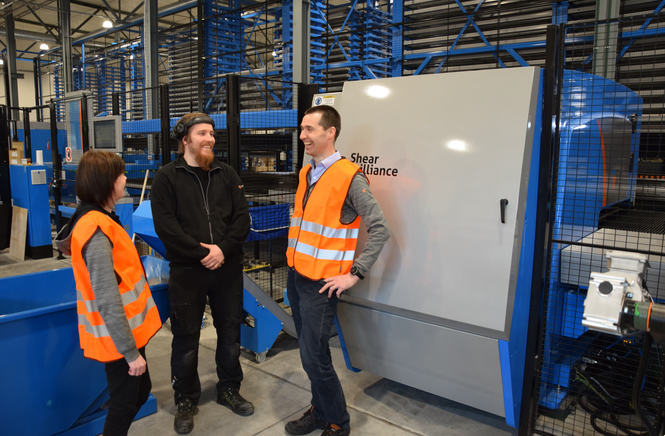
Steelcomp invests in a new factory with advanced automation
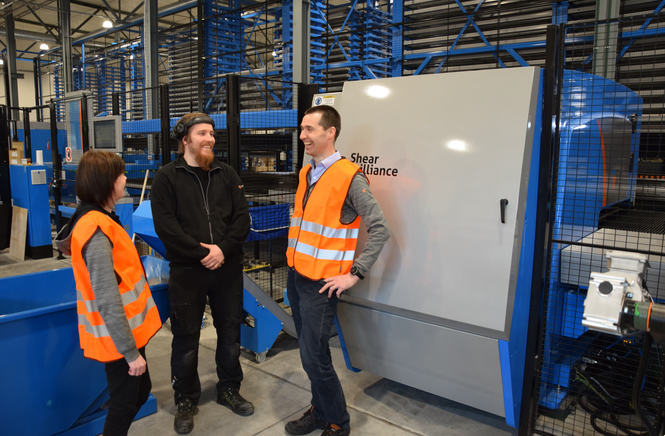
Steelcomp Oy will continue its strong production development work in its operations in Kauhava, Finland. With a newly completed plant extending over more than 5,000 square meters and extensive investments in Prima Power production automation, the company is on the road to strong growth for years to come.
Steelcomp’s momentum continues. The company, which started in 2006, has now grown into a group employing about one hundred metal professionals, across operations in Kauhava, Vaasa and Vähäkyrö in western Finland. Steelcomp Oy’s net sales totaled approximately €8.7 million in 2021, and Steelcomp Vaasa Oy’s were €10.8 million.
“Steelcomp has always relied on bold moves in its operations, and that means investing in both technology and expansion,” says Kimmo Niska, the company’s founder, President and CEO.
“Steelcomp has always relied on bold moves in its operations, and that means investing in both technology and expansion.”
The big leap forward for the company was the acquisition that led to the creation of another Steelcomp unit in Vaasa, ten years ago. Hence, Steelcomp became the group that now includes both Steelcomp Oy and Steelcomp Vaasa Oy. “In Kauhava, we subcontract extensive sheet metal production, and in Vaasa, the core is contract manufacturing, welding, surface treatment and assembly with stages, often for international players,” Niska concludes.
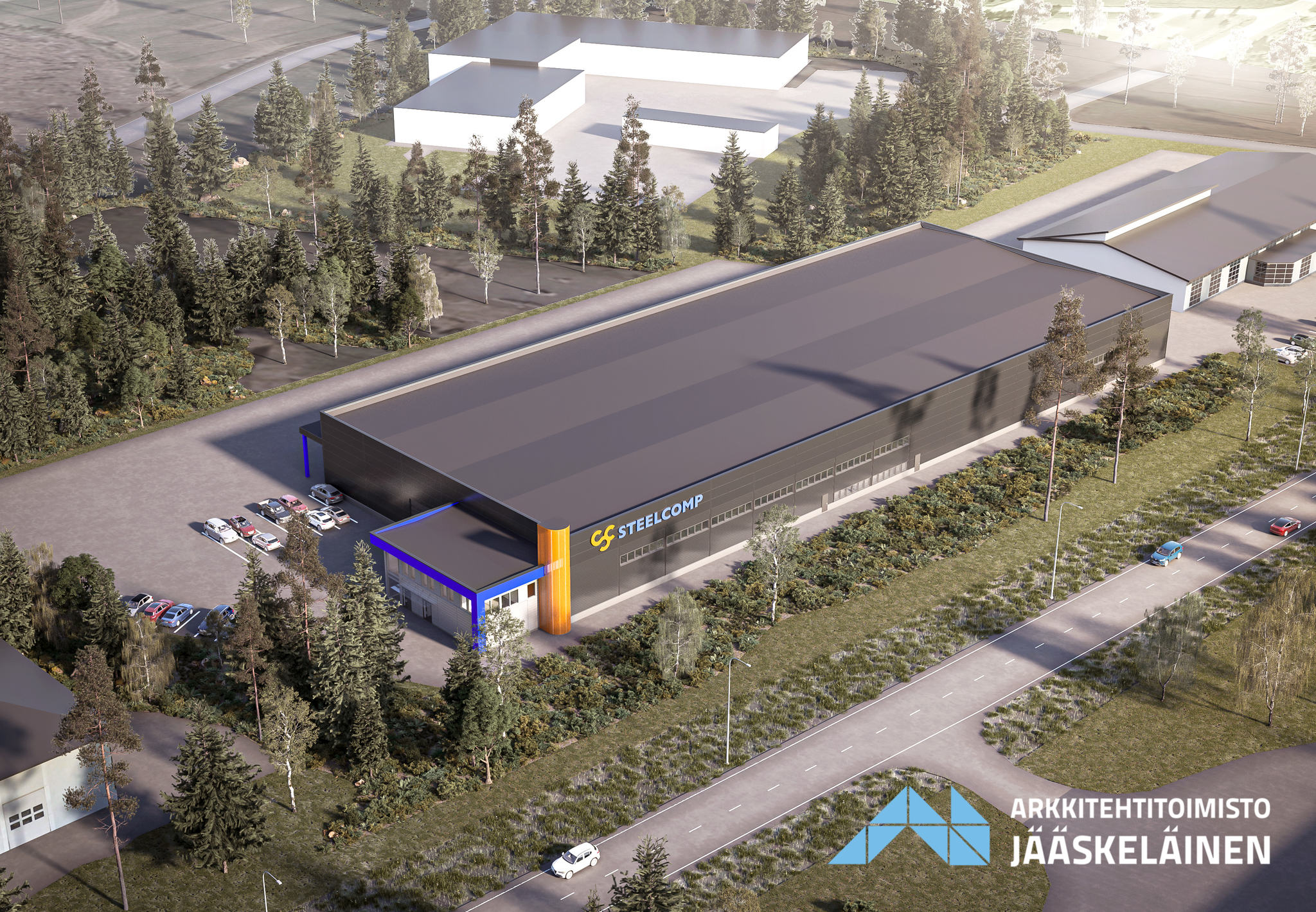
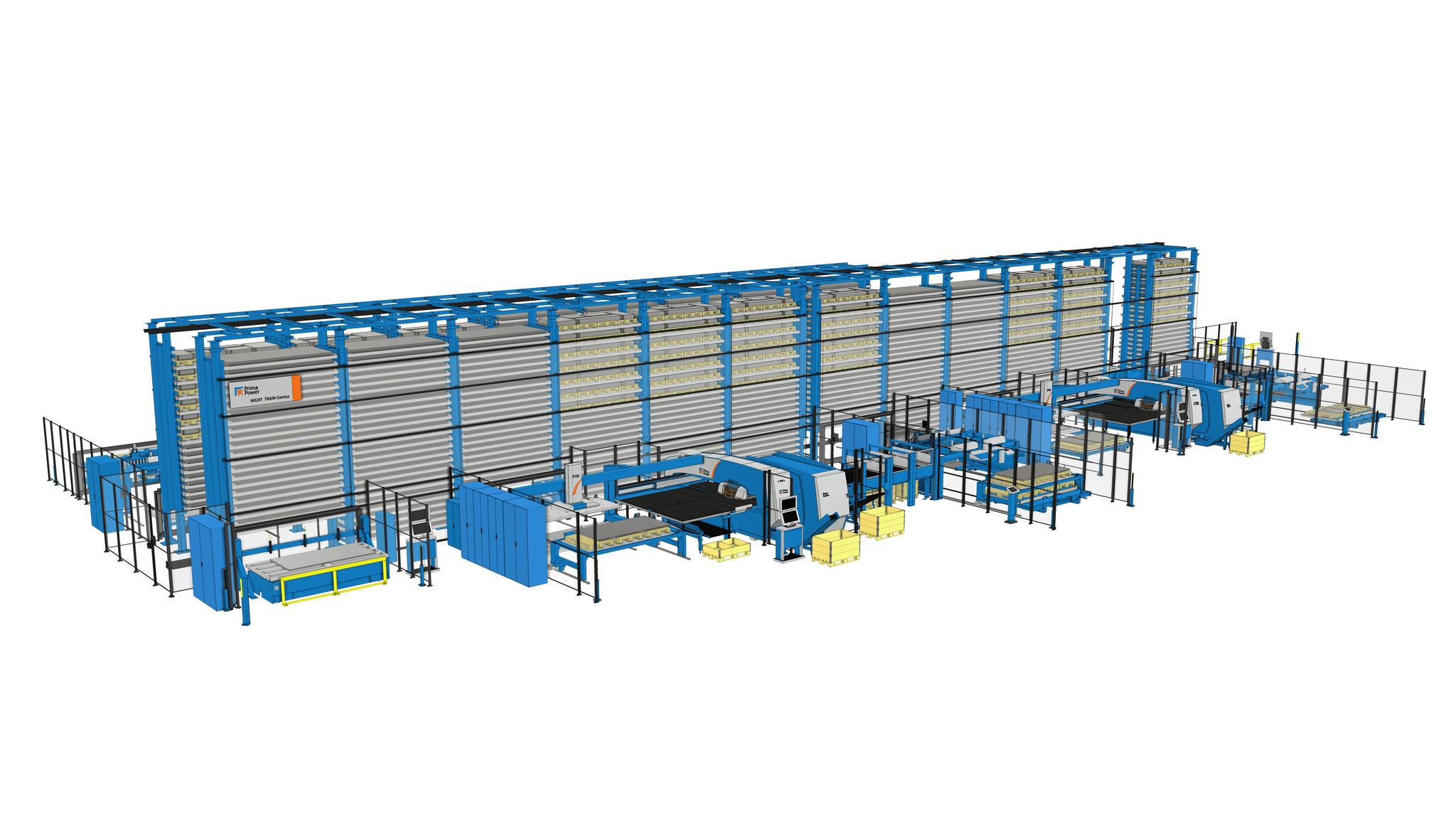
A NEW PRODUCTIONE SPACE OF 5,300 SQUARE METERS
The Steelcomp Group is currently renewing its technology in line with its long-term strategic guidelines. A new round of investment is allowing it to take another step along its journey: according to the principles it has followed since the beginning, the goal is to increase automation in production.
“Today, automation is becoming a key success factor in the industry. Automation is a crucial element in production efficiency, it increases competitiveness in the market and it also alleviates the challenges related to the bigger issue – that is, the availability of skilled labor. Indeed, an important image factor comes into play, because automation increases the company’s attractiveness both for customers and for top production professionals,” says Niska.
“Automation increases the company’s attractiveness both for customers and for top production professionals.”
To enable a fresh investment round focusing on automation, Steelcomp has recently relocated its operations in Kauhava to new 5,300-square-meter premises, a project implemented together with the City of Kauhava. The new area will allow for further new extensions in the future.
“The location is great, right along the main road, and the facilities are tailored to our needs. There are enough light and space, and we addressed one aspect of job satisfaction by dividing the production space into two parts, which can affect the transmission of sound. The lightweight wall structure we added strongly isolates the sound-producing sheet metal work center area from the bending and assembly area,” says Niska.
Environmental issues have also been taken into account. “The new plant is energy efficient; it heats with low-emission energy, and – just to mention one example – we carefully utilize the heat generated by the machines,” says Kukka-Maaria Kenkkilä, Development Manager.
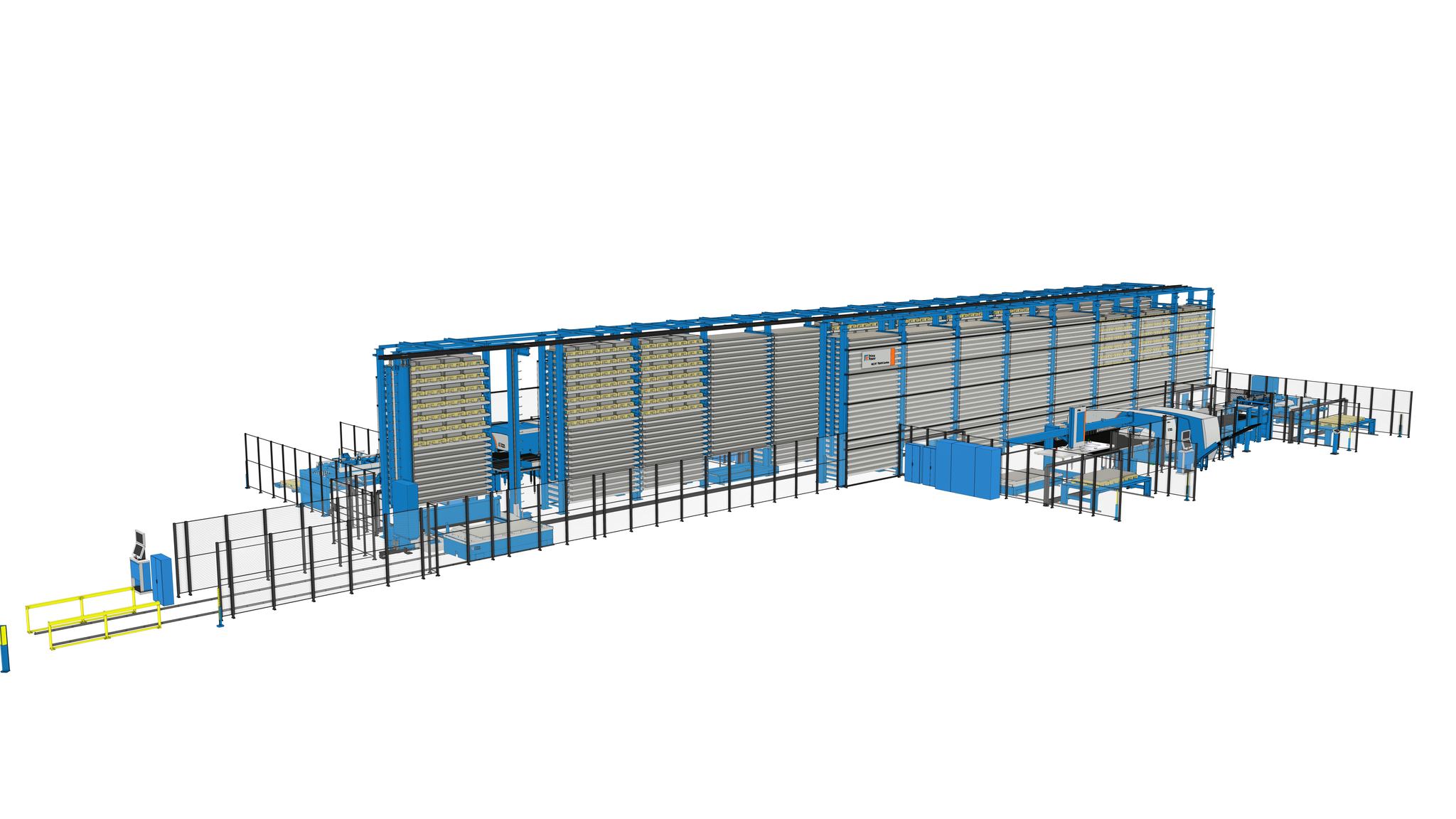
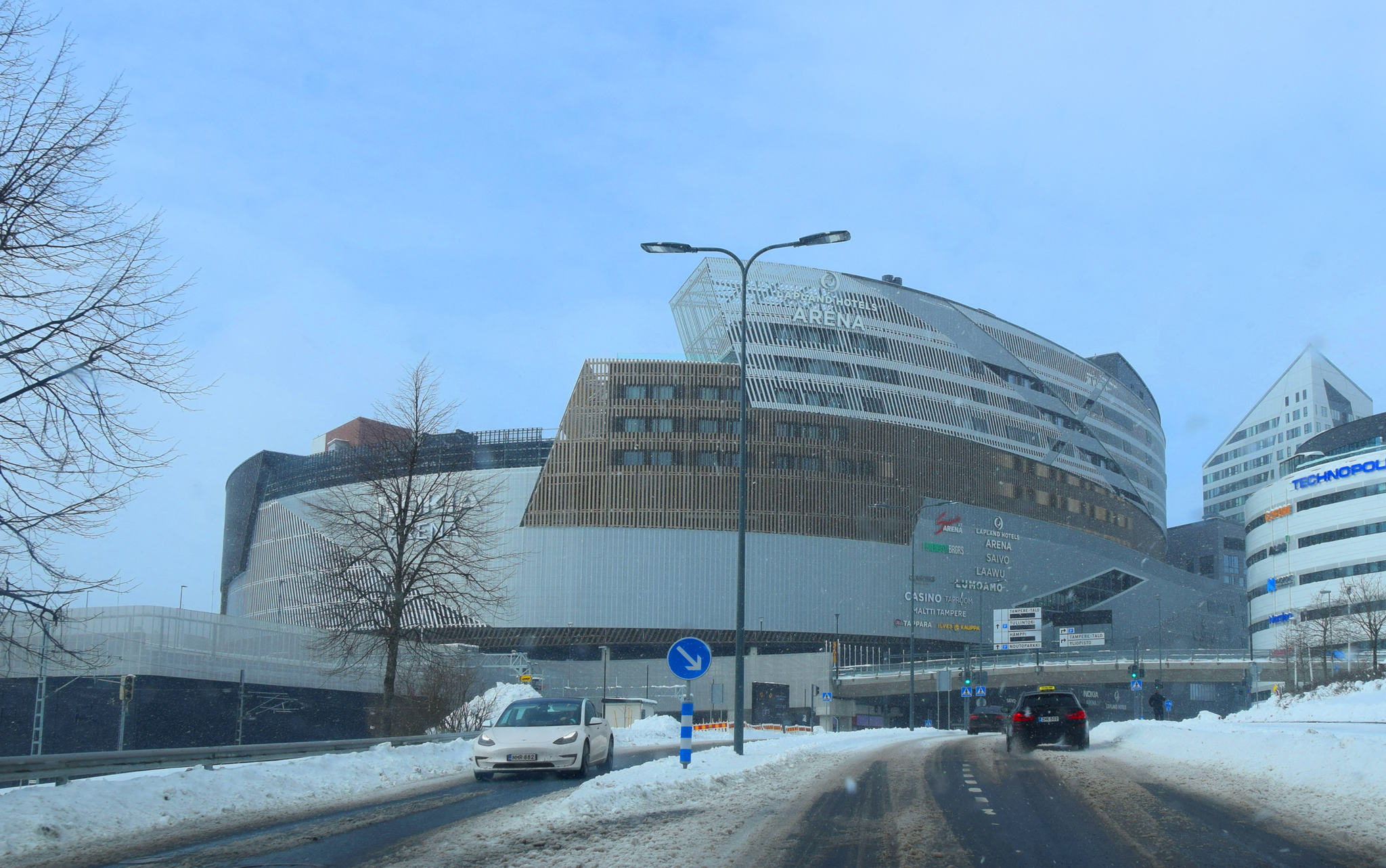
AUTOMATION TECHNOLOGY FOR FUTURE PRODUCTION
The move to new premises has made it possible to invest in new production technology. Steelcomp Oy is currently strengthening its production machinery with specific investments, and the first units have already arrived at the new plant.
"The new facility allowed Steelcomp’s plant to invest in Prima Power’s Night Train FMS automated storage system, a flexible and modular storage solution to automate the material flow."
The new facility allowed Steelcomp’s plant to invest in Prima Power’s Night Train FMS automated storage system, a flexible and modular storage solution to automate the material flow. The system installed at Steelcomp is more than 50 meters long and has a total capacity of over 400 drawers; it automates the material and information systems of the factory’s cutting and punching operations and combines the individual manufacturing steps into one process. In addition, the warehouse is very space efficient.
Four machine units in the punching and cutting sector will be connected to the system in the future, thus enabling even more efficient automatic production.
In connection with the Night Train, existing machinery and two completely new production units will be integrated in the new location. Already in place at the new plant is the fresh Shear Brilliance, a fast Prima Power combined punching and right-angle shearing system capable of processing plates up to four meters. The composite materials, the servo-electric technology and the linear drives all contribute to enabling high-performance yet ecological production work. Prima Power’s ECOPUNCH® concept is an astonishing money saver in terms of energy consumption, making it possible to manufacture more parts with the same energy.
"Prima Power’s ECOPUNCH® concept is an astonishing money saver in terms of energy consumption."
Another new machine for the manufacturing line will arrive in the fall: Prima Power’s 4-kW Combi Genius, which combines punching and laser cutting functions in one machine. In total, Steelcomp’s investment in machinery and equipment is over three million euros.
“The new factory and recent technology investments will enable the company to grow in the future, which always remains our goal. At the same time, the new plant and investment will create new jobs, and we aim to increase the number of employees by at least twenty new professionals in the near future. Recruitment is underway,” says Niska.
In the next few years, technology development will continue at Steelcomp Oy, especially in regard to bending operations. “Substantially increasing automation is a key goal in this sector as well,” says Niska.
Read this and many other stories on the last issue of our Power Line magazine.
The article, written by Kari Harju, was first published in Finnish trade magazine Konekuriiri.
The new plant is energy efficient; it heats with low-emission energy, and – just to mention one example – we carefully utilize the heat generated by the machines.
Are you looking for a similar solution for your company? Find it here
Night Train FMS®
FLEXIBLE MANUFACTURING SYSTEMS
Leading technology storage solution in automated flexible manufacturing systems
Combi Genius
PUNCHING AND LASER CUTTING COMBINED MACHINES
Punching + Laser cutting = Superior manufacturing economy
1+1>2
Shear Brilliance
PUNCHING AND SHEARING COMBINED MACHINES