
Night Train vie kohti parempaa tuottavuutta

Minerva Group Italian Bolognassa on osaamista, teknologiaa ja yrittäjähenkeä arvostava yritys.
Selkeät ideat ja päättäväisyys auttoivat konsernin tietohallinto- ja teknistä johtajaa Andrea Salati Chiodinia keskittymään konepajalla prosessiautomaatioon. Yritys pystyi saavuttamaan kilpailullisen edun voimakkaasti säädellyllä elintarviketeollisuuskoneiden toimialalla. Tämä kaikki tuli mahdolliseksi, kun yritys asensi käyttöönsä Prima Powerin täysin automaattisen ja integroidun joustavan Night Train -valmistusjärjestelmän (FMS). Se pystyy tuottamaan puolivalmiin tuotteen, joka on heti valmiudessa seuraavaan valmistusvaiheeseen.
Minerva Omega Groupin kansainvälinen maine on kasvanut nykyaikaisen hallintajärjestelmän myötä. Sillä on tänä päivänä yksi markkinoiden monipuolisimmista tuotevalikoimista, vakiintunut asiakaskanta, toimintaa jokaisella elintarvikesektorilla ja jälleenmyyjiä maapallon jokaisessa maassa. Salati Chiodini sekä hänen veljensä ja siskonsa ovat jo perheen kolmas sukupolvi, joka on tämän pitkäikäisen teollisuusyrityksen johdossa.
Minerva Omega Group s.r.l. perustettiin vuonna 2012. Se syntyi kahden historiallisen yrityksen, bolognalaisen Minervan ja vareselaisen Omega Cegin, fuusiosta. Molemmilla yrityksillä on pitkä ja perinteikäs historia ja valtavasti kokemusta. La Minerva, joka juhlisti 75-vuotista toimintaansa vuonna 2020, perustettiin vuonna 1945 Bolognassa alueella, jolla on vahvat mekaniikan ja konetekniikan perinteet. Aloitteen yrityksen perustamisesta teki Mario Chiodini, joka on nykyisen omistajan isoisä. Se suunnittelee ja valmistaa koneita lihankäsittelyn, catering-palveluiden, elintarvikekäsittelyteollisuuden ja pakkauskeskusten tarpeisiin ja tarjoaa laadukkaita tuotteita, joilla on erinomainen hinta-laatusuhde ja pitkä käyttöikä.
”Olemme yksi Italian vanhimmista perheyrityksistä”, Andrea Salati Chiodini toteaa. ”Yrityshenkinen ja markkinointipainotteinen johtaminen saivat Minervan ostamaan joitakin kilpailijoitamme: ensin vuorossa oli bolognalainen Artex, sitten Omega, joka omistaa muita historiallisia merkkejä, kuten Ceg, General Machine, Regina ja Suprema, ja viimeksi Aria ja Mincer2000, jotka kaikki ovat alansa tunnettuja merkkejä ympäri maailmaa.”
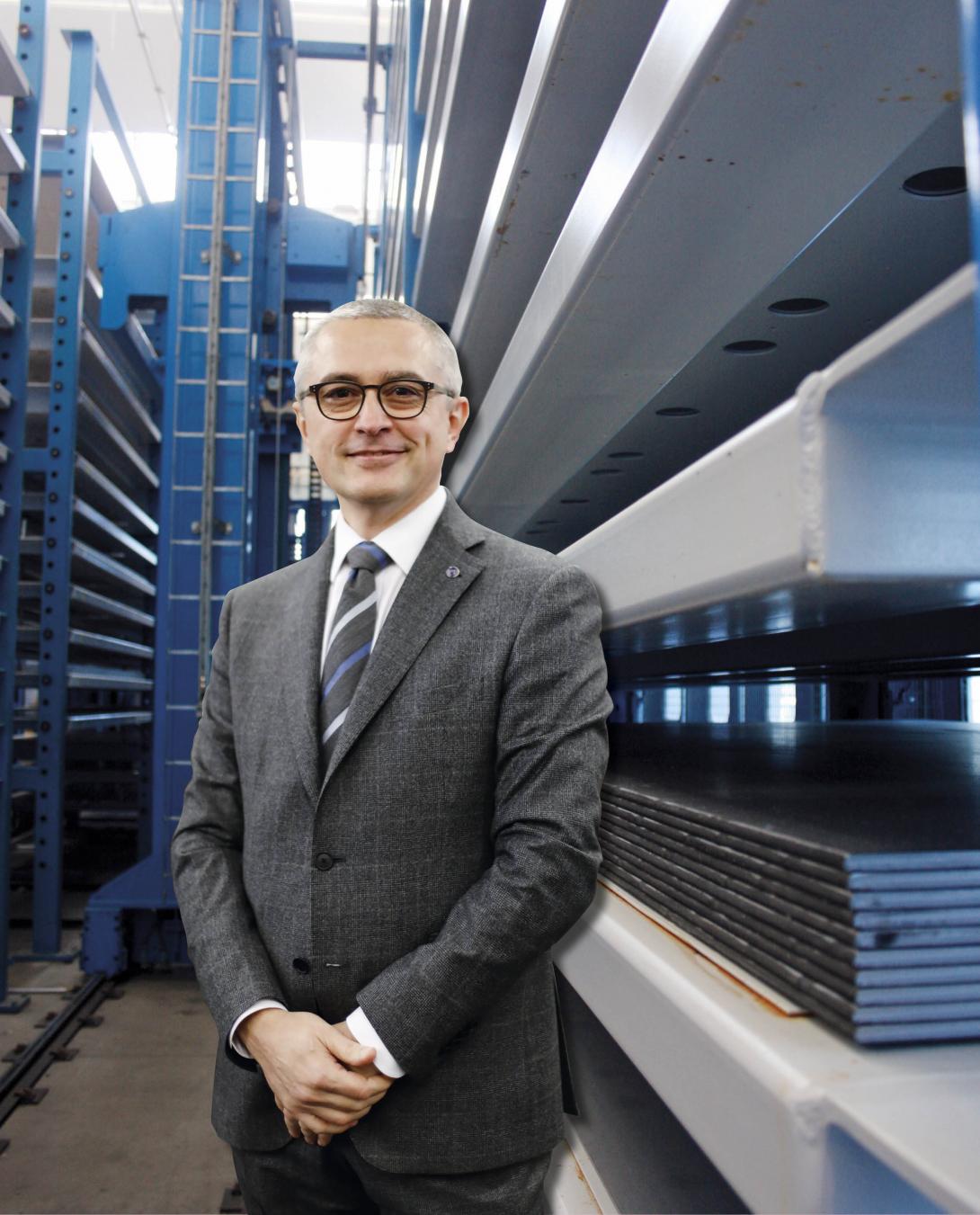
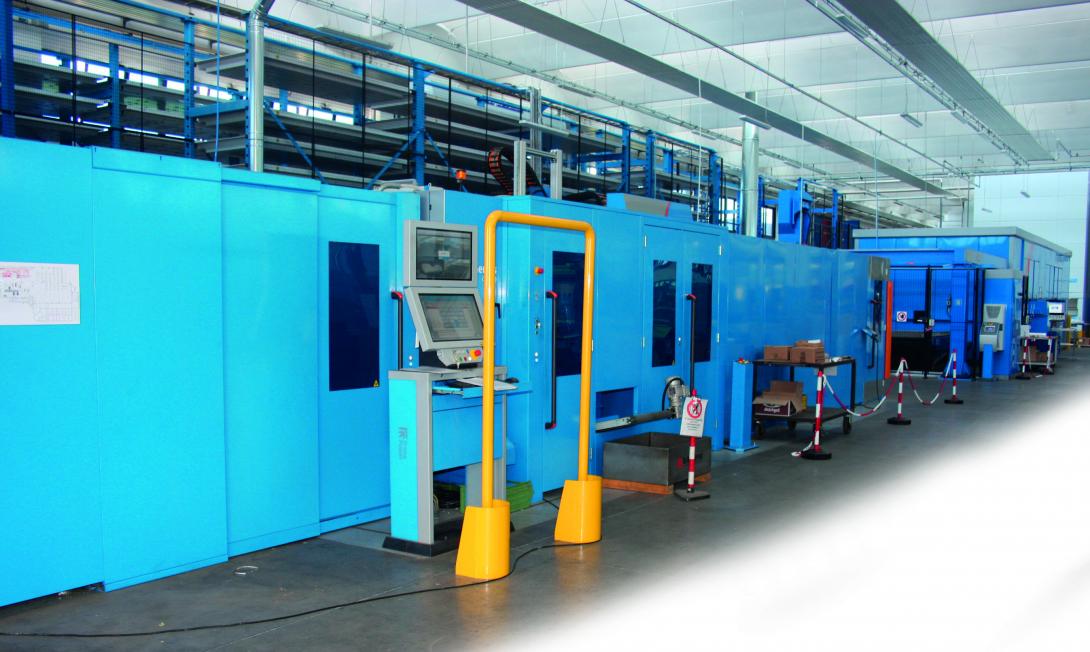
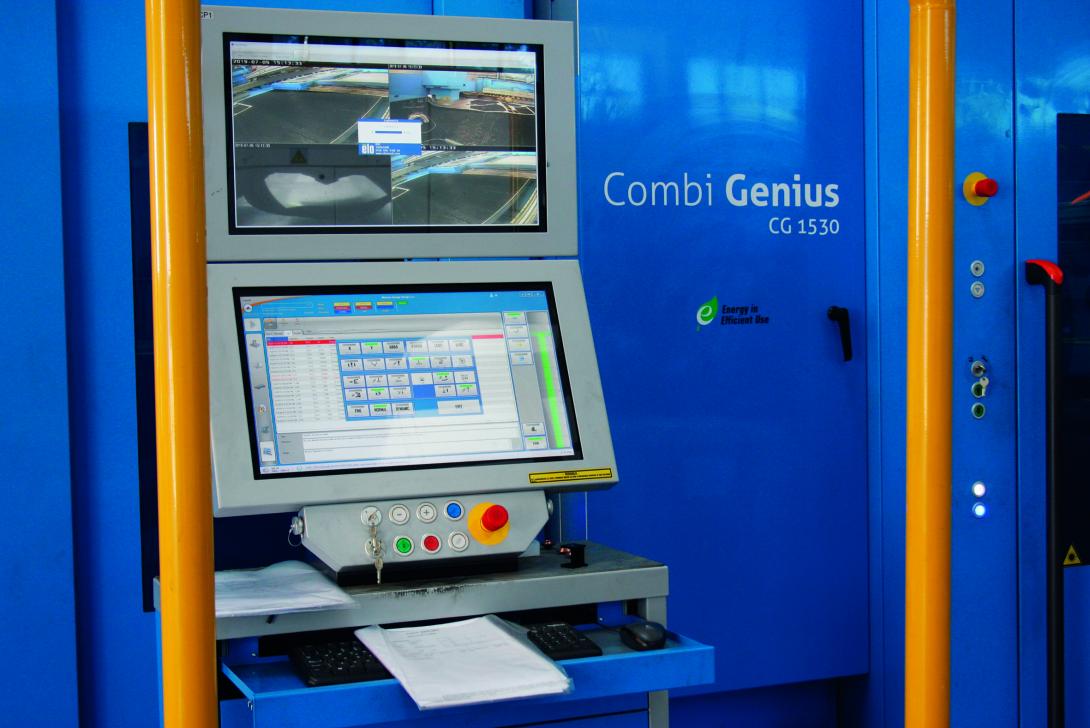
PERI-ITALIALAINEN KOKEMUS
Minerva Omega Group on vakiintunut peri-italialainen esimerkki oman alansa menestyjästä, joka investoi paljon uusien mallien suunnittelu- ja kehitystyöhön sekä automatisoituihin laitteisiin ja tuotantolinjoihin. ”Sitoudumme korkeaan työn laatuun, josta vastaavat työntekijämme ja yhteistyökumppanimme”, Salati Chiodini sanoo.
”Vaikka olemme kohdanneet vaikeuksia ja kovaa kilpailua maista, joissa valmistuskustannukset ovat huomattavasti alhaisemmat, puolustamme ja tuemme italialaista tuotantoa kaikin voimin. Emme halua siirtää pääkomponenttien tuotantoa tai koneiden kokoonpanoa pois Bolognan ja Varesen tehtaista.”
Sitoutuminen on tärkeää, ja investoinnit pitävät meidät teknologisesti ja laadullisesti kilpailukykyisinä. Investointeja tehdään säännöllisesti, ja ne koskevat koko toimitusketjua. Korkea laatu ja kilpailukyky ovat meille äärimmäisen tärkeitä arvoja. Yrityksen jatkuva kasvu kaikilla markkinoilla on paras vastaus kysymykseen, kannattaako italialaiseen tuotantoon enää sijoittaa.”
MERKITTÄVÄ TEKNOLOGINEN VALINTA
Minerva Omega Groupin tehtävä on selkeä. Jokin aika sitten yritys aloitti hankkeen, jonka tavoitteena oli automatisoida kehittyneimmät valmistusprosessit. Taustalla oli tarve parantaa kilpailukykyä ja ylläpitää elintarvikekoneita koskevia laatustandardeja.
”Esittelimme ensimmäiset automaattiset koneet vuonna 1984”, Salati Chiodini kertoo. ”Ne olivat lastunpoistotyökaluja, sillä tuotteemme syntyivät aikaisemmin valurunkojen käsittelystä. Käytimme hyvin vähän metallilevyä, ja sen käsittely ulkoistettiin. Vuosina 1994–95 aloimme havaita muutoksia markkinoilla. Toimivuuden lisäksi koneilta alettiin edellyttää tiettyä estetiikkaa. Otimme käyttöön ruostumattoman teräksen ja aloimme valmistaa joitakin koneita tästä materiaalista luottaen samalla alihankkijoihin."
"Vuonna 1998 päätimme ostaa ensimmäisen laserleikkausjärjestelmämme. Se oli Prima Industrie Platino -järjestelmä, jossa oli 1 500 x 3 000 mm:n työskentelyalue ja automaattinen paletinvaihtaja. Se piristi liiketoimintaamme huomattavasti. Vuonna 2002 aloimme rakentaa uutta päämajaamme ja asensimme sinne Finn Powerin laserleikkaus/-lävistysratkaisun 2,5 kW:n CO2-lähteellä. Käytimme sitä viime vuoteen asti. Valintaan päädyttiin halusta automatisoida käsittelyjakso mahdollisimman kattavasti. Siksi päätimme yhdistää koneeseen Night Train FMS -varastoyksikön, jossa on 10 tornia 12 laatikolla. Tämä oli innovatiivinen ja tehokas tuotantojärjestely, jonka ansiosta liiketoimintamme sai vahvan piristysruiskeen. Valitettavasti 18. tammikuuta, 2018 tulipalo raivosi metallilevyosastollamme, mikä pakotti meidät ulkoistamaan teräksenkäsittelyn muutamaksi kuukaudeksi. Aloimme korvata tuhoutunutta tuotantoa ja tutkimme kaikkia vaihtoehtoja markkinoilla, vaikka loppujen lopuksi halusimmekin jatkaa samalla teknologisella polulla, jolla aloitimme useita vuosia aikaisemmin. Päädyimme Prima Poweriin, sillä se oli ainoa järjestelmä, joka takasi meille jatkuvuutta. Voi vaikuttaa siltä, että valinta tehtiin tunnepohjalta, mutta vakuutan, että harkitsimme tarkkaan jokaista vaihtoehtoa ja niiden heikkouksia ja vahvuuksia. Tiesimme täsmälleen, mitä tarvitsimme, ja Prima Power oli parhaiten linjassa tuotantoon kohdistuvien odotustemme ja tarpeidemme kanssa myös tehtaan layoutin suhteen.”
”Teimme päätöksen jatkuvuuden ehdoilla”, Andrea Salati Chiodini jatkaa. ”Kyse oli myös ajoituksesta, sillä mahdollisuus käyttää samaa varastoyksikköä lyhensi asennusaikoja kuukausilla. Se oli viisas valinta ja se oli yhdenmukainen halumme kanssa vähentää seisonta-aikaa mahdollisimman paljon. Ulkoisiin kumppaneihin turvaaminen metallilevyjen käsittelyssä ei anna meidän täysin hallita tilannetta ajoituksen ja asiakkaiden odottaman laatutason suhteen.”
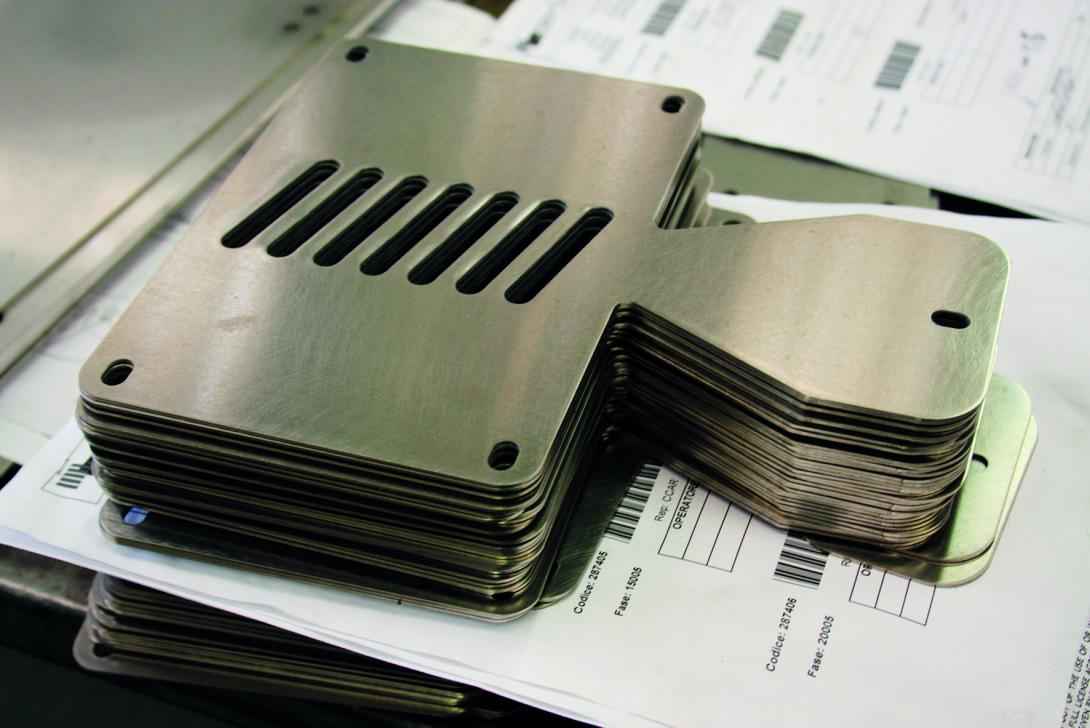
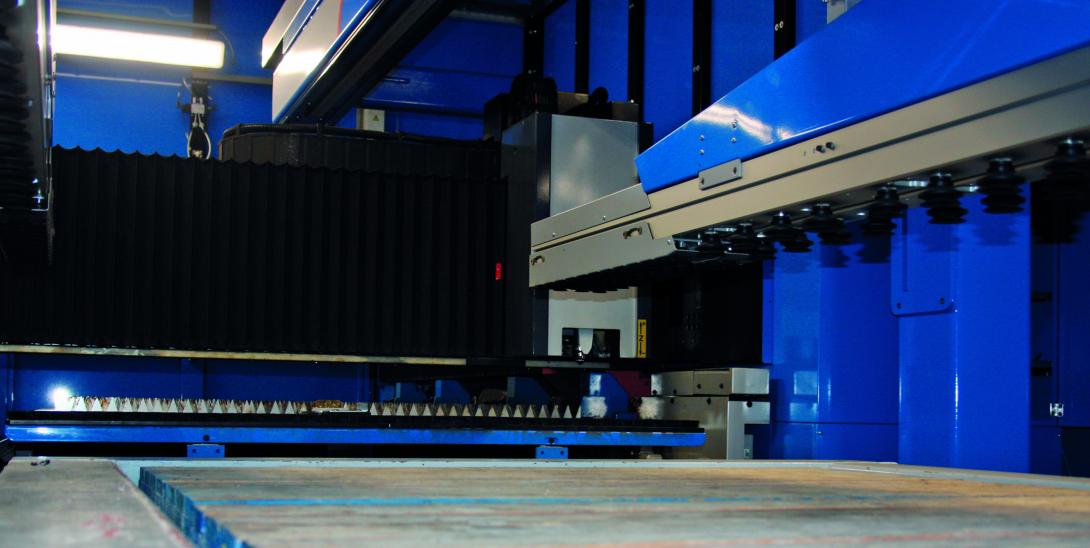
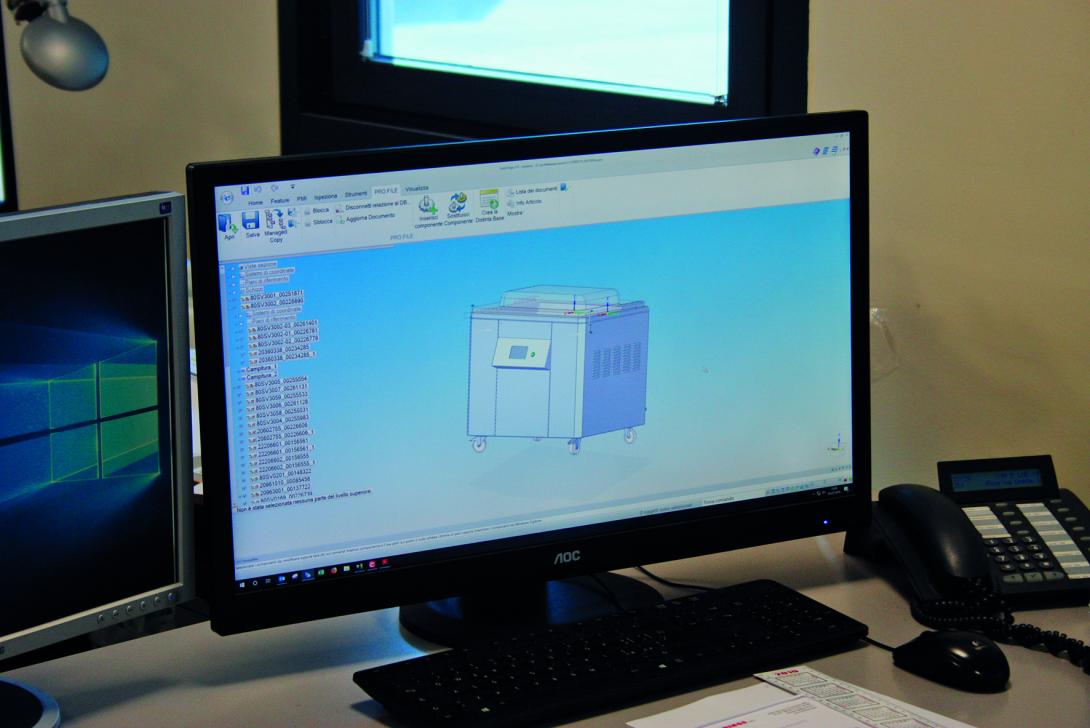
AIDOSTI RÄÄTÄLÖITY JÄRJESTELMÄ
Nykypäivänä on itsestään selvää, että Minerva Omegan tuotannon sydämenä sykkii Night Train, joka koostuu 14 lohkosta ja 200 laatikosta. Se erottuu edukseen automatisoitujen varastoyksiköiden joukosta. Se on yhdistetty lävistys-/laserleikkauskoneeseen Prima Power Combi Genius 1530, jossa on 4 kW:n kuitulaser ja LSR6-lastaus-/purku- ja pinontarobotti, sekä kaksiulotteiseen laserkuituleikkausjärjestelmään Prima Power Laser Genius 1530, jossa on lineaarimoottorit, 6 kW:n kuitulähde, LU-levyn lastaus- ja purkurobotti sekä automaattinen LST-lajittelu- ja pinontarobotti.
”Pohdimme neljää eri layoutia, kun yritimme optimoida järjestelmän käytettävissä olevan tilaan mukaan, olipa kyse sitten vain 15–20 senttimetristä. Halusimme parantaa kaikkia yksityiskohtia, kuten haarukkatrukin reittejä, lastunpoistovirtaa ja tarkastusluukkuja”, Salati Chiodini jatkaa. ”Haluan tässä yhteydessä korostaa Prima Powerin halukkuutta ja kykyä räätälöidä tuote juuri meidän tarpeitamme vastaavaksi. He astuivat meidän saappaisiimme ymmärtääkseen paremmin tilannettamme eivätkä koskaan ehdottaneet oikoteitä vakioratkaisuihin turvautuen. He ymmärsivät välittömästi, kuinka tärkeä täysin automatisoitu tuotantojärjestelmä on. Järjestelmän täytyy pystyä luomaan puolivalmis tuote, joka on heti valmiudessa siirtymään seuraavaan vaiheeseen. Metallilevy syötetään sisään, ja valmis tuote vaaditulla viimeistelyllä tulee ulos. Meille tämä on aina ollut tuottoisa toimintatapa, joka on syntynyt mahdollisuudesta työskennellä vuorokauden ympäri. Teknologia on saavuttanut niin hyvän luotettavuuden, että voimme käynnistää nestauksen perjantai-iltapäivänä, ja kaikki kappaleet ovat maanantaiaamuna valmiina lajittelua varten taivutusalueella – jolla on sähköservokäyttöinen Prima Power eP-0520 -särmäyspuristin – ja kokoonpanoalueella. Tämä on tärkeää, jotta voimme suunnitella työmme, vähentää seisonta-aikaa ja minimoida hylkäykset.”
YHDISTELMÄKONE VAI LASERLEIKKAUS?
Prima Power Night Trainin asennuksen layout antaa Minerva Omegalle mahdollisuuden käyttää varastoyksikköä sekä tilauksiin perustuvaan tuotantoon että meneillään olevan tuotannon varastointiin, jolloin sinne voidaan varastoida myös puolivalmiita kappaleita. Tilaustöiden käsittelyyn sisältyvät ulkomaiset tilaukset, joille on ominaista tuotteiden suuri määrä. Tilaus syötetään yrityksen hallintajärjestelmään, minkä jälkeen luodaan arvioitu toimitusaika (asiakkaan odotusten mukaisesti) ja tuotanto käynnistetään. Tuotannonohjaus käsittelee kaikkea tilauksista osien toimittajiin ja sisäisesti myös lastunpoiston ja metallilevyn leikkauksen toimintoja. Jakson jokainen vaihe on ajoitettu suunnittelutyökalulla, joka loogisesti ja tehokkaasti ohjaa työnkulkua eri koneilla ja eri vaiheissa tuotteen kokoonpanoon ja toimitukseen asti. Prima Power Night Train -järjestelmään liittyvissä tuotannon käynnistyksissä Minervalla yritetään hyödyntää koneistettuja nestausprosesseja, jotta metallijätteen määrä on mahdollisimman vähäinen ja käsittely voidaan optimoida.
”Kun kappaleet on 90-prosenttisesti valmistettu ruostumattomasta teräksestä, pystymme aina luomaan erinomaisia nestausprosesseja, joissa yhdistyvät parhaat kappaleet – jopa kulutustavarat – käsiteltävien työtilausten mukaisesti. Yritämme kerätä nestaukseen mahdollisimman monta kappaletta, jotta saamme levyn täyttöprosentiksi 85 %”, Salati Chiodini kertoo.
Oli myös kiintoisaa oppia, mitä tekijöitä otetaan huomioon, kun päätetään, käsitelläänkö työkappale Combi Genius- vai Laser Genius -leikkausjärjestelmällä. Tässä tapauksessa Salati Chiodinin vastaus oli yksiselitteinen: ”Teemme vain leikattavia tai paksuja kappaleita laserjärjestelmällä ja käytämme yhdistelmäkonetta kappaleisiin, jotka tarvitsevat muita työprosesseja, kuten taivutusta, kierrereikiä, kohokuviointia, lovia ja uria. Jos minun on kuitenkin tehtävä vertailua menneeseen, kun meillä oli CO2-laserit kuitulähteiden sijaan, sanoisin, että selkein tekijä liittyy energiankulutukseen. Säästöt ovat melkoiset, kun otetaan huomioon, että yhdistelmäkone yksin kulutti noin 80 kW. Tänä päivänä emme pääse samoihin lukemiin edes molemmat koneet yhdessä.
Kuitulaser vaatii hyvin vähän kunnossapitoa ja takaa useimmissa tapauksissa paremman ja hienomman leikkauksen. Tämä koskee sekä 4 kW:n Combi-konetta että 6 kW:n Laser Genius
-konetta, mikä varmistaa vertailukelpoisen leikkaustehon.
Laser Geniuksen teho on suurempi ja – materiaalin paksuuden ollessa yhtä suuri – se tuottaa hieman parempaa laatua lyhyemmässä ajassa. Sanoisin kuitenkin, että molemmissa tapauksissa, 15 mm:n paksuuteen asti, saamme käytännössä täydellisen leikkauslaadun, joka on meitä koskevien vaatimusten mukainen. Paras leikkauksen viimeistelyn laatu ilman purseita tarkoittaa, ettei meidän tarvitse käsitellä kappaleita uudelleen tai hioa niitä. Kaikki tämä vähentää tarvittavaa aikaa, tarjoaa huomattavia taloudellisia etuja ja ilahduttaa loppuasiakasta.”
Käännetty, muokattu ja julkaistu uudelleen Deformazione Magazinen luvalla, lokakuu 2019.
Kuitulaser vaatii hyvin vähän kunnossapitoa ja takaa useimmissa tapauksissa paremman ja hienomman leikkauksen. Tämä koskee sekä 4 kW:n Combi-konetta että 6 kW:n Laser Genius -konetta, mikä varmistaa vertailukelpoisen leikkaustehon.
Etsitkö vastaavaa ratkaisua yrityksellesi? Löydä se täältä
Combi Genius
LÄVISTYKSEN JA LASERLEIKKAUKSEN YHDISTÄVÄT KONEET