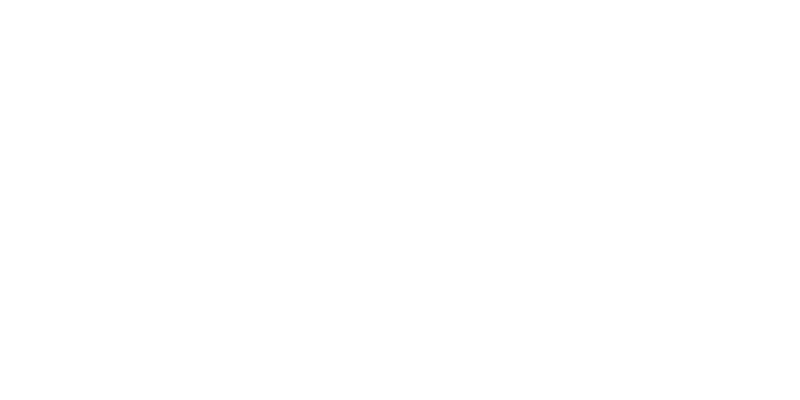
SPE installs state-of-the-art Prima Power BCe 2720 panel bender
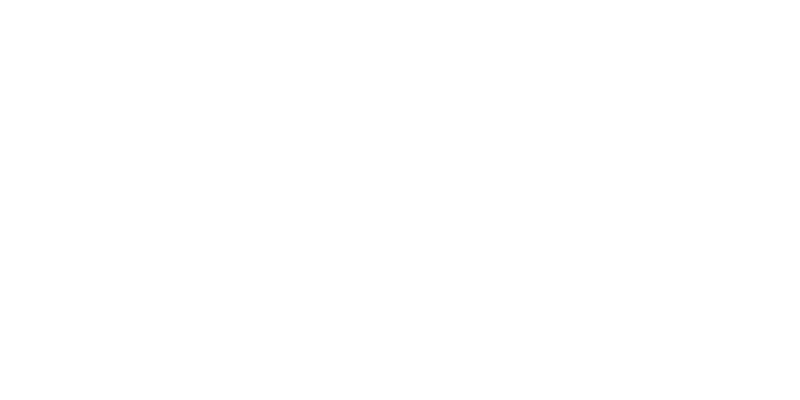
Generally speaking, fabrication is not what many would consider a glamourous process to watch, but bending with the Prima Power BCe 2720 panel bender is something to behold. Watching this semi-automatic bending center going about its task of high-precision bending is a bit like watching poetry in motion.
Established in 1989 and based Roodepoort, Gauteng and achieving various ISO and EN certification accreditations that include ISO 9001 accreditation for the past 20 years, ISO 3834 Part 2 and EN15085-2 CL1, Stainless Precision Engineering (SPE) is a one-stop metal product fabrication facility, where products or components are manufactured in medium to high volumes according to customers specific requirements.
SPE is able to offer a full range of sheet metal and fabrication services due to the utilisation of state-of-the-art CNC machinery that include lasers, punching machines, manual and robotic press brakes, panel bending, milling, turning, manual and robotic mig welding, tig welding, laser welding, spot welding, tube bending and many more supporting processes and equipment such as but not limited to grinding/fettling, polishing/brushing, powder coating, wet spray, electroplating, full product assembly and packaging.
New Prima Power BCe 2720 panel bender
Supplied and installed in March 2024 by Talmac Machine Tools, the Prima Power BCe 2720 panel bender was up and running just after that and has the ability to replace three other bending machines.
“Like with everything, machines have their limits and capabilities, but if you want to compare it outright, given the right job and components being processed, you could get rid of three press brakes and just use the panel bender. We predominantly work with light to medium gauge material between 1.6mm and 2mm – yes, we do process higher and lower thicknesses – but for our applications this machine is the perfect fit,” explained SPE’s owner, Dean Findlay.
SPE mainly fabricate with aluminium, carbon steel and stainless steel and process these materials for the retail, point of sale, access control, IT and communications, warehousing, hospitality, healthcare, banking, safety and security and rail industries.
“We always want to be leaders when it comes to the technology that we make use of, and not that panel benders are new technology, but it is this sort of equipment that helps us improve our processes and makes us more efficient. And that’s what we are all about – continuous improvement.”
“The technology in these machines has come a long way since we first looked into the idea of a panel bender many years ago. Back then the accuracies just weren’t there at the time. The technology utilised by this particular panel bender is extremely advanced and one of the main reasons we chose this machine was due to its software interface,” continues Findlay.
“Although the machine is in a stand-alone operating situation at the moment with manual loading and offloading, we have set it up in such a way that we can add robotics if we like and turn into a fully automated cell, but for now we are just learning about its capabilities and finding our feet with it. Again, another of the many pros to this panel bender is that there are no tooling changes or setups required when switching between operations. Once your programming is done it is very easy to switch between jobs regardless of thicknesses or materials. And this literally takes seconds to do. It really is impressive,” stated Director André Durandt who played an integral role in the machine selection and current Prima operations including design and programming.
The Prima Power BCe 2720 is servo-electric operated and equipped with eight independent motors and several CNC axes. The BCe 2720 allows you to process material thicknesses of 0.5mm up to 3.2mm of mild steel, up to 2.2mm of stainless steel and up to 4mm of aluminium. The machine has a maximum bending length of 2 750mm, accommodates a maximum sheet length of 2 850mm, has a maximum sheet width of 1 500mm, maximum panel diagonal of 3 000mm, a maximum bend height of 264mm with a bending force of 41 ton and clamping force of 90 ton.
It features exceptional bending quality that is achieved through the use of an angle correction database and servo-electric technology. The LUT table enables you to prepare the next part during the machining of the current sheet, thus optimising efficiency of both the machine and its operator. Manual loading is straightforward, accommodating batches of any size, whether these are flatpack kits or individual components. Additionally, the 3D programming features integrated simulation of the bending cycle to give an operator a clear picture before starting a batch run.
Currently SPE has around 30 CNC machines and systems on the well-designated and departmentally organised shop floor. Each of these departments has their own manager thereby integrating an accountability and quality control process of their own. These include press brakes, the new panel bender, CNC milling and turning machines, fiber lasers including one with fully automated loading and unloading as well punching machines. SPE occupy roughly 17 000m2 under roof and employ around 350 staff.
In addition to fabrication, SPE also offers integrated design and engineering consultation as part of their service offering. Their team collaborates closely with clients to understand their specific needs, providing insights and recommendations that enhance the functionality and efficiency of the components being manufactured. This consultative approach has earned them a reputation as a trusted partner in the engineering sector as an OEM manufacturer and supplier. This includes everything from custom components to complete systems.
SPE truly are a what you would refer to as a one-stop shop operating out of a world-class facility - a philosophy that has long been their approach to manufacturing for the more than 30 years that they have been in business. Over the years, SPE has managed to bring in-house pretty much every aspect of the fabrication process. It is this kind of quality control over the entire engineering process that supports the production of critical components that require exacting standards to ensure safety and efficacy.
Running as a virtually paperless facility, SPE has always been software oriented boasting its own in-house developed ERP manufacturing software solution tracking all aspects of fabrication from quotation, draughting, stockholding, scheduling, invoicing and all relevant ISO systems to production runs and quality control checks.
This system is something SPE has been continuously developing over the last 20 years and one of the biggest benefits of this system, especially for a jobbing shop, is traceability. When you are manufacturing thousands and thousands of components every month, being able to use software to track the entire manufacturing process is hugely beneficial, adds Managing Director Kaveshan Nayager.
Exploring new shores
To remain complacent in an ever-expanding world of interconnectivity could be considered resting on one’s laurels. SPE has only recently started operations in the USA located in Jacksonville, FL and currently has a warehousing and distribution facility with the ability to perform light manufacturing, finishing or assembly processes.
The immediate plan is to produce high quality products in South Africa and distribute them in the USA.
SPE-USA’s location in Jacksonville, FL is ideal due to the Port, CSX rail network and easy access to the I-10 and I-95.
“At this stage we are only using the facility for warehousing and distribution as we get a feel for a new market and a new culture. We have a small client base at the moment, but the idea is to see how that grows. It’s a tough market, it’s a big market, it’s not easy, but we will just have to see how things go and take it from there,” concludes Findlay.
The author of the article is Damon Crawford, Metalworking News
The photo at the top of the page shows us Director Andre Durandt, CEO and President Dean Findlay and Managing Director Kaveshan Nsayager