
A bordo del Night Train per essere più competitivi

Minerva Omega Group è un’azienda che racchiude in sé competenza, tecnologia e imprenditorialità, ovvero quel mix di caratteristiche tipiche di chi primeggia in Italia e nel mondo.
Idee chiare e determinazione sono le caratteristiche che hanno permesso ad Andrea Salati Chiodini, CIO e responsabile tecnico del Gruppo, di puntare sull’automatizzazione dei processi in officina per essere competitivi e rispondere ai dettami qualitativi richiesti dalle normative che regolano il mondo delle macchine alimentari che li vede da tempo primeggiare. Parliamo di un sistema completamente automatizzato e integrato Night Train di Prima Power in grado di garantire loro un semilavorato finito, subito pronto per le fasi successive di produzione.
Minerva Omega Group s.r.l. nasce nel 2012 dalla fusione tra due aziende storiche nella progettazione e produzione di macchine e sistemi per le lavorazioni delle carni e degli alimenti in generale: la bolognese Minerva e Omega Ceg, di Varese. Entrambe le aziende hanno una storia, una tradizione e un’esperienza che arriva da lontano. La Minerva, che festeggerà nel 2020 i 75 anni di attività, nasce nel 1945 a Bologna, territorio di forte tradizione meccanica e motoristica, per l’intraprendenza imprenditoriale di Mario Chiodini, nonno degli attuali titolari.
Progetta e produce macchine per la lavorazione delle carni, la ristorazione, l’industria di trasformazione alimentare, i centri di confezionamento, e propone una gamma di elevata qualità con un ottimo rapporto qualità-prezzo-durata. La gestione aziendale è affidata alla terza generazione della famiglia Salati Chiodini, ancorata saldamente alla loro tradizione, alla cultura e al territorio di origine.
“Siamo una delle aziende familiari più longeve in Italia - racconta il signor Andrea Salati Chiodini - ed è grazie a questa leadership imprenditoriale e a una mentalità manageriale orientata al marketing, che abbiamo portato Minerva ad acquisire e incorporare alcuni concorrenti: prima la ditta Artex di Bologna, poi la Omega, proprietaria di altri marchi storici come Ceg, General Machine, Regina, Suprema e, recentemente, Aria e Mincer2000, tutti marchi molto conosciuti dagli addetti ai lavori in tutto il mondo”. “Omega Ceg dal 1950 è invece sinonimo di affettatrici e altre macchine per la lavorazione degli alimenti” prosegue il signor Salati Chiodini. “Un marchio conosciuto e apprezzato che abbiamo voluto mantenere localizzato nel suo territorio di origine, la provincia di Varese, con il preciso intento di assicurare lo stesso livello qualitativo di prodotto e servizio che da sempre ha distinto il marchio, grazie anche alla forte specializzazione e all’esperienza storica dell’indotto presente nell’area. Con questa operazione abbiamo salvato un marchio storico con una forte presenza in Italia e all’estero e completato la gamma di macchine La Minerva per dare un nuovo impulso al brand, grazie anche a una forte organizzazione commerciale verso tutti i paesi europei ed extra europei”.
Oggi Minerva Omega Group, ulteriormente rafforzato nella sua fama internazionale grazie anche a un sistema di gestione moderno e vincente, può dunque vantare una gamma tra le più complete del mercato, un portafoglio clienti consolidato con presenza in ogni settore alimentare sia nella grande distribuzione organizzata che attraverso rivenditori in ogni paese del mondo.
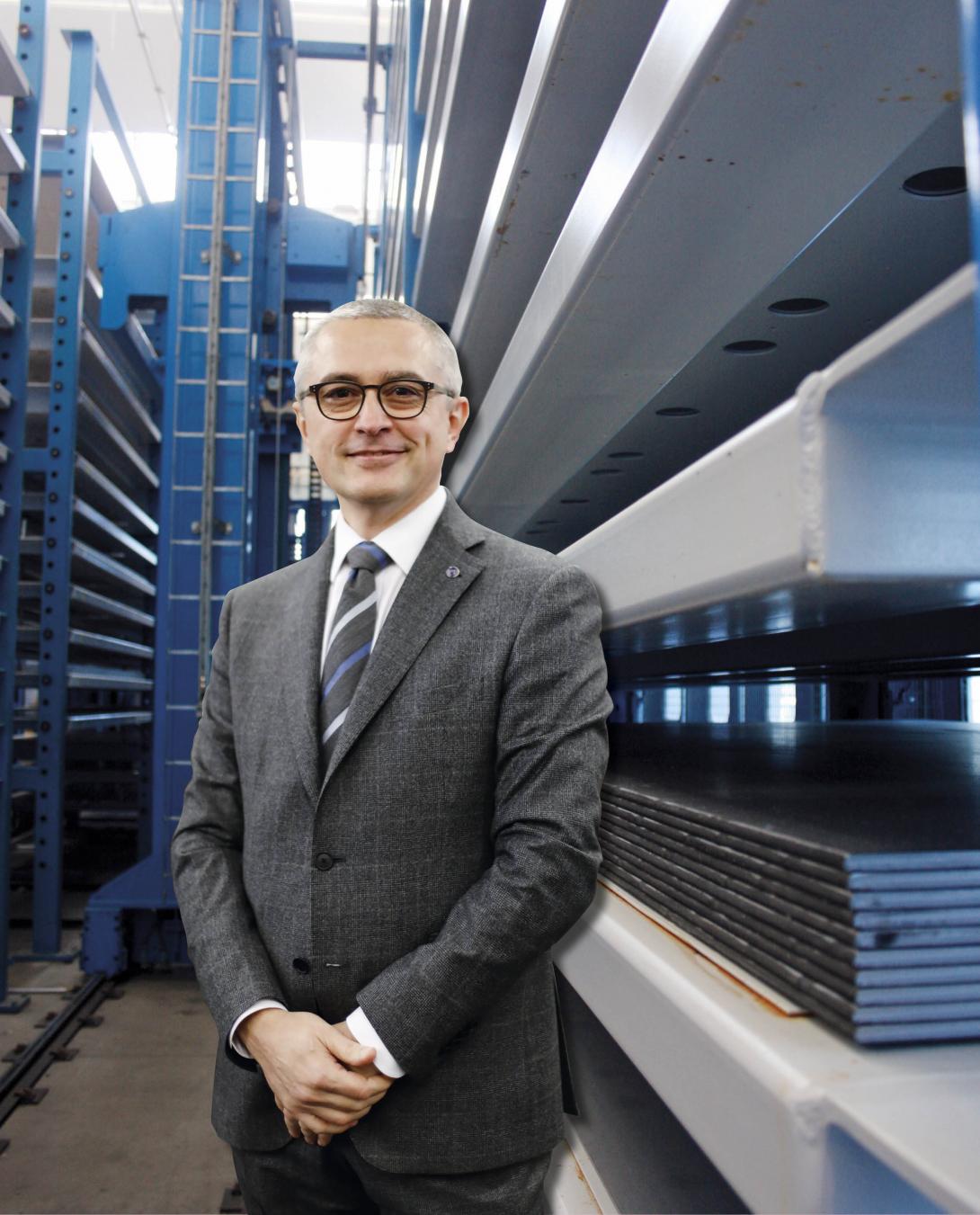
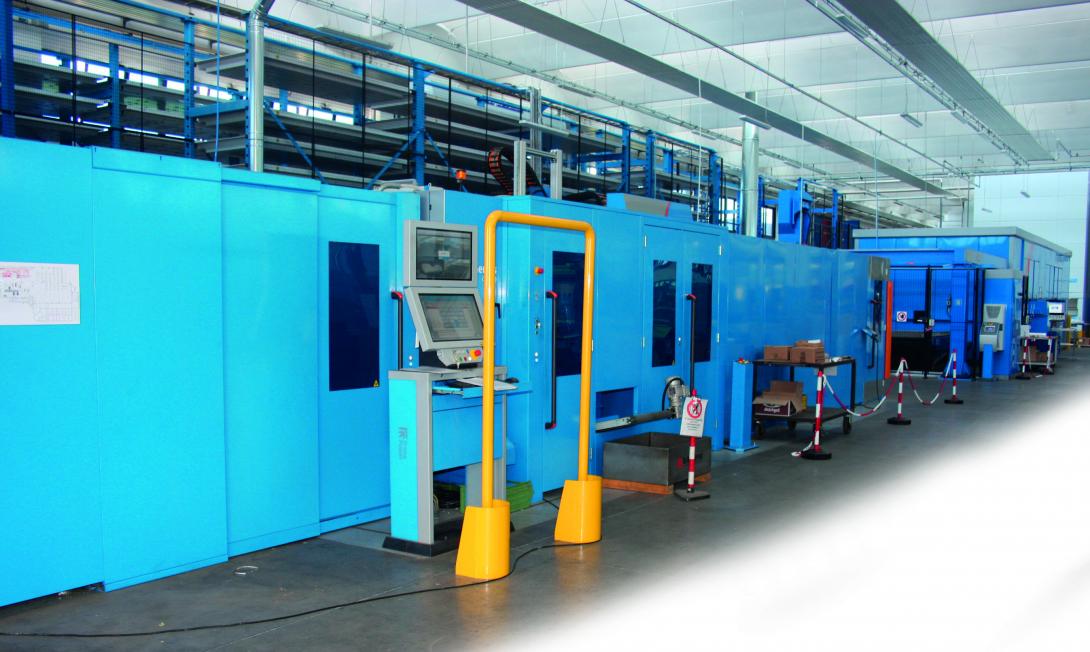
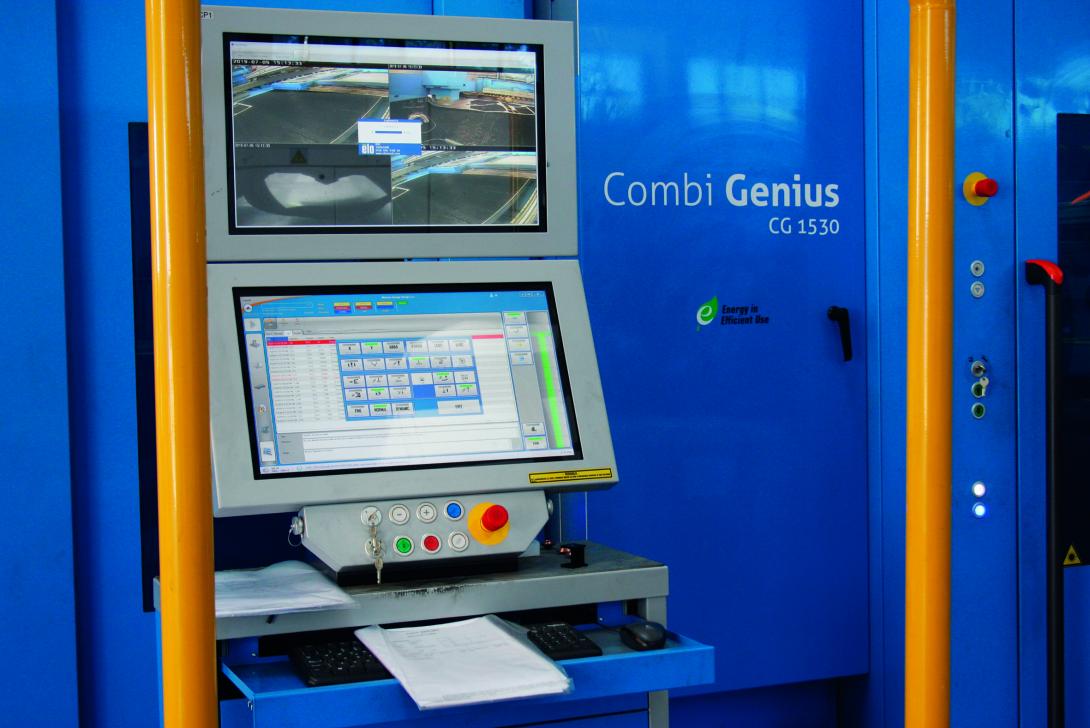
Un’eccellenza tutta italiana
Minerva Omega Group S.r.l. rappresenta dunque una realtà consolidata, un’eccellenza tutta italiana nel settore, con forte capacità di investimento in progettazione e sviluppo di nuovi modelli, in attrezzature e linee produttive automatizzate. “Crediamo nella qualità del lavoro, frutto di un importante impegno di gruppo sviluppato dai nostri dipendenti e collaboratori. - Spiega Salati Chiodini -
“Nonostante le grandi difficoltà e la concorrenza di paesi nei quali produrre costa molto meno, difendiamo e sosteniamo il Made in Italy con tutte le nostre forze, senza delocalizzare la produzione dei principali componenti e l’assemblaggio delle macchine nelle sedi bolognese e varesotta”
“L’impegno è notevole, gli investimenti per mantenerci tecnologicamente e qualitativamente concorrenziali sono frequenti e coinvolgono l’intera filiera. L’eccellenza, la competenza e la qualità sono per noi valori irrinunciabili. Lo sviluppo continuo dell’azienda su tutti i mercati è la migliore risposta alla domanda se oggi vale ancora la pena investire nella produzione manifatturiera italiana”. Parole che testimoniano quella imprenditorialità che non fa certo difetto alla famiglia Salati Chiodini e al nostro interlocutore, in particolare, diventato tra l’altro, dal marzo scorso, presidente di Assofoodtec, L’Associazione Italiana Costruttori di Macchine, Impianti, Attrezzature per la Produzione e la Lavorazione Alimentare, federata ad ANIMA Confindustria.
Una scelta tecnologica importante nel segno della continuità
Quella di Minerva Omega Group è dunque una mission chiara, in ragione della quale, da tempo, è stata intrapresa la strada dell’automatizzazione dei processi di lavorazione più all’avanguardia per essere competitivi e in linea con i dettami qualitativi richiesti e imposti dalle normative vigenti in fatto di macchine alimentari.
“Abbiamo introdotto le prime macchine automatiche nel 1984 - racconta il signor Salati Chiodini -; erano macchine ad asportazione truciolo perché, in precedenza, il nostro prodotto nasceva dalla lavorazione di corpi fusi. Era veramente poca la lamiera utilizzata e la sua lavorazione era data in outsourcing. Intorno al 1994/95 abbiamo però iniziato a percepire un cambiamento del mercato che, oltre alla funzionalità, iniziava a richiedere anche un certo valore estetico dei macchinari. Abbiamo quindi introdotto l’acciaio inossidabile e cominciato a produrre alcune macchine con questo materiale continuando comunque ad appoggiarci esternamente a dei terzisti.
Solo nel 1998, vedendo che la lamiera stava diventando sempre più preponderante nella nostra tipologia di prodotto abbiamo deciso di portarci in casa anche questo tipo di lavorazione e siccome, per scelta, cerchiamo di investire sempre in macchine e soluzioni innovative di ultima generazione, abbiamo acquistato il nostro primo sistema di taglio laser, un Platino di Prima Industrie con il classico campo di lavoro da 1.500 x 3.000 mm e cambio pallet automatico dando un forte impulso all’attività. Nel 2002 abbiamo iniziato la costruzione di questa nuova sede in cui abbiamo installato anche una combinata laser della Finn Power con sorgente CO2 da 2,5 kW che abbiamo utilizzato fino allo scorso anno. Fu una scelta legata alla volontà di automatizzare il più possibile il ciclo di lavorazione ragion per cui scegliemmo, già allora, di abbinare alla macchina anche un magazzino Night Train con 10 torri con 12 cassetti intorno al quale abbiamo organizzato tutta l’officina con varie presse piegatrici, anche robotizzate, nuovi centri di lavoro e tutte le altre macchine già presenti nella vecchia officina. Insomma, un’organizzazione produttiva innovativa ed efficiente che ci ha permesso di dare forte impulso all’attività senza intoppi fino al 18 gennaio del 2018, quando un incendio ha devastato il nostro reparto lamiere, costringendoci per alcuni mesi ad attivare dei fornitori esterni per le lavorazioni dell’acciaio. Abbiamo inoltre iniziato a sostituire ciò che era andato distrutto, rimettendo in gioco tutti i principali player del mercato anche se, alla fine, abbiamo preferito proseguire lungo la strada tecnologica intrapresa parecchi anni prima e optato per quella continuità che Prima Power era in grado di assicurarci dopo l’acquisizione di Finn Power. Potrebbe sembrare una scelta di simpatia ma vi assicuro abbiamo davvero rimesso in gioco tutti e analizzato pregi e difetti delle soluzioni proposte da ognuno ma alla fine quella di Prima Power, ben sapendo ciò di cui avevamo bisogno, si è rivelata quella più in linea con le nostre aspettative produttive e adatta alle nostre esigenze anche in termini di layout dell’impianto”.
“Abbiamo scelto nel segno della continuità - spiega ancora Andrea Salati Chiodini - anche in virtù delle tempistiche poiché il poter sfruttare lo stesso magazzino ci ha permesso di accorciare di mesi l’installazione. È stata quindi una scelta oculata e in linea con la nostra volontà di restare fermi il meno possibile, anche perché rivolgendosi a partner esterni per la lavorazione della lamiera non si è mai realmente padroni della situazione, sia come tempistiche ma anche come livello di qualità cui era abituata la nostra clientela”.
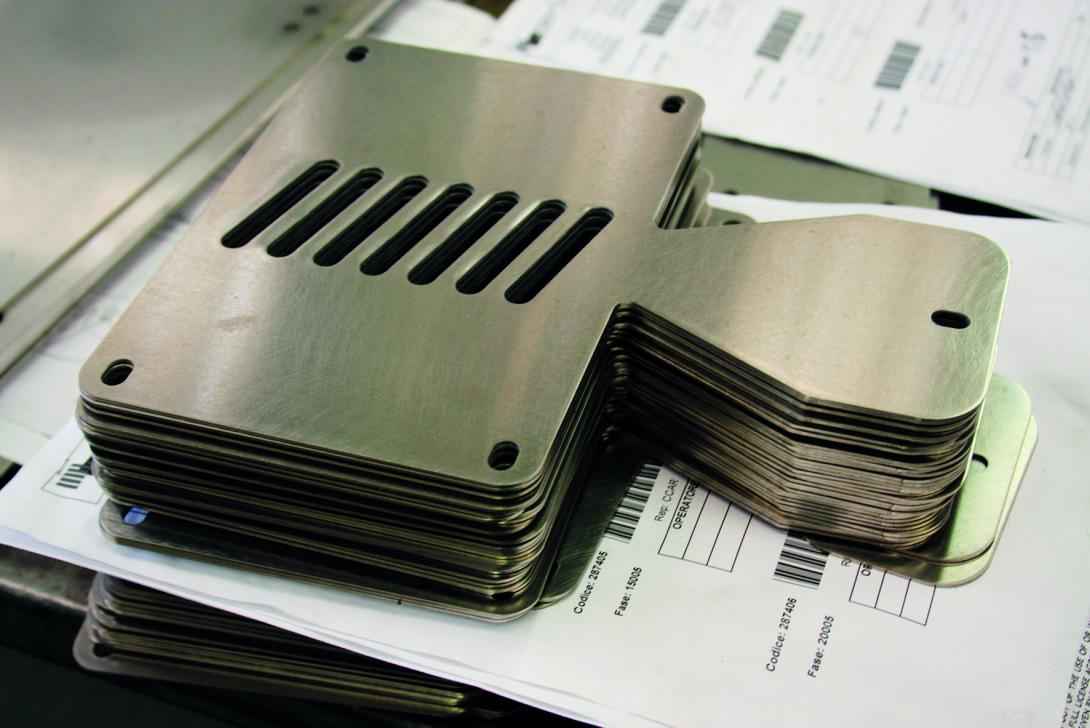
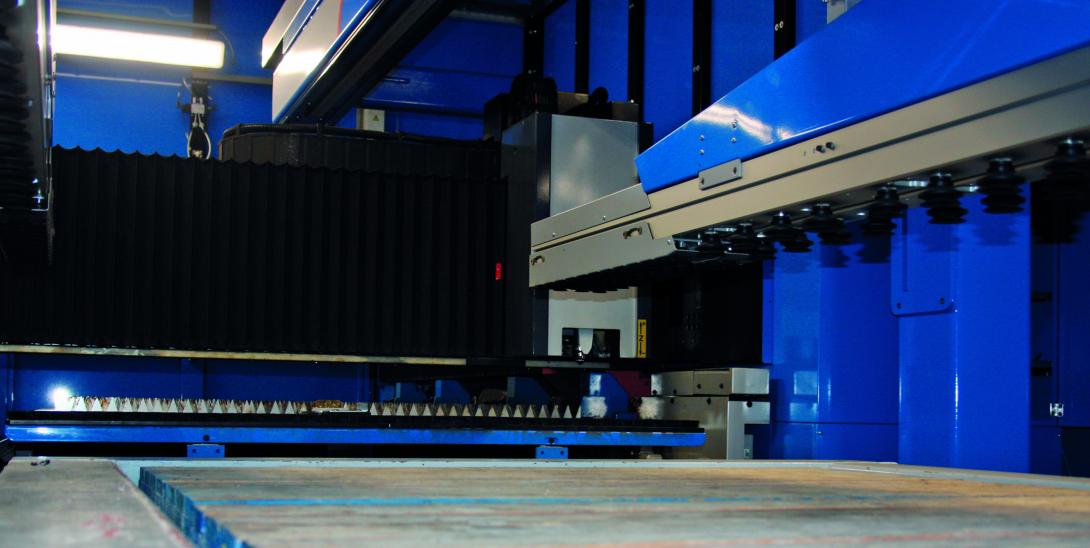
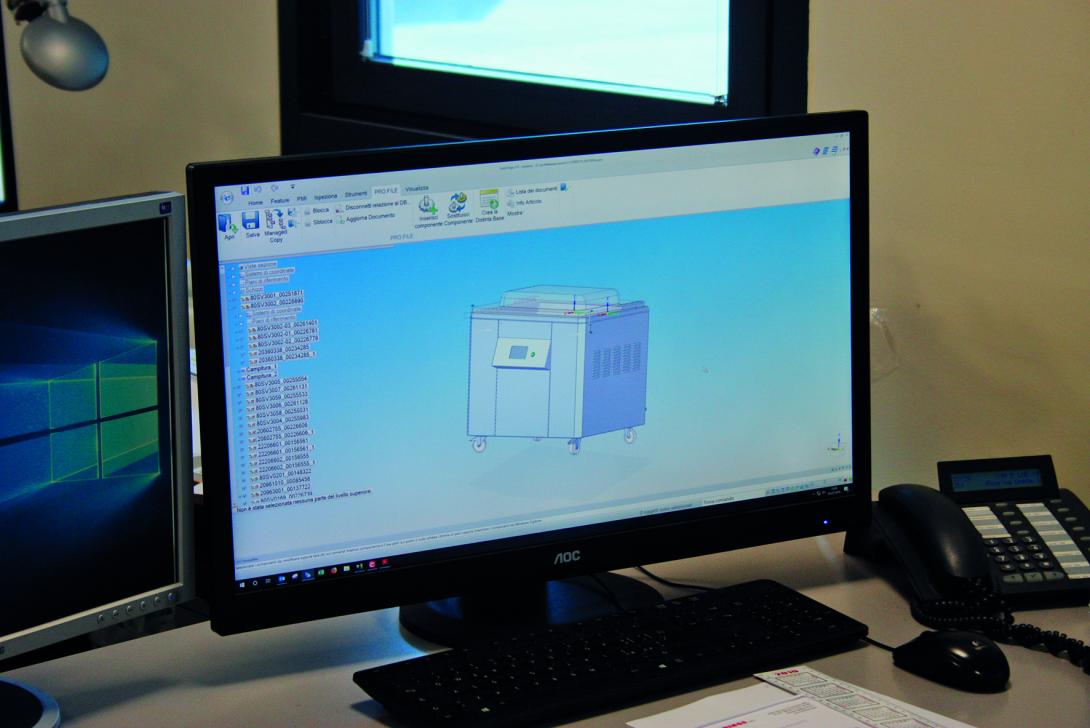
Un impianto realmente tailor made
Oggi, il nuovo cuore pulsante della produzione di Minerva Omega è quindi ancora il Night Train, composto di 14 blocchi e 200 cassetti, che rappresenta lo stato dell’arte in materia di magazzini automatici. A esso sono collegate la macchina combinata punzonatrice laser Prima Power Combi Genius 1530 con laser fibra da 4 kW e robot di carico/scarico e impilaggio LSR6, oltre che un sistema di taglio laser fibra bidimensionale Prima Power Laser Genius 1530 con motori lineari equipaggiato con una sorgente fibra da 6 kW, robot di carico e scarico lamiere LU e robot di sorting e impilaggio automatico LST.
“Si è passati da una pluralità di soluzioni che abbiamo sottoposto al vaglio della famiglia Salati Chiodini ma alla fine ha prevalso quella più simile alla precedente, a testimonianza della validità delle scelte già fatte in passato sotto l’aspetto della logica produttiva, che sono state ovviamente riviste e aggiornate. Oggi come ieri, il magazzino Night Train costituisce dunque il polmone centrale dell’officina che alimenta la nuova combinata e il sistema di taglio Laser Genius” racconta Cesare Brunelli, sales area manager di Prima Power per l’Emilia Romagna.
“Abbiamo lavorato su un’ipotesi di quattro layout perché abbiamo cercato di ottimizzare l’impianto in funzione dello spazio a disposizione andando a recuperare, dove è stato possibile, anche 15/20 cm per migliorare ogni piccolo dettaglio come per esempio il passaggio dei muletti piuttosto che i flussi di scarico degli sfridi di lavorazione o gli accessi per gli operatori” racconta ancora il signor Salati Chiodini. “In questo mi preme sottolineare la grande disponibilità e la capacità sartoriale di Prima Power nel riuscire a fare un prodotto realmente “tailor made” poiché si sono calati nel nostro ruolo per comprenderne al meglio le problematiche e non hanno mai proposto una scorciatoia rappresentata da una o più soluzioni standard. Hanno compreso fin da subito l’importanza di proporre un sistema produttivo totalmente automatizzato in grado di dare un semilavorato finito, subito pronto per le fasi di successive. Entra la lamiera ed esce il prodotto finito con il livello di finitura che richiediamo. Per noi questo è sempre stato l’aspetto vincente in virtù del fatto che lavoriamo h 24, sette giorni su sette. Lo era prima e lo è adesso che la tecnologia ha raggiunto un livello di affidabilità tale da consentirci di lanciare un nesting il venerdì pomeriggio e arrivare il lunedì mattina con tutti i particolari pronti per essere smistati in piegatura (dove è stata anche installata una presso piegatrice servo-elettrica Prima Power eP-0520) e in montaggio; è per noi un aspetto imprescindibile che ci permette di programmare il lavoro abbattendo i tempi morti e minimizzando gli scarti”.
“È stato un lavoro complesso ma sfidante e per questo appassionante - racconta nuovamente Brunelli di Prima Power - poiché le macchine sono state, da prima, consegnate funzionanti stand alone e solo successivamente, dopo aver fatto il revamping del magazzino Night Train, collegate a esso. Tra l’altro, anche il retrofit del magazzino è stato piuttosto importante poiché quello in essere era fermo a due generazioni precedenti rispetto al livello tecnologico di un moderno Night Train. Oggi, al netto della carpenteria, il magazzino è assolutamente un magazzino nuovo sotto ogni aspetto, sensoristica, software, controllo, motori elettrici e meccatronica in generale”.
Combinata o taglio laser? Dipende dalla natura del pezzo
Oggi, la configurazione del Night Train Prima Power installato consente a Minerva Omega di lavorare sia su commessa che su stock per il magazzino che viene usato anche per lo stoccaggio dei semilavorati. La lavorazione su commessa, in genere, riguarda gli ordini esteri caratterizzati da grossi quantitativi per cui viene inserito l’ordine nel gestionale aziendale, generata una data di consegna stimata (in linea con le aspettative del cliente), e lanciata la produzione. L’MRP gestisce tutto, dagli ordini ai fornitori della componentistica commerciale piuttosto che, internamente, le lavorazioni di asportazione di truciolo e di taglio lamiera. Ogni fase del ciclo è schedulata mediante un planning che gestisce in modo logico ed efficiente il flusso di lavoro sulle varie macchine in officina e nei vari step di avanzamento fino ad arrivare al montaggio e alla consegna del prodotto.
Per quanto concerne i lanci di produzione legati all’operatività del sistema Night Train Prima Power, in Minerva cercano di sfruttare i nesting di lavorazione per avere il minor sfrido possibile ottimizzando al massimo le lavorazioni.
“Avendo dei particolari che per il 90% sono in lamiera di acciaio inossidabile riusciamo sempre a creare dei nesting ottimali che accorpano il mix migliore di parti, anche di consumo, in ragione delle commesse da realizzare. Cerchiamo di radunare nei nesting quanti più pezzi è possibile per arrivare a una percentuale di riempimento delle lamiere dell’85%” precisa Salati Chiodini.
Interessante è stato capire anche quali siano gli aspetti che determinano il fatto che una tipologia di pezzi venga lavorata sulla Combi Genius piuttosto che sul sistema di taglio Laser Genius. Anche in questo caso, la risposta del signor Salati Chiodini è stata chiara e inequivocabile: “Sul laser facciamo solo i particolari di taglio o di grosso spessore mentre sulla combinata realizziamo tutti quei pezzi che necessitano anche di altre lavorazioni quali deformazioni, fori filettati, bugnature piuttosto che delle scantonature e delle asole. Se dovessi invece fare un paragone con il passato, quando avevamo i laser CO2 anziché le sorgenti in fibra, direi che l’aspetto più evidente è forse quello legato ai consumi in quanto stiamo avendo un risparmio piuttosto significativo se si pensa che la sola combinata consumava circa 80 kW mentre oggi, con entrambe le macchine, non arriviamo a questo valore.
Il laser fibra garantisce poi una ridottissima manutenzione e un taglio migliore e più fine nella maggioranza dei casi e questo vale per entrambe le macchine che, avendo rispettivamente potenze di 4 kW, la combinata e 6 kW, la Laser Genius, assicurano prestazioni di taglio paragonabili.
La Laser Genius, avendo una potenza superiore, a parità di spessore, riesce ad avere una qualità leggermente superiore con tempistiche inferiori, direi però che in entrambi i casi, fino ai 15 mm di spessore, riusciamo ad avere una qualità di taglio praticamente perfetta e in linea con quanto previsto dalle certificazioni cui siamo sottoposti. Tra l’altro, il fatto di avere un taglio privo di bave e finito al meglio per noi significa evitare di riprendere i pezzi per sabbiarli o smerigliarli. Tutto questo comporta riduzione di tempi e vantaggi economici non indifferenti che ricadono a favore del cliente utilizzatore finale”.
Articolo apparso originariamente su Deformazione Magazine, Ottobre 2019.
Il laser fibra garantisce una ridottissima manutenzione e un taglio migliore e più fine nella maggioranza dei casi e questo vale per entrambe le macchine, sia per i 4 kW della combinata che per i 6 kW della Laser Genius
Stai cercando una soluzione simile per la tua azienda? Ecco qui
Combi Genius
MACCHINE COMBINATE PER PUNZONATURA E TAGLIO LASER