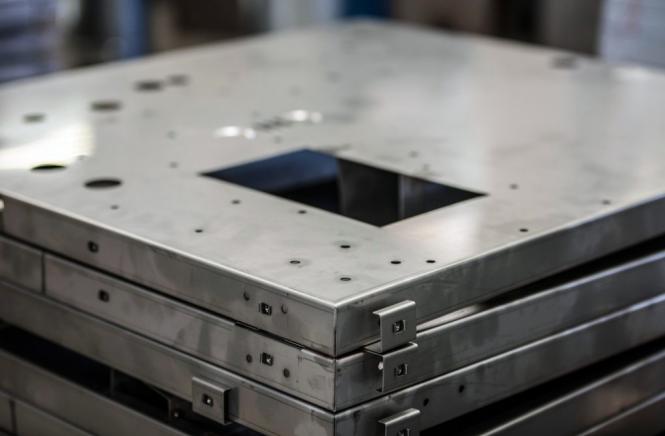
L'ordre et l'efficacité sont les moteurs de la productivité, de la première coupe au produit fini
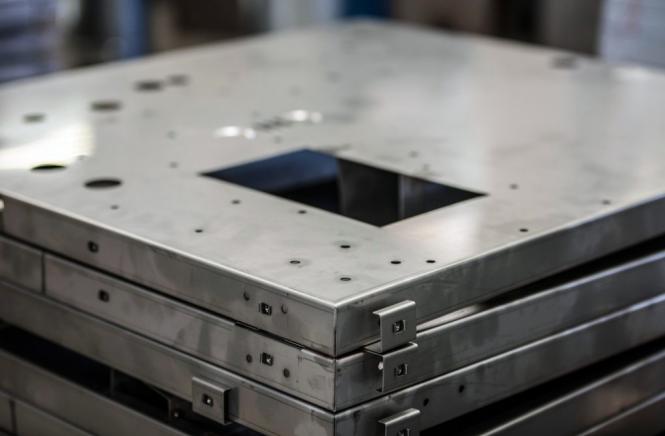
Astra a été fondée il y a un peu moins de trente ans, à la suite d'une intuition novatrice qui s'est avérée payante en quelques années : l'acier inoxydable allait devenir le matériau technologique de l'avenir.
Aujourd'hui, il est transformé et façonné par un système productif et efficace dans lequel chacune des phases opérationnelles, de la découpe laser, du poinçonnage, du pliage, du panneautage, jusqu'à son stockage automatique (le cœur du processus) sont prises en charge par Prima Power
Astra est spécialisée dans la conception et la transformation de la charpente métallique, produisant principalement des composants en acier inoxydable allant du semi-fini au produit fini. Créée en 1991, l'entreprise a toujours eu pour objectif de répondre aux plus hauts niveaux de qualité requis tout en suivant la vision du fondateur Rudy Peruzzetto, qui avait identifié que l'acier inoxydable deviendrait le matériau technologique de l'avenir. Sur cette base, les ressources et les compétences ont été immédiatement orientées vers des secteurs exigeants tels que l'industrie hospitalière et pharmaceutique, et en 1997, la production a été étendue pour la première fois. La même année, un partenariat a également débuté avec un grand groupe multinational, Electrolux Professional, leader mondial de l'électroménager et des équipements à usage professionnel, pour lequel Astra est également devenu un fournisseur agréé. Et c'est précisément le secteur professionnel qu'elle continue de servir à travers la production et la fourniture de produits modulaires, semi-finis et finis utilisés dans les grandes installations professionnelles, ou de solutions de lavage, de cuisson et de réfrigération. Il s'agit d'une collaboration efficace dans laquelle la satisfaction du client va au-delà de l'excellent rapport qualité/prix et pour laquelle l'entreprise est reconnue et respectée, même dans le domaine de la construction par des tiers.
« Les résultats opérationnels significatifs que nous avons obtenus », déclare le propriétaire Rudy Peruzzetto, « nous ont permis d'accroître encore notre capacité de production pour atteindre un total qui s'élève aujourd'hui à 6 000 mètres carrés intérieurs et autant d'espace extérieur répartis entre 3 usines à San Polo di Piave, dans la province de Trévise. »
L'expansion de l'entreprise a toujours été parallèle à sa tendance inhérente à l'innovation, soutenue au fil du temps par un fort idéal de développement durable (par exemple, le nouvel entrepôt est alimenté par des sources d'énergie renouvelables via un système photovoltaïque dédié). L'attention particulière portée à l'environnement se traduit également par le remplacement progressif de l'ensemble du parc de machines par des modèles de plus en plus fonctionnels et écologiques. Cette même flotte assure aujourd'hui un processus de production performant et efficace dans lequel toutes les technologies, de la découpe laser au poinçonnage, au pliage, au panneautage, jusqu'au système de stockage automatique, sont toutes fournies par Prima Power, la division Machines du groupe Prima Industrie. Parmi ceux-ci, les derniers ajouts par ordre chronologique ont été le nouveau centre de pliage BCe 2720 et le système de stockage automatique Night Train FMS complet avec robot de chargement/déchargement LU6 pour soutenir la découpe laser (ces systèmes ont été installés au début de 2020).
Des petits lots à la production de masse
Aujourd'hui, Astra travaille notamment pour le secteur hospitalier/pharmaceutique, ainsi que pour les grandes installations et le secteur naval. Le filtre labyrinthe pour hottes industrielles Sabik est un produit propre, mais aussi une référence en matière d'ingéniosité, de simplicité et d'efficacité (imaginé et réalisé par Rudy Peruzzetto lui-même), qui démontre le savoir-faire et la capacité de l'entreprise à soutenir le client dans la réalisation d'un produit fini, comme d'innombrables autres articles (vérins de levage de plaques et de plateaux, chariots de service, etc.) en acier inoxydable, mais aussi en acier galvanisé, en aluminium ou en cuivre.
« Environ 80 % de ce que nous traitons est de l'acier inoxydable, » précise Peruzzetto, « et nous travaillons normalement avec des épaisseurs allant jusqu'à 5-6 mm, bien que nos équipements nous permettent de traiter même plus de 10 mm, ce qui couvre toute la chaîne d'approvisionnement, des produits semi-finis au produit fini. Nous sommes capables de gérer 1, 10 ou 100 pièces avec la même flexibilité que des milliers de pièces. »
À cet égard, la première percée en matière de production a eu lieu dans l'entreprise il y a plus de dix ans, avec l'achat de la première poinçonneuse combinée, une SG8 1530 avec cisaille à angle, à la société Finn Power de l'époque. Cette intégration a plus que triplé la quantité de tôle qui pouvait être traitée jusqu'alors. Une nouvelle étape décisive a été franchie il y a une dizaine d'années avec l'introduction d'un système de découpe laser à haute performance, un laser à fibre Prima Power 2D, une Platino de 3 kW équipée d'un robot de palettisation/empilage LST pour la sélection automatique des pièces, et une plieuse de panneaux électrique EP 1030. Comme nous l'avons déjà mentionné, l'installation la plus récente de la plieuse de panneaux BCe 2720 a eu lieu il y a quelques mois seulement, en tant que mise à niveau du système précédent, en même temps que le système de stockage automatique Night Train FMS qui comprend un robot de chargement/déchargement LU6 pour la découpe laser.
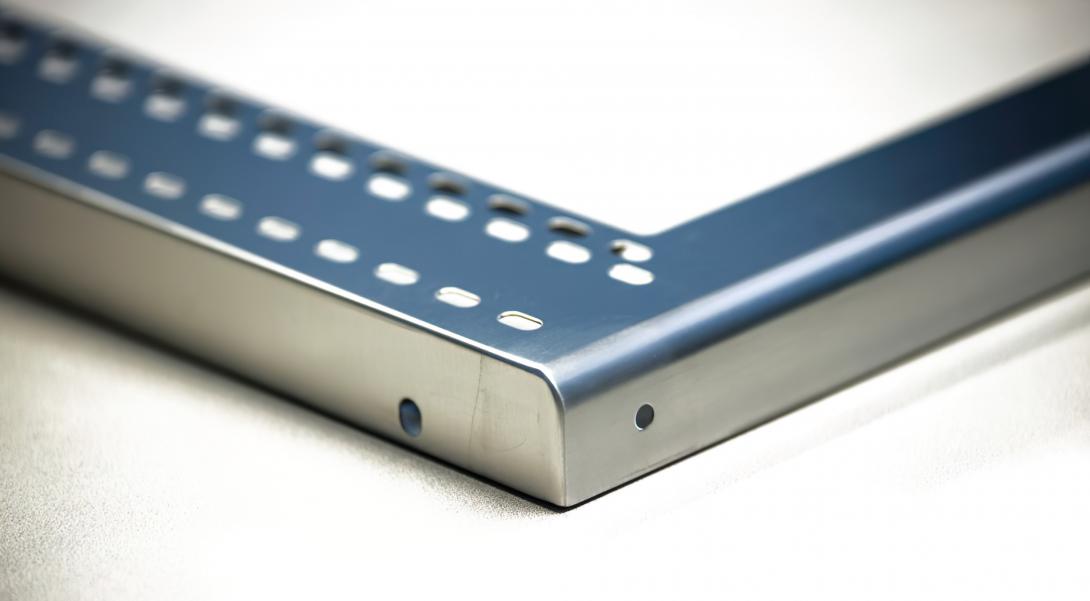
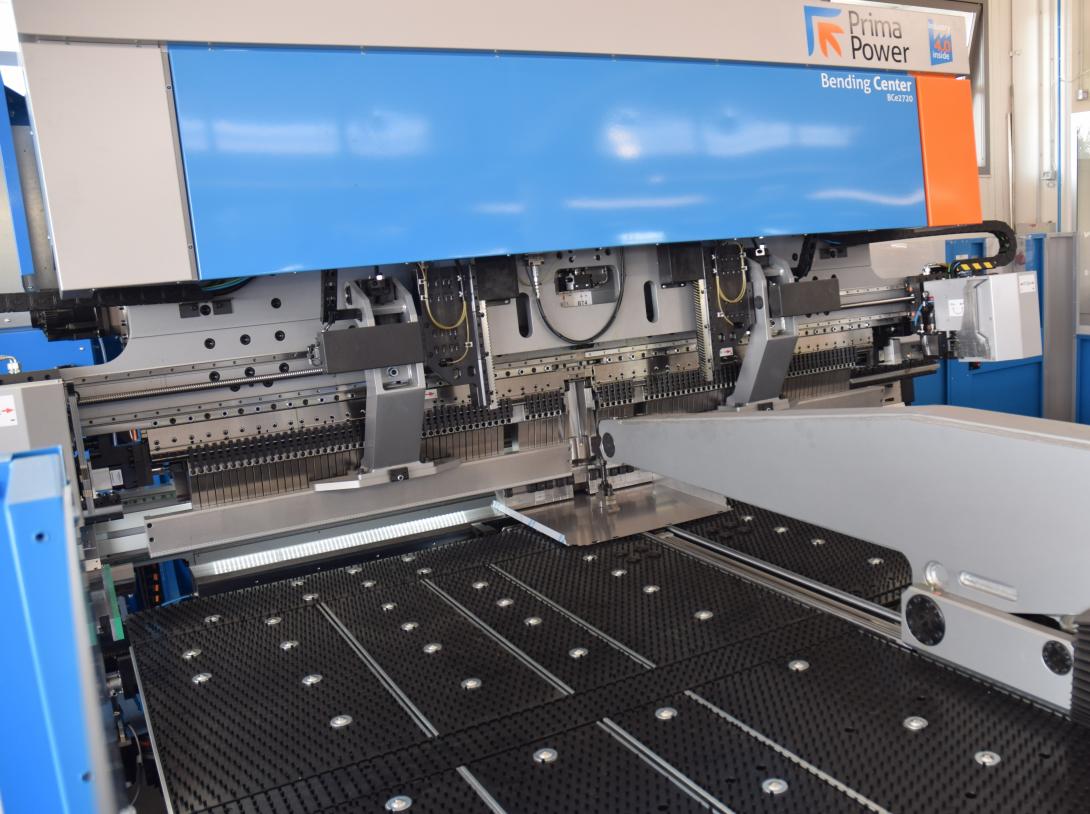
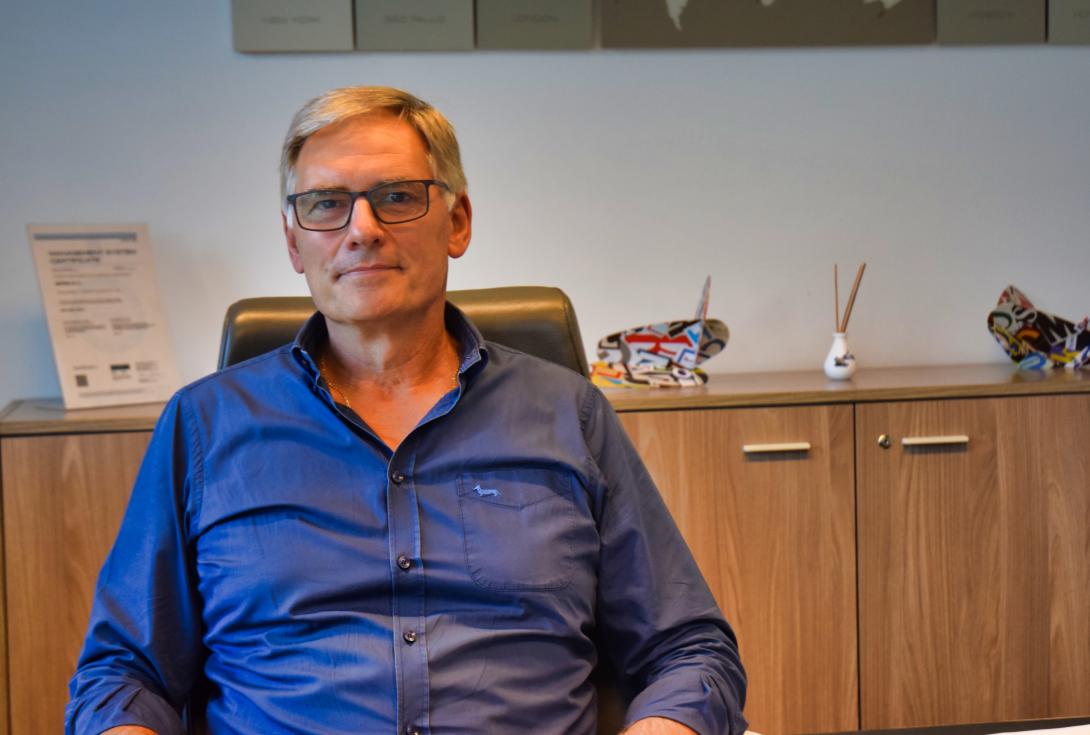
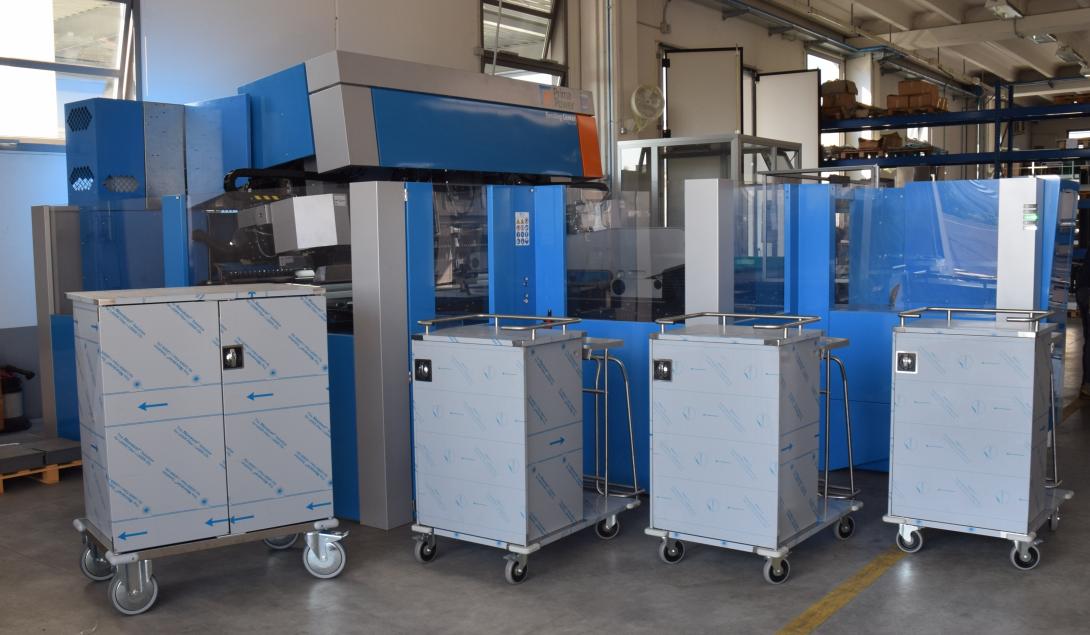
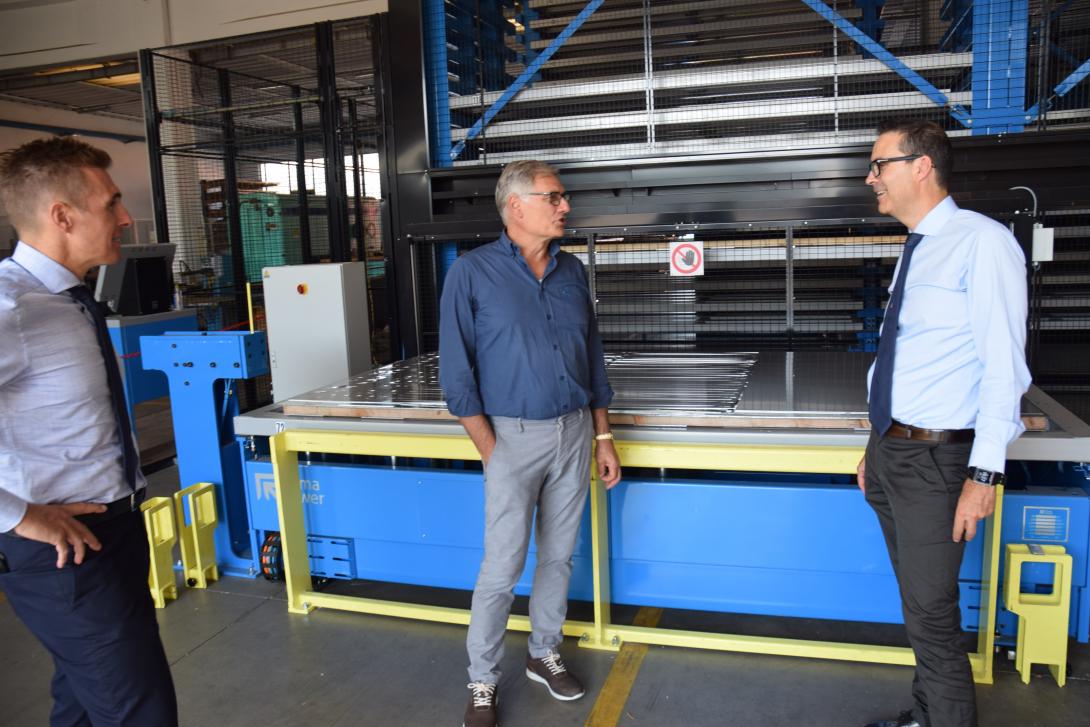
Centre de pliage très flexible avec la même productivité
Le centre de pliage BCe de Prima Power offre la solution idéale pour ceux qui, comme Astra, traitent des pièces uniques, des petits lots ou des productions de masse. En effet, cette plieuse de panneaux vise à combiner les avantages bien connus du produit lambris, à savoir la flexibilité, la précision et la haute qualité, avec un processus semi-automatique mais hautement productif où la machine est toujours en marche grâce à la table de chargement et de déchargement LUT qui permet le chargement et le déchargement des pièces pendant le fonctionnement. L'alimentation manuelle permet également de plier des pièces qui ne sont pas facilement transportables par des systèmes de chargement automatique. La production de pièces entièrement perforées, de formes longues ou larges, ou même de pièces présentant des ouvertures intérieures plus grandes devient ainsi tout à fait réalisable. Servoélectrique et équipée de 8 moteurs indépendants et de plusieurs axes CNC, la BCe 2720 vous permet de traiter des épaisseurs de 0,5 à 3,2 mm d'acier (jusqu'à 2,2 mm d'acier inoxydable et jusqu'à 4 mm d'aluminium). Cela a également permis à l'entreprise d'augmenter la longueur de pliage maximale du système précédent, qui est passée de 2 250 mm à 2 750 mm, ainsi que d'accroître le niveau d'automatisation du processus. Le système AUT (Auxiliary Upper Tools) est également très apprécié. Il s'agit d'un système d'outils auxiliaires supérieurs qui aident à réaliser des courbes particulières, démontrant ainsi la flexibilité de la machine.
« Notre décision d'opter pour une nouvelle plieuse de panneaux plus performante », explique M. Peruzzetto, « est fondée sur notre conviction consciente et sur l'expérience acquise au cours de la dernière décennie quant à la difficulté de trouver du personnel spécialement qualifié, dans ce cas pour les plieuses de panneaux. Cette pénurie de compétences peut parfois mettre en péril la vision future de l'entreprise ou, du moins, modifier sa trajectoire de croissance. J'ai donc choisi de me concentrer sur une technologie de pliage différente, où la programmation et l'automatisation sont la base de la productivité. À première vue, la plieuse est certainement plus facile à programmer car il s'agit d'une technologie plus connue et, grâce à ses caractéristiques, vous pouvez même traiter des pièces qui ne seraient pas possibles avec une plieuse de panneaux. Mais l'identification du bon produit et notre capacité de conception pour ajuster certaines pièces afin de rendre leur traitement possible sur cette machine nous ont permis d'obtenir de grands avantages en termes de temps d'exécution, ainsi que d'outillage pour atteindre la qualité attendue. »
Cet équipement technologique a considérablement élargi le potentiel de production de l'entreprise, qui peut désormais traiter des formats plus importants.
L'efficacité des processus (également) commence par la gestion des matières premières
Comme nous l'avons déjà souligné, Astra a également intégré le nouveau système de stockage automatique Night Train FMS, complet avec le robot de chargement/déchargement LU6 pour soutenir la découpe laser, et une fois encore, ce système a été fourni par Prima Power. Les propriétaires ont décidé de cet investissement afin d'optimiser la gestion de la tôle, qui dépasse depuis quelque temps les 100 000 kilogrammes par mois, soit environ 200 palettes en assortiment et rotation continus.
« C'est un montant trop important en termes d'efficacité, » déclare Peruzzetto, « par rapport aux ressources nécessaires pour la localisation et l'approvisionnement de la matière première pour la découpe laser, et à la dynamique opérationnelle à laquelle nous devons répondre avec un maximum de flexibilité. »
Le nouveau système de stockage automatique a été relié au logiciel de gestion interne et permet de suivre tous les mouvements dans une perspective 4.0. En d'autres termes, une fois la feuille chargée, sa disponibilité est mise à jour en temps réel, tout en éliminant efficacement toute erreur et en synchronisant chaque heure la présence réelle avec le logiciel de gestion. Il ne faut pas oublier que le vaste portefeuille de clients de l'entreprise entraîne la nécessité de coordonner une multitude de formats de tôle différents, dont beaucoup ne sont pas standard et comportent de nombreuses subtilités.
« L'efficacité et la valeur de l'investissement, » observe Peruzzetto, « ne se sont pas fait attendre. En fait, au cours du premier mois suivant la mise en service, la production de laser a déjà presque doublé, tout en minimisant les temps d'arrêt dus à la gestion des matières premières. La nécessité de créer de l'ordre et de garder le matériel sous contrôle a donc apporté des avantages indirects supplémentaires. Enfin, nous avons également économisé l'espace au sol qui était auparavant occupé par les différentes palettes de tôle, soit en transit, soit en attente de traitement. »
Grâce au robot de chargement/déchargement et au système d'empilage, la nouvelle Prima Power FMS peut également être alimentée en produits semi-finis prédécoupés, qui peuvent ensuite être transformés à un stade ultérieur, selon les besoins.
« La phase d'imbrication a également été améliorée, » ajoute Peruzzetto, « car la nouvelle méthodologie permet d'inclure dans le même lot des pièces à couper qui ne sont pas strictement liées à la commande, mais qui peuvent être temporairement « stockées » dans la cassette (dans n'importe quel wagon disponible), ce qui optimise encore l'efficacité. En bref, le stockage automatisé est devenu le cœur battant de notre flux de travail interne. Cette technologie vous permet de vous appuyer sur des processus continus non supervisés. »
Travailler mieux pour produire plus
Le parc de machines d'Astra (qui, outre les machines Prima Power, comprend d'autres presses plieuses, ainsi que des cellules de soudage et de nettoyage, et de grenaillage) permet de délimiter et de surveiller étroitement l'ensemble du processus de fabrication. L'excellence de la production naît précisément de l' étroite collaboration entre le professionnalisme d'un personnel qualifié et une technologie de pointe, permettant de réduire les temps de production et d'améliorer les résultats opérationnels qui peuvent ensuite être perfectionnés, si nécessaire.
« Dans cette installation, » conclut Peruzzetto, « les ajouts les plus récents ont permis d'augmenter la productivité et l'efficacité avec le même effectif. Grâce au nouveau FMS Night Train, nous pouvons désormais planifier une production sans personnel sur 3 équipes, tout en triant les pièces déjà empilées en fin d'équipe et prêtes à être traitées. Mon objectif est de poursuivre l'automatisation partout où cela est possible, afin de permettre au personnel de mieux travailler tout en augmentant notre capacité de production. »
Cette recherche d'une plus grande efficacité et compétitivité est réaffirmée par les nouveaux projets en cours de développement qui permettront à l'avenir de connecter d'autres systèmes au stockage automatique.
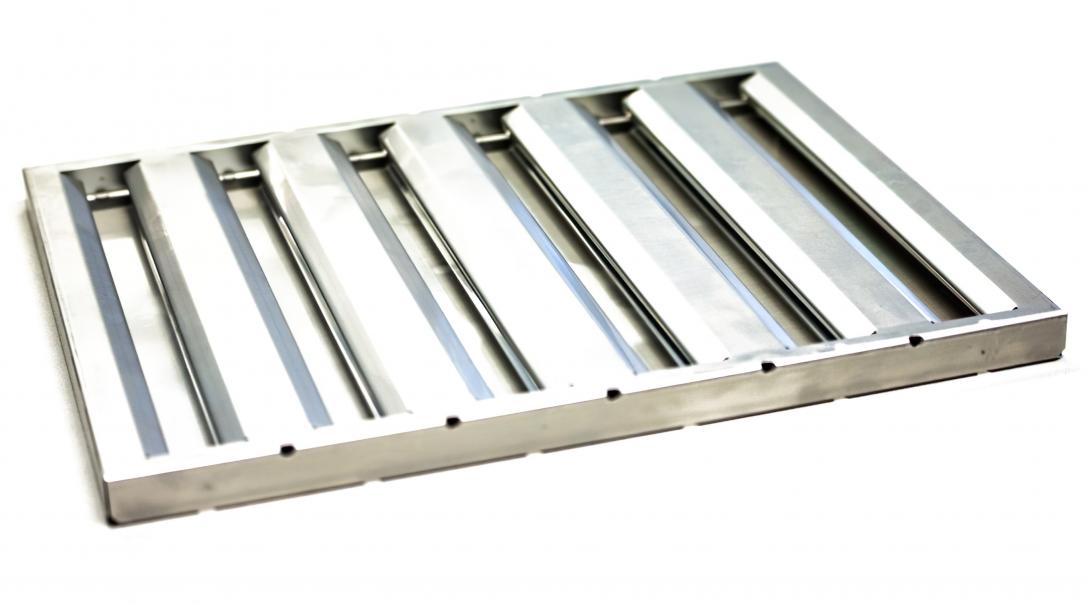
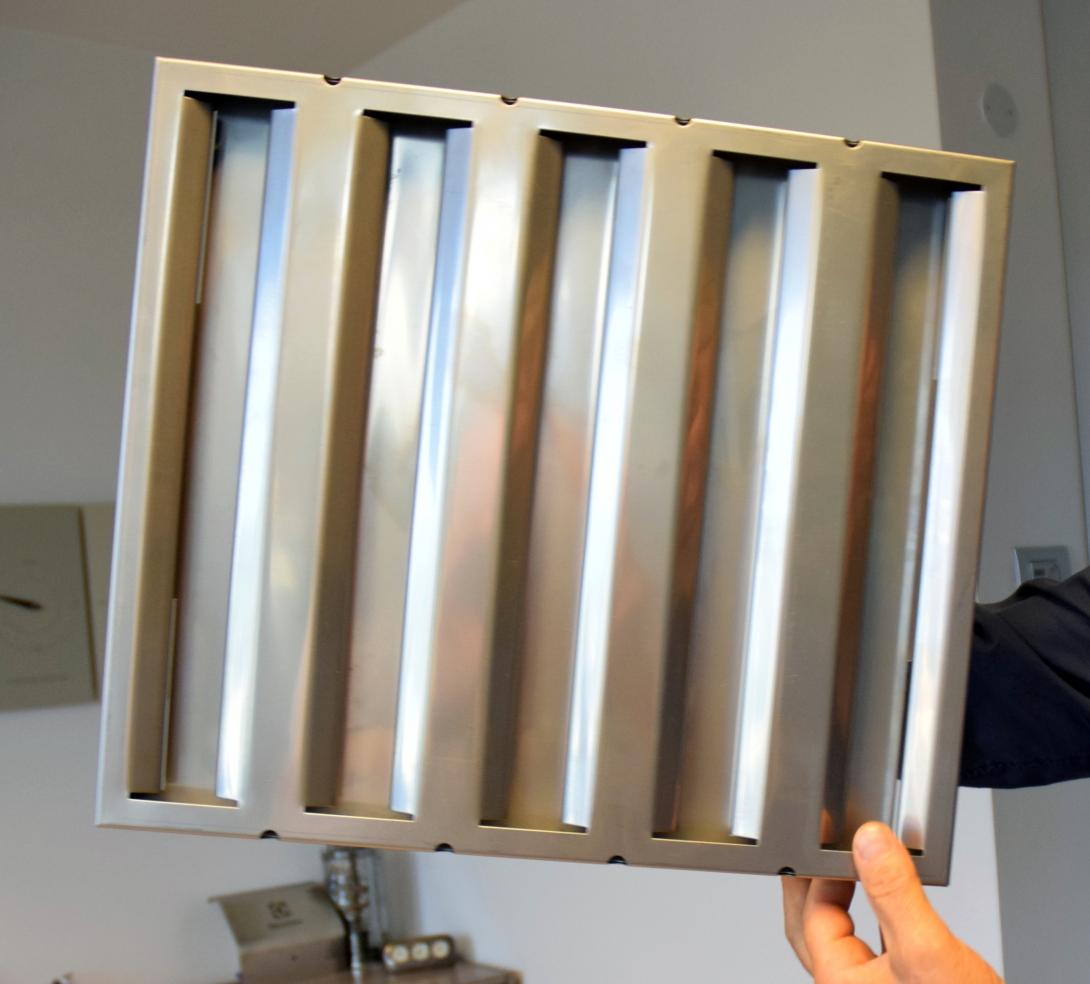
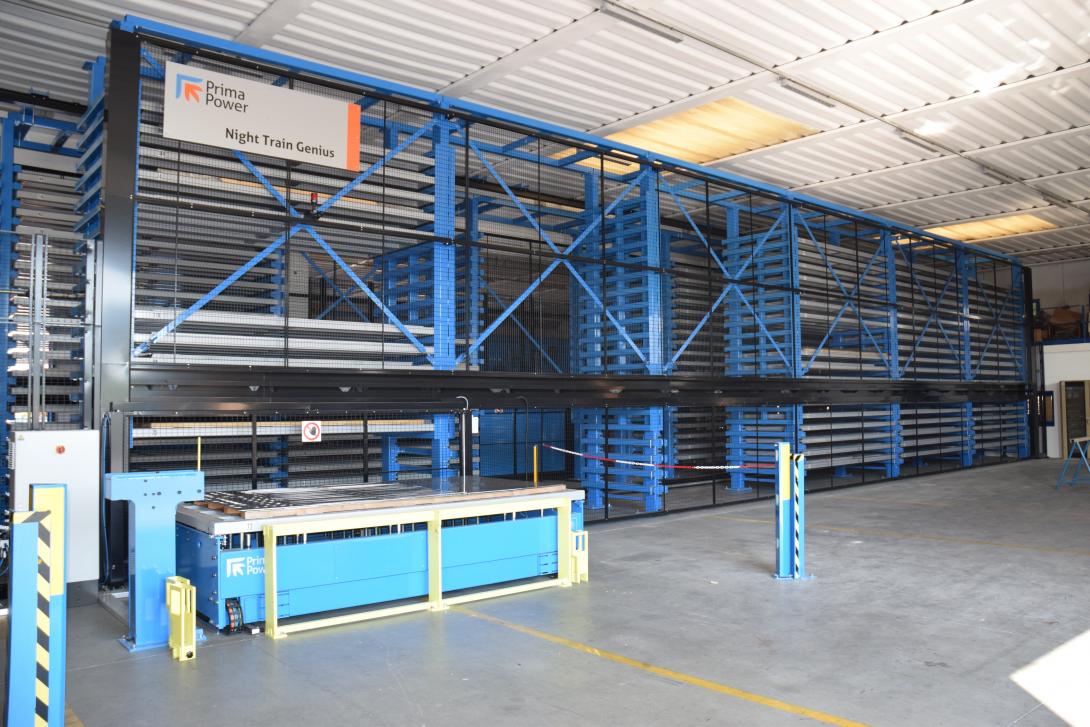
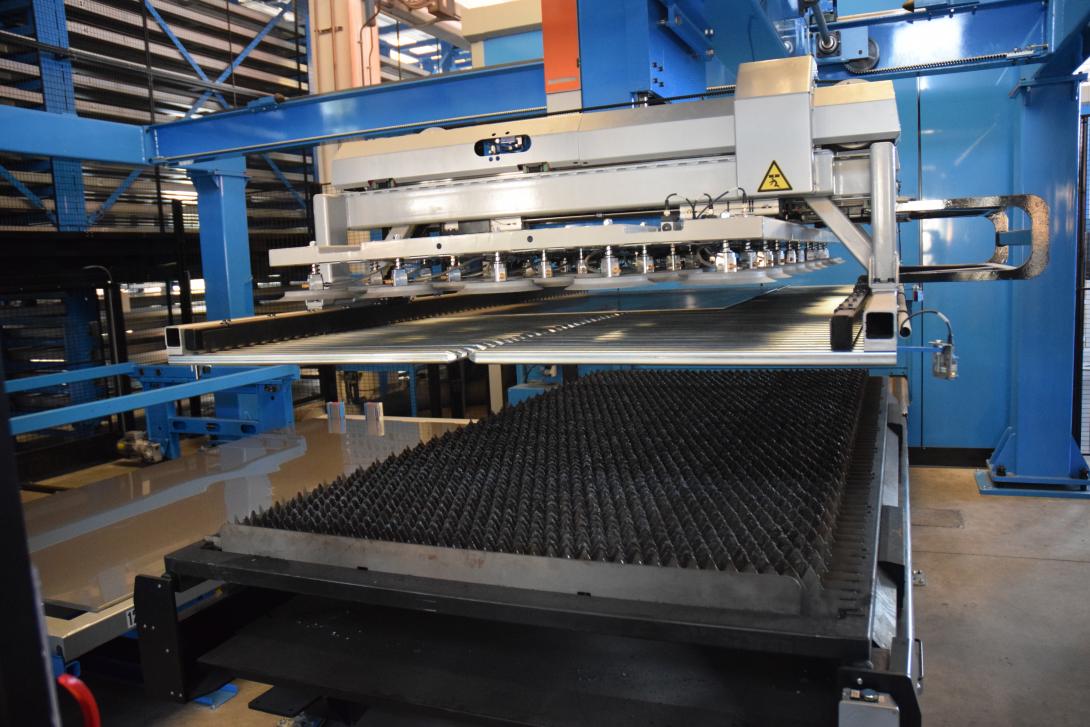
Des filtres à capuchon pour ceux qui ont de grandes aspirations
Les filtres pour hottes industrielles Sabik sont exclusivement conçus et réalisés en acier inoxydable pur 304 2B 6/10 par Astra. Ils se caractérisent par des détails plus fins qui permettent d'acheminer, de condenser et d'expulser les fumées de la manière la plus appropriée, tandis que les éléments plus substantiels, comme les graisses, sont collectés. La structure du filtre a été spécialement conçue pour minimiser l'utilisation de l'unité de dépoussiérage grâce à l'application de principes physiques simples. Un système de ventouses plus larges, l'angle interne de 141°/90° et la structure permettent de réduire la puissance d'aspiration tout en augmentant les mètres cubes absorbés par heure. De cette manière, les coûts de gestion sont réduits de manière drastique. Ce système avancé mais très simple facilite également le nettoyage et l'entretien, garantissant ainsi une plus longue durée de vie et des performances élevées et constantes. La précision et l'esthétique sont toutes deux garanties par la qualité du processus dans lequel les technologies de Prima Power sont utilisées, ainsi que par la méthodologie opérationnelle habituelle suivie par le personnel d'Astra : cette synergie rend le produit unique en son genre.
Sabik est le filtre pour hottes conçu et fabriqué exclusivement par Astra, en acier inoxydable pur 304 2B 6/10.
L'automatisation aux côtés de la production flexible, et vice versa
Le FMS Night Train de Prima Power automatise la gestion des matériaux et des informations connexes, en combinant les processus de production individuels en une seule ligne flexible. La façon dont le système est conçu et structuré permet une plus grande rentabilité et une plus grande flexibilité dans la fabrication des pièces et convient parfaitement à la production de petits lots et de séries. Le système modulaire vous permet de construire et de structurer le projet en fonction des exigences spécifiques du système dans lequel il est installé. Dans le cas de l'entreprise de Vénétie, la configuration choisie pour supporter (pour le moment) le système de découpe laser à fibre a été d'opter pour 12 unités de stockage, chacune modulaire et d'un peu moins de 6 m de haut avec un maximum de 24 cassettes (permettant de stocker 3 tonnes de matériaux ou de composants empilés dans chaque cassette). Cela donne 288 cassettes théoriques, contre 150 actuellement utilisées. Le principal atout du système est sa capacité à s'adapter dans le temps à l'évolution des besoins de production : les cellules, les machines individuelles, les postes de travail peuvent tous être mis à jour, modifiés ou ajoutés, et la capacité de stockage peut être étendue.
Le FMS Night Train de Prima Power a permis à Astra de structurer la gestion des matières premières, de libérer de l'espace au sol et de rendre le processus de découpe laser et sa ligne de production plus efficace.
L'efficacité et la valeur de l'investissement ne se sont pas fait attendre. En fait, au cours du premier mois suivant la mise en service, la production de laser a déjà presque doublé, tout en minimisant les temps d'arrêt dus à la gestion des matières premières.
Are you looking for a similar solution for your company? Find it here
Centre de pliage BCe
PANNEAUTEUSES
Panneauteuse semi-automatique alliant flexibilité et productivité
Platino Fiber
CORTE A LASER 2D
Rentável para uma mistura de produção que inclui todos os materiais e espessuras
Night Train FMS®
SYSTÈMES DE FABRICATION FLEXIBLES