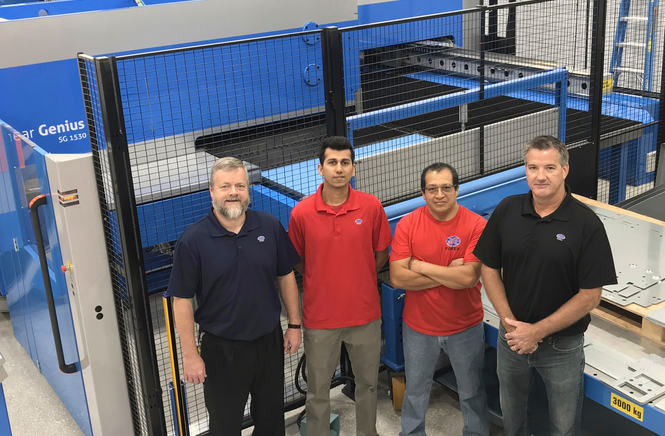
JST Power Equipment, having the right facilities to say ‘yes’ to clients is priceless.
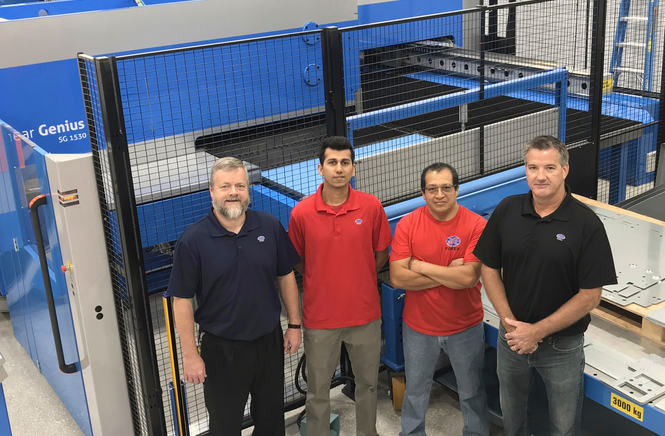
Switchgear lineups are engineered-to-order products with a lot of variation among jobs, including fabricated sheet metal parts. Enabling the new JST Power Equipment switchgear-manufacturing plant to excel at taking on low-volume production: an automated punch-shear combination machine.
Traditionally a manufacturer of transformers, JST Power Equipment has spent the last several months charging up a new manufacturing location in Lake Mary, FL, to produce a new product line: air-insulated switchgear. The firm, originally located in New Jersey and also operating transformer and switchgear-production facilities in Mexico and China, sought to make the Florida plant as vertically integrated as possible. That project landed squarely in the hands of Mark Smith, vice president of operations.
Smith joined JST in July 2020 with the assignment to formulate a plan for the initial startup operation at the Lake Mary facility. This included purchasing updated fabrication capabilities.
“Part of my scope in 2020 was to decide how big the expansion needed to be,” recalls Smith. “In my previous positions with other companies, I’ve had experience with both fully integrated manufacturers and a company with absolutely no vertical integration."
“Today, our facility here in Florida is completely vertically integrated, ensuring product quality while reducing lead times,” explains Smith. “Our sheet metal capabilities include punching, shearing, forming, bending and powder coating.”
ON THE FLOOR: CNC PUNCH-SHEAR COMBO AND ELECTRIC PRESS BRAKE
Smith began his efforts by conducting weeks of research and hosting several meetings with equipment manufacturers to evaluate fabricating- equipment capabilities for the plant’s sheet metal fabrication shop—a new 6000-sq.-ft. addition to the existing 57,000-sq.-ft. building the firm acquired in 2019. Soon after, he led the JST management team’s efforts to purchase a servo-electric punch-shear combination machine (a Shear Genius from Prima Power) equipped with a Prima Power Combo Tower for metal-sheet storage. Also on the docket: a Prima Power model eP-Press servo-electric press brake.
“Prior to building up our fabrication department, we outsourced sheet metal work overseas,” Smith says. “The development cycle back then for bringing a new product to market—as significant as our new switchgear project—lasted 5 to 8 years."
“In this case, leveraging the new fabrication department,” Smith continues, “we were able to roll out the new product line in just 14 months. Switchgear are engineered-to-order products; there’s a lot of variation from job to job, and that variation normally affects just a handful of fabricated-steel components, which doesn’t interest too many contract fabricators. The same holds true for rapid-prototyping work. Our new sheet metal fabrication equipment allows us to excel at taking the low-volume and rapid-prototyping work away from our sub-suppliers, so that we don’t disrupt their operations.”
PUNCH-SHEAR COMBO MAKES QUICK WORK OF FULL SHEETS
With the Shear Genius concept, the objective is to provide equipment capable of transforming a full-sized sheet into finished parts. These parts can be moved to the final production stages for immediate integration directly with the final switchgear assembly.
At the heart of the Shear Genius SGe: an updated servo-electric 30-metric-ton punching machine with 1000-hits/min. stroke speed, 250-rpm index speed and 150 m/min. sheet-positioning speed. The right-angle shear features a servo-electric actuation system, which delivers quick, fully CNC-controlled shear movement. The machine can shear mild steel sheet to 4 mm thick, aluminum to 5 mm, and stainless steel to 3 mm. Automatic loading has been integrated, along with programmable and automatic part removal and part sorting.
“We also appreciate the ability to take SolidWorks CAD files straight to the machine,” Smith adds, “and not have to always program offline. This dramatically improves our flexibility to get us out of binds. While we of course can program the machine offline—for nesting and to optimize sheet utilization—we don’t have to. If we need a part immediately, we can take the SolidWorks drawing to the machine and make the part. We like that a lot. Speed to market, and the ability to say ‘yes’ to our customers is priceless. That’s why we invested in the combination machine rather than purchase separate machines. So many manufacturers, when their customer needs something special, they say ‘no.’ We want to say ‘yes’ to our customers, regardless of their needs.”
The SGe eliminates wasteful skeletons and costly secondary operations such as deburring. Nibbled edges on the part exteriors are eliminated through the use of the integrated right-angle shear. Full sheets—4 by 8 or 5 by 10 ft.—are retrieved automatically from the storage tower and loaded and squared in the machine, without human intervention, ensuring accuracy. And, the same clamps that hold the sheet for punching also hold it for shearing.
As loading, punching, forming and upforming on the punch-shear combo become automated, as well as unloading, sorting and stacking, the result is finished parts with little to no scrap, minimal manual labor and optimum productivity.
“Another really nice feature is the upforming capability, for forming louvers and other features,” adds machine operator Milton Fuentes. “We have specialty tooling for those operations.”
“In essence,” Smith says, “the Shear Genius allows the automated process to begin with a full-sized sheet of matrial and end with a finished part after automated loading, punching, forming, shearing and unloading–all in one operation.”
“We don’t have to shake the parts out or deal with a skeleton, which is a huge plus for me,” says Fuentes. “It also has a very tight footprint, which was really important to us.”
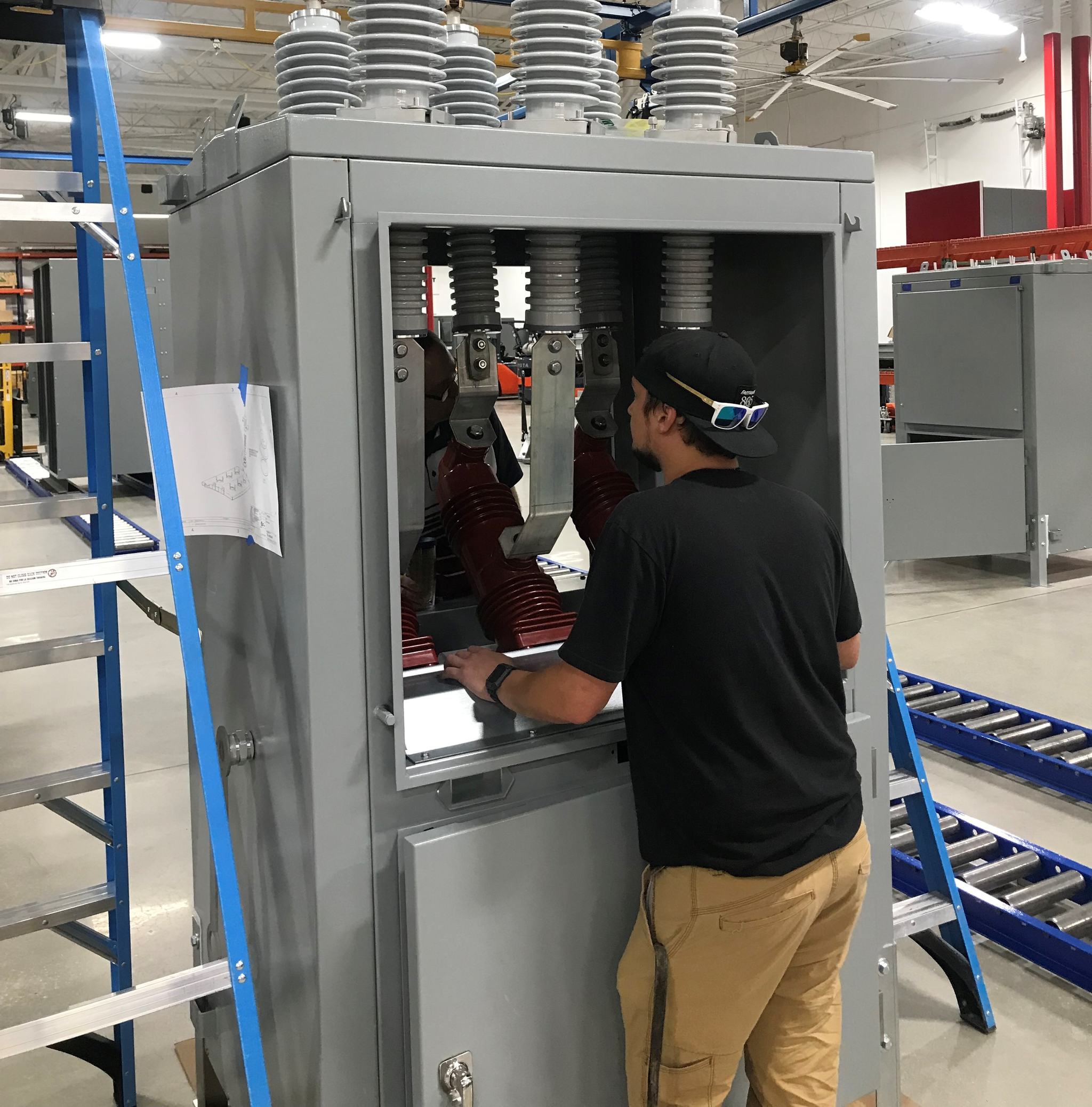
PERFECT COMPLEMENTS: COMBO TOWER, SERVO-ELECTRIC PRESS BRAKE
The 10-station Combo Tower allows JST to store several gauges of galvanized cold-rolled steel, stainless steel and aluminum.
“It’s a great space savings and ideal for material tracking. It paid for itself very quickly,” Smith says. Overall, the SGe and Combo Tower “have shortened dramatically our lead time to market,” continues Smith. “We now can go from concept to prototype in a matter of hours, while our vendor lead times during Covid stretched from 6 to 8 weeks. Having this inhouse capability has allowed us to stay on schedule for a number of deadlines.”
Meanwhile, downstream from the automated punch-shear machine, virtually every piece the highly productive cell fabricates makes its way to the Prima Power eP-series press brake. Smith credits the brake for being able to keep up with the constant flow of parts, due to the high acceleration, deceleration and fast response times from its servo-electric drive system.
“Compared to the conventional hydraulic press brakes I’m used to,” Smith says, “the quick setup, operating speed and quality from the electric press brake results in considerably greater productivity with reduced cycle times.”
The press brake, an eP 1336 model, features backgauge upgrades from Prima Power that the firm says optimize system rigidity, including a steel frame (rather than aluminum), a double-hardened linear guide for the Z axis and a double guide on the X axis. Smith opted to include the optional bending follower with the brake to avoid the need for an extra operator when bending larger parts and help to ensure bend-angle accuracy.
Technical specs: 130 tons of bending force, 144-in. bed length with 155 in. between side frames. Bend-angle accuracy and consistency are optimized due to the pulley-belt system driving the press brake, actuated by servo drives and distributing bending force over the entire bending length. The system consists of fixed and moving rolls spread out over the total working length of the upper beam. Servo-motor drives offer superior movement control and accuracy. And, Smith opted to add the CNC crowning option to compensate for lower-frame deflection during bending.
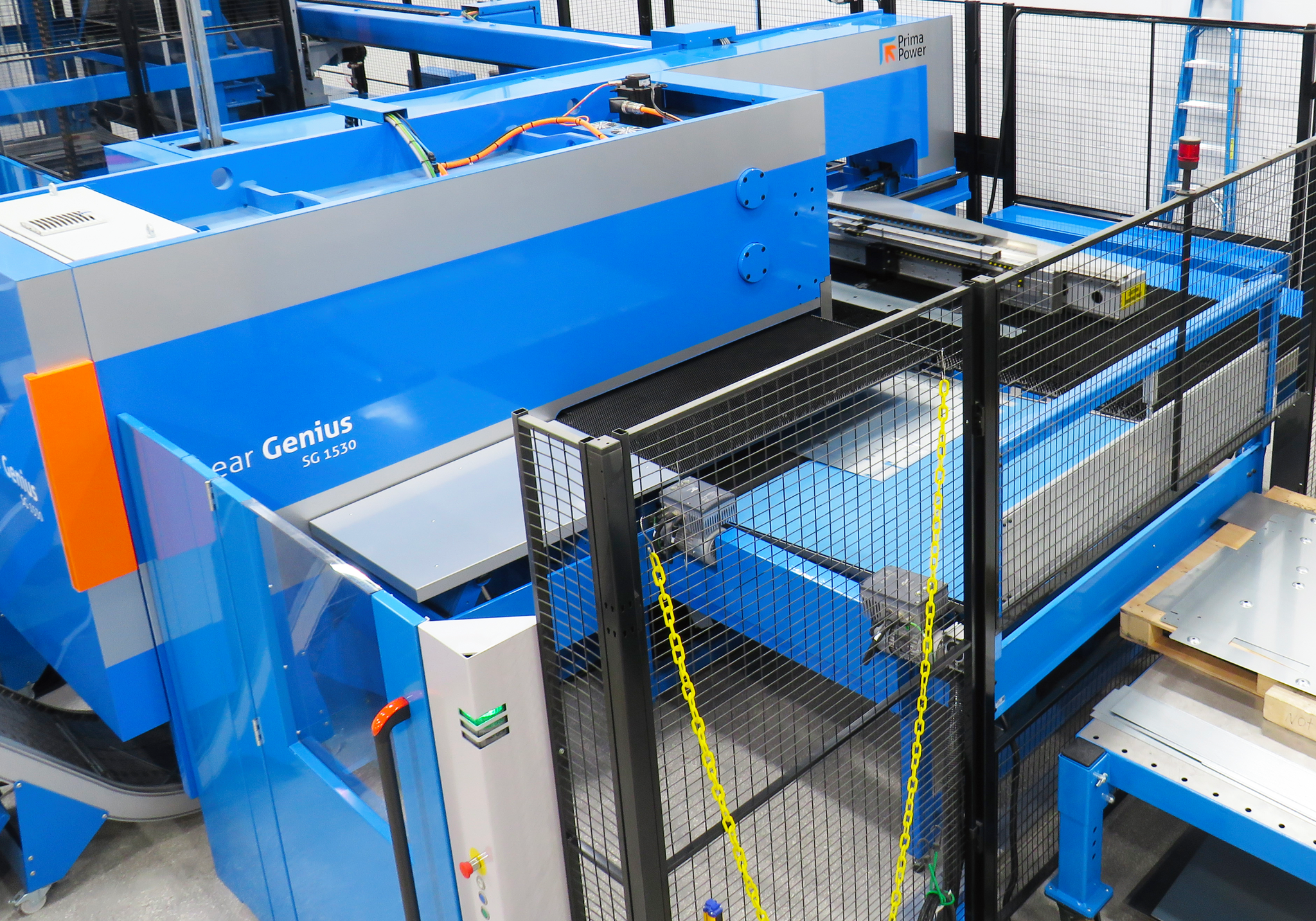
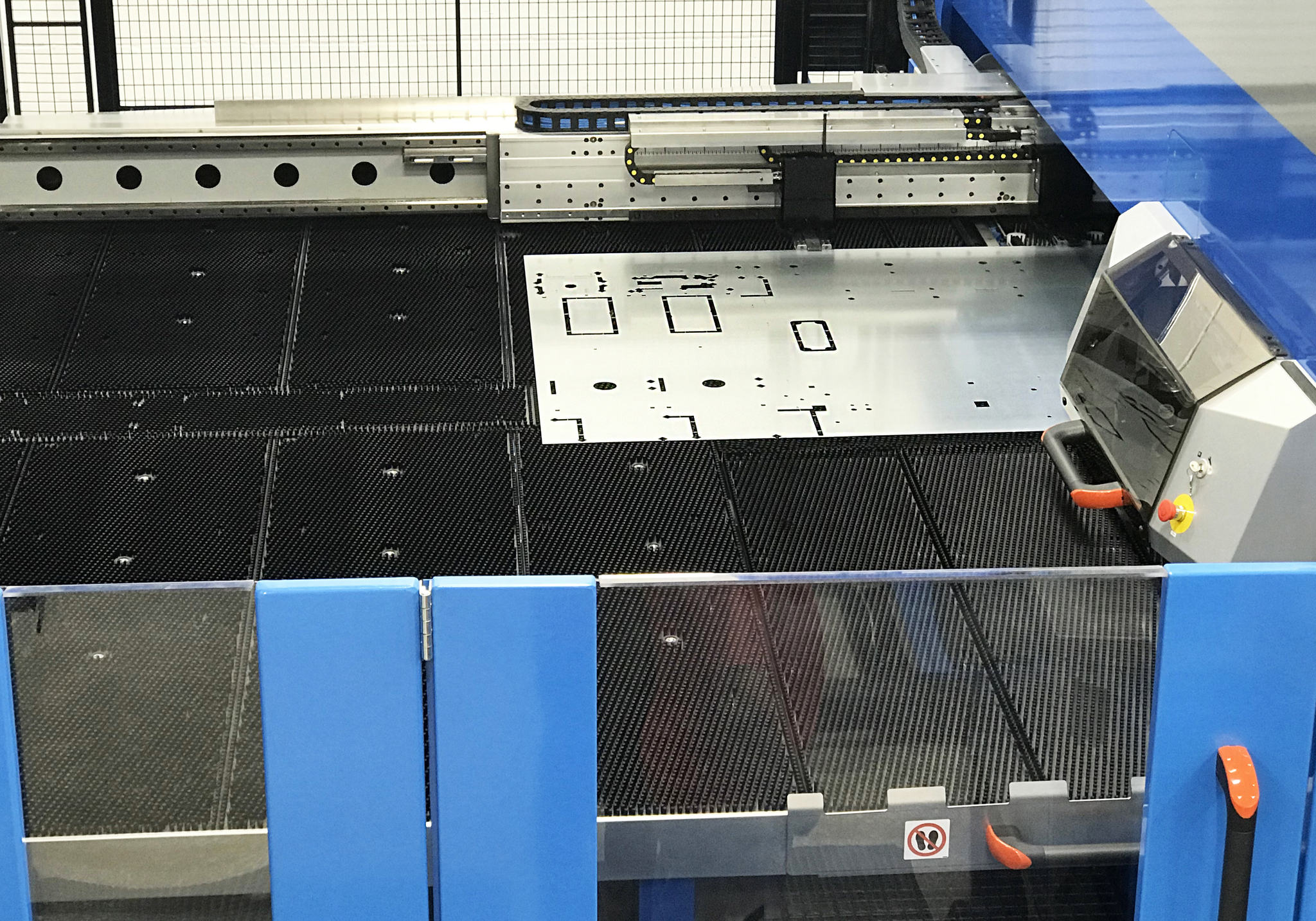
Prima Power eP-series brakes also feature a rigid O-frame design to help ensure tool alignment even under stress deformation, as there is no horizontal displacement. The position of the upper beam, in relation to the lower beam, is measured by dual Y1 and Y2 linear encoders attached independently of the machine frame, and which are bed-referenced. This design, according to Prima Power, isolates ram-positioning accuracy from any deflection in the side frames under load and maintains accurate positioning even during off-center bending operations. Ram repeatability: ±0.005 mm.
“We’re able to combine small, segmented 100- or 200-mm dies to custom lengths, rather than handling larger dies, “Smith says, “which greatly reduces setup time compared to having to completely remove a large die section and replace it with another die to accommodate a new setup. And, we get first-part quality,no scrapped parts with each setup. I’m used to throwing away the first part during every setup."
“Our new sheet metal fabrication equipment allows us to handle the low-volume production, the one-piece parts and all of the late engineering changes common to the switch-gear industry,” concludes Smith. “We designed our fab shop to handle the custom and quickdemand prototyping portion of our business. Every job we build is custom. We knew going in that we were not looking for high utilization and a quick return on investment. We wanted the capabilities.”
Overall, the SGe and Combo Tower have shortened dramatically our lead time to market. Having this in-house capability has allowed us to stay on schedule for a number of deadlines.