Prima Power in the Energy sector
Find out what we do in the energy sector.
Analysts predict that electricity demand will grow significantly through direct electrification and the uptake of green hydrogen. In this context, renewables will rapidly increase to half of electricity generation by 2035. Yet fossil fuels will continue to play a major role in the energy market until 2050, driven by growth in areas such as chemicals and aviation. (Source: McKinsey, Global Energy Perspective 2021)
We understand the main challenge this sector has to face is the qualification of the processes. Machines used for drilling, cutting and welding applications must be particularly precise, stable, and reliable to maintain the certified parameters to ensure quality work while also avoiding waste and costly rework.
And we also know that you need intensive supplier support, which must be provided by consultants who know your case well and have highly specialized technical know-how.
Process control is the driving force when manufacturing components for the energy industry.
Documentation supplied with the machine must be clear, accurate, and exhaustive. Training must be highly customized so that your company can make the most of individual systems.
Knowing these dynamics in depth means that Prima Power machines are widely used in the aerospace industry in different applications, mainly for drilling cooling holes on hot turbine engine parts (both for aerospace and energy production) and for the manufacture of complex parts that require cutting and welding processes.
EXPERIENCE
We have been operating in the energy sector since 1977.
LISTENING
We customize our machines to your actual needs.
ACCURACY
Our machines allow machining that satisfies even the most stringent testing.
Solutions
Find your ideal solution
Learn how our systems work and how our offerings set us apart from other manufacturers.
Our Laserdyne systems, as well as Laser Next product family, guarantee accuracy and repeatability. These can be equipped with one or more numerically controlled rotary tables to machine cylindrical parts for the turbine, even during loading/unloading phases in masked time.
Our systems can measure/find parts using integrated sensors (optical and/or capacitive). This increases the accuracy of the system without the need for expensive equipment. It also allows you to compensate for any errors in the shape of the component.
Our unique process control solution on laser drilling systems, known as FlowComp™, enables airflow requirements on parts to be met while complying with the tightest tolerances. The FlowComp™ performs automatic compensation and adjusts the size of the drilled holes using measurements from a specific airflow test bench integrated with the machine. The numerical control and CL50K laser, both developed and manufactured at Prima Industrie, just like the machine, manage the correction without operator intervention.
Our experts are highly specialised in this area: they provide added value and help you maximise profit.
Our qualified services complement our advanced technology and are the key to improved productivity and higher profit.
All our systems are designed and developed based on the “Green Means concept”, which means they are productive and eco-sustainable at the same time.
Application examples
Behind each component there is a Prima Power machine
- engine and turbine components
- transition ducts
- turbine plenums
- combustion chambers
- rotor and stator blades
- chassis
- aircraft structural components
Related technologies
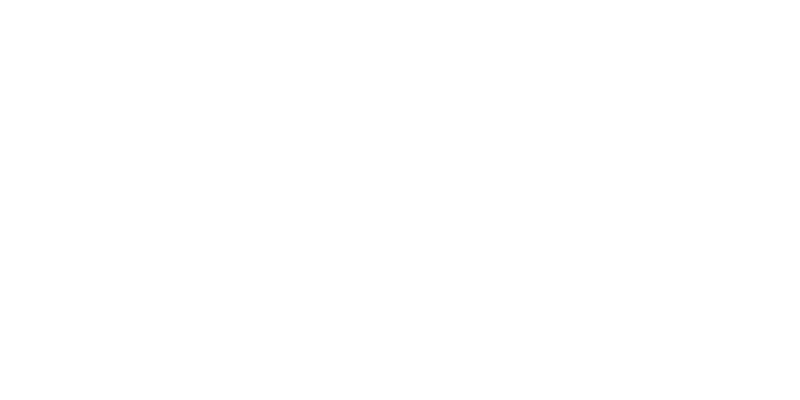
Browse our technologies to choose your machine
eP Genius
PRESS BRAKES
Efficient servo-electric bending solution with a fast and automatic tools change storage
FBe Fast Bend
PANEL BENDERS
The answer to multiple applications. Semi-automatic bending solution for simple, flexible and accessible production
BCe Bending Centre
PANEL BENDERS
Flexibility at your service semi automatic panel bender combining flexibility and productivity
PunchBend
FLEXIBLE MANUFACTURING SYSTEMS
From cut-to-size material to ready-bent components
Night Train FMS®
FLEXIBLE MANUFACTURING SYSTEMS
Leading technology storage solution in automated flexible manufacturing systems
Fast Loading storage
STORAGE SOLUTIONS
A fast and economical solution for material flow
Combo Tower Laser
STORAGE SOLUTIONS
The key module to automate material flow with 2D laser machines
Punch Sharp
PUNCHING MACHINES
State-of-the art in servo-electric punching technology
Punch Genius
PUNCHING MACHINES
Outstanding energy efficiency, low maintenance requirement and a high speed of operation.
Shear Genius EVO
PUNCHING AND SHEARING COMBINED MACHINES
Highest productivity with integrated punching and shearing
Shear Brilliance
PUNCHING AND SHEARING COMBINED MACHINES
Outstanding productivity
Combi Sharp
PUNCHING AND LASER CUTTING COMBINED MACHINES
Integrated punching and laser cutting at an affordable price
Combi Genius
PUNCHING AND LASER CUTTING COMBINED MACHINES
Punching + Laser cutting = Superior manufacturing economy
1+1>2
STORIES OF EVOLUTION
Find out how a Prima Power machine took part in an Energy company's success
Prima Power PSBB Helps Power Generation Giant Build Flexible Manufacturing System
Headquartered in Spain, with 8 production centers, 13 subsidiaries worldwide, and a global network made up of 1,000 employees who work closely with more than 130 distributors around the world, HIMOINSA, part of the Yanmar Group, is one of the top global giants that designs, manufactures and distributes power generation equipment.
30+ Years of experience and still growing
Lasercraft USA Knows 5-Axis Laser Cutting Backed By 30 Years Experience And The Latest Technology -- Success Grows Using A Newly Acquired LASERDYNE® 430 With BeamDirector®
Prima Power EBe Express Bender Increases Productivity & Quality at Georgia Job Shop
When Randy Williams opened his job shop, he was already a seasoned fabricator. “I grew up with metal fabrication,” explains Williams. “My dad was an aerospace engineer who built trampolines part-time when I was 10 years old, and I helped build parts in the basement. His business evolved into making ferris wheels and other portable amusement rides, but eventually the liability insurance became too challenging for the small company.”
Laser Genius: a smart buy for Midwest Job Shop
For the past five years, R & M Manufacturing has faced an interesting challenge. The company has experienced a strong growth cycle, and projections are even stronger for the future with such customer industries as electrical, power generation, solar, air purification, HVAC, home & building, etc.