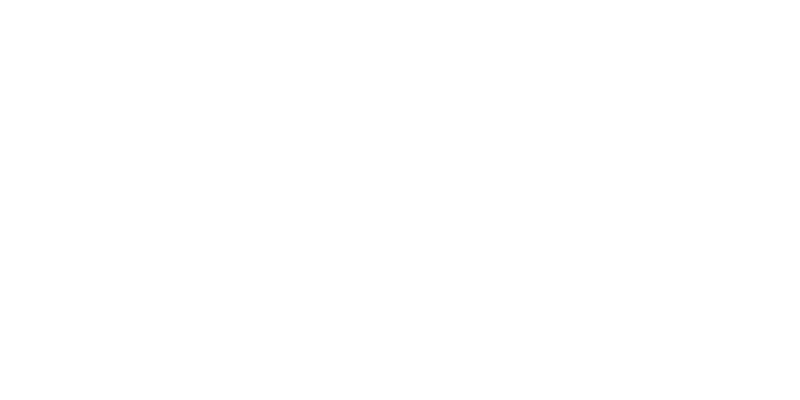
Взгляд на технологии, лежащие в основе решений для органического птицеводства под ключ
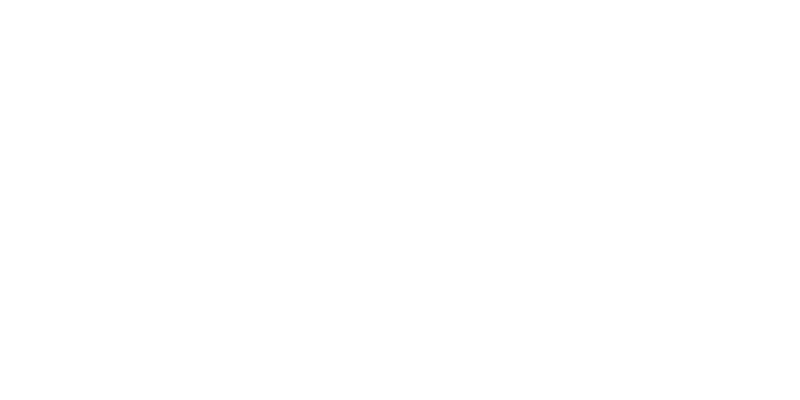
Компания SKA srl занимается производством птицеводческих систем для разведения органических кур свободного выгула, разрабатывая проект в полном соответствии с пожеланиями клиентов и используя преимущества инновационных технологий Prima Power.
Автоматизированная складская система Night Train, подключенная к комбинированной установке пробивки и гильотинной резки Shear Genius и роботизированной комплексной системе гибки, состоящей из панелегиба Fast Bend FBe и листогибочного пресса EP 1030, которые все вместе являются ключевыми элементами разноплановой производственной деятельности, требующей высокой производительности и эффективности, а также гибкости и универсальности для оперативного управления и контроля за любыми изменениями продукции.
Сколько раз вы представляли себе классический фермерский дом со счастливыми курами, копошащимися на скотном дворе, когда покупали яйца с органической фермы в супермаркете? Лично я думаю об этом каждый раз, когда читаю такую формулировку на упаковке. Однако реальность очень отличается от этого идиллического образа, даже если это, к счастью, не так уж далеко от истины, по крайней мере, с точки зрения благополучия животных. Это связано с работой тех, кто, как и компания SKA, всегда занимался производством современного инновационного оборудования для птицеводства и кролиководства. У такой производственной среды на вид довольно простые производственные потребности, но, как мы увидим ниже, ей также приходится иметь дело с целым рядом проблем при обработке деталей из листового металла, а это совсем не тривиально. Данные проблемы являются результатом восхитительного филантропического подхода, направленного на то, чтобы дистанцироваться от всего, что хотя бы отдаленно связано с концепцией интенсивного фермерского хозяйства. Подобное решение привело компанию Sandrigo из провинции Виченца к тому, что она активно занялась автоматизацией производственных процессов, которую они считают единственным эффективным способом адекватно реагировать на потребности в индивидуализации продукции, предлагая при этом превосходное качество. Это также организовано и обеспечено технологическим партнером, которого они выбрали десять лет назад: Prima Power.
Птицефабрики под ключ
Начнем с того, что компания SKA srl работает в секторе птицеводства с 1954 года и производит всё, что связано с органическим сельским хозяйством, а с 2011 года после приобретения компании Meneghin из Тревизо также занимается производством оборудования для кролиководства. Решение заниматься исключительно сельскохозяйственным оборудованием для органического фермерского хозяйства на протяжении многих лет сделало компанию SKA авторитетным ориентиром для ведущих итальянских и международных групп, и вместе с тем оказало непосредственную поддержку небольшим фермам.
«С момента основания мы всегда шли против течения по сравнению со многими другими компаниями в этом секторе, и благодаря традиционной склонности к индивидуализации птицефабрик, нам удалось отличиться и со временем построить высокотехнологичную бизнес-структуру, всегда оставаясь рядом с фермерами-животноводами», – сказал Дино Поццато, председатель группы SKA.
«Прямой диалог с клиентом позволил нам накопить успешный опыт в управлении агропредприятиями, занимающимися органическим фермерским хозяйством, и в решении связанных с ними проблем. Наши системы кормления, поения, освещения и кондиционирования воздуха, например, разработаны с учетом благополучия животных и действующих нормативных требований. Материалы долговечны и гигиеничны, а компоненты оборудования легко доступны для тщательной очистки. Благодаря широкому ассортименту продукции, подходящей для бройлеров, кур-несушек, индеек и племенных птиц, а также уток и перепелов, мы можем удовлетворить любые потребности».
Эффективное управление и контроль за любыми изменениями продукции
Каким образом компания SKA связана с Prima Power? Совершенно очевидно, если задуматься о том, сколько компонентов из листового металла имеется на птицефабрике. Однако проблемы обработки, связанные с высоким уровнем индивидуализации продукции и решением работать только с органическим птицеводством и соблюдением этических принципов обращения с животными, банальны и очевидны. Как нам пояснил Диего Поццато, директор завода SKA: «Мы предлагаем полный комплекс услуг под ключ, от птичника до внутренних систем, продуманных и разработанных до мельчайших деталей. Мы можем эффективно поддерживать наших фермеров-животноводов, помогая им находить конкретные ответы и решения для каждой потребности. Мы собираем практические данные и выполняем структурные расчеты для составления технических чертежей, одновременно делясь каждым шагом с клиентом и рекомендуя определенное оборудование, работая над поиском наиболее подходящего решения на основе эталонных стандартов и типа сельхозпредприятия. Наша цель – сделать управление более функциональным и повысить производительность. Наше собственное техническое бюро обеспечивает немедленный переход от разработки продукта к его изготовлению.
Однако, преимущественное изготовление объектов и оборудования, специально предназначенных для органического сельского хозяйства, снижает их количество по сравнению с интенсивным фермерским хозяйством. При этом качество превыше количества, а благополучие животных важнее чисто экономических интересов, поскольку в нем задействовано гораздо меньшее количество животных. Следовательно, устройства и оборудование, которые должны быть изготовлены для такого сельхозпредприятия, также различны; это означает, что мы производим большое количество серий, но меньшими партиями, чем можно было бы подумать. Нужно быть достаточно гибкими, чтобы производить то, что требуется конкретным птицеводам, поскольку учитывается большое количество переменных, в зависимости от типа кур, которые будут выращиваться, и размер которых, например, будет определять выбор оборудования для оснащения. Это означает, что наше производство должно быть высокоэффективным и производительным, а также гибким и универсальным для оперативного управления и контроля за любыми изменениями продукции».
Взаимовыгодное сотрудничество, укрепившееся со временем
Компания SKA является давним клиентом Prima Power. Все началось с приобретения в 1998 году координатно-пробивного пресса F5 с устройством загрузки/выгрузки, а затем компания совершила эволюционный скачок, перейдя на комбинированную установку пробивки и гильотинной резки Shear Genius, которая затем была подключена к автоматизированной складской системе Night Train. Недавно они также подключили роботизированный комплекс для гибки, состоящий из панелегиба Fast Bend FBe 5, листогибочного пресса EP 1030 и антропоморфного робота.
«С 1998 года мы неизменно выбираем Prima Power,» – повторил Диего Поццато. «Мы были первопроходцами в использовании их координатно-пробивного пресса F5, который мы затем заменили в 2011 году на нынешнюю комбинированную установку SGe6. Затем в 2017 году мы добавили к ней автоматизированную складскую систему Night Train, а в 2019 году роботизированный комплекс для гибки. В настоящее время мы оцениваем возможность включения системы лазерной резки в нашу гибкую производственную систему, которая станет наилучшим дополнением к нашему оборудованию и удовлетворит наши потребности в обработке листового металла, даже несмотря на то, что у нас уже есть непрерывный, оптимизированный и эффективный технологический процесс, спроектированный и налаженный совместно с компанией Prima Power. Конкретный пример – роботизированная ячейка для гибки, которую мы установили в начале 2020 года; мы начали с мысли о покупке автоматизированного станка для изготовления панелей, но на этапе оценки мы поняли, что это не самое идеальное решение для нашей задачи. Поэтому мы выбрали такое решение, которое наилучшим образом сочетает в себе потенциал эффективного сервоэлектрического панелегиба и современного электрического гибочного пресса, что позволяет нам выполнять все операции обработки в кратчайшие сроки и наиболее эффективно благодаря сочетанию обеих технологий.»
Максимальная производительность обработки
Компания SKA всегда верила в автоматизацию производственных процессов, что считается единственным способом эффективной организации производства с высокой степенью индивидуализации продукции. Действительно, наше производство характеризуется большим числом серий, но небольшими объемами партий. «Речь идет, конечно, не о 15 экземплярах, но и не о 100000 единиц», – сказал Диего Поццато. Таким образом, необходимость в автоматизации этапа гибки главным образом возникает из-за того, что универсальность и производительность комбинированной установки Shear Genius в сочетании со складской системой Night Train создают своего рода узкое место на этапе резки и штамповки деталей.
«Раньше с системами, которые мы использовали,» – пояснил Диего Поццато, – «мы могли легко осуществлять гибку около 60% нашей продукции, фактически создавая узкое место. Поскольку цель заключалась в достижении того непрерывного, плавного и эффективного производственного потока, о котором мы говорили ранее, мы решили восполнить этот пробел, производя недостающие 40% с помощью системы такого типа. Оптимальное сочетание двух технологий гибки теперь гарантирует нам феноменальные показатели обработки, поскольку покрывает 100% наших потребностей в гибке. Это невероятно эффективное и интересное решение, в котором две разные системы гибки работают вместе для производства деталей; панелегиб справляется с тем, чего не может гибочный пресс, и наоборот. Это обеспечивает наилучшее исполнение различных деталей. Большим преимуществом является то, что вся система управляется в автономном режиме; это означает, что техническое бюро может планировать производство во время холостого хода, пока ячейка занимается изготовлением. То есть, время простоя сведено к минимуму, а производительность обработки действительно максимальна.»
Два станка, интегрированные в ячейку, могут работать последовательно или параллельно, в том смысле, что антропоморфный робот может управлять работой обоих станков одновременно, обеспечивая доработку детали на гибочном прессе после того, как она была частично изготовлена на панелегибе, либо он может управлять одним из двух станков в то время, как другой работает параллельно в режиме ручного управления. Таким образом, это очень гибкое решение, где станция выгрузки перемещает паллету, поступающую из накопителя складской системы Night Train, в котором хранятся полуфабрикаты. Следовательно, полуфабрикат подается не напрямую от установки Shear Genius, а всегда от накопителя, так что даже здесь обеспечивается максимальная гибкость в управлении технологическим процессом. Так называемый этап вырубки не обязательно должен сопровождаться последующей гибкой именно потому, что в середине находится накопитель, который действует как буфер для сбора деталей, поступающих от других станков в цехе.
Интегрированная роботизированная система гибки
«Повышенная эффективность интегрированной роботизированной системы гибки Prima Power, принятой компанией SKA, определяется именно простой и быстрой автономной программируемостью станков и робота, включенных в ячейку, особенности функционирования которой были исключительно важным поворотным моментом для отрасли, когда она была представлена в 2018 году», – сказал Роберто де Росси, старший менеджер по коммерческому развитию в области обработки тонкого листового металла компании Prima Power. «Это решение, которое позволяет получить максимальную выгоду от вложений, поскольку эффективность системы гарантирована при производстве как небольших, так и более крупных партий. Это затрагивает еще одну задачу, которую компания SKA поставила перед нами в качестве цели, а именно оптимальное управление двумя ветвями основного производства. «Их производство характеризуется выпуском повторяющихся элементов, которые ежегодно выпускаются в больших количествах согласно регулярному недельному графику или иному графику, составленному на весь год, путем запуска изготовления оптимальных и повторяющихся партий. Однако, имеется и другая часть производства, где небольшими партиями выпускается продукция, специально разработанная в соответствии с конкретными производственными потребностями отдельно взятого клиента.
Поэтому, чтобы придать заводу большую гибкость, мы также предусмотрели возможность эксплуатации станков традиционным способом, позволяя роботу изготавливать повторяющиеся детали и использовать станки в автономном режиме для выполнения обработки в режиме ручного управления. Это представляло еще одну проблему, поскольку нам пришлось разрешить доступ в ячейку несмотря на присутствие робота, отвечающего за работу обоих станков.
Воспользовавшись тем фактом, что станки расположены бок о бок, мы разработали решение, которое по сути также является автоматическим, когда робот может перемещаться (седьмая ось робота) по 19-метровой направляющей, встроенной в основание на полу. Это означает, что отсек, в котором робот перемещается по направляющей, также может быть закрыт при необходимости, позволяя оператору получить доступ к тому или иному станку для устранения неисправности или предотвращения любой чрезвычайной ситуации, которая может возникнуть во время производства. В данном конкретном случае речь идет об очень малых количествах деталей, где робот не давал бы большого дополнительного преимущества. Интересно то, что при необходимости робот сам подготовится и автоматически закроет колею крышками люков. Дополнительный элемент эксплуатационной гибкости заключается в том, что панелегиб FBe 5 может использоваться в режиме ручного управления в то время, когда пресс eP 1030 работает автоматически под управлением робота, обрабатывая мелкие детали, складываемые внавалку в контейнере и отслеживаемые системой визуального распознавания отдельной детали.
Гибочный пресс зависит от панелегиба, а не наоборот
В настоящее время ясно, что в компании SKA всегда обеспечивается оптимальное управление производством благодаря множеству функций, предоставляемых автоматизированной складской системой Night Train. Это то, что составляет реальную основу всей ГПС, вокруг которой сосредоточены различные комплексы Prima Power, автоматизированные ячейки и все другие производственные участки цеха. Что касается работы роботизированного комплекса для гибки, то каков тот определяющий фактор, по которому система или тот, кто программирует систему, решает, которые детали изготавливаются с помощью гибочного пресса, а которые – с помощью панелегиба, или даже те детали, которые изготавливаются поочередно с помощью обоих станков для получения готового изделия? Диего Поццато ответил следующее: «Панелегиб является самым удобным из двух станков, поскольку он гарантирует непревзойденную скорость гибки; однако, для изготовления некоторых профилей, например, С-образных профилей с особо высокими полками, гибочный пресс является единственно возможным вариантом. Следовательно, это зависит от формы, которую требуется получить, и ее размеров. Наше техническое бюро работает над «перепроектированием» различных проектов, отдавая предпочтение панелегибу или, по крайней мере, изучая, какие формы обеспечивают максимальную эффективность взаимодействия между двумя станками, учитывая при этом тот факт, что гибочный пресс eP 1030 зависит от панелегиба и наоборот. Панелегиб Fast Bend по-прежнему остается предпочтительным средством для повышения производительности и гибкости. Неудивительно, что наши первоначальные рассуждения касались одного автоматического панелегиба, а не интегрированной роботизированной ячейки для гибки, ныне установленной у нас. Мы пришли к такому выводу только после глубокого и детального исследования, проведенного совместно с Prima Power. Оно показало, что панелегиб не способен полностью покрыть наши технологические потребности. Из-за своей формы некоторые детали невозможно было полностью согнуть с помощью панелегиба Fast Bend, поэтому мы решили добавить потенциал и универсальность электрического гибочного пресса».
И гибочный пресс, и панелегиб оснащены сервоэлектрическим приводом. Это важный аспект по двум причинам: сниженное энергопотребление и, прежде всего, абсолютная точность и повторяемость, которые они обеспечивают при обработке.
Панелегиб с ручным управлением и роботизированной загрузкой/выгрузкой
Выбор панелегиба Fast Bend FBe 5 был обусловлен нашим сотрудничеством с компанией SKA,» – пояснил Кристиано Поррати, менеджер компании Prima Power по работе с партнерами в странах Южной Европы. «Поскольку многие детали серийного производства имеют узкую форму, это не позволяет в полной мере использовать манипулятор с захватным устройством, который характерен для обычных панелегибов, поэтому требовалось что-то другое. Выбор пал на тот, который наилучшим образом характеризует нас в этом технологическом сегменте, являясь наиболее универсальным из всех и обладая такой особенностью, как манипулятор с вакуумными присосками, что было очень важно для компании SKA. На начальном этапе анализа и исследования стало понятно, что панелегиб Fast Bend может быть наиболее подходящим станком для продукции компании SKA, но он был «ограничен» ручной блокировкой. Действительно, панелегиб Fast Bend обладает довольно ограниченной автоматизацией, поскольку он только перемещает детали, не поворачивая их, операции загрузки и выгрузки обычно являются прерогативой оператора, которого в данном конкретном случае заменили антропоморфным роботом. Это означает, что FastBend становится полностью автоматическим. Робот свободно перемещается перед станком по 19-метровой направляющей, что позволяет ему охватить как гибочный пресс, так и панелегиб, а также легко достигать любой из трех платформ выгрузки согнутых изделий с несколькими секциями для паллет, где он может размещать изделия, предназначенные для данной секции.
Компоновка включает магазин для сменных устройств, захватывающих детали. Их робот меняет в полностью автономном режиме в соответствии с перечнем изготавливаемой продукции, который был удаленно составлен техническим бюро. Эта очередь на обработку может отправлена непосредственно на панелегиб, который благодаря развитой ИТ-инфраструктуре и программному обеспечению управления предприятием может вызвать паллету из накопителя складской системы Night Train с полуфабрикатами, необходимыми конкретно для этой партии продукции, а затем запустить программу с использованием робота, который начнет работать с ними, как ожидалось, перемещая их для обработки на панелегиб или листогибочный пресс, а затем складывая готовые детали.»
Замыкает этот круг лазерная резка
Компания SKA всегда была в авангарде инноваций; поэтому неудивительно, что она уже нацелена на дальнейший рост, который позволит ей превратиться в полномасштабного интеллектуального производителя, соответствующего критериям концепции Индустрия 4.0, всего за несколько лет. «Мы уже работаем и занимаемся подготовкой как на аппаратном, так и на программном уровне для управления всем производством в целом», – говорит Диего Поццато. «На этот счет я хотел бы подчеркнуть, что все установленные системы Prima Power готовы к Индустрии 4.0 и что мы намерены объединить складскую систему Night Train с системой лазерной резки, как упоминалось в начале. Это позволит нам действительно замкнуть круг наших производственных возможностей, поскольку тогда мы даже сможем изготавливать изделия нестандартной формы из нержавеющей стали с той же точностью, что и на установке SG – эти изделия нестандартной формы в настоящее время передаются на аутсорсинг компаниям-партнерам. Shear Genius фактически представляет собой пробивной пресс со встроенными гильотинными ножницами для резки под прямым углом, что лучше всего подходит для изготовления полуфабрикатов квадратной формы. Исходя из того, что складская система останется основой всей производственной системы, новая задача, которую мы намерены решить с Prima Power, состоит в том, чтобы иметь возможность обрабатывать металлические листы сначала на комбинированной установке Shear Genius, выполняя все отверстия и придавая изделиям нужную форму, затем сортировать их для последующей отправки на установку лазерной резки с помощью все той же системы Night Train, перемещающей полуфабрикаты, где они будут подвергнуты лазерной резке и возвращены в накопитель перед последующей отправкой в интегрированную роботизированную ячейку для гибки. Здесь они пройдут завершающий этап обработки путем наилучшего сочетания двух предусмотренных технологий. Мы уверены, что компания Prima Power, используя самое лучшее из своего обширного ассортимента станков и решений по автоматизации для обработки листового металла в сочетании с ее компетенцией и опытом, снова сможет точно понять наши запросы и полностью удовлетворить ожидания нашего технического бюро, с которым всегда было эффективное взаимодействие и сотрудничество».
Большим преимуществом является то, что вся система управляется в автономном режиме; это означает, что техническое бюро может планировать производство во время холостого хода, пока ячейка занимается изготовлением. То есть, время простоя сведено к минимуму, а производительность обработки действительно максимальна
Вы ищете аналогичное решение для вашей компании? Найдите его здесь
Автоматическая система Night Train FMS®
ГИБКИЕ ПРОИЗВОДСТВЕННЫЕ СИСТЕМЫ
Ведущее технологическое решение для безлюдных и гибких производственных систем.
Комбинированный пресс с угловыми ножницами Shear Genius
КОМБИНИРОВАННЫЕ ВЫРУБНЫЕ ПРЕССЫ С УГЛОВЫМИ НОЖНИЦАМИ
Высочайшая производительность благодаря интеграции пробивки и резки ножницами
Роботизированные гибочные ячейки
Роботизированные гибочные ячейки