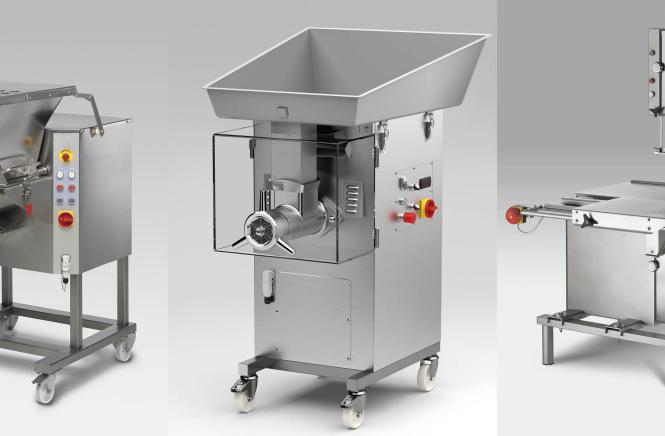
Abordo del Night Train hacia una mayor productividad
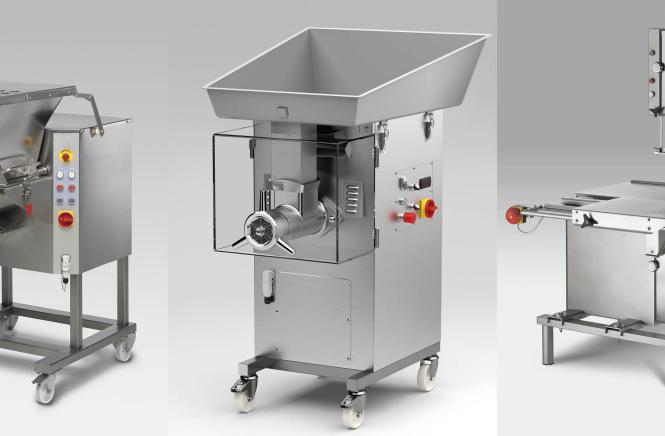
Abordo del Night Train hacia una mayor productividad
El Minerva Group en Bolonia, Italia es una compañía que realmente personifica destrezas, tecnología y espíritu emprendedor.
Las ideas claras y la determinación son los rasgos que han hecho posible que Andrea Salati Chiodini, CIO y Gerente Técnico del Grupo, se centrara en la automatización de procesos en el taller. Esto permitió a la compañía obtener una ventaja sobre sus competidores en el mundo altamente regulado de las máquinas para la industria alimentaria. Esto se logró gracias a la instalación del sistema de fabricación flexible (FMS) con Night Train totalmente automatizado e integrado de Prima Power, capaz de producir un producto semiterminado que está inmediatamente listo para los siguientes pasos de la manufactura.
Actualmente, el Minerva Omega Group, cuya reputación internacional se ha fortalecido aún más con un sistema de gestión moderno y ganador, puede presumir de tener una de las gamas de productos más completas del mercado y una cartera de clientes bien establecida con presencia en todos los sectores alimentarios, en las tiendas minoristas masivas y a través de distribuidores en todos los países del mundo. Salati Chiodini, junto con su hermano y su hermana, son la tercera generación de la familia al frente de esta histórica y longeva compañía industrial.
Minerva Omega Group s.r.l. se creó en 2012 a partir de la fusión de dos compañías históricas, Minerva de Bolonia y Omega Ceg de Varese. Ambas compañías tienen una larga historia, tradición y experiencia. La Minerva, que celebrará 75 años de actividad comercial en 2020, se fundó en 1945 en Bolonia, una zona con una fuerte tradición mecánica y de ingeniería, gracias a la iniciativa emprendedora de Mario Chiodini, el abuelo de los actuales propietarios. Diseña y fabrica máquinas para la industria del procesamiento de carne, banquetería, procesamiento de alimentos y centros de envasado, además ofrece una variedad de productos de alta calidad con una excelente relación calidad-precio y vida útil.
"Somos una de las compañías familiares más antiguas de Italia", explica Andrea Salati Chiodini. "Es precisamente gracias a este liderazgo emprendedor y a una mentalidad de gestión orientada a la mercadotecnia que hemos llevado a Minerva a adquirir e incorporar a algunos de nuestros competidores: primero la compañía Artex basada en Bolonia, y después Omega, propietaria de otras marcas históricas como Ceg, General Machine, Regina, Suprema y, recientemente, Aria y Mincer2000, todas ellas marcas muy conocidas por los expertos del sector en todo el mundo".
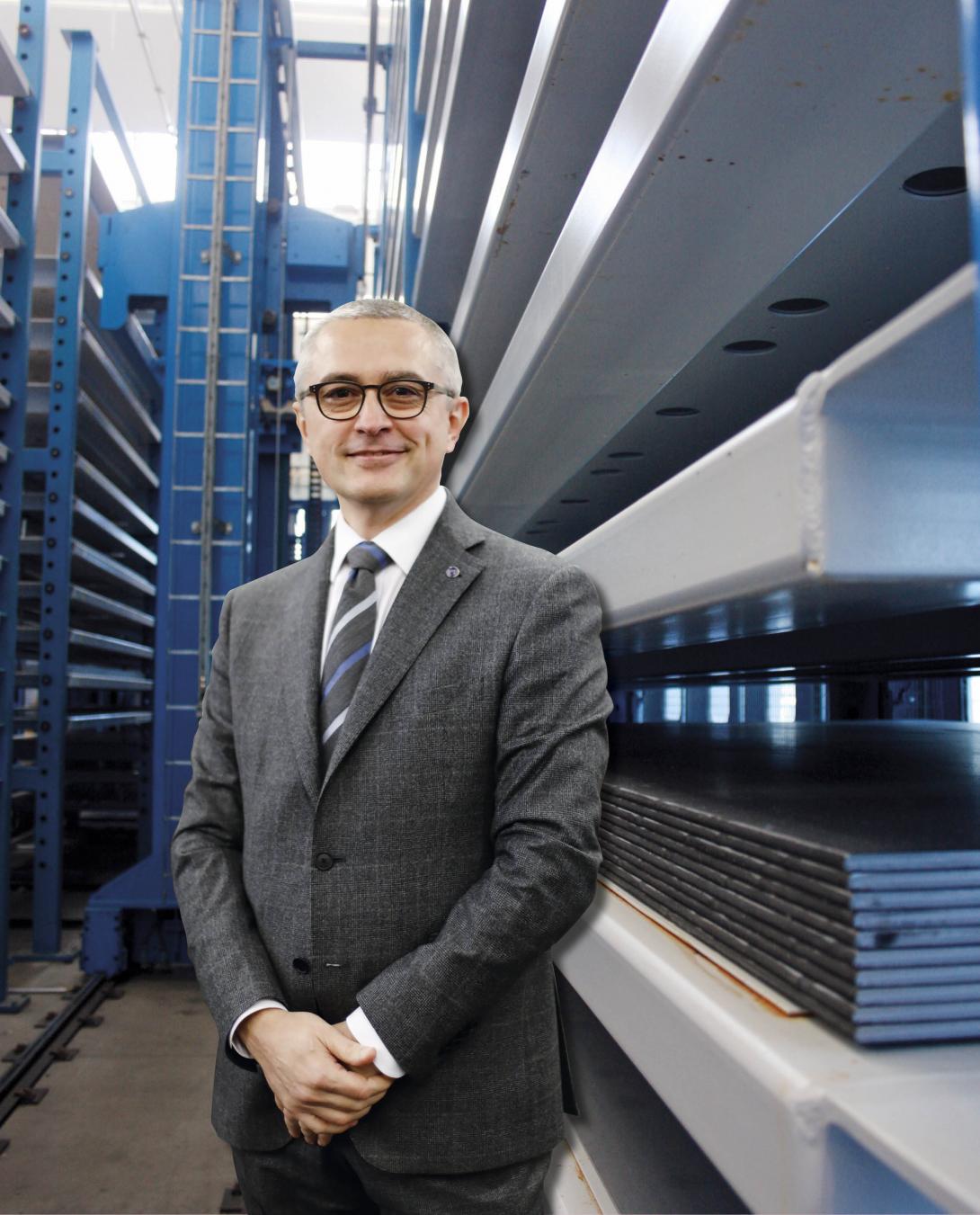
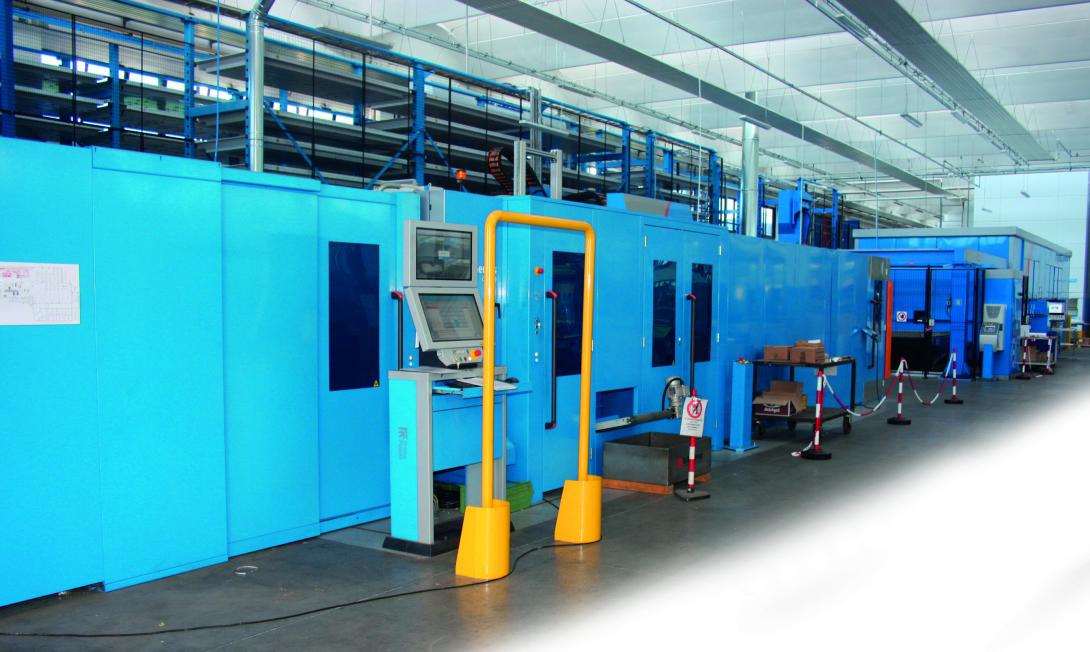
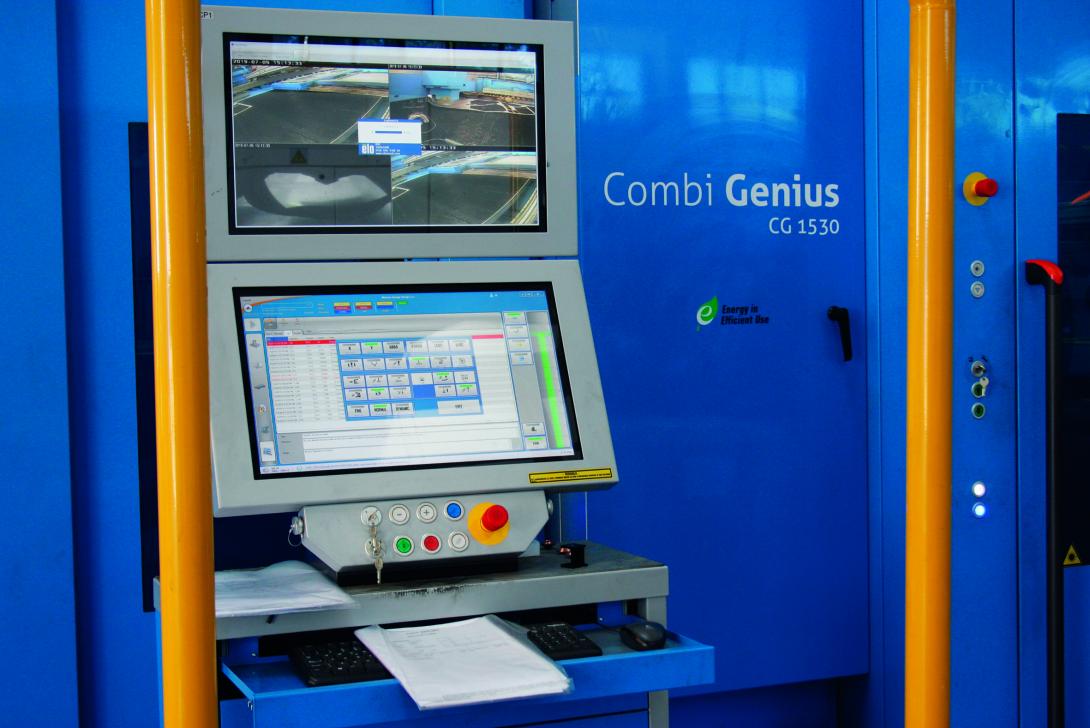
Excelencia totalmente italiana
El Minerva Omega Group es un ejemplo bien establecido y totalmente italiano de la prominencia en la industria, con una fuerte capacidad de inversión en el diseño y el desarrollo de modelos nuevos, en equipos automatizados y en líneas de producción. "Creemos en la calidad del trabajo, que es la evidencia del gran compromiso en grupo llevado a cabo por nuestros empleados y colaboradores", explica Salati Chiodini.
"A pesar de las grandes dificultades y de la competencia de países en donde la manufactura tiene un costo muy inferior, defendemos y apoyamos la marca Hecho en Italia con todas nuestras fuerzas, sin reubicar la producción de componentes principales y el montaje de maquinaria de las instalaciones de Bolonia y Varese".
El compromiso es importante... y las inversiones, para mantenernos competitivos desde el punto de vista tecnológico y cualitativo, se hacen con regularidad e involucran a toda la cadena de suministro. La excelencia, la competitividad y la calidad son valores imperativos para nosotros. El crecimiento continuo de la compañía en todos los mercados es la mejor respuesta a la pregunta de si sigue mereciendo la pena invertir en la producción manufacturera italiana actual".
Una elección tecnológica importante
La misión del Minerva Omega Group es clara. Hace tiempo que la compañía emprendió el camino hacia automatización de los procesos de manufactura más vanguardistas, no solo con el fin de ser competitiva, sino para cumplir con los estándares de calidad que exige la normativa vigente en materia de maquinaria alimentaria.
"Introdujimos las primeras máquinas automáticas en 1984", dice Salati Chiodini. "Se trataba de máquinas-herramienta para eliminar virutas, ya que nuestro producto resultó anteriormente del procesamiento de piezas fundidas. En realidad, se utilizó muy poca chapa metálica y su procesamiento se subcontrató. Sin embargo, alrededor de 1994/95 empezamos a percibir un cambio en el mercado. Además de la funcionalidad, se empezaba a exigir un cierto valor estético a la maquinaria. Por ello, introdujimos el acero inoxidable y empezamos a fabricar algunas máquinas con este material, aunque seguimos dependiendo de los subcontratistas".
"Para 1998, decidimos comprar nuestro primer sistema de corte por láser, un sistema Prima Industrie Platino, con un área de trabajo típica de 1.500 x 3.000 mm y un cambiador automático de palets, lo que dio un fuerte estímulo al negocio. En 2002, empezamos a construir estas nuevas oficinas centrales, donde también instalamos una solución combinada de láser/punzón de Finn Power con una fuente de CO2 de 2,5 kW, que hemos utilizado hasta el año pasado. Fue una elección derivada del deseo de automatizar al máximo el ciclo de procesamiento, por lo que decidimos combinar la máquina con una unidad de almacenamiento Night Train FMS que incluye 10 torres con 12 cajones. Se trataba de una organización de producción innovadora y eficaz que nos permitió dar un fuerte estímulo al negocio sin contratiempos hasta el 18 de enero de 2018, cuando un incendio arrasó nuestro departamento de chapa metálica, obligándonos a subcontratar el procesamiento del acero durante unos meses. También empezamos a reemplazar lo que se había destruido, volviendo a poner sobre la mesa a todos los principales actores del mercado, aunque al final, preferimos continuar con la ruta tecnológica que habíamos emprendido varios años antes y optamos por Prima Power, el único sistema que nos aseguraba la continuidad después de hacernos cargo de Finn Power. Podría parecer que fue una elección basada en una simpatía, pero le aseguro que realmente incluimos a todos en la decisión analizando los puntos fuertes y débiles de la solución de cada uno. Finalmente, siendo muy conscientes de lo que necesitábamos, Prima Power resultó ser el sistema que más se ajustaba a nuestras expectativas de producción y a nuestras necesidades también en cuanto a la disposición de la planta".
"Hemos tomado una decisión bajo el signo de la continuidad", añade Andrea Salati Chiodini. "También en términos de tiempo, ya que poder utilizar la misma unidad de almacenamiento nos permitió reducir los tiempos de instalación en meses. Fue una decisión acertada, consistente con nuestro deseo de reducir al máximo los tiempos de inactividad, ya que, al recurrir a colaboradores externos para el trabajo de la chapa metálica, nunca se puede dominar realmente la situación, tanto en lo que respecta a los plazos de tiempo como al nivel de calidad al que estaban acostumbrados nuestros clientes".
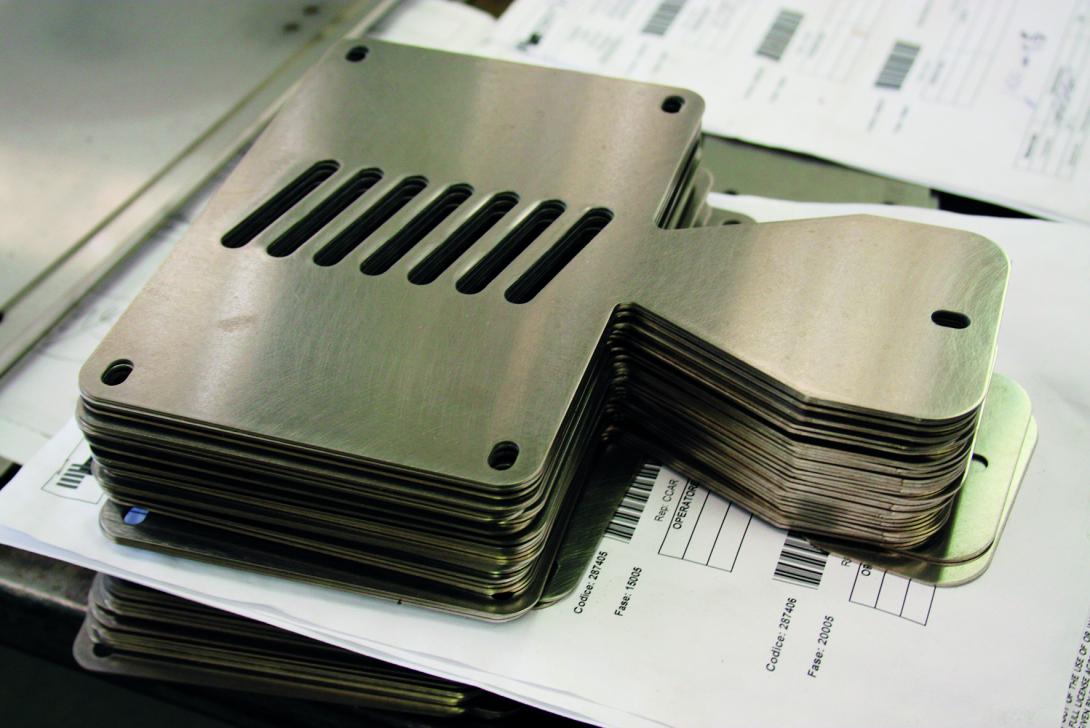
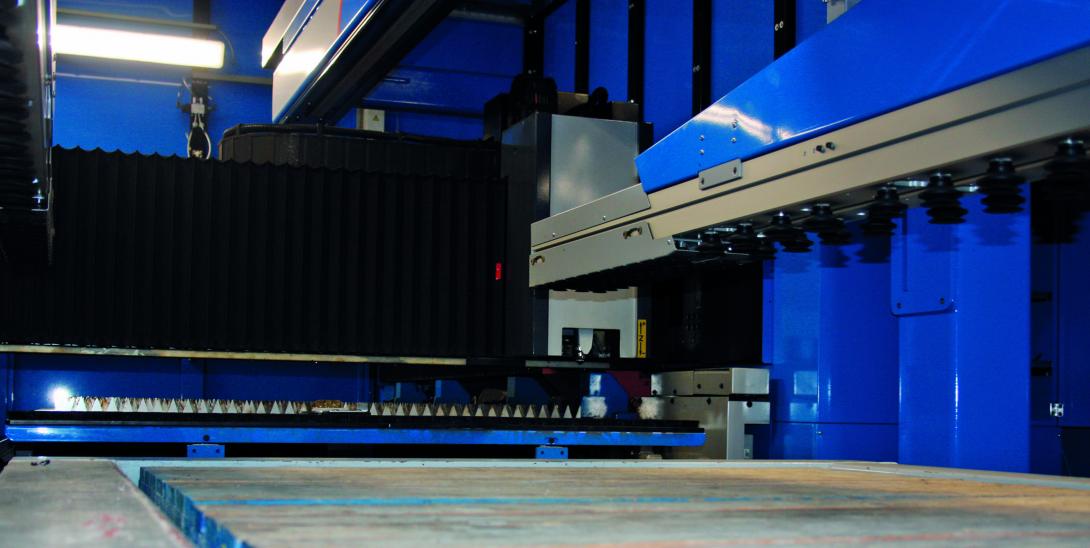
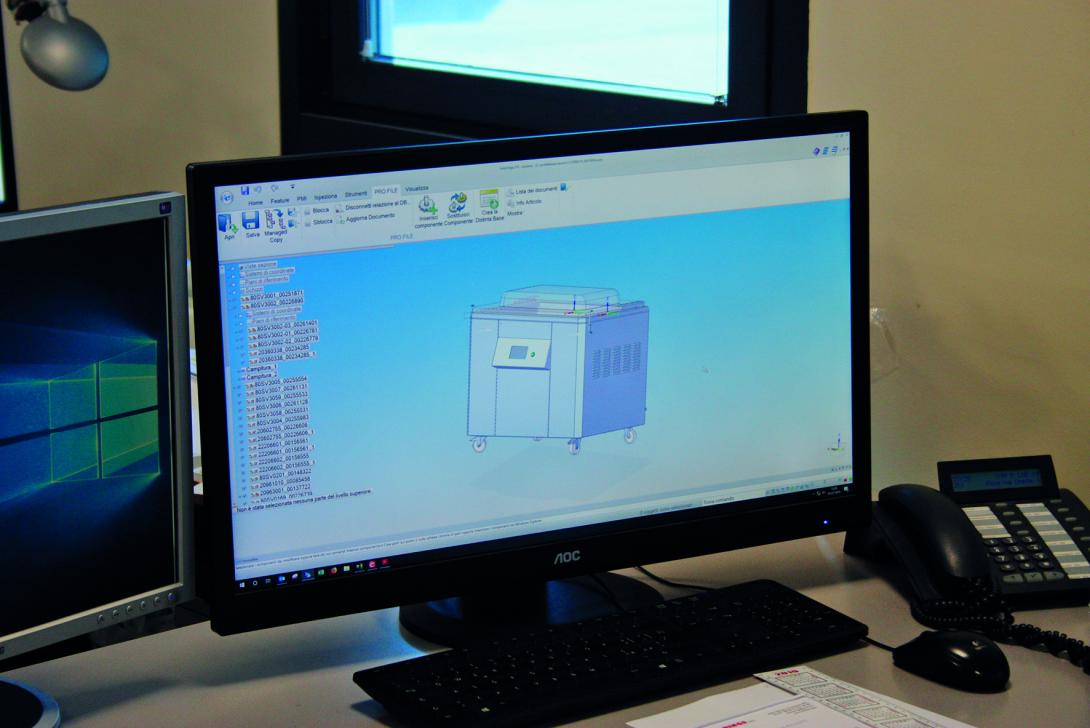
Un sistema realmente a la medida
Actualmente, no hace falta decir que el nuevo corazón de la producción de Minerva Omega sigue siendo el Night Train, compuesto por 14 bloques y 200 cajones, que destaca como tecnología de punta en el campo de las unidades de almacenamiento automatizadas. Se conecta a la punzonadora/cortadora por láser de Prima Power Combi Genius 1530 con láser de fibra de 4 kW y un robot de carga/descarga y apilado LSR6, así como un sistema de corte por láser de fibra bidimensional de Prima Power Laser Genius 1530 con motores lineales, equipado con una fuente de fibra de 6 kW, un robot de carga y descarga de chapa metálica LU y un robot de clasificación y apilado automático LST.
"Analizamos cuatro disposiciones, ya que intentamos optimizar el sistema según el espacio disponible recuperando, donde era posible, incluso solo 15/20 cm para mejorar cada pequeño detalle, como el paso de los montacargas o los flujos de descarga de residuos metálicos o las puertas de acceso de los operadores", continúa Salati Chiodini. "En este sentido, me gustaría resaltar la gran disposición y capacidad de adaptar a la medida que tiene Prima Power para poder crear un producto realmente hecho a la medida, ya que se pusieron en nuestro lugar para entender mejor nuestros problemas y nunca sugirieron atajos en términos de soluciones estándar. Inmediatamente comprendieron la importancia de ofrecer un sistema de producción totalmente automatizado, capaz de producir un producto semiterminado que estuviera inmediatamente listo para los siguientes pasos. Se alimenta la chapa metálica y se saca el producto terminado con el nivel de acabado que necesitamos. Para nosotros, esto siempre ha sido un aspecto ganador y el resultado de estar acostumbrados a trabajar las 24 horas del día y los 7 días de la semana. La tecnología ha alcanzado un nivel de confiabilidad tan alto que podemos lanzar un anidamiento un viernes por la tarde y el lunes por la mañana tener todas las piezas listas para ser clasificadas en el área de plegado, donde una también se ha instalado una prensa plegadora servoeléctrica eP-0520 de Prima Power, y en el área de montaje; este es un aspecto fundamental para poder planificar nuestro trabajo, reducir el tiempo de inactividad y minimizar los rechazos".
¿Máquina combinada o de corte por láser?
En la actualidad, la disposición de instalación del Night Train de Prima Power hace posible que Minerva Omega opere tanto en la fabricación por pedido como en el inventario del trabajo en curso con la unidad de almacenamiento, que también se utiliza para almacenar piezas semiterminadas. El procesamiento de fabricación por pedido incluye los pedidos extranjeros que se caracterizan por ser de cantidades grandes. Se ingresa un pedido en el sistema de gestión de la compañía, se genera una fecha de entrega estimada (de acuerdo con las expectativas del cliente) y se inicia la producción. El MRP se encarga de todo, desde los pedidos a los proveedores de componentes comerciales hasta las operaciones internas de la eliminación de virutas y el corte de la chapa metálica. Cada fase del ciclo se programa mediante una herramienta de planificación que gestiona de forma lógica y eficaz el flujo de trabajo en las diferentes máquinas del taller, así como en los distintos pasos del avance, hasta el montaje y la entrega del producto. En cuanto a los lanzamientos de producción relacionados con el rendimiento del sistema Night Train de Prima Power, en Minerva intentan aprovechar el maquinado de los procesos de anidamiento para obtener la menor cantidad posible de desechos, al tiempo que se optimiza al máximo el procesamiento.
"Al tener piezas que son en un 90 % de chapa de acero inoxidable, siempre conseguimos crear excelentes procesos de anidamiento que combinan la mejor mezcla de piezas, incluso de consumibles, según los pedidos de trabajo que deben procesarse. Intentamos reunir el mayor número posible de piezas en el anidamiento para alcanzar un porcentaje de llenado de la chapa de 85 %", explica Salati Chiodini.
También fue interesante entender qué aspectos se tienen en cuenta a la hora de decidir si un tipo de pieza de trabajo se va a procesar en un sistema de corte Combi Genius o en una Laser Genius. En este caso, la respuesta de Salati Chiodini fue clara e inequívoca: "Solo fabricamos piezas para cortar o piezas gruesas en el sistema de láser, mientras que utilizamos la unidad combinada para fabricar todas aquellas piezas que necesitan otros procesos de trabajo como deformaciones, agujeros roscados, repujados, muescas y ranuras. Sin embargo, si tuviera que establecer una comparación con el pasado, cuando teníamos láseres de CO2 en lugar de fuentes de fibra, diría que el aspecto más evidente es quizás el relacionado con el consumo de energía, ya que estamos teniendo un ahorro bastante significativo si se tiene en cuenta que la máquina combinada por sí sola consumía alrededor de 80 kW, mientras que hoy, con ambas máquinas, no llegamos a esta cifra.
El láser de fibra requiere muy poco mantenimiento y garantiza un corte mejor y más fino en la mayoría de los casos y esto se aplica tanto a la máquina Combi de 4 kW como a la Laser Genius de 6 kW, que aseguran un rendimiento de corte comparable.
La Laser Genius, al tener mayor potencia, y espesores iguales, logra obtener una calidad ligeramente superior y un tiempo más corto. Sin embargo, diría que en ambos casos, para hasta 15 mm de espesor, podemos obtener una calidad de corte prácticamente perfecta, de acuerdo con las disposiciones de las certificaciones a las que estamos sujetos. Además, tener un corte bien acabado y sin rebabas significa para nosotros evitar volver a trabajar las piezas para lijarlas o rectificarlas. Todo ello supone una reducción de tiempo y considerables ventajas económicas con un impacto favorable en el usuario final".
Traducido, editado y reimpreso con permiso de la revista Deformazione en octubre de 2019.
El láser de fibra requiere muy poco mantenimiento y garantiza un corte mejor y más fino en la mayoría de los casos y esto se aplica tanto a la máquina Combi de 4 kW como a la Laser Genius de 6 kW
Busca una solución similar para su empresa? Encuéntralo aquí
Combi Genius
MÁQUINAS COMBINADAS DE PUNZONADO Y CORTE POR LÁSER