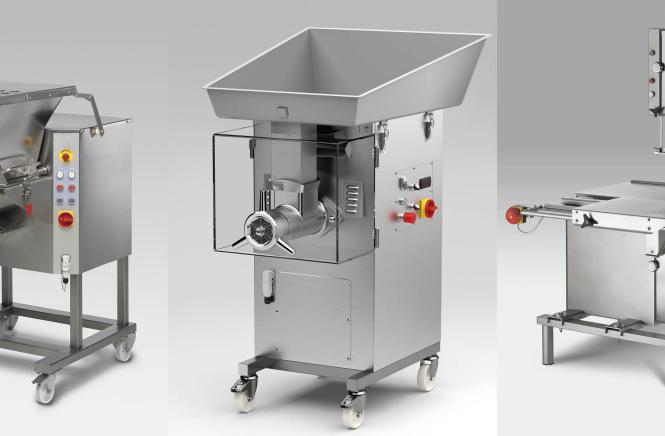
Вперед, к повышению эффективности с Night Train!
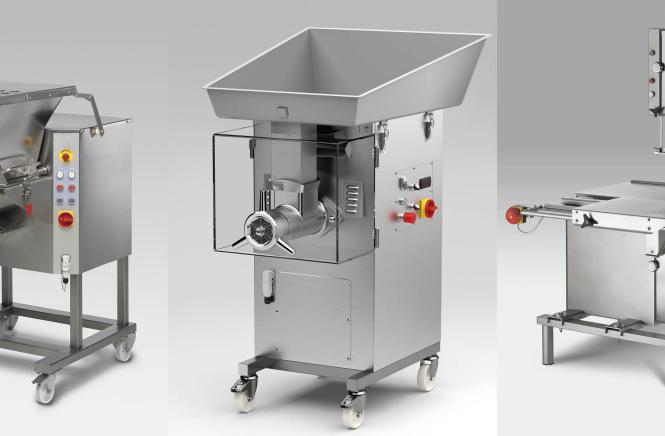
Итальянская компания Minerva Group олицетворяет собой непрерывное развитие, современные технологии и предпринимательский дух.
Четкие цели, решительность и знания – вот те качества, которые позволили техническому директору Андреа Салати Кьодини, сконцентрироваться на автоматизации производственных процессов. Они позволили компании получить решающее преимущество перед конкурентами в жестко регламентированном бизнесе оборудования для пищевой промышленности. Это было достигнуто за счет полностью автоматизированной и гибкой производственной системы Night Train от Prima Power, которая позволяет производить детали из листа, которые готовы к следующим этапам производства.
На сегодняшний день, группа Minerva Omega, чья международная репутация была еще более укреплена благодаря современной системе управления, может похвастаться самым широким ассортиментом продукции и солидным клиентским портфелем, присутствуя и в секторе пищевой промышленности, и в секторе розничной торговли, а также реализуя продукцию через дилерскую сеть по всему миру. Салати Кьодини вместе со своими братом и сестрой являются третьим поколением семьи, стоящей у руля этой промышленной компании со своей длительной историей.
Компания Minerva Omega Group S.r.l. была основана в 2012 году в результате слияния двух компаний, Minerva из Болоньи и Omega Ceg из Варезе. Обе компании имели долгую историю, традиции и опыт. La Minerva, которой в 2020 году исполнится 75 лет, была основана в 1945 году в Болонье, в регионе с сильными машиностроительными традициями, благодаря предпринимательской инициативе г-на Марио Кьодини, деда нынешних владельцев. Компания занимается разработкой и изготовлением машин для мясопереработки, общественного питания, пищевой промышленности, упаковочных центров и предлагает широкий ассортимент высококачественной продукции с отличным соотношением «цена-качество» и длительным сроком службы.
"Мы являемся одним из старейших семейных предприятий в Италии", – пояснил г-н Андреа Салати Киодини. – "Именно благодаря этому предпринимательскому лидерству и ориентированному на маркетинг управленческому мышлению мы привели компанию Minerva к приобретению и объединению некоторых наших конкурентов: сначала компании Artex из Болоньи, затем компании Omega, владевшей другими историческими брендами, таким как Ceg, General Machine, Regina, Suprema, а из недавних Aria и Mincer-2000, и это всё бренды, хорошо известные специалистам в этой области по всему миру."
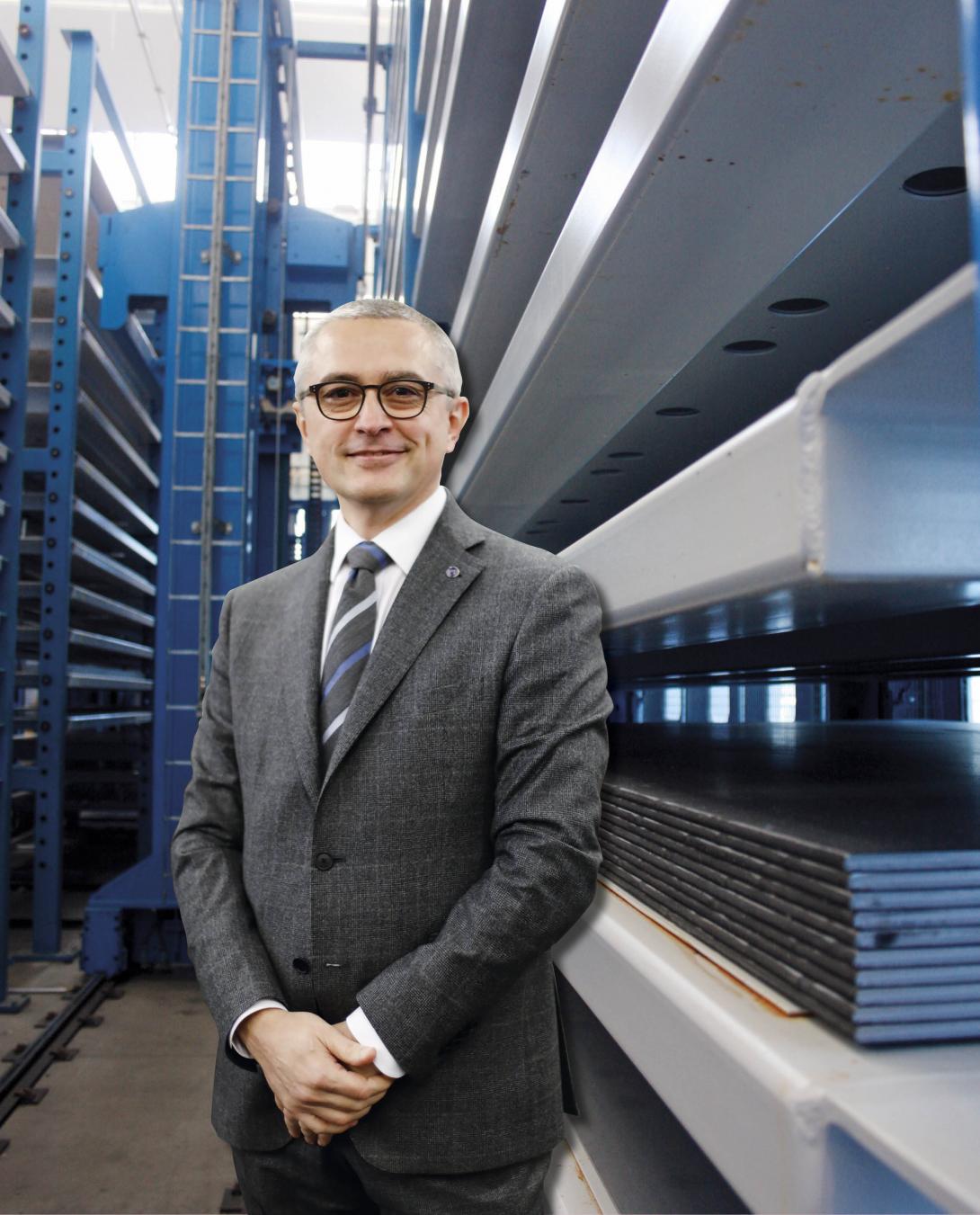
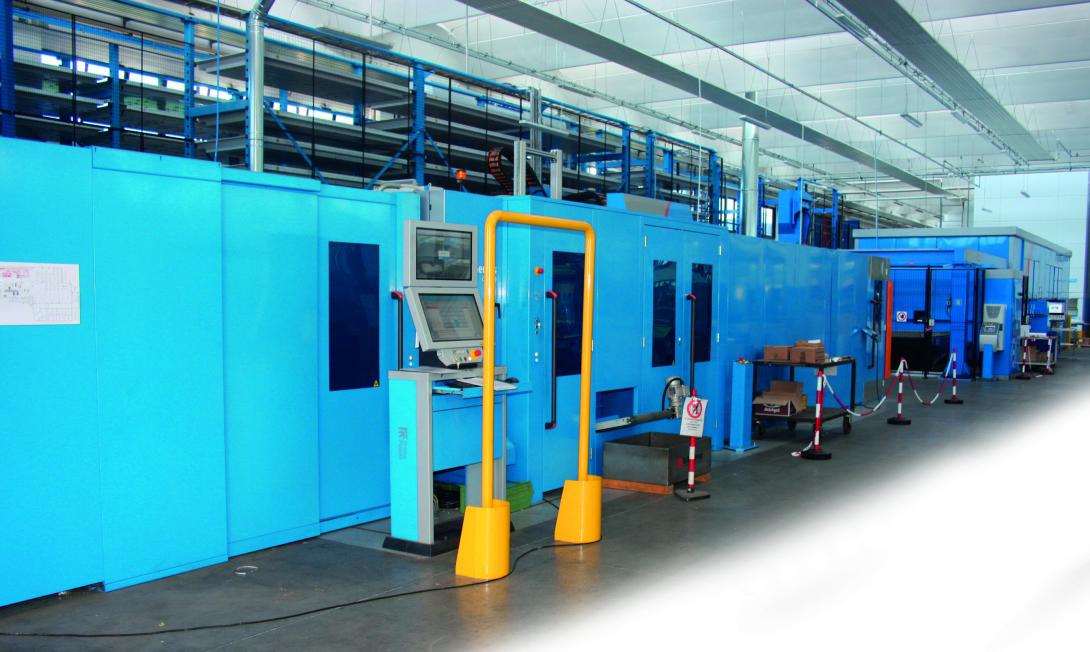
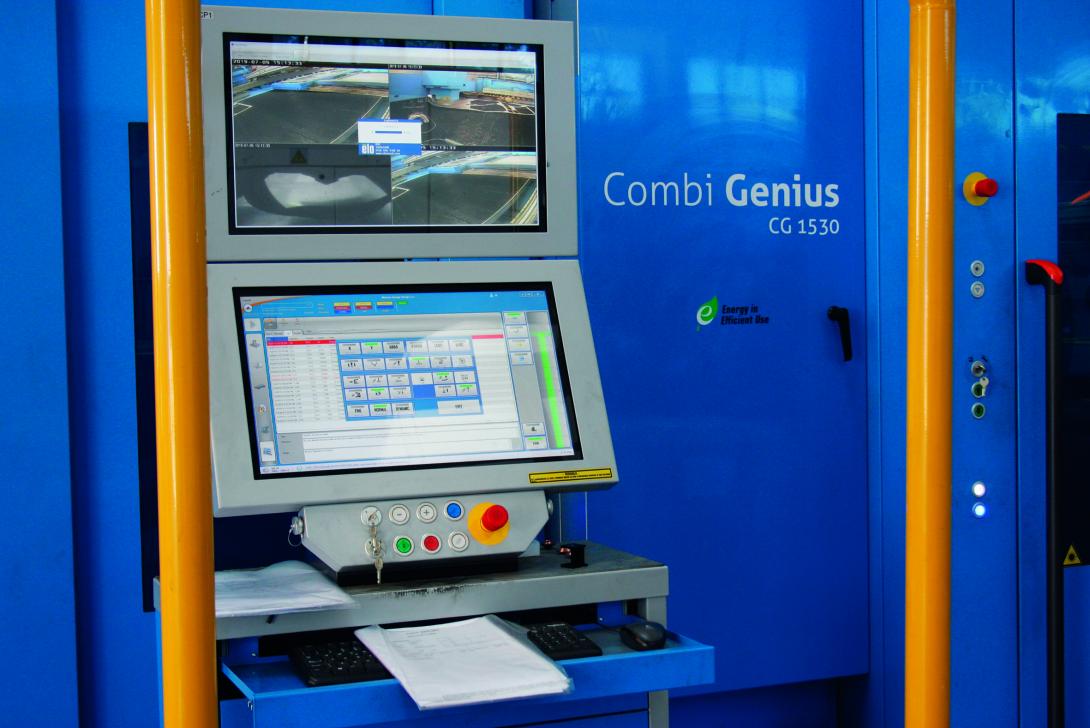
Всеитальянское совершенство
Minerva Omega Group – это хорошо зарекомендовавший себя в Италии пример компании, занимающей доминирующее положение в отрасли, обладающей сильными инвестиционными возможностями в проектировании и разработке новых моделей, выпуске автоматизированного оборудования и производственных линий. «Мы верим в качество работы, свидетельствующее о приверженности основной группе и ответственном подходе наших сотрудников и партнеров,» – пояснил Салати Кьодини.
«Несмотря на большие трудности и конкуренцию со стороны стран, в которых производство имеет гораздо более низкую стоимость, мы всеми силами защищаем и поддерживаем бренд Made-in-Italy (Сделано в Италии), не перенося производство основных компонентов и сборку оборудования из подразделений в Болонье и Варезе.»
Приверженность имеет существенное значение. Не менее важны инвестиции для поддержания нашей технологической и качественной конкурентоспособности, которые осуществляются на регулярной основе и охватывают всю цепочку поставок. Совершенство, конкурентоспособность и качество являются для нас важнейшими ценностями. Продолжающийся рост компании на всех рынках является лучшим ответом на вопрос о том, стоит ли по-прежнему инвестировать в итальянское товарное производство сегодня.»
Главный технологический выбор
Миссия Minerva Omega Group ясна. Некоторое время назад компания встала на путь автоматизации самых передовых производственных процессов, не только чтобы обеспечить конкурентоспособность, но и соответствовать действующим стандартам качества, которые устанавливают требования к оборудованию для предприятий пищевой промышленности.
«Мы представили первые автоматические машины в 1984 году,» – сказал Салати Кьодини. «Это были станки для удаления стружки, поскольку ранее наша продукция была результатом обработки литых корпусов. Фактически использовалось очень мало листового металла, а его обработка выполнялась сторонним подрядчиком. Однако примерно в 1994/1995 году мы стали замечать изменения на рынке. В дополнение к функциональности, от машин стали ожидать еще и некой эстетической ценности. Поэтому мы внедрили в производство нержавеющую сталь и начали изготавливать некоторые машины из этого материала, продолжая полагаться на субподрядчиков.»
«К 1998 году мы решили приобрести нашу первую систему лазерной резки -- установку Platino от группы компаний Prima Industrie со стандартной рабочей зоной 1500 x 3000 мм и автоматическим устройством смены паллет, что дало мощный импульс развитию бизнеса. В 2002 году мы начали строительство нового головного подразделения, где мы также установили комбинированный станок для пробивки и лазерной резки от Finn Power с CO2-лазером мощностью 2,5 кВт, который мы использовали до прошлого года. Это был выбор, обусловленный желанием максимально автоматизировать цикл обработки, поэтому мы решили объединить станок со складской ГПС Night Train, состоящей из 10 башенных накопителей и 12 секций. Это была инновационная и эффективная организация производства, которая позволила дать мощный импульс нашему бизнесу, работавшему без сбоев до 18 января 2018 года, когда в нашем цехе обработки листового металла случился пожар, вынудив нас на несколько месяцев передать обработку стали на аутсорсинг. Мы также начали заменять то, что пришло в негодность, возвращая всех ведущих игроков на рынке, пусть даже в конечном итоге мы предпочли продолжить технологический путь, по которому мы пошли несколько лет назад, и сделали выбор в пользу Prima Power, единственной системы, которая обеспечила преемственность после поглощения компании Finn Power. Может показаться, что это был выбор, основанный на симпатии, но я уверяю вас, что мы действительно пустили все в ход, проанализировав сильные и слабые стороны каждого решения. В конце концов, точно осознавая, что нам нужно, мы пришли к выводу, что Prima Power является системой, которая в наибольшей степени соответствует нашим производственным ожиданиям и нашим потребностям, в том числе с точки зрения планировки завода.»
«Мы приняли решение под знаком преемственности», – добавляет Андреа Салати Кьодини. «Сроки тоже играют роль, поскольку благодаря возможности использования одной и той же складской системы мы сэкономили месяцы на сокращении времени операций установа. Это был мудрый выбор, так как он соответствовал нашему желанию сократить время простоя до минимума, и к тому же, прибегая к услугам внешних партнеров для обработки листового металла, никогда нельзя по-настоящему быть хозяином положения, как в плане сроков, так и в плане уровня качества, к которому привыкли наши клиенты.»
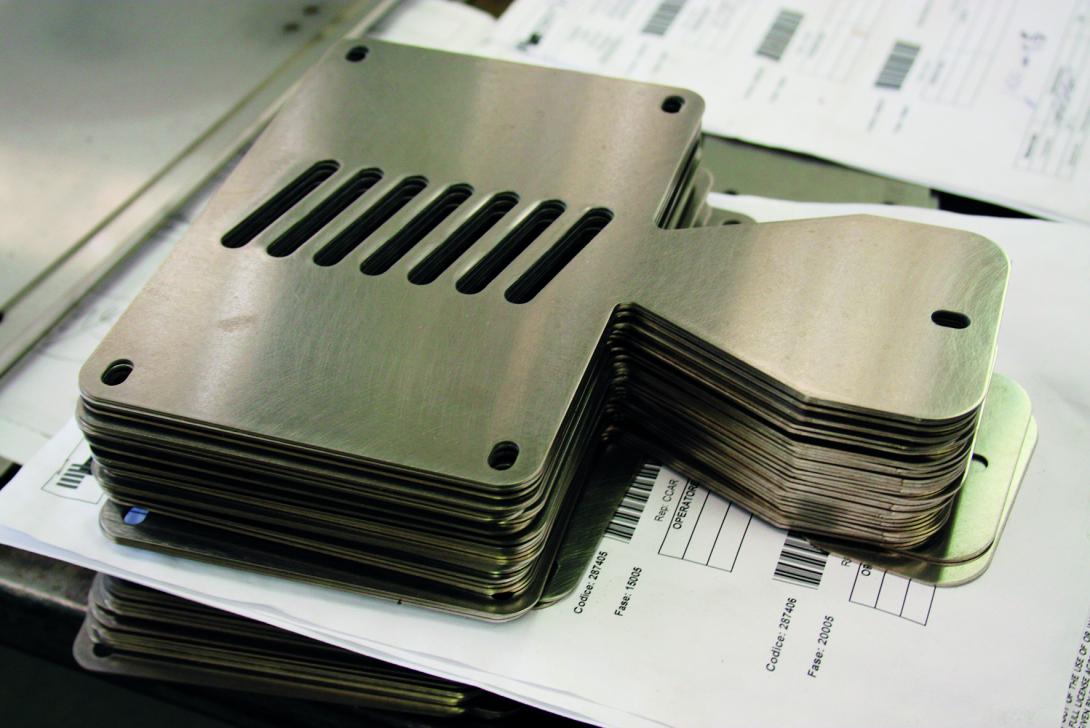
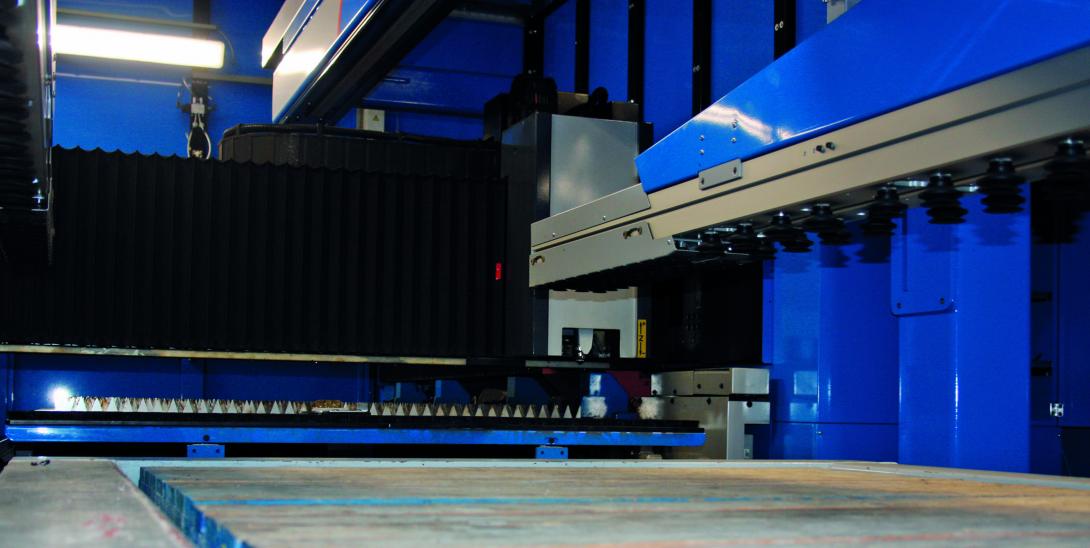
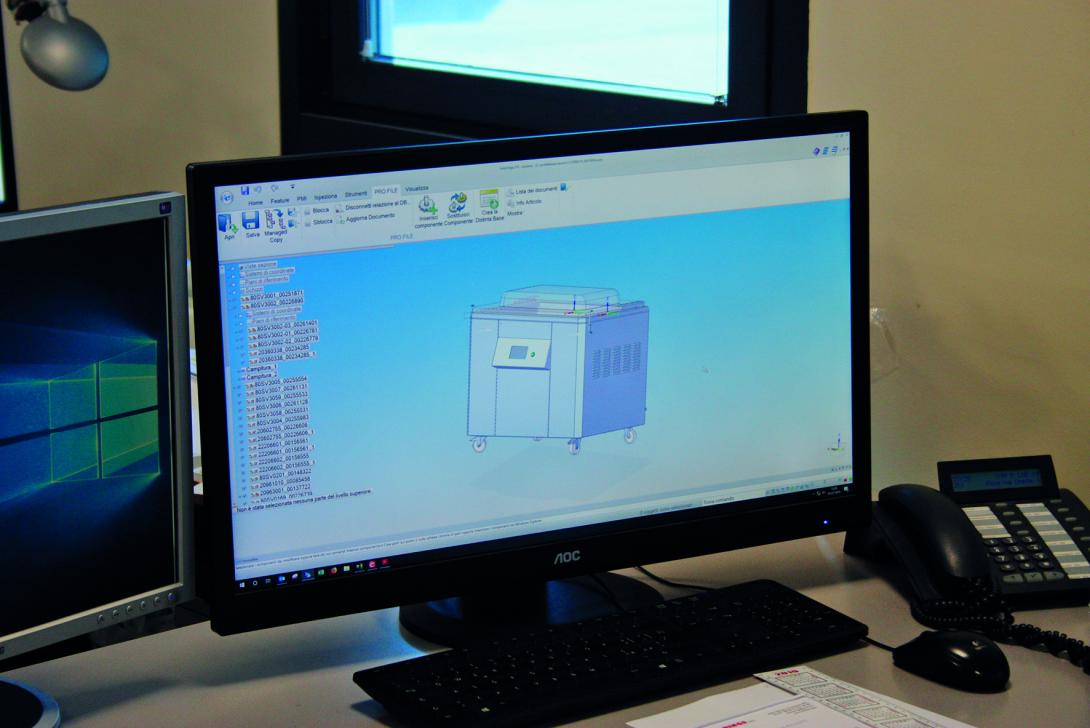
По-настоящему индивидуальная система
Сегодня, излишне говорить, что новым сердцем производства группы компаний Minerva Omega опять же является система Night Train, состоящая из 14 накопителей и 200 секций, которая выделяется как ультрасовременная в области автоматизированных складских систем. Она объединена с комбинированным станком для пробивки и лазерной резки Prima Power Combi Genius 1530с волоконным лазером мощностью 4 кВт и погрузочно-разгрузочным и штабелирующим роботом LSR6, а также с установкой двухмерной лазерной резки Prima Power Laser Genius 1530 с линейными двигателями, оснащенной источником волоконного лазера мощностью 6 кВт, погрузочно-разгрузочным роботом LU для листового металла и роботом LST для автоматической сортировки и укладки деталей.
Мы размышляли над четырьмя схемами компоновки, пытаясь оптимизировать систему в соответствии с имеющимся пространством, выкраивая по мере возможности даже по 15/20 см, чтобы предусмотреть каждую мелочь, такую как проем для проезда вилочного погрузчика, либо потоки выгрузки стружки/отходов, либо дверцы для доступа оператора,» продолжал Салати Кьодини. «В этой связи я хотел бы подчеркнуть огромную готовность и способность Prima Power создавать действительно индивидуальные решения, поскольку они представили себя на нашем месте, чтобы лучше понять наши проблемы, и не стали предлагать короткие пути с точки зрения стандартных решений. Они сразу поняли важность предложения полностью автоматизированной производственной системы,, способной производить полуфабрикаты, которые сразу же готовы к следующим этапам производства. Подается листовой металл, и на выходе получается готовое изделие с требуемым качеством обработки поверхности. Для нас это всегда было выигрышным аспектом и результатом того, что мы привыкли работать 24 часа в сутки, 7 дней в неделю. Технология достигла такого высокого уровня надежности, что мы можем запустить раскрой в пятницу днем, а в понедельник утром получить все подготовленные к сортировке детали в зоне гибки, – где также был установлен сервоэлектрический листогибочный пресс Prima Power eP-0520 – и в зоне сборки; то важный аспект для нас, чтобы иметь возможность планировать нашу работу, сокращать время простоя и минимизировать количество брака.»
Комбинированный станок или установка лазерной резки?
Сейчас компоновка системы Prima Power Night Train позволяет компании Minerva Omega заниматься как единичным производством, так и серийным производством полуфабрикатов, которые также могут храниться в складской системе. Обработка на заказ включает и иностранные заказы, характеризующиеся большими объемами. Заказ вводится в систему управления предприятием, формируется ориентировочная дата поставки (в соответствии с ожиданиями клиента) и запускается производство. Система управления ресурсами предприятия (MRP) обрабатывает всю информацию, от заказов до поставщиков компонентов, а также внутренние операции по удалению стружки и резке листового металла. Каждый этап производственного цикла распределяется при помощи средства комплексного планирования, которое логично и эффективно управляет технологическим процессом на различных станках в цехе, также отслеживает все этапы выполнения вплоть до сборки и поставки изделия. Что касается запусков производства с учетом производительности системы Prima Power Night Train, в компании Minerva стараются использовать операции раскладки и раскроя таким образом, чтобы получить как можно меньше отходов, максимально оптимизируя обработку.
«Имея детали, на 90% изготовленные из листа нержавеющей стали, мы всегда можем создать оптимальную раскладку для раскроя, подобрав наилучшие сочетания деталей и даже расходных материалов в соответствии с рабочими заданиями, которые предстоит обработать. Мы стараемся собрать в раскладке как можно больше деталей для раскроя, чтобы процент заполнения листа составлял 85%», – поясняет Салати Кьодини.
Также было интересно понять, какие аспекты принимаются во вниманиепри принятии решения о том, следует ли обрабатывать заготовку данного типа на комбинированном станке Combi Genius или на установке лазерной резки Laser Genius. В данном случае ответ Салати Кьодини был ясным и недвусмысленным: «Детали, требующие только резки, и детали из толстых листов мы изготавливаем на установке лазерной резки, в то время каквсе те детали, которые требуют других видов обработки, таких как формовка, выполнение отверстий под резьбу, тиснение, высечка и прорезание пазов, мы изготавливаем на комбинированном станке . Однако если бы мне пришлось провести сравнение с прошлым, когда у нас были CO2-лазеры вместо волоконных лазерных источников, я бы сказал, что наиболее очевидным аспектом, возможно, является тот, который связан с потреблением энергии, поскольку мы получаем довольно значительную экономию, если учесть, что один комбинированный станок потреблял около 80 кВт, в то время как сегодня с обеими системами мы не достигаем этой цифры.
Волоконный лазер требует минимального обслуживания и в большинстве случаев гарантирует лучший и более тонкий рез, и это относится как к комбинированному станку Combi Genius мощностью 4 кВт, так и к установке Laser Genius мощностью 6 кВт, которые обеспечивают сопоставимую производительность резки.
Установка Laser Genius, обладая более высокой мощностью при той же обрабатываемой толщине, обеспечивает чуть более высокое качество и более короткое время обработки. Однако я бы сказал, что в обоих случаях при толщине до 15 мм мы можем получить практически идеальное качество резки в соответствии с положениями сертификации, которые мы проходим. Более того, получение качественно обработанного реза без заусенцев означает, что мы можем избежать повторной обработки деталей с целью их зачистки или шлифовки. Все это предполагает сокращение времени и ощутимую экономическую выгоду с благоприятным результатом для конечного пользователя.»
Переведено, отредактировано и перепечатано с разрешения журнала Deformazione, октябрь 2019 г.
Волоконный лазер требует минимального обслуживания и в большинстве случаев гарантирует лучший и более тонкий рез, и это относится как к комбинированному станку Combi Genius мощностью 4 кВт, так и к установке Laser Genius мощностью 6 кВт, которые обеспечивают сопоставимую производительность резки.
Вы ищете аналогичное решение для вашей компании? Найдите его здесь
Комбинированный пробивной пресс с лазером Combi Genius
КОМБИНИРОВАННЫЕ ПРОБИВНЫЕ/ЛАЗЕРНЫЕ СТАНКИ