
Metaltecnica, Italian passion for the catering industry worldwide

Metaltecnica manufactures equipment designed to maximize efficiency and reduce energy consumption, while also boosting performance to enable maximum hygiene in kitchens around the world. This wide range of solutions is divided into six product categories and includes a number of high-performance Prima Power plants in their manufacture.
A LONG STORY OF STAINLESS STEEL PRODUCTION
It has more than 30 years of business behind it, over 6,000 square meters of production area, about 400 square meters of showroom, and 50 employees. We're talking about Metaltecnica, a company operating in the field of stainless steel equipment for public restaurants and catering, based in Bellaria Igea Marina (RN). It was founded by Vincenzino Baietta and Isora Baschetti, whose dedication, experience, and expertise succeeded in transforming a small company producing a range of equipment for hotels into a solid and structured business that now has as many as 6 diverse production lines: furnishings, trolleys, pastry-bakery, self-service, refrigeration, and extractor hoods.
"Our production lines," explains production manager Alessandro Baietta, the second generation at the helm of the company alongside his brother Michele, who in turn presides over and coordinates various commercial activities, "are aimed at producing everything required to set up and fit stainless steel kitchens, canteens, hospitals. In short, everything for the public restaurant and catering industry, but specifically solutions designed to maximize efficiency and reduce energy consumption, while also boosting performance to enable maximum hygiene in the kitchen"
Production operations are supported and sustained by two sales offices operating on both Italian and foreign markets, fluent in 4 languages, in synergy with a sales network of more than 1,400 selected and approved partners in over 50 countries. This vast and diversified customer portfolio boasts a wide range of solutions and product types, the manufacture of which includes some high-performance plants from Prima Power.
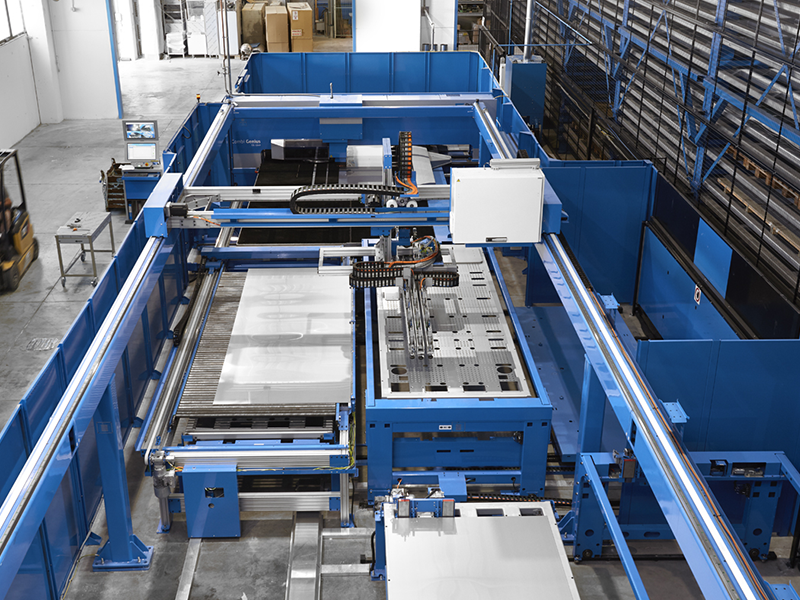
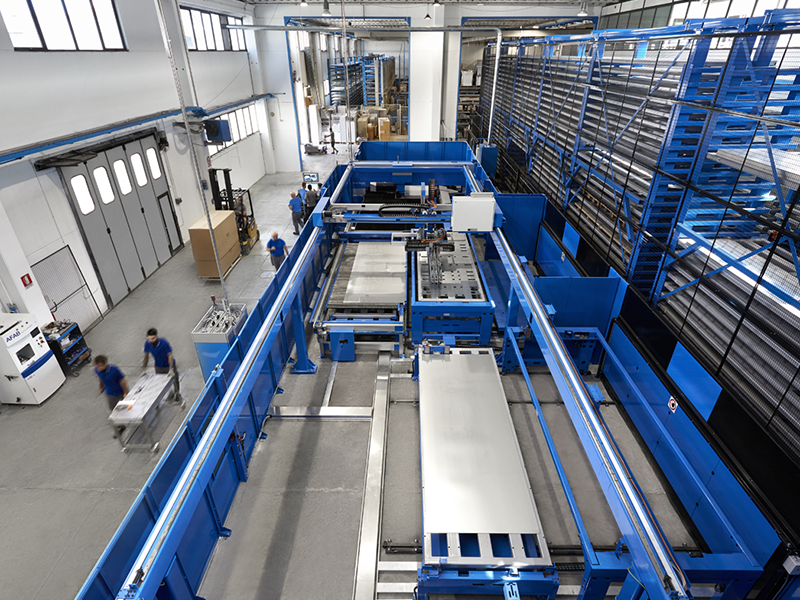
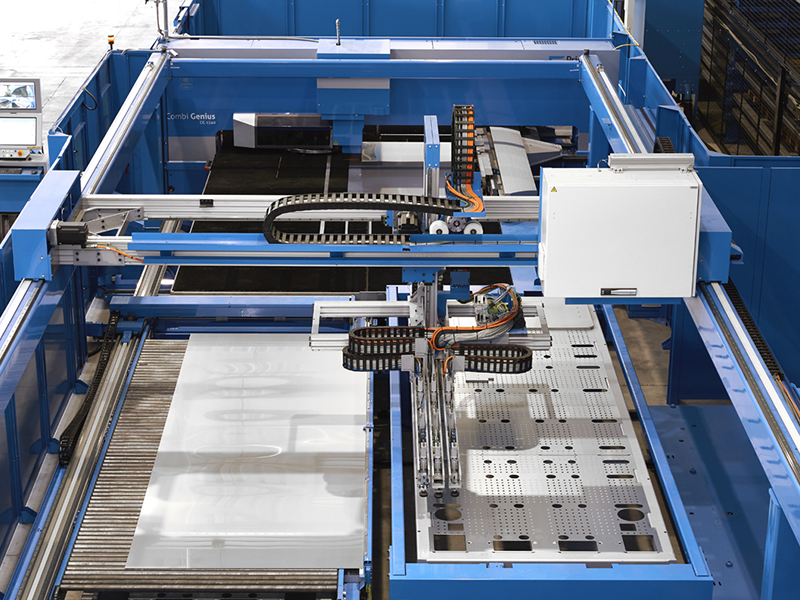
PRODUCTION QUALITY REQUIREMENTS ACHIEVED
What motivated you to acquire process technologies from Prima Power and what were the goals in terms of added value for your business?
"We chose Prima Power," says Baietta, "because it was our goal to optimize our production process with machinery, or rather a production system, that would allow us to maintain an increasingly high quality standard while giving us the speed required to cope with the high volume of orders we process daily. On top of that, we specifically wanted to adhere to all requirements of Industry 4.0 as part of our innovation process, so that we would be able to support the company's growth in an even more organized and efficient way."
Undoubtedly taking on the star role in process management at the company's production facility is the Night Train FMS automated storage solution, which is connected to an integrated Combi Genius 1540 punching/laser cutting system with CF 3000 fiber laser as well as LSR loading, unloading and stacking robots.
The integrated Combi Genius system uses numerically controlled servo-electric axes, with low energy consumption, limited maintenance requirements, and quick operation. Its high productivity is based on a large number of installable tools that are quick and easy to set up. The fiber laser has a very high throughput and is great for processing materials up to 8 mm thickness. The high precision of servo-electric technology, forming and the many auxiliary processes that have been made possible by the customized tower design all ensure high performance while also avoiding any scratches or other imperfections on the material at Metaltecnica.
The company also has an EBe5 servo-electric panel bender, supplied by Prima, which guarantees the bending quality required in the manufacture of industrial and design parts. Optimized axis control has made this possible: a fast and smooth bending process with versatile programming. The use of servo motors also effectively removes the influence of environmental heat conditions in which the machinery operates.
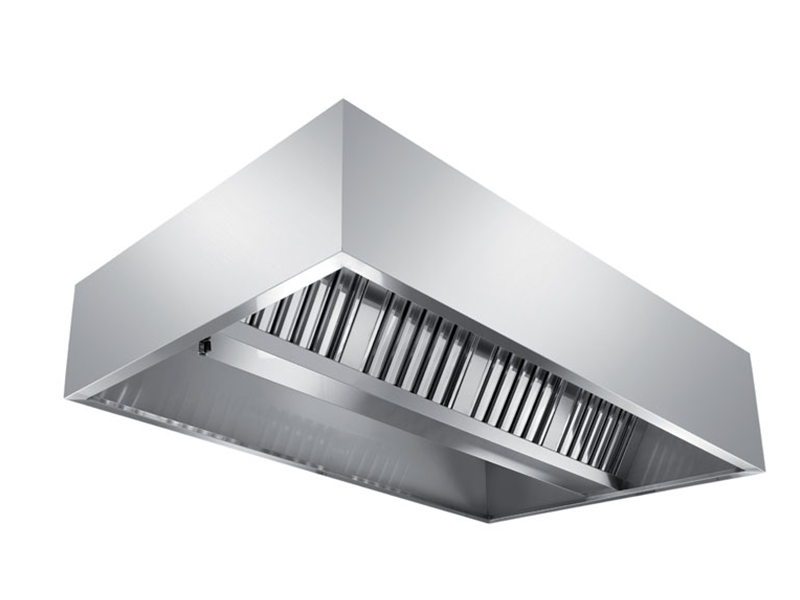
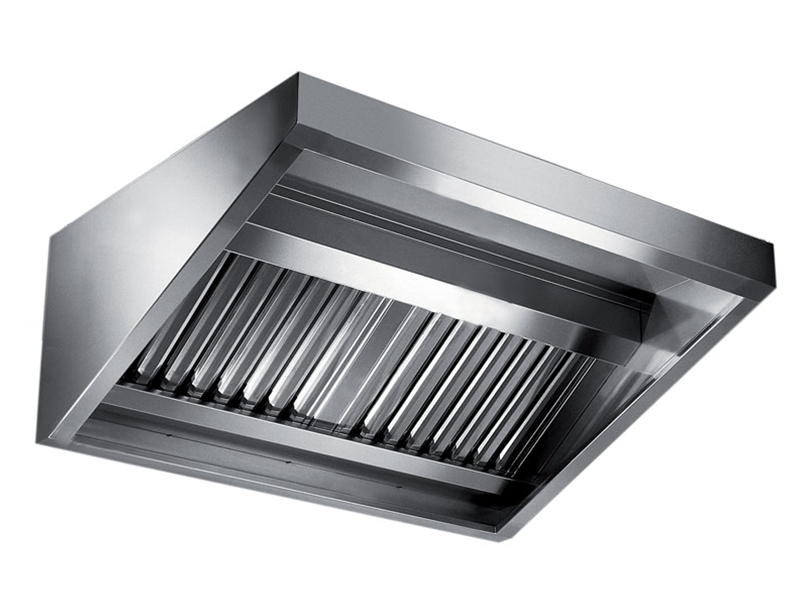
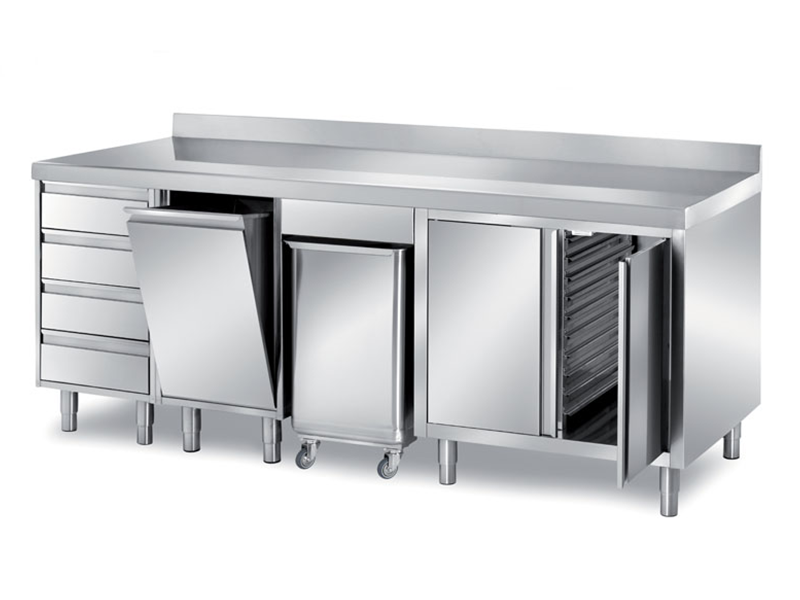
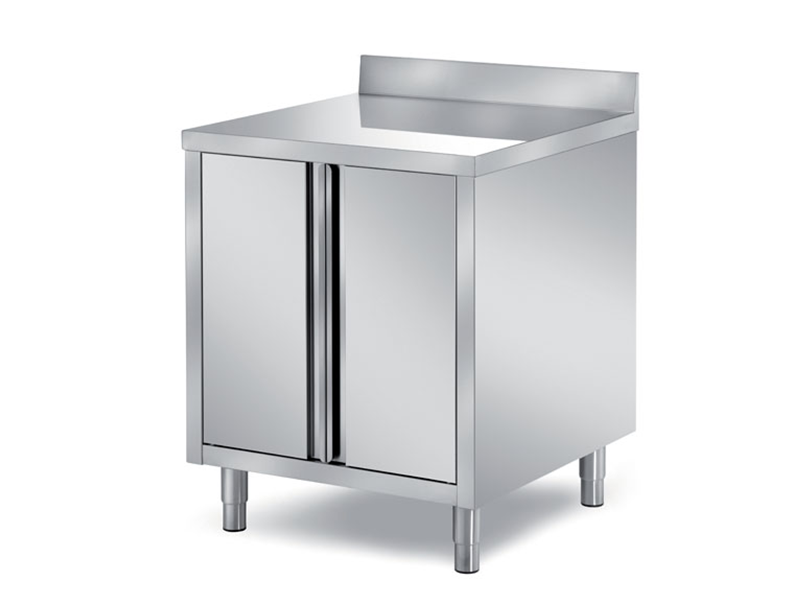
MULTIPLE PROCESSES IN A SINGLE SYSTEM
Which machine strengths are most valued and why?
"The technological equipment we got from Prima Power," Baietta concludes, "I believe manifests a deliberate, targeted, forward-looking and profitable choice from every angle. On the whole, the machines ensure process flexibility and productivity. In the former case, the undisputed added value lies in the fact that we can perform multiple processes with a single system. In the latter case of productivity, small batches, customization and mass production can be processed and optimized for scheduled times and resources."
As is evident, Metaltecnica has invested and continues to invest in cutting-edge sheet metal processing machinery to be able to guarantee high precision and even faster production times.
The technological equipment we got from Prima Power, I believe manifests a deliberate, targeted, forward-looking and profitable choice from every angle. The machines ensure process flexibility and productivity. In the former case, the undisputed added value lies in the fact that we can perform multiple processes with a single system. In the latter case of productivity, small batches, customization and mass production can be processed and optimized for scheduled times and resources.
Are you looking for a similar solution for your company? Find it here
Combi Genius
MASZYNY KOMBI DO WYKRAWANIA I CIĘCIA LASEROWEGO
Wykrawanie + Cięcie laserowe = Większa ekonomiczność produkcji
1+1>2
Urządzenie do załadunku i stertowania (LSR)
PRZEMIESZCZANIE MATERIAŁU
Robot do przemieszczania materiałów i detali dla wielofunkcyjnych maszyn laserowych i do wykrawania
Night Train FMS®
ELASTYCZNE SYSTEMY PRODUKCYJNE FMS