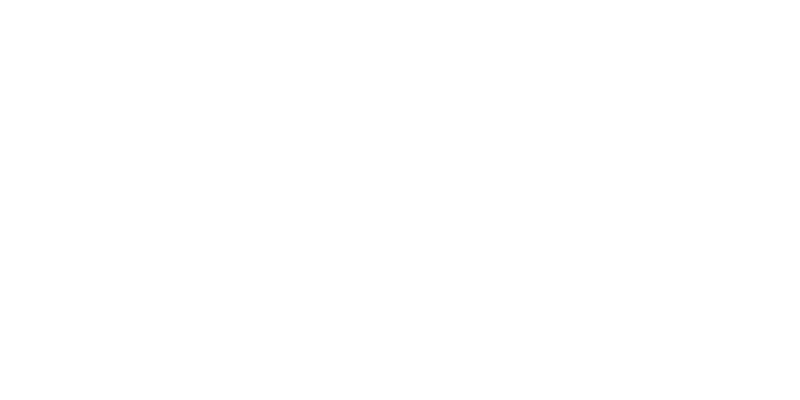
Ein Bick auf die Technologie hinter schlüsselfertigen Bio-Geflügelanlagen
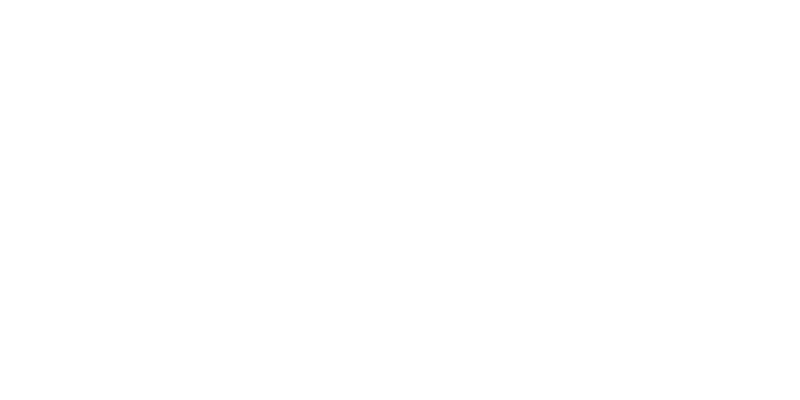
SKA srl fertigt Geflügelsysteme für die ökologische Freilandhaltung mit einem hohen Maß an Produktanpassung durch die Nutzung der innovativen Prima Power Technologie.
Ein automatisches Night Train-Lager, das mit einem kombinierten Shear Genius- und Roboter-Biegesystem, bestehend aus einer Fast Bend FBe Plattenbiegemaschine und einer EP 1030 Abkantpresse, verbunden ist, sind die Eckpfeiler einer abwechslungsreichen Produktion, die hohe Leistung und Produktivität sowie Flexibilität und Vielseitigkeit zur effizienten Bewältigung jeglicher Produktänderungen erfordert.
Wie oft haben Sie sich beim Kauf von Bio-Eiern im Supermarkt schon das klassische Bauernhaus mit glücklichen Hühnern vorgestellt, die im Stall herumscharren? Ich persönlich denke jedes Mal daran, wenn ich diesen Schriftzug auf der Packung gelesen habe. Die Realität unterscheidet sich jedoch stark von diesem idyllischen Bild, auch wenn sie zum Glück zumindest in Bezug auf den Tierschutz nicht allzu weit entfernt ist. Dies ist der Arbeit derjenigen zu verdanken, die sich wie SKA seit jeher mit der Herstellung innovativer Spitzengeräte für die Geflügel- und Kaninchenzucht beschäftigen. Diese Produktionsumgebung hat scheinbar recht einfache Produktionsanforderungen, aber wie wir weiter unten sehen werden, gibt es bei der Bearbeitung von Blechteilen häufig Probleme und diese sind alles andere als trivial. Diese Probleme sind das Ergebnis der bewundernswerten und menschenfreundlichen Entscheidung, Abstand von allem zu schaffen, was auch nur im Entferntesten mit dem Konzept der intensiven Landwirtschaft zu tun hat. Diese Entscheidung führte dazu, dass die Firma Sandrigo aus der Provinz Vicenza stark auf die Automatisierung der Produktionsprozesse setzt, die sie als einzige effektive Möglichkeit ansieht, den Anforderungen der Produktindividualisierung gerecht zu werden und gleichzeitig höchste Qualität zu bieten. Dies wird auch durch den vor zehn Jahren gewählten Technologiepartner kontrolliert und garantiert: Prima Power.
Schlüsselfertige Geflügelanlagen
Beginnen wir damit, dass SKA srl seit 1954 im Bereich der Geflügelanlagen tätig ist und alles produziert, was mit der biologischen Landwirtschaft zu tun hat, und dass sie seit 2011 durch die Übernahme der Firma Meneghin aus Treviso auch Kaninchenzuchtanlagen herstellen. Die Entscheidung, nur und ausschließlich mit biologisch wirtschaftenden Betrieben zu handeln, hat SKA im Laufe der Jahre zu einem maßgeblichen Bezugspunkt für führende italienische und internationale Konzerne gemacht und gleichzeitig eine direkte Unterstützung für kleinere Betriebe ermöglicht.
„Seit unserer Gründung sind wir im Vergleich zu vielen anderen Unternehmen der Branche immer gegen den Strom geschwommen. Dank der traditionellen Berufung, Geflügelanlagen nach Maß zu fertigen, ist es uns gelungen, uns zu unterscheiden und im Laufe der Zeit eine hochtechnologische Unternehmensstruktur aufzubauen, wobei wir immer an der Seite der Züchter standen“, sagt Dino Pozzato, Vorstand der SKA-Gruppe.
„Durch den direkten Dialog mit dem Kunden konnten wir nachweisliche Erfahrungen im Management von Biobetrieben und bei der Lösung der damit verbundenen Probleme sammeln. Unsere Fütterungs-, Tränk-, Beleuchtungs- und Klimatisierungssysteme sind beispielsweise auf das Wohlbefinden der Tiere und die geltenden Vorschriften abgestimmt. Die Materialien sind langlebig und hygienisch, und die Gerätekomponenten sind für eine gründliche Reinigung leicht zugänglich. Dank der breiten Produktpalette, die für Masthähnchen, Legehennen, Puten und Züchter sowie Enten und Wachteln geeignet ist, sind wir in der Lage, jeden Bedarf zu decken“.
Effizientes Management bei jeder Produktänderung
Aber wie ist SKA mit Prima Power verbunden? Es versteht sich von selbst, wenn man bedenkt, wie viele Blechteile es in einer Geflügelanlage gibt. Die Verarbeitungsprobleme durch den hohen Grad der Produktindividualisierung und die Entscheidung, nur biologische und ethische Geflügelhaltung zu beliefern, sind jedoch banal und offensichtlich. Das erklärt uns Diego Pozzato, Werksleiter bei SKA: „Wir bieten einen kompletten schlüsselfertigen Service, vom Stall bis zu den internen Systemen, die bis ins kleinste Detail geplant sind. Wir sind in der Lage, unsere Züchter effizient zu unterstützen, indem wir ihnen helfen, konkrete Antworten und Lösungen für jeden einzelnen Bedarf zu finden. Wir sammeln nützliche Daten und führen statische Berechnungen für technische Zeichnungen durch, während wir jeden Schritt mit dem Kunden teilen und bestimmte Anlagen empfehlen, wobei wir daran arbeiten, die geeignetste Lösung auf der Grundlage der Referenzstandards und der Art des Betriebs zu ermitteln. Unser Ziel ist es, die Handhabung funktionaler zu gestalten und die Produktivität zu steigern. Unser hauseigenes technisches Büro sorgt für einen sofortigen Übergang vom Produktdesign zur Produktion.
Die Herstellung von Anlagen, die speziell für den ökologischen Landbau konzipiert sind, reduziert jedoch die Anzahl im Vergleich zur intensiven Landwirtschaft. Dabei wird die Qualität über die Quantität gestellt und das Wohl der Tiere über das reine wirtschaftliche Interesse gestellt, da es sich um eine viel geringere Anzahl von Tieren handelt. Dementsprechend unterschiedlich sind auch die Geräte und Ausrüstungen, die für eine solche Anlage zu produzieren sind. Das bedeutet, dass wir zwar große Stückzahlen in Serie produzieren, aber mit kleineren Losen, als man meint. Man muss ziemlich flexibel sein, um das zu produzieren, was bestimmte Züchter benötigen, da die involvierten Variablen zahlreich sind, wie die Art der Henne, die aufgezogen werden soll, deren Größe die Wahl der Ausrüstung bestimmen wird, die berücksichtigt werden soll. Das bedeutet, dass unsere Produktion leistungsstark und produktiv sein muss, aber auch flexibel und vielseitig, um alle Produktänderungen effizient zu bewältigen“.
Eine synergetische Beziehung, die sich im Laufe der Zeit konsolidiert
SKA ist ein langjähriger Kunde von Prima Power. Sie begannen 1998 mit einer F5-Stanzmaschine mit Be-/Entladung, bevor sie einen Evolutionssprung machten, indem sie auf eine kombinierte Shear Genius Stanz-Schneide-Maschine umstiegen, die dann mit dem automatischen Night Train-Lager verbunden wurde. Kürzlich haben sie auch eine Roboter-Biegeinsel an das Lager angeschlossen, bestehend aus einer Fast Bend FBe 5 Blechbiegemaschine, einer EP 1030 Abkantpresse und einem anthropomorphen Roboter.
„Seit 1998 fällt unsere Wahl immer wieder auf Prima Power“, erklärt Diego Pozzato weiter. „Wir waren Pioniere bei der Verwendung ihrer F5-Stanzmaschine, die wir dann 2011 durch die aktuelle SGe6 ersetzt haben, zu der wir 2017 die automatische Lagereinheit Night Train und 2019 das integrierte Roboter-Biegesystem hinzugefügt haben. Wir evaluieren derzeit die Aufnahme eines Laserschneidsystems in unser Flexibles Fertigungssystem, das unsere Anforderungen an die Blechbearbeitung am besten ergänzen würde, obwohl wir bereits über einen kontinuierlichen, optimierten und effizienten Arbeitsablauf verfügen, der in Synergie mit Prima Power konzipiert und entwickelt wurde. Das konkrete Beispiel ist die Roboter-Biegezelle, die wir Anfang 2020 installiert haben. Wir begannen mit der Idee, eine automatische Verkleidungsmaschine zu kaufen, aber während der Evaluierungsphase stellten wir fest, dass sie nicht die ideale Lösung für unsere Arbeit war. Deshalb haben wir uns für diese Lösung entschieden, die das Potenzial einer effizienten servoelektrischen Blechbiegemaschine und einer modernen elektrischen Biegemaschine am besten kombiniert - und die es uns aufgrund der Kombination beider Technologien ermöglicht, alle Prozesse in kürzester Zeit und auf die effizienteste Weise durchzuführen.“
Die Prozesseffizienz ist maximal
SKA hat schon immer an die Automatisierung von Produktionsprozessen geglaubt, die als einzig effektiver Weg zur Bewältigung einer hohen Individualisierung angesehen wird. Die Produktion zeichnet sich zwar durch große Serien aus, aber nicht durch riesige Mengen. „Wir reden nicht von 15 Stück, aber auch nicht von 100.000 Stück“, sagt Diego Pozzato. Die Notwendigkeit, die Biegephase in so erheblichem Maße zu automatisieren, ergibt sich daher aus der Tatsache, dass die große Vielseitigkeit und Produktivität der Shear Genius in Verbindung mit der Night Train-Lagereinheit eine Art Engpass nach der Schneide- und Stanzphase der Teile bildete.
„Früher konnten wir mit den von uns verwendeten Systemen“, erklärt Herr Diego Pozzato, „etwa 60 % unserer Produktion leicht biegen, was tatsächlich einen Engpass darstellte. Da das Ziel darin bestand, diesen kontinuierlichen, flüssigen und effizienten Produktionsfluss zu erreichen, über den wir zuvor gesprochen haben, beschlossen wir, diese Lücke zu schließen, indem wir die fehlenden 40 % mit dieser Art von System produzieren. Durch die optimale Kombination der beiden Biegetechnologien garantiert sie uns jetzt einen beispiellosen Betrieb, da sie 100 % unseres Biegebedarfs abdeckt. Es ist eine unglaublich wertvolle und interessante Lösung, bei der zwei verschiedene Biegesysteme zusammenarbeiten, um Teile zu produzieren. Die Blechbiegemaschine erledigt, was die Biegemaschine nicht kann und umgekehrt. Dies gewährleistet die optimale Ausführung der verschiedenen Teile. Der große Vorteil ist, dass das gesamte System offline verwaltet wird, was bedeutet, dass das technische Büro die Produktion parallel planen kann, während die Zelle produziert. Kurzum, die Ausfallzeiten sind auf ein Minimum beschränkt und die Prozesseffizienz ist wirklich maximal.“
Die beiden in der Zelle integrierten Maschinen sind in der Lage, in Serie oder parallel in dem Sinne zu arbeiten, dass der anthropomorphe Roboter beide Maschinen gleichzeitig steuern kann, um sicherzustellen, dass ein Teil auf der Blechbiegemaschine teilweise hergestellt und auf der Biegemaschine fertiggestellt wird, oder er kann eine der beiden Maschinen steuern, während die andere parallel im Handbetrieb arbeitet. Es handelt sich also um eine sehr flexible Lösung, die von einer Ausgabestation mit einem Waggon gespeist wird, der aus dem Night Train-Lager kommt, in dem die Halbfertigprodukte gelagert werden. Es handelt sich also nicht um eine direkte Einspeisung aus der Shear Genius, sondern immer aus der Lagereinheit, so dass auch hier maximale Flexibilität in der Steuerung der Arbeitsabläufe besteht. Die so genannte Stanzphase muss nicht unbedingt mit dem nachfolgenden Biegen abgeglichen werden, denn in der Mitte befindet sich das Lager, das als Puffer für das Sammeln der von anderen Maschinen in der Werkstatt kommenden Teile dient.
Das integrierte Roboter-Biegesystem
„Die gesteigerte Effektivität des integrierten Roboter-Biegesystems von Prima Power, das von SKA übernommen wurde, ergibt sich gerade aus der einfachen und schnellen Offline-Programmierbarkeit der Maschinen und des Roboters, die Bestandteil der Zelle sind und deren Betriebsart, die bei der Präsentation 2018 einen außergewöhnlichen Wendepunkt für die Branche darstellte“, sagt Roberto De Rossi, Senior Manager Business Development Thin Sheet Metal bei Prima Power. „Es ist eine Lösung, mit der Sie maximalen Nutzen aus der Investition ziehen können, da die Effizienz des Systems sowohl für die Produktion kleiner als auch größerer Chargen gewährleistet ist. Dies berührt eine weitere der Herausforderungen, die SKA uns als Ziel gesetzt hat, nämlich die optimale Bewirtschaftung ihres doppelt produktiven Kerns“, erklärt De Rossi. „Ihre Produktion zeichnet sich durch wiederholbare Elemente aus, bei denen es offensichtlich größere Mengen gibt, die jährlich in Abhängigkeit von einem regelmäßigen wöchentlichen Zeitplan produziert werden, oder andere Typen, die über das Jahr verteilt sind, indem sie günstige und wiederholbare Produktionschargen starten. Es gibt jedoch auch einen Teil der Produktion, der die Ausführung von Chargen mit kleineren Mengen erfordert, die ausdrücklich auf die Produktionsrealität des einzelnen Kunden abgestimmt sind.
Um der Anlage mehr Flexibilität zu geben, haben wir daher auch die Möglichkeit vorgesehen, die Maschinen auf herkömmliche Weise zu nutzen, so dass der Roboter wiederholbare Teile erstellen kann und die Maschinen im Standalone-Modus für manuelle Bearbeitungen eingesetzt werden können. Dies war eine weitere Herausforderung, da wir den Zugang zur Zelle trotz der Anwesenheit des Roboters, der für beide Maschinen zuständig ist, ermöglichen mussten.
Unter Ausnutzung der Tatsache, dass die Maschinen nebeneinander stehen, haben wir eine Lösung geschaffen, die auch im Wesentlichen automatisch ist, bei der sich der Roboter (siebte Achse des Roboters) über eine 19 m lange, im Bodenfundament eingebettete Schiene bewegen kann. Das bedeutet, dass das Fach, in das der Roboter gleitet, bei Bedarf auch geschlossen werden kann, so dass der Bediener Zugang zu der einen oder anderen Maschine hat, um sich um eventuelle Notfälle während der Produktion zu kümmern. In diesem speziellen Fall handelt es sich um sehr kleine Mengen, bei denen der Roboter keinen zusätzlichen Nutzen bringen würde. Das Interessante daran ist, dass sich der Roboter bei Bedarf selbst vorbereitet und die Gleisgrube automatisch mit Kanaldeckeln verschließt. Ein weiteres Element der Flexibilität ergibt sich aus der Tatsache, dass eine FBe 5 Blechbiegemaschine manuell eingesetzt werden kann, während die eP 1030 automatisch unter dem Roboter arbeitet, der auch kleinere Teile verarbeiten kann, die als Schüttgut in einen Behälter gelegt werden. Weiter ist ein Visionssystem für die Erkennung des Einzelteils vorhanden.
Die Biegemaschine ist abhängig von der Verkleidungsmaschine und nicht umgekehrt
An dieser Stelle wird deutlich, dass bei SKA aufgrund der vielen Funktionen des Night Train-Lagers stets ein optimales Produktionsmanagement gegeben ist. Das ist der eigentliche Produktionskern des gesamten FMS, um den sich die verschiedenen Prima Power-Inseln, automatischen Zellen und alle anderen Abteilungen der Werkstatt gruppieren. Was ist das Unterscheidungsmerkmal, nach dem das System oder derjenige, der das System programmiert, festlegt, welche Teile mit der Biegemaschine und welche mit der Blechbiegemaschine hergestellt werden, oder sogar, welche Teile beide Maschinen nacheinander verwenden, um die Form zu vervollständigen? Diego Pozzato antwortet: „Die Blechbiegemaschine ist die bequemste der beiden Maschinen, weil sie unschlagbare Biegegeschwindigkeiten garantiert. Bei bestimmten Profilen, wie z. B. "C"-Formen mit besonders hohen Kanten, ist die Biegemaschine jedoch die einzig mögliche Option. Es hängt also von der herzustellenden Form und deren Abmessungen ab. Unser technisches Büro arbeitet daran, die verschiedenen Projekte mit einer Präferenz für die Blechbiegemaschine „umzugestalten“ oder zumindest zu untersuchen, welche Formen die betrieblichen Synergien zwischen zwei Maschinen am besten nutzen, wobei auch die Tatsache berücksichtigt wird, dass die Biegemaschine eP 1030 von der Blechbiegemaschine abhängig ist und umgekehrt. Die Fast Bend Blechbiegemaschine ist immer noch die Waffe der Wahl für Produktivität und Flexibilität. Es überrascht nicht, dass unsere anfänglichen Überlegungen eine einzelne automatische Plattenbiegemaschine betrafen und nicht eine integrierte Roboter-Biegezelle wie die aktuelle. Zu diesem Schluss kamen wir erst nach einer eingehenden und detaillierten Studie, die wir zusammen mit Prima Power durchgeführt haben. Dabei stellte sich heraus, dass die Blechbiegemaschine nicht geeignet war, um unseren Bearbeitungsbedarf vollständig abzudecken. Einige Teile konnten aufgrund ihrer Form nicht vollständig mit der Fast Bend gebogen werden, weshalb wir uns entschieden, das Potenzial und die Vielseitigkeit einer elektrischen Biegemaschine hinzuzufügen“.
Sowohl die Biegemaschine als auch der Blechbiegemaschine werden servoelektrisch betrieben. Dies ist aus zwei Gründen ein wichtiger Aspekt: der reduzierte Energieverbrauch und vor allem die absolute Präzision und Wiederholbarkeit, die sie bei der Verarbeitung gewährleisten.
Eine manuelle Blechbiegemaschine mit robotergestütztem Be- und Entladen
„Die Auswahl der Fast Bend FBe 5 Blechbiegemaschine ist der Synergie zwischen uns und SKA zu verdanken“, erklärt Cristiano Porrati, Prima Power Countries Manager South Europe. „Da viele Teile in der Standardproduktion eine schmale Form haben, die mit dem für „konventionelle“ Blechbiegemaschinen typischen Greifermanipulator nicht gut funktioniert, musste etwas anderes her, und die Wahl fiel auf den, der uns in diesem technologischen Segment am meisten auszeichnet, da er der flexibelste von allen ist und die Besonderheit hat, einen Saugnapfmanipulator zu haben, was für SKA wichtig war. In der ersten Analyse- und Studienphase war klar, dass die Fast Bend die am besten geeignete Maschine für das SKA-Produkt sein könnte, aber sie war durch die manuelle Verriegelung „eingeschränkt“. In der Tat ist die Fast Bend eine Maschine mit recht begrenzter Automatisierung, da sie die Teile nur bewegt und nicht dreht. Be- und Entladevorgänge sind normalerweise das Vorrecht des Bedieners, der in diesem speziellen Fall durch den anthropomorphen Roboter ersetzt wurde. Dies bedeutet, dass die FastBend vollautomatisch wird. Der Roboter bewegt sich frei an der Vorderseite der Maschine entlang seiner 19 m langen Schiene, wodurch er sowohl die Biegemaschine als auch die Blechbiegemaschine abdecken kann. Außerdem erreicht er problemlos jede der drei Entladestationen für gebogenes Material mit mehreren Palettierbereichen, wo er die für diesen Bereich bestimmten Teile ablegen kann.
Das Layout beinhaltet selbstverständlich ein Magazin für Teile zum Greifen, das der Roboter in völliger Autonomie je nach der vom technischen Büro ferngesteuerten Teileproduktionsliste wechselt. Diese Produktionswarteschlange kann direkt an die Verkleidungsmaschine geschickt werden, die dank der entwickelten IT-Infrastruktur und der Software für die Anlagenverwaltung den Waggon mit den für diese bestimmte Produktionscharge benötigten Halbfertigprodukten aus dem Night Train abrufen und dann das Programm über den Roboter starten kann, der sie wie erwartet zu bearbeiten beginnt und sie an die Blechbiegemaschine oder die Abkantpresse delegiert, wo sie verarbeitet und anschließend gestapelt werden.“
Laserschneiden schließt den Kreis
SKA war schon immer ein Vorreiter in Sachen Innovation. Daher ist es nicht verwunderlich, dass das Unternehmen bereits weiteres Wachstum geplant hat, dass es innerhalb weniger Jahre zu einem vollwertigen Smart Manufacturer machen wird, der die Anforderungen des Industrie 4.0-Protokolls erfüllt. „Wir arbeiten bereits daran und bereiten die Dinge sowohl auf Hardware- als auch auf Softwareebene für die Verwaltung der gesamten Produktion vor“, sagt Diego Pozzato. „Zu diesem Thema möchte ich betonen, dass alle installierten Prima Power Systeme „Industrie 4.0 ready“ sind und dass wir, wie eingangs erwähnt, den Night Train mit einer Laserschneidanlage kombinieren wollen. Damit könnten wir den Kreis der Arbeitsmöglichkeiten wirklich schließen, denn wir wären dann sogar in der Lage, unregelmäßige Edelstahlformen mit der gleichen Präzision zu fertigen wie das SG - diese unregelmäßigen Formen werden derzeit an Partnerfirmen ausgelagert. Die Shear Genius ist eigentlich eine Stanzmaschine kombiniert mit einer integrierten Winkelschere, die am besten bei der Produktion von Halbzeugen mit einer regelmäßigen quadratischen Form funktioniert. Ausgehend von der Lagereinheit, die das Herzstück des gesamten Produktionssystems bleiben wird, besteht die neue Herausforderung, die wir bei Prima Power in Angriff nehmen wollen, darin, dass wir in der Lage sein werden, zunächst die Bleche auf der Shear Genius zu bearbeiten, um alle erforderlichen Löcher und Verformungen an den Teilen vorzunehmen, um sie dann zur künftigen Laserschneidanlage zu sortieren, wobei der Night Train immer noch für Halbfabrikate verwendet wird, wo diese geschnitten und erneut gelagert werden, bevor sie an die integrierte Biegezelle geschickt werden. Sie werden dann durch die bestmögliche Kombination der beiden geplanten Technologien fertiggestellt. Wir sind uns sicher, dass Prima Power mit seinem reichhaltigen Angebot an Maschinen und automatischen Lösungen für die Blechbearbeitung in Verbindung mit seiner Kompetenz und Erfahrung erneut in der Lage sein wird, angemessen auf unsere Anfragen zu reagieren und die Erwartungen unseres technischen Büros, mit dem schon immer eine effektive Synergie und Zusammenarbeit bestand, voll zu erfüllen“.
Der große Vorteil ist, dass das gesamte System offline verwaltet wird; das bedeutet, dass das technische Büro die Produktion in maskierter Zeit planen kann, während die Zelle fertigt. Kurzum, Ausfallzeiten werden auf ein Minimum begrenzt und die Prozesseffizienz ist wirklich maximal.
Sie suchen eine ähnliche Lösung für Ihr Unternehmen? Finden Sie es hier
Night Train FMS®
FLEXIBLE FERTIGUNGSSYSTEME
Führende technologische Blechlagerlösung in Kombination mit automatisierten flexiblen Fertigungssystemen
Shear Genius EVO
KOMBINIERTE MASCHINEN ZUM STANZEN UND SCHEREN
Höchste Produktivität durch integriertes Stanzen und Scheren
Roboter-Biegezellen
ROBOTER-BIEGEZELLEN