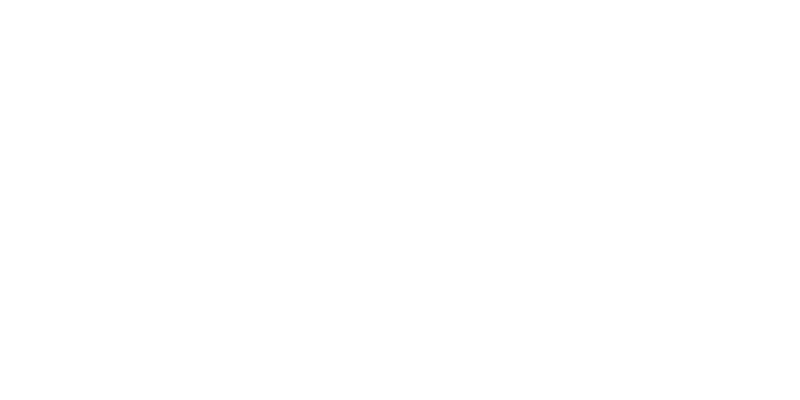
Fortschrittliche Laser erfüllen vielfältige Anforderungen der Tooling Group - Diversified Tooling
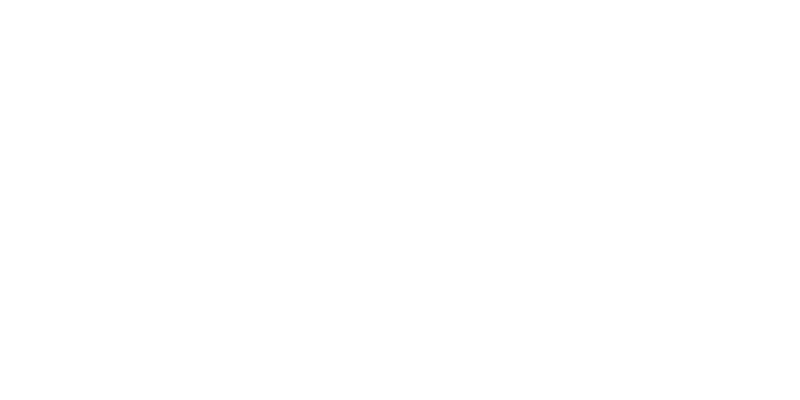
Die fortschrittliche Lasertechnologie hat dazu beigetragen, dass die vier verbundenen Unternehmen der Diversified Tooling Group (DTG), Madison Heights, Michigan, zu einem führenden Anbieter von Fertigungslösungen aus einer Hand für die Automobil-, Schwerlast-, Verteidigungs-, Industrieausrüstungs-, Energieerzeugungs-, Eisenbahn- und Gießereiindustriegeworden sind.
Wie der Name schon andeutet, umfasst das breit gefächerte Leistungsspektrum von DTG die Herstellung von Stanzwerkzeugen für die Prototypen- und Serienfertigung, die Produktion von Stanzteilen und Baugruppen in kleinen Stückzahlen sowie die Fertigung, Bearbeitung und Montage von hochentwickelten Komponenten.
DTG ist ein privat geführtes Unternehmen mit einem Management in der dritten Generation. „1973 begann mein Vater dieses Geschäft in einer kleinen 465 m2 großen Werkstatt mit drei Mitarbeitern, die Hilfsmittel für Kopierwerke und Stanzwerkzeuge herstellten“, sagt John J. Basso, Eigentümer und Präsident. „Ich kam 1975 an Bord. Heute ist mein Sohn John Michael Basso ebenfalls Eigentümer und Vizepräsident des Unternehmens, und wir sind auf vier Unternehmen mit insgesamt 775.000 ft2 (72.000 m²) Konstruktions- und Fertigungsfläche und 425 hochqualifizierten Mitarbeitern gewachsen.“
Zu den vier angeschlossenen Unternehmender Diversified Tooling Group gehören Superior Cam, Midland Design, Bespro Pattern Inc. und American Tooling Center Inc. Durch die Integration dieser vier Unternehmen ist DTG in der Lage, seinen Kunden einen kompletten Werkzeug- und Matrizenservice zu bieten. „Die Prototypen werden bei Superior Cam hergestellt, die Entwürfe für die Produktionswerkzeuge werden bei Midland Design angefertigt. Die Muster werden bei Bespro Pattern hergestellt, und die Produktionsstempel werden von American Tooling Center gefertigt. Und diese Werkzeuge werden an die großen nordamerikanischen Automobilhersteller verkauft“, so Mike Austin, Director of Manufacturing Engineering.
„Wir sind ein Tier-1-Werkzeuglieferant. Die meisten Teile, die wir heute mit unseren Werkzeugen herstellen, sind die großen Klasse-A-Teile, also die sichtbaren Teile eines Autos oder eines schweren LKWs, bei denen eine hohe Oberflächenqualität gefordert ist“, so Austin. „Der andere Teil unseres Geschäfts ist im Verteidigungssektor angesiedelt. Wir sind vor 20 Jahren in das Verteidigungsgeschäft eingestiegen, um unser Geschäft abzurunden und Überkapazitäten zu nutzen, die im Werkzeug- und Formenbau naturgemäß entstehen. Wir begannen mit der Herstellung der Teile, die in Bodenverteidigungsfahrzeuge eingebaut werden sollten. Wir begannen mit der Herstellung von Panzerplatten und schweren Blechen. Und das war für uns eine der ersten Anwendungen beim Laserschneiden mit Prima Power. Da wir dünnere Stahlbleche lieferten, die in verschiedenen Verteidigungsfahrzeugen eingesetzt werden sollten, benötigten wir einen 2D-Laserschnitt. Und wir brauchten auch einen Laser für das 3D-Laserschneiden zum Beschneiden und Durchbohren.“
Im Laufe der Jahre hatten sich die DTG-Unternehmen mit den Lasern von Prima Power North America, Arlington Heights, Illinois, vertraut gemacht, darunter ein frühes Modell des Laserdyne, zwei Platino 2D-Laser, vier Rapido 3D-Laser und zuletzt zwei Laser Next Fünf-Achsen-Laser.
„2014 brauchten wir einen großen und schnellen Fünf-Achsen-Laser zur Unterstützung unserer Heißprägepresse“, sagt Basso. „Als wir die Maschinen evaluierten, verglichen wir den Prima Power Laser Next mit den konkurrierenden fünfachsigen Maschinen und dem Roboter-Laserschneiden. Wir testeten jede dieser Maschinen auf die Einfachheit der Einrichtung, die Einfachheit der Programmierung, die Genauigkeit des Schneidens, wie schnell wir den Zuschnitt machen konnten, die Einfachheit der Wartung, die Unterstützung durch die Hersteller, das technische Niveau der Maschine und die Gesamtzykluszeit der Maschine. Ausgewählt wurde die Laser Next, weil sie die Konkurrenz in fast jeder Kategorie klar geschlagen hat“, so Basso.
DTG besuchte in diesem Jahr die FABTECH-Messe und kaufte die ersten Laser Next, die in Nordamerika verkauft wurde , und installierte sie bei American Tool Center. „Nachdem wir die Laser Next 1530 installiert hatten und sie für die Erprobung und Entwicklung des Prozesses einsetzten, waren wir erstaunt, wie schnell die Maschine war“, so Austin.
„Sie war Lichtjahre jenseits von allem, was wir uns erträumt hatten. In Bezug auf die Leistung brauchte der Roboter über zwei Minuten, um das Teil zu schneiden, der konkurrierende Fünf-Achsen-Laser brauchte über eine Minute, um das Teil zu schneiden. Die Laser Next schneidet es in 45 Sekunden. Dieser Leistungsunterschied hat die Entscheidung über den Haufen geworfen. Das und die langjährige Zusammenarbeit mit Prima Power machten uns die Entscheidung leicht“, sagt er.
PrimaPower hat die Laser Next entwickelt, um die Anforderungen der Automobilproduktion an spezielle Produkte zum Schneiden von Blechteilen zu erfüllen. Die Laser Next maximiert die Maschinenverfügbarkeit, indem sie die Wartung vereinfacht und reduziert, um Nebenzeiten und den Bedarf an spezialisierten Ressourcen für diese Tätigkeiten zu verringern.
Die Laser Next hat einen Arbeitsbereich von 3.050 x 1.530 x 612 mm und ist wahlweise mit einem 3 oder 4 kW hochbrillanten Faserlaser ausgestattet. Seine kompakte Kopffokussierung ist für besten Schutz vollständig umhüllt. Zu den Merkmalen gehören direkt angetriebene Motoren, ein doppelt geschütztes Safe Impact Protection System (SIPS), ein vollmetallischer Sensor und die Fokuspositionskontrolle. Der hochpräzise und dynamische Drehtisch mit Servomotor und Absolutwertgeber ist laut Prima Power auf höchste Zuverlässigkeit, Sicherheit und Ergonomie ausgelegt. Bei den Blockierzeiten ist der Abstand zwischen Tisch und Lichtvorhängen kurz, was schnellere und komfortablere Be-/Entladevorgänge bei voller Sicherheit ermöglicht.
Bei DTG, so Austin, wird die Laser Next 1530 hauptsächlich für den Heißprägeteil des Unternehmens eingesetzt, einschließlich F&E-Arbeiten, Prototypenarbeit, Produktionswerkzeugerprobung und Prozessentwicklung, einschließlich Laserschneidentwicklung und Kleinserienproduktion.
„Wir haben von der Laser Next 1530 gelernt, dass der Drehtisch ein großer Vorteil ist, um die verlorene Zeit beim Be- und Entladen zu minimieren. Die Maschine steht zum Be- und Entladen der Teile nur minimal still. Unsere Kosten für das Laserschneiden hängen sehr stark davon ab, dass der Strahl in Betrieb bleibt. Es ist sehr selten, dass man sie ohne Werkzeuge auf beiden Seiten des Tisches laufen sieht, damit wir die Be- und Entladezeit minimieren“, sagt Austin.
„Bei American Tooling Center schneidet die Laser Next 1530 einige exotische Materialien mit hohem Gewicht“, sagt Basso. „Das Hauptaugenmerk liegt auf dem Material für die Heißprägung, das eine andere Stahlsorte ist. Diese Maschine hat den Geschwindigkeitsanforderungen standgehalten. Alle Heißprägeteile müssen zwangsläufig mit dem Laser beschnitten werden. Sie können keine Trimmstempel verwenden. Diese Maschine hat sich bei der ganzen Produktion, die wir haben, hervorragend bewährt“, sagt er.
Im Jahr 2016benötigte ein anderes DTG-Unternehmen, Superior Cam, einen sehr großen Fünf-Achsen-Laser, um Prototypen von Karosserieseiten zu erstellen. „Wir haben eine Laser Next 2130 mit größerem Arbeitsbereich gekauft , um den Anforderungen des Auftrags gerecht zu werden“, so Basso. „Unsere beiden Laser Next-Maschinen sind langlebig und zuverlässig, und die Geschwindigkeit und Genauigkeit sind hervorragend. Es gab nur sehr wenige Ausfallzeiten. Sie sind sehr zuverlässig gelaufen.“ Laut Frank Delkov, Werksleiter von Superior Cam, hatte das Unternehmen vor der Laser Next 2130 zwei CO2-Laser in der Produktion von Türbaugruppen für einen LKW der Klasse A. „Wir hatten eine Maschine, die linke Türausgänge herstellte, und eine andere Maschine, die rechte Türausgänge herstellte. Wir haben diesen Auftrag auf die Laser Next 2130 verlagert.“
„Wir fertigen jetzt sowohl den linken als auch den rechten Türausgang in einer Vorrichtung an der Laser Next. Was uns über drei Minuten pro Türöffnung gekostet hat, dauert jetzt 30 Sekunden“, sagt Delkov. „Die Verbesserung der Produktivität war enorm“, fügte er hinzu.
"Die Schnittqualität ist exzellent und wir machen das mit nichts anderem als Hochdruck-Werkstattluft. Es werden keine Spezialgase benötigt. Das ist großartig. Es ist einfach, effektiv und die Qualität ist ausgezeichnet. Die Laser Next ist auch eine bedienerfreundliche Maschine. Wir führen alle unsere Schulungen intern zwischen unseren Bedienern durch; innerhalb weniger Wochen können wir jemanden aus dem Betrieb nehmen und ihn an die Laser Next arbeiten lassen.“
„Die Genauigkeit, Wiederholbarkeit und Präzision der Laser Next haben es uns ermöglicht, einige Matrizen und Stanzformen durch Laserschneiden zu ersetzen“, so Basso. „Das macht den Prozess für unsere Kunden wettbewerbsfähiger. In vielen Fällen beliefern wir unsere Kunden mit Teilen und Werkzeugen, die es ihnen ermöglichen, Teile in kleinen Stückzahlen zu fertigen, die sie sonst nicht herstellen könnten. Einige dieser Teile sind Kaltprägeteile und andere sind Warmprägeteile, aber ohne das Laserschneiden könnten wir uns die Werkzeuge zur Herstellung dieser Teile nicht leisten. Das Laserschneiden in Kombination mit der präzisen und wiederholgenauen Prima Power Laser Next 2130 und 1530 ermöglicht es uns, die Werkzeugkosten für Beschnitt- und Stanzwerkzeuge für Kaltstanzteile zu eliminieren und so die Investitionen für die Kleinserienfertigung zu reduzieren. Die Produktionskosten sind vergleichbar mit einem Werkzeug-Komplettprozess“, erklärt Basso.
„Dies hat uns neue Geschäftsfelder in den Bereichen Automobil, LKW, Verteidigung und Spezialitäteneröffnet. Es ist ein Fertigungsverfahren, das wir bisher nur für Prototypen verwendet haben. Und wenn neue Prozesse eingeführt werden, wissen wir, dass Prima Power uns unterstützen wird“, so Basso abschließend.
Wir führen jetzt sowohl die linke als auch die rechte Türaußenseite in einer Vorrichtung auf dem Laser Next. Was uns pro Türaußenseite über drei Minuten gekostet hat, dauert jetzt 30 Sekunden. Die Produktivitätssteigerung war enorm!