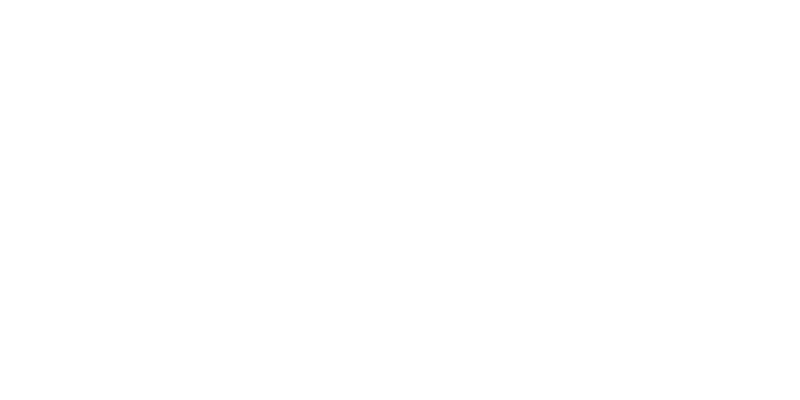
A look at the technology behind turnkey organic poultry plants
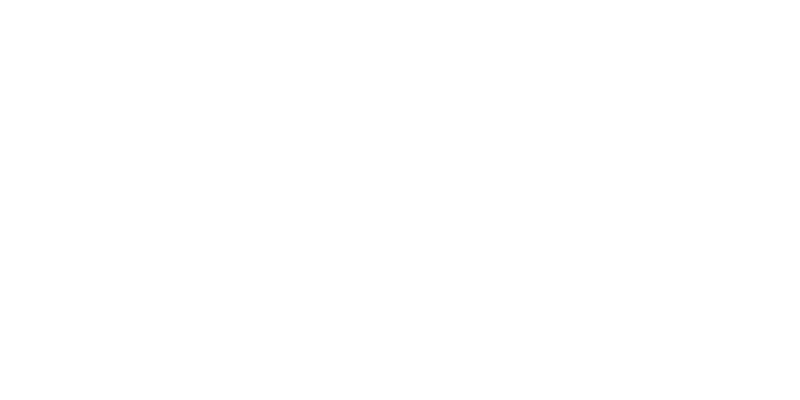
SKA srl manufactures poultry systems for organic free-range farming with high levels of product customisation by taking advantage of innovative Prima Power technology.
A Night Train automatic storage unit connected to a combined Shear Genius and robotic bending system, consisting of a Fast Bend FBe panel bender and an EP 1030 press brake, are the cornerstones of varied production activity which demands high performance and productivity, as well as flexibility and versatility to efficiently manage any product changes.
How many times have you imagined the classic farmhouse with happy hens scratching around in the barnyard when buying organically farmed eggs at the supermarket? Personally, I think about it every time I've read that wording on the package. The reality, however, is very different from that idyllic image even if it’s thankfully not too far away at least in terms of animal welfare. This is due to the work of those who, like SKA, have always been involved in manufacturing innovative cutting-edge equipment for the poultry and rabbit breeding sector. This production environment has apparently rather simple production needs but, as we will see below, it often has its fair share of issues when machining sheet metal components and these are anything but trivial. These issues as a result of the admirable and philanthropic choice to create distance from anything remotely related to the concept of intensive farming. This decision led the Sandrigo company from the province of Vicenza to be strongly driven by the automation of production processes, which they consider the only effective way to adequately respond to the needs of product customisation while offering superior quality. This is also controlled and guaranteed by virtue of the technological partner they chose ten years ago: Prima Power.
Turnkey poultry plants
Let's start by saying that SKA srl has been operating in the poultry plant sector since 1954 and produces everything related to organic farming on land and that, since 2011, the acquisition of the Treviso-based Meneghin means they also manufacture rabbit breeding equipment. The decision to deal solely and exclusively with organic farming plants over the years has made SKA an authoritative point of reference for leading Italian and international groups as well as simultaneously providing direct support to smaller farms.
"Since our foundation, we have always gone against the tide compared to many other companies in the sector and, thanks to the traditional vocation to customise poultry plants, we have managed to distinguish ourselves and build a highly technological business structure over time, while always standing alongside the breeders" says Dino Pozzato , Chairman of the SKA Group.
“Direct dialogue with the customer has allowed us to develop proven experience in the management of organic farms and in solving the problems connected to them. Our feeding, watering, lighting and air conditioning systems, for example, are designed to meet the well-being of animals and the regulations in force. The materials are durable and hygienic, and equipment components are easily accessible for thorough cleaning. Thanks to the wide range of products, suitable for broilers, laying hens, turkeys and breeders, as well as ducks and quail, we are able to satisfy every need”.
Efficiently managing any product change
But how is SKA linked to Prima Power? It goes without saying if we think about how many sheet metal components there are in a poultry plant. Processing problems from the high level of product customisation and the decision to use only organic and ethical poultry farming, however, are banal and obvious. This is explained to us by Diego Pozzato, plant manager of SKA: “We offer a complete turnkey service, from the barn to the internal systems, designed to the finest detail. We are able to efficiently support our breeders, by helping them to find concrete answers and solutions for each and every need. We collect useful data and perform structural calculations for technical drawings, while sharing each step with the customer and recommending certain equipment, working to identify the most suitable solution based on the reference standards and the type of farm. Our goal is to make management more functional and to increase productivity. Our in-house technical office ensures an immediate transition from product design to production.
However, primarily making plants specifically designed for organic farming reduces the numbers compared to intensive farming. This prizes quality over quantity, and favours animal welfare over pure economic interest as it involves a much lower number of animals. Consequently, devices and equipment to be produced for such a plant are also different; this means that we produce large quantities of series but with smaller batches than one might think. You have to be rather flexible to produce what specific breeders require since the variables involved are numerous, from the type of hen that will be reared, the size of which, for example, will determine the choice of equipment to be adopted. This means that our production needs to be high performing and productive while also being flexible and versatile in order to efficiently manage any product changes”.
A synergistic relationship consolidated over time
SKA is a longstanding customer of Prima Power. They started in 1998 with an F5 punching machine with loading/unloading before making an evolutionary leap by switching to a combined Shear Genius punching-shearing machine, which was then connected to the Night Train automatic storage unit. Recently, they also connected a robotic bending island to the storage unit, consisting of a Fast Bend FBe 5 panel bender, an EP 1030 press brake and an anthropomorphic robot.
“Since 1998, our choice has consistently been Prima Power,” explains Mr. Diego Pozzato again. "We were pioneers in the use of their F5 punching machine, which we then replaced in 2011 with the current SGe6 to which, we added the Night Train automatic storage unit in 2017 and the integrated robotic bending system in 2019. We are currently evaluating the inclusion of a laser cutting system in our Flexible Manufacturing System that would best complement our sheet metal processing needs even though we already have a continuous, optimised and efficient workflow designed and developed in synergy with Prima Power. The concrete example is the robotic bending cell that we installed at the beginning of 2020; we started with the idea of buying an automatic panelling machine but during the evaluation phase we realised it was not the ideal solution for our work. So, we opted for this solution which best combines the potential of an efficient servo-electric panel bender and a modern electric bending machine - which allows us to carry out all the processes in the shortest time possible and in the most efficient way thanks to the combination of both technologies.”
Process efficiency is maximum
SKA has always believed in the automation of production processes, which is considered the only effective way to manage high customisation. Indeed, production is characterised by large series, but not by huge quantities. “We are not talking about 15 pieces but we’re not talking about 100,000 pieces either,” says Diego Pozzato. The need to automate the bending phase in such a substantial way therefore arises from the fact that the great versatility and productivity of the Shear Genius combined with the Night Train storage unit created a sort of bottleneck downstream of the cutting and punching phase of parts.
“Previously with the systems we were using,” explains Mr. Diego Pozzato, “we were able to easily bend about 60% of our production, effectively creating a bottleneck. Since the goal was to achieve that continuous, fluid and efficient production flow that we talked about previously, we decided to fill this gap by producing the missing 40% with this type of system. By combining the two bending technologies in the best possible way, it now guarantees us unprecedented operations, since it covers 100% of our bending needs. It’s an incredibly valid and interesting solution in which two different bending systems work together to produce parts; the panel bender handles whatever the bending machine cannot and vice versa. This ensure the best execution of the various parts. The great advantage is that the whole system is managed offline; this means that the technical office can schedule production in masked time while the cell is manufacturing. In short, downtime is limited to a minimum and the process efficiency is truly maximum.”
The two machines integrated in the cell are able to work in series or in parallel, in the sense that the anthropomorphic robot can control both machines at the same time to ensure that a piece is partially made on the panel bender and finished on the bending machine, or it can control one of the two machines while the other works in parallel in manual mode. It is thus a very flexible solution fed by an output station with a wagon that comes out of the Night Train storage unit where the semi-finished products are stored. It is therefore not a direct feed from the Shear Genius but always from the storage unit so, even here, there is maximum flexibility in managing workflows. The so-called blanking phase does not necessarily need to be balanced with bending downstream precisely because there is the storage unit in the middle that acts as a buffer for collecting the pieces coming from other machines in the workshop.
The integrated robotic bending system
“The increased effectiveness of the Prima Power integrated robotic bending system adopted by SKA derives precisely from the simple and fast offline programmability of the machines and robot included in the cell, the operating mode of which was an exceptional turning point for the sector when it was presented in 2018,” says Roberto De Rossi, Senior Manager Business Development Thin Sheet Metal at Prima Power. “It is a solution that allows you to achieve maximum benefits from the investment, since the efficiency of the system is guaranteed for the production of both small and larger batches. This touches on another of the challenges that SKA set us as an objective, namely the optimal management of their double productive core,” explains De Rossi. “Their production is characterised by repeatable elements in which there are obviously larger quantities to be produced annually depending on a regular weekly schedule or other types scheduled throughout the year by launching convenient and repeatable production batches. However, there is also a part of the production that requires the execution of batches with smaller quantities expressly dedicated to the production reality of the individual customer.
To give the plant greater flexibility, we have therefore also envisaged the possibility of using the machines in a traditional way, allowing the robot to create repeatable parts and to use the machines in standalone mode to perform machining in manual. This was a further challenge since we had to allow access to the cell despite the presence of the robot in charge of both machines.
Taking advantage of the fact that the machines are side by side, we came up with a solution which is also substantially automatic, where the robot can move (seventh axis of the robot) over 19m of track embedded in the floor foundations. This means that the compartment in which the robot slides can also be closed when needed, thus allowing the operator access to one machine or the other to take care of any emergencies that might arise during the production phase. In this specific case, we are talking about very small quantities where the robot would not give added value. The interesting thing is that, when necessary, the robot will prepare itself and automatically close the track pit over with manhole covers. A further element of flexibility comes from the fact that an FBe 5 panel bender can be used manually while the eP 1030 works automatically under the robot which can process smaller parts placed in bulk in a bin and there is a vision system in place for the recognition of the single piece.
The bending machine depends on the panelling machine and not vice versa
At this point, it is clear that there is always optimal production management at SKA thanks to the many functions provided by the Night Train storage unit. This is what constitutes the real production core of the entire FMS, around which the various Prima Power islands, automatic cells and all other departments of the workshop gravitate. In reference to the robotic bending cell operation, what is the discriminating factor for which the system, or whoever programs the system, establishes which pieces are made with the bending machine and which are made with the panel bender or, even, which parts use both machines consequentially to complete the shape? Diego Pozzato answers: “The panel bender is the most convenient of the two machines, because it guarantees unbeatable bending speeds; however, certain profiles, such as “C” shapes with particularly high edges, mean the bending machine is the only possible option. It therefore depends on the shape to be made and its dimensions. Our technical office is working on “redesigning” the various projects with a preference to the panel bender or, at least, studying which shapes make the most of the operational synergies between two machines while also considering the fact that the eP 1030 bending machine depends on the panelling machine and vice versa. The Fast Bend panel bender is still the weapon of choice for productivity and flexibility. Not surprisingly, our initial reasoning involved a single automatic panel bender and not an integrated robotic bending cell like the current one. We came to this conclusion only after an in-depth and detailed study carried out alongside Prima Power. This revealed that the panel bender was not suitable to fully cover our processing needs. Due to their shape, some parts could not be completely bent with the Fast Bend, which is why we decided to add the potential and versatility of an electric bending machine”.
Both the bending machine and the panel bender are servo-electrically operated. This is an important aspect for two reasons: reduced consumption, and above all the absolute precision and repeatability they ensure while processing.
A manual panel bender, with robotic loading and unloading
“The selection of the Fast Bend FBe 5 panel bender is thanks to the synergy between us and SKA,” explains Cristiano Porrati, Prima Power Countries Manager South Europe. “Since many parts in their standard production have a narrow shape, this does not work well with the gripper manipulator typical of “conventional” panel benders, something different was needed and the choice fell on the one that most characterises us in this technological segment, being the most flexible of all and with the peculiarity of having a suction cup manipulator, which was essential for SKA. From the initial phase of analysis and study, it was clear that the Fast Bend could be the most appropriate machine for the SKA product, but it was "limited" by manual interlocking. Indeed, the Fast Bend is a machine with fairly limited automation as it only moves the pieces and does not rotate them, loading and unloading operations are typically the prerogative of the operator who, in this specific case, has been replaced with the anthropomorphic robot. This means the FastBend becomes fully automatic. The robot moves freely on the front of the machine along its 19 m track, which allows it to cover both the bending machine and the panel bender as well as to easily reach any of the three unloading bays of bent material with multiple palletising areas where it can deposit the pieces meant for this area.
The lay-out obviously includes a magazine for piece gripping parts that the robot changes in total autonomy depending on the parts production list generated remotely by the technical office. This production queue can be sent directly to the panelling machine which, thanks to the developed IT infrastructure and the plant management software, can recall the wagon from the Night Train with the semi-finished products required for that particular production batch and then launch the program via the robot which will start to manage them as expected, delegating them to the panel bender or the press brake where they will be processed and, consequently, stacked.”
Laser cutting closes the circle
SKA has always been at the forefront of innovation; it is therefore not surprising that it has already planned further growth which will turn it into a fully-fledged smart manufacturer that meets the requirements of the Industry 4.0 protocol within just a few years. “We are already working and preparing things both on a hardware and software level for the management of the entire production,” says Diego Pozzato. “On this topic, I would like to emphasize that all Prima Power systems installed are “Industry 4.0 ready” and that we intend to combine the Night Train with a laser cutting system, as mentioned at the beginning. This would allow us to really close the circle of working possibilities since we would even be able to manage irregular stainless steel shapes with the same precision as the SG - these irregular shapes are currently outsourcing to partner companies. The Shear Genius is actually a punching machine combined with an integrated angular shear that works best in the production of semi-finished products with a regular square shape. Starting from the storage unit which will remain the core of the entire production system, the new challenge we intend to get stuck into at Prima Power is to be able to process, firstly, metal sheets on the Shear Genius, to make all holes and deformations required on pieces, to then sort them to the future laser cutting system, still using the Night Train as a semi-finished products, where they will be cut and re-stored before sending them to the integrated bending cell. They will then be finished by combining the two technologies envisaged in the best possible way. We are positive that from the very top of its plentiful range of machines and automatic solutions for processing sheet metal combined with its competence and experience, Prima Power will once again be able to respond adequately to our requests and fully satisfy the expectations of our technical office, with which there has always been an effective synergy and collaboration”.
The great advantage is that the whole system is managed offline; this means that the technical office can schedule production in masked time while the cell is manufacturing. In short, downtime is limited to a minimum and the process efficiency is truly maximum
Are you looking for a similar solution for your company? Find it here
Night Train FMS®
FLEXIBLE MANUFACTURING SYSTEMS
Leading technology storage solution in automated flexible manufacturing systems
Shear Genius EVO
PUNCHING AND SHEARING COMBINED MACHINES
Highest productivity with integrated punching and shearing
Robotic Bending Cells
ROBOTIC BENDING CELLS
Full performance optimization into your arms
FBe Fast Bend
PANEL BENDERS