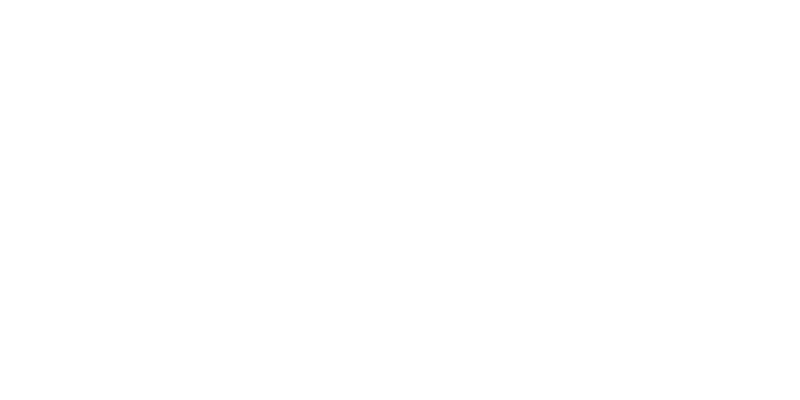
Automatic cutting, storing, and sorting, with 850 million combinations
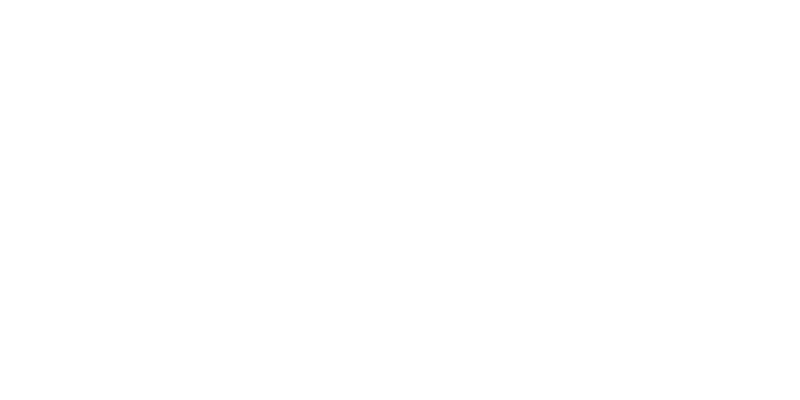
Specialising in manufacturing components and accessories for HVAC systems, Tecno-Ventil internally manages the entire production chain: assembled products created from 15,000 primary parts, are combined to create innovative, intelligent, and stylish solutions. A process where the sheet metal department makes the most of a high-performance, continuously running Prima Power system consisting of a fiber laser cutting machine, a storage unit, and an automatic parts sorting system.
Located in Spino d’Adda, Tecno-ventil is specialized in manufacturing components and accessories for HVAC systems, with a particular focus on residential and commercial systems that require air treatment, and not just heating or cooling. The business offers approximately 15,000 items that can be combined to create 850 million product configurations. “Products,” explains Andrea Fasoli, owner of the business together with his brothers, Marco and Alessandro, and father, Mario, “that in 80% of cases are tailor-made. Our mission has always been product innovation, as well as process innovation, also by identifying equally innovative technologies that allow us to best meet our final objective – that of satisfying our customers with customized solutions.” The company, which was founded in 1984, immediately set itself apart thanks to its creativity, proactiveness, and flexibility, firmly establishing itself in its sector within just a few short years.
Another differentiating element was the brave decision to produce almost its entire range of products internally, managing the full chain, from design to inspection of the incoming materials, from processing to painting, right up to suitability testing of the finished product. “We manufacture almost all our components,” adds Fasoli, “going as far as producing the smallest parts, thereby eliminating third-party manufacturing, and ensuring maximum flexibility, quality, and customization of our solutions ourselves. In so doing, we ensure quick turnaround times – order confirmation to delivery ranges between just 7-10 working days.”
A decisive factor in optimizing product development was without a doubt the sheet metal cutting department, which today includes a high-performance Prima Power system consisting of a 2D Laser Genius 1530 cutting machine with 4kW laser source, a Compact Tower Twin storage system, and an LST automatic parts sorting system.
Maximum productivity with no interruptions
The system purchased from the Machinery Business Unit of the Prima Industrie Group was not Tecno-ventil’s first. In fact, as Fasoli himself recalls, “we first started dealing with the company some 20 years ago now when we purchased a previous generation laser cutting machine. The machine set itself apart over time because of its excellent reliability and that convinced us to reconsider Prima Power among various other brands for the new solution we were looking for.” After reaching maximum production capacity, the business opted for a new investment that included not only the cutting and feeding of the material, i.e. the sheet metal, but especially, sorting of the processed parts. The previous system allowed for continuous processing of cut parts with separation of the components done by one or more operators, who were responsible for separation and palletising the parts based on the various orders. All of which took a significant amount of time and resulted in inefficiencies that understandably also included possible errors on the part of the operator.
“A deciding factor,” Fasoli explains, “in choosing the new system was solving this critical matter, or in other words, evaluating the prospect of speeding up the step after cutting in an ordered and definitive way, palletising the parts so that they are ready for the next steps in the process, but by employing sorting systems that would completely replace the need for manual operations. Prima Power’s system was the one that impressed us the most, both in terms of production capacity as well as its high performance. Compared to the systems of other manufacturers, the LST sorting system of the cut parts was, in our opinion, the most functional.”
It is worth noting that the types of products manufactured by Tecno-ventil require various material thicknesses (i.e., semi-finished products mainly in thin galvanized sheet metal of between 0.8 and 3mm). Hence the reason why to maximise the efficiency of the process, a twin tower automatic storage system was chosen, to ensure, also in this case, no interruptions during processing and to avoid manual operations.
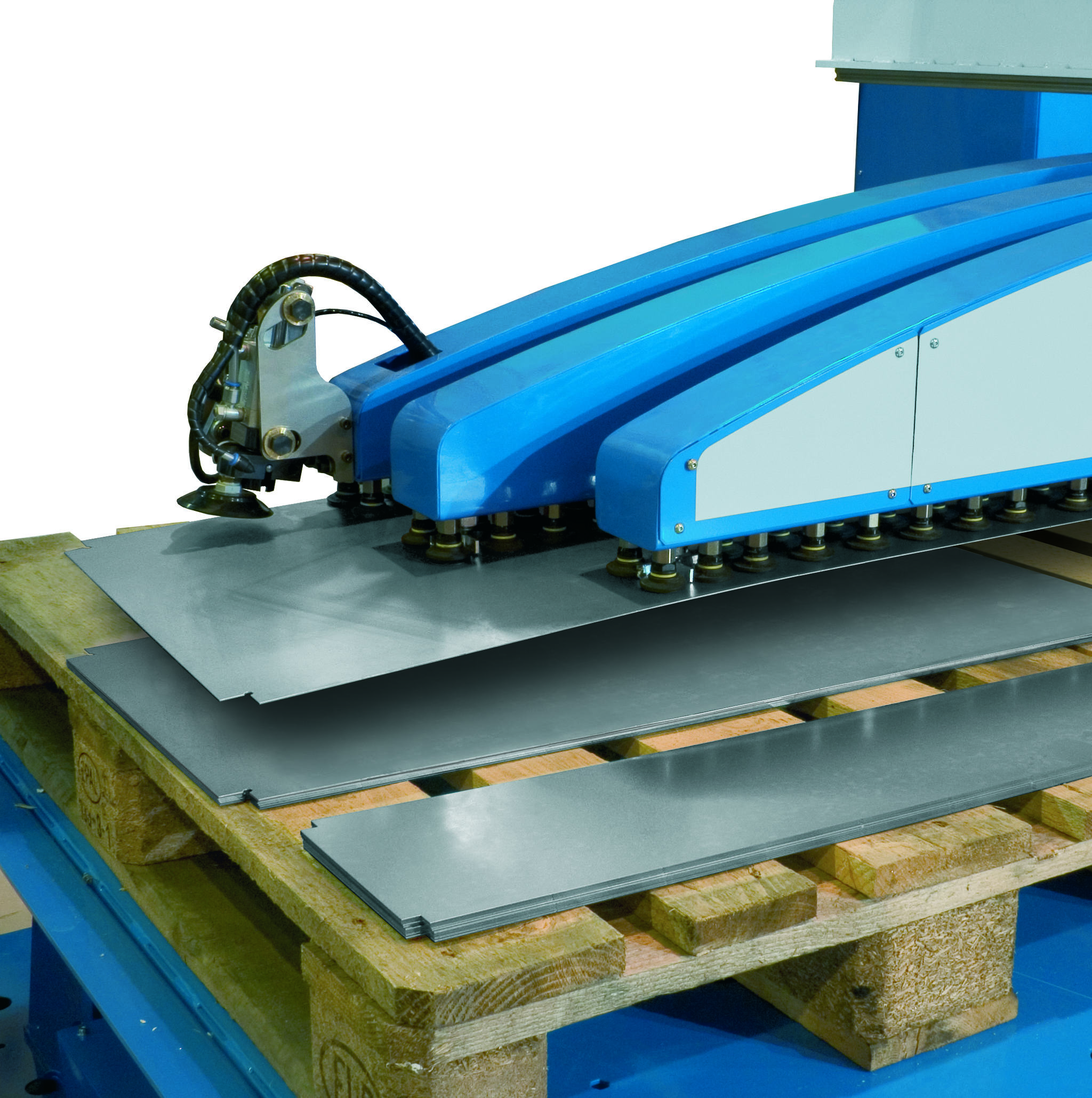
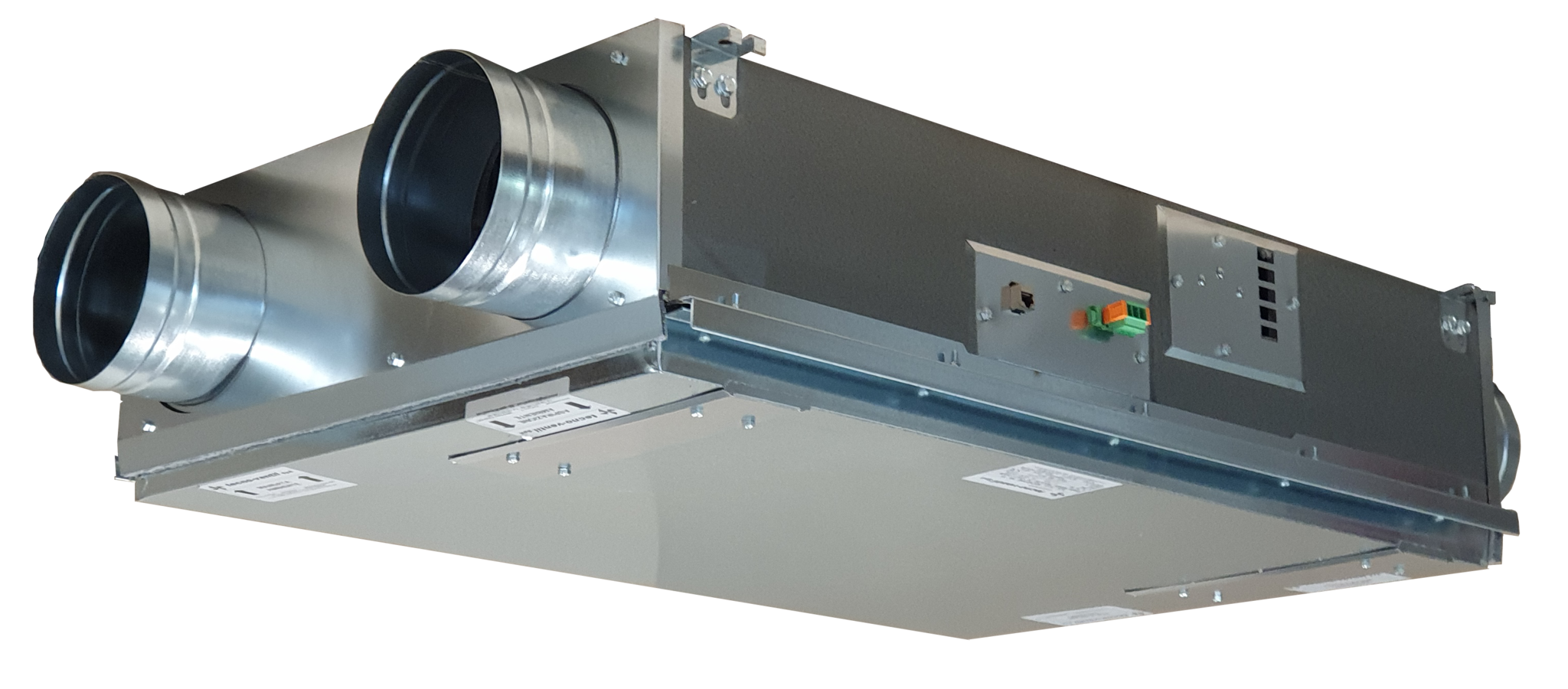
The system and its solutions
Looking at it in greater detail, Tecno-ventil’s Prima Power system firstly includes a Laser Genius 1530, a high-end 2D cutting machine, which combines flexibility, excellent dynamic performance, and high levels of efficiency and precision, thanks to the innovative use of materials such as carbon fiber and synthetic granite. The new cutting head and the optional suites (Smart Cut, Max Cut, and Night Cut) optimize the laser cutting process for each application. The Compact Tower Twin, on the other hand, is the flexible system for 2D lasers that integrates loading and unloading of the processed and rough sheets onto two storage towers (with 26 or 36 pallets). Increasing the level of automation and making the system even more efficient is the LST system that automatically picks the cut parts and stacks them thanks to simple programming. Reliable, accurate, and efficient, the system allows for three different procedures for picking parts: RALC (Robot-Assisted Last Cut), where the robot holds onto the part before the laser finishes cutting the last profile; Pre-Sorting, where the robot reaches the operating area while cutting takes place, and resumes as soon as the robot moves away; and Sorting, where the part is cut before being picked with the robot stationary outside the working area. To avoid unwanted movement during sorting, the system comes with additional clamps to hold the sheets.
The added value of process digitization
Following the new investment, Tecno-ventil now has a sheet metal cutting department which consists of 4 systems in total: two laser cutting systems (including the one covered by this article), a combined laser machine, and a combined punch with right-angle shear. The latter is a Prima Power SGe Shear Genius connected to a coil system, which ensures several advantages based on the products manufactured. “The main advantage,” reveals Fasoli, “is certainly the reduction in wasted material, as parts can be processed with certain characteristics that result in waste or scrap that is close to zero.”
The company produces over 50% of its components with the new laser cutting system – a large percentage that fully exploits the production potential of the system.
“In addition to the benefits of the sorting system already mentioned,” adds Fasoli, “the support of the automatic loading/unloading storage system has allowed us to significantly increase production capacity while reducing production time and running costs since it allows for unmanned shifts.”
Data is objective and constantly verified thanks to production that in Tecno-ventil is managed using Industry 4.0 technology with MES software and an IT infrastructure that connects all the machines, including Prima Power’s.
“The move toward digitization,” Fasoli concludes, “has significantly facilitated management of our large number of items, that in the past were recorded manually on paper, thanks to highly qualified and, above all, well-trained staff, who were able to deal with any type of order issues. It is easy to imagine how the transition to digital is not easy, as was in our case, and this happens when more innovative and advanced technologies arrive in the various departments. It’s also true though that after that initial phase of reluctance and reticence, it is those same operators who don’t want to go back. In any event, thanks to advances in technology and digital in terms of 4IR, we have undoubtedly made our entire business system more efficient and rationalized, increasing the levels of monitoring and control, and speeding up the entire process: from production, to storage, to delivery. The infrastructure created allows us to track and measure data for continuous work improvement, to create value that will be passed on to the market, transforming it into satisfaction and greater competitiveness for our customers.”
Article from Lamiera magazine, September 2021 issue
You can read this and other articles in the latest issue of Power Line, the Prima Industrie magazine. Read it here.
Prima Power’s system impressed us both in terms of production capacity as well as its high performance. Compared to the systems of other manufacturers, the LST sorting system of the cut parts was, in our opinion, the most functional
Are you looking for a similar solution for your company? Find it here
Laser Genius+
WYCINARKI LASEROWE 2D
Talent do upraszczania pracy i zwiększania zysku.
System sortujący dla maszyn laserowych (LST)
PRZEMIESZCZANIE MATERIAŁU
Zautomatyzowany, ekonomiczny i wysokowydajny system sortowania arkuszy dla maszyn laserowych 2D
Combo Tower Laser
PRZECHOWYWANIE