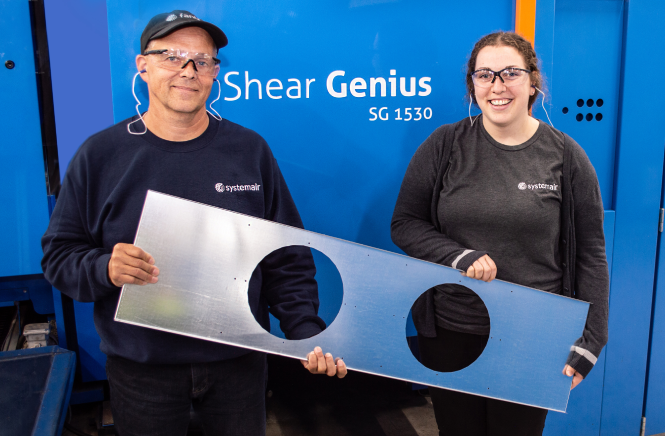
Systemair | A 30-year partnership yielding exceptional production milestones
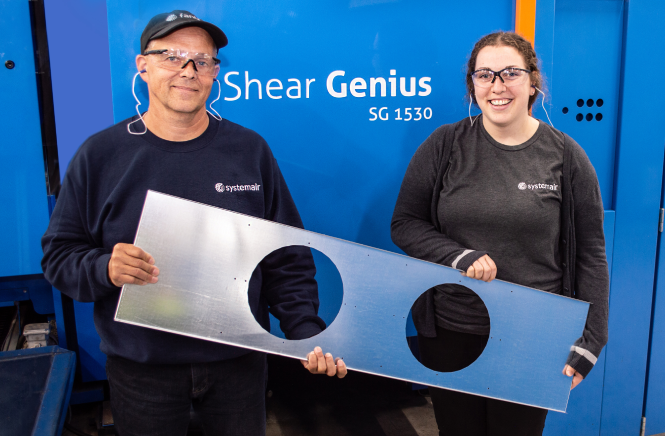
A leading global supplier of high-quality ventilation, heating, and cooling products and systems, Systemair’s extensive product range is a key element in its success story. Headquartered in Sweden, the company has operations in 51 countries in Europe, North America, the Middle East, Asia, Australia, and Africa.
Systemair’s relationship with Prima Power can be traced to 1994 when the first punching/shearing Shear Genius cell with automatic stacking was delivered to Systemair Denmark (previously Danvent A/S). Over the years, this close cooperation thrived with new investments, machine transfers, service, and training. Today, Prima Power equipment serves many of the company’s 26 factories across 18 countries.
THE CHOICE TO EVOLVE BY INTEGRATION
Systemair’s two factories in Canada – one in Tillonsburg, Ontario and one in Bouctouche, New Brunswick – use identical Prima Power Shear Genius (SG) cells and Express Bender (EBe) automated benders, integrated into a PSBB (Punching, Shearing, Buffering, Bending) flexible manufacturing line. The Systemair facility in New Brunswick purchased its first Shear Genius in 2007. According to Ron Gallant, fabrication/maintenance manager: “A strong demand for additional production capacity led the company to purchase a system composed of a new servo-electric Shear Genius and an EBe automated bender in 2018. We also added Prima Power servo-electric press brakes in 2012, 2014, and two more this year.” Today, the 13,000-square-foot Systemair facility in New Brunswick employs 220 workers and is currently running at full capacity.
“We are now operating 24 hours per day with our current equipment,” notes Sylvie LeBlanc, production manager.
UNLOCKING PRODUCTION POTENTIAL WITH SHEAR GENIUS
With the Shear Genius concept, the goal is to provide a machine capable of transforming a full-size sheet into finished parts. These parts can be moved to the final production stages for direct integration into the final product assembly. The Shear Genius (SGe) can perform the most demanding jobs with minimal set-up times and lights-out unmanned operations, thus increasing material productivity through efficient and versatile nesting programs.
“Since our parts are fairly square and rectangular in shape, the Shear Genius is ideal for our product line,” explains LeBlanc.
“We have different products that require many diverse tools, and having the three Multi-Tools and the auto-index stations allows us to produce a variety of designs. From an engineering standpoint, we don’t feel limited. Today, we are challenging engineering a little bit more to increase our throughput.”
The SGe eliminates wasteful skeletons and costly secondary operations, such as deburring; the same clamps that hold the sheet for punching also hold it for shearing. “The Shear Genius is a big advantage,” continues LeBlanc. “It has eliminated shaker parts and tabs by producing a finished part ready for stacking and bending without the need for secondary operations.”
In essence, the Shear Genius allows the automated process to begin with a full-sized sheet of material and end with a finished part after automated loading, punching, forming, shearing, and unloading – all in one operation.
“The Shear Genius allows us to run lights-out over the weekend and have parts ready for bending by Monday morning,” adds Gallant. “We also purchased a coil feeder in 2018 to load both Shear Genius cells. This saves us 15-20% on metal, not counting labor and material handling savings.”
EXPRESS BENDER: IT’S A BENDING REVOLUTION
The servo-electric Express Bender is a bending solution designed to enable each production’s requirements to achieve maximum productivity, quality, and repeatability. EBe provides the high bending quality required by demanding applications with fully automated bending operations, from loading flat-punched parts to unloading the finished product. Systemair’s EBe features a PCD (picking and centering device) and a multi-functional table for positioning and centering parts.
“Today, a part takes 30 seconds to set up with the Express Bender, while it took 10-15 minutes on the press brake,” says Gallant,“and we achieve more consistent quality with the panel bender. It also allows us to do precision hemming on our doors.”
TAKING THE EFFICIENCY LEAP WITH PRIMA POWER
“We gained 50% additional capacity with the Prima Power Shear Genius & EBe Express Bender system,” notes LeBlanc. “This purchase allowed us to grow 20% per year over the past five years. We were able to double our production.”
“We have enjoyed a very good relationship with Prima Power,” concludes LeBlanc. “Prima Power technology has allowed us to produce a lot more and grow as a company, but also, from an employee standpoint, to work safely and more comfortably.”
The Prima Power Shear Genius & EBe Express Bender system allowed us to grow 20% per year over the past five years. We were able to double our production.
KOMBINERADE STANS- OCH KLIPPMASKINER
Expertis inom integration
Kundfokuserad strategi
Snabba, flexibla lösningar
© PRIMA INDUSTRIE S.p.A., single-member company | Via Torino-Pianezza, 36 - 10093 COLLEGNO (TO) ITALIA | Share Capital €26.208.185 | VAT 03736080015 - C.C.I.A.A. Torino 582421 | Reg. Impr. Torino n. 03736080015