,“ poznamenává Peruzzetto, „se projevila zanedlouho. Již během prvního měsíce po uvedení do provozu se produkce laseru téměř zdvojnásobila. V neposlední řadě jsme také ušetřili podlahovou plochu.
Hledáte pro svou společnost podobné řešení? Najdete ho zde
Ohýbací centrum BCe
OHÝBACÍ CENTRA
Flexibilita ve vašich službách. Poloautomatické ohýbací centrum kombinující flexibilitu a produktivitu
Platino Fiber
CORTE A LASER 2D
Rentável para uma mistura de produção que inclui todos os materiais e espessuras
Night Train FMS®
FLEXIBILNÍ VÝROBNÍ SYSTÉMY