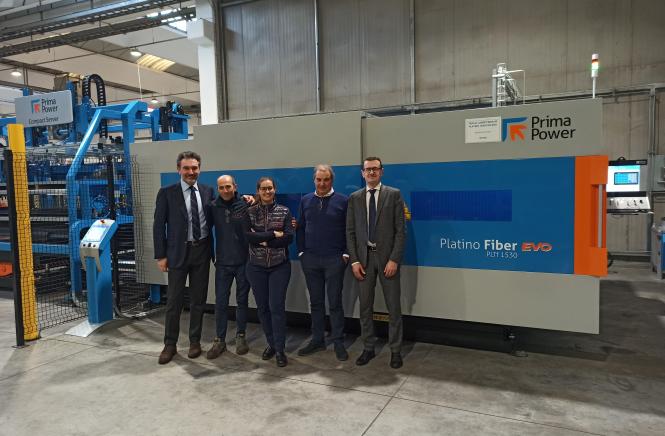
Flexibility and precision in the manufacture of custom rack cabinets
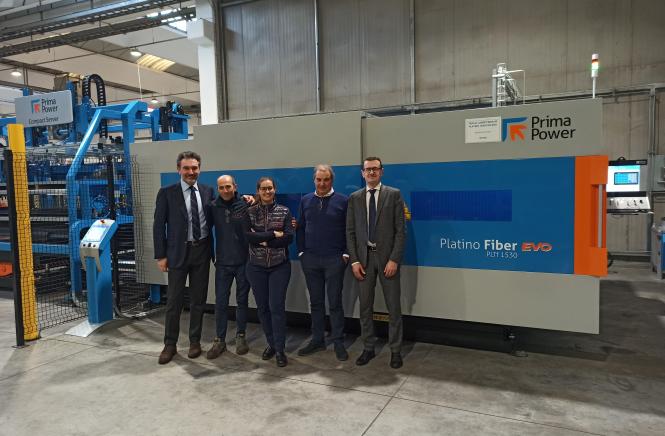
After having chosen Prima Power as the supplier of the company's very first laser cutting machine, ATP decided to continue focusing on the quality and technology of the Italian manufacturer by also investing in a servo-electric bending machine
The decrease in batch volumes and the growing demand for product customisation in the last decade have led manufacturing companies in the sheet metal and carpentry industry to seek greater flexibility to maintain competitiveness while simutaneously containing costs. Modern numerical control machines for sheet metal processing enable greater flexibility and precision when processing single pieces. This is precisely why ATP from Spino d’Adda, Cremona has turned to Prima Power solutions for the renewal of its fleet. ATP was founded by Gianpaolo Prandelli and his brother Giacomo in the late 1980s as a construction company for moulds and metal blanking. “In the mid-90s, we also installed CNC milling and turning centres to adapt to customer demands,” begins Gianpaolo Prandelli, owner of ATP. “Subsequently, the market moved towards production with greater flexibility, lower costs and a decrease in the supply of equipment, so we decided to invest in cutting and bending machines for sheet metal.” ATP immediately specialised in the production of carpentry for electronics, such as data transmission and telephony cabinets. Today the company's target market is the railway sector, divided between the station and line signalling sector and the rolling stock sector, i.e. the locomotive. “We have been certified for welding on board trains for the last 12 years,” continues Prandelli, “We’ve become specialised in custom rack structures on board trains for telecommunications, power electronics and signalling in carriages. Cabinets are supplied both to design and by customising the structure depending on the internal components and how it will be fixed to the locomotive. Our technical department adapts our frame to the customer's specifications and then we also carry out a FEM analysis for resistance checks, as required by railway regulations.”
Support in engineering
ATP is a structured company with 30 employees and an annual turnover of more than €6m. It has rapidly evolved to provide complete support throughout the design phase. In addition to working as a contractor for the production of carpentry, it also provides engineering services. The technical department receives customer drawings, studies the best solution for the production process and cost optimisation before then sending the modified drawings back to the customer to be updated. The experience and various certifications achieved over the years enables ATP to guarantee high quality standards. The only currently outsourced processing stages are surface treatments and painting. “We have set up a partnership with another company in Spino d’Adda since they have quality standard certifications and use state-of-the-art equipment such as nanotechnology cleaning,” says the owner of ATP. “This means we are able to be competitive with costs of the finished product and we can guarantee quality and reliability of the painting in compliance with the deadlines.” The support given from the design of the additional processes right through to the cutting and bending of the sheet metal is the added value that ATP provides their customers. To achieve greater reactivity and better control of the quality of the complete product, the ATP owners have also decided to internalise the laser cutting process, which was previously outsourced for thicker sheets.
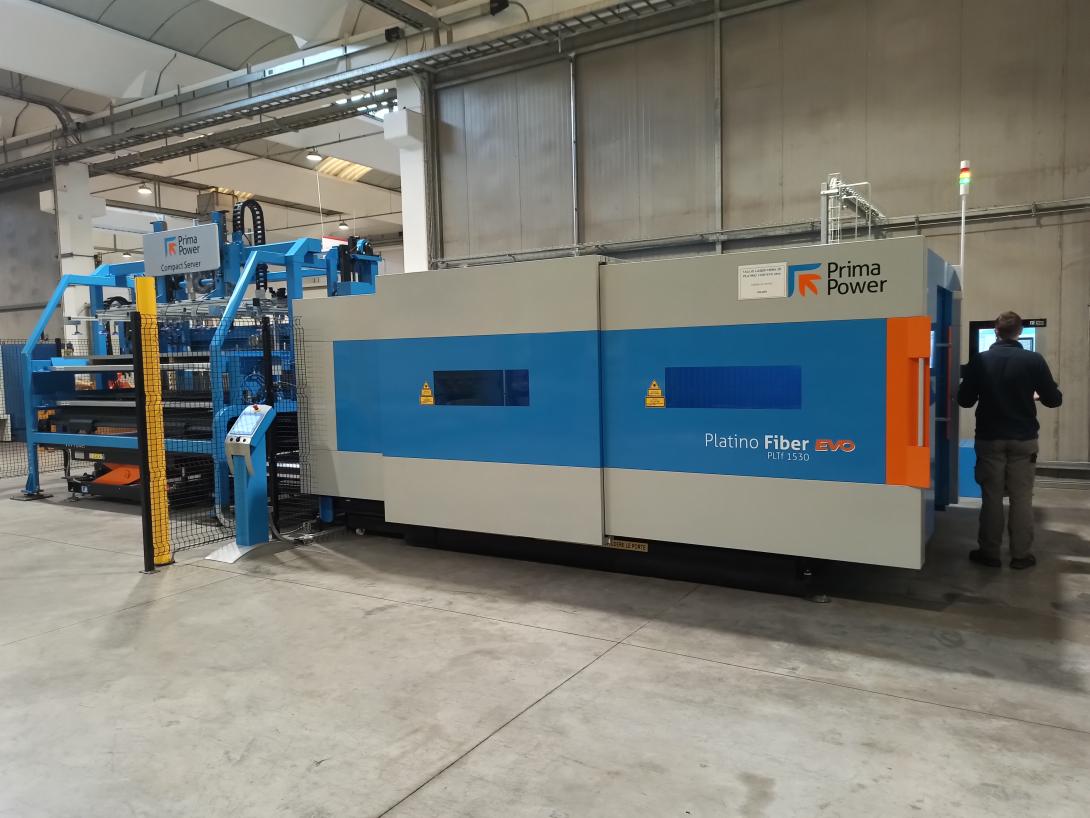
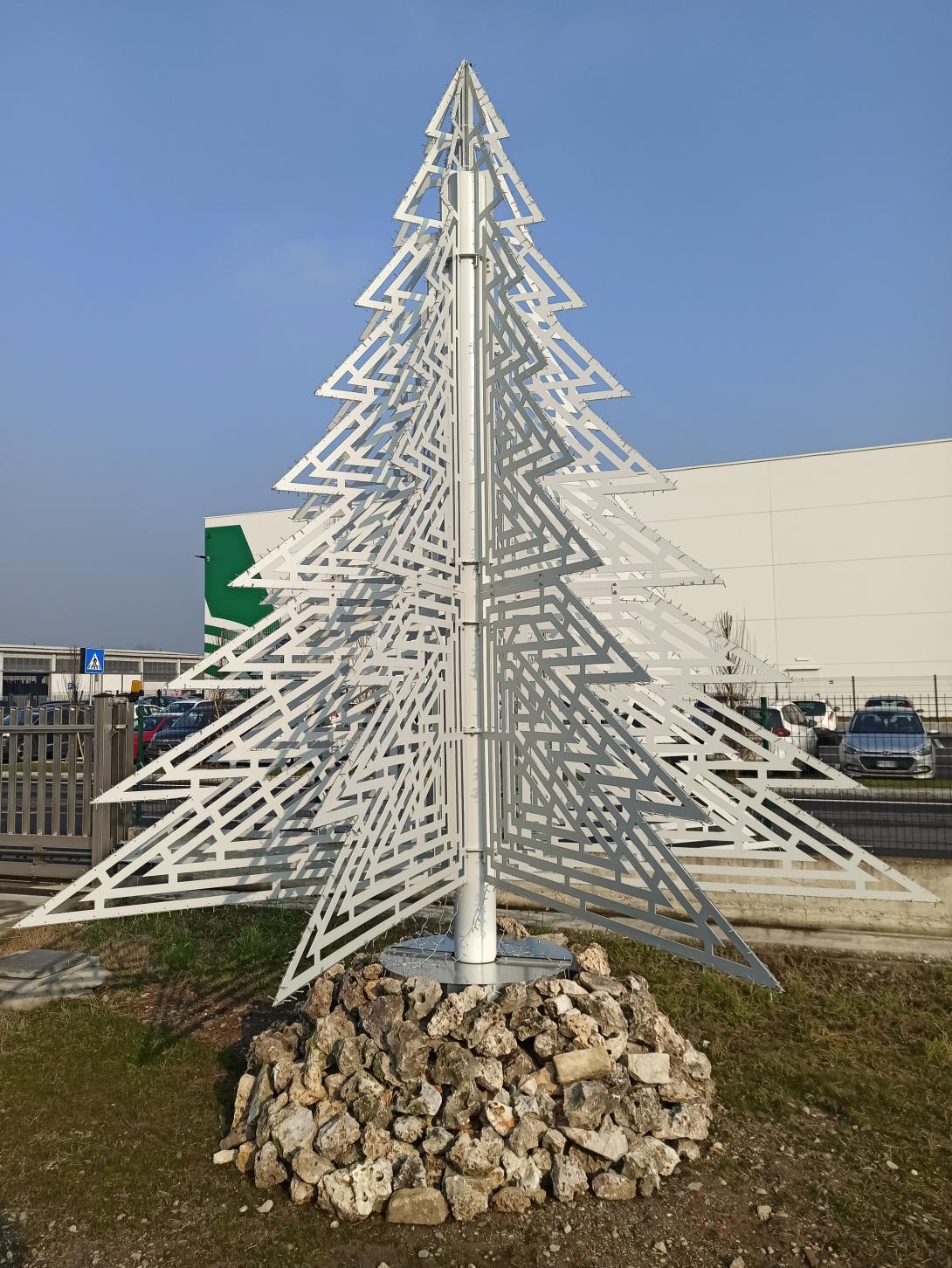
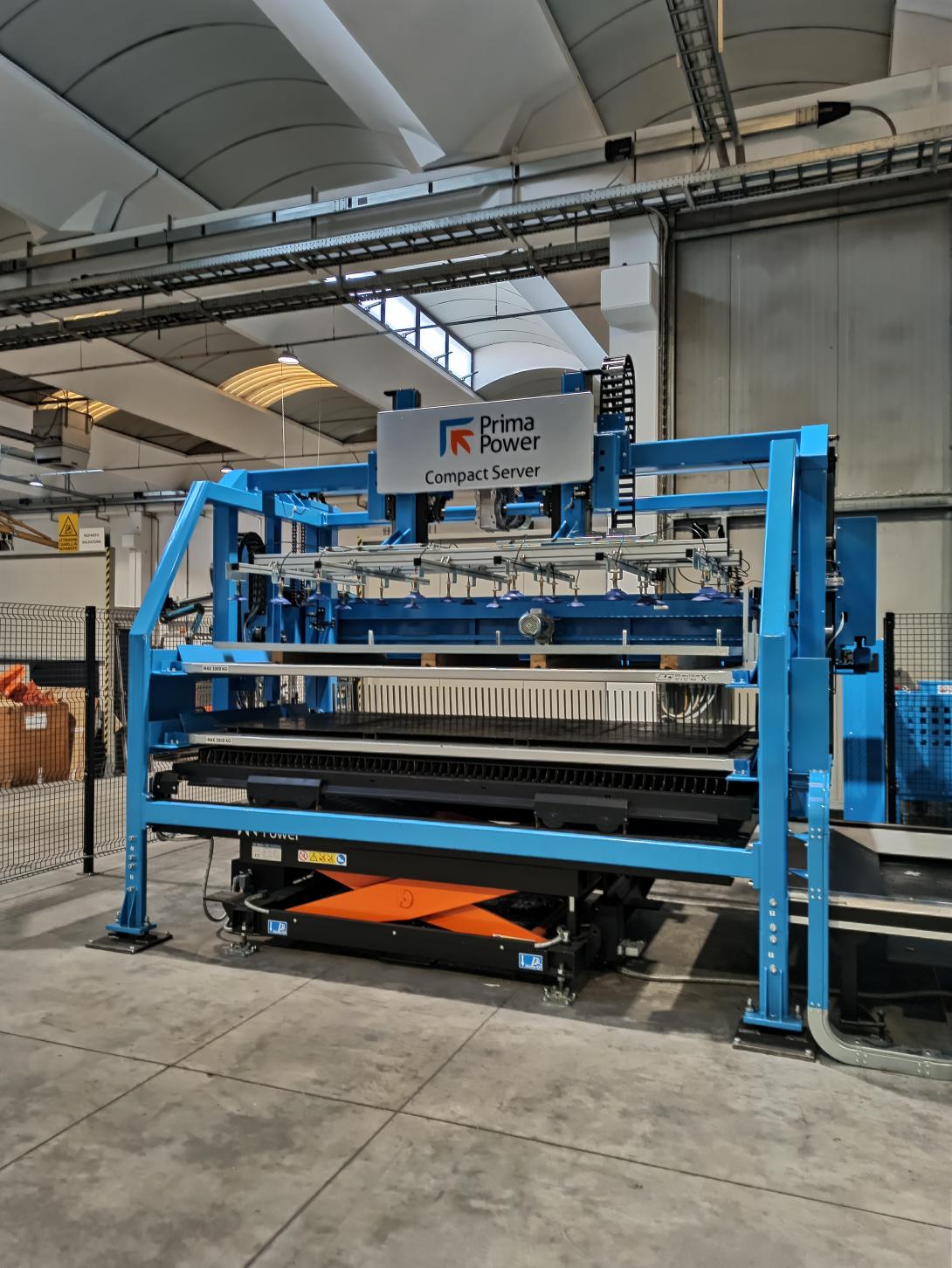
Precision laser cutting
“Outsourcing penalised our flexibility,” explains Gianpaolo Prandelli, “when faced with an important order for a foreign customer last year, we decided to invest in a laser cutting machine. Our contact with Prima Power was consolidated during the Open House event by the Prima Industrie group. We were positively impressed by the technical solutions during our visit to the showroom and we jumped at the specificities and advantages we would gain over our direct competitors. We found a reliable partner in Prima Power, who delivered the machine to us in a very short space of time.” ATP decided to go with the Platino Fiber 1530 model for 2D cutting with a CF series 4kW fibre source. The machine has a 3m x 1.5m working area and is equipped with an additional side opening as well as the front one. The Platino is characterised by its high rigidity that comes from the synthetic granite bearing structure supporting the cutting head on an aluminium cantilever beam. “This configuration,” says the ATP owner, “allows greater access to the work area through the side door. This feature gives a significant advantage in terms of cleanliness and flexibility. You can easily access inside the Platino with a vacuum cleaner from the side door and you can put a new piece on the cutting table.” If the user needs to cut a new piece with a certain thickness, the batch can be interrupted to add the new piece through the side opening. Once the cutting program has been set, the new piece is processed, extracted through the same opening and batch processing can resume without further downtime. The Platino Fiber is also recognisable for its precision. “Our pieces are quite complex geometric shapes and are already finished with a limited machining allowance, so we can’t afford any dimensional deviations,” points out Prandelli. “One of the first tests we carried out on the Prima Power machine was to cut a piece at both ends of the working volume. In terms of dimensional accuracy, we found that the machine was precise to the nearest hundredth. In the past, we usually made the edge slightly higher on the first pieces, while the new machine gives us the exact same edge on the first piece as it does on the last.”
Additional benefits
The Platino Fiber allows ATP to cut very small pieces with reduced sheet thicknesses, down to 0.5 mm. The company used to use wire EDM for this type of processing in the past because it was very difficult to get high dimensional accuracy using blanking dies without deforming the piece. In terms of environmental sustainability and in addition to replacing the EDM processing, the Prima Power machine has also allowed ATP to avoid processing satin finishing. Material can be cut directly with the protective film and use of the wet polishing machine is no longer required. This brings about both economic and ecological savings by removing the disposal of sludge and cloths for satin finishing. In terms of optimal sheet metal exploitation, Prima Power programming software adds the different geometries of the pieces to be produced to the available area according to the quantities entered by the operator and calculates the number of sheets required to complete production with limited waste. “The software,” highlights Prandelli, “is another Prima Power strong point, because it gives high performance whilst also being intuitive and easy to use, which reinforces the flexibility of the machine. We avoid stocking up on smaller volumes and batches of pieces. As for punching machines, it's now easier for us to customise a product for customers who require drilling or ventilation openings on the standard panel. Furthermore, laser power was parametrised according to the thickness of the sheet and material type during its installation.” This means ATP operators don’t have to change processing parameters as the product changes. The Platino is designed to work even on unmanned shifts. Indeed, it is equipped with an auto shut-off system ?? and a Compact Server loading and unloading system, with an automatic nozzle changer and a camera that checks for tool centring and wear. If excessive nozzle wear is detected, the system will replace the tool.
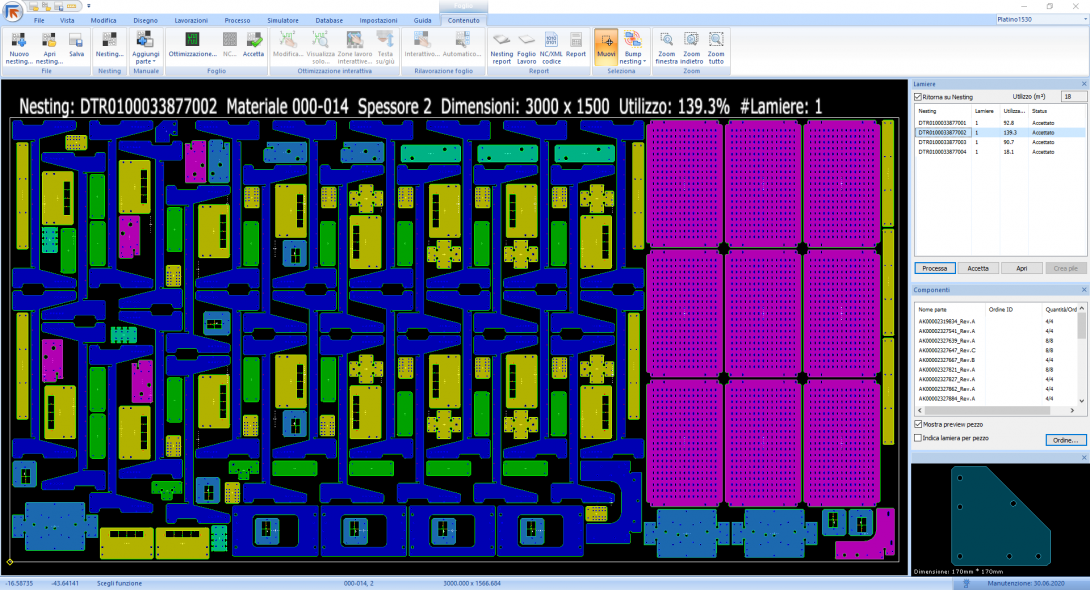

Outsourcing penalized us on flexibility: to deal with an important order with a foreign customer, last year we decided to invest in a laser cutting machine. In Prima Power we found a reliable partner who delivered the machine to us in a short time
Are you looking for a similar solution for your company? Find it here
Platino Fiber
CORTE A LASER 2D
Rentável para uma mistura de produção que inclui todos os materiais e espessuras
eP Series
SERWOELEKTRYCZNE PRASY KRAWĘDZIOWE