Prima Power in the metal furniture, panels and storage sector
Find out what we do in the metal furniture, panels, and storage sector
If metal furniture was traditionally bought for factories and offices, today it is increasingly being used in places such as schools, hospitals, and gyms, where efficient, well organized spaces are needed. The modern trends meet the use of pre-finished, high-quality materials, which respond to the need of a contemporary design and innovative aesthetic standards, as well as of lockers, which are located in easily accessible public spaces and can be used for courier delivery.
We are well aware of the main need in this sector: high productivity combined with very high quality parts.
The metal furniture sector also has a growing need for production volume flexibility and freedom of design, with a consequent demand for highly versatile production tools.
Another typical aspect of this sector is the wide use of pre-painted materials.
ADAPTABILITY
Efficient on their own and unbeatable when integrated into a system, our machines enable rapid product switching.
LISTENING
We customise our machines to your actual needs.
SMART
Smart machines, equipped with software, are the perfect allies to design your production.
Solutions
Find your ideal solution
Our punching machines and our wide range of press brakes are the most widespread machines in this sector, especially among small and medium-sized businesses as they allow extreme flexibility as well as an excellent cost efficiency ratio.
Our combined punching-shearing systems allow for maximum flexibility and productivity with exceptional material savings.
Our panel benders are widely used for manufacturing metal furniture components because they suit the part dimensions, gauge, volumes, and batches typical of the steel furnishing industry.
Our PSBB (short for punching, right-angle shearing, buffering and bending) is a fully automated manufacturing line for processing raw sheets from packs or directly from coils into pre-bent, high-quality sheet metal components. It is the perfect solution for lights-out production for even the most complex components from a variety of materials that can be managed automatically.
The use of 2D laser technology offers flexibility in terms of component shape, lot size, and design freedom. There is virtually no limit to the shapes that can be made with the laser.
The flexibility of the punch-laser combination is a winning feature when you require different processing technologies.
Our 3D laser machines are also used to customize standard profiles in small batches or even as a single piece. The flexibility of the laser is a winning feature when it comes to customizing products after the forming process, as there is a significant level of low-cost personalization with very high accuracy.
The wide range of Prima Power automation modules combines high productivity with flexibility and can be gradually integrated as production needs grow.
Our range of services complements our advanced technology and is the key to increasing productivity and profit.
All our products are designed and developed based on the "Green Means concept" which brings together productivity and eco-compatibility.
Application examples
Behind every component there is a Prima Power machine
- all sheet metal parts and panels can be processed with our machines
- customised profiles
Related technologies
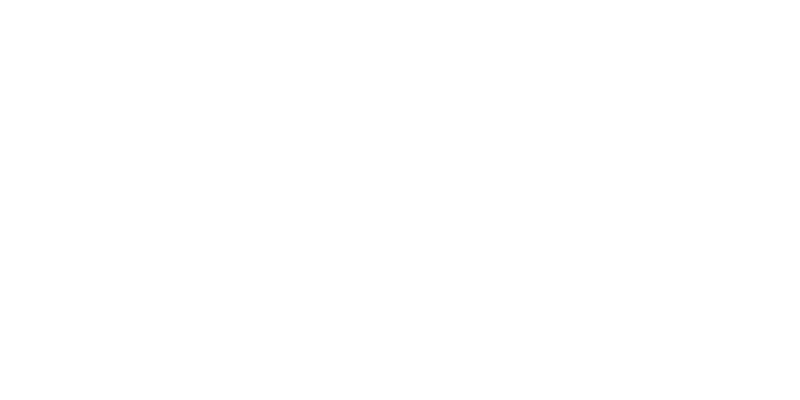
Browse our technologies to choose your machine
Platino Linear
2D LASER CUTTING MACHINE
The reliable and productive solution for cost-effective 2D laser processing
eP Genius
PRESS BRAKES
Efficient servo-electric bending solution with a fast and automatic tools change storage
FBe Fast Bend
PANEL BENDERS
The answer to multiple applications. Semi-automatic bending solution for simple, flexible and accessible production
BCe Bending Centre
PANEL BENDERS
Flexibility at your service semi automatic panel bender combining flexibility and productivity
PunchBend
FLEXIBLE MANUFACTURING SYSTEMS
From cut-to-size material to ready-bent components
Night Train FMS®
FLEXIBLE MANUFACTURING SYSTEMS
Leading technology storage solution in automated flexible manufacturing systems
Fast Loading storage
STORAGE SOLUTIONS
A fast and economical solution for material flow
Combo Tower Laser
STORAGE SOLUTIONS
The key module to automate material flow with 2D laser machines
Punch Genius
PUNCHING MACHINES
Outstanding energy efficiency, low maintenance requirement and a high speed of operation.
Punch Sharp
PUNCHING MACHINES
State-of-the art in servo-electric punching technology
Combi Sharp
PUNCHING AND LASER CUTTING COMBINED MACHINES
Integrated punching and laser cutting at an affordable price
Combi Genius
PUNCHING AND LASER CUTTING COMBINED MACHINES
Punching + Laser cutting = Superior manufacturing economy
1+1>2
STORIES OF EVOLUTION
Find out how a Prima Power machine took part in a Steel furniture, panels and warehousing company's success
Deluxe sheet metal processing
The construction phase of the new Biohort manufacturing site in Herzogsdorf (Upper Austria) lasted just over a year. With cutting-edge industry standards and optimised process cycles, the specialist for storage space solutions created new resources for further growth with new Plant 2, an addition to its Neufelden headquarters.
Vision: that all-human drive towards evolution
Discover Brink and Prima Power partnership, a success story made of human connections.