
De Night Train naar hogere productiviteit rijden

De Minerva Group in Bologna, Italië is een bedrijf dat vakmanschap, technologie en ondernemersgeest echt belichaamt.
Heldere ideeën en vastberadenheid zijn de eigenschappen die het Andrea Salati Chiodini, de CIO en technisch manager van de Groep, mogelijk maakten zich te concentreren op de procesautomatisering in de werkplaats. Zo kon het bedrijf een voorsprong nemen op de concurrentie in de sterk gereglementeerde wereld van machines voor de voedingsmiddelenindustrie. Dit werd bereikt door de installatie van het volledig geautomatiseerd en geïntegreerd Nachttrein Flexibel Productie Systeem (FMS) van Prima Power, in staat om een halffabrikaat te produceren dat meteen klaar is voor de volgende productiestappen.
Vandaag kan de Minerva Omega Groep, waarvan de internationale reputatie nog versterkt werd door een modern, winnend managementsysteem, dan ook bogen op een van de meest uitgebreide productengamma’s op de markt, and een gevestigde klantenportefeuille met aanwezigheid in elke levensmiddelensector, in de grootwinkelbedrijven en via dealers in alle landen van de wereld. Salati Chiodini staat, samen met zijn broer en zus, als derde generatie van de familie aan het roer van deze historische en langlevende industriële onderneming.
Minerva Omega Group s.r.l. ontstond in 2012 uit de fusie van twee historische bedrijven, Minerva uit Bologna en Omega Ceg uit Varese. Beide bedrijven hebben een lange geschiedenis, traditie en ervaring. La Minerva, dat in 2012 zijn 75 jaar in bedrijf in 2020, werd opgericht in 1945 in Bologna, een streek met een sterke mechanische en ingenieurstraditie, dankzij het ondernemersinitiatief van Mario Chiodini, de grootvader van de huidige eigenaars. Het ontwerpt en vervaardigt machines voor vleesverwerking, catering, de voedselverwerkende industrie, verpakkingscentra, en biedt een assortiment producten van hoge kwaliteit met een uitstekende prijs-kwaliteitverhouding en levensduur.
“We zijn een van de oudste familiebedrijven in Italië,” verklaart Andrea Salati Chiodini. “Juist door dit ondernemende leiderschap en een marketinggerichte managementmentaliteit hebben we Minerva ertoe gebracht enkele van onze concurrenten over te nemen en in te lijven: eerst het in Bologna gevestigde Artex, daarna Omega, eigenaar van andere historische merken als Ceg, General Machine, Regina, Suprema en, recentelijk, Aria en Mincer2000, allemaal merken die bij deskundigen in het vak wereldwijd bekend zijn..”
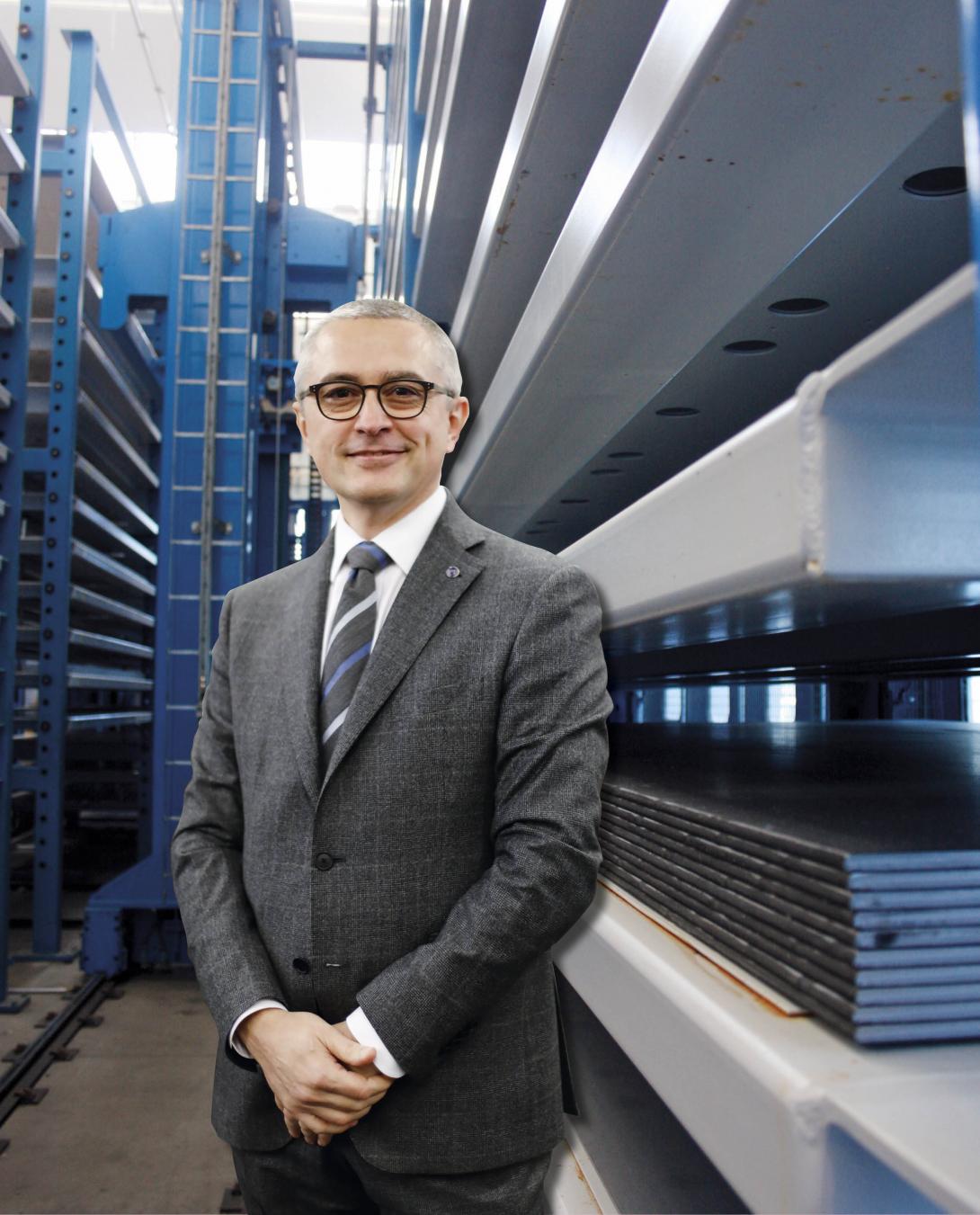
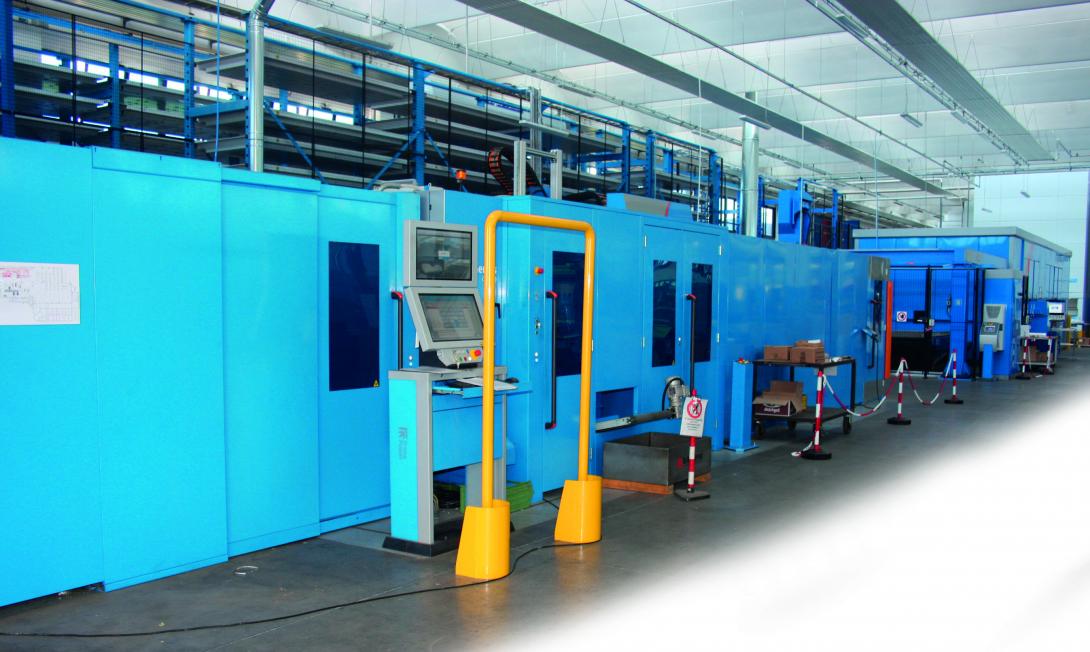
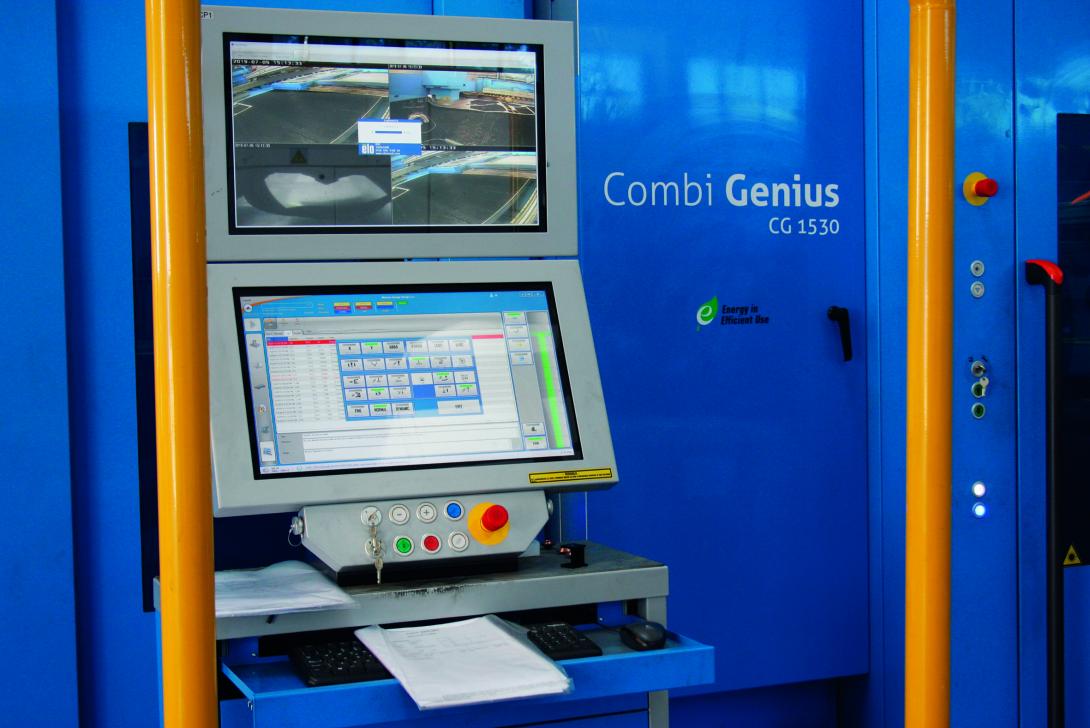
Compleet Italiaanse Excellentie
De Minerva Omega Groep is een gevestigd geheel Italiaans voorbeeld van vooraanstaandheid in de sector, met een sterk investeringsvermogen in het ontwerp en de ontwikkeling van nieuwe modellen, in geautomatiseerde apparatuur en productielijnen. “Wij geloven in de kwaliteit van het werk, het bewijs van een grote inzet van de groep, uitgevoerd door onze medewerkers en medewerkers,” verklaart Salati Chiodini.
“Ondanks de grote moeilijkheden en de concurrentie van landen waar de fabricage veel goedkoper is, verdedigen en ondersteunen wij het merk Made-in-Italy met alle kracht, zonder de productie van hoofdonderdelen en de assemblage van machines uit de fabrieken in Bologna en Varese te verplaatsen.”
Verbintenis is belangrijk… en investeringen, om ons technologisch en kwalitatief concurrerend te houden, worden regelmatig gedaan en betrekken de hele toeleveringsketen erbij. Uitmuntendheid, concurrentievermogen en kwaliteit zijn voor ons dwingende waarden. De aanhoudende groei van de onderneming op alle markten is het beste antwoord op de vraag of het vandaag nog de moeite waard is in Italiaanse productie te investeren.”
Een belangrijke technologische keuze
De missie van Minerva Omega Group is duidelijk. Enige tijd geleden begaf de onderneming zich op een weg naar het automatiseren van de meest geavanceerde fabricageprocessen, niet alleen om concurrerend te zijn, maar ook om te voldoen aan de kwaliteitsnormen die de geldende verordeningen inzake voedselmachines opleggen.
“We introduceerden de eerste automatische machines in 1984,” zegt Salati Chiodini. “Het waren spaanverwijderingsmachines, omdat ons produkt vroeger voortkwam uit de bewerking van gegoten lichamen. Er werd eigenlijk maar heel weinig plaatwerk gebruikt, en de verwerking ervan werd uitbesteed. Rond 1994/95 begonnen we echter een verandering in de markt waar te nemen. Behalve functionaliteit begon men ook een zekere esthetische waarde voor machines te eisen. Daarom introduceerden we roestvrij staal en begonnen we enkele machines met dit materiaal te vervaardigen, terwijl we een beroep bleven doen op onderaannemers.”
”In 1998 besloten we onze eerste lasersnij-installatie te kopen — een Prima Industrie Platino systeem, met een typisch werkgebied van 1.500 x 3.000 mm en een automatische palletwisselaar, en geeft zo een sterke impuls aan het bedrijf. In 2002 begonnen we met de bouw van deze nieuwe hoofdkanrevolver, waar we ook een Finn Power laser/pons combinatie installeerden oplossing met een CO2 bron van 2,5 kW, die we tot vorig jaar gebruikten. Het was een keuze die voortkwam uit de wens om de verwerkingscyclus zo veel mogelijk te automatiseren, en dat is de reden waarom we besloten de machine te combineren met een Night Train FMS opslagunit met 10 revolvers met 12 laden. Dit was een vernieuwende en efficiënte productieorganisatie die het ons mogelijk maakte om een sterke stimulans voor het bedrijfsleven zonder haperen tot 18 januari 2018, toen een brand onze plaatwerkafdeling teisterde, waardoor we gedwongen waren de staalbewerking een paar maanden uit te besteden. We begonnen ook met de vervanging van wat vernield was, en legden alle belangrijke spelers op de markt weer op tafel, ook al gaven we er uiteindelijk de voorkeur aan verder te gaan op de technologische weg die we enkele jaren eerder waren ingeslagen, en kozen we voor Prima Power, het enige systeem dat ons continuïteit garandeerde na de overname van Finn Power. Het lijkt misschien een keuze op basis van sympathie, maar ik verzeker je dat we echt iedereen opnieuw in het spel brachten door de sterke en zwakke punten van ieders oplossing te analyseren. Uiteindelijk, precies wetend wat we nodig hadden, Prima Power bleek het systeem te zijn dat het meest aansloot bij onze productieverwachtingen en onze behoeften ook wat betreft de inrichting van de fabriek.”
“We namen een beslissing in het teken van continuïteit,” voegt Andrea Salati Chiodini toe. “Ook wat timing betreft, want doordat we dezelfde opslagplaats konden gebruiken, konden we de installatietijd met maanden bekorten. Het was een verstandige keuze, die strookte met ons streven om de stilstandtijd tot zo weinig mogelijk te beperken ook al omdat je, door je toevlucht te nemen tot externe partners voor plaatbewerking, de situatie nooit echt onder de knie kunt krijgen, zowel wat betreft timing als wat betreft het kwaliteitsniveau dat onze klanten gewend waren.”
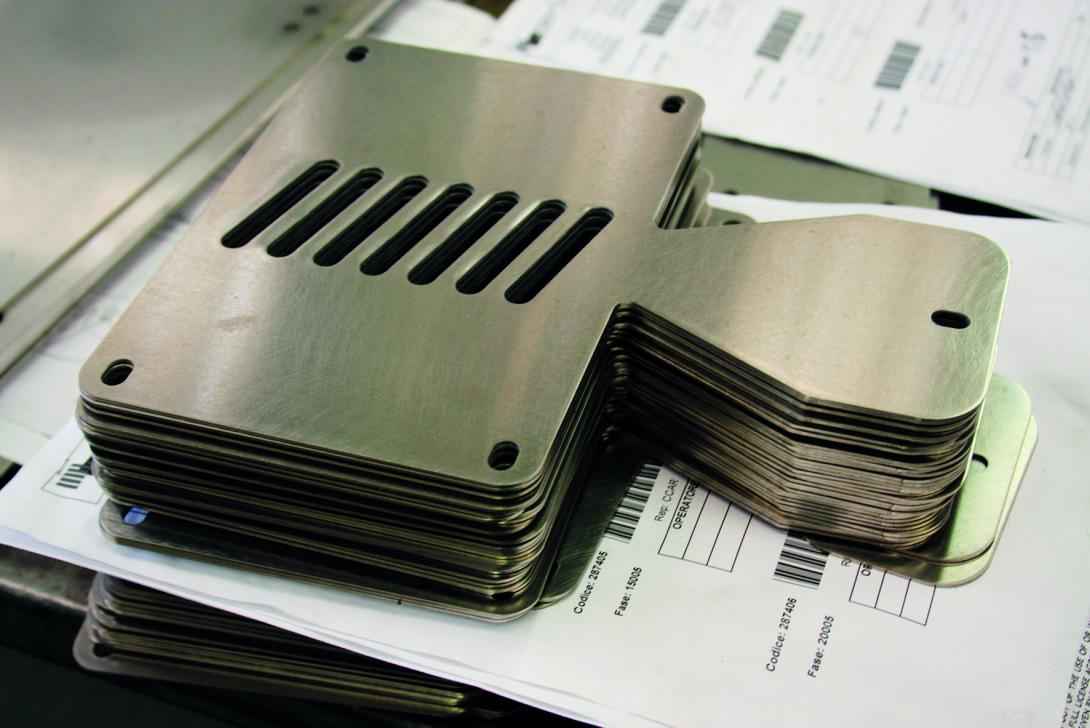
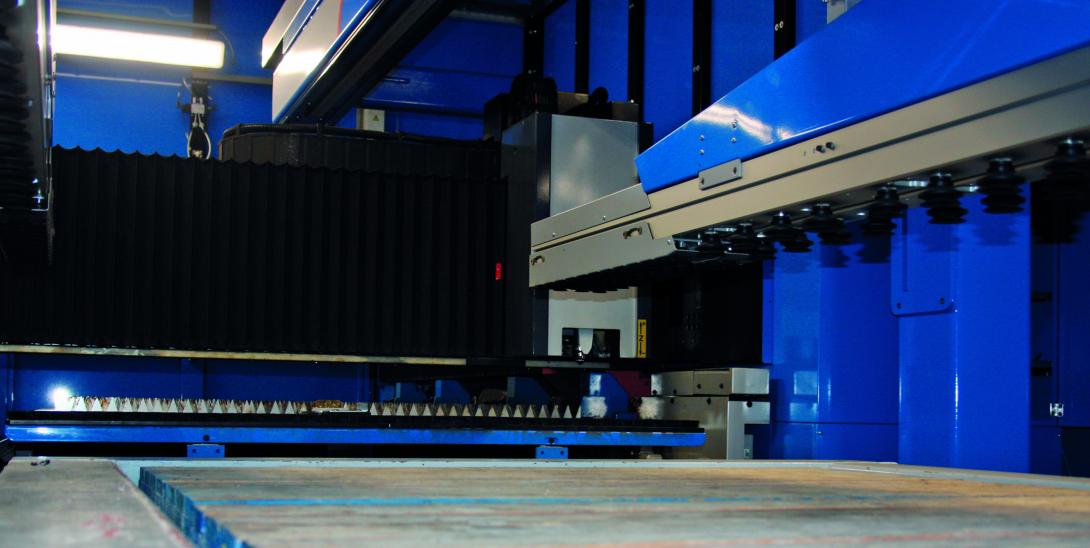
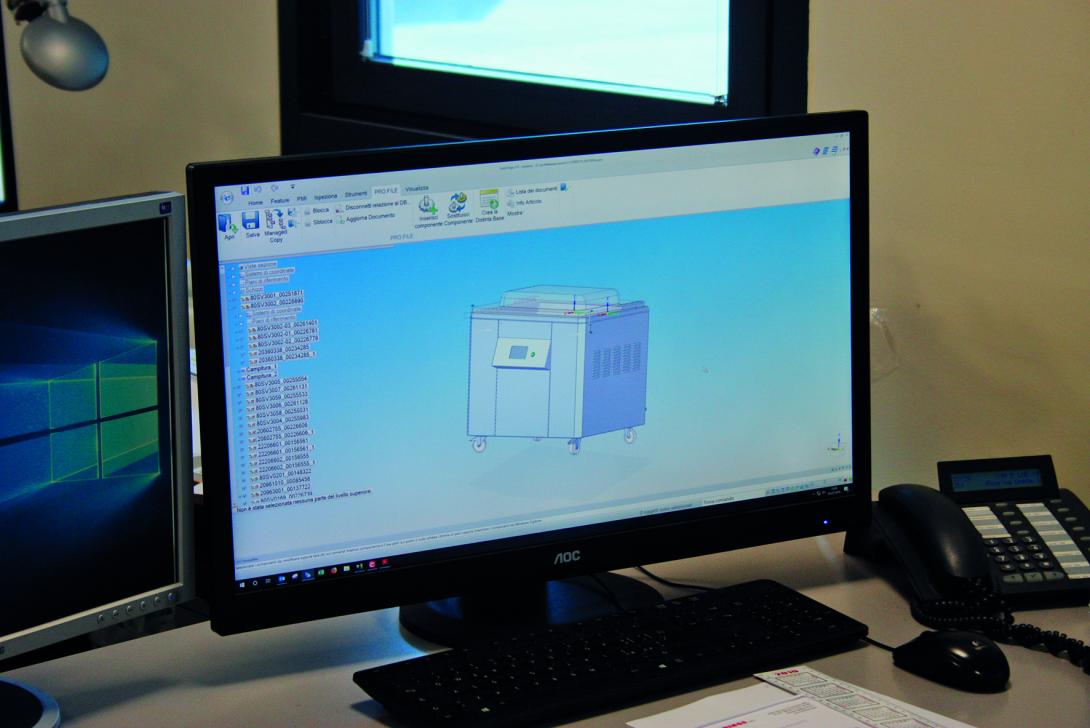
Een echt op maat gemaakt systeem
Vandaag spreekt het voor zich dat het nieuwe kloppende hart van Minerva Omega’s productie nog steeds de Nachttrein is, bestaande uit 14 blokken en 200 laden, die opvalt als state-of-the-art op het gebied van automatische opslageenheden. Hij is verbonden met de pons/lasersnijmachine Prima Power Combi Genius 1530 met 4 kW fiber laser en LSR6 laad/los- en stapelrobot, en ook een tweedimensionaal vezellasersnijsysteem Prima Power Laser Genius 1530 met lineaire motoren, voorzien van een 6 kW vezelbron, LU plaatstaal laad- en losrobot en LST automatische sorteer- en stapelrobot.
“We speculeerden op vier indelingen, want we probeerden het systeem te optimaliseren volgens de beschikbare ruimte door, waar het mogelijk was, zelfs maar 15/20 cm terug te winnen om elk klein detail te verbeteren, zoals de doorgang voor de vorkheftruck of het lossen van spaanders, of de toegangsdeuren voor de operator,” vervolgt Salati Chiodini. “In dit verband wil ik graag benadrukken Prima Power’s grote bereidwilligheid en aanpassingsvermogen om een echt op maat gemaakt product te kunnen maken, omdat ze wel in onze schoenen stapten om onze problemen beter te begrijpen, en nooit sluiproutes voorstelden in de vorm van standaardoplossingen. Ze begrepen meteen hoe belangrijk het was een totaal geautomatiseerd productiesysteem aan te bieden, in staat een halffabrikaat af te draaien dat meteen klaar is voor de volgende stappen. Plaatwerk wordt ingevoerd, en het eindproduct met de door ons gewenste afwerkingsgraad wordt naar buiten gevoerd. Voor ons is dit altijd een winnend aspect geweest en het resultaat van het gewend zijn om 24/7 te werken. De technologie heeft zo’n hoge graad van betrouwbaarheid bereikt dat we op vrijdagmiddag een nesting kunnen starten, en op maandagochtend alle onderdelen klaar hebben om in de buigruimte te worden uitgezocht – waar eenPrima Power eP-0520 servo-elektrische kantpers machine werd ook geïnstalleerd - en in de montageruimte; dit is een essentieel aspect voor ons om ons werk te kunnen plannen, de uitvaltijd verminderen, en afkeur tot een minimum beperken.”
Combinatiemachine of lasersnijden?
De installatie-indeling van Prima Power Night Train maakt het vandaag mogelijk voor Minerva Omega om zowel op bestelling te werken als op basis van werkvoorraad met de opslageenheid, die ook gebruikt wordt om halffabrikaten op te slaan. Make-to-order verwerking omvat buitenlandse bestellingen die gekenmerkt worden door grote hoeveelheden. Een bestelling wordt in het bedrijfsbeheersysteem ingevoerd, een geschatte leveringsdatum (in overeenstemming met de verwachtingen van de klant) wordt gegenereerd, en de productie wordt gestart. MRP handelt alles af, van bestellingen tot leveranciers van handelsonderdelen en ook, intern, spaanafvoer en plaatbewerkingen. Elke fase van de cyclus wordt gepland met behulp van een planningshulpmiddel dat de werkstroom op de verschillende machines in de werkplaats, en in de verschillende voortgangsstappen logisch en efficiënt beheert, tot aan de assemblage en aflevering van het product. Wat de productielanceringen betreft die te maken hebben met de prestaties van het Prima Power Night Train systeem, probeert men bij Minerva bewerkingsnesten zo uit te buiten dat er zo weinig mogelijk uitval is, terwijl de bewerking zo veel mogelijk geoptimaliseerd wordt.
“Met onderdelen die voor 90% uit roestvast stalen plaat bestaan, slagen we er steeds in uitstekende nestings te maken die de beste mix van onderdelen, zelfs van verbruiksgoederen, combineren volgens de te verwerken werkopdrachten. We proberen zoveel mogelijk stukken in de nesten te verzamelen om tot een plaatvullingspercentage van 85% te komen,” verklaart Salati Chiodini..
Het was ook interessant om te begrijpen welke aspecten beschouwd worden wanneer je beslist of een soort onderdeel op een Combi Genius of op een Laser Genius verwerkt moet worden snijsysteem. In dit geval was het antwoord van Salati Chiodini duidelijk en ondubbelzinnig: ”We maken alleen te snijden of dikke delen op het lasersysteem, terwijl we de combinatie-eenheid gebruiken om al die onderdelen te maken die andere bewerkingen nodig hebben, zoals vervormingen, draadgaten, reliëfvormen, inkepingen en sleuven. Als ik echter een vergelijking zou moeten trekken met vroeger, toen we CO2 lasers hadden in plaats van vezelbronnen, dan zou ik zeggen dat het meest voor de hand liggende aspect misschien wel dat van het energieverbruik is, want we hebben een vrij aanzienlijke besparing als je bedenkt dat de combinatiemachine alleen al ongeveer 80kWverbruikte, terwijl we dit cijfer vandaag, met beide machines, niet halen.
Fiber laser vraagt zeer weinig onderhoud en garandeert in de meeste gevallen een betere en fijnere snede, en dit geldt zowel voor de 4kW Combi machine als voor de 6kW Laser Genius, die vergelijkbare snijprestaties garanderen..
De Laser Genius, met hoger vermogen, bij gelijke dikte, slaagt erin een iets betere kwaliteit en kortere timing te krijgen. Toch zou ik zeggen dat we in beide gevallen, tot 15 mm dikte, een vrijwel perfecte snijkwaliteit kunnen krijgen, in overeenstemming met de bepalingen van de certificeringen waaraan we onderworpen zijn. Bovendien betekent het hebben van een best afgewerkte snede zonder bramen voor ons dat we het opnieuw bewerken van stukken om ze te schuren of te slijpen kunnen vermijden. Dit alles betekent tijdwinst en aanzienlijke economische voordelen met een gunstige invloed op de eindgebruiker.”
Vertaald, bewerkt, en met toestemming herdrukt door Deformazione Magazine, okt. 2019.
Fiberlaser vereist zeer weinig onderhoud en garandeert in de meeste gevallen een betere en fijnere snede, en dit geldt voor zowel de 4kW Combi machine als 6kW Laser Genius, die zorgen voor vergelijkbare snijprestaties.
Ben je op zoek naar een soortgelijke oplossing voor je bedrijf? Hier kun je het vinden
Combi Genius
PONS- EN LASERSNIJMACHINES GECOMBINEERD