
Díky Night Train k vyšší produktivitě

Minerva Group v Bologni v Itálii je společnost, která skutečně ztělesňuje dovednosti, technologie a podnikatelského ducha.
Jasné nápady a odhodlání jsou vlastnosti, které umožnily Andreovi Salatimu Chiodinimu, CIO a technickému řediteli skupiny, zaměřit se v dílně na automatizaci procesů. To společnosti umožnilo získat náskok před konkurencí v přísně regulovaném světě strojů pro potravinářský průmysl. Toho bylo dosaženo instalací plně automatizovaného a integrovaného systému Night Train Flexible Manufacturing System (FMS) od společnosti Prima Power, který je schopen vyrábět polotovar, který je okamžitě připraven k dalším výrobním krokům.
Skupina Minerva Omega, jejíž mezinárodní renomé bylo dále posíleno moderním, vítězným systémem řízení, se dnes může pochlubit jednou z nejrozsáhlejších produktových řad na trhu a dobře zavedeným portfoliem zákazníků, kteří jsou zastoupeni ve všech potravinářských odvětvích, v hromadném maloobchodě i prostřednictvím prodejců ve všech zemích světa. Salati Chiodini je spolu se svým bratrem a sestrou již třetí generací rodiny, která stojí v čele této historické a dlouholeté průmyslové společnosti.
Minerva Omega Group s.r.l. vznikla v roce 2012 spojením dvou historických společností, Minerva z Bologne a Omega Ceg z Varese. Obě společnosti mají dlouhou historii, tradici a zkušenosti. Minerva, která oslaví v roce 2020 75 let své činnosti, byla založena v roce 1945 v Bologni, v oblasti se silnou strojírenskou tradicí, díky podnikatelské iniciativě Maria Chiodiniho, dědečka současných majitelů. Navrhuje a vyrábí stroje pro zpracování masa, gastronomii, potravinářský průmysl, balicí centra a nabízí vysoce kvalitní sortiment výrobků s vynikajícím poměrem ceny, kvality a životnosti.
„Jsme jedním z nejstarších rodinných podniků v Itálii,“ vysvětluje Andrea Salati Chiodini. „Právě díky tomuto podnikatelskému vedení a marketingově orientovanému manažerskému myšlení jsme dovedli Minervu k akvizici a začlenění některých našich konkurentů: nejprve boloňského Artexu, poté Omegy, vlastníka dalších historických značek, jako jsou Ceg, General Machine, Regina, Suprema a nedávno Aria a Mincer2000, což jsou všechno značky, které jsou dobře známé odborníkům v oboru po celém světě.“
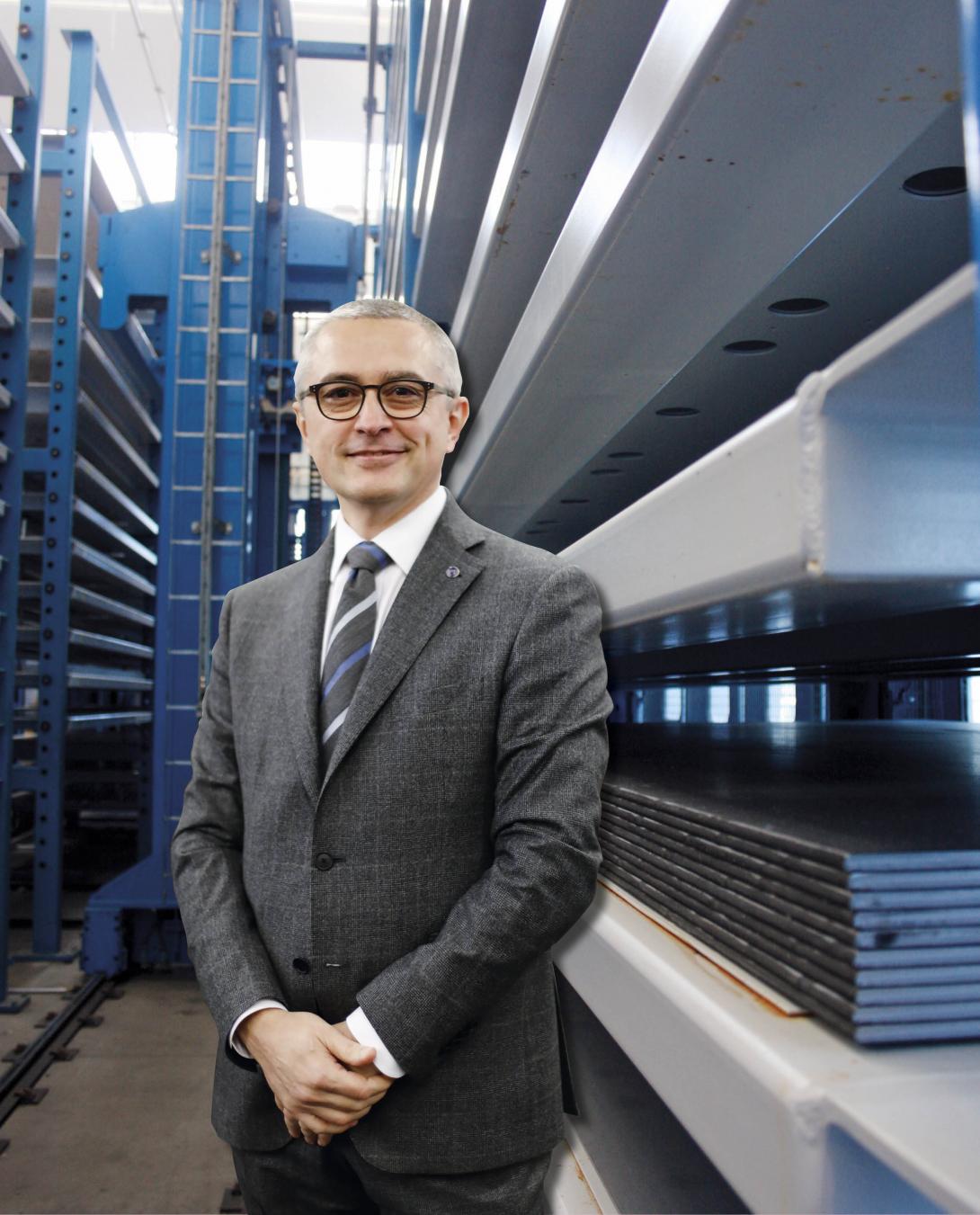
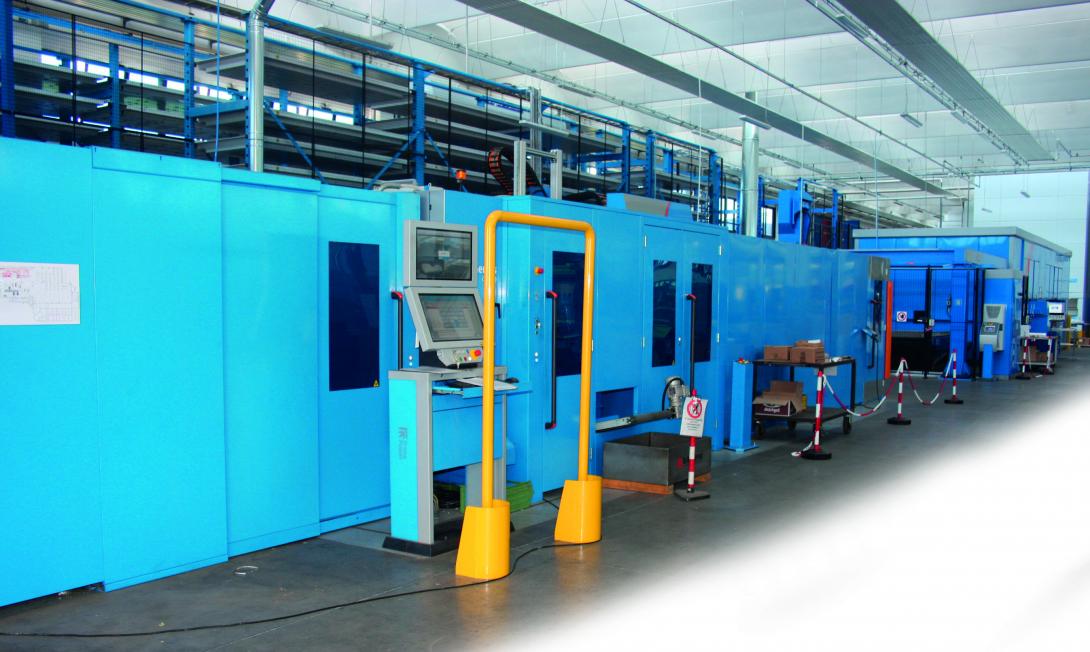
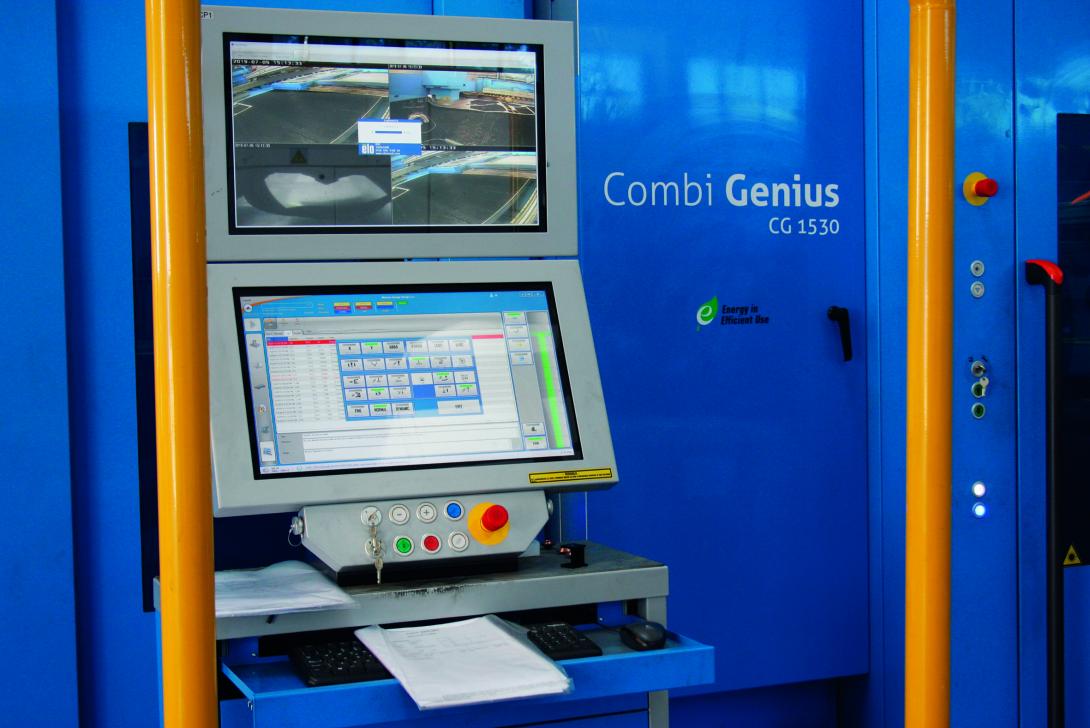
Italská dokonalost
Minerva Omega Group je dobře zavedeným celoitalským příkladem významného postavení v oboru, se silnou investiční schopností v oblasti konstrukce a vývoje nových modelů, automatizovaných zařízení a výrobních linek. „Věříme v kvalitu práce, která je důkazem velkého skupinového nasazení našich zaměstnanců a spolupracovníků,“ vysvětluje Salati Chiodini.
„Navzdory velkým obtížím a konkurenci ze zemí, kde je výroba mnohem levnější, bráníme a podporujeme značku Made-in-Italy ze všech sil, aniž bychom přesunuli výrobu hlavních komponentů a montáž strojů ze závodů v Bologni a Varese.“
Závazek je významný... a investice, které nás udržují technologicky a kvalitativně konkurenceschopné, jsou prováděny pravidelně a zahrnují celý dodavatelský řetězec. Dokonalost, konkurenceschopnost a kvalita jsou pro nás základními hodnotami. Pokračující růst společnosti na všech trzích je nejlepší odpovědí na otázku, zda se dnes ještě vyplatí investovat do italské výroby.“
Hlavní technologická volba
Poslání společnosti Minerva Omega Group je jasné. Před časem se společnost vydala na cestu k automatizace nejmodernějších výrobních procesů, a to nejen s ohledem na konkurenceschopnost, ale i v souladu s kvalitativními standardy, které vyžadují platné předpisy pro potravinářské stroje.
„První automatické stroje jsme představili v roce 1984,“ říká Salati Chiodini. „Jednalo se o obráběcí stroje pro odstraňování třísek, protože náš produkt dříve vznikal zpracováním odlitků. Ve skutečnosti se používalo jen velmi málo plechů a jejich zpracování se zadávalo externě. Kolem roku 1994/95 jsme však začali vnímat změnu na trhu. Kromě funkčnosti se od strojů začala vyžadovat i určitá estetická hodnota. Proto jsme zavedli nerezovou ocel a začali vyrábět některé stroje z tohoto materiálu, přičemž jsme se nadále spoléhali na subdodavatele.“
„V roce 1998 jsme se rozhodli zakoupit náš první laserový řezací systém – Prima Industrie Platino systém s typickou pracovní plochou 1 500 x 3 000 mm a automatickou výměnou palet, čímž se podnikání silně rozjelo. V roce 2002 jsme začali stavět nové sídlo, kde jsme také instalovali kombinaci laseru a děrovačky Finn Power se zdrojem CO2 o výkonu 2,5 kW, který jsme používali až do loňského roku. Tato volba vycházela z touhy co nejvíce automatizovat cyklus zpracování, a proto se jsme se rozhodli kombinovat stroj se skladovací jednotkou Night Train FMS, která má 10 věží s 12 zásuvkami. Jednalo se o inovativní a efektivní organizaci výroby, která nám poskytla silný impuls pro podnikání bez problémů až do 18. ledna 2018, kdy naše oddělení plechů zpustošil požár, který nás donutil na několik měsíců zadat zpracování oceli externím dodavatelům. Začali jsme také nahrazovat to, co bylo zničeno a vrátili jsme na stůl všechny hlavní hráče na trhu, i když jsme nakonec raději pokračovali v technologické cestě, kterou jsme se vydali před několika lety a rozhodli jsme se pro Prima Power, jediný systém, který nám po převzetí Finn Power zajistil kontinuitu. Mohlo by se zdát, že šlo o výběr na základě sympatií, ale ujišťuji vás, že jsme do hry zapojili opravdu všechny analýzou silných a slabých stránek řešení každého z nich. Nakonec jsme si přesně uvědomili, co potřebujeme. Ukázalo se, že systém Prima Power nejvíce odpovídá našim výrobním očekáváním a potřebám i z hlediska uspořádání zařízení.“
„Rozhodli jsme se ve znamení kontinuity,“ dodává Andrea Salati Chiodini. „Také z časového hlediska, protože možnost používat stejnou skladovací jednotku nám umožnila zkrátit dobu instalace o několik měsíců. Byla to moudrá volba, která je v souladu s naším přáním zkrátit prostoje na co nejmenší možnou míru i proto, že při využívání externích partnerů pro zpracování plechů nelze nikdy skutečně zvládnout situaci jak z hlediska časového, tak z hlediska úrovně kvality, na kterou byli naši zákazníci zvyklí.“
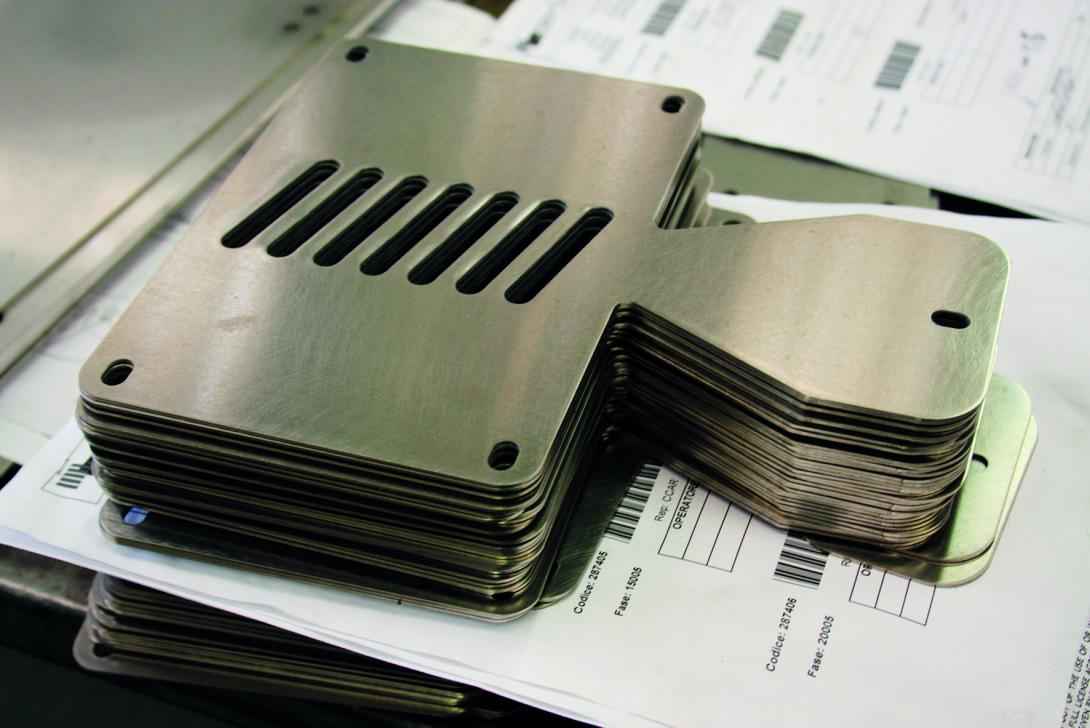
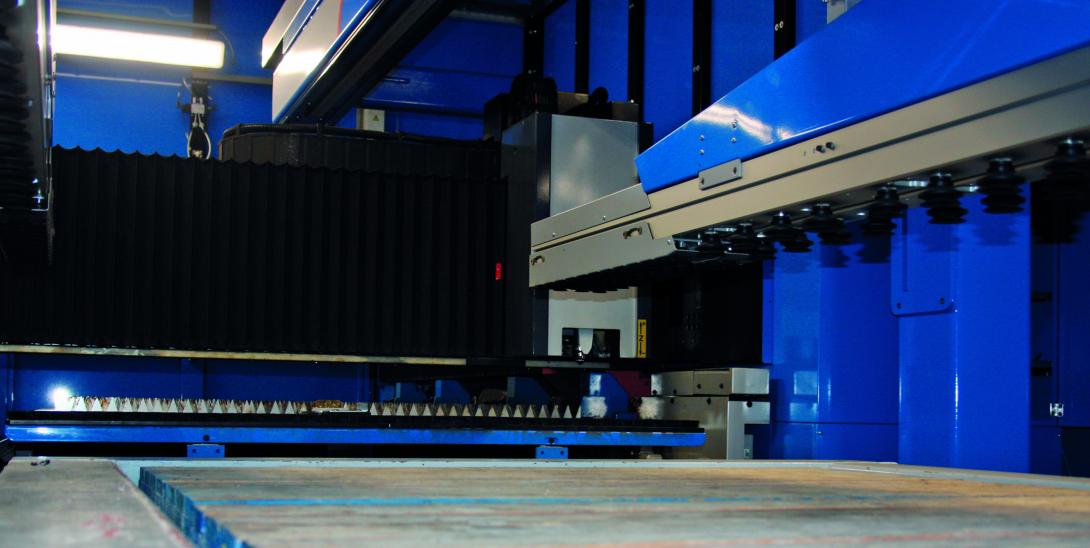
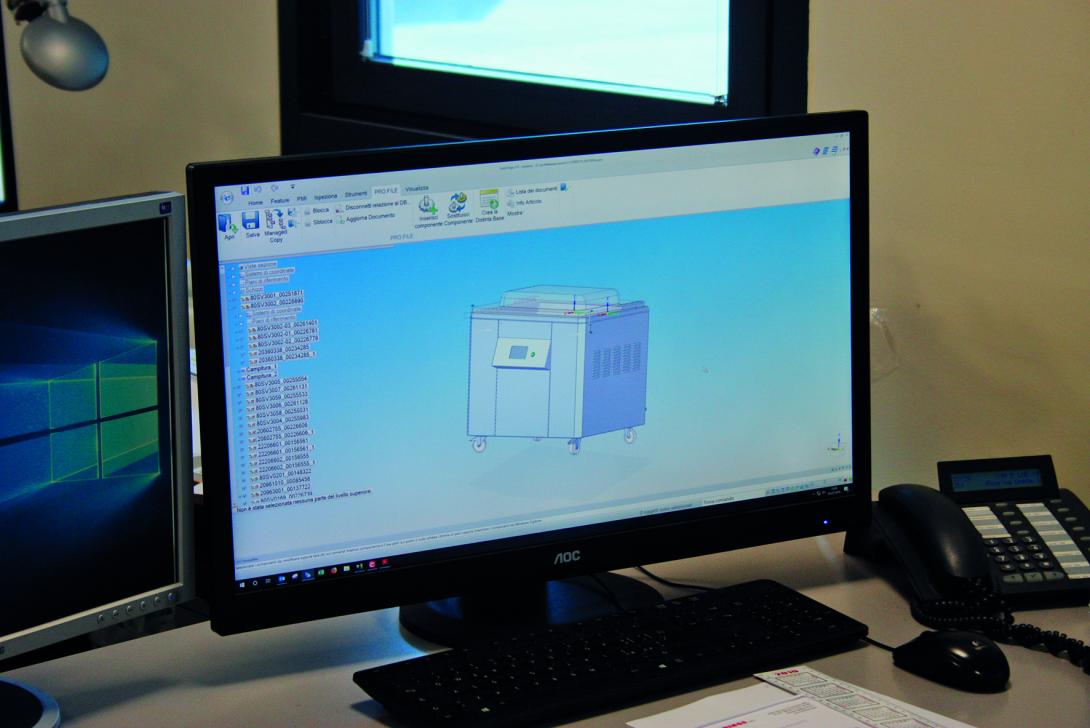
Skutečně na míru šitý systém
Dnes je samozřejmé, že novým tepajícím srdcem výroby společnosti Minerva Omega stále zůstává systém Night Train, který se skládá ze 14 bloků a 200 zásuvek a který vyniká jako nejmodernější v oblasti automatizovaných skladovacích jednotek. K němu je připojen k děrovací/laserový řezací stroj Prima Power Combi Genius 1530 s vláknovým laserem o výkonu 4 kW a LSR6 nakládací/vykládací a stohovací robot a také 2D řezací vláknový laserem Prima Power Laser Genius 1530 s lineárními motory, vybavený vláknovým zdrojem o výkonu 6 kW, robotem pro nakládání a vykládání plechů LU a automatickým třídicím a stohovacím robotem LST.
„Spekulovali jsme o čtyřech uspořádáních, protože jsme se snažili optimalizovat systém v dostupném prostoru tím, že jsme tam, kde to bylo možné, upravili třeba jen 15/20 cm, abychom vylepšili každý detail, jako je průjezd vysokozdvižného vozíku nebo toky vykládky třísek či přístupové dveře pro obsluhu,“ pokračuje Salati Chiodini. „V této souvislosti bych rád zdůraznil velkou ochotu a schopnost společnosti Prima Power vytvořit produkt skutečně na míru, protože se skutečně vžili do naší situace, aby lépe porozuměli našim problémům, a nikdy nenavrhovali zkratky ve smyslu standardních řešení. Okamžitě pochopili, že je důležité nabízet zcela automatizovaný výrobní systém, který dokáže vyprodukovat polotovar, jenž je okamžitě připraven k dalším krokům. Plech je vložen dovnitř a hotový výrobek s požadovanou úrovní povrchové úpravy je vyveden ven. Pro nás to byl vždy vítězný aspekt a výsledek toho, že jsme zvyklí pracovat 24 hodin denně, 7 dní v týdnu. Technologie dosáhla tak vysoké úrovně spolehlivosti, že můžeme v pátek odpoledne spustit prosces rozmístění dílů na materiál a v pondělí ráno mít všechny díly připravené k vytřídění v ohýbárně - kde byl nainstalován servoelektrický ohraňovací lis Prima Power eP-0520 - a v oblasti montáže. To je pro nás zásadní aspekt, abychom byli schopni plánovat naši práci, zkrátit prostoje a minimalizovat zmetky.“
Kombinovaný stroj nebo laserové řezání?
Instalační uspořádání systému Prima Power Night Train dnes umožňuje společnosti Minerva Omega provozovat jak výrobu na zakázku, tak i mít zásoby na základě rozpracované výroby se skladovací jednotkou, která se používá i pro skladování polotovarů. Zpracování na zakázku zahrnuje zahraniční objednávky, které se vyznačují velkým množstvím. Objednávka se zadá do systému řízení společnosti, vygeneruje se odhadovaný termín dodání (v souladu s očekáváním zákazníka) a zahájí se výroba. Systém MRP vyřizuje vše, od objednávek pro dodavatele obchodních komponentů až po interní operace odstraňování třísek a řezání plechů. Každá fáze cyklu je naplánována pomocí plánovacího nástroje, který logicky a efektivně řídí pracovní postup na různých strojích v dílně i v různých postupových krocích až po montáž a dodání výrobku. Co se týče spuštění výroby v souvislosti s výkonem systému Prima Power Night Train, ve společnosti Minerva se snaží využívat procesy rozmístění díl na materiál tak, aby vznikalo co nejméně zmetků a zároveň se co nejvíce optimalizovalo zpracování.
„Vzhledem k tomu, že díly jsou z 90 % vyrobeny z nerezového plechu, daří se nám skvěle procesy rozmístění dílů na materiál, který najde nejlepší kombinaci dílů, dokonce i spotřebního materiálu, podle zpracovávaných zakázek. Snažíme se srozmístit co nejvíce kusů na materiál, abychom dosáhli 85% naplnění plechu,“ vysvětluje Salati Chiodini.
Bylo také zajímavé pochopit, jaké aspekty jsou brány v úvahu při rozhodování o tom, zda má být daný typ dílu zpracováván na zařízení Combi Genius nebo na řezacím systému Laser Genius. V tomto případě byla odpověď společnosti Salatimu Chiodinimu jasná a jednoznačná: „Na laserovém zpracovávat pouze díly určené k řezání nebo tlusté díly, zatímco kombinovanou jednotku používáme k výrobě všech těch dílů, které potřebují další pracovní postupy, jako jsou deformace, otvory se závitem, ražení, zářezy a drážky. Pokud bych však měl provést srovnání s minulostí, kdy jsme měli CO2 lasery místo vláknových zdrojů, řekl bych, že nejzřetelnějším aspektem je asi ten, který se týká spotřeby energie, protože máme poměrně výrazné úspory. Dříve jen kombinovaný stroj spotřebovával asi 80 kW, zatímco dnes s oběma stroji tohoto čísla nedosahujeme.
Vláknový laser vyžaduje velmi malou údržbu a ve většině případů zaručuje lepší a jemnější řez, což platí jak pro 4kW kombinovaný stroj, tak pro 6kW Laser Genius, které zajišťují srovnatelný řezný výkon.
Laser Genius má vyšší výkon a při stejné tloušťce dosahuje o něco lepší kvality a kratšího času. Řekl bych však, že v obou případech, až do tloušťky 15 mm, můžeme dosáhnout prakticky dokonalé kvality řezu v souladu s ustanoveními certifikací, kterým podléháme. Díky tomu, že máme co nejlépe dokončený řez bez otřepů, se navíc vyhneme opětovnému opracovávání kusů pískováním nebo broušením. To vše znamená zkrácení času a značné ekonomické výhody s příznivým dopadem na koncového zákazníka.“
Přeloženo, upraveno a přetištěno se svolením časopisu Deformazione, říjen 2019.
Vláknový laser vyžaduje velmi malou údržbu a ve většině případů zaručuje lepší a jemnější řez, což platí jak pro 4kW kombinovaný stroj, tak pro 6kW laser Genius, které zajišťují srovnatelný řezný výkon.
Hledáte pro svou společnost podobné řešení? Najdete ho zde
Combi Genius
DĚROVACÍ A LASEROVÉ ŘEZACÍ STROJE KOMBINOVANÉ