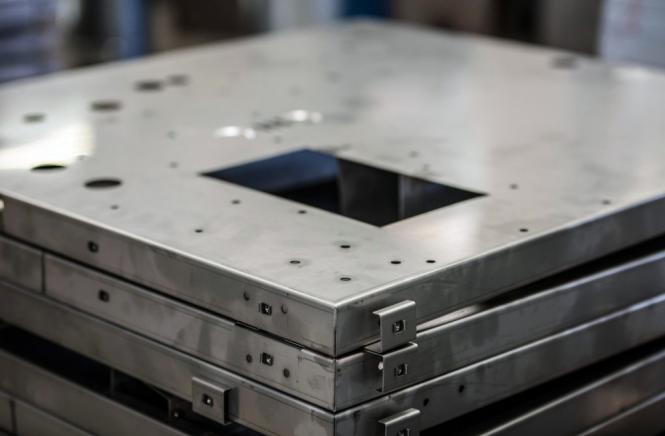
El orden y la eficiencia impulsan la productividad
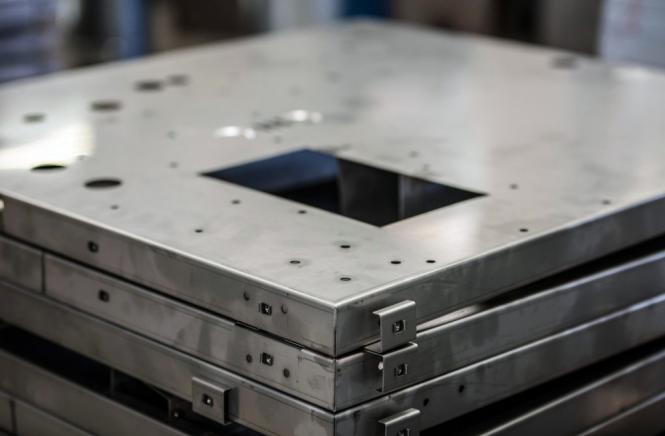
Astra se fundó hace poco más de treinta años como resultado de un instinto innovador que resultó ser un éxito en pocos años, esto es que el acero inoxidable se convertiría en el material tecnológico del futuro.
Actualmente, se procesa y se le da forma a través de un sistema productivo y eficiente en el que cada una de las fases operativas, desde el corte por láser, el punzonado, el plegado, el empanelado hasta su almacenamiento automático (el centro del proceso) son consideradas por Prima Power.
Astra se especializa en el diseño y el procesamiento de la carpintería metálica y produce principalmente componentes de acero inoxidable que varían desde productos semiterminados hasta los terminados. La compañía, fundada en 1991, siempre ha tenido como objetivo alcanzar los más altos niveles de calidad requeridos, siguiendo la perspicacia del fundador Rudy Peruzzetto, quien identificó que el acero inoxidable se convertiría en el material tecnológico del futuro. Sobre esta base, los recursos y las destrezas se orientaron inmediatamente hacia sectores exigentes como la industria hospitalaria y farmacéutica y en 1997 se amplió la producción por primera vez. Ese mismo año también se inició una colaboración con el enorme grupo multinacional Electrolux Professional, líder mundial en electrodomésticos y equipos de uso profesional para el que Astra también se convirtió en un proveedor certificado. Y es precisamente al sector profesional al que continúa sirviendo a través de la producción y el suministro de productos modulares, semiterminados y terminados que se utilizan en instalaciones profesionales grandes o en soluciones de lavado, cocción y refrigeración. Se trata de una colaboración eficaz en la que la satisfacción del cliente va más allá de la excelente relación calidad/precio y por la que la compañía es reconocida y respetada, incluso en el área de la construcción de terceros.
"Los importantes resultados operativos que hemos obtenido", afirma el propietario Rudy Peruzzetto, "nos han permitido ampliar aún más nuestra capacidad de producción hasta un total que hoy asciende a 6,000 metros cuadrados en interiores y la misma cantidad en espacio en exteriores dividido entre 3 plantas en San Polo di Piave, en la provincia de Treviso".
La expansión de la compañía siempre ha sido paralela a su tendencia inherente hacia la innovación, apoyada con el tiempo por el fuerte ideal de desarrollo sustentable (por ejemplo, el nuevo almacén se alimenta con fuentes de energía renovable mediante un sistema fotovoltaico específico). El especial cuidado del medio ambiente también se aprecia en el reemplazo gradual de toda la flota de máquinas por modelos cada vez más funcionales y ecológicos. Esta misma flota garantiza hoy en día un proceso de producción eficaz y de alto rendimiento en el que todas las tecnologías, desde el corte por láser hasta el punzonado, el plegado y el empanelado hasta el sistema de almacenamiento automático son suministradas por Prima Power, la División de Maquinaria del Grupo Prima Industrie. Entre ellas, las últimas incorporaciones en orden cronológico fueron el nuevo centro de plegado BCe 2720 y el sistema de almacenamiento automático Night Train FMS junto con el robot de carga/descarga LU6 para apoyar el corte por láser (estos sistemas se instalaron a principios de 2020).
Desde lotes pequeños a la producción en masa
En la actualidad, Astra trabaja para el sector hospitalario/farmacéutico en particular, así como para grandes instalaciones y el sector naval. El filtro de laberinto para las campanas industriales Sabik es su producto propio, además de un referente de ingenio, sencillez y eficacia (ideado y creado por el propio Rudy Peruzzetto), que demuestra el conocimiento técnico y la capacidad de la compañía para apoyar al cliente en la creación de un producto terminado, al igual que otros innumerables artículos (cilindros de elevación de placas y elevadores de bandejas, carros de servicio, etc.) en acero inoxidable, así como en acero galvanizado, aluminio o cobre.
"Alrededor del 80 % de lo que procesamos es acero inoxidable", especifica Peruzzetto, "y normalmente trabajamos con espesores de hasta 5-6 mm, aunque nuestros equipos nos permiten procesar incluso más de 10 mm, lo que abarca toda la cadena de suministro, desde los productos semiterminados hasta el producto terminado. Podemos manejar 1, 10 o 100 piezas con la misma flexibilidad que miles de piezas”.
En este sentido, el primer avance de producción se produjo en la compañía hace más de una década con la adquisición de la primera punzonadora combinada, una SG8 1530 con cizalla angular de la entonces Finn Power. Esta integración triplicó con creces la cantidad de chapa metálica que se podía procesar hasta ese momento. Hace aproximadamente una década se dio un paso decisivo con la introducción de un sistema de corte por láser de alto rendimiento, un láser de fibra 2D de Prima Power, una Platino de 3 kW junto con un robot de paletización/apilado LST para la selección automática de piezas, y una plegadora de paneles eléctrica EP 1030. Como ya se ha mencionado, la instalación más reciente de la plegadora de paneles BCe 2720 se llevó a cabo hace solo unos meses como modernización del sistema anterior, junto con el sistema de almacenamiento automático Night Train FMS que incluye un robot de carga/descarga LU6 para apoyar al corte por láser.
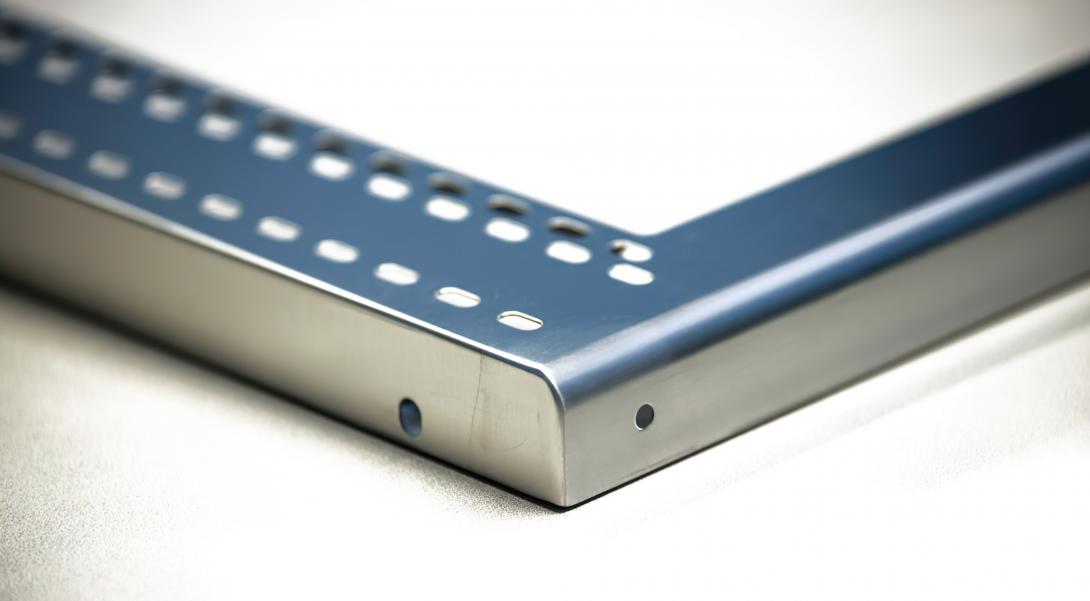
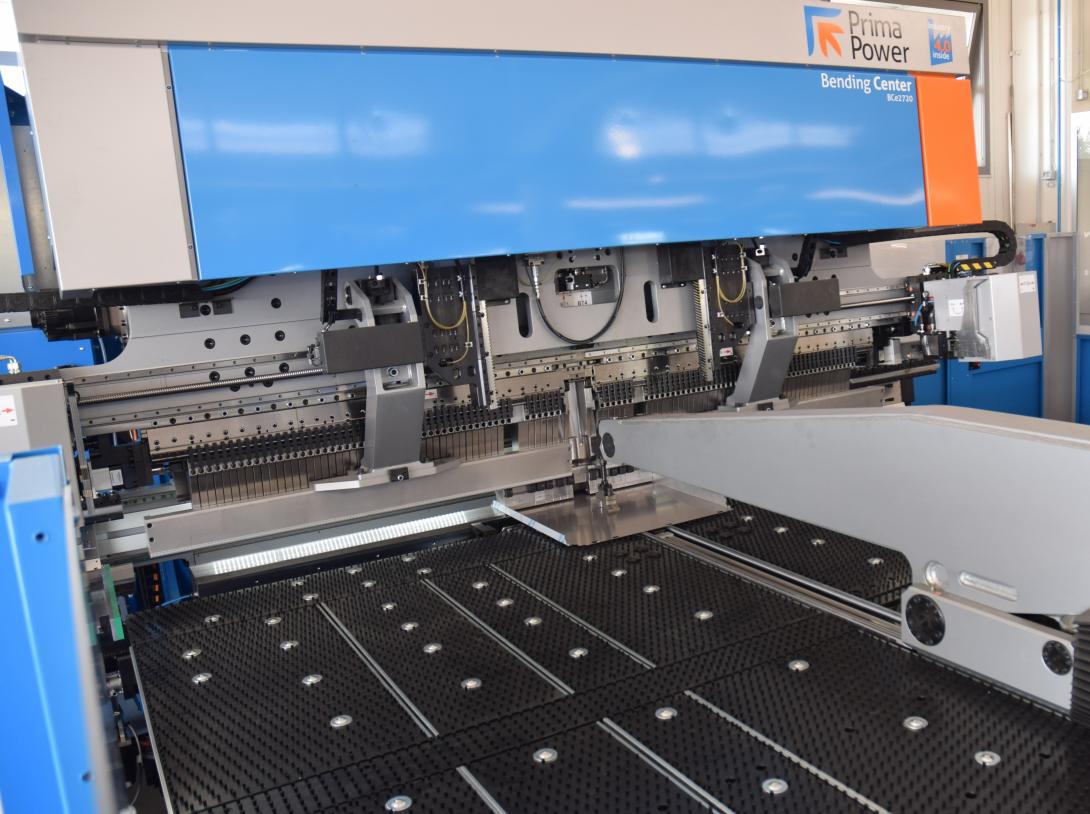
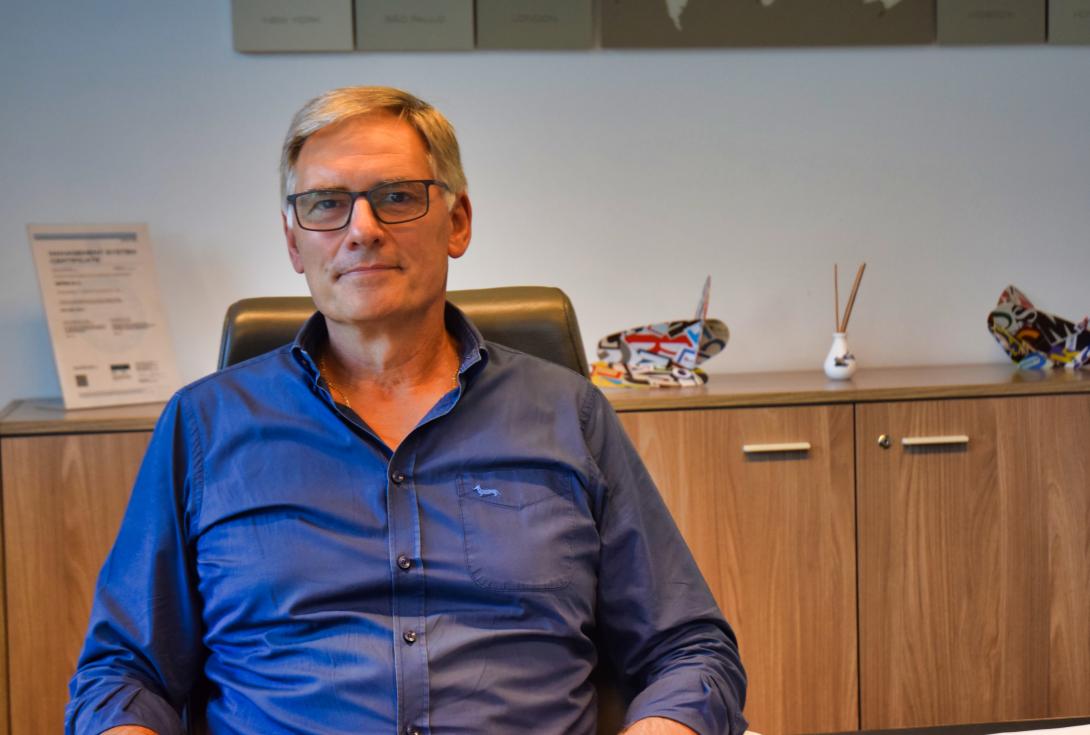
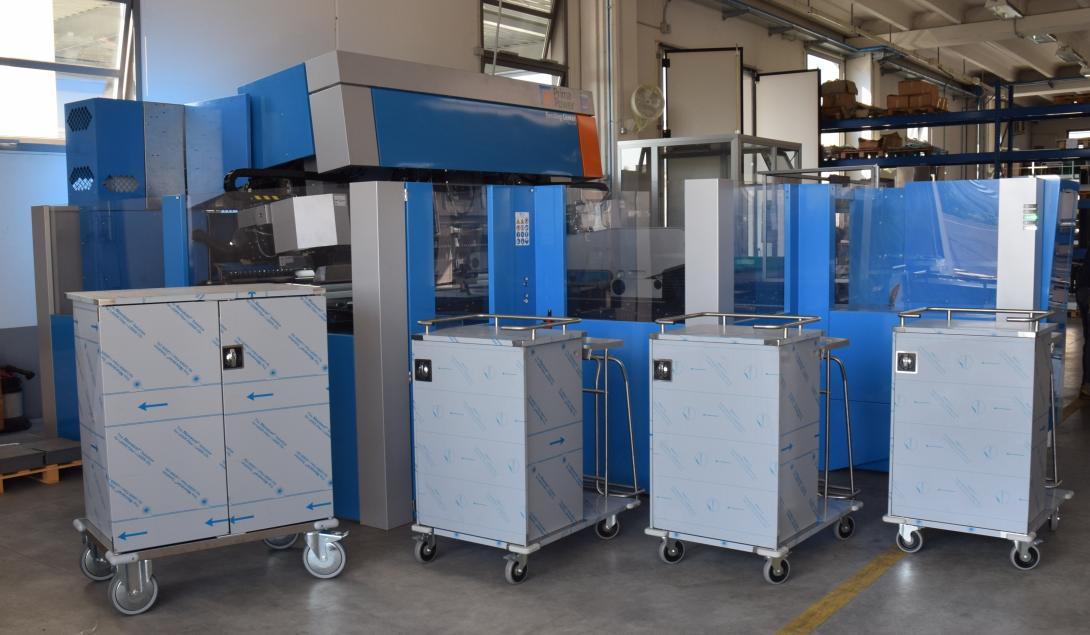
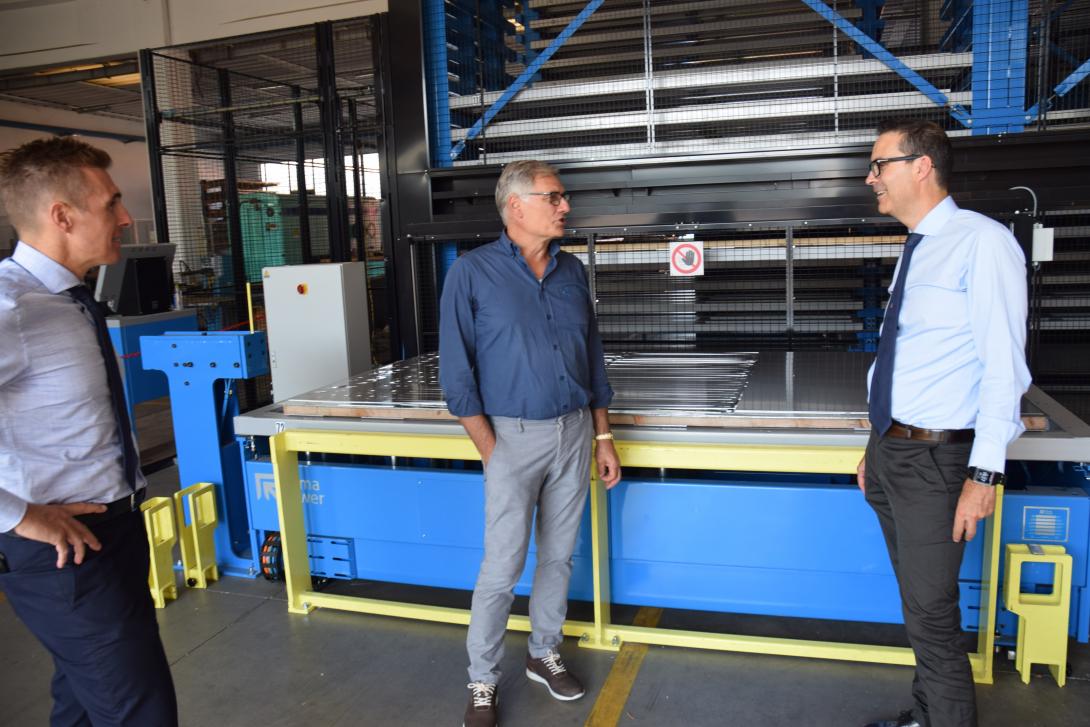
Centro de plegado altamente flexible con la misma productividad
El centro de plegado BCe de Prima Power ofrece la solución ideal para quienes, como Astra, trabajan con piezas individuales, lotes pequeños o producción en masa. De hecho, esta plegadora de paneles pretende combinar las conocidas ventajas del producto de empanelado, es decir, la flexibilidad, la precisión y la alta calidad con un proceso semiautomático, pero altamente productivo en el que la máquina está siempre en funcionamiento gracias a la mesa de carga y descarga LUT que permite cargar y descargar piezas durante la operación. La alimentación manual también permite el plegado de piezas que no son fáciles de transportar mediante sistemas de carga automáticos. De este modo, la producción de piezas totalmente perforadas, de figuras largas o anchas, o incluso de piezas con aberturas interiores más grandes, se vuelve algo totalmente factible. Al ser servoeléctrica y estar equipada con 8 motores independientes y varios ejes CNC, la BCe 2720 permite procesar espesores de 0,5 hasta 3,2 mm de acero (hasta 2,2 mm de acero inoxidable y hasta 4 mm de aluminio). Esto también ha permitido a la compañía aumentar tanto la longitud máxima de plegado del sistema anterior de 2.250 mm a los 2.750 mm actuales, así como elevar el nivel de automatización del proceso. El sistema AUT (herramientas auxiliares superiores) también es muy valorado. Se trata de un sistema de herramientas auxiliares superiores que ayudan a llevar a cabo determinados pliegues, lo que demuestra aún más la flexibilidad de la máquina.
"Nuestra decisión de optar por una nueva plegadora de paneles de mayor rendimiento", explica Peruzzetto, "se basa en nuestra convicción consciente y en la experiencia de la última década sobre lo difícil que es encontrar personal especialmente calificado, en este caso para las plegadoras de paneles. Esta escasez de destrezas puede, en ocasiones, poner en peligro la visión del futuro de la compañía o, al menos, cambiar su trayectoria de crecimiento. Por lo tanto, he optado por centrarme en una tecnología de plegado diferente, en la que la programación y la automatización son la base de la productividad. A primera vista, la plegadora es ciertamente más fácil de programar porque es una tecnología más conocida y, debido a sus características, puede incluso procesar piezas que no serían posibles con una plegadora de paneles. Pero identificar el producto correcto y nuestra capacidad de diseño para ajustar ciertas piezas a fin de hacer posible su procesamiento en esta máquina nos han permitido obtener grandes beneficios en términos de tiempo de ejecución, así como de herramental para lograr la calidad esperada"
Este equipo tecnológico ha ampliado considerablemente el potencial de producción de la compañía, que ahora puede procesar formatos más grandes.
La eficiencia de los procesos (también) comienza con el manejo de la materia prima
Como ya se ha destacado, Astra también integró el nuevo sistema de almacenamiento automático Night Train FMS, junto con el robot de carga/descarga LU6 para apoyar al corte por láser y una vez más estos fueron proporcionados por Prima Power. Los propietarios decidieron esta inversión para optimizar el manejo de la chapa metálica, que desde hace tiempo supera los 100.000 kilogramos al mes, lo que equivale a unos 200 palets en una clasificación y rotación continua.
"Es una cantidad demasiado grande en términos de eficiencia", dice Peruzzetto, "en comparación con los recursos necesarios para la ubicación y la obtención de la materia prima para el corte por láser y la dinámica operativa a la que debemos responder con la máxima flexibilidad".
El nuevo sistema de almacenamiento automático se ha vinculado con el software de gestión interno y mantiene un seguimiento de todos los movimientos desde una perspectiva 4.0. En otras palabras, una vez cargada la chapa, su disponibilidad se actualiza en tiempo real y elimina eficazmente cualquier error y sincroniza la presencia real cada hora con el software de gestión. Debe tenerse en cuenta que la amplia cartera de clientes de la compañía conlleva la necesidad de coordinar una multitud de formatos de chapa metálica diferentes, muchos de los cuales no son estándar e implican muchas complejidades.
"La eficacia y el valor de la inversión", observa Peruzzetto, "no tardaron en manifestarse. De hecho, en el primer mes después de la puesta en marcha, la producción del láser ya casi se ha duplicado, al tiempo que se han minimizado los tiempos de inactividad por el manejo de las materias primas. Así que la necesidad de crear orden y mantener el material bajo control trajo consigo beneficios indirectos adicionales. Por último, pero no por ello menos importante, también hemos ahorrado el espacio que antes ocupaban los distintos palets de chapa metálica, ya sea en tránsito o en espera de ser procesados".
Gracias al robot de carga/descarga y al sistema de apilado, la nueva FMS de Prima Power también puede alimentarse con productos semiterminados precortados, que pueden procesarse en una etapa posterior, según sea necesario.
"También se ha mejorado la fase de anidamiento", añade Peruzzetto, "ya que la nueva metodología permite incluir piezas a cortar en el mismo lote que no son estrictamente relevantes para el pedido, pero éstas pueden "almacenarse" temporalmente en el casete (en el vagón que esté disponible), optimizando aún más la eficiencia. En resumen, el almacenamiento automatizado se ha convertido en el centro de nuestro flujo de trabajo interno. Esta tecnología le permite contar con procesos continuos no supervisados".
Trabajar mejor para producir más
La flota de máquinas de Astra (que, además de las máquinas de Prima Power, incluye otras prensas plegadoras, así como celdas de soldadura y limpieza y, granallado) permite delinear y supervisar de cerca todo el proceso de manufactura. La excelencia en la producción se deriva precisamente de la estrecha colaboración entre el profesionalismo del personal calificado y la tecnología de vanguardia, lo que permite reducir los tiempos de producción y mejorar los resultados operativos que luego se pueden perfeccionar, si es necesario.
"En esta instalación", concluye Peruzzetto, "las últimas adiciones han resultado en un aumento de la productividad y la eficacia con la misma fuerza laboral. Gracias al nuevo Night Train FMS, ahora podemos planificar la producción sin personal a lo largo de 3 turnos, al tiempo que clasificamos las piezas que ya están apiladas al final del turno y que están listas para su posterior procesamiento. Mi objetivo es buscar la automatización siempre que sea posible, para que el personal trabaje mejor al tiempo que aumenta nuestra capacidad de producción".
Esta búsqueda de mayor eficiencia y competitividad se reafirma con los nuevos proyectos en desarrollo que conectarán otros sistemas al almacenamiento automático en el futuro.
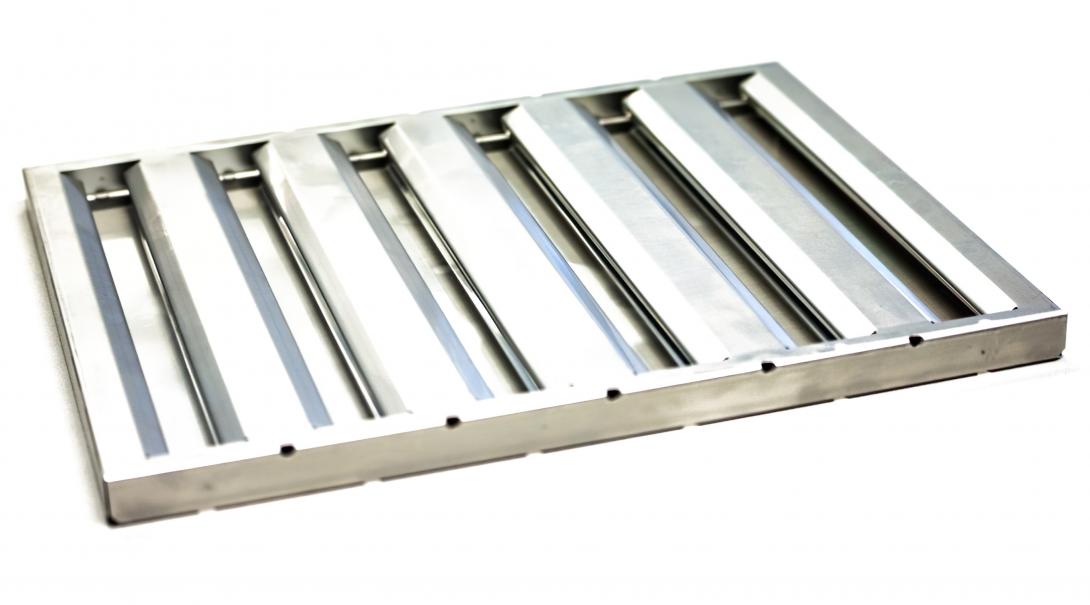
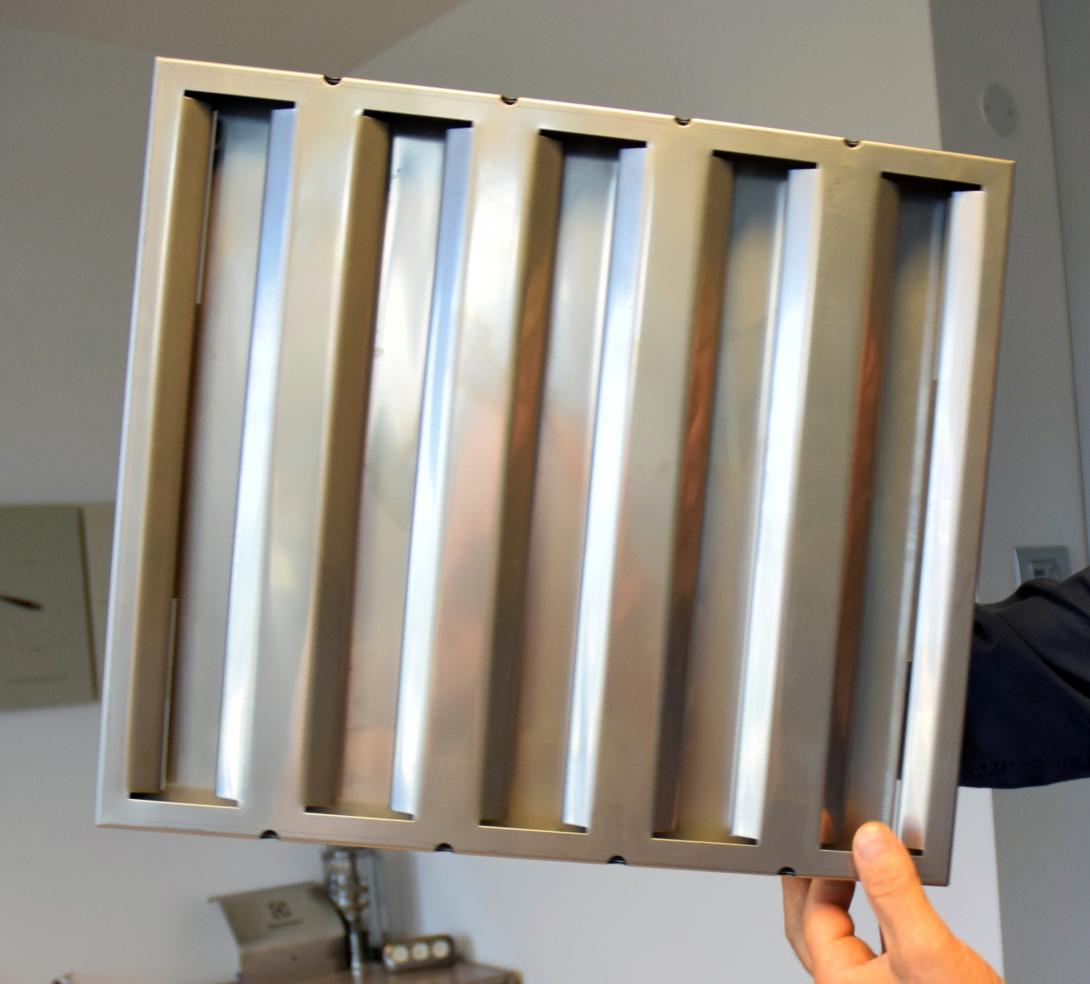
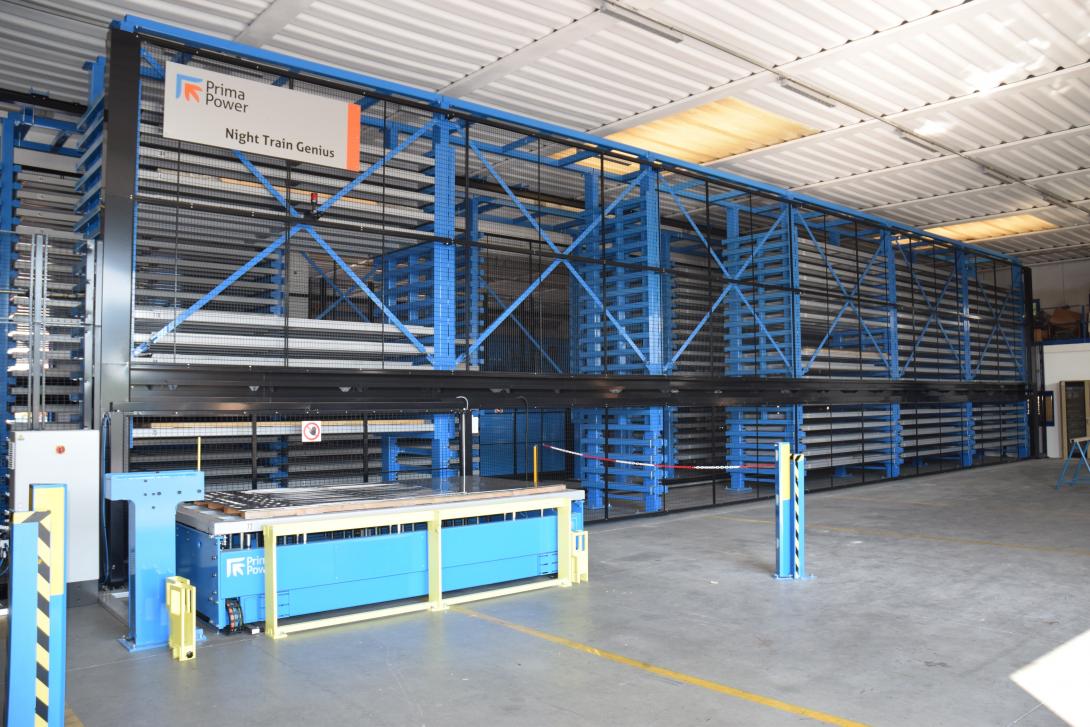
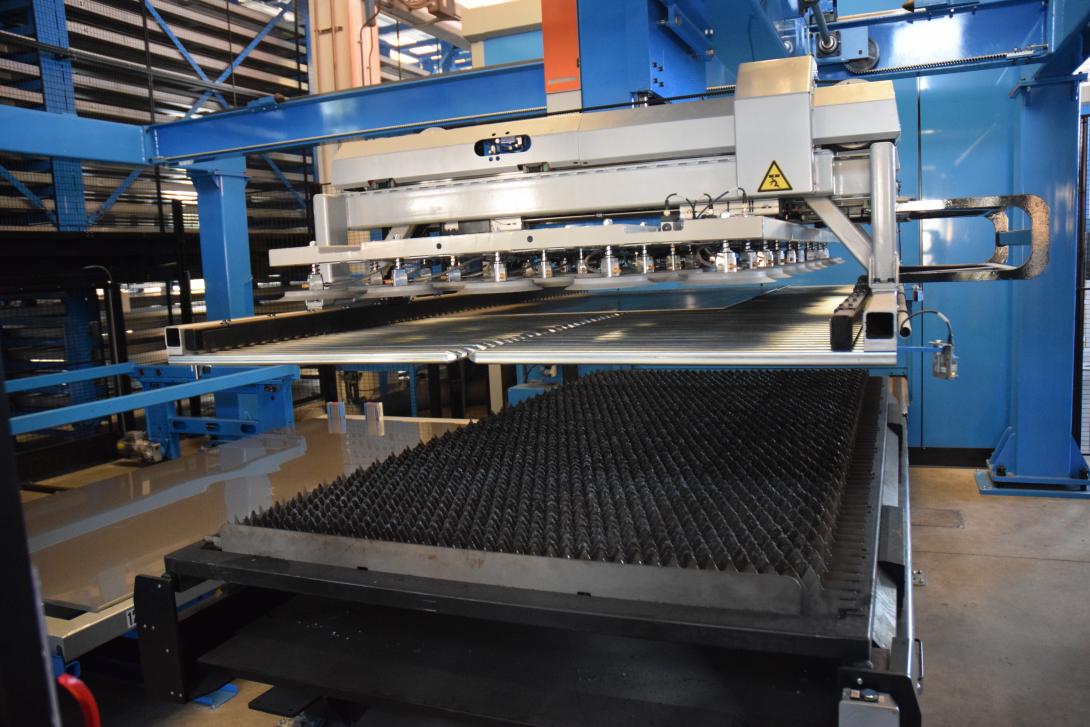
Filtros para campana para los que tienen grandes aspiraciones
Astra diseña y crea filtros para las campanas industriales Sabik exclusivamente en acero inoxidable puro 304 2B 6/10. Se caracterizan por tener detalles más finos que permiten transportar, condensar y expulsar los humos de la manera más adecuada, al tiempo que se recogen los elementos más sustanciales, como la grasa. La estructura del filtro se ha diseñado específicamente para minimizar el uso de la unidad del colector de polvo gracias a la aplicación de la física simple. El sistema de tazas más anchas, el ángulo interno de 141°/90° y la estructura permiten reducir la potencia de succión al tiempo que también aumentan los metros cúbicos que se absorben cada hora. De este modo, los costos de manejo se reducen drásticamente. Este sistema avanzado, pero muy sencillo también facilita la limpieza y el mantenimiento y garantizan una mayor vida útil, así como un alto rendimiento consistente. Tanto la precisión como la estética están garantizadas por la calidad del proceso en el que se utilizan las tecnologías de Prima Power, junto con la metodología operativa habitual que sigue el personal de Astra; esta sinergia hace que el producto sea único.
Sabik es el filtro para campanas diseñado y fabricado exclusivamente por Astra, en acero inoxidable puro 304 2B 6/10.
La automatización junto con la producción flexible, y viceversa
El Night Train FMS de Prima Power automatiza el manejo de los materiales y la información relacionada, además combina los procesos de producción individuales en una única línea flexible. La manera en que está diseñado y estructurado el sistema permite una mayor rentabilidad y flexibilidad en la manufactura de las piezas y se adapta perfectamente tanto a la producción de lotes pequeños como a la producción en serie. El sistema modular permite construir y estructurar el proyecto según los requisitos específicos del sistema en el que se instala. En el caso de la compañía de Veneto, la configuración elegida para apoyar (por el momento) el sistema de corte por láser de fibra fue optar por 12 unidades de almacenamiento, cada una de ellas modular y con poco menos de 6 m de altura, con un máximo de 24 casetes (lo que permite almacenar 3 toneladas de material o componentes apilados en cada casete). Esto proporciona 288 casetes teóricos, frente a los 150 actuales. La fortaleza principal del sistema es la capacidad de adaptarse con el tiempo a las cambiantes necesidades de producción, es decir, las celdas, las máquinas individuales y las estaciones de trabajo pueden modernizarse, modificarse o añadirse y la capacidad de almacenamiento puede ampliarse aún más.
El Night Train FMS de Prima Power ha permitido a Astra estructurar el manejo de las materias primas, así como liberar espacio en el suelo y hacer generalmente más eficiente el proceso de corte por láser y su línea de producción.
La eficacia y el valor de la inversión no tardaron en manifestarse. De hecho, en el primer mes después de la puesta en marcha, la producción del láser ya casi se ha duplicado, al tiempo que se han minimizado los tiempos de inactividad por el manejo de las materias primas
Busca una solución similar para su empresa? Encuéntralo aquí
Centro de panelado BCe
PANELADORAS
Paneladora semiautomática que combina flexibilidad y productividad
Platino Fiber
CORTE A LASER 2D
Rentável para uma mistura de produção que inclui todos os materiais e espessuras
Night Train FMS®
SISTEMAS DE MANUFACTURA FLEXIBLE